
8 minute read
BRAND NEW
JOSCO Will Apply the FASTAR® Coating to Its Next Generation 1100TEU Liners
The antifouling system FASTAR® I developed by Nippon Paint Marine will be used to protect energy efficient vessels.
The Tsuneishi Group Shipbuilding has recently announced that it is using Nippon Paint Marine’s nano-based antifouling FASTAR I® to protect a trio of energy-efficient box ships that the company is building for Jiangsu Ocean Shipping Co (JOSCO). Each of the three vessels has an overall length of 146 metres and a 23.25 metres beam and employs Tsuneishi’s low-resistance hull form and an array of energy-saving technologies: the TOP-GR system optimises number, diameter, shape and geometric distribution of propeller blades to achieve greater propulsive efficiency, while MT-FAST adds a wing-like device to the front of the propeller to alter water flows. In addition, the company is planning to also use the antifouling FASTAR I, a solution developed by Nippon Paint Marine that contains completely new hydrophilic and hydrophobic nano-sized silyl acrylate components that will allow a more precise control of the release of biocides. “We have very good experience with Nippon Paint Marine systems on our vessels, so were keen to add to the overall energy efficiency of these next generation vessels with the new FASTAR system. With the installation of advanced technologies designed to reduce energy consumption and emissions, these vessels will be the greenest in the JOSCO fleet. The application of these two technologies combined with FASTAR is expected to contribute to significant fuel savings and help us meet environmental standards,” stated Lian Jian Guo, the general manager of the Technical Division at JOSCO. “JOSCO’s experience with our LF-Sea® and A-LF-Sea® antifouling systems has delivered fuel savings of up to 8%, which can equate to a voyage free of fuel costs every twelfth trip or so. We anticipate FASTAR will deliver further cost savings and environmental efficiencies. It is by precisely controlling the release of biocides that we have been able to deliver a high-performing, low-polishing antifouling system that not only delivers unprecedented commercial benefits but also helps shipowners and operators meet emissions abatement and energy efficiency targets,” added Gerald Mao, the Senior Director of Nippon Paint Marine. “Liner operators like JOSCO are facing increased congestion at port with at least 30-day waiting times so need a coating that delivers consistent 60-month performance unaffected by seawater temperature and vessel speed. FASTAR I has been designed to deliver optimum performance and save fuel after longer idling times, when conventional coatings experience increased biofouling.” The antifouling FASTAR system has already been applied to a passenger ferry and a bulk carrier, and Tsuneishi will also employ it for three similar 1091TEU vessels designed for the intra-regional trade that the company is planning to construct for Taicang Container Lines Co., LTD. “For a containership with 80% activity, operating at 18kts in seawater temperatures of 26 °C, a FASTAR scheme provides 60 months of service from a dry film thickness of 260 μm on the vertical sides and a 160 μm coat of on the flat bottom. A conventional antifouling covering the same 2000m2 area would require 1018 litres of paint versus 1330 litres. We are delighted that Tsuneishi Group’s next generation of energy efficient box ships are being specified with FASTAR. It’s a win-win coating for owners and builders,” concluded Jun Ye, the M & R Sales Director for Nippon Paint Marine in China.
For further information:
© Nippon Paint Marine
www.nipponpaint-marine.com
The mobile and high-performance solution developed by Graco allows to maximise productivity and portability.
Graco Inc. has recently presented the air-powered protective coatings sprayer Contractor King™ and the spray gun Silver Plus HP™, two professional, mobile and high-performance solutions specifically developed for contractors who need a more compact and lighter coatings sprayer. The Contractor King offers the same performances of traditional air-powered sprayers, but ensures a more compact footprint, allowing to maximise productivity and portability: it is mounted on a professional grade compact frame, it is up to 85 pounds (38,5 kg) lighter and 48% smaller. The Silver Plus HP gun is pressure rated up to 7,250 psi (500 bar) and is designed to handle all protective coatings, including high-solid coatings. “Typical air-powered sprayers in the marketplace are very large and heavy-trequiring more time and labour to transport and manoeuvre. The Contractor King air-powered sprayer solves this by offering a smaller weight and size, while at the same time offering the same ‘Big Job’ performance of larger sprayers,” stated Bob Gundersen, the Global Product Marketing Manager for Specialty Applications at Graco. The Contractor King products range is offered in 45:1, 60:1 and 70:1 pressure ratio and it is also available in several packages, including the new “Big 150” ready-to-spray package configured with pressure-rated accessories such as the Xtreme Duty™ high-pressure fluid hose, the Silver Plus spray gun, fittings and the XHD spray tips. In addition, the airpowered sprayer is designed with the QuickChange™ Endurance™ pump that allows an easy on-the-job pump removal and maintenance.
For further information: www.graco.com
© Graco
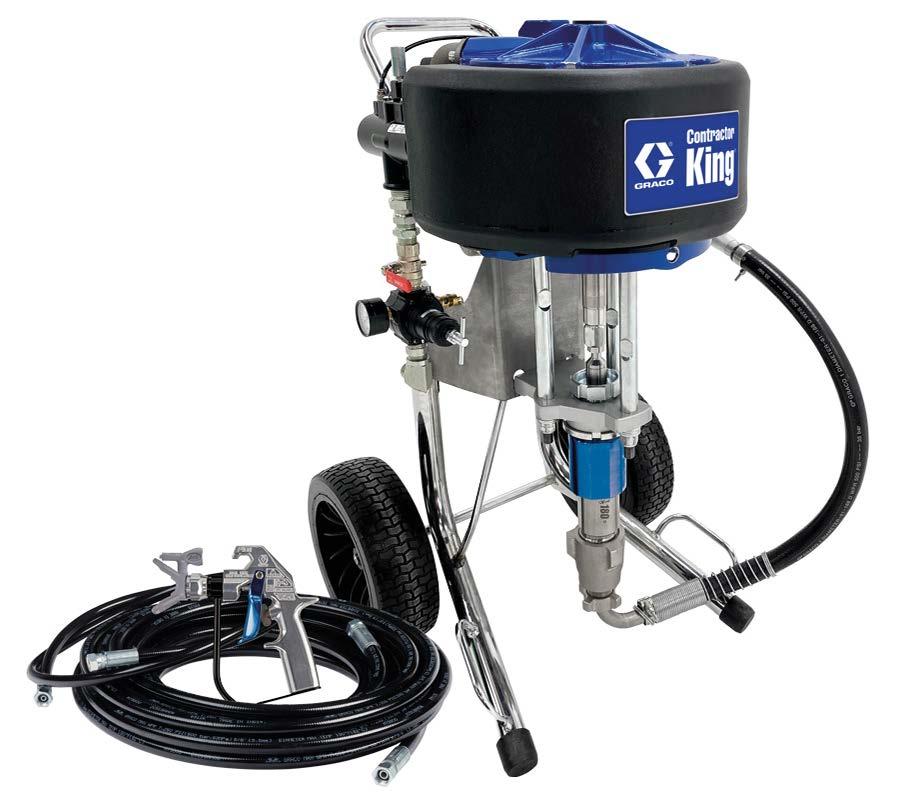
Jotun Will Begin Paint Production in Algeria for the Local Market
The joint venture with Med Investment Holding Spa will allow Jotun to manufacture protective coatings directly in Algeria.
The Jotun Group has recently announced that it has reached an agreement with Med Investment Holding Spa for establishing the joint venture Technover P, that will manufacture paints and coatings in Algeria. In the new site in the district of Tizi-Ouzou (east of Algiers) built by the German company Netzsch, the joint venture will produce Jotun decorative paints and protective coatings according to international standards. With this new investment, Jotun aims to satisfy the increasing demand of the Algerian construction, industrial and energy sector. “This investment shows Jotun’s long-term commitment to the Algerian market. We can now bring our clients in Algeria the highest quality, internationally approved decorative paints and protective coatings. This is in line with Jotun Group’s strategy and values and fits well with Med Investment’s long industrial experience in Algeria,” stated Richard Chapman, the regional director for MEIA Emerging Markets at Jotun. “This production investment is in line with our continuous strategy and focus of developing competitive and quality-focused local production. We have successfully done that in the pharmaceutical sector by increasing significantly locally produced medicine market share. With Jotun’s high quality and technically performing products, we expect that our partnership will succeed in increasing the market share of locally produced quality and performant paint and coating,” concluded Lies Kerrar, the general manager of Med Investment Holding.
For further information: www.jotun.com
Representatives from Jotun, Med Investment and Alusys after signing the agreement.

© Jotun
New Interpon Powder Coatings White Paper
New Interpon powder coatings white paper helps businesses explore innovations and solutions in corrosion protection.
With the damaging effects of corrosion estimated to cost more than 1.5% of a country’s Gross Domestic Product (GDP), businesses are increasingly aware of the critical need to protect the products, buildings, and other structures they create. But since different metal surfaces present different issues and require different approaches to corrosion protection, choosing the right system based on location and application is critical. It not only protects reputations, but it also protects lives. Against this backdrop, AkzoNobel’s Interpon powder coatings team has published a new white paper that explores the principal causes of corrosion and how they can be prevented. It begins by looking at the differences between ferrous and non-ferrous substrates and the different kinds of chemical and mechanical pre-treatments available. It highlights the International Standard against which protective paint systems are measured (ISO 12944), and explains how to accurately benchmark competing products, to ensure like-for-like comparisons and judgments are made. It details the categorization of corrosion (based on C1 being very low risk to C5 very high) and specifically the different systems available within Interpon’s Redox range of powder coatings, including its latest innovation, Redox One Coat. Jorrit van Rijn, Global Segment Manager Industrial in AkzoNobel Powder Coatings, says corrosion protection coating jobs can be complex tasks and various factors need to be taken into consideration. The substrate and how that substrate is pre-treated are key: “Getting this right will determine which powder coating system to use, based on the environment and conditions to which the surface will be exposed,” Jorrit explains. “Choosing the right products to protect metal surfaces from the damaging and costly effects of corrosion is essential, but so too is understanding the different categorization of corrosion and how to meet international standards. Our White Paper helps take the guesswork out of choosing the right system to meet your specific needs.” Jorrit says that whether working through Interpon’s approved applicator network or being supported by its technical support team direct, they help businesses arrive at the right decision: “With the support of our local R&D laboratories, which can provide extensive testing services, and our bespoke System Finder tool, we can guide our customers to the appropriate coating system for the most difficult of tasks.”
For further information: https://bit.ly/3GTIuHT

© Teknos
Teknos Launches All-In-One Solution for Fire Protection of Steel
Teknos launched a new, all-in-one 100% solids 2-component fire protection coating for steel applications in indoor and outdoor spaces.
Teknos launched HENSOTHERM 920 KS, a new intumescent 100% high solids VOC-free coating that reaches all four fire classes R30/60/90/120. The quality of passive fire protection is ensured with ETA accreditation, with further environmental and standardization certificates. The full coating system includes Teknos primer and topcoat, which ensure corrosion protection and a high-quality finish. With this intumescent system, corrosivity category up to C5 High can be achieved. The system is ideal for paint shop application, for which it is mainly recommended but, when necessary, it can also be applied on-site. The quick drying time of the new paint system enables more economical construction projects, as it contributes to shorter lead times and advances delivery date. In fact, the coated steel objects can be transported after 24 hours of drying time.
For further information: www.teknos.com
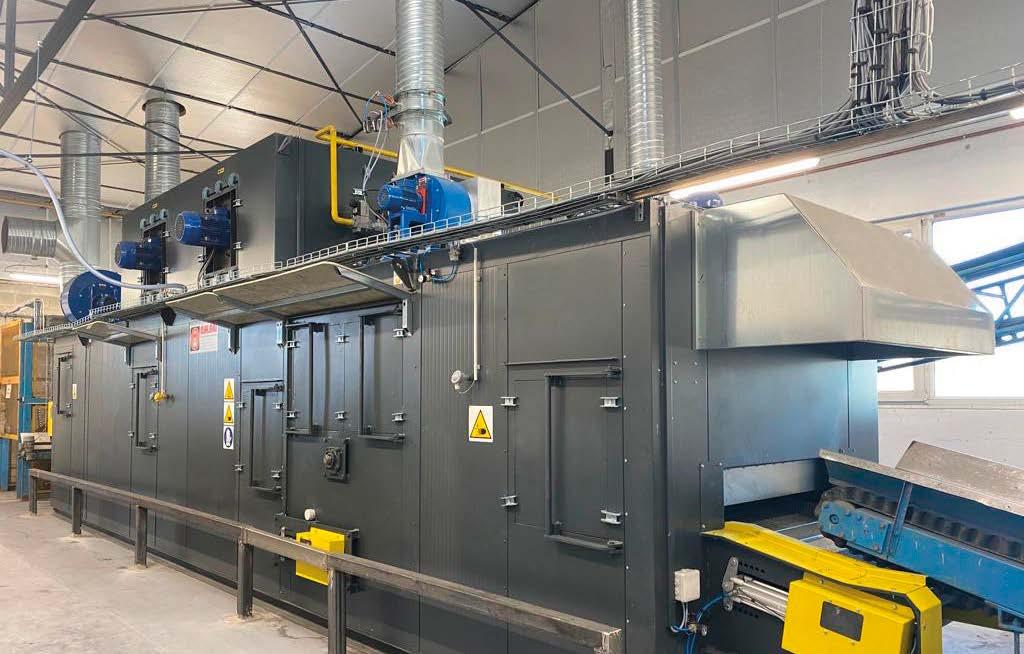
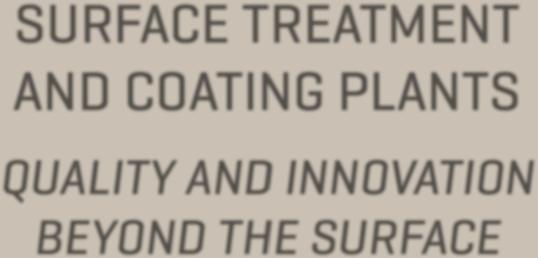
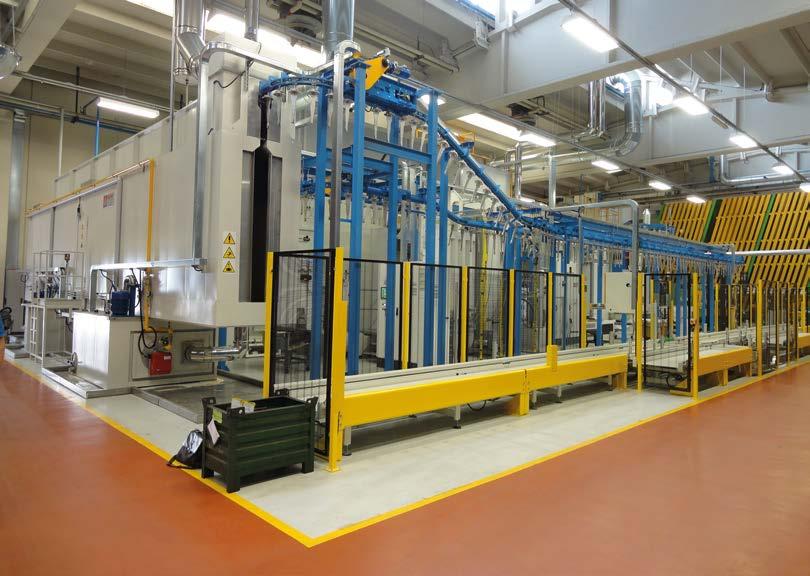