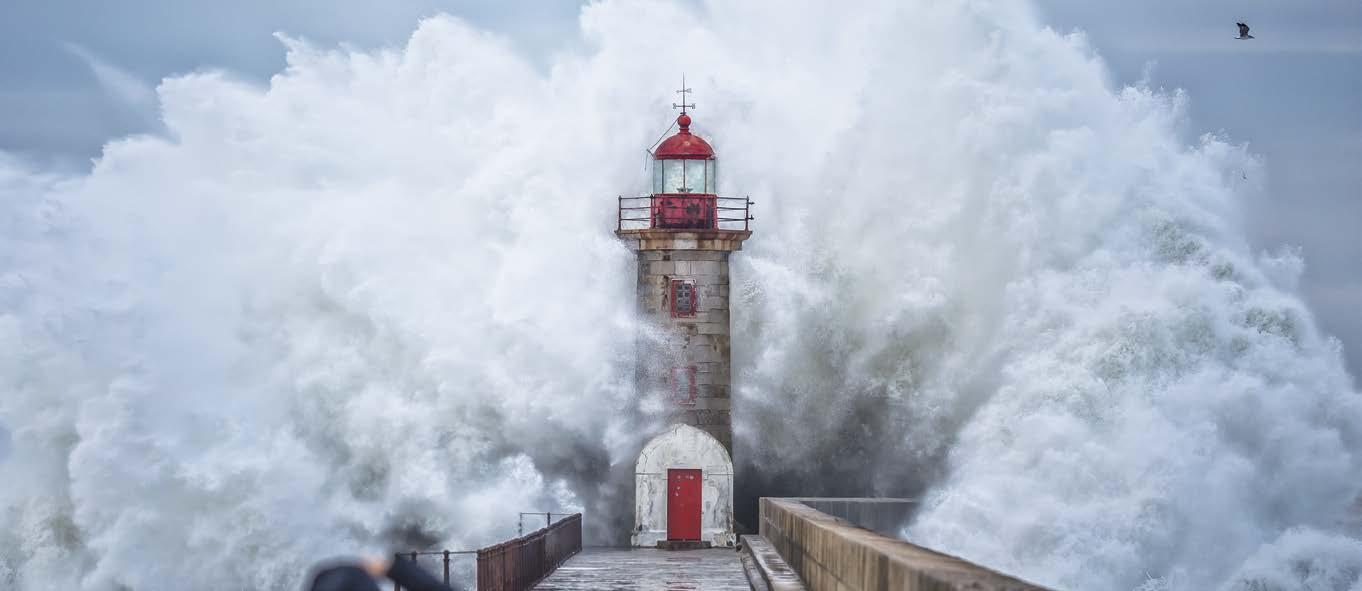
11 minute read
INNOVATIONS:PRESENT&FUTURE
Axalta Coating Systems Introduces a New Series of Anticorrosion Solutions for Every Possible Requirement
Edited by ipcm®
Sustainability, cost, life cycle, and material efficiency – these are all issues our industry must face now to be future-ready. Whitin the sustainability issue, the fight against corrosion plays a fundamental role because it affects the durability of assets: this means costs for maintenance or premature replacement of the asset. According to the WCO (World Corrosion Organization), corrosion accounts for 3.4% of global gross domestic product. Axalta Coating Systems anticorrosion technologies portfolio has been recently updated with a bunch of new anticorrosion solutions for every possible requirement.
Corrosion is an electrochemical process that consists of cathodic and anodic reactions produced by electrons and ionic diffusion. A proper and accurate surface pre-treatment and applying a first-rate, optimised anti-corrosion system extends the life of coated surfaces. Axalta’s coating technologies inhibit at least one of these reactions. The cathodic reaction is halted or reduced because the coating acts as a barrier; it markedly reduces the diffusion of the elements involved in the corrosion process (H2O, O2). At the same time, Axalta coating technologies maintain strong adhesion and prevention migration, inhibiting anodic reaction. Consequently, no electrochemical action or electrons are generated. Efficient corrosion protection is intrinsically linked to four main factors: • the specific environment and type of corrosion your project will encounter; • the metallic substrate in scope; • the surface pre-treatment used; • the coating product selected. With a comprehensive thermoplastic, thermosetting and electrocoating technologies portfolio to choose from, Axalta is well equipped to match your project to the best coating. These technologies empower you to combat the maximum range of corrosion challenges in every climate.
The importance to identify the substrate
Where powder coating is concerned, substrates are divided into degassing substrates and non-degassing substrates. Substrate identification is crucial and depends on the substrate’s nature or design. And often, both need to be carefully considered in advance.
Non-degassing substrates: • Steel with low carbon content • Alloyed steel • Zinc electroplating • Sendzimir • Aluminium
Substrates prone to outgassing: • Cast Iron • Hot dip galvanised steel • Zn or ZnAl metallised steel.
During the curing process, substrates prone to degassing may cause surface defects. For that reason, adapted coating is required to counteract the effect of these substrates. Another critical element to consider is sharp edges. These tend to be particularly vulnerable to corrosion and require custom coating to prevent degradation. Standard surface treatment and coating does not suffice.
Axalta Technologies: Thermoplastic - Thermosetting - Liquid
Axalta’s innovative technological approach and solid resources give it a competitive corrosion protection edge. It stands out for its powder coating treatments uniquely produced with thermoplastic, thermosetting and electrocoat technologies. These technologies provide the customer’s project with the best corrosion protection solution based on its unique circumstances. Thermoplastic and thermosetting applications are powder coatings with distinct properties that derive from the chemical and physical performance of the material while Axalta’s high-performance electrocoats are designed to provide reliable mechanical strength and superior corrosion protection. Every product is also water-based, making them environmentally friendly and more sustainable. At the same time, they’ve been formulated to ensure superior performance across a wide variety of substrates, including hot-rolled steel, cold-rolled steel galvanised steel, aluminium, and magnesium. Axalta also supplies a diverse mix of e-coat formulations, including leadfree and tin-free products, low VOC and HAPS-free systems, as well as formulations with unique benefits such as improved edge protection, lowtemperature bake capability, and improved throwing power. Last April Axalta kicked off a European roadshow to announce new additions to its all-in-one anticorrosion portfolio. The first leg of this European roadshow at the Parc Olympique Lyonnais in the French city of Lyon, where a select group of customers, journalists and industry stakeholders were given a sneak preview of the latest ground-breaking additions to the Axalta range of anticorrosion solutions. These include: • Alesta® ZeroZinc Uniprime – a universal primer that enables the use of a single primer for any substrate; • Abcite® 2060 - a single-layer anticorrosion solution that can be applied with flame spray technology; • AquaEC™ 3500 EP- the latest generation of cathodic tin-free electrodeposition coatings which offers superior corrosion protection performance for sharp edges; • Plascoat® PPA 742 primer - a single layer thermoplastic that can be used as primer and is specifically designed to be overcoated with Alesta® topcoat. These latest product arrivals build on the success of its existing anticorrosion product portfolio, which comprises a full suite of solutions across its Abcite®, Plascoat®, Alesta® ZeroZinc, and AquaEC™ ranges, to accommodate an increasingly specific variety of anticorrosion requirements. Pascal Nicard, Senior Global Technology Manager at Axalta, commented: “This announcement is a pivotal moment within the anticorrosion industry. We recognise that customer needs are continuously changing and have developed an environmentally friendly all-in-one anticorrosion offer that can accommodate the requirements of any project, no matter how harsh the environment. Drawing on 150 years of expertise within industrial coatings and insights from our global customer base, we are the only business that can provide the full range of protection through our portfolio of thermoplastic, thermosetting and liquid anticorrosion solutions, which offer full compliance from an international regulatory standpoint.” Those in attendance were introduced to Axalta’s full suite of digital tools and educational resources aimed at providing the clearest and simplest route to optimal surface coating results. By providing customers with the full range of information on the technical aspects of Axalta’s product range, Axalta is making the process of identifying and implementing the best possible solutions as streamlined as possible. Pascal Nicard continued: “Our goal is to partner with our customers throughout the entirety of their anticorrosion journey, helping them to navigate their way to exceptional surface coating by equipping them with the tools and knowledge they need to succeed. We believe in making this journey as straightforward as possible and are committed to supporting customers through a combination of educational materials, training programmes, and dedicated technical support. In doing so, we empower them to apply products in a way that maximises productivity, efficiency, and quality. The event also highlighted the importance of sustainability within the context of anticorrosion. An increased focus on the environment has played a significant role in the design of this latest range of anticorrosion solutions, all of which are ISO 12944-6/9 accredited and provide exceptional performance and aesthetics without the use of solvent materials”. Pascal Nicard concluded: “The importance of meeting the sustainability requirements of the market cannot be overstated and we believe our solutions can play an integral part in the preservation of the planet and its resources by extending the life of surfaces in a range of demanding
environments. Providing greater levels of surface protection is more costeffective and efficient for our customers in the long term, eliminating the costly requirement for materials to be replaced. Effective anticorrosion coatings must not come at the expense of the environment, which is why our solutions offer full compliance with environmental regulations across the globe, giving customers peace of mind from both a performance and environmental compliance perspective.” Let’s have a deeper look into Axalta’s new additions to its all-in-one anticorrosion portfolio.
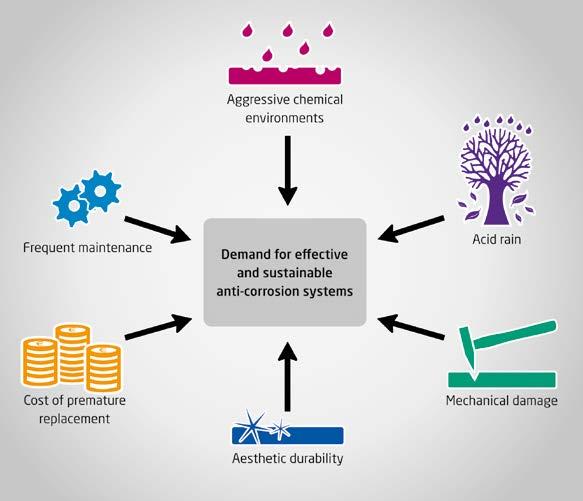
Abcite® 2060
The Flame Spray Technology is the only system which can apply powders on site and with no need for a coating line. It involves depositing semimolten polymer particles onto a heated surface, a process whereby heat causes the particles to flow and fuse into a complete cohesive polymer coating. Abcite® 2060 has been specially designed for this coating technology, combining the exceptional anticorrosion and mechanical performance of Abcite® with the simplicity of use and mobility of the Flame Spray Coating technology. By using Abcite® 2060, the end-user will be able to protect large metal structures on site, in most weather conditions and easily repair unplanned damage without dismantling the structure. Abcite® 2060 possesses exceptional anticorrosion performance: this 1-layer system is certified CX for extreme corrosive environments in accordance with the ISO 12944-6/-9 standard for galvanized and gritblasted steel.
Applications • Corrosion protection in highly corrosive marine, agricultural and industrial environments; • Pipes, bridges, metal structures, water-proofing, offshore installations.
Typical coating thickness: 400μm-3000 μm
Key features and benefits • Application in situ with no need for a coating line • Specially designed for large structures • Outstanding corrosion protection and best in class for salt • Excellent resistance to alkaline and acid chemical attacks • Impermeable barrier, even in case of permanent immersion or condensation • Performance unchanged by UV exposure and weathering • Service temperature from -60°C to 75°C • Tough and flexible for high impact and abrasion resistance • No primer, self-adhering mono layer • Excellent edge and corner coverage BPA, VOC and halogen free.
© Axalta
AquaEC™ 3500 EP
AquaEC™ 3500 EP is the latest generation of cathodic tin-free electrodeposition coatings from Axalta. This new product shows superior corrosion protection performance at sharp edges. Customers benefit from a highly efficient system due to a low dry film density. On top, the modular mixing concept allows to customize the optimum cost solution whilst maintaining the performance. The product does not contain organic tin compounds and is compliant with REACh regulations. The new e-coat technology offers an energy saving potential due to its full cure even at a baking temperature of 150°C and has excellent chemical and corrosion resistance in combination with very good mechanical properties and adhesion on various substrates. Manufacturers in many sectors are looking for solutions that will improve performance and meet increasingly complex market demands that reflect different substrates, parts designs, and pre-treatment options. The technology behind the new AquaEC™ 3500 EP is specifically formulated to meet those requirements.
Market segments • Automotive parts and accessories • Agriculture and construction equipment • General industry • Industrial job coaters.
Key features and benefits • Excellent edge corrosion protection • Free of tin and toxic heavy metals • Low curing temperature • Robust operation window
© Axalta
• Superior corrosion protection performance • Stable UF flux rate • REACh and Haps compliant.
Plascoat® PPA 742 primer
Plascoat® PPA 742 is a single layer thermoplastic that can be used as primer and is specifically designed to be overcoated with Alesta® topcoat. Even for parts with strong differential of thermal mass or with sharp edges Plascoat® PPA 742 will bring optimal protection.
Key features and benefits • Improved edge covering • Excellent compatibility with Alesta® topcoat • Excellent intercoat adhesion • Strong stability during curing of Alesta® • Good impact and sand abrasion resistance • Excellent adhesion to metallic substrate • Will not crack, chip, flake or fracture.
Applications • Urban furniture, fencing, construction, lamposts, metallic structures • Metal parts with strong differential of thermal mass • Recommended Coating Thickness: 170-300μm • Appearance Smooth/Glossy – Gloss: 60.

Primer Alesta® ZeroZinc Uniprime: the universal primer - entirely safe
Products from the Alesta® ZeroZinc range are formulated in accordance with the High-Density Crosslinking (HDC) technology and provide a solution tailored to every substrate, including degassing metals, and for demanding shapes: expanded metal, perforated sheet steel, sharp edges. Alesta® ZeroZinc Uniprime is THE multi-function primer: it meets the most stringent anti-corrosion requirements, regardless of the shape and type of the part. It covers the areas that are most difficult to reach. Owing to its versatility, Alesta® ZeroZinc Uniprime enables the use of a single primer, whatever the nature of the substrate (black steel, galvanised steel, metallised steel, aluminium, etc.) offering ease of application, better stock control and increased productivity. Owing to these properties, Alesta® ZeroZinc Uniprime is the first-choice primer which meets the construction (e.g. metal structures, exterior claddings, wrought iron), transport (e.g. chassis, systems), industrial machinery, agricultural equipment and all those industries which demand high quality, anti-corrosion protection, with all the advantages of a powder paint. Alesta® ZeroZinc Uniprime, formulated from epoxy resin, is Qualisteelcoat approved and has been designed to meet the following criteria: • Stability and robustness in application (application and oven-baking) • Coating areas that are hard to reach • Excellent anti-corrosion performance (to the ISO 12944-6 standard) • Degassing performance.
Digital Tools to help the customer choose the perfect solution
Axalta has come up with a range of digital tools and resources to keep the customers informed of the latest developments in coating technologies and products. That way, end-users can have rapid access to anticorrosion-related information that’s always accurate and up to date.
Website The website www.axalta.com/anticorrosion provides the customer with the latest, accurate information about anti-corrosion facts, tips, advice, products and services. Even better, the website is constantly updated. That means that the end-user can stay on top of the latest anti-corrosion technology solutions and learn about the latest colours and trends.
Product Selector The user can select and configure its project’s criteria, and Axalta product selector will match it to the system that offers the best corrosion protection. The tool provides detailed specifications and product information so that the customer can make its decision fully informed of every product’s pros and cons.
Videos Axalta website features a library of technical videos, including some about powder coating products undergoing various lab tests. That provides the customer with the visual proof it needs to choose a product. ‹