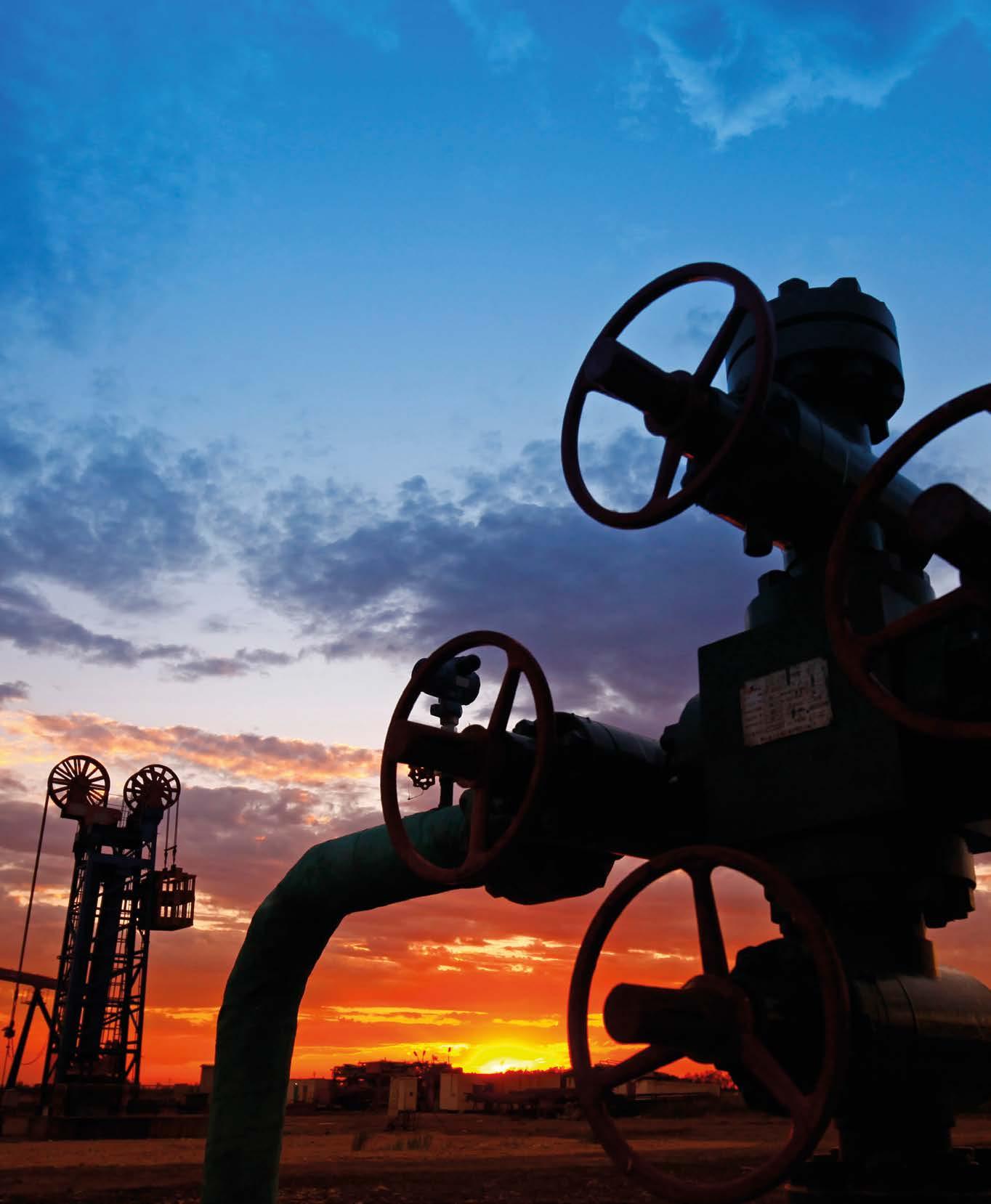
10 minute read
ANALYSIS
Valve Manufacturing: Qualification Requirements for Shop-Applied Internal FBE Coatings
Meshari S. Al-Otaibi, Hassan S. Al-Sagour and Talmiz Ur Rehman
Saudi Aramco, Dhahran – Saudi Arabia
In this paper, a group of valve manufacturers in Italy was surveyed to evaluate the root causes behind coating failures in valves with an internal FBE coating. Subsequently, the requirements of qualifying internal coatings for valves were evaluated by the end-user’s representative in Europe. The survey included 15 valve manufacturers and covered a period of 10 years, and the survey was either physical or online. The result of the survey was not expected as it revealed that none of the approved valve manufacturers had the capability to perform such a critical process in house. In all cases, the coating application was outsourced to specialized coating applicators located mainly in Milan, Italy. Furthermore, the questionnaire revealed that more than 60% of the coating applicators exhibited gaps in the process of compliance with the international standard requirements. Based on the survey, recommendations were given to improve quality control during the application of coating to valves.
Fusion Bonded Epoxy (FBE) coating is a thermosetting material that achieves a high bond to metal surfaces as a result of a heat generated chemical reaction. FBE coatings are used for optimum corrosion protection of metals in severe corrosive environments, including saltwater, wastewater, petrochemicals, solvents and corrosive gases. Many valve manufacturers use FBE coating as a special process for corrosion protection, especially on the wetted parts of the valves and fittings for service such as potable water, saline water, sweet and sour crude, liquid and gas etc. FBE Coatings are foreseen applicable on a range of valves such as ball, butterfly, gate, globe, check and plug-valves etc. as per relevant industrial standards.
End-user’s specifications and purchase orders have clearly mandated manufacturer responsibility for full compliance with the requirements of internal FBE coatings through maintaining adequate quality assurance and quality control processes to guarantee 100% defect-free products. In the latest revision of relative standards, the requirement mandating approval of coating procedures by the customers’ central engineering organization had been removed to improve the logistics. Consequently, this revision had transferred the full responsibility of correct selection and application of the FBE coating to valve manufacturers, assuming they have the right knowledge, technical understanding and ability to apply protective coating in accordance with end-user’s coating specifications.
Study objective & methodology
The objective of this study was to identify the main root causes of FBE coating failures during the manufacturing phase, receiving inspection or site acceptance test (SAT). Identifying root causes will lead to improving the current end-user’s mandatory requirements and enhancing the control of the internal FBE coating processes. In this study, the team collected and analysed data of reported cases of internal FBE coating failures, which were observed during the manufacturing phase and receiving inspection at project sites. Several Non-Compliance Reports (NCRs) and Equipment Deficiency Reports (EDRs) were issued by inspection teams of capital projects in the last 10 years related to this issue. The investigation highlighted in the EDRs revealed that there were several gaps in interpretation of the customer’s specifications between the manufacturer and their sub-suppliers, which led to such failures.
Data analysis
The data analysis indicated in Figure 1 illustrates the valve defect types with respect to the affected quantities reported during inspection at the site since 2007. The coating defects represent the third largest quantity in terms of overall detected defects on received valves. The internal FBE coating failure during the inspection at manufacturing phase and receiving inspection (including site acceptance tests) is one of the major issues in terms of valve failures. These details will be further elaborated in the following sections of this study.
© Saudi Aramco
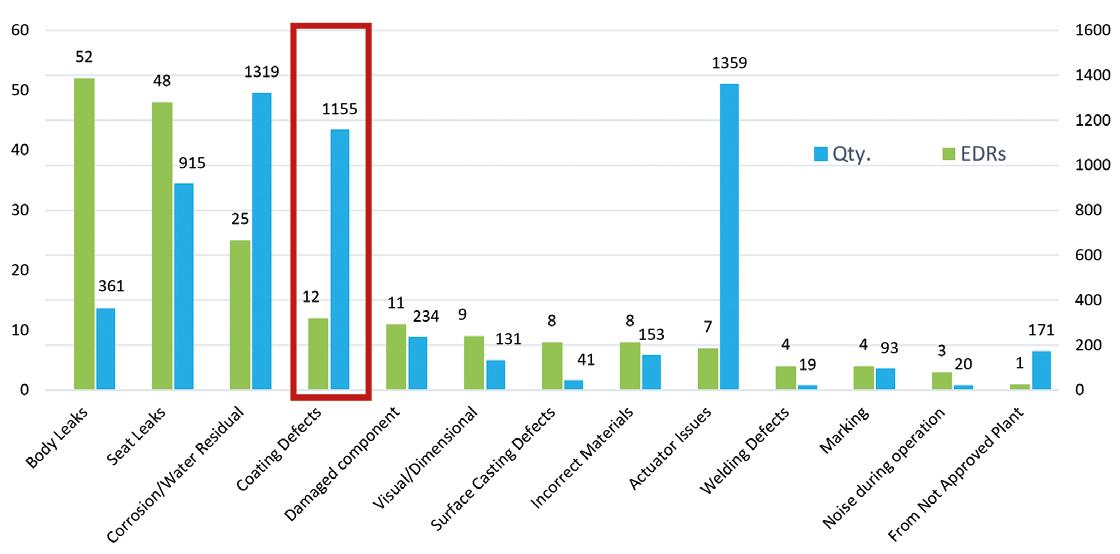
Figure 1 - Distribution of valve defect types and affected quantities.
© Saudi Aramco © Saudi Aramco
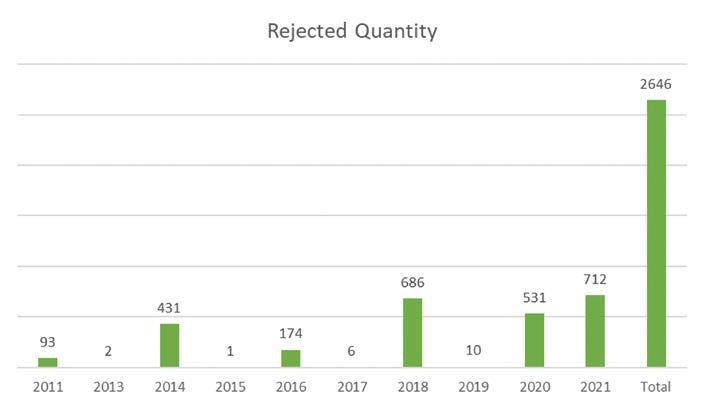
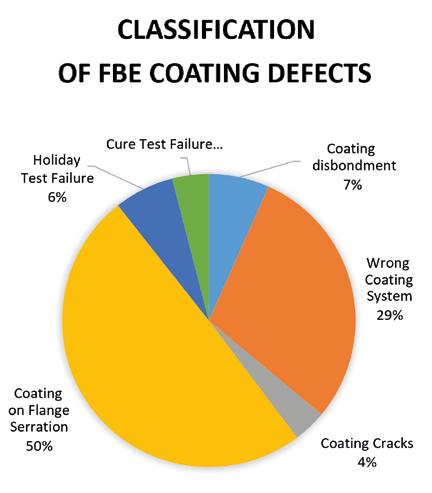
Figure 2 - Statistics of rejected quantity (EDR + NCR). Figure 3 - Classification of FBE coating defects.
Figure 2 shows the rejected quantity needed to split all those defects in different types based on their associated root causes. The rejected quantities are cumulative of EDRs and NCRs during the manufacturing phases. A total of 1407 valves were reported as defective and trend along the years shows that huge quantity of defects was encountered in the past 10 years.
Breaking down the relevant defects identified within the EDRs and NCRs, as per Figure 3 coating defects on flange serrations represents 50% of the total reported issues while wrong coating system applied represents 29%. As illustrated in Figure 4, end-user’s Inspection team performed further investigation to figure out root causes behind the aforementioned defects. The investigation on RCA reveals that 79% of the reported issues are due to lack of awareness and lack of interpretation of the requirements stipulated in the applicable international standards and customer’s specifications. The second largest cause is the manufacturer’s lack of control on the outsourcing as well as poor quality control coverage by the coating sub-supplier as required by the end-user’s standards.
Gap analysis
The results of the distributed questionnaire shown in Figure 5 reveals that 39% of the manufacturer are able to comply fully with standard requirements. Another 39% of the manufacturers exhibited minor gaps with respect to the standard requirements and 22% of the manufacturers represented major gaps with respect to compliance with standard requirements. In total, 61%, of the manufacturers were identified with minor and major gaps with reference to the standards requirements.
Major Gaps • Poor control on the painting supplier • Lack of review and approval of quality documents of coating subsupplier • Poor control on the process parameters • Lack of qualification of the coating procedures by valve manufacturers by type, size and class • Lack of validation of cure testing.
Minor Gaps • Unavailability of manufacturers direct NACE qualified personnel • Lack of manufacturer’s QC coverage during interim coating application strategies • No distribution of up-to-date quality requirements to the coating applicators by valve manufacturers • Lack of involvement and implementation of repair procedures by the coating sub-supplier in case of damage during machining • Unclear responsibility in case of customer claim.
© Saudi Aramco © Saudi Aramco
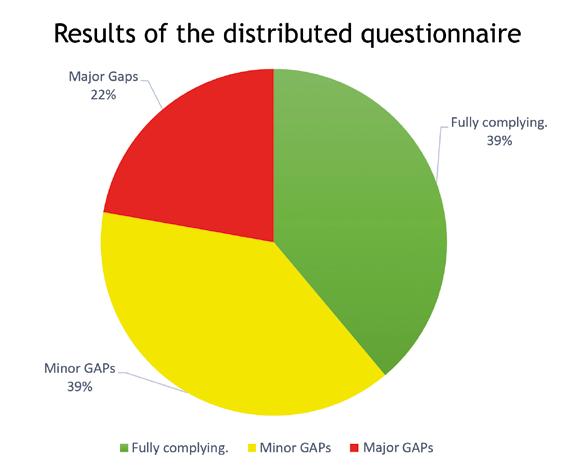
Figure 4 - Classification of FBE coating defects based on RCA.

Through analysing the results of the distributed questionnaire, several gaps were clearly identified, which can be summarized in the Table 1 in the next page.
Case study
To further build upon the findings from past NCRs and to understand the root causes of failures related to internal FBE coating in valves, one of the NCRs related to the wrong interpretation of the customer’s specifications is described as a case study below: • Valve details: CL 600, WCB Material (CS), Ball valve - Quantity: 686 Investigation details: the Inspection team conducted a focus assessment and discovered the FBE coating for 600 valves was not aligned with a standard clause prohibiting FBE coating covering on flanges. All the raised face flanges, with exception of few millimetres, were coated despite the requirements. • Root cause: lack of awareness of the applicable standard requirement (5.2.10: The internal coating shall be extended up to the face of flat- and raised-face flanges that will not be in contact with the gasket. The coating applied shall be machined and ground to ensure that the surface is levelled properly and to avoid misalignment of gasket. Only approved coatings that can be machined after application shall be used). Such defects represent 50% of reported defect types and 79% of major root causes, as indicated in Fig. 3 and 4 in this study. Recommendations: • Define requirements to qualify valve FBE coating suppliers and reconsider the need for central engineering to review and approve coating procedures. • Manufacturers to maintain a list of qualified coating sub-suppliers and evidence of proper control at their shops. • Adopt the checklist developed by the end-user as best practice and use it during the assessment of coating suppliers. • Require valve manufacturers to validate applicable coating procedures based on service and relevant design parameters in addition to qualification procedures. • Introduce more approved products suitable for machining. • Valve manufacturers to clearly indicate the areas to be machined after FBE coating application, and inspection point to be incorporated in the relevant inspection forms and manufacturer’s Inspection & Test Plan (ITP). • DFT thickness range to be specified in coating standards before and after machining and the same to be reflected in relevant inspection forms. • Coating standards to clearly specify the circumference of the area to be excavated and repaired in case of holiday is detected. • It is recommended to specify the use of Garnet for cast steel valves/ material and metallic abrasive for forged steel valves/material. All pieces that required FBE coating are Carbon Steel (CS) material, so
Figure 5 - Results of the distributed questionnaire.
using metallic abrasive for forged for blasting activities and garnet for cast components is a more efficient way to have a better anchor profile. • Revise the relevant inspection form to incorporate witness point for holiday check & Final DFT after machining at valve manufacturer’s premises before final assembly.
Conclusion
In view of the above-mentioned synopsis, we concluded and highly recommended to continue the review and approval process for performing Internal FBE coating procedures from the coating suppliers by the end user’s central engineering. ‹
Acknowledgment The authors would like to thank referees for helpful data without implication for any remaining errors. References - Equipment Deficiency Log, AOC-H-QAU - Saudi Aramco specs. (09-SAMSS-091, SAES-H-001, H-002&002V, IR091300, etc.) & relevant International Standards. - Vendor Questionnaire (Internal FBE Painting suppliers): Contributed by various SA-approved valve manufacturers in Italy. - Deficiency and Benchmarking Study, Rev. 4. By Nicola Cevoli (QMDAOC-H-QMU-Supervisor), Meshari Al-Otaibi (QMD-AOC-Italy-Inspection Representative), Abdul Aziz Zahrani (SAO-VID). - FBE coating MAPS on various types of Valves: Courtesy Of various SAapproved valve manufacturers in Italy.
No.
Table 1 - Summarized results of the distributed questionnaire.
GAP LIST
1. Inconsistent approach among vendors to qualify and manage sub-supplier activities.
2. No clear criteria adopted by the valve manufacturers to ensure that the outsourced coating activities are fully controlled.
3. No proper coating selection criteria although clearly specified by customer’s standards.
4.
5.
6.
7.
8.
Missing validations for special sub-processes as machining, verification steps such as holiday tests, repairs in case of pin holes detected, repair products to be used, testing and Dry Film Thickness (DFT) measurements to be performed after final machining by the valve manufacturer. Coating qualification procedures are not adopted by the valve manufacturers although mandated by end-user’s Standards mandatory requirements Not all approved products by the customer were suitable for machining. Generally, in all types of the valves, machining of certain internal areas is required especially on the FBE-WO interface: however, some products do not guarantee the integrity of the coating after machining. No proper control neither by the valve manufacturers nor the coating applicator during interim stages, such as: a) Surface preparation, preheating (baking temperature validation based on the base material) after primer application. b) Powder-based final coats application (only one-time application to achieve desired coating thickness DFT value). c) Methods to apply liquid-based repair coatings in case of low thickness or holidays detection. d) Any machining required in case of over thickness applied. e) Validation of Cure Test and identification of samples per batch by DSC calorimetry (typical duration for the cure test results is 10 days in case of non-availability of DSC scanner). For the coating applicator, to have a DSC scanner should be mandated.
The latest editions of the customer’s standards do not require any more approval of coating procedures but the inspection forms still mandate the approval of FBE coating procedure.