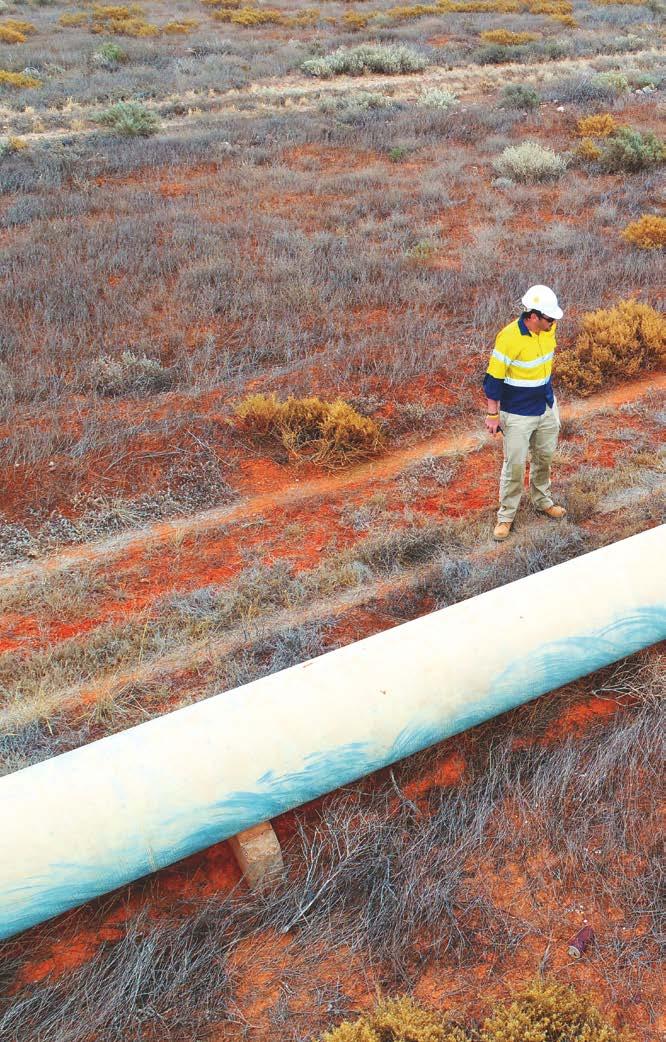
7 minute read
INSPECTION LOGBOOK
Coating Inspections: Inspection of Steel Surface Preparation, Part 7
Massimo Cornago
NACE International Certified Coating Inspector, NACE CIP PEER Reviewer
cornago@ipcm.it
Our series of articles about the inspection of surface preparation operations on steel and the tests this requires continues with the presentation of other tests related to surface contamination after the surface preparation phase itself. In this article, we will deal with soluble test contamination, grease and oil contamination, and dust. Again, in these cases, the international standards normally used are NACE, SSPC, ISO, ASTM, and so on.
After surface preparation, the Inspector may be required to check that surfaces are free of soluble salt contamination. This test is normally performed after steel has been prepared by blast cleaning. However, if a long interval occurs between the application of two coating layers (i.e. full top coating of a shop-applied primer), it may be advisable to check for contaminants on the existing layer to be overcoated. Contamination of otherwise visually clean steel surfaces can have very serious effects on the coatings applied over them. These adverse effects include as follows: • Osmotic blistering of coatings. • Acceleration of corrosion. • Interference with the action of chemical corrosion inhibitors, such as chromates (particularly with chloride contamination).
There are numerous sources of soluble salt contamination, including the following ones: • Atmospheric contamination from ocean spray, combustion of fuel (sulphates), and chemical processes. • Exposition to and direct contact with seawater. • De-icing salts on highways and bridges, especially in the winter season. • Contaminated abrasive.
Chlorides and sulphates being the most common soluble salt contaminants, their effects on coating performance depend on as follows: • Service environment. • Nature and amount of contamination. • Generic type and design of the coating system. • Coating thickness.
The international standard NACE5/SSPC-SP12 defines three levels of soluble salt contamination as follows: 1. Condition SC-1: An SC-1 surface shall be free of all detectable levels of contaminants as determined using available field test equipment with sensitivity approximating laboratory test equipment. For purposes of this standard, contaminants are water-soluble chlorides, iron-soluble salts, and sulphates. 2. Condition SC-2: An SC-2 surface shall have less than 7 µg/cm2 chloride contaminants, less than 10 µg/cm2 of soluble ferrous ion levels, and less than 17 µg/cm2 of sulphate contaminants, as verified by field or laboratory analysis using reliable, reproducible test equipment. 3. Condition SC-3: An SC-3 surface shall have less than 50 µg/cm2
© Adobe Stock

chloride and sulphate contaminants as verified by field or laboratory analysis using reliable, reproducible test equipment.
The standard SSPC91-07 titled “Effect of Surface Contaminants on Coating Life” describes several extraction procedures, such as the swabbing method and the Bresle method. In fact, possible extraction methods include as follows: • Limpet (Soltz) cell: it consists of a machined plexiglass cell plate with four adjustable magnets to hold the cell onto a steel surface, and a rubber seal to retain the aqueous extracts. A syringe is used to pump extraction water in and out of the cell into a sample container. The cell contains a built-in conductivity meter. • Swabbing techniques: this extraction operation is conducted using a measured amount of distilled water (from a graduate cylinder), cotton swabs, gloves (to prevent contamination by hand perspiration), and a collection container. The extraction process is not very efficient, as only half of a contaminant may be recovered. • Bresle cell (ISO 8502-6): it is a small adhesive patch (latex rubber cell) that forms a pocket when attached to a steel surface (vertical or horizontal). A syringe is used to apply water onto the surface to be tested for about 15 seconds and transfer the extract into a sample container (vial). The aim is to determine its chloride ion concentration, ferrous ion concentration, or pH soluble salt concentration by different methods: titration test strips for chloride ions, test strips for ferrous ions, field titration for chloride ions (ISO 8502-2), testing for sulphates, and a conductivity meter for soluble salts (ISO 8502-9).
Grease and oil contamination
After surface preparation, the Inspector may also be required to check that the surface is free of grease and oil contamination as specified. Indeed, visually clean coated or uncoated surfaces may be contaminated with a thin film of grease, oil, or other water insoluble materials. Unless detected and removed before coating, such contamination may reduce coating adhesion. The most common sources of grease and oil contamination in painting operations are natural oils from the hands of workers and from lubricants used in compressors or power tools used in mechanical cleaning. The more common testing methods are the following ones:
1. Detecting non-visible grease or oil with the water break test: it is used to detect films of grease, oil, or other water-insoluble contaminants on coated or uncoated surfaces that visually appear to be clean. This test visually distinguishes differences in water-spreading characteristics (surface energy) between clean and contaminated surfaces. It is conducted as follows: • Spray a mist of atomised distilled water on the surface to be tested and observe what happens. • If the water gathers in lenses that last about 25 seconds before flowing out, the surface is clean. • If the water gathers into droplets (forming a “water break”) within 25 seconds, the surface is likely contaminated with grease, oil, or other water-insoluble materials.
2. Detecting non-visible grease or oil with ultraviolet (black) light: it is used to detect grease or oil contamination as required in specifications. However, observations are subject to different interpretations. This test is more commonly done on cleaned surfaces; occasionally, however, it is employed prior to cleaning, when solvent cleaning to remove grease or oil is required before washing in the surface preparation specifications. This procedure is most commonly employed on crude oil tanks. Because these products absorb UV light and then emit this energy as visible light, some synthetic oils do not exhibit fluorescence. A shield (black cloth) must be used during daylight
hours; however, lint on the cloth may produce a slight fluorescence, so care must be taken not to confuse it with fluorescence from contaminated surfaces. The test is conducted as follows: • Shine a UV lamp onto the surface and observe what happens. • “Bright yellow” or “lime green” fluorescence indicates contamination by grease and oil. • Absence of fluorescence indicates that the surface is not contaminated by grease and oil.
Dust
Any dust particles collected on cleaned surfaces can interfere with coating adhesion. The Inspector should therefore verify that the prepared surfaces are free of dust. Abrasive blasting and other sources at the jobsite can leave dust on a cleaned surface. Several simple tests are available for detecting dust on a steel surface. These involve wiping the surface with a clean rag or contacting the surface with the sticky side of clear tape. The rag or tape is then visually examined for particles. If dust is detected on a prepared surface, the Inspector should check that it is removed before coating application is allowed to start. Dust should be removed by vacuuming, if possible. It may also be removed by blow-off with compressor air; however, care must be taken to ensure that the air is clean and dry, using the blotter test method.
1. Detecting dust using the pressure sensitive tape method (ISO 8502-3): The method consists in pressing a clear adhesive cellophane tape onto the surface, removing it, and searching for any dust particles. The tape is examined by placing it on a display board of a contrasting colour and comparing it to pictorial references. The test is conducted as follows: • Press a piece of clear adhesive cellophane tape against the cleaned surface leaving one end up for easy removal of the tape, taking care not to contaminate the surface with oil from fingers. • Remove the cellophane tape using the exposed end and visually compare it to pictorial references.
2. Detecting dust using the clean cloth method: The presence of dust on a steel surface already prepared for coating can be detected by rubbing it with a clean cloth. However, this method is less precise than the pressure sensitive tape one and it may deposit lint on the surface. Moreover, the amount of particles on the cloth must be subjectively evaluated. It is very impractical to expect a surface to pass a white glove test. In determining the presence of excessive dust, it is more practical to examine the surface for streaks or marks left by the cloth. The test is conducted as follows: • Wrap a clean cloth around the index fingertip and make strokes (around 15 cm) across the surface with medium pressure. • Remove the cloth and visually inspect the cloth itself and the surface for any dust.
In conclusion, in order to ensure proper surface preparation, the Inspector should verify that the specified level of surface cleanliness is attained (using visual and/or written standards and jobsite standards), that the specified surface profile is attained, and that the surface contamination degree lies within the range allowed by the specifications. ‹
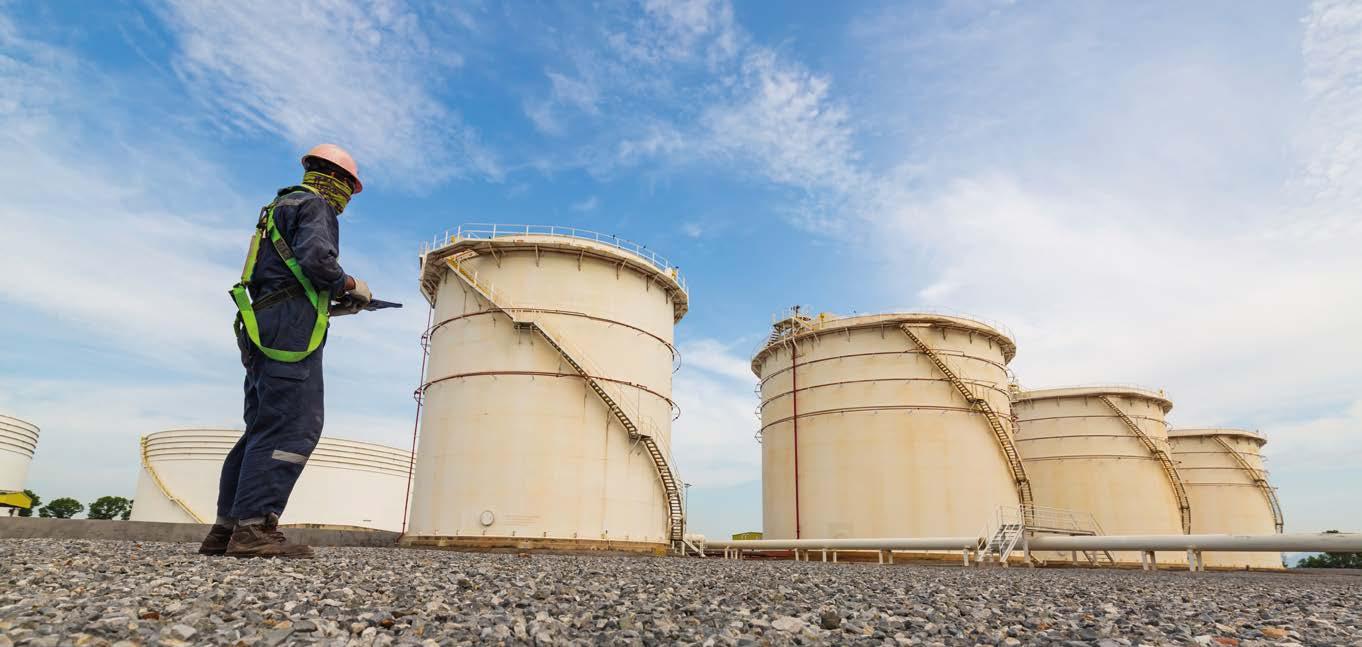