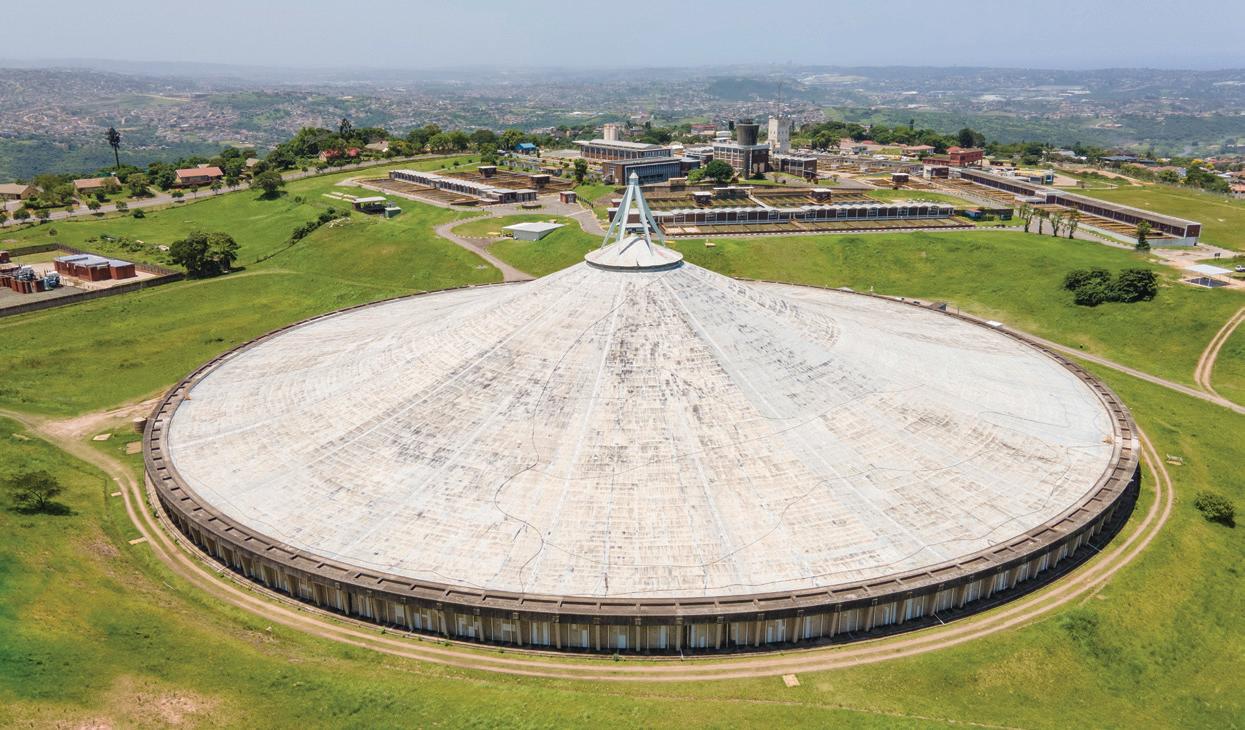
4 minute read
Important fix for Durban reservoir
Important fix for
DURBAN RESERVOIR

Concrete panels forming the roof of a 350ML reservoir in Durban have been repaired and sealed to prevent potentially harmful contaminants from polluting the potable water supply to more than 500 000 people in the region.
Durban Heights Reservoir 3 is situated in the suburb of Reservoir Hills, KwaZuluNatal. Constructed in 1971, it is one of the biggest concrete reservoirs in southern Africa. The reservoir design is unique, as it has a single support in the middle and a roof shaped like a circus tent. The roof is made up of 120 steel post-stressed cables that radiate from the centre roof support to the outer base support.
In 2003, a full diagnostic survey of the concrete roof panels was done. A variety of issues were identified, but of particular interest was the existence of a micro-climate within the reservoir. This micro-climate, with wet-dry cycles, creates a favourable environment for contaminants to be absorbed into the reinforced concrete panels, causing corrosion of the reinforcing.
Operational reservoir
Based on the original diagnostic survey, rehabilitation proposals and the subsequent product trials, a tailored solution from speciality chemical company Sika was evaluated and chosen to perform the repairs. Umgeni Water appointed Royal HaskoningDHV to take on this rehabilitation project as the project engineer and Sika products were specified on the tender. Smart Civils Construction was the specialised civil contractor.
As the work was being done in an operational reservoir, the product choice was paramount to health and safety in ensuring they posed no risk of water contamination. The project’s other challenges were identifying alternative methods of gaining access to the roof structure and shortening the repair time. Smart Civils developed an inventive idea where access to the roof was provided by a design innovation.
This involved erecting 550 tonnes of scaffolding, in a bird-cage configuration, from the floor to just under the soffit. The scaffolding would give the contractor access to one-quarter of the roof at any given time, before being dismantled and re-erected as the works progressed.
Sika solutions
To fulfil the intended task, a decision was made to use SikaTop Armatec-110 EpoCem as the primary rebar protective coating for the concrete repair to protect the reinforcing of steel and inhibit corrosion. Due to the difficult conditions, Sika MonoTop-610 was used as a primer to the concrete substrate. The decision to use Sika MonoTop-412 NFG as a repair mortar was because of its unique properties as an excellent wet spray mortar.
This application method improved the compaction of repair mortar and increased the application rate of the product. Sika MonoTop-412 NFG also differentiates itself as a single-component, polymer-modified, fibre-reinforced, low-shrinkage structural repair mortar with Sika FerroGard-903 Plus corrosion inhibitor. That is a threein-one solution which delays the start of corrosion and reduces the corrosion rate when it occurs. It also increases the service
(Left and right): Rehabilitation of the 350ML Durban Heights Reservoir 3.
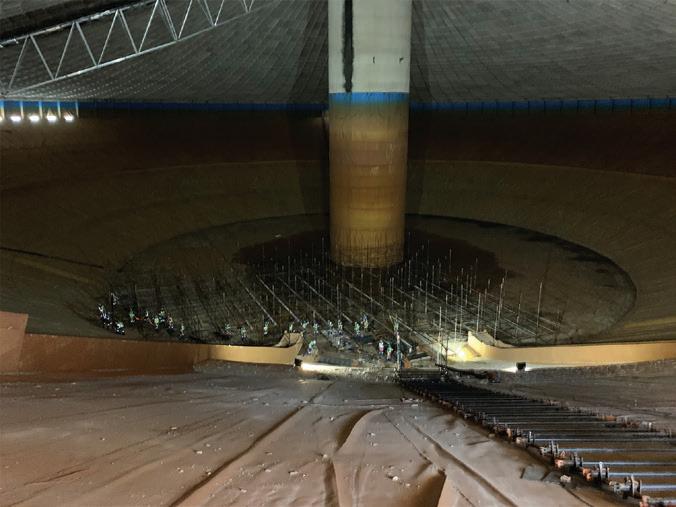

life of a reinforced concrete structure.
Sika’s carbon fibre fabric impregnated with a structural epoxy resin, SikaWrap-230C, was used due to the age of the structure and minimal concrete cover. Sika Injection-307 was used for refilling the ducts. Sika Injection-307 is a low-viscosity elastic polyacrylic injection resin that can be adjusted to set at a pre-determined time, forming a passivating permanently elastic matrix.
Protective coatings
Two protective coating systems were applied to the panels, namely Sika FerroGard-903 Plus, which is a corrosion inhibitor that penetrates down to rebar level over time and forms a protective monomolecular layer on the surface of the reinforcing steel. The final protective coating in the solution was Sikagard-705 L, a singlecomponent, low-viscosity, solvent-free and reactive impregnation product for concrete and cementitious substrates based on silane. Its unique properties allow moisture vapour to escape from the concrete panels, ensuring they stay dry and thus preventing further ingress of contaminants.
Other Sika systems used on site were Sika Primer-3 N and Sikaflex PRO-3 i-cure, a single-part, moisture-curing elastic joint sealant with high mechanical resistance used to seal the expansion joints of the soffit. Sikadur-43 ZA is a solventfree, three-component repair and filling mortar used to do roof repairs next to the cable ducts.
Smart Civils generated 100 local jobs for the duration of 14 months in the Reservoir Hills community. The use of exceptionally durable and high-performing Sika products in the refurbishment of this reservoir will lessen the future refurbishment cycles, saving on material consumption and time throughout the structure’s lifespan.