JET LIFE
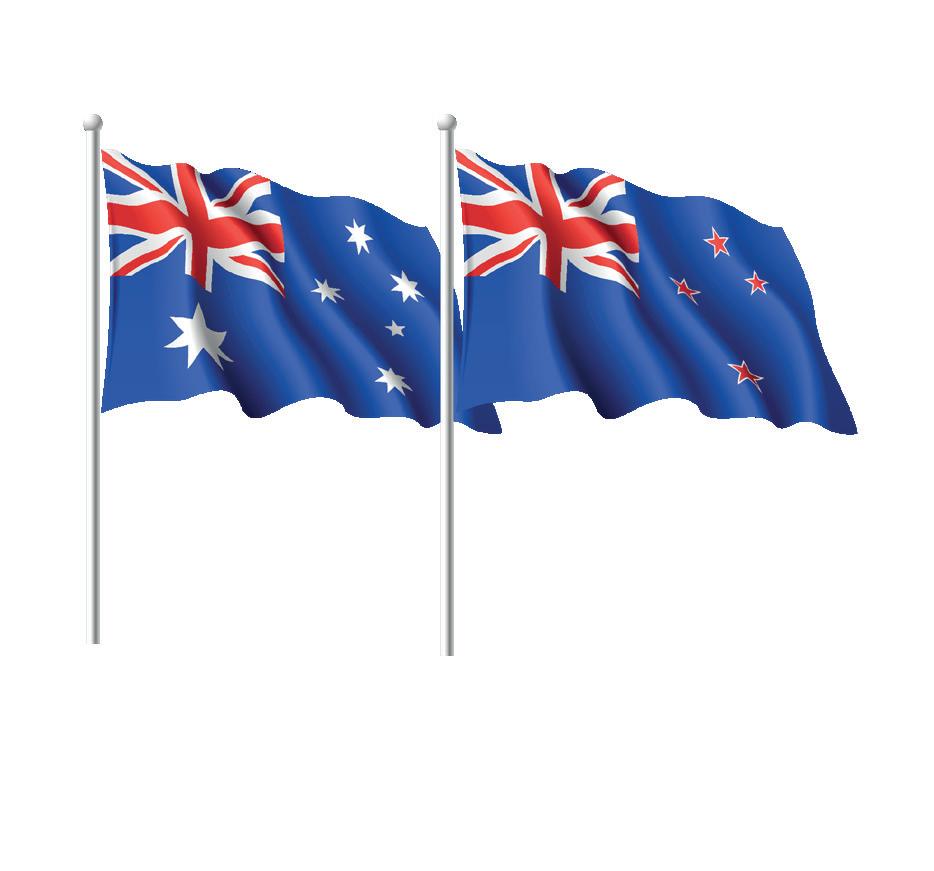
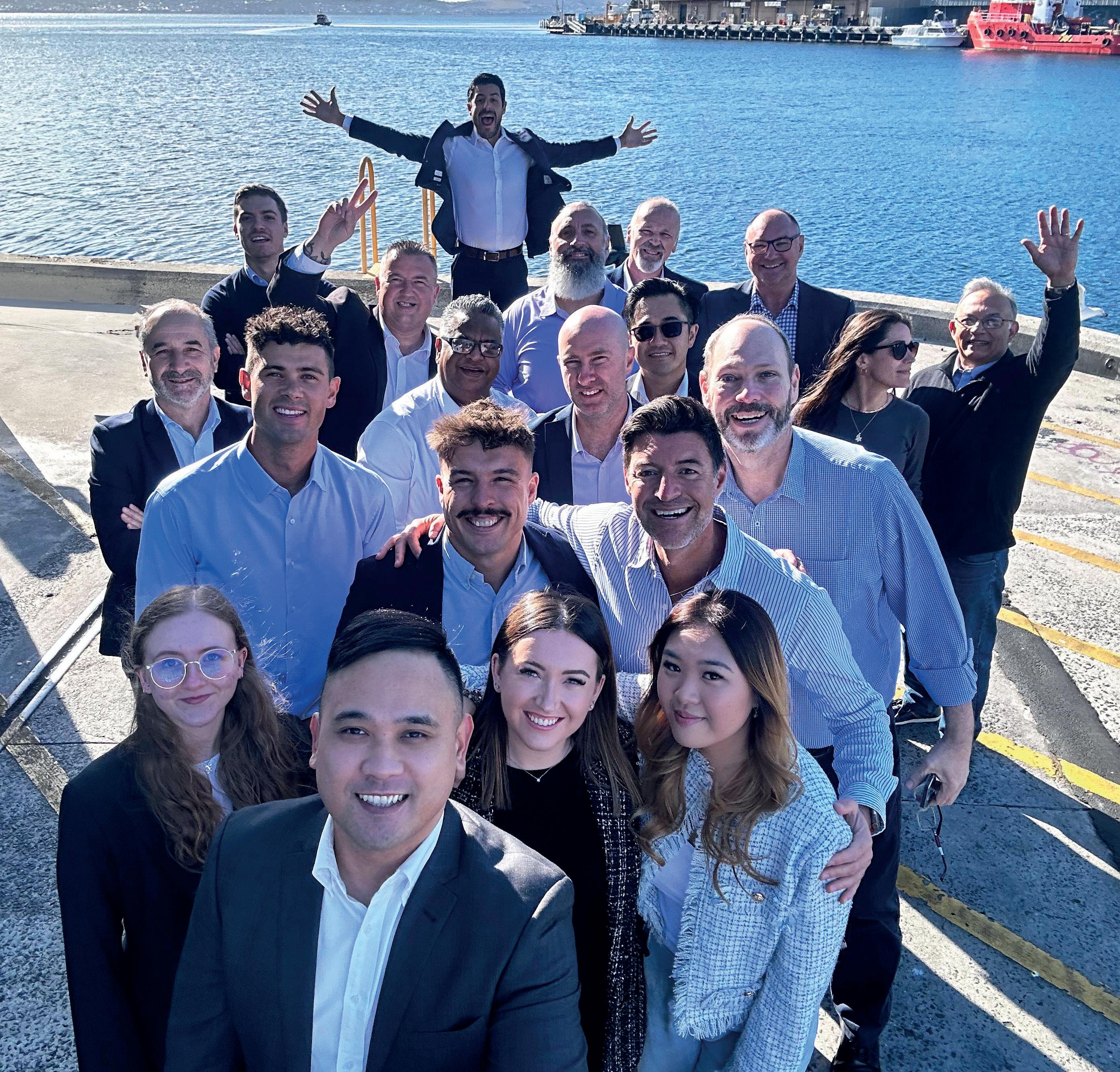
Orders
orders@jet-ap.com
is published by Jet Technologies Pty Ltd
ABN 12 515 939 347
19 Rosebery Ave Rosebery NSW 2018
2024 has hardly begun and yet, there is excitement brewing for the upcoming Drupa exhibition, held in Dusseldorf this year between the 28th of May and 7th of June.
It has been a long 8 years since the last Drupa in 2016 and frankly, the Printing industry has transformed dramatically in those years.
Gone are the days where a printer could rely purely on “heavy metal” analogue printing. “Digital everything” is part of our world these days, from prepress, to workflows and automations and of course the actual print devices themselves.
More importantly, we no longer think about print as “ink on paper” – it has become so much more.
Printers have diversified dramatically to find their unique selling points, with entire print categories growing daily that did not even exist 8-10 years ago.
Energy and the environment have played a significant role in shaping our landscape in recent years too, with the circular economy and printing
in a more sustainable manner now the central theme for many printers and brandowners alike.
Jet Technologies is bursting with excitement about the innovations and developments that we will be able to show clients at the Drupa and bring back to Australia shortly after.
Inkjet continues to be a central theme, with product offerings that cover Labels, Packaging, Publishing, Can Printing and many other areas of print and packaging.
The leaps in conventional print are also exciting to demonstrate, with the AsahiEsko “Crystal Clean Connect” a perfect example of that.
Last but not least, we have now opened up our very own Office & Distribution centre in Brisbane, adding to our Sydney and Melbourne HQ’s to better service our QLD clients.
We look forward to seeing you all in Dusseldorf! Jack Malki
Jet Technologies is delighted to announce the opening of our QLD Distribution Centre in Brisbane.
Located in the strategically located suburb of Crestmead, Jet Technologies is located within 40 minutes of 90% of our client base that operates as far as the Northern suburbs of Brisbane, the western suburbs (approaching Ipswich) and Gold Coast to the South. With more than 2,500 SQM of modern, high-clearance warehouse space, the Distribution Centre has been setup to be able to offer sameday delivery on a wide range of products.
Recognising that the Metropolitan Brisbane/Gold Coast areas have grown substantially, it is our goal to be able to support those clients with the best possible service levels. For many years, we have operated 3PL warehouses and whilst they have been a fantastic stepping stone, there is no substitute for controlling your own Distribution Centre.
Jet Technologies is located at 45-49 Quilton Place, Crestmead.
Jet Technologies is excited to announce a strategic partnership with Actega, enhancing sustainable and innovative packaging solutions in Australia and New Zealand. This partnership merges Jet’s extensive industry knowledge and customer service dedication with Actega’s 25 years of innovation in eco-friendly coatings, sealants, printing inks, and adhesives. Actega’s commitment to sustainability, encapsulated by their motto “Let us make the world a little bluer,” aligns with their approach to incorporating sustainability into all aspects of their business. The partnership will introduce Actega’s advanced, sustainable products, including abrasionresistant coatings and ACTGreen® Barrier Coatings, addressing the rising demand for environmentally friendly packaging. These initiatives aim to improve food protection, facilitate recycling, and reduce packaging waste, in line with both companies’ commitment to innovation and sustainability. This collaboration marks a significant step towards meeting the increasing sustainability and regulatory demands of the regional packaging industry, showcasing a shared vision for a more sustainable future.
We are pleased to announce our new supplier, Epple. A leader in the sustainable inks industry renowned for their commitment to quality and innovation, Epple will supply us with three advanced products:
1. IML Performance NG: An eco-friendly in-mould label printing ink designed for offset printing, free of mineral oil and cobalt, ensuring rapid drying and compliance with packaging industry standards.
2. Extreme PSO SF: A versatile, all-round ink series is mineral oil-free, semi-duct fresh and made from renewable raw materials and has been evaluated according to the Cradle to Cradle™ product standard and awarded the PLATIN level.
3. LightStar UV LE/LED Premium: A modern offset printing ink optimized for energy-saving LED UV drying systems. It provides excellent printability, reduced waste, and is ideal for paper substrates.
Epple’s expertise in creating high-quality, sustainable printing solutions perfectly aligns with our mission to deliver top-tier products. Their holistic approach combines technical excellence with a deep commitment to environmental responsibility, making them an invaluable addition to our offerings.
please contact us here:
For over 25 years, Jet Technologies have been at the forefront of films, with the widest range in Australia & NZ. Protect, Embellish and add a sense of Touch to your print and connect consumers to your brand with a premium experience. Most films are available in Regular&Thermal versions, in a wide range of sizes, with custom sizes available.
Long-term users know that our standard range of films are still given our utmost attention and are designed to be used at high speed, with maximum reliability and a minimum of fuss, no matt what the application.
Studies show that when you pick up a product and have a sensory reaction, there is an immediate connection between the consumer and the brand. Jet Technologies pioneered this segment with the launch of the Soft Touch range of films many years ago and has kept at the forefront with a number of additional sensory experience films.
Encore Gloss & Matt BOPP – Made with 30% recycled resins, these films look and feel normal but are part of the circular economy.
SteriLam Gloss & Matt BOPP – Protection from all kinds of microbes and bacterial for 10+ years. This includes a substantial reduction in the microbes that cause Covid-19. Perfect for print that is located in public, aged-care and health settings.
Direct Thermal White BOPP – Perfect for use with Direct Thermal equipment in applications ranging from carcass tags to luggage tags. Utilised around the ANZ region for 15+ years, this has proven to be a tough and reliable product.
UniLam Gloss & Matt BOPP – For all manner of digital print, UniLam thermal films are a highly reliable solution that provide a strong bond to all kinds of toners, inkjet and other digital printers.
Upgrade silk screen and analog processes to digital inkjet with the Xaar Versatex Printbar, featuring Xaar Nitrox printheads. Benefit from industry-leading technology, achieve added value for your application and enhance profitability
Key Benefits:
• Easily incorporate creativity and innovation for enhanced value
• Utilise Xaar’s industry-leading printhead technologies for outstanding uniformity, productivity, and performance
• Attain a rapid return on investment through the advantages of digital technology
How it works?
To ensure a smooth printing process, the Xaar Versatex Printbar includes a standard ‘TIFF catching’ workflow. The operator can easily input a printable job into the software, make real-time amendments, and seamlessly integrate it with industry-standard workflows like Esko for direct printing, maximizing efficiency.
Applications
Tailored for a variety of industry-standard self-adhesive label and flexible packaging substrates, encompassing coated paper, polypropylene, polyethylene, and shrink sleeves across diverse sectors like personal care, food and beverage, and pharmaceuticals.
Jet Technologies is pleased to introduce a new option for finishing in the Australian & NZ print markets. In recent years, it has become apparent that the local market needs a new and reliable option for finishing. Jet Technologies have worked diligently to bring the best option to the market, pairing it with reliable service partners that cover all regions in Australia and New Zealand.
Unimax, a prominent Labels & Packaging printer based in the Auckland suburb of Avondale upgraded to Jet Technologies L350UV SAI S Inkjet printer, making it the very first of its kind in New Zealand.
Sold and supported in combination by Jet Technologies and Fujifilm NZ, the L350UV SAI replaced an older model L350UV, bought over 5 years ago that had completely revolutionised their business, moving them from Letterpress to the Digital age.
Back in 2017, there was disbelief as jobs that required setup times of 4-5 hours on their letterpress machines, would set up and print in a matter of minutes. That enabled Unimax to expand substantially their client base and grow their business in higher-value markets, where precision artwork and multiple SKU’s were no issue at all for their new press.
Along came the new L350UV SAI S and the print results have been taken to the next level, with the addition of additional colours (orange and blue) to substantially increase the colour gamut. Productivity increased by 20% on all jobs and by an astounding 67% for jobs containing Screen’s high opacity white. The range of substrates that Unimax could print onto has also increased substantially with this model, enabling Unimax to print on thinner synthetic stocks, as well as a thicker range of paper and hybrid products.
Unimax Director Dinesh Kumar said “We have always been huge fans of inkjet – we were the first to bring the L350UV into New Zealand and can proudly say that we are now the first with the new SAI model. The original press was extremely reliable over its 5 years with us and upgrading was an easy decision, especially with the service we receive from both Jet Technologies & FFNZ”.
For more information, visit our website at www.jet-ap.com or contact David Reece at dreece@jet-ap.com.
Digital label printing specialist, Theia, has become the first company in Indonesia and Southeast Asia to invest in the Screen L350UV SAI Inkjet Series through Jet Technologies.
Theia, a division of Cahaya Jakarta, one of Indonesia’s leading label printing companies that was founded in 1991, was setup to focus entirely on digital label printing in its very own facility in Cikarang, just outside of Jakarta.
Danny Lim, Sales and Marketing Director of Theia, said, “We had been watching inkjet technology for many years as we understood that the productivity benefits were substantial. With the L350UV SAI, we have a press that can deliver outstanding quality print on a wide range of materials with productivity that approaches flexo. Our focus is service and quality, and the L350UV allows us to improve our service substantially, whilst maintaining the highest quality standards. It’s a win-win for us.”
“Cahaya Jakarta started out with letterpress printing, before investing in flexographic printing in 2002 and the first industrial digital printing press in Indonesia in 2009. To be able to install the very first L350UV SAI in Indonesia is another exciting milestone for the entire company and our Theia division,” Danny added.
Sold and installed by labels & packaging specialist, Jet Technologies, the L350UV SAI supports printers to significantly increase turn-around speeds for digital printing jobs by automating the process. With its software generated ‘lead in, lead out’ and ‘reverse-feed’ function, the system also works to considerably lower ink and material waste, reducing overhead costs and improving sustainability standards within operations.
Jet Technologies has a long history with Cahaya Jakarta and Theia, having installed an Omet X6 530-wide flexo press at Cahaya Jakarta in 2016, which at the time was Indonesia’s widest and most productive label press.
“We’re excited to have partnered with Theia and the Cahaya Jakarta group to enhance their digital printing production and provide them with a strong advantage in what is an ultra-competitive label printing market in Indonesia,” said Yulianawati, Sales Manager of Jet Technologies Indonesia. “Theia’s dedicated team has ensured that they bring the very best of digital label printing to Indonesia, with HP Indigo presses previously installed and now the addition of a complimentary L350UV inkjet press.
“Installation and training on the L350UV has now been completed – we promised Theia that it would deliver extremely reliable and consistent print – it is pleasing to see that they are achieving those goals.”
The L350UV SAI is the most flexible and automated label production system in its class. The machine offers seven vibrant colours at 60 meters a minutes, (50 meters a minute when using white) and is fully supported by local Jet Technologies and SCREEN factory-trained engineers. The L350 delivers unrivalled colour reproduction as well as superior scalability, enabling it to meet an even wider variety of market needs.
For more information, visit our website at www.jet-ap.com or contact Yulianawati at yuli@jet-ap.com
Commercial label printing specialist, Label Plus, is now providing its customers with the latest advancement in printing technology following its recent investment in the L350UV SAI Inkjet Press from Jet Technologies, making it the very first of its kind in Queensland.
Label Plus offers a wide variety of self-adhesive labels from its production site in Luscombe, Queensland, with its sister- company (Labelhouse) based in Melbourne, Victoria. Its printing production includes flexography, offset and digital and its diverse customer-base is across pharma, health & beauty, chemical, food, household and wine.
“Our company’s objective is to achieve complete customer satisfaction in all facets of our operations and to be a preferred supplier within the printing industry,” explained James Atkins, General Manager of Label Plus. “Therefore, our focus is on providing excellent quality, whilst maintaining a flexible approach to production, thus offering short lead times at a competitive price.”
“In a challenging industry, Label Plus has evolved into a dynamic organisation, by seeking and embracing new technologies and systems. We’re excited to be elevating our printing quality and customer service even higher with the addition of the L350UV SAI.”
Sold and installed by labels & packaging specialist, Jet Technologies in combination with Screen Australia, the L350UV SAI supports printers to significantly increase turn-around speeds for digital printing jobs by automating the process. With its software generated ‘lead in, lead out’ and ‘reverse-feed’ function, the system also works
to considerably lower ink and material waste, reducing overhead costs and improving sustainability standards within operations.
The L350UV SAI is the most flexible and automated label production system in its class. The machine offers seven vibrant colours at 60 meters a minutes, (50 meters a minute when using white) and is fully supported by local Jet Technologies and SCREEN factory-trained engineers. The L350 delivers unrivalled colour reproduction as well as superior scalability, enabling it to meet an even wider variety of market needs.
“We’re excited to have partnered with Label Plus to enhance their digital printing production and provide the company with the necessary edge to remain on top in a competitive industry,” said David Reece, Sales Director of Jet Technologies.“Installation and training on the L350UV has now been completed and the printing press is not only meeting, but exceeding Label Plus’ well-informed expectations.”
Label Plus added the L350UV SAI to their digital label production capabilities after a very thorough evaluation process of a number of options, including spending time with Jet Technologies in the UK at some impressive L350UV SAI users, in order to properly understand the benefits and how it was being utilized in another sophisticated market.
For more information, visit our website at www.jet-ap.com or contact David Reece at dreece@jet-ap.com.
(L to R): James Atkins General Manager at Label Plus, Chris Lee Production Manager at Label Plus, & David Reece Sales Director at Jet TechnologiesThe continuous expansion and development of the world leading GapMaster system from Kocher+Beck continues with the introduction of the new EM (Electronic Move).
A proven market leader for the adjustment of the gap between the anvil cylinder body and the magnetic or cutting cylinder the GapMaster has been further enhanced with this latest market offering.
The GapMaster EM has in built on-board motors which allow for easy and simple gap alterations from 0.25µm to 10µm.
The system can be quickly calibrated and provides live gap feedback with a useful option for job storage. This makes the entire process more efficient and accurate.
The HMI can be updated to industry 4.0 when required.
The GapMaster is a popular industry choice and is installed throughout the globe, so we have developed a retrofit version of the EM system that is compatible with any pre-installed GapMaster.
The EM Retrofit and EM IC Retrofit can easily be installed on site with the removal of the mechanical handle and replacement with an electrical drive unit.
Offering the same fine control for the setting of the gap regardless of the GapMaster age.
expands its global presence with a new production facility in Poland
KOCHER + BECK, a global leader in innovative solutions for the label and packaging printing industry, is thrilled to announce the opening of its state-ofthe-art production facility in Poland. This strategic expansion marks a significant milestone in their commitment to providing world-class products and services to valued customers.
Located in Świebodzin, Poland, the new production facility is equipped with cutting-edge technology and advanced manufacturing processes. The facility will enhance production capacity to meet the growing demand from customers across Europe and beyond. With a focus on efficiency, sustainability, and quality, the Polish plant will play a crucial role in global operations.
The main features of the new KOCHER+BECK production facility in Poland include:
The facility is equipped with the most sophisticated machines and production processes, ensuring precision and quality in every manufactured product.
With this expansion, KOCHER + BECK can offer a broader range of products and solutions, including innovative printing cylinders, magnetic cylinders, and state-of-the-art printing and packaging components.
KOCHER + BECK is dedicated to sustainability, and the Polish plant is designed with environmentally friendly practices in mind, reflecting their commitment to responsible manufacturing.
This expansion reaffirms Kocher+Beck’s promise to deliver outstanding value and service to our customers. We’re extremely excited about the opportunities brought by this new production facility and look forward to continuing to serve the printing and packaging industry with all its advantages.
Left to right: Joachim Settnik, Slawk, Eric Prabu, Nick MauserThe combination of the CDI Crystal flexo imager with the XPS Crystal exposing unit offers a perfect, consolidated flexo platemaking workflow. The CDI Crystal XPS excels in efficiency and offers distinct benefits :
• Reduce manual steps by 50%
• Reduce errors by 50% – less plate waste
• Reduce operator time with 73%
Our Prepress selector will help you identify whether ArtPro+ or DeskPack is the right tool for your specific needs.
For more information,
our website at www.jet-ap.com or contact Darryl at dwilson@jet-ap.com
Easily prepare artwork for printing production & work directly on PDF files with enhanced editing features, with ArtPro+ the native PDF editor for packaging prepress
Native PDF prepress editor
ArtPro+ Enfocus PitStop Preflight® checks over 200 rules, automatically detecting print issues. Access transparency and object levels for accurate edits without dismantling the PDF, enhancing efficiency in addressing specific concerns.
Cross file format
ArtPro+ opens PDFs, including normalised or classic ArtPro files, preserving packaging metadata like barcodes. It aligns with ‘PDF for packaging’ standards, including ISO 19593-1 for standardized finishing data.
Blazing speed
Read and render PDF content at superspeed, and with uncompromising accuracy. Open large design files in seconds with the state-of-the-art 64-bit core.
Intuitive interface
Conduct complex editing operations without the need for extensive training with an intuitive user interface.
ASAHI PHOTOPRODUCTS has recently achieved a significant milestone by obtaining a carbon-neutral certification in partnership with Carbon Trust for their AWP-DEW CleanPrint flexographic plates, which adhere to PAS 2060 standards and can be rinsed with water. This certification is periodically reviewed and updated, ensuring that the carbon reduction criteria become increasingly stringent with each iteration. The primary goal of this certification is to reduce the carbon footprint of these products throughout their entire lifecycle, including the procurement of raw materials, packaging, product delivery, usage by consumers, and eventual disposal.
The AWP-DEW CleanPrint plates are designed for high-quality flexographic printing applications, such as flexible packaging and labels. Developed by Asahi’s team of chemical engineers, these plates are distinguished by their ability to efficiently transfer ink to the printing surface, thereby minimising the need for frequent cleaning. This feature ensures consistent print quality and enhances the Overall Equipment Effectiveness (OEE) within the printing industry.
Jet now offers the Asahi AFPTM-R solvent washable plate, enhancing environmental sustainability and boosting pre-press and press efficiency. It reduces solvent use by 30% and cuts platemaking time by 50%, saving both time and energy. This advancement marks a significant step in Asahi’s commitment to sustainable product development. Designed for high-quality flexible packaging, labels, and paper applications, this hard flexo plate outperforms standard solvent-wash plates through several functional improvements.
For more information, visit our website at www.jet-ap.com or contact Darryl at dwilson@jet-ap.com
Premium photopolymer plates, suitable for water-based cleaning, enable high-resolution screening and the creation of fine dots.
Exceptional ink transfer achieved through CleanPrint technology significantly reduces disruptions caused by the need to clean printing plates, thus enhancing overall profitability.
The ability to seamlessly transition tonal gradients, improved by the use of highlight dots, facilitates the easy adoption of printing tasks from other printing technologies.
These plates are compatible with a wide variety of inks, including solvent-based, water-based, and most UV-based formulations.
The remarkable flexibility of these plates reduces the difficulties associated with handling them on smaller printing cylinders.
The entire plate-making process can be completed in less than one hour, streamlining production.
These advancements make flexographic printing more environmentally friendly.
• One single ink system that can be used with both traditional and LED UV.
• LED delivers more stable light, resulting in improved consistency of curing and print.
• LED bulbs use less energy – lower energy costs mean lower bills.
• Instantly on – no warm-up needed, saving more energy!
• LED lamps last longer than traditional UV bulbs, reducing costs further.
• Make the switch in your own time –press by press – avoid having two ink inventories.
• Ease of disposal when end-of-life.
• Pre-empts legislative change and issues with traditional mercury based UV.
• Better for the printer and the planet!
Correct anilox selection is one of the biggest hurdles in printing for spot colours. Each change brings the potential for errors, waste, and unnecessary cost – eating into your capacity.
Rather than deliberating over which anilox to use for each colour, or struggling to make your flexo labels look like your digital labels, consider switching to Monolox Fixed Anilox Printing.
Monolox Fixed Anilox Printing is a revolution for the flexo industry. As label designs become more complex, this process makes it possible to produce any spot colour using just one anilox volume, the specially formulated PureTone® ink range, and a bespoke mixing database. As a result, printers can install a fixed anilox set without the need to change rollers between jobs. It ensures instant colour matching and perfect prints, every time.
With pressures mounting in terms of short runs, high volumes, and compressed lead times, it’s important that you can protect your margins and operate e ciently. Fixed Anilox Printing helps you achieve just that.
Save time selecting the right roll
Minimise press downtime
Remove variability from anilox selection
Have control and consistency in your prints
Deliver a service that stands out in a crowded print landscape
With Monolox Fixed Anilox Printing, it’s easy to manage digital to flexo press transitions. PureTone’s unique high-strength formulation means that, when used alongside calibration so ware, you can achieve exemplary run-to-run consistency and repeatability across di erent print methods, making it simpler to scale jobs.
It’s easy to make the change to Monolox Fixed Anilox Printing – many converters are managing it in less than a week. This process has already proven its success with many leading label printers, and is easy to understand and implement. The Pulse Roll Label Products team will be on hand to lend you their full support with the transition.
In the dynamic world of commercial print,ical for meeting customer expectations. The eXact 2 and IntelliTrax2 Pro, two cutting-edge solutions that are reshaping the landscape of colour control in the industry, can help you achieve just that.
The eXact 2 stands out with its unmatched versatility, providing precise colour measurement across a variety of printing technologies.
the eXact 2 ensures consistent colour accuracy, empowering print professionals to meet the diverse demands of their clients.
If you’re looking for automated, press side scanning capabilities, the IntelliTrax2 Pro takes colour control to the next level. This device seamlessly integrates with printing press-
es to instantly measure colour bars and make ink key adjustments in real-time. This not onlyduces waste, making it an eco-friendly choice for environmentally conscious businesses.
These state-of-the-art solutions are setting a new standard for color control in the Australian market. Scan the QR code to learn more and elevate your print quality and operational
Scan to request a demo
THE SCIENC EO FC OL OUR, AP R INTING BY NUMBER S
A PP ROAC H IN THE DIGI TA LE RA
a*,b* chromaticity diagram
Di
indicates lightness is the red/green coordinate is the yellow/blue coordinate.
Deltas for , maybepositive (+) or negative (-)
The total di erence, Delta E however, is alwayspositive
Representationof
Anilox Reverse Technology - designed for Flexo Printing, offset coating, gravure, and laminating applications.
For many years flexographic printers have struggled with ink spitting during some jobs. Ink spitting can be caused by a number of factors, however to combat ink spitting, Praxair have developed Proline ISF cell engraving. ISF engraving has proven over the years to reduce the occurrence of ink spitting and reduce costly downtime on the press
Recyl’s Cobra is the global leader for Anilox Deep Cleaning gel to unplug tough to clean anilox rolls Cobra has established itself as the one-stop solution for Anilox deep-cleaning and complete restoration of ink-transfer capacity. Cobra restores the full volume of your cells and maximizes the ink-transfer capacity of your ceramic anilox rolls. Cobra works on any type of ink as well as coatings. Cobra adds value in all segments of the flexo-printing industry.
Contact dwilson@jet-ap.com for a demonstration request
The fully automatic anilox roll cleaners are designed to deep clean/restore anilox rolls, sleeves or gravure cylinders of all sizes. Furthermore, it is also a very good tool for the daily washing and maintenance of rollers.
• Fully Automatic Cycle with Short Washing Time
• Recirculation/Re-use of Liquid
• Harmless to the Rollers
• Cell Volume Completely Restored
• Safe and Easy Washing
• Stainless Steel
• Reduction in downtime
RotaPlate® features a patented SPGPrints process to enhance mesh material, creating distinct textures on each side. The smooth squeegee side minimizes wear, while the sharp-edged printing side ensures precise and clear results for customers.
RotaPlate® screens boast 40% more holes per square centimetre than woven screens, enabling precise ink transfer for sharper fine prints and smoother solids.
The emulsion in RotaPlate® is selected for its sensitivity to the human eye, providing pre-press operators with improved contrast for easier scrutiny of fine details during development before printing.
Our comprehensive service package includes installation, application support, and training. On-site experts provide tailored advice, and our Technology Centre allows testing of new products in a real production setting. RotaPlate® boosts competitiveness and protects margins, ensuring excellence at every production stage.
Eric Prabu from Jet Technologies Australia recently visited SPG Prints in Boxmeer, Netherlands, exploring screen production, specifically focusing on SPG’s Rotary Screen technology. Guided by Eberhard Klenner, Eric was impressed by SPG’s transparent and quality-driven approach, expressing confidence in their commitment to topnotch products. This visit underscores SPG Prints as a leader in Rotary Screen technology, blending expertise and innovation.
“Eberhard Klennerand the SPG team’s hospitalityduring myvisit to their Boxmeer facility was exceptional. Touring the manufacturing processes from start to finish, I gained confidence in the high quality products SPG provides.” – Eric Prabu
For more information, visit our website at www.jet-ap.com or contact Eric at eprabu@jet-ap.com
Many of you will have come across Christine over her 12+ years with Jet Technologies - Christine is part of the Customer Service team, managing all manner of orders and client enquiries.
Christine also holds the title of “Jet Coffee Art Champion” with her impressive work. When you next visit us in Sydney, be sure to ask Christine for a coffee!
Sydney
19 Rosebery Ave
Rosebery NSW 2018
t: +61 2 8399 4999
f: +61 2 8399 2277
e: orders@jet-ap.com
Melbourne
7 Yazaki Way, Carrum Downs, VIC 3201
Brisbane
45-49 Quilton Place
Crestmead, QLD 4132
Jl. Kenari Raya Blok A /No. 11
Delta Commercial Park
Delta Silikon 6, Lippo Cikarang
17550 Indonesia
t: +62 21 899 11 392
f: +62 21 579 98 080
e: info@jet-ap.co.id
Jet Technologies global partner network
Our strength is our unequalled access to a global network of partners, meaning we can bring you the perfect solution for your product.
www.jet-ap.com