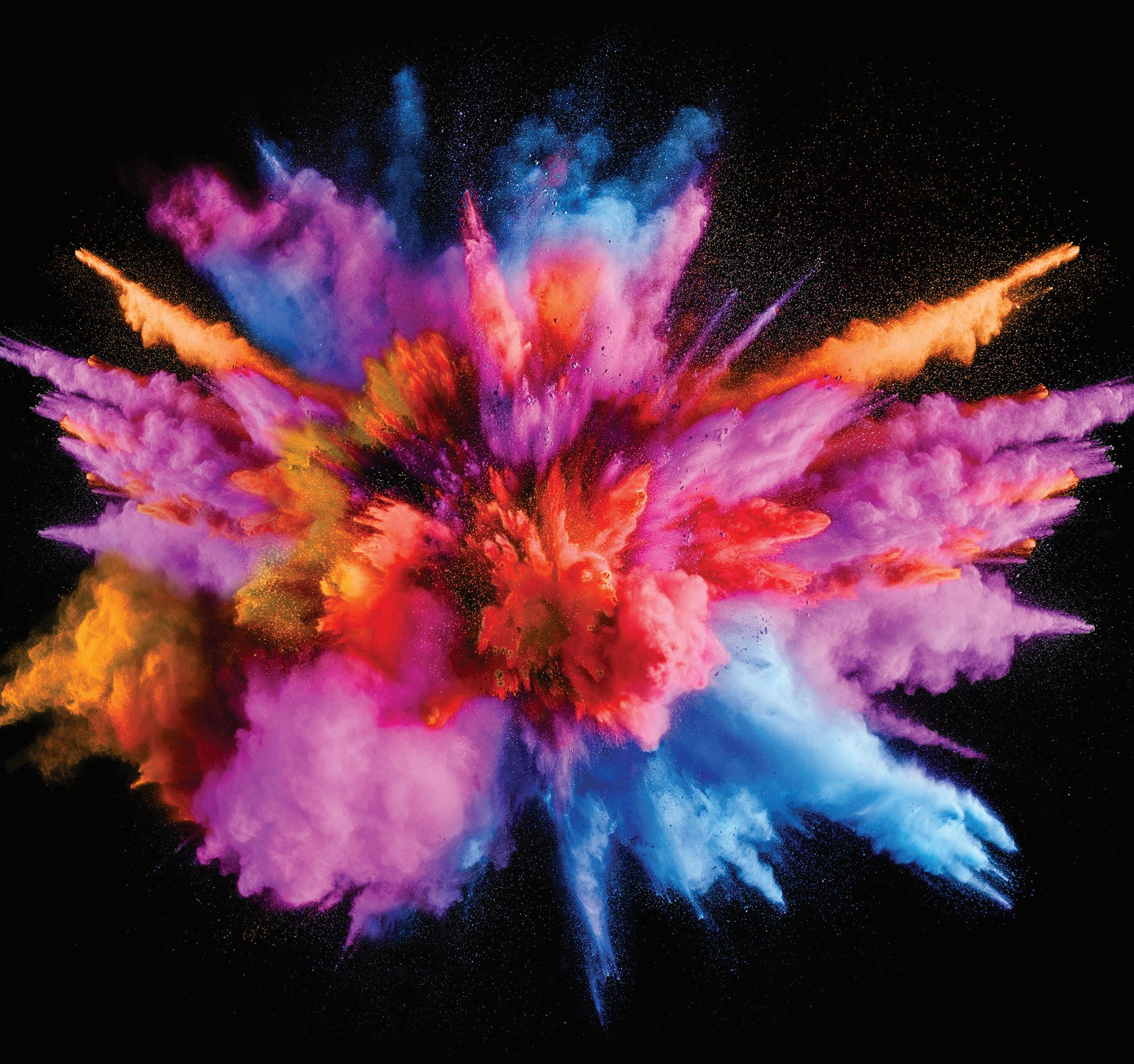
jmalki@jet-ap.com
Editor Sandeep Chouta schouta@jet-ap.com
Orders orders@jet-ap.com
Design
Sanja Spuzanic
JET LIFE
is published by Jet Technologies Pty Ltd
ABN 12 515 939 347
19 Rosebery Ave
Rosebery NSW 2018
JET Media
jmalki@jet-ap.com
Editor Sandeep Chouta schouta@jet-ap.com
Orders orders@jet-ap.com
Design
Sanja Spuzanic
JET LIFE
is published by Jet Technologies Pty Ltd
ABN 12 515 939 347
19 Rosebery Ave
Rosebery NSW 2018
JET Media
While the past couple of years has brought with it many challenges and an upheaval with the pandemic, current war in Ukraine, inclement weather, and global supply chain issues our industry has been resilient and has faced these challenges head on.
During these challenging times Jet Technologies has continued to invest to deliver unrivalled level of customer service, which has been invaluable in supporting our customers during an incredibly challenging time – whether due to slow-downs or spikes in business. We have increased our investment primarily in increasing our inventory levels and IT systems.
Foreseeing the global supply chain turmoil, we have invested in stocking more inventory, with stock levels approximately double what they were in 2019. Whilst much of the growth has been in our Sydney and Melbourne primary warehouses, we have also employed several 3PL warehouses across the country and also made distribution agreements in WA and NZ in order to best serve clients across this very large geographical area. As we publish this edition, we are looking to expand our Melbourne facility substantially within the end of 2022.
We have also made a huge investment on our IT system. It may sound simple, however that has been to develop our own systems, for example one that constantly tracks our inward shipments by
container number and delivers updated vessel tracking information to our SAP system. Whereas in the past we may have had the occasional shipping delay/change, these days it is normal for multiple delays for each shipment and having up to date information is critical in maintaining the best possible supply-chain. Clients are now also able to logon to our Jet Live system to automatically complete their consignment counts or request additional stock mid-month, with automated delivery and tracking information sent once consignments leave our warehouses.
After 40 years as a leader in the printing and packaging industry, Jet Technologies’ dedication to providing support for its customers during these challenging times is testament to its resilience. We will strive to continually improve and provide improved levels of service to our clients.
In June this year we will be participating in the PacPrint exhibition held in Melbourne. We are looking forward to having face to face interaction with so many of our customers and other industry participants/ visitors during this event.
We hope you enjoy reading this edition of Jet Life!
Jack MalkiTAKE A FRESH LOOK AT THE L350UV SAI
Screen L350UV SAI series delivers:
• Industry-leading productivity (up to 80m/min)
• Highest reliability (>93% Uptime)
• Ability to upgrade on site
Melbourne-based narrow web print provider, Onpack, has enhanced its digital operations by upgrading to the latest automated label production system – the Screen L350UV SAI Inkjet Series.
Sold and installed by Onpack’s longterm partner, Jet Technologies, the latest SAI Series, featuring improved colour reproduction and scalability to meet a diversity of industrial and market needs, is an upgrade from the Screen L350UV V1 and V1+ that it initially used.
Onpack said it upgraded its technology as its recent venture into labels and packaging has since seen it service a variety of industries – including food and beverage, FMCG, commercial, health and beauty, and sports and nutrition.
“Our first investment in the original L350 series gave us the platform to meet our growth ambitions as a business, whilst optimising our digital printing capabilities with process control, enhanced quality, and improved efficiency,” Onpack founder and managing director Michael Nankervis said.
“Four years on, we grew even more, and with the continued support of Jet Technologies, we were ready to expand into Flexo graphic printing and grew our capacity even further.”
Earlier this year, the latest Screen L350UV SAI Series was officially released and demonstrated at Jet Technologies’ Sydney demonstration room. After witnessing its improved capabilities and features, Onpack placed its order of the system which is now in operations at its head facility in Melbourne.
Nankervis said the new L350UV SAI Series delivers a higher level of productivity and
has since improved Onpack’s production capacity by 20 per cent for colour printing and 60 per cent for highest opacity white colours, along with an extremely high level of printing repeatability.
The upgraded system has additionally enabled Onpack to operate with an exceptionally wide range of colours, without ink wastage.
“Since installation, the SAI upgrade has enabled us to significantly increase our turn-around speed for digital printing jobs by automating the process. With its software generated lead in lead out and reverse-feed function, we’ve also considerably lowered our ink and material waste, which has reduced overhead costs and improved our sustainability standards,” Nankervis added.
Jet Technologies sales director David Reece said the L350UV SAI Series’ ability to print on a diversity of local and imported materials has positioned it as one of the most innovative and efficient automated label production printers available today.
“Even more so, with improved productivity rates of up to 60 per cent compared to the previous model, the SAI serves as one of the fastest solutions on the market, with the highest-quality results, and we’re incredibly pleased to see Onpack further its digital innovation by upgrading to this latest model,” Reece mentioned.
Sydney-based packing and labelling specialist Luminar has expanded its digital printing operations with the deployment of the Screen L350UV Inkjet Series.
Supported by Screen’s 10-year partner Jet Technologies, the L350UV is an inkjet press for both the labelling and packaging sectors. Since the implementation of the L350UV, Luminar has extended its digital printing capacity and streamlined its existing digital operations.
Positioned as a hybrid digital labelling and flexible packaging company, Luminar’s broad industry base includes industrial and automotive customers such as ACCO Brands, and food and beverage customers such as My Muscle Chef and Mingle Seasoning, as well as craft beer and health and beauty customers.
“With such a diversity of customers, we needed a solution that would increase our printing efficiency without sacrificing quality or attention to detail. The decision to select the L350UV came about after a long association with Jet Technologies, where they systematically proved the L350UV’s unrivalled reliability and high productivity,” Luminar managing director Matt Ellis said.
“Since working with the new system, we have found that it is incredibly efficient and agile; offering a wide range of material solutions that are used to service our existing customers whilst also supporting our growth trajectory as a business.”
The L350UV is a flexible and automated label production system in its class, delivering speeds of up to 60 meters per minute, with a prominent inkjet-head technology ensuring both quality and throughput.
“Since 2018, our flexible packaging sales have grown by over 100 per cent year on year, and in an effort to continue servicing our customers at the highest level, we felt the L350UV was the best solution for us and our customers to cater to this business growth.
“Having the local support from Screen and Jet Technologies made the decision a no-brainer, and we are excited about the additional strength this system will provide for our already-strong printing capabilities,” Ellis said.
Jet Technologies director of sales David Reece said the printer will expand Luminar’s capabilities.
“We have worked with Luminar for many years and are very excited at the digital printing opportunities that the L350UV will bring for their business,” Reece said.
“The L350UV is an incredibly reliable and highly productive machine and will support Luminar’s ongoing growth across multiple markets.”
SteriLam Anti-Microbial Films are safe and contain an invisible and odourless ingredient –Biomaster – which is based on Silver-ion technology and inhibits the growth of microbes by up to 99.99% and reduces Covid viral load by > 84%. The films destroy bacteria, fungi, and moulds including antibiotic-resistant bacteria such as Staphylococcus aureus (MRSA) and Vancomycin-resistant Enterococcus (VRE).
Independent accredited laboratories have tested how well our SteriLam Anti-Microbial films perform in keeping their surfaces free from viruses and bacteria and preventing the spread of contagions. The results are remarkable!
Key Benefits include:
l Antiviral
l Antibacterial
l Gloss and Matte finishes
l Resistant to washing and cleaning
l Fully recyclable
Applications include:
l Pharmaceutical and supplement packaging
l Hospital communication material and packaging
l School and university books
l Printed items displayed in public transport and restaurant materials
l Packaging of personal care products
SteriLam Anti-Microbial Films remain effective for a period of ten years or longer, regardless of how many people come into contact with the product, as they are durable and don’t wear off or leach out.
For further details please contact Luke Welsh at lwelsh@jet-ap.com
Jet Technologies supplies a range of specialty films and grades that are optimal for all your print operations. Our range of films include:
SteriLam: Protection from all kinds of microbes and bacteria for 10+ years!
Rough Touch: A rough textured film with superior protection that makes your product hard to put down. Now also slip rated for floor applications.
Soft Touch Plus: Adds the ultimate sensory experience taking your print and packaging elements to a whole new level. The films are Anti-Scuff, AntiFingerprint and Over-printable.
Samurai: Our standard range of gloss and matt is ever reliable and available in many standard sizes from stock.
UniLam: For digital print, this film is unbeatable for finish and consistency.
In addition to films, we also stock adhesives and UV Coatings.
Perfect binding hotmelt (standard and PUR) suitable for large production machines as well as smaller digital finishing machines.
Hot melt adhesives for folder/gluers
A large number of finishes available to suit every application.
Please contact Luke Welsh, Films Business Development Manager, lwelsh@jet-ap.com for any enquiries.
Esko, the global developer of integrated software and hardware solutions for the packaging and labels markets, has collaborated with Asahi Photoproducts, a pioneer in flexographic photopolymer plate development, on the innovative flexo platemaking solution. CrystalCleanConnect fully automates the entire platemaking process, from imaging and exposure through to plate production, reducing the number of steps in the flexo platemaking process from 12 to just one. This equates to a reduction from 36 minutes in platemaking and plate cutting to just 2.5 minutes of operator time to complete all processing steps.
“With CrystalCleanConnect we have brought together key hardware and software technologies from both organisations to deliver a number of breakthrough advantages from design to print,” said Pascal Thomas,
Director of Flexo Business with Esko. “CrystalCleanConnect delivers a cleaner, more environmentally balanced operation that simplifies the flexo platemaking process, improves safety and boosts print quality consistency.
“With CrystalCleanConnect, the operational benefits to businesses are as pronounced as the environmental benefits,” said Pascal. “With the removal of so many process steps, there’s an immediate 90% reduction in required operator time, which not only eliminates the potential for human error but also delivers immediate efficiency gains. Quality is assured through Asahi and Esko technologies working in complete harmony, and the combination of improved efficiency and quality delivers an average increase of 25% in press OEE.”
Dieter Niederstadt, Technical Marketing Manager for Asahi Photoproducts said: “Flexo needs to simplify processes while improving quality, consistency and profitability. In doing so, flexo can create new business opportunities and positively transform into a printing technology in balance with the environment.
“This breakthrough innovation is different in many ways to other solutions on the market,” Dieter said. “It is not just an assembly of available plate making processes delivered inline, but rather a holistic approach to connecting technologies, up and downstream of the prepress value chain, using an intelligent automation hub as the backbone and heart of the solution. CCC is truly pushing boundaries to the current scope of plate automation delivering a
mount-ready plate as well as being the first automated production solution without the need for VOC-based washout solvents in in the platemaking process.”
Pascal Thomas added: “At Esko, we have long been dedicated to improving the platemaking experience, in terms of quality, productivity and connectivity. Together with Asahi Photoproducts, we are taking the flexo platemaking process to a brand-new level, enabling our customers to be even more competitive while also ensuring they can meet today’s demands for flexible and sustainable supply.
“With CrystalCleanConnect, our ultimate objective is to improve our customers’ overall business performance and profitability,” said Pascal.
In response to market demands for haptic coatings that add a premium touch and feel to a consumer package or label, the PureFX sp e cial effects range includes UV flexo varnishes formulated to provide rough and soft tactile effects for sensory consumer engagement.
Rough Texture Varnish FPC236
Soft Touch Varnish FPC238
FPC = Food Packaging Compliant
Both products comply with the regulations and guidelines for non-direct food contact packaging applications and provide an ideal sensory solution for finishing either conventional UV flexo or digital print.
Formulated for excellent adhesion, fast cure, high chemical resistance and low gloss levels, the PureFX Rough Texture and Soft Touch Varnishes are suitable for printing on substrates including coated PE and PP, aluminium foils and papers.
PureFX Rough Texture Varnish - adds another dimension to enhance and embellish labels and packaging with a rough matt textured effect. Different tactile effects, fine or coarse, can be achieved dependent on film weight. With excellent printability, it is a popular finish for craft beer, wine and other alcoholic beverage labels, but increasingly for other consumer-packaged goods such as food and personal care.
PureFX Soft Touch Varnish - formulated to offer narrow web printers a cost-effective, sustainable alternative to soft touch laminating film and a more consistent and durable finish compared to water-based soft touch coatings. This smooth tactile effect is perfect for providing a premium quality soft touch on labels and other printed packaging. With excellent overprintability, press stability, and high rub resistance, this product is particularly well-suited for end-use markets including cosmetics, beauty, personal care, baby care and beverages.
Pure FXΔL* indicates lightness
Δa* is the red/green coordinate
Δb* is the yellow/blue coordinate.
Deltas for L* (ΔL*), a* (Δa*) and b* (Δb*) may be positive (+) or negative (-)
The total difference, Delta E (ΔE*), however, is always positive
ΔL* (L* sample minus L* standard)
= difference in lightness and darkness (+lighter, -darker)
Δa* (a* sample minus a* standard)
= difference in red and green (+redder, -greener)
Δb* (b* sample minus b* standard)
= difference in yellow and blue (+yellower, -bluer)
Representation of colour solid for L*a*b* colour space a*,b* chromaticity diagramThe partnership with Stockman Paper Merchants and Jet Technologies commenced in 2019 and has helped position Stockman Paper Merchants as the leading supplier of laminating film in the West Australian market.
“Stockman Paper Merchants were already at the forefront in W.A, supplying a wide range of BOPP Wet Lamination films into the reel fed label market, utilising our vast experience in this sector and having the most modern, state of the art slitter / rewind facility in Perth. With the addition of Thermal Laminating Films and having access to Jet Technologies warehouses in Melbourne and Sydney, our position in the market has grown much stronger” says Christopher Grant, product manager Stockman Paper Merchants. He further added “We are recognised by the W.A market as a reliable supplier of both Wet and Thermal Laminating Films and we are now finding an increased demand for our specialty films, such as Soft Touch, Anti Scuff, Metalized Soft Touch, and the new Rough Touch film.”
Rough Touch is quite unique and has been getting used for Boutique beverage can labels for well over 12 months now, with the demand growing.
Recently, Perth’s leading Printing Company, Scotts, who are recognised Australia wide as an innovative, quality Printer, have produced a range of promotional pieces for specialty laminates. Scotts recognised the marketing opportunities for specialty laminates and have already been successful in securing business utilising Rough Touch.
“I am thrilled with the Rough Touch product. I recently had a presentation folder project for a construction company.”
“Theywanted something hard wearing that would align with their image and branding.”
“RoughTouchwasperfect.”
“The presentation folders were embossed, UV varnished and die cut.”
“They turned out perfectly and the client was thrilled.”
“RoughTouch has filled a real gap in the offerings of laminates.”
“I am always looking for new applications for it.”
Ben Brennan Account Manager ScottsPrinters today face a multitude of challenges as they try to remain competitive and – at the same time – meet brand owners’ requirements for quality and flexibility of service. SPGPrints’ screens give you an exceptionally reliable, longlasting and highly accurate means of printing on a wide range of web widths.
The ultimate workhorse in screens for rotary screen integration
SPGPrints’ RotaMesh® is a top-quality screen customised for the SPGPrints Rotary Screen Integration (RSI®) printing unit. A RotaMesh® screen is a non-woven, electroformed mesh made out of 100% nickel. The unique hexagonal ‘honeycomb’ structure ensures sharp printing quality, maximum stability and consistency.
The perfectly fitting mesh for all rotary screen printing presses
RotaPlate® is an excellent alternative for users of woven screen material. It’s strong, stable and offers a long working life. Thanks to a patented production process, SPGPrints’ RotaPlate® features a pre-sensitised coating and a hexagonal ‘honeycomb’ structure that is made out of 100% nickel. The result is excellent print performance at each stage of production. Get more printed metres out of your mesh.
Jet technologies offers local technical support by simplifying digital pre-press workflow for rotary screen making, starting with cutting and punching facilities, on all sizes of rotary screen material as well as welding and film free state of the art laser exposing technology. All these services are based at our head office in Sydney and backed up by SPG Prints global service.
We also offer a wide range of rotary screen-printing consumables as well as the latest developing and drying system to standardise quality and accelerate throughput in your pre-press workflow.
We all know that cleaning press parts is a hassle and really hard work. There are a lot of parts that must be consistently clean if you want continually high output from your printing machine. There is no easy way to go about it, or is there?
Automated cleaning of press parts is the smart way to make sure you have consistent high output from your printing machine and the highest possible printing quality. It does not matter whether you clean with solvents, non-flammable liquids or alkaline liquids you get the same high results every time.
With staff shortages during the pandemic there is a focus on automation to increase efficiency, save time and reduce manual labour.
When you implement automated cleaning into your production you significantly increase the overall cleanliness of your workplace. However, the most important thing is that you reduce the number of do-over printing jobs you have in your production, your print quality improves, and you will potentially be able to scale up your production to do even more printing jobs.
The printing machinery you have invested in has certain numbers that you bought into, amongst other printing speed time to set up and quality etc. none of those can on day-to-day basis be reached if you run the operation based on manual cleaning.
Downtime is bad for business. One thing is that the productions halts, because of a flaw or failure - the worst thing is that you must spend valuable time finding, where the fault is and then most of the time start all over again on your project.
With an automated cleaning machine for your press parts, you make sure that your printing machine is always clean and is always ready to do your next printing job – and do it well.
Your printing machine is the heart of your production. It is the main thing that makes you money, but do you know what else makes you money? Proper cleaning.
Proper cleaning of you printing machine prolongs its lifetime and you get more in return on your investment and fewer do-over jobs, because you have a clean machine that does not affect your printing job.
Manual cleaning of your press parts is a slow and tedious process that takes a lot of manpower. But what is even worse is the effect manual cleaning has on the cleaner’s health. Research show that a person that does manual cleaning is more likely to get sick and leave their position. Even if you want to do it right, setting up a manual cleaning operation without any health hazards is challenging.
Implementing automated cleaning significantly increases the overall health and safety of your employees and they are more likely to remain in their job for longer, which means you can concentrate on more important matters, than rehiring for the same position repeatedly.
Manual cleaning takes up a lot of space. You need space for all the equipment, solvents, and workers. Then you also need a place to dry all your press part and lastly you need a place to store the used material safely. With an automated cleaning machine, you immediately reduce the amount of space you need.
When you switch to automated cleaning you can create a new unique workflow for your production, where you bring the cleaning closer to the printing machine and in return reduce the time it takes to clean your machine even more.
Australia
Sydney
19 Rosebery Ave
Rosebery NSW 2018
t: +61 2 8399 4999
f: +61 2 8399 2277
e: orders@jet-ap.com
Melbourne
31-33 Cyber Loop
Dandenong South
VIC 3175
Jl. Kenari Raya Blok A /No. 11
Delta Commercial Park
Delta Silikon 6, Lippo Cikarang
17550 Indonesia
t: +62 21 899 11 392
e: orders@jet-ap.co.id
t: +64 21 743 407
e: orders@jet-ap.co.nz
Our strength is our unequalled access to a global network of partners, meaning we can bring you the perfect solution for your product.