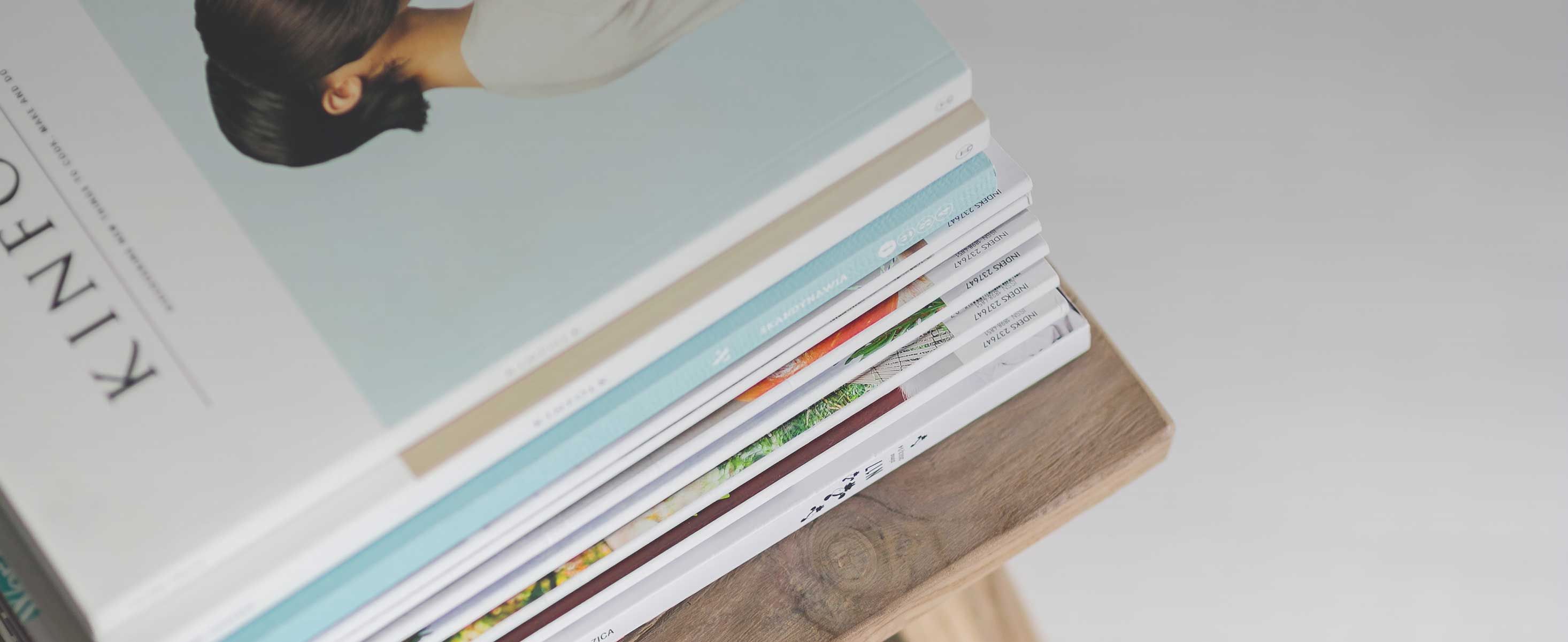
6 minute read
Capítulo V –Dentro da Fábrica
CAPÍTULO V
DENTRO DA FÁBRICA
Advertisement
No mundo, na vida, nada é permanente; tudo pode mudar a qualquer momento. Na nossa casa então, nem se fala! Uma nova pintura, uma ampliação, uma demolição, um eletrodoméstico novo, descarte daquilo que não serve mais, um conserto aqui, outro ali... Parece que nunca termina! Numa Indústria não é diferente.
MUDANÇAS e AUTOMAÇÃO
Lembro-me que, todo ano ao se aproximar o período de férias coletivas na Refrigeração Paraná, havia uma movimentação entre o pessoal da Manutenção, Planejamento Industrial e Engenharia, para traçar planos de trabalho para quando a fábrica parasse a produção. Era nesse intervalo de produção que o interior da fábrica virava um canteiro de obra, com alteração no “layout” das linhas de montagem, retirada de equipamentos obsoletos, instalação de novos, mudança no piso, pintura nova, reparos em telhado, instalações elétricas e muito mais. O cronograma era apertado e tinha que ser concluído antes do retorno do pessoal. Salvo algum contratempo por conta de fornecedores, as coisas acabavam satisfatoriamente. Anualmente, o aspecto interno da fábrica ia mudando com as modificações e, principalmente com os novos equipamentos para a produção. A fábrica ficava mais moderna, mais limpa e, portanto, mais produtiva.
A modernidade numa indústria vem para simplificar a fabricação de seus produtos, tornando mais rápida a produção, mas também tem o seu lado obscuro, que às vezes passa quase despercebido. Quando a Refrigeração Paraná (e outra indústria qualquer) nas décadas passadas produzia seus produtos, não havia muita tecnologia na fabricação; os equipamentos eram antigos, pouco produtivos e empregava muita mãode-obra braçal mesmo, pincipalmente na Metalurgia.
Lembro-me da grande quantidade de pessoas em volta das máquinas e dos dispositivos, manuseando e soldando grandes peças metálicas, outros martelando, outros lixando. O ambiente era muito barulhento e com pouca ventilação. Para produzir um refrigerador tipo monobloco, isto é, um gabinete composto de várias peças unidas entre si, como era o caso dos produtos na época – anos 60/70, esse processo era quase artesanal, e por isso, muito demorado. Não apenas na área metalúrgica, mas também em outros setores da fábrica acontecia a mesma coisa. No setor de plásticos tinha muita mão-de-obra no acabamento e colagem de peças. Na pintura era tudo manual; os pintores com gorros, óculos, máscaras e com pistolas davam conta do recado, já que a produção era pequena. Mais tarde a pintura foi automatizada na fábrica 1, dando mais impulso à produção.
Outro ponto problemático na produção estava na linha de montagem do refrigerador. Sendo o gabinete composto de várias peças metálicas, sempre havia frestas entre elas que deveriam ser vedadas internamente, antes de seguirem em frente na linha. Essa vedação era muito importante, pois sem ela o produto poderia apresentar sudação externa durante o uso.
Na época, essa vedação era feita com asfalto – isso mesmo – que era derretido num recipiente aquecido a gás, no início da linha de montagem. O funcionário enchia uma caneca no recipiente que continha o asfalto e derramava naquelas frestas a fim de vedá-las. Mas antes dessa operação, e paraevitar que o asfalto escorresse para fora do gabinete, as frestas internas maiores eram preenchidas com pedaços de jornal velho –por incrível que pareça, um item “importante” na fabricação da geladeira era... Jornal velho, sim senhor! Ao lado da linha tinha uma pilha da Gazeta do Povo e da Tribuna do Paraná! O pessoal, de vez em quando, até dava uma lida em notícias velhas! Agora, imagine a poluição, o cheiro forte no local com o asfalto sendo derretido num caldeirão na sua frente! Não era trabalho fácil para os operadores.
(Houve pelo menos um caso, em que o operador da caneca deixou de efetuar a vedação numa geladeira, e essa geladeira foi parar justamente na casa do meu sogro; algum tempo de uso, começou a sudação externa e umidade no chão. Desconfiei do problema e desmontei-a e, de fato, estavam lá todas as frestas sem jornal, sem asfalto, e com a lã de vidro encharcada! Tive que fazer a vedação com um punhado de asfalto que levei da fábrica e, depois de secar a lã montar tudo novamente).
A seguir eraintroduzida no gabinete uma manta isolante de lã de vidro, antes de encaixar o gabinete interno no externo. O manuseio dessa manta exigia que os operários naquele posto – e também na montagem de portas - usassem máscaras, gorros, óculos de proteção e luvas sintéticas longas. A movimentação dessa manta tinha que ser com muito cuidado para não dispersar resíduos no ar do local. Havia, de fato um pouco de poluição. Mas esse era o método de fabricação vigente. Era o que se fazia na época naqueles produtos; calafetador químicos para o caso era muito caro, razão para que se usasse o asfalto.
Esse processo perdurou até o dia em que a fabricação daqueles produtos foi definitivamente encerrada, dando lugar a uma nova geração de produtos que viria a seguir, com novos métodos de trabalho, novos equipamentos e automação de processos, simplificando a produção, o que resultava num ambiente mais limpo, mais seguro, mas também na redução do número de pessoas nos postos de trabalho.
Lembro-me de alguns cortes de pessoal, principalmente no chão de fábrica, o que nos deixava entristecidos vendo aquelas pessoas sendo dispensadas do seu trabalho.
Às vezes os cortes de pessoal tinham – e ainda tem - outros motivos, como, a baixa demanda dos produtos no mercado e acúmulo de estoque; outras vezes, não havia dispensa, mas eram dadas férias coletivas fora de época, enquanto o estoque permanecia alto. Em casos mais sérios, chegava-se ao cancelamento de algum turno de
20 trabalho. Às vezes era motivos financeiros mesmo como “redução de custo”, não apenas no chão de fábrica, como também na área administrativa e técnica.
O interessante é que, quando passava aquela fase ruim, a empresa voltava a contratar, dando preferência para ex-funcionários. Por outro lado, conheci muitas pessoas que, por razões pessoais, saíram da empresa para novos desafios, como costumavam dizer, porém, passados alguns anos, lá estavam trabalhando novamente na Refrigeração Paraná. Parece que a empresa era um ímã que atraía muitos daqueles que se afastavam, e também segurava muitos daqueles que pretendiam sair. Eu mesmo, em duas ocasiões, pensei em sair da Refrigeração Paraná, e até fui a outras empresas procurando uma vaga. Numa delas cheguei a fazer uma entrevista, mas nunca mais voltei lá para saber o resultado. Acredito que os amigos que trabalharam lá na época, vãose identificam com essa situação. Mais recentemente na Electrolux, fui dispensado e, no entanto, pouco mais de um ano depois fui chamado de volta para fazer aquilo que mais gostava: Projetar!
É traumáticopara um trabalhador, ser dispensado do seu emprego, porém, uma empresa é impessoal; tem a finalidade de gerar lucro para seus proprietários ou acionistas, e só sobrevive com a venda dos seus produtos, caso contrário, fecha as portas. Isso lembra uma frase atribuída a Henry Ford: “Não é o empregador que paga os salários –ele apenas administra o dinheiro -Quem paga o salário é o produto”. Logo, se o produto é bom, moderno, bem feito, atrativo e competitivo, só pode ter boa aceitação no mercado, dar lucro para a empresa, e satisfação para aqueles que contribuíram de alguma maneira na sua fabricação.