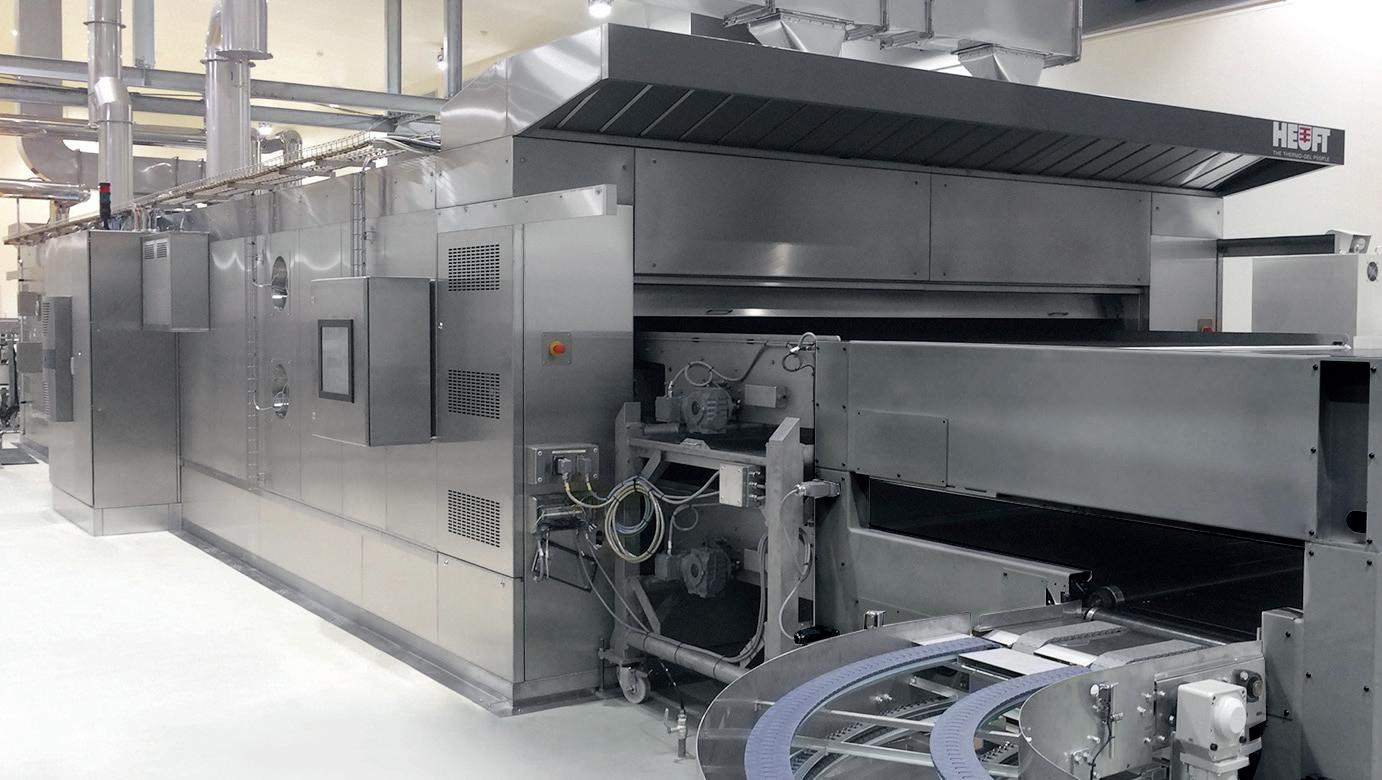
8 minute read
Heuft Industry: Energy savings at the end of the tunnel oven
from f2m Automation Book
by landmagd
Energy savings at the end of the tunnel oven
+Thermal oil provides unique benefits when used as a liquid heat transfer medium in baking. Heuft tunnel ovens are the reflection of how the technology encapsulates these advantages to provide constant temperatures throughout the oven, in a gentle and even heat transfer to the products, while also achieving significant energy savings. This is the result of Heuft’s 50-year expertise in the field of thermal oil, and a background in oven manufacturing dating back 300 years.
Unique advantages of thermal oil
Thermal oil has very high heat conduction properties, minimizing the temperature difference between the transfer medium and the oven chamber. This helps thermal oil ovens to reach the baking temperature very fast; during the baking process, the thermal oil circulates at a constant temperature through the oven system. Depending on the number of products and pans per square meter in the baking area, a certain heating capacity is required, and such volume changes can result in unwanted heat variations. With its huge capacity for heat transfer, thermal oil always has enough power to keep the temperature constant during the baking process. The thermal oil technology perfected by Heuft ensures minimal temperature fluctuations in the baking process and leads to uniform, reproducible quality
www.heuft-industry.com
Wehrer Str. 21 56745 Bell Germany info@heuft1700.com Fon +49 2652 9791 0 Fax +49 2652 9791 31

© Heuft Thermo-Oel
consistently. Thermal oil not only conducts a lot of heat but also transfers this heat evenly to the products through the radiator plates inside the baking chamber. A constant temperature is maintained thanks to the three-way valves that are continuously regulating the amount of hot oil going into the oven to preserve the requested temperature.
The small temperature difference between the heat transfer medium and the baking chamber is made possible due to the high heat storage capacity of the thermal oil, which is approximately 2,700 times higher than some of the other heat transfer mediums such as hot air. With this low Delta-T, there is no flash heat in the oven and, in case of an empty spot, the products are not burned; instead, this powerful heat is gently transferred to the baked goods. The result is a bigger volume, a better crust and a longer shelf life with a moist crumb, as the product is not dried as much as with other baking methods.
The amount of thermal oil required varies depending on the size of the oven, and it can sustain baking cycles for years. With our new oil ‘HE30green’ in combination with our upgraded Nitrogen blanketing system, the lifetime of the thermal oil is assured for many years.
Premium quality in an industrial dimension – tunnel ovens
Our latest tunnel ovens running with thermal oil technology can have up to three decks that add up to a useful baking surface of up to 4m in width and 60m in length. We have perfected thermal-oil baking technology for half a century. While the basics of this technology have remained unchanged since then, our breakthrough developments have come with new oven models. The main one was launched in 1988, when we started producing static rack ovens heated with thermal oil. In the following years, we have been inventing different new oven solutions, most of which are custom-made. Over the last 10 years, we have focused on bringing serious improvements to and developing our industrial ovens, which is reflected in our newest equipment.
With either a two- or three-deck setup, our tunnel ovens save considerable production space and are much more flexible than tunnel ovens with a single deck. Product-specific oven parameters allow us to reach the required baking result precisely; they include steam quantity, top and bottom heat, different temperature zones, convection zones, steam extraction and fresh air inlet. Our continuous product development always
Our way to thermal oil
+With a history dating back over 300 years, Heuft is the oldest oven manufacturer in the world. + The Heuft group of companies is a family-run business, now in its 8th generation, with Thomas Heuft as owner and managing director. + Bakeries in over 24 countries rely on the
Heuft Thermal-Oil ovens. + Heuft can look back on more than 50 years of thermal oil technology.
The Heuft philosophy of specializing in
‘100% thermal oil’ has been successfully established on the market. Today Heuft is the market leader for ovens with
Thermal Oil technology.
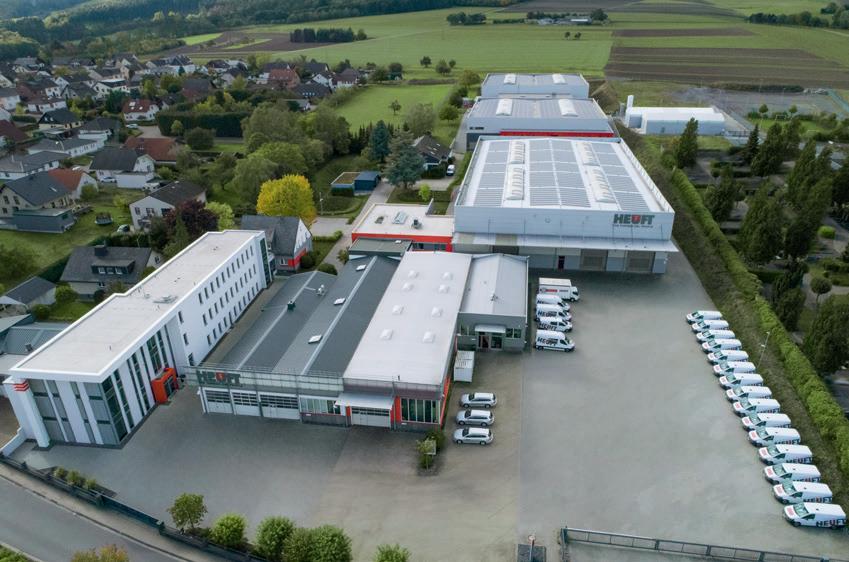
keeps our technology one step ahead. Production capacities can reach tremendous volumes. Each deck can be continuously fed with products via an ingenious but simple table-lift that provides products alternately to each deck. In a different setup, each deck could also receive products from two different production lines and bake just like two independent production lines. Further expansion is being considered. While adding decks at a later time may not always be a viable option because it means stopping the line, the oven can feature built-in additional decks for the future, which can be easily enabled at the appropriate time.
Production capacities can vary broadly: our Euroback multi-deck tunnel ovens, for example, can have up to 12 decks ranging from 3 to 15m, with a step loading system. The total baking surface of this setup can reach 540m². The products are loaded continuously, as they are predominantly part of fully automated lines: the loading system can load the products step by step in each deck or it can be set to load each deck batch-wise. Fewer decks can be used in the case of big product varieties. Different belts can be used, depending on the products being baked: + Hinge plate belt (baking on steel with a baking result that is very close to that achieved with stone baking);
Thermal oil at a glance
+Thermal Oil technology ensures minimal temperature fluctuations in the baking process and leads to absolutely uniform, reproducible quality 24/7, batch after batch. + The small temperature difference between the heat transfer medium and the baking chamber is due to the high heat storage capacity of the thermal oil, which is approximately 2,700 times higher than some other heat transfer mediums such as hot air. With this low
Delta-T, the powerful heat is gently transferred to the baked goods. The result is larger volume, better crust and longer shelf life due to reduced drying of the product.
+ Stone plate belt made from natural granite stone; + Mesh belt with open structure for tins or trays; + Mesh belt with a closed structure for free baked products.
Custom-made ovens are no problem at Heuft. We build an oven for your products and not the other way around! Customizations can include: + Stone belts, hinge plate belts or different kinds of mesh belts are possible choices, depending on the products to be baked. + Separate top and bottom heat; temperature, steam and turbulence zones can be configured individually, to match product requirements. + The very high vertical range of manufacturing – all our ovens are completely built in Germany directly at the Bell plant, including associated components such as central heat exchangers.
Significant savings
The physical properties of thermal oil are the reason for the highest energy efficiency that can be achieved on the market. This results in enormously high energy savings, measured by comparing the heating capacity per square meter of baking surface, which is much lower with a thermal oil oven. Measurable energy savings are at least 25% and can easily go up to more than 40%, depending on the system it is compared with. Additionally, our Energy Management software makes it possible to save even more energy, and with our Bakery Information Center (BIC) the efficiency in the processes can be optimized. At the BIC, we can centralize all baking parameters to help you to reach the highest possible production efficiency. Our energy management system (EMM) is designed for larger installations, where we use more than one heat exchanger. This system can determine the required energy during the production process and can shut down one heat exchanger if its capacity is not needed.
In addition to the savings achieved with the thermal oil technology, we can also recover the heat from the combustion gases and the dampers on the oven, which can be used to heat up water. This hot water is stored in water tanks and can be used for many different purposes such as providing water for your crate washing machine, heating the offices, for cleaning purposes, or for sanitary use.
To assist bakeries to maximize their savings, our Heuft-Energy department will make a projectrelated study and advise how and where energy can be saved.
Baking green
This level of energy savings contributes to significant drops in CO2 emissions and supports process sustainability efforts. With our central heating system, only one burner need to be installed, which further (and significantly) lowers CO2 emissions. A thermal oil oven with a baking surface of around 150 m², working three shifts, will emit more or less 6,000 tons of CO2 less each year.
Be prepared for future energy changes
With our thermal oil system, it is possible to heat the oil with electricity, gas or oil. If in the future it seems that renewable electricity will be much cheaper, you won’t have to change your oven, but just adapt the central heating system!
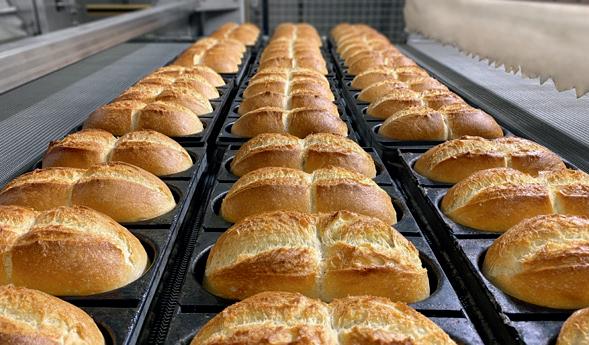
© Heuft Thermo-Oel
ENERGY SAVINGS + Around 6,000 tons of CO2 less emissions per year + Measurable energy savings can range from 25% to more than 40% + The Energy Management Software can contribute to even additionals savings + Heat recovery is also an option
Contact us
Curious to know how much you would save? E-mail us at: energysavings@heuft1700.com