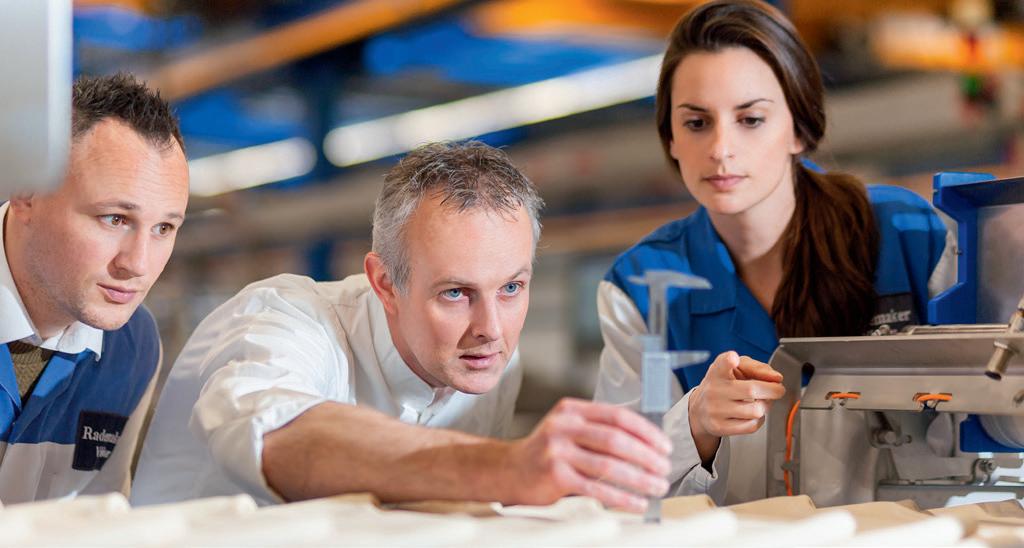
9 minute read
Rademaker B.V.: Training is money well spent
from f2m Automation Book
by landmagd
Rademaker Academy: quality in bakery knowledge
Training is money well spent
+With over 40 years of experience in the development and global supply of industrial food processing equipment and bakery production systems, Rademaker has accumulated extensive knowledge of food products and production technology. Maintaining and sharing this knowledge is the goal of the Rademaker Academy in Culemborg. Kasper Rozeboom, Aad den Braven and Jan Willem Jansen are the driving forces behind the Academy.
Rademaker started its Rademaker Academy in 2015 as an additional service. The aim was to familiarize operators and maintenance engineers with a new production line and to retain and share knowledge both internally and externally via high-level courses and training. This made Rademaker the first producer of food processing equipment to have its own Academy. Now there’s a Rademaker Technology Centre (RTC) in Culemborg, a fully-fledged teaching and training location complete with a teaching room, a practice room with a fully operational two-section laminator and universal line, and a virtual reality lab (VR lab). On-site training is also an option using a mobile VR setup. Rademaker offers basic and advanced training (see box) in both operating as well as maintaining Rademaker machines. The basic training begins with a broad explanation of the machine and focuses on building the basic knowledge of dough technology and production technology required for optimal machinery operation. The advanced training focuses on more specific and in-depth content. On a technical level, the training could address fat pump or dosing
Rademaker B.V.
Plantijnweg 25 4104 BC Culemborg, The Netherlands Phone: +31 345 543 543 E-mail: office@rademaker.nl Website: www.rademaker.com
machine maintenance and in a technological area, training can relate to specific actions in the production process.
Sharing knowledge
Kasper Rozeboom was involved in the Rademaker Academy from the start. He first worked as a technical trainer to train Rademaker production line users. These training courses were a success and it quickly became clear from the growing number of requests that more people were needed for this. As a general trainer, Kasper now develops and delivers the various Academy training courses, together with Aad den Braven, technical trainer, and Jan Willem Jansen, technological trainer. Rozeboom: “With the new, well-equipped location in Culemborg, we have taken a huge step in offering an even better service to our customers. When knowledge is passed on by people who understand the practice, this offers true added value.” Den Braven added: “I sometimes compare it with obtaining a driving license. You can only drive a car as it should be driven if you have a driving license. It’s the same with our machinery. The users obtain their ‘driving license’ at the Rademaker Academy, which ensures that they can operate the machinery optimally in their own environment.”
Jansen: “If a customer’s employee leaves, their knowledge disappears too. New operators don’t always know what they should do if the products that are rolling from the production line no longer meet the required specifications, for example with respect to weight or shape. We help bring their knowledge to the right level. We also use the training to demonstrate to our customers exactly what they may expect from a production line, enabling them to estimate accurately whether they can meet the requirements of their own customers.”
Retaining knowledge
As well as sharing knowledge there’s another reason for the establishment of the Rademaker Academy. “There are many people working within Rademaker who jointly have huge amounts of knowledge and if any colleagues leave, we don’t
Training on offer
A team of technologists and technical trainers developed two training themes that focus on the efficient operation of the Rademaker production lines. Training is given in Dutch, English or German. An interpreter is engaged for any other language.
Basic training
80% of the basic training focuses on production line information and 20% on dough technology. The purpose of this training is to familiarize the team with the production line to ensure a smooth start-up that results in efficient production performance. Up to eight participants per trainer.
Basic operator training
For operators, managers and line managers. Theory: unit descriptions, cascade, synchronization (if applicable), virtual reality training and touch panel explanation. Practical: practice using dough on the line, problem-solving and cleaning training.
Basic maintenance training
For maintenance engineers and managers. Theory: unit descriptions, cascade, synchronization (if applicable), virtual reality training and touch panel explanation. Practical: training in preventive maintenance, controlling transport lines, lubrication, problem-solving and cleaning.
Advanced training
The advanced training covers machinery settings and process interactions. As well as the basic principles of technology and working on product refinement, this also includes production line operation, coordination, maintenance and cleaning. Up to five participants per trainer.
Advanced operator training
For product developers, managers, technologists and line managers. This training focuses on specific units, ingredient information and product and process knowledge and is tailored to the customer. Teams can resolve production line problems after training.
Advanced maintenance training
For maintenance engineers and managers. Customized training that focuses on specific units, electrical systems, the process and advanced mechanical knowledge. After training, teams can resolve the bigger problems and maintain the production line correctly.
COMPANY REPORTS
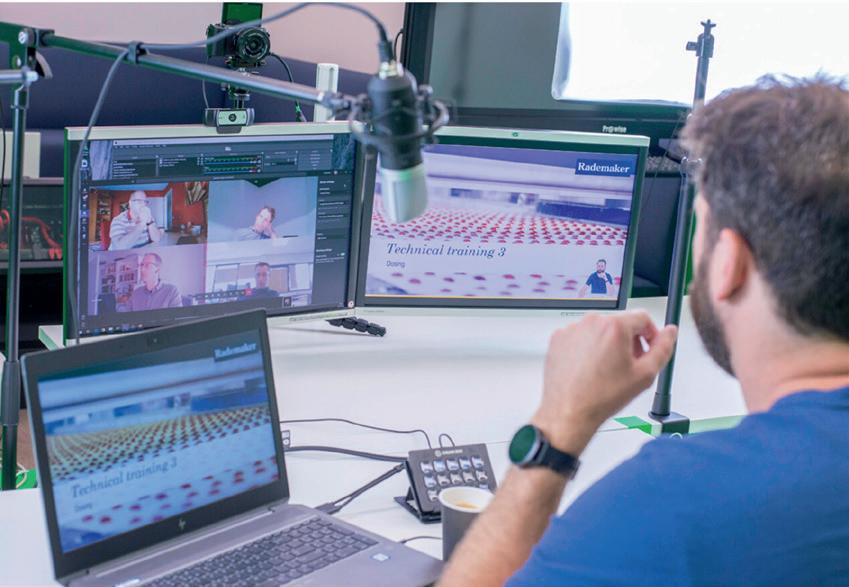
want their knowledge to be lost. By collecting knowledge we can retain this and incorporate this in training that we can then offer at the right time”, explained Den Braven, “and that doesn’t necessarily need to be straight after installing a production line. Our customers can decide to first gain experience with the machinery and study it in more depth later at their own site or our RTC, or they can have their employees trained or retrained. When the engineer installs the machinery, he will give a brief explanation of its operation. During the delivery of a production line, there’s not much time for a detailed explanation and it’s often not the right time as it’s too much for people in one go.”
It’s fine to make mistakes
There’s a practice space in the Academy that can be used specifically for training purposes, for instance, to demonstrate the most important facets of maintenance and production. Rozeboom: “The course participants come to Culemborg, so that they can focus entirely on the training, without the usual distractions present in their own workplace environment. We can explain the essence of a production line perfectly in small groups.”
Jansen: “It’s also a safe environment. This training line’s first production steps match the large production lines that participants use in their workplace. The big difference is that it’s OK to make mistakes. After all, that’s how you learn. Moreover, the small group size means that everyone receives the attention they need. As trainers, we adapt the training to the group’s needs.” Den Braven added: “Our experience helps us in this. All three of us have tremendous practical experience and have rolled up our sleeves and learned on the job. We know exactly who to turn to within Rademaker if we need specific knowledge, which means we always have up-to-date information within the Academy.” This enables us to continue to expand the Academy’s knowledge base.”
VR lab
“We’ve been offering part of the operator training in the form of virtual reality training for the past year,” explained Rozeboom, “a fantastic way
to practice operating a production line reliably without waste or financial consequences. We do this at our Academy in Culemborg, but with a mobile setup, we can offer it anywhere in the world. Initially, it takes a while for people to get used to walking around with a VR headset. Once they are used to it, the participants are all very enthusiastic. We’ll certainly be developing this further.”
“The VR training is also a great interim step to clarify the theory. Participants start with the theory that they can then use ‘in practice’ in virtual reality. After that, they use the knowledge they have gained on the training line in the practice area and then they are ready for the real thing,” stated Jansen. Den Braven added: “This training also has a didactic advantage. Sometimes during production line training in practice, a participant may need to be ‘skipped’ due to time pressure, but with the VR version everyone gets a turn.”
Combining knowledge
Baking is a traditional craft but, following technical developments, it has changed a lot over the years. Jansen: “The range of products across the world is huge and our production lines can do a lot, but basic baking knowledge continues to be important. This knowledge of the craft is increasingly disappearing, but knowing what happens to dough under certain conditions is still needed when making that switch to machinery. This requires knowledge of ingredients and production processes, which is also something we cover in our training. Just like the technical machine aspects for that matter.” The Rademaker Academy trainers have sometimes become aware of friction in this. Den Braven added: “You do sometimes see two camps: operators versus technicians. To optimize the customer’s use of our machinery, it is vital that our training courses are well-aligned. Then operators and technicians strengthen each other and resolve any problems more quickly to keep the machinery running.”
Continued development
The teaching location in Culemborg and the on-site training, with or without virtual reality, provide a firm foundation for the continued development of the Rademaker Academy. Rozeboom: “New production lines are arriving all the time and existing lines continue to be developed. This means that we will need to develop new training and will have to keep adjusting the existing training. The operation screens used in the lessons must always match the screens that customers use in their production lines. Virtual reality will replace some of the theory and practice, and the online training that we developed in connection with Covid-19 is also here to stay. We see these types of training as a fantastic addition to our range.”
Jansen and Den Braven agree that the Academy will increasingly meet demand: “More and more requirements are set for products and, with the right training, we can help our customers meet those requirements,” stated Jansen, “in addition, good training prevents unnecessary production cost increases and retains or even improves production quality. This means that investment in training is money well spent.”
Aad den Braven is a technical trainer and is in charge of developing and delivering the maintenance part of the training. With his extensive experience as a service engineer, he trains colleagues across Rademaker and, together with Jan Willem Jansen, also supports customers on-site, as well as increasingly delivering online training.
Jan Willem Jansen knows everything about the dough processing on the production lines and how to operate these. The teacher training he followed ensures that he is able to optimally ‘translate’ his knowledge of manual food production processes into machine operations. He also thinks it’s important to remove people’s fear of the scale of the equipment.
Kasper Rozeboom is a general trainer, develops new training and coordinates the teaching program. He was the first technical trainer and has also helped to develop the Rademaker Academy in recent years with the teaching and practice areas and the VR lab. +++