
3 minute read
TECNOPOOL S.p.A.: Complete spiral system control
from f2m Automation Book
by landmagd
Complete spiral system control
+Tecnopool has always provided complete services for total processing, which comprehensively cover the entire spectrum of required temperatures, from deep-freezing, cooling, baking, pasteurizing, proofing, to product handling and frying. They are all customized to specific needs, thanks to the flexibility of the spiral design. Tailor-made configurations are essential when referring to a system’s integration/overhauling, as the widths of the belts can vary significantly, with values anywhere from 250mm to 1,500mm, for example.
The spiral is at the core of solutions from Tecnopool, and is built as a flexible and modular system that can support all processes in automated bakery production, from conveying to baking, through to cooling and freezing. Spiral technology can be universally applied and optimized throughout bakery manufacturing processes thanks to its structural flexibility and innovation. Dedicated materials and technical solutions help adapt spirals to perform in all conditions in the production chain.
Comprehensive system diagnostics: the next step
As Tecnopool researches solutions based on real-live production needs that are shared by customers, what defines a ‘complete’ system has been changing along with technology innovation. Built on patented spiral technology, solutions continuously incorporate various new developments to meet the manufacturers’ production requirements. Efficiency is the first priority. To increase production efficiency, “Over the years, the customer has requested an increasingly detailed and complete system diagnostic, so we have implemented the mechanical and electrical control of plants and lines, as well as the related warning and alarm signals,” explains Massimo Petranzan, automatic and electric engineering project manager of Tecnopool.
Moreover, energy efficiency is one of the priorities for bakeries and for Tecnopool. The company’s solutions aim to lower production costs while being mindful of the impact on the environment: innovations provided help save up to 20% in
© Tecnopool
TECNOPOOL S.p.A.
Via Buonarroti, 81 35010 – San Giorgio in Bosco – PD, Italy Phone: +39 049 94 53 111 Fax: +39 049 94 53 100 E-mail: info@tecnopool.it Website: www.tecnopool.it
energy, while still supporting the manufacturing of high-quality products consistently. Similarly, Tecnopool prioritizes sustainability not only for customers, to meet multiplying requests, but also adheres to it for its own operations.
Accurate fine-tuning of all processes + Proofing
Tecnopool offers a choice of two different Air
Treatment Logic solutions: a Centralized Air
Treatment Unit or a precise Zone Management
System, to ensure precise climate conditions throughout the proofing room. 3D humidity and temperature controls grant an optimal climate inside the cabinet and help the customer to handle even the most sensitive product.
+ Cooling and freezing
A dedicated internal software monitors, calculates and optimizes the temperature of each product. Deep freezing can be particularly challenging to maintain within constant settings, in order to minimize the formation of frost. We offer solutions that implement sequential defrosting of evaporators, where each evaporator defrosts autonomously, while the others keep running to allow customers to operate 24/7.
+ Baking
The temperature regulation in individual temperature zones is very precise, with a +/-2°C variation; very accurate and flexible baking temperature regulation is possible, even down to the level of a single baking deck, both by deck length and height.
Under development, always
Tecnopool creates bespoke designs with innovations and features uniquely applied to the customer’s production needs and plans. The core spiral technology and all auxiliary components have been continuously developed over time. Research and development receive 10% of the company’s turnover to achieve continuous innovation. Some of the newest updates the company provides include the addition of checks on the mechanics of the machine to detect any malfunctions, effectively preventing potential breakdowns and downtimes that might occur if repairs were needed. Another tool, particularly useful in present circumstances caused by COVID-19 measures, and a necessary step up going forward, is remote assistance. “We have inserted a remote assistance system that allows us to assess the status of the machine remotely. This system also allows us to record the variations in the machine’s parameters at a distance. Recorded alert events provide valuable information to help us understand how the machine is working and to intervene where necessary.”
+++
Tecnopool TP FOOD GROUP: World leader in the design, manufacturing and installation of equipment for complete production lines, covering food industry heat treatments during all stages of processing: proofing, baking, cooling, freezing and pasteurization, from -40°C to +300°C, with infinite fully customizable layout configurations. Tecnopool TP Food Group is positive and determinate about its future, driven by the strength of six leading worldwide recognized companies. Constant commitment and ambition will be the leitmotif for continuous growth, to remain on the leading edge of a constantly evolving market.
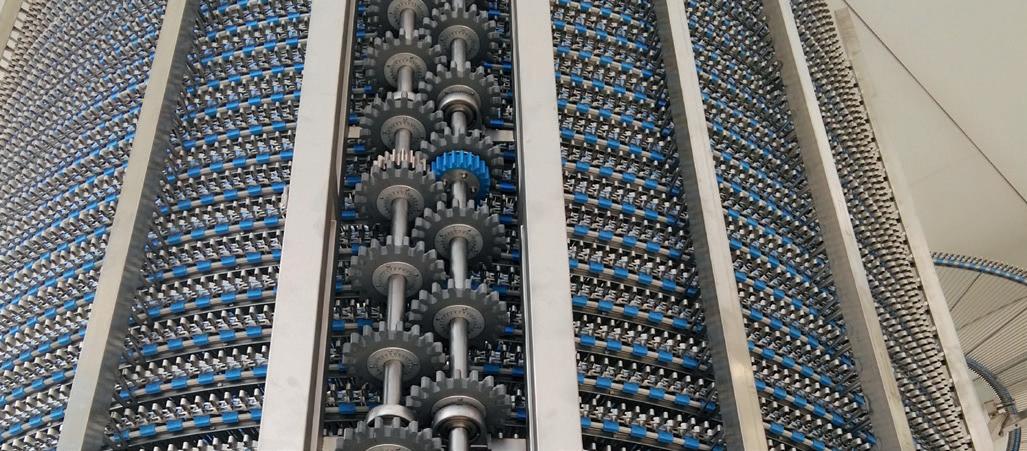
© Tecnopool