
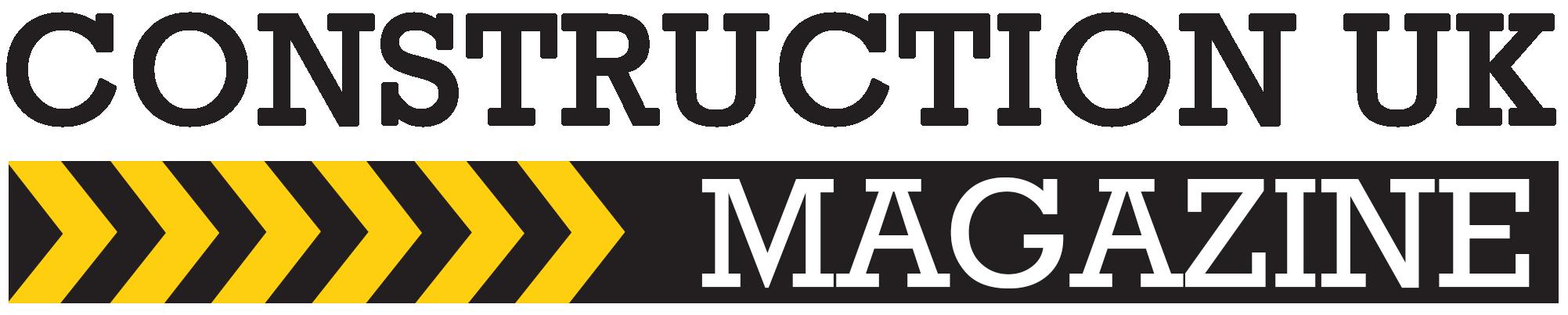
Aston Villa has released a host of new CGI images to illustrate their vision for the future of Villa Park.
This comes as the club announces that they will submit a planning application for the redevelopment and expansion of the stadium at the end of August 2022.
The £100m first phase plans will pave the way to create a world-class sporting venue, increasing the stadium’s capacity from its current 42,785 to more than 50,000. The move follows a public consultation that ran in June and July, in which nearly 10,000 residents and businesses, stakeholders and fans had their say on the plans.
Aston Villa CEO Christian Purslow said: “Following a successful consultation period, we are pleased to announce that we will be submitting our proposals for the redevelopment and expansion of Villa Park at the end of the month.
“We have received a hugely positive response from the local community, our supporters and other stakeholders and are confident that this project will transform both the stadium and the local area.
“These new CGI images showcase our spectacular vision for Villa Park which includes a brand-new commercial destination, Villa Live and high-quality public space for the community. We look forward to continuing to work with all partners to realise our future vision.”
Triton Construction has completed a multimillion pound contract to deliver a new 80,303 sq ft Sure Store facility in Wokingham. The contract for expanding self-storage company, Flexiss is the third for Triton following the successful delivery of new build facilities in Wigan and Ashton-Under-Lyne.
The project represents the first venture for Flexiss in partnership with the Industrial Property Investment Fund (IPIF) for Legal & General which owns and funded the development. The partnership seeks to identify and build out best in class facilities with Wokingham being the
in 2016 by industry entrepreneurs Mike Wilson and Andy Wood, Flexiss is a managed storage
group offering traditional storage and business start-up support services under the Sure Store brand. It already has ten stores in Bolton, Cannock, Northwich, Bury, Lichfield, Stafford, Wigan, Burton, Manchester, and Ashton-Under-Lyne and has plans to expand further with sites acquired in Southport and York as well as
the demolition works of an existing unit on the 1.5-acre site on Molly Millars Lane to deliver a new fourstorey modern facility to the same design criteria of the Wigan and Ashton-UnderLyne sites that Triton delivered last year. Working alongside architects C4 Projects, Triton provided full design, construction and fit out services as well as external car parking and landscaping.
Chris Quinn, Regional Director at Triton Construction said, “We are pleased to complete our third contract with Sure Store which is proving successful in its UK extension. Our credentials in building storage and warehouse facilities that stand out from the ordinary are strong and we look forward to working with Sure Store to deliver further new developments.”
Triton Construction is a £65 million turnover company providing design and build, civils, fit out and refurbishment services. Established for more than 16 years it employed over 80 people across offices in the Northwest and Yorkshire.
Its commercial portfolio includes Big Yellow, Production Park, Econ Engineering, Kemira Chemicals, Gordon Rhodes Foods, Chancerygate, Tech Folien and Home Bargains.
Other project highlights for Triton include the ongoing Premier Inn hotels, a new testing facility for British institution and gear engine pioneer David Brown Santasalo, and the sensitive refurbishment of the iconic Royal Liver Building in Liverpool.
Our credentials in building storage and warehouse facilities that stand out from the ordinary are strong and we look forward to working with Sure Store to deliver further new developments.
Kier has been awarded a contract by Camden and Islington NHS Foundation Trust to deliver a new £17m mental health facility at 1 Lowther Road in Islington, London.
Appointed through the Procure Partnerships Framework, the project forms the first integrated community mental health facility in the Trust’s St Pancras Transformation Worksprogramme.include
the demolition of the existing facility on site and construction of a new four-storey building which will include stateof-the-art facilities. The new space will provide interview, counselling and treatment rooms, and agile workspace for staff as well as a café and group collaboration zones. There will also be a ‘pocket’ park to support visitor and staff wellbeing.
With the project set to achieve BREEAM excellent standards, the environmental efficiency is a key focus of this scheme. Key features include curtain walling with bolt on solar shading to prevent heat gain and reduce the demand on mechanical ventilation systems. There will also be 70m² of solar panels on the roof of the building to support renewable energy being used when the building is operational.
The new partnership with Node will see the firm deliver 63 luxury apartments in Brixton, with premium views across London.
the development of a fifth additional floor containing 6 additional luxury apartments. The penthouses will boast premium views across the capital city with a number of iconic buildings in sight, including The Shard, The City, Canary Wharf, Big Ben and the Palace of SpeakingWestminster.onthe
Enrok Construction has commenced work with Node to deliver 63 one-andtwo-bed luxury apartments in Brixton, TheLondon.construction
specialist has worked
on the project since March 2022 and is now able to announce the formal contract. In a short time Enrok has played a pivotal role, completing roof works, installing windows and commencing the cladding and internal fit out, and is now committed to the successful completion of the scheme.
In its entirety, the project will see the conversion of a four-story building on Shakespeare Road with work to include
project, Simon Bennett MCIOB, Enrok’s Operations Manager, commented: “We have been working closely with the team at Node for four months now, and it’s great to be able to shout about what will become our flagship project. Building outwards is not always feasible in high-density areas, so developing upwards is an effective solution – and something that is becoming increasingly popular across London and other densely populated cities where space is at a premium. Working in London does come with its own challenges, but our project planning and existing presence in London has enabled us to hit the ground running on the scheme and we are looking forward to delivering it successfully. We hope that this marks the start of a strong working relationship with Node and very much look forward to the prospect of future collaborations.”
Increasing environmental responsibilities and sustainability targets are driving the construction industries ongoing needs for cost effective, easy to use solutions for dealing with wastewater onsite. Sites need quick replies, concise information, simple transactions and deliveries without hassle. For the past 9 years Kelly Tanks has enjoyed providing all of these whilst building a large customer base, expanding their team and facilities, and responding to customer demand with innovative new products year on year.
Mark, Kelly and team KT provide a selection of Water Treatment and Concrete Washout Solutions for hire or purchase. Their popularity and proven track record is a result of providing the kit you need, in the manner you want, at a price you’re happy with. Match this with their eager to please attitudes and above and beyond aftercare and its easy to see why their customers keep returning.
Various concrete washout solutions, to allow concrete trucks and equipment to be washed off safely onsite, including closed loop washwater recycling, washwater filtration sacks, pH correction, robust washout trays and skip washouts.
Self contained units or full systems to separate and treat wastewater and Water Quality Monitoring Systems including Settlement & lamella Tanks, flocculation and pH adjustment dosing, pH/TSS/ Turbidity remote monitoring, auto desludging.
Water Treatment Solutions for high alkaline hydrodemolition waste, used to retain solids and automatically correct pH.
Automated daily prevention for concrete drum build-up. Using recycled or fresh water the highly efficient electric driven pump combined with the water jets at the tip of the boom remove the days build up before it hardens. DrumBlaster Build-up Control Technology incorporates an extendable boom with a rotating head allowing the mixer drum to remain stationary.
Tailor made solutions to suit all applications. Whether an idea or a full plan, we can accommodate. We can also tweak our existing products and/or have them sprayed in your corporate colours.
Complete onsite Water Management. Consultancy, Testing, Supply, Install and Maintenance.
KEY BENEFITS YOU CAN EXPECT FROM KELLY TANKS EQUIPMENT:
• Designed to meet the rigours of the construction industry
• Fast and Simple to Set up
• Small Footprint equipment available
• Units can be linked to handle range of flows, pumps sizes & particle characteristics
• Easy to Maintain and Monitor equipment
• Reduce off-site disposal costs
• Reduce risk of pollution
• Easy to use equipment
Kelly Tanks take pride in the quality of their products and have a classy approach to customer service making them a real pleasure to deal with. For further info give them a call on 01889 508944, email info@kellytanks.co.uk or check out their website www.kellytanks.co.uk.
Independent qualification guarantees highquality technical advice.
Members of British Gypsum’s Technical Support team have successfully completed a leading industry qualification on designing buildings to minimise the risk of fire.
The 14-strong team has achieved the Institution of Fire Engineers (IFE) Certificate in Passive Fire Protection, a universally respected, industry-standard course aimed at professional fire engineers and those who carry out fire assessments on
are believed to be among the first employees from a construction product manufacturer to complete the course, reflecting British Gypsum’s commitment to ensuring the highest levels of knowledge and expertise among its staff.
Training for the IFE Certificate was delivered by the Association of Specialist Fire Protection (ASFP) and included content around general fire protection as well as plasterboard systems. Completion of the training means that the British Gypsum team is equipped with specialist knowledge and is better placed to advise its customers.
David Robinson, Head of Technical Support at British Gypsum explained: “It is vital that anyone involved in a construction project is totally clear when it comes to the required performance of systems and products.
“As a business, it is important to us that our team is highly trained and qualified to give advice relating to safety-critical design. The IFE Certificate in Passive Fire Protection is a great way for them to demonstrate the level of knowledge and expertise they have developed around fire protection and general fire design,
A home counties-based social enterprise, which provides training and employment opportunities for young people in the construction industry, has secured a £900k project for its eco-house building division from affordable housing provider Fairhive following a £200k cash injection from Reward Finance Group.
New Meaning Construction, a licensed builder of the Beattie Passive low carbon housing system, is expanding its capacity to meet the increased demand for its services to deliver more new homes. In addition to the latest contract, it has recently successfully completed ecohomes for Vale of Aylesbury Housing Trust and Warwickshire Rural Housing Association, as well as several private developments.
A cash injection provided by Reward Finance Group through its Business Finance product has been instrumental in driving forward New Meaning’s business by providing the company with a flexible working capital facility, which it can use for the procurement of building materials to enable housing projects to commence.
New Meaning Construction was originally created as a spin-off of the training company founded in 2006, New Meaning Training, which helps young people find their strengths and develop the confidence and skills to earn their own living, primarily in the construction sector. Through its five training centres, the programme works with around fifty students every year, with some going on to secure full-time employment and developing a career in New Meaning’s construction division.
David Lett, co-founder and joint-CEO of New Meaning Construction, said: “Our recent Beattie Passive House projects have attracted strong interest from social housing providers keen to create low carbon, highly energy efficient homes for their residents, so it is tremendous that we can now unlock our potential for growth through this new funding. In fact, without having the working
and it gives our customers confidence that they can continue to trust our guidance.
“This training not only ensures that our team is competent to an independently recognised standard, but also gives them confidence in their own abilities. It is a further example of how British Gypsum continues to push the boundaries in terms of technical advice.”
For further information about British Gypsum https://www.british-gypsum.com/visit
capital facility in place with Reward, we would not have been able to win our latest new contract.
Working with Reward was very easy, and they were absolutely true to their word. Everything that they said would happen, happened, and they took the time to understand our business and do their due diligence, which I believe is crucially important. I don’t often say this about a finance provider, but I really feel like Reward have got our back.
Alan Sanderson, senior relationship manager at Reward Finance Group, added: “Given how the building industry is having to adapt to address climate change and spiralling energy costs, as well as deal with widespread skills shortages, New Meaning Construction is extremely wellplaced and capable of meeting an emerging demand for sustainable new homes. We are pleased to be able to provide David and his team with a flexible working capital facility that means short term hurdles needn’t stand in the way of their long-term growth plans.” COURSE
Tellon Capital have appointed Henry Construction Projects Limited as the main contractor for the construction phase on their site at 40 Broadway in the heart of Westminster.
The 40 Broadway site originally comprised a mid-1960s office building at 40/48 Broadway with large car park, 1920s “warehouse” style building at 1/11 Carteret Street and a further 1980s office building at 13/15 Carteret Street.
Tellon secured planning permission in 2018 for a redevelopment.comprehensiveThescheme proposes complete redevelopment to create a distinct office building providing approximately 135,000 sqft GIA of new high quality bespoke accommodation in this sought after location. The scheme includes a series of terraces at various levels with views across St James’s Park.
Demolition of the existing buildings is now nearing completion and Henry Construction Projects Limited have been appointed for the construction phase to bring the proposed plans to reality from the end of October.
Tellon Capital was established in 2014 and via the acquisition of high quality investments patiently unlocks asset potential and has developed a reputation for delivering high level returns through innovative and well executed asset management initiatives.
James Burchell, a partner at Tellon said “We are excited about delivering a top quality ESG compliant office building in this prime location and are thrilled to have appointed Henry Construction Projects Limited to be our main contractor for the construction phase at 40 Broadway. Their focus on delivering many services in-house means we can deliver a scheme of the highest standards. We look forward to working with them”
Henry is one of the UK’s leading construction firms. Their focus is on using traditional building techniques and modern methods of construction and can now deliver between 50-70% of the trades in-house.
Mark Henry, Director of Henry Construction Projects Limited said “We are delighted to have been appointed as main contractor for the construction of new offices at 40 Broadway. We look forward to delivering a high quality scheme in a prime location.”
In previous decades when energy costs were affordable, we heated our poorly insulated buildings in winter and then switched on air conditioning in summer to keep them cool. The extensive use of fossil fuels to heat and cool our properties has contributed to placing us on a global warming roadmap which we are now eager to apply the brakes, if we can find them in time!
Whilst we generally think that a Passivhaus design building maintains a comfortable internal environment given the colder zones of the northern climate, the reverse is also true. Utilising colder evening temperatures in hot climates to cool the structure, internal temperatures can be kept at a comfortable level during the hottest of days.
There are five key elements to understand about Passivhaus before starting to look at the technical requirements. First and foremost, Passivhaus is fundamentally about integrated design where the whole building team are involved at the outset. Whilst it may seem that Passivhaus is designed just for colder climates, the second key element is information about location, as a well designed Passivhaus structure can now effectively be installed anywhere in the world. Orientation, the third key element, has a part to play in ensuring that solar heat gains are minimised. The fourth key element is the building form; whilst a Passivhaus construction can take any form, physics confirms that a convoluted shape with a resulting greater surface area for a given space, will likely allow for more heat transfer through the building fabric. Finally, the fifth element is that of the construction methodology itself. Passivhaus maintains a fabric first approach and whilst any material can be utilised, the focus on airtightness and thermal insulation are paramount. Thermal bridges are to be avoided at all costs to maximise insulation at critical points of the structure. In Passivhaus, it is the building fabric design that HELPS PASSIVHAUS KEEP ITS COOL’
does all the heavy work of maintaining a steady, comfortable internal temperature.
Whilst ‘Passivhaus’ is commonly considered as a German innovation, in fact, it was an American physicist, William Shurcliff who in 1982 published a book “The Saunders-Shrewsbury House,” in which he describes the concepts of “superinsulation” and passive solar as “passive house.” In the late 1980s a passive house movement had emerged in North America, but, shortly after America lost its appetite for energy conservation and Germany picked up the reins. German physicist Wolfgang Feist refined the passive house concept to further improve efficiency and proposed a passive house concept with an annual energy demand of just 15 kilowatthours per square metre of floor area.
Members of the UK Passivhaus Trust, Aluprof’s class leading MB-104 window and door system has gained the Passivhaus Institute Darmstadt certification. The MB-104 Passive Aero has excellent thermal insulation performance for an openable window system with a Uw as low as 0.53 W//m2K and for a door with a UD as low as 0.62 W//m2K.
As the UK has recently seen temperatures reach 40º Celsius, many of our buildings fail to cope with keeping internal spaces at a constant comfortable and safe temperature. It is estimated that there are currently around 2,000 heat-related deaths in the UK every year with a further 10,000 deaths due to the cold. With increasing extremes of weather, these figures will likely increase over time. Keeping our buildings within a temperature comfort zone throughout the daily and yearly cycle will ensure a safe and healthy environment is maintained for occupants.
Designing high insulation wall elements can be relatively straightforward, but when these elements are perforated by windows and doors, robust detailing is needed to minimise thermal bridging and maximise air tightness. Window and door systems chosen must offer the highest levels of thermal insulation including the adoption of triple and quadruple glazing. Few systems meet these high performance characteristics, most are supplied by aluminium systems companies with wide, high performance thermal breaks. Aluprof, one of Europe’s leading aluminium systems companies, offer a range of systems that can be specified by architects to meet the requirements of Passivhaus design.
Members of the UK Passivhaus Trust, Aluprof’s class leading MB-104 window and door system has gained the Passivhaus Institute Darmstadt certification. The MB-104 Passive Aero has excellent thermal insulation performance for an openable window system with a
Uw as low as 0.53 W//m2K and for a door with a UD as low as 0.62 W//m2K. With glazing widths up to a class leading 81mm in thickness, doors can also be assembled into panel doors as well as fully glazed
Whilstoptions.high performance curtain walling, windows and doors can greatly assist in thermal insulation, especially when specified with high performance glazed units, it should be remembered that there are also additional products that may be used to enhance thermal stabilisation of a building space. Solar shading, or brise soileil, can offer sun shading of glazing helping to reduce solar gains. Solar shading can take the form of fixed louvres or external Venetian or roller blinds. Enhancing thermal insulation, roller shutters can be added at the design stage to external window reveals, furthermore, shutters can also offer enhanced building security, especially at ground floor level. Aluprof offer a wide range of additional products that can be discussed as options during the early design stages.
At the design concept it is crucial that the right product is specified along with detailing to ensure that the building will meet Passivhaus standards. Aluprof can assist in product choice, often tailoring the system chosen to offer the best specification for its location. The technical team at Aluprof can also offering assistance in the reveal detailing, which will minimise thermal bridging in the interface between the building fabric and window
up the Aluprof Office at the Business Design Centre in London, the company has rapidly grown their specification influence in the UK with their high-performance architectural aluminium systems. Further expansion of the company’s headquarters in Altrincham now provides specifiers with meeting facilities and an extensive showroom of commercial systems to view.
Further information is available on the company’s website at aluprof.co.uk or direct from their UK head office in Altrincham on 0161 941 4005.
Aluprof can assist in product choice, often tailoring the system chosen to offer the best specification for its location.
Technical innovation has taken insulation products, PIR panels in particular, to unprecedented levels of thermal performance and usability. For instance, the precision-cut tongue-and-groove joint that features on all four edges of Recticel’s rigid full-fill panel, Eurowall®+ ensures the boards lock tightly together, minimising heat loss through thermal bridging. The panel is capable of achieving a U-value of 0.18 W/m2K in a traditional 100mm masonry cavity wall, with the 10mm gap making for a more convenient fit for installing bricklayers.
In terms of flat roofs, the development of single-layer tapered insulation systems - such as those supplied by our tapered insulation division Gradient - have advanced the performance of flat roofs by providing a quicker, more accurate and flexible way of achieving of thermal performance combined with a degree of fall for roofing projects.
Whatever the benefits of certain products, long-term thermal performance requires good planning and specifying a suitable insulation system for a property to achieve the required U-value.
The importance of maintaining good practice in respect of U-value calculation should not be underestimated. Failure to comply with standards during the process potentially jeopardises homeowner safety, results in higher fuel bills and is damaging to the environment.
outcomes with an energy consultant who can give advice based on the Standard Assessment Procedure (SAP). With this methodology, the thermal ratings of walls, floors, roofs, junction details and any renewable technologies are put into a metaphorical mix, the performance of which must correspond with or exceed the required regulations for the building. These elements can be changed, as long as the property achieves the required dwelling performance. The alternative to carrying-out the SAP assessment is to work on the notional dwelling specification, which has to be followed as a minimum to achieve a pass. Working to backstop values only, however, will result in Pre-installationfailure.
good practice includes a contractor carrying out a survey of the building itself. Issues can occur when the insulation system is ordered on the strength of the architectural drawings, but it transpires that the property is constructed differently.
Prior to installation work, basic care and attention should be paid as to how materials are stored. For pitched roofs or floor applications involving Eurothane GP boards, if left loose-laid unfixed in cool temperatures there is potential for the boards to warp due to the differential floor-air temperature. Although extremely rare, this generally occurs when the temperature is about 5-degrees or lower. Installers should therefore ensure all boards are laid as close to the screed/slab installation as possible.
Correct product selection is another ‘best practice’ essential for installation preparation to pay-off in the form of a well-insulated, thermally-efficient property. The Code for Construction Product Information (CCPI) will assist in improving this process by helping manufacturers drive higher standards in the presentation of building product information. Recticel is a huge advocate of this initiative, which prioritises building safety and quality. Setting out a product’s terms of use and intended outcomes clearly will not only inspire confidence in the user, it could help close the muchmaligned performance gap and ensure properties are built as-designed.
When it comes to achieving U-values for domestic new-build projects it is a requirement to discuss stipulated
Trusted, reliable manufacturers such as Recticel remain focused on improving levels of insulation performance to not only uphold their industrywide reputation for quality and ingenuity, but to help create a healthier, more sustainable built environment for generations to come. It is proof that best practice permeates every aspect of our culture, including our ideology.
Trusted, manufacturersreliablesuch as Recticel remain focused on improving levels of insulation performance to not only uphold their industrywide reputation for quality and ingenuity, but to help create a healthier, more sustainable built environment for generations to come.
Growing urbanisation and increasing population levels in urban areas are spawning increasingly stringent noise and vibration standards and regulations. As a result, there is higher demand for high quality and sustainable sound and vibration insulation systems (suitable for internal or external sources in each building).
Amorim Cork Composites has just launched Acousticork by Amorim - a new product range of cork-based materials, providing sound insulation and impact noise control in buildings. Cork, a 100% natural, recyclable and reusable raw material, combines the high technical performance that is required by the market, with the sustainability credentials required to guarantee the future of cities.
Noise pollution is a serious environmental problem in European cities that has been recognised by the World Health Organisation. However, since this is not a new problem, the construction industry has been looking for solutions to combat noise over recent decades and cork is an old ally in this context.
To understand why, we must look closer at this raw material: cork has a microscopic cellular structure that resembles a beehive, filled with an air-like gas, and primarily coated with suberin and lignin. The high gas content in each cell explains cork’s extraordinary lightness.
Studies indicate that for each ton of cork produced, the cork oak forest can sequester up to 73 tons of CO2*, and thus helps to reduce the Global Warming Potential. But nature is just the starting point. The fact that this material is a natural carbon sequester has a positive impact on the construction industry, one of the world’s most pollutant industries.
The association of these cells, as if they were a small set of cushioned pads, explains the cells’ compressibility and elasticity. These characteristics also mean that cork has exceptional performance in terms of sound buffering, that depends on the existence of pores and gaps in the connections between materials. Sound buffering causes sound energy to dissipate, in the form of mechanical waves that circulate inside. Cork is a good option for any building application where such characteristics are valued, for example: control of vibrations in buildings, or insulation against sound transmission.
In response to this need, the Acousticork by Amorim range offers efficient and more environmentally friendly solutions, such as cork-based underlayments, underscreeds and materials for vibration control.
Produced using the best sustainability principles, the Acousticork by Amorim underlayments offer high performance, protect the building's floor and guarantee the ability to withstand high and variable loads. When installed under a floor, the underlayments provide greater comfort, protection and longevity, whether for ceramic, wood, LVT or laminated floors.
a resilient layer applied to the floor between the structural slab and the screed during the construction process. This range offers resilient layers made from natural and recyclable materials, that improve quality of life and work
Anotherenvironments.application in which cork is equally valued is in vibration control materials, which isolate the sources of vibration in buildings, due to the decoupling of the elements. When applied consistently throughout the building, these materials significantly improve quality of life and extend the equipment’s working life.
Studies indicate that for each ton of cork produced, the cork oak forest can sequester up to 73 tons of CO2*, and thus helps to reduce the Global Warming Potential. But nature is just the starting point. The fact that this material is a natural carbon sequester has a positive impact on the construction industry, one of the world’s most pollutant industries.
The Acousticork by Amorim range combines performance with longterm sustainability, not only due to its negative carbon footprint, but also due to the circular principles on a daily basis, transforming what was previously considered to be surplus production into new solutions, capable of responding to the world’s most demanding industries and enhancing the natural characteristics of our sustainable raw material – cork.
In addition to the underlayments, the Acousticork range also includes underscreeds - an ideal product to meet the most demanding acoustic requirements. Intended to reduce the propagation of impact noise and improve the acoustic insulation of buildings, an underscreed is information
A new net zero carbon project has started in Wales this month - with sustainability and environmental impact key.
Two new business units will be built at Treowain Enterprise Park, Machynlleth, by contractors SWG Group.
The company is using designs and materials that are sustainable, robust, low maintenance and durable ensuring minimal maintenance required to ensure the project has a net zero carbon footprint.
Instead of Ordinary Portland Cement, SWG is using Ground Granulated Blast Furnace Slag (GGBS), a by-product of iron and
steelmaking and so has virtually zero CO2 associated with it, and fibres will be used as alternative reinforcement products instead of steel bars and mesh, again reducing CO2
there will be air permeability testing and thermal modelling carried out to ensure all materials used will satisfy regulations for building, glazing and doors.
Jacqui Gough, Director at SWG, said: “We are thrilled to be working with the Welsh Government to deliver this exciting and important project. SWG Group put sustainability at the heart of our business and already have plans and procedures in place
to ensure our projects are as sustainable as possible.
Leading wet civil engineering firm, Land & Water, is set to start a six week project at Polson Bridge on the Devon, Cornwall border starting this month. The contract is part of the Environment Agency’s ongoing work at a weir on the River Tamar adjacent to the bridge.
The work will involve the rebuilding of a failed stone wall, dewatering of the working area and important focus on control of the water quality throughout.
For centuries, Polson Bridge was the main entry point into Cornwall and, since the
addition of Launceston’s dual carriageway bypass, is now just a few hundred metres from the current A30 route.
Fiona Moore, Divisional Business Manager at Land & Water, said: “We are extremely excited to be delivering these works alongside the Environment Agency in the Devon and Cornwall region.
Land & Water will be working collaboratively with the Project Manager within the Environment Agency and their team to ensure procedures are adhered to and the surrounding area is protected as much as
The work at the site in Powys started on August 15 and will include one unit of approximately 620m² floor area including mezzanine for single occupation. The other unit will be divided into two equal units each with a floor area of approximately
as the building work, SWG Group will also create car parks, paths, landscaping, drainage and services
the project is achieving carbon zero status is by SWG encouraging car sharing and using a vehicle tracker system to monitor speed and distance travelled of low emission company vehicles to reduce carbon footprint.
Once completed, the new units will be rented to local businesses.
possible. Once we have finished at Polson Bridge the works will help to protect this important Gauging Station for years to come and protect the natural river banks from further erosion”.
This project not only takes that one step further by being zero carbon, but it will also have a huge impact on the local economy and employment options. We are excited to make a difference in Machynlleth like this.
Belfast Harbour has welcomed Belfast City Council’s decision to grant planning permission for a new high quality logistics warehouse facility located at Westbank Road on the Harbour Estate.
With sustainability at its core, the development of the new 50,000 sq ft warehouse represents an investment of £9m and will include provision of high efficiency chilled and ambient warehouse space with 17 loading docks, over 40 HGV parking spaces, and parking provision for both cars and bicycles.
The site on Westbank Road is in close proximity to the Port’s RoRo ferry terminals, providing unrivalled operational efficiencies for the occupier for freight travelling to and from GB and further afield.
The high-quality specification and occupierled design of this new facility will allow for flexible use of the space, as well as energy and cost-efficient operations for users with the development being constructed to a BREEAM ‘Excellent’ rating.
With the volume of RoRo traffic moving through Belfast at an all-time high, the recent investments made by the Port in terminal infrastructure and StenaLine’s addition of new ships serving NI to GB routes, makes Belfast Harbour a compelling location for logistics operators. Opportunities exist for the development of further warehousing capacity in this location for operators seeking to leverage the competitive advantage of the location.
The central location within Belfast Harbour, flexible leases and the connectivity of the location are key attractions and by putting sustainability to the fore of the development offers occupiers warehousing solutions that are net zero carbon ready.
Work has started on the third phase of housing development at Birtley, Gateshead.
Part of a project which has already delivered 194 homes at The Sycamores and The Aspens, the third phase, the £17.5 million Cedars, will provide 73 two bedroomed, three and four bedroomed homes of which 49 will be for private sale and 24 for shared ownership with partner Home Group.
The development is part of a £350 million, housing led regeneration initiative being driven by the Gateshead Regeneration Partnership (GRP).
GRP comprises Gateshead Council, construction and regeneration specialist Vistry Partnerships North East and Home Group, one of the UK’s largest
housing associations. Its vision is to create over 2,000 new homes on 16 sites across the borough, that offer exceptional space standards, energy efficiency and value for money.
To date the partnership has delivered over 450 homes, on eight developments. As well as improving housing quality and choice, the initiative is providing opportunities for local business and people to thrive through job and training opportunities – a minimum of 25% of which go to local people - and an economic uplift – a quarter of the supply budget is committed to businesses within the borough.
The first residents at The Cedars are expected to move in during the summer of 2023 with the development expected to be completed in early 2025.
Minimising thermal bridging at the wall connection to the floor, or floor slab, is an ongoing problem with reinforced concrete construction, However, a dedicated new solution – the Sconnex type W – has been developed by Schöck and is being installed in what is currently the largest Passivhaus accredited social housing scheme in the North of England. The ‘Greenhaus’ nine-storey development of 96 affordable homes in Chapel Street, Salford, is part of the 50-acre Salford Central regeneration and the result of a collaboration between The English Cities Fund (ECF) – a national development partnership between Muse, Legal & General and Homes England –contractor Eric Wright Construction and Salix Homes. The scheme focuses on sustainability and is designed to reduce the energy consumption of the building. With Passivhaus, energy savings can be as much as 90% compared with the average building stock and more than 75% compared to average new builds.
The unique Schöck Sconnex type W makes a major contribution to achieving this initiative and is a product based on derivative technology from Schöck. Sconnex utilises the company’s longstanding expertise in structural thermal breaks for balconies and other cantilever constructions and applies it to reinforced concrete wall and support applications. By installing the Sconnex product in Chapel Street, thermal losses are greatly reduced and the surface temperature in the rooms increases to considerably more than the critical dew point temperature. Heating costs are lower, a pleasant room climate is created and the linear thermal
transmittance (Psi) of the connected reinforced concrete wall is reduced by as much as 80%. This outstanding insulation performance is combined with an excellent load-bearing capacity. It transmits very high pressure, tensile and shear forces, in the longitudinal and transverse direction, made possible by the use of a pressure buffer consisting of ultra-high performance fibre reinforced concrete. Compressive strength levels in excess of 175 N/mm2 are achieved, with extremely good flexural strength. A further important benefit is the significant cost reduction involved when compared to installing insulation beneath the floor slab.
Eric Wright and Salix have key roles
Greenhaus forms part of ECF’s wider £1bn, 50-acre, Salford Central masterplan transforming former surface car parks and derelict buildings into a vibrant and diverse community. John Hartnett, managing director at Eric Wright Construction, comments: “We are proud to be supporting
not only a green future for Salford, with the delivery of high efficiency buildings built to Passivhaus standards, but also supporting Eric Wright’s own journey to net zero carbon. These new homes will deliver valuable social housing in partnership with Salix Homes.“
Sue Sutton, chief executive at Salix Homes, also adds: “Chapel Street enjoys an incredibly rich history and the innovative Greenhaus development marks the next exciting chapter for this historic part of Salford. At a time when affordable housing is in such short supply, we’re very proud to work alongside our partners to deliver these high quality, sustainable, eco-homes of the future, and we look forward to seeing this ambitious development take shape on the Salford skyline.”
ChapelThe scheme focuses on sustainability and is designed to reduce the energy consumption of the building.
Tilbury Douglas, a leading UK building, infrastructure, engineering and fit-out company, has successfully completed construction schemes at The Ladder School and Walsall Studio School, both located in Walsall.
Awarded by the Department for Education under the DfE 2017 Construction Framework Medium Value Band, the two separate schools will be operated by The Mercian Trust, which is a diverse multi-academy trust bringing together different schools catering to a wide range of individual needs.
Designed in collaboration with Race Cottam Architects, The Ladder School is an entirely new build campus; providing alternative provision for young people in the Walsall area who are at the risk of exclusion from mainstream education. The new two and three storey building offers up to 112 students in Key Stage Four and post 16
education a high-quality performance and a digitally rich industry-led learning
site, Tilbury Douglas has completed the construction of the extended accommodation for Walsall Studio School. The school offers a bespoke curriculum designed to engage students on a fouryear professional journey that allows them to thrive in the creative, digital and health industries. The new building will provide dedicated and specialist space to further this Overwork.theduration
of the project, Tilbury Douglas exceeded their social value targets, achieving over £2.7m in social value pounds (according to TOMs Framework metrics). The comprehensive social and sustainability plan focussed on harnessing local SME
supply chains, undertaking community work and providing T-level placements for students at Walsall College and Dudley
Midlands Regional Managing Director of Building – at Tilbury Douglas, commented: “As an experienced contractor within the education sector, we are proud to have successfully delivered two important projects that will positively impact on students within the local community.”
Chris Bury, Principal at The Ladder School, said: “From the start of construction, the Tilbury Douglas team engaged with us well, answered our questions and regularly invited us to site to see the progress. Since moving in the team has been supportive to ensure there was no delay in opening the school for students. We have been blown away with the effort Tilbury Douglas has gone to, to turn drawings and ideas into our school that will transform young people’s lives!”
The biggest annual event for construction in Kent is nearly here.
On Thursday 6th October, everyone who’s anyone in construction will be descending on the Kent Event Centre in Detling. The Kent Invicta Chamber of Commerce event, running for over 14 years now, provides a valuable platform for the entire construction industry, for open conversation, collaborative working, education, new faces and opportunities.
The Kent Construction EXPO attracts around 2,500 visitors each year and delivers a full day of educational and inspirational speakers, ‘meet the buyer’ sessions, round table discussions and the opportunity to wander exhibition halls filled by over 150 different businesses from across the supply chain.
The opening keynote is being made by Roma Agrawal, the structural engineer responsible for the Shard’s spire, with her speech ‘Breaking the Black Box’ of engineering technology.
Local industry heavyweights including Baxall, Jenner, Bauvill, Kier, Willmott Dixon, DHA Planning, Lee Evans Partnership and Clague Architects will be there, as well as clients, consultants, educators and building control officers, looking to keep themselves updated, seeking inspiration and taking the opportunity for interactive and free speech on topics such as building sustainably, new building regulations and digital construction.
The opening keynote is being made by Roma Agrawal, the structural engineer responsible for the Shard’s spire, with her speech ‘Breaking the Black Box’ of engineering technology. Also speaking is government advisor on the golden thread and The Building Safety Act, Bola Abisogun OBE, and circular economy expert Duncan Baker-Brown of Baker-Brown (architects).
To see the full line up of speakers and the list of exhibitors attending the Kent Construction EXPO, visit the website here - www.kentconstructionexpo.com
The event is all about promoting knowledge and collaborative working. With developers, designers, contractors, surveyors, consultants, product manufacturers and many more attending this event, businesses from all over Kent are given a brilliant opportunity to develop through being informed and meeting new business contacts, thanks to the Kent Invicta Chamber of Commerce.
Whether you’re interested in new technology and products, searching for a specialist contractor, or needing inspiration for your next construction project, the Kent Construction EXPO is the place you need to be on Thursday 6th October.
Silica is found in construction materials
– Natural stone, sandstone, bricks, clay, and concrete products. It is even found in some plastics as silica is used as a filter during the production process.
What is silica?
Silica is a natural compound and has multiple uses in the construction industry.
However, exposure to fine silica particles vary between distinct types of materials with fine dust remaining in the air from many different working activities. For example:
• Quarrying and stone processing - Rock drilling, blasting, breaking, crushing, and screening
• Stone production (particularly on sandstones as they are made-up of around 70% silica) into architectural masonry, cladding, traditional masonry blocks, and natural walling stone
• Refractory production, cutting, polishing, and finishing products
• Concrete product and manufacturing and production
• Demolition processes where encountering concrete, natural stone, brick, mortar, plaster, roofing products are prevalent
Be informed about the effects of breathing silica dust.
Workers do not have to get sick when
working with materials containing silica. Silica related illnesses are 100%
steps to prevent exposer while working around construction products include:
• Using the correct responsive respiratory protective equipment
• Wear a face mask, and protective clothing
• Use blasting cabinets and proper ventilation
• Use wet production methods when cutting, or grinding products
• Limit the time you work in duty production environments
• Follow good personal hygiene rules:
• Do not eat or drink in dusty workrelated areas
• Always Shower and change clothes after work to prevent taking dust particles home
So, know the hazards and take precautions to avoid exposure.
Remember, continued exposure can lead to developing health complications including, silicosis a long-team lung disease caused by inhaling fine crystalline silica dust over many years.
It is the responsibility of employers to provide a safe working environment for all employees.
If you find yourself in a workplace or working on construction sites where you are working around products that are known to contain crystalline silica there are health and safety training programmes that you can sign-up to.
Essential Site Skills offer extensive workplace health & safety training courses including our popular Face Fit Train the Tester course that provide those who are required to wear responsive respiratory protective equipment, the knowledge of how to conduct face fit testing using Qualitative method. If you are responsible for health and safety within your organisation, then it is essential that face fit testing is conducted correctly, and documented evidence is
Allrecorded.ESSface
fit testing and train the tester courses are delivered by our Fit2Fit accredited tutors.
If you want to know more about our Face fit and related Health and Safety courses
Asbestosincluding:
Awareness UKATA Control of Substances Hazardous to Health (COSHH)
Risk Assessment Training Non-Licensable work with Asbestos category/face-fit-testingGo(UKATA)tohttps://essentialsiteskills.co.uk/
The lead contractor behind the redevelopment of Birmingham’s iconic Alexander Stadium is reflecting on the success of the project and the wide range of community benefits brought to the local area following its recent completion.
McLaughlin & Harvey has detailed the outcomes of its social value programme which was implemented over the course of the redevelopment in a report, including impressive local job creation figures, ethical procurement, and a range of community partnerships.
A total of 370 jobs were created and sustained throughout the redevelopment of the stadium over the last two years, as well as a total of 35 apprenticeships, work placements and internships, and 756 weeks’ worth of vocational training.
58% of employment was created for those living within 30 miles of the site, and an
impressive 334 members of the workforce were upskilled throughout the course of the project.
91 community and education groups and over 600 school pupils have been engaged throughout the redevelopment, and £80,000 of community investment, both financial and in-kind, was achieved.
McLaughlin & Harvey recently won the Inspiring Change in the Community Project Award for their Employment & Education Academy initiative on the project, which addressed the employment and skills gap by removing inequalities and barriers in employment and education.
Judges at the Inspiring Change Conference & Awards, organised by CECA, praised the contractor for their outreach to local ‘hard to reach’ community groups, which ultimately led to 48 new entrants to the industry, including 26 long-term
and working with
local suppliers was also key to McLaughlin & Harvey’s social value programme. 50% of project spend was with local businesses and in total the social value programme generated £21.5m of local economic value.
Martin Keys, Operations Director at McLaughlin & Harvey, said: “The greatest
challenge faced was ensuring the project ran to time and budget. This was achieved amidst a world health pandemic and a global shipping crisis - to name a few – thanks to the collaboration, engagement and one-team approach from all partners involved.
“Alongside this excellent achievement, today’s report also highlights the real benefit we have brought to local communities here in Birmingham, both engaging with young people and hard-to-reach groups, encouraging them into work and bringing a lasting legacy to the area, which as a business, we are very proud of.”
The £72.4m stadium redevelopment project was part-funded by West Midlands Combined Authority (£25m) and the Greater Birmingham and Solihull Local Enterprise Partnership (£20m), with Birmingham City Council providing the remainder of the funding.
Cllr Ian Ward, Leader of Birmingham City Council, said: “Anyone who visits the venue knows what an amazing job our contractors have done on the redevelopment of the Alexander Stadium – which is now the undisputed premier athletics facility in the “Butcountry.the
community story is just as impressive. McLaughlin & Harvey told us they would be good neighbours and project partners and they backed up their words with a really impressive programme of community engagement and support for grassroots projects not only in Perry Barr, but right across the city. They’ve set a standard for other firms working on projects for the council to meet.”
Andy Street, Mayor of the West Midlands and WMCA chair, said: “We invested in the stadium redevelopment because we knew that it would provide a world class sporting facility for the region and enhance our reputation on the global stage. Anyone can see the contractors have certainly delivered on that.
This project also creates a social legacy as we can see with hundreds of quality construction jobs and training opportunities created and supported through the pandemic and engagement with the community including local school children who will be inspired by their experiences for years to come.
Anita Bhalla, Interim Chair, Greater Birmingham and Solihull Local Enterprise Partnership (GBSLEP) said: “After successfully completing the redevelopment of Alexander Stadium on time and on budget, this latest report highlights how McLaughlin and Harvey also managed to deliver a wide-ranging and impactful community engagement
“Increasingly,programme.socialvalue
is at the heart of how we measure our GBSLEP investments like the £20 million that went into this City Council project. We recognise how critical it is that local people feel the benefits of the major developments that are happening on their doorstop. This contributes to driving inclusive and sustainable economic growth across our region and for all our communities.”
The report can be viewed at pdfalexander-stadium-social-impact-report.www.mclh.co.uk/media/6076/mclh-https://
Profile: Martin Keys, Operations Director, McLaughlin & Harvey
Martin Keys, Operations Director at McLaughlin & Harvey, a privatelyowned contractor with 170 years of experience in civil engineering and the built environment, played a key role in the recent redevelopment of Birmingham’s Alexander Stadium.
Martin, who has been with McLaughlin & Harvey for 20 years after originally joining the team as a graduate in 2002, led the team of 20 throughout the two-year long, £72m project, which saw the stadium transformed with the construction of a new west stand, new north and south bowl seating, and the installation of the World Athletics Class 1 facility including a new 400m six lane warm up track and relaying of a new 400m nine lane competition standard Worktrack.
commenced in May 2020 after the contract – which was supposed to be finalised the week the country went into a nationwide lockdown – was put on hold while discussions were held on how the project could be safely and effectively delivered during this period of such Unsurprisingly,uncertainty.additional time was required, and the original proposal was re-worked significantly to allow for ongoing restrictions and enhanced health and safety measures as per Government guidelines.
Martin oversaw the implementation of all Covid mitigation measures such as split team arrangements and regular on-site testing, and believes this stringent approach is largely to thank for not a single outbreak of the virus occurring on-site throughout the build Covidperiod.was
not the only obstacle encountered during the redevelopment of the Alexander Stadium. As well as a global pandemic, the last couple of years have also seen a shipping crisis, hyperinflation, trade barriers as a result of Brexit. Lorry strikes and resource problems in the job market.
Martin said: “If you think about every possible challenge you could come up against on a development – we faced pretty much all of them. There was a range of supply issues with certain materials coming from the USA and China, and as a result of the shipping crisis, certain shipments were stuck in various ports which caused delays and had a knock-on effect when it came to things like installing certain parts of the stadium at specific times for optimal weather conditions.
It was incredibly challenging, but we just took each obstacle as they came and devised strategies to counteract every problem we faced and ensured our contingency plans were delivered effectively.
“The success of the project was a result of the ‘one-team’ approach we took, making sure everyone involved was on the same page and working towards one common goal. Open lines of communication were key and I wanted to make sure everyone’s input was heard and valued so there was a strong sense of teamwork rather than an individual or siloed approach.”
Discussing the technical aspects of the project, Martin said: “Building a stadium is more technically challenging than lots of other types of developments due to the intricate details and precise coordination required to make sure each step was taken at the right time. The Alexander Stadium was a particularly unique design.
“Seeing it all come together once the redevelopment was complete was a huge honour. I’m really proud to have been part of the team that brought the stadium to life. We overcame so many challenges and everyone stayed focus on the end goal throughout. It’s a great feeling to see all the years of hard work come to fruition.”
In an increasingly connected digital world, data centres are critical. With 3.6 million m² in use by data centres in Europe alone and over 70 projects (851,000 m²) in progress in 12 European countries (ResearchAndMarkets), their growth continues to accelerate to meet the needs of cloud technology, AI, 5G,
Internet of Things (IoT) data storage and the shift to hybrid working. This trend is mirrored globally, with investment in data centres projected to rise from $244.74 billion in 2019 to $432.14 billion in 2025 (ResearchAndMarkets ).
Safeguarding Service. Eliminating Downtime.
To ensure 24/7 365 operation and minimise the risk of downtime, data centres are constructed with the highest performance, highest quality building materials available, with every part of a facility meticulously
planned. Infrastructure is an integral part, normally comprising of an Uninterruptible Power Supply (UPS), power distribution, cooling systems, fire systems and security systems, many of which have redundancies (2N+1 for Tier 4 facilities, guaranteeing 99.995% uptime) including back-up power generators to prevent interruption of service. Two contemporary products being adopted by leading data centres across the globe are Fibrelite’s lightweight FRP composite trench access covers (to protect and provide easy access to underground infrastructure) and KPS’ HDPE piping (to fuel backup generators).
High-Performance Backup Generator Fuelling Systems.
A reliable fuel supply is key to backup generators’ smooth operation, connecting generators to fuel storage tanks and tanks to fill points. Nicolas Lefebvre, Generator Activity Manager at Flipo-Richir (France) commented “We regularly install generators to back up data centres in the event of a power cut. We have been using KPS double wall piping exclusively for more than 10 years to connect generators to underground storage tanks.
KPS piping is easy to install, mainly thanks to the assembly by thermo-welding, and the range of products is very complete, which makes it possible to create any type of network, even complex.
Corrosion-resistant, safe and easy to install (due to compact electrofusion fittings) the KPS HDPE piping system helps fuel flow safely, even providing protection against ground movements (using the elasticity and flexibility of HDPE). Safety can be enhanced further by installing KPS’ conductive piping option, ensuring continuous conductivity between the tank and the end of the line (which can be earthed). This helps to prevent the accumulation of electric charges that could otherwise be created by the friction of the fuel velocity and the plastic inner surface. KPS’ 4” (110mm) piping also delivers a 933 litre/minute flow rate, making it ideal for fill lines (KPS piping is available in 1” to 4” diameters in single or double wall). KPS will also soon be releasing a 6” double wall product range.
Simple, Safe Underground Infrastructure Access.
Another contemporary product line seeing widespread global adoption by architects, design engineers and specifiers to enable easy access to underground infrastructure is Fibrelite’s modular FRP composite
trench/channel access covers. These are now often specified at the outset of new build data centre projects. Bespoke, modular and lightweight, Fibrelite covers are designed to be removed quickly and easily by two people using Fibrelite’s ergonomically designed lifting handles, even where heavier load ratings are required (e.g. channels running between buildings with vehicle traffic). Due to their unique custom engineering capabilities, Fibrelite can manufacture access covers at all load ratings up to F900 / 90 tonne (A15, B125, D400, E600 and F900). Traditionally, for the past 100 years, access covers have been made from concrete or metal which are 3-4 times the weight of Fibrelite covers, often requiring specialised lifting equipment to remove and replace. Fibrelite covers are also impervious to corrosion and have a unique anti-slip walking surface.
In many instances where Fibrelite access covers are adopted, companies choose to specify a bespoke option, custommanufactured to specific requirements including size, colour, load rating, fittings (e.g. securing systems) and moulded identification of below ground services. Fibrelite has also undertaken projects where they have designed and manufactured retrofit replacements for previously installed heavy concrete or metal access covers.
“We are proud to be involved in data centre projects across the globe, with our Fibrelite trench access covers facilitating easy safe access to below ground infrastructure, and our KPS piping providing a reliable fuel supply to backup generators. In many cases, we actually custom design and engineer bespoke products to fit each facility’s requirements.”
- Jo Stott, Marketing Director, OPW Global (a Dover company and parent company of Fibrelite and KPS).
KPS’The fastest-growing security company in the UK has once again been recognised for its industryleading standards with a gold accreditation from Constructionline, the country’s most connected and progressive provider of procurement and supply chain management services.
Swindon-based SSGC was awarded with the highest honour from the coveted platform following a deep dive examination into its policies and Theprocedures.goldstatus demonstrates to potential buyers on the platform that the organisation has been subjected to increased scrutiny around governance and risk management.
David Stubbs, CEO of SSGC, said: “The gold status really demonstrates our commitment to carry out all facets of work to the highest standards and our dedication towards the industry and its
management, the best possible terms of employment for our staff and ensuring our suppliers adopt to our inclusive culture is something we take great pride in here at SSGC, so we are thrilled that our practices and procedures are being recognised on such a national scale.”
To secure the accreditation, the team had to demonstrate excellence through a rigorous process of validation checks, within environmental management, quality management, equal opportunities, modern slavery act adherence and anti-bribery and corruption policies.
SSGC was also able to showcase the business and its team met the requirements of an extended verified pre-qualification questionnaire including equalities and diversity, environmental management and quality management.
Another great achievement for the construction industry, Chris Yates, CEO at FFX (Folkestone Fixings Limited) has picked up the prestigious award of ‘CEO of the Year’ from The Business Magazine. Selected from a list of top 250 privately owned companies in the Surrey, Kent and Sussex regions, the award is sponsored by BDO, CMA Recruitment Group, HSBC, Irwin Mitchell and Zeus.
Chris Yates was delighted to receive the award on behalf of FFX. “This award really reflects the efforts of the entire team at FFX to service Trades Persons throughout the UK. It’s been a pleasure to lead them to achieve so much.”
“As leaders, we owe it to ourselves to help others because you don’t always know what skills your business will need next. Our company has tripled in size over
the last 10 years and we have the same people in the same jobs but doing more, so we have invested in management development as well as training and coaching our people to be successful.”
“I am also grateful to our customers. These highly skilled Trades Persons make an enormous contribution to the UK economy and we hope to continue providing them with the tools they need for years to come.”
Construction work has started on a new eco-friendly residential affordable housing scheme for people over the age of 55 in Penshaw.
The scheme, which has been named Penshaw Gardens, will feature 72 selfcontained properties over three storeys, consisting of one and two bedroom
Penshawapartments.Gardens, situated off Station Road, is being developed by regeneration specialists, Vistry Partnerships North East, for Sunderland-based housing association, Gentoo Group.
The Vistry and Gentoo partnership will see a brownfield site redeveloped for affordable housing that was previously used for office space by Sunderland City Council.
The building is eco-friendly and will feature renewable energy technology, such as air source heat pumps. The building will also be built without a gas supply, minimising its carbon emissions.
The site features a walled garden, which will also be restored and brought back into use alongside the new apartment complex.
Properties in the building will be modern and extremely spacious, meeting nationally described space standards (NDSS). There will also be free on-site parking, including electric car charging points, and an internal buggy storage area with direct access into the building.
All 72 properties will be made available for affordable rent via Gentoo’s usual Homehunt allocations system. Affordable rent is a formula set by central government and is 80% of the local market rent.
It’s a big year for Flannery Plant Hire – 2022 marks their 50th anniversary. Many ingredients have contributed to the resilience and success of this family run company, including their belief in putting people first and the importance of lasting relationships.
The relationship between Finning, Cat, and Flannery Plant Hire goes back to
2008 and is closely linked to their shared focus on customer service excellence and the power of innovation.
The Cat machines that Finning UK and Ireland supply have been at the forefront of digital machine technology developments over the past two decades, with Flannery investing more than £146M in the last 2 years alone.
Chris Matthew, Flannery Plant Hire’s Strategic Manager, points out: “Without sacrificing performance metrics, the industry’s emphasis on sustainability and carbon reduction is well served by the Cat portfolio of machines.
“It’s not yet available on every construction site but keeping operators safe and well by any means is key, and Flannery will continue to explore and invest in machines that support this.” MACHINERY
“Operating a digger remotely was considered the stuff of sci-fi only a few years ago but it is now a reality, as demonstrated by the latest Cat Command technology.
Planning permission has been granted on a new manufacturing facility in Scotland – producing HVDC cables for what will be the world’s longest subsea infrastructure for the Morocco – UK power project. The infrastructure forms part of an ambitious initiative that will power seven million UK homes by 2030.
Leading independent property, construction and infrastructure consultancy Pick Everard has been acting as lead consultant on the project, appointed by HVDC subsea cable manufacturer XLCC.
The new facility, in Hunterston, North Ayrshire, will produce four 3,800km long cables, connecting solar and wind energy all the way from the Sahara to the UK, as part of the Xlinks project.
Once operational, the brownfield site is expected to support up to 900 jobs, with thousands more generated in the wider supply
Santoshchain.Patel, director at Pick Everard said: “We’re excited and proud to be involved in creating a new high tech green industry for the UK and supporting the drive towards Net Zero. From a manufacturing perspective, it will see undersea cables created to a length not previously seen, while consumers
will be able to benefit from a much lower unit cost for their energy once the project is fully implemented. Net zero requires huge expansion of solar and wind to be a success, and XLCC stands to help deliver in this respect.”
XLCC’s manufacturing operation in Hunterston will meet the UK’s growing demand for high-voltage, direct current (HVDC) power transmission.
Landowners at Hunterston have thrown their support behind the scheme, with work transfer opportunities expected to be provided for local employees, following the decommissioning of Hunterston’s B power nuclear station after 46 years.
Seventeen modular low-carbon homes are to be built in the South Downs National Park in West Sussex – nine of which will be for affordable rent or shared ownership.
The homes have already been manufactured offsite in Dorset by offsite building specialists Rollalong and they will be transported and installed on site in the autumn.
The site on land south of Heather Close in West Ashling near Chichester is allocated for housing development in the South Downs Local Plan. Planning permission for the development was granted by the Planning Committee for the National Park Authority, following a Planning Committee meeting in October 2020.
West Ashling will be a flagship landled development and Rollalong’s first on behalf of its parent company, the Newship Group, which owns a number of packaging, construction, manufacturing and premium hire
Upskilling the next generation of construction workers has been the central focus of the delivery of the new Showtown – Blackpool’s first museum – with contractor, Conlon Construction, ensuring local youngsters play an integral role in its completion.
The £13million attraction, which will be located in the heart of the seaside town, has seen a wealth of regional
construction suppliers – including James Mercer Group, Chris Bowker Electrical and LN Joinery – come together under Conlon’s lead to enable young people the opportunity to learn key skills on site as part of apprenticeships, T Levels and HNC qualifications.
In total, 11 students have been involved in the landmark project, which Bamber Bridge-based Conlon says will play a big role in ensuring the local construction talent pipeline is armed for years to Showtown,come.
due to open its doors in spring 2023, is a vital regeneration project for Blackpool, and is set to welcome 290,000 visitors each year offering a significant boost to tourist numbers and economic growth.
Jamiebusinesses.Turpin, Construction and Development Director at Newship Group, said: “West Ashling is a great rural residential scheme and the perfect development opportunity we’ve been seeking to combine our current ideal blend of scale and location. There has long been a shortage of modest new homes in the favoured western sector of Chichester and the addition of 17 new homes will help support the local housing
currently working closely with South Downs National Park Authority to fine-tune the sustainable approach on construction, material selection, drainage strategy and hard/soft landscaping designs. We look forward to getting the scheme under way in the coming months.”
Rebate amounts for CIS-registered workers in the 2021/22 tax year, initial data indicates that rebates amounts are on average 17% higher than pre pandemic levels, according to specialist construction accountancy firm, Brian Alfred.
New data linked to the tax bills of selfemployed construction workers suggests the sector is on track to return to prepandemic levels of activity.
Tax rebate firm Brian Alfred, which specialises in looking after workers who are Construction Industry Scheme (CIS) registered, has revealed that initial figures indicate self-employed construction rebates are around 17 per cent higher than pre-pandemic, with their average client looking set to receive a tax rebate of more than £1,600 from the current tax year.
That’s an increase from an average rebate of £1,370 in 2021 – partly due to reduced incomes because of COVID working restrictions, and the added complexities of the government’s SelfEmployment Income Support Scheme (SEISS), which was deemed as taxable income by HMRC.
The data also highlighted how more than 90 per cent of Brian Alfred clients look set for rebates so far, which is a significant increase on 2021 when just 69 per cent of workers were due rebates.
Stephen Chapman, Senior Tax Manager at accountancy firm, Brian Alfred, said: “We’re optimistic about the figures we’ve seen so far in relation to the rebate positions of the CIS-registered workers we
processed hundreds of selfassessment forms and the data shows a clear increase from the average figures from the 2020/21 tax year, when we really saw the impact of COVID on the construction sector and self-employed workers within it. This suggests that the sector is returning to the kind of levels of activity we saw before COVID arrived. We will continue to monitor these figures as the year progresses but it’s encouraging to see the numbers so far, and we hope the trend continues.”
Although some workers did receive a rebate in the 2020/21 financial year, there were others who received nothing at all, and in some cases owed money to HMRC due to the impact of the government SEISS grants.
Insights found that for the 2018/19 and 2019/20 tax years – before COVID working restrictions and support schemes were introduced – the average rebate amount was £1,590 for those eligible for one.
Any money claimed through the various SEISS grants were classed as taxable income by HMRC, which saw many of those who typically expect a tax rebate at the end of the financial year instead faced with a surprise tax bill.
Stephen added: “Those that received a SEISS grant in the 2020/2021 tax year will have seen the erosion of rebates – or a tax bill that would not normally be expected. This was compounded by the fact that expenses were likely to be much lower due to less work taking place throughout
our construction workers to prepare their SATR well in advance to understand what they might owe to HMRC, with the impact of SEISS being relatively unknown for many. However, there were still many who left their self-assessment submission until the last minute. Many of these people had no idea that they would owe money to HMRC, and therefore weren’t prepared for potential bills.
The majority of self-employed construction workers in the UK are CIS registered, which means deductions of 20 per cent to their earnings are made at source. This money is then passed onto HMRC to count as payment towards tax and National Insurance contributions.
These workers must then submit an annual self-assessment declaring all earnings and expenses, and this often results in a tax rebate being paid back to them.
“Thankfully, we’re seeing a return to more normal rebate amounts this year, and this is positive for self-employed construction workers, many of whom rely on their annual rebate to fund other things.
“However, our advice is still for people to get their returns in early to understand what kind of rebate they might be due, and also to ensure they work with specialist accountants to maximise what they can legitimately claim back and stay on the right side of HMRC and the law.”
For more information about Brian Alfred and the CIS, visit www.brianalfred.co.uk SELF-EMPLOYED
Thankfully, we’re seeing a return to more normal rebate amounts this year, and this is positive for selfemployed construction workers, many of whom rely on their annual rebate to fund other things.
Every season presents its own unique challenges when it comes to maintaining the health of your property’s drains - and winter is arguably the most challenging season of all. With plunging temperatures, heavy rainfall and ice damage around the corner, it is important to ensure that your drains are properly prepared for winter.
Whether you are a homeowner or a business owner, you will need to know how to keep your outside drain pipes from freezing, and how to keep your wastewater systems flowing clearly. If you do not take the right precautions, pipes and drains can become prone to cracking, bursting and blockages during winter, resulting in flooding and costly damage to your property.
In order to help prevent the risk of frozen pipes in winter, Lanes has put together this
AliMet Fabrications has become a member of the Automatic Door Suppliers Association (ADSA) –opening doors to a key market segment for the supply of door sets and entrance requirements.
Winter Drainage Guide, explaining all of the steps you can take to keep your property’s drainage safe against the harsh effects of the winter weather.
How does winter weather affect pipes and drains?
As water freezes, it expands. It’s a simple rule that holds true even when water is contained within a pipe, and the expansion of the liquid as it solidifies can place considerable pressure on the structural integrity and stability of the pipe.
As such, when sub-zero temperatures hit, it can create a range of problems for your property. Frozen masses can create stubborn blockages within the pipe, preventing water from moving through the system and leading to indoor flooding. At worst, the pressure created by the frozen water will crack and burst the pipes,
leading to much more significant property damage that can be extremely costly and time-consuming to repair.
The problems caused by blocked and damaged pipes will be aggravated by the amount of rain and snow that tends to fall in winter, as well as the presence of dead leaves, branches and other debris clogging up the system. By failing to prepare your pipes and drains properly for the cold weather, you could be at risk of a waterlogged property with serious structural damage, at a time when the weather outside is at its worst.
How to prepare your property against burst drains and frozen pipes this winter Preparing your property for a forthcoming cold spell is vitally important, but fortunately isn’t too difficult. Taking precautions against winter weather should be a top priority for any home or business
Tim Moore, AliMet’s Technical Sales Consultant has been actively involved with ADSA for more than 20 years - including two as its chair. He is keen to ensure that AliMet benefits from industry guidance and support.
“The automatic door industry is a significant part of our customer base. We regularly undertake door, window and screen fabrication for a number of leading manufacturers and smaller companies, so it makes sense for AliMet to become an ADSA member and be more directly involved.
“ADSA is at the forefront of maintaining quality and safety standards and training. We intend to keep on top of changes that relate to our customers to ensure that we can respond to their needs.” he said.
AliMet, which is based in Bridgnorth, Shropshire, will also be taking advantage of ADSA member benefits including technical and industry updates and resources to support business operations.
Website: www.alimet.co.uk
ahead of harsh winter weather, but is particularly essential for properties with:
• Outdoor taps
• Swimming pool houses
• Water sprinkler apparatus
• Pipes in areas of the property that aren’t heated, such as garages, outhouses and lofts
By taking the following easy steps, you will be able to protect your pipes from freezing or bursting this winter:
Make sure any drips and leaks have been repaired
As winter approaches, it pays to take a look around your property to inspect all of your taps and amenities, in order to check for any existing leakages on your property. If you find any, these need to be fixed immediately, as this will waste water and increase the likelihood of pipes
can sometimes be patched up using a patch kit, but in most cases it is easier and safer to use the services of a professional - especially if the damaged pipe services your heating or water mains.
You should drain all of the water from pipes that service outdoor water-based appliances that are not going to be used in winter, taking the instructions provided by the manufacturer into account. As a rule, this can be done by shutting off the main water connection to the relevant tap, and then allow the water to run until there is none left.
Antifreeze is not a prerequisite, as these chemicals can damage pipelines and the environment. If you have any hose pipes
located in unheated or outdoor zones of your property, these should also be drained and stored in a warmer area of your home. If you have any taps in these areas, the indoor valves should be closed, but the outdoor ones should be left open; this will allow the water to expand safely, thanks to the lack of pressurisation.
Insulating your pipes ahead of the winter will help protect them from freezing, while delivering the additional benefit of reducing your energy expenditure.
Insulation is one of the best and most affordable ways of guarding against frost damage to any pipes, drains, cisterns and other water-containing structures that are going to remain in use throughout the winter. Circular polyethylene insulation can be quickly and easily wrapped around any at-risk piping, and is available from any good DIY store, while heat tape or cable also works well for thinner pipes.
Insulating your pipes ahead of the winter will help protect them from freezing, while delivering the additional benefit of reducing your energy expenditure.
Clear out your drains and install drain protection
The quickest and easiest way to make sure your drains are operating at peak efficiency over the cooler months is, quite simply, to clean them. Remove any leaves, mud or other detritus from the grate to stop any potential freezing and blocking of your drains.
It can also be a good idea to purchase and fit a drain protector, made out of a nonfreeze plastic, to help stop any more dead leaves and other debris from entering the pipes.
One of the most common reasons why pipes tend to get damaged during winter is the fact that many property owners choose to switch their heating off while it is not in use. This increases the risk of the pipes freezing over, but this can be avoided by simply keeping your heating on at a low level throughout the winter
to protecting the pipes, this is also unlikely to result in a higher heating bill, as stop-start periods of heating and sudden cooling will require more energy than maintaining a steady, lukewarm
your property from draughts Small gaps between masonry or under doorways, particularly in the garage, can quickly cool down and freeze any at-risk pipes in the home. Plug these up using insulation, wood or plastic, in order to ensure these draughts do not contribute to the risk of frozen pipes.
Bear in mind that you should avoid accidentally blocking any exterior vents, such as those connected to the heating system, unless you do not plan on using this appliance at all over the winter.
The easiest way to make sure you have properly prepared for all of the risks winter can bring is to arrange a professional drain inspection. By calling on expert drain surveyors, you will be able to establish whether your pipes have any preexisting leaks, damage or blockages, and ensure they have been properly cleaned out to get them into the best possible working condition.
By getting in touch with Lanes, we will be able to thoroughly check the condition of your property and take any actions needed to address any current maintenance issues. We will also provide you with recommendations and guidance on any additional steps you can take to keep your home guarded against frozen water damage this winter.
Taking a vigilant approach to protecting your property means you will have no regrets during the chilliest time of the year. To find out more, just give Lanes a call on 0800 526 488 - we can be reached 24 hours a day and seven days a week.
The specification and installation of a new replacement rainwater system at a London primary school had to be cost effective whilst offering high performance and exceptional aesthetics. Brett Martin’s Cascade cast iron effect rainwater system was up for the challenge, offering period styling without compromising on drainage performance.
Forming part of Brent Council’s school expansion programme, Fryent Primary School in Kingsbury is one of three primary schools being refurbished and transformed with new-build modular extensions incorporating classrooms, kitchens and multi-use halls. As part of the refurbishment of the existing period building, Brett Martin provided the architect and contractor with full on-site technical support, as well as recommending a cost-effective rainwater solution which had the look and feel of the existing cast iron system, but offered the long-term benefits of plastic.
The architect Peter Balham attended the Brett Martin CPD ‘Specifying Appropriate Rainwater Systems to Achieve Your Architectural Vision’ which became the catalyst for the specification of the Cascade system. Brett Martin met with the architect, providing samples and together had the product approved by the school governors and the London Borough of Brent.
We had been looking for an authentic and costeffective cast-iron replacement for the main school building for some time and Cascade was far and away the best choice when compared to other rainwater systems and offered by far, the most comprehensive range to accommodate both the domestic and industrial scaled requirements on this project. It’s a quality, high performance product with period-style detailing that looks perfect and will protect the building against the ingress of water.
Following a site visit and a take-off being carried out, the architect’s specification included a comprehensive range of Cascade cast iron effect rainwater systems in a range of domestic and high capacity systems, all in Classic Black. The installation saw the 112mm Roundstyle gutter and 68mm round downpipe installed at the east end of the main entrance block.
For the larger roofs across the other school entrances, rear and inner courtyard, play area and classroom dormer, the 115mm Deepstyle and higher capacity 170mm Deepstyle gutter systems were used to offer increased roof drainage. To deal with rainwater run-off from the flat roofed buildings surrounding the courtyard and astroturf play areas, the 105mm round and 100mm x 75mm rectangular downpipes and undated hoppers were installed.
Commenting on the specification, architect Peter Balham said: “We had been looking for an authentic and costeffective cast-iron replacement for the main school building for some time and Cascade was far and away the best choice when compared to other rainwater systems and offered by far, the most comprehensive range to accommodate both the domestic and industrial scaled requirements on this project. It’s a quality, high performance product with period-style detailing that looks perfect and will protect the building against the ingress of water.”
Significantly lighter than cast iron rainwater systems, Cascade is much quicker, easier and safer to install at a height and helped to offer the local authority huge savings in terms of on-site installation costs which was a key consideration during the approvals
a variety of projects from domestic new-build and refurbishment projects, church and barn conversions, Georgian and Victorian shop frontages, flats and apartments, schools and hotels, the Cascade system has been designed and developed by Brett Martin using over 60 years’ experience at the forefront of plastics technology and a unique patented manufacturing process to achieve the authentic cast iron finish.
With the refurbished building and modular extension now completed, Brett Martin’s Cascade cast iron effect rainwater system has ensured an architecturally-sympathetic appearance was achieved with a reliable, durable and cost-effective drainage system that will continue to perform for many years to come.
To find out more about Brett Martin visit: www.brettmartin.com
A fully comprehensive and inclusive nationwide consultancy service bringing together the planning, design and building of your project from inception to completion. We work nationally with a single point of contact.
Deep professional knowledge, combined with the network and connections that come from significant industry experience. Working with you, we can identify the right combination of services to configure a ‘dream team’ that will achieve the most effective and efficient outcomes. By retaining all these services under one roof and tailoring them to each individual project, we can keep overall costs low without sacrificing quality.
Building projects combine a range of overlapping disciplines. We understand when and how to combine different professional services, from architecture to quantity surveying, to construction management to design and build. This guarantees the best possible team for any given project.
Architects – undertake the design of a building AND ensure compliance with local planning laws, as well as cultural and historical considerations, making sure the right building goes in the right place. In addition to our consultant architects, Erimus also provides services for partner architects.
Quantity Surveyors (QS) – offer a full preand post-contract QS service to clients, building contractors and other stakeholders. Pre-contract QS involves preparing bills of quantities, cost estimating and comparisons, works scheduling, feasibility checks and more.
Post-contract QS entails overseeing tender processes, bid analysis, brokering and negotiating deals, JCT contract administration issuing payment certificates, managing and accessing variations and final accounting. This is an area where significant savings can be made through effective collaboration.
Construction Managers Our construction management procurement route combines quantity surveying, contract administration and project management, our construction management procurement route allows the flexibility to procure and award tenders to several trade contactors for each individual aspect of your project. This adds a unique feature which allows greater control & deliver of the project, and by correctly administering each contractor and acting as a single point of contact, we can achieve significant cost savings – up to 20% on construction costs and professional fees, depending on the project.
Design and build – A model that encompasses every aspect of a project; from sketching out plans to snagging and final fixes. This overarching approach helps achieve greater cost certainty and faster project completion.
Our team also includes:
Structural Engineers – combine technical know-how and creativity to ensure buildings are safe, strong and reliable.
Project Managers – design the overall workplan to identify areas for time or cost savings, and to ensure that every professional does the right thing at the right time.
Contract Administrators – Our Contract Administrators are experts in delivering a full suite of JCT, NEC and bespoke contracts. They liaise between all parties involved in a project to make sure decisions are fair, transparent and adhered to.
Planning Consultants – Our planners have comprehensive understanding of planning regulations who prepare all aspects of a case to apply for planning consent.
Principal Contractors – ensure all contracting and processes are compliant with CDM regulations and HSE guidelines.
Principal designers – have overall control of the pre-construction phase of any project who plan and manage health and safety risks prior to construction, and work handin-hand with Principal Contractor.
Erimus Architectural Design and Build is your single point of contact for the planning, design and building of your project, from inception to completion. We provide both individual and combined services to housing developers, building contractors, investors & private clients. This flexibility, grounded in years of industry experience, and ability to coordinate the right people for the job, guarantees an approach that is both reassuringly professional and cost effective.
In construction, working in a wide range of diverse environments on a daily basis can be high risk and involve potentially dangerous machinery and equipment, which means that safety must come first. One key aspect of ensuring physical safety is by wearing the correct clothing.
Workwear choices are just as important as having the right tools and the relevant qualifications. If you’re not geared up with the right clothing or footwear, you won’t be able to do your job as well as you possibly can - not to mention the fact that you could also be putting yourself at risk.
Steve Davidson at U-PRO Trade Supplies, an online retailer which serves customers across the construction industry, shares his tips on choosing workwear and what to consider before making a purchase.
Whether it’s heavy machinery use, scaffolding, working at a height or with hazardous chemicals or materials, construction workers must wear appropriate workwear that keeps them safe from workplace injury. Such items include safety goggles, knee protectors, high visibility jackets and, dependent on the nature of the job, the use of a safety mask or respirator in environments where the normal air supply is compromisedfor example when there’s been a gas leak.
Given the heavy objects involved in a typical construction role, work boots
should be made from thicker, more protective material than standard work boots. Construction workers’ boots should feature a steel toe cap to protect from injury due to falling parts or objects. Boots such as The Switchback 3 boots feature a water-resistant upper and composite midplate for lightweight, flexible protection from sole puncture, anti-static for prevention of electrostatic build-up and they’re also slip-resistant for safe working. What’s more, they come with a durable moulded toe section that protects against scuffs. A Poron insole provides extra cushioning for added underfoot comfort and Micro-fresh® technology prevents the growth of mould to reduce odours and enhance wearability.
After safety comes comfort and functionality. You must remember that you’ll be wearing your workwear day in day out for hours at a time.
Key aspects to think about are: functionality - what do I need from my workwear? How can it help me in my job? What kind of movement will I need to do in my work clothes? This can range from walking and climbing to standing and kneeling. You must also think about how many pockets you need for easy access to regularly used tools and parts.
Both jackets and trousers should be made of a thicker material for most construction roles - they need to be resilient and keep you warm in cold and unpredictable weather. As working on your knees is commonplace as a construction worker it will be important to choose workwear
trousers that have reinforced knee sections with extra protection. Flexibility is key in jackets and shirts too, so that you can move freely without risk of tears to the Comfortclothing.isalso important because if we are not comfortable, we’re never going to feel our best. You need to be able to move without restriction, given you’re often accessing difficult areas, and to avoid feeling overheated or cold. Scruffs is a well-known workwear brand that provides durability, functionality and comfort. They provide a wide range of affordable, high-quality and robust workwear options that are perfectly suited to the diverse roles.
For example, the Scruffs Trade Holster trousers are durable work trousers made from heavy duty twill fabric, with stretch panels for comfort and flexibility. They are two-layered and have long-lasting performance, with easy access holster pockets that have loops for tool and accessory storage.
Affordability without compromising quality
Affordability will also play a significant role in your decision-making. Whilst budget is of course important, you have to consider quality. If you purchase workwear purely based on cost alone, it’s only going to prove more expensive in the long run, as you will have to replace clothing more often because it doesn’t last as long. Good, high quality workwear also gives a better impression to clients and employees, demonstrating a professional and trustworthy worker that is well equipped and highly trained to carry out the job in hand.
Finally, before investing in any workwear clothing, it’s important to do your research, read reviews online about popular brands, the ranges they offer, and how the clothing will meet your needs in terms of safety, functionality and comfort. This will enable you to make an informed choice on the workwear that’s right for you.
An extended range of sustainable and functional High Visibility working clothes for light to night, dawn to dusk.
As workplace visibility decreases and the potential for accidents increase, Snickers Workwear High Visibility garments work hard to protect your wellbeing and safety on site.
The extensive range of Jackets, Trousers, Shorts, Toolvests, Shirts and Fleeces all work together to satisfy the requirements of Class 1, 2 and 3 protection levels.
These outstanding products combine Snickers’ unrivalled hallmarks for Protective Wear with the requirements of the EN 20471 standard for high visibility warning and sustainable SORONA fabrics, all these working clothes have durable, colour-fast protection retaining shape and comfort throughout the life of the garments. Added to which, all Snickers Hi Vis garments can be custom profiled to ensure ‘stand out’ coverage for your corporate brand.
For more information on the Snickers Workwear Protective Wear range, call the Helpline on 01484 854788; check out www.snickersworkwear.co.uk and download a digital catalogue or email sales@hultaforsgroup.co.uk
HVO will reduce CO2 emissions by over 90% and other harmful pollutants by over 80%.
Ireland’s largest construction company, John Sisk & Son (“Sisk”) has announced an agreement with Certa to supply Sisk with Hydrotreated Vegetable Oil (HVO) for use in plant and machinery on all of its Irish construction sites. Sisk is the first construction business in Ireland to mandate the switch to HVO across all sites.
HVO is a fossil-free biofuel typically made by reacting waste vegetable oils and animal fats with hydrogen to create fuel suitable for use in diesel engines.
The switch to HVO will deliver Sisk a 90 percent reduction in CO2e and 85 percent reduction in other harmful emissions such as particulate matter. The amount of diesel that Sisk uses annually emits 3,000 tonnes of CO2, this accounts for 60 percent of its scope 1 carbon emissions.
Komatsu comfort to provide a fast response and unrivalled productivity for its Theseclass.excavators are the latest machines to join Howard Civil Engineering’s growing fleet of Stage V plant following a recent delivery of six new Kobelco SK130 13-tonne excavators and 11 new Doosan excavators ranging from five to 14 tonnes in size.
Earlier this year, Sisk successfully trialled HVO across a number of its civil engineering projects. With greater volume and distribution of HVO coming onto the Irish market, Sisk will implement HVO across its Irish business by the end of 2022. The business is also exploring similar supply arrangements for its European projects.
Ian O’Connor, Energy Manager, John Sisk & Son said:
Howard Civil Engineering, based in Leeds and operating across the north of England, has expanded its growing fleet of plant machinery with the purchase of 36 new Komatsu excavators.
Six new Komatsu PC210LC-11E0 excavators, the first of the new purchases to arrive, have recently been delivered to two large projects in York and TheseSunderland.20-tonne
excavators feature a powerful Komatsu EU Stage V engine, Komatsu’s Closed Centre Load Sensing (CLSS) hydraulic system and first-class
The SME civil engineering company, which also operates a plant hire business, is expecting more deliveries of a new D61 dozer and at least 10 excavators from Marubeni-Komatsu over the next 12 months, and has purchased new trucks and trailers to assist with the transportation of plant between Managingprojects.director
Michael Howard says this investment highlights Howard Civil Engineering’s ongoing commitment to health, safety, and sustainability.
In addition to the new Stage V engines, Howard Civil Engineering is also rolling out several environmentally friendly initiatives to reduce carbon emissions and increase sustainability.
These include the company’s recent relocation into a brand-new energy efficient head office, the utilisation of HVO fuel, and the rolling out of ecowelfare units on its sites.
Our transition to HVO is a major strategic step change and it will positively impact our carbon performance immediately. We estimate a 60 percent reduction of our Scope 1 emissions when the entire company is using this fuel. We have set ourselves ambitious targets to achieve carbon neutrality by 2030 and this is another important milestone on the journey. We will continue to monitor new technologies and innovation to ensure we are at the forefront of clean and efficient sustainable solutions.
Andrew Graham, Managing Director, Certa Ireland said: “We are delighted to be supplying Sisk with our ground-breaking GD+ HVO product. This is a great opportunity to facilitate Sisk in their journey to achieve Net Zero by 2030.”
Sisk was the first construction business in the UK to utilise this sustainable fuel at its Northstowe project in Cambridgeshire for its client, Homes England. This project used circa 1.5 million litres of HVO. In April, 100 percent of site fuel procured by Sisk projects in the UK was HVO. As a result, carbon emissions of Sisk UK operations have been reduced by 36 per cent.
Fast-growing plant and powered access hire specialist FGS Plant has placed its biggest ever order for access platforms - investing over £2million in a range of LGMG scissor lifts and boom lifts.
Access Platform Sales, the UK and Ireland distributor for LGMG, is delivering the platforms in two tranches, the first in August and September 2022, the rest in early 2023.
The platforms are being shared between FGS Plant’s own fleet, based at its HQ depot in Aylesford, Kent, and its access rental business, Hire Access Platforms, in Poole, Dorset.
FGS Plant and Hire Access Platforms closely examined different options to renew and expand its fleet before deciding that investing in LGMG platforms was the stand-out solution, said Managing Director Stuart Willy.
Chinese manufacturer LGMG offers a full range of electric and diesel scissor lifts and boom lifts, which are distributed to more than 30 countries.
It is at the forefront of producing and marketing lithium electric platforms, including rough terrain models.
FGS Plant has built a strong reputation for quality and service since it was established in 2004 and is determined to maintain these standards as it rapidly
expands its presence in the access rental
Themarket.company’s success is founded on the hire of excavators, dumpers, rollers, telehandlers, shovels and attachments across the South-East, but it sees access platform hire as a key growth area.
Hire Access Platforms is also taking two of the new BoSS PA-lift push around scissor lifts, which have an industry leading working height of 5.4m.
The construction of a new speculative 160,800 sq ft industrial warehouse on the site of the former Weetabix factory on the Earlstrees Industrial Estate in Corby has been given the green light by councilors.
Copley Point Capital – on behalf of its Block Industrial program and Pembury Real Estate Ltd – submitted a planning application to North Northamptonshire Council earlier this year having purchased the 8-acre site on one of the town’s prime industrial parks. This application has just been approved by local councilors at a planning committee meeting.
The demolition of the existing building is close to being completed and the construction of the new unit will commence shortly with a view to delivering a new bestin-class facility by Q3-2023. The unit will be BREEAM Very Good rated and will feature a 12.5m minimum clear eaves height, 16-dock and two-level access doors, together with a 50m Copleyyard.Point
Capital, Director, Nimit Oberoi, said: “We’re very pleased to have obtained planning permission for ‘Earlstree160’ just seven months after our acquisition. This is a testament to the hard work of our team and the positive and pragmatic attitude of North Northamptonshire Council. The development is in an excellent location where there is very little supply of new, high-specification industrial units. Earlstree 160 is best placed to help satisfy the strong demand for Grade A urban logistics and industrial space that there is for businesses operating locally, regionally and nationally.”
Prop-Search, Cushman & Wakefield and Potter Learoyd have been appointed as marketing agents and Richard Baker, a Director of Prop-Search, added: “We are already encouraged by the level of enquiries we have received. The appetite for ‘A’ grade warehouse space in the region remains high and this development will further support local economic growth and offer new job opportunities.”
Leading East Midlands contractor Kori Construction has broken ground on a new care home development in Rayleigh, Essex, in a contractor worth £10m.
The business is bringing forward the high quality, 60-bedroom facility on Rawreth Lane in the town, on behalf of independent care provider Barchester Healthcare. The care home is part of a wider plan for a new residential scheme on land to the north of London Road which includes outline planning permission for up to 500 houses as well as non-residential facilities.
Occupying a 0.44 hectare green field site, it will provide high quality living
accommodation and care to elderly and frail residents, along with communal facilities, landscaped grounds and parking facilities for visitors.
Wayne Bedier, Project Manager for Kori Construction at Rayleigh, said the care home had been designed with a contemporary material palette to reflect the style of the surrounding properties.
The layout of the home has been carefully considered to provide a safe and secure environment for residents, along with effective infection control. The three storey property will have a total internal area of 3572m2. The design includes 15 ground floor bedrooms, 21 bedrooms on the first floor, and 24 on the second floor.
Building materials include red multi brick walls with dark grey cladding, dark grey roof tiles and natural stone window sills.
The development was also designed with sustainability in mind, achieving a ‘very good’ BREEAM rating due to PV panels on the roof, and a target to reduce water usage on site by 25%. There will also be four EV charging points in car park which has a total of 24 car parking spaces, including two disabled spaces.
Mr Bedier added the development was forecast to be completed by December, 2023.
Work is due to start to improve an existing access road and create a new route into the £800 million Fairham neighbourhood in Nottinghamshire.
The work is taking place off the Mill Hill roundabout and on the Clifton South tram terminus access road from the A453 Remembrance Way.
Day and night-time works will start to increase from Monday 5th September 2022 with a completion in April 2023 in order to create a new access road and controlled junction for Fairham, along with improved access to the existing Park & Ride site.
Access to and from the Clifton South Park & Ride will be maintained at all times to keep traffic flowing while works to create new
earthworks, carriageway and signalisation takes place. Construction traffic will be rerouted away from civilian traffic during the works.
The 606-acre site is in the process of becoming a whole new neighbourhood for Nottingham with 3,000 new homes, one million sq ft of employment space and 200 acres of open green space. The works are all part of £100 million of infrastructure improvements scheduled for Fairham.
O’Brien Contractors Ltd will be carrying out the work on behalf of Clowes Developments, the company behind the Fairham masterplan. Fairham is being brought forward in partnership with Homes England, the government’s housing accelerator.
As well as new homes and employment space, there will also be a neighbourhood centre plus new educational, community and sports and leisure facilities at Fairham, along with a protected future route for the NET
England have been working with Highways England, Nottinghamshire County Council, Nottingham City Council and Rushcliffe Borough Council to ensure the access works achieve the maximum benefit for the least amount of disruption for the travelling
bring thousands of new homes, jobs and opportunities to Nottingham, Fairham will be the East Midlands’ most significant mixed-use development.
It creates a thriving new community and neighbourhood that is well-planned, safe and friendly; a place that has a vibrant mix of residential and commercial amenities, all designed and built to the highest standards.
The new community has been designed around a highly sustainable, ultraconnected location set amid the green landscape of south Nottinghamshire.
With all amenities co-located alongside one another, it will be one of the most highly accessible as well as greenest new communities in the region.
The scheme will help provide new employment opportunities across the region as well as assisting Rushcliffe Borough Council in meeting its new homes target of 13,500 dwellings by 2030.
Mixing commercial and residential, living and working, it is already establishing itself as the benchmark for future developments, becoming the region’s finest place to live, work and flourish. MILLION
Bellway has acquired land for a new development of 358 homes in Stafford.
The 30-acre site off Lichfield Road, previously occupied by the General Electric factory and to be known as Victoria Gate, already benefits from outline planning permission which was granted in October 2021.
The former factory and its associated buildings were demolished and cleared from the site early last year. Bellway has submitted a reserved matters application
to Stafford Borough Council and are hopeful to secure approval by the end of the year.
If Bellway’s plans are approved, construction work could begin on the site later this year, with the first homes expected to go on sale in March next year.
Bellway’s proposals will include a mix of two, three and four-bedroom properties, comprising 323 homes for private sale and 35 affordable homes for low-cost rent or shared ownership.
As part of the planning agreement for the development, Bellway will provide funding of over £2.5 million for local services and infrastructure, including £1,903,633 for educational places and facilities, £334,184 for the provision and maintenance of public open space, and £275,185 towards local sports facilities.
Beko plc has appointed Steve Clarke as its new Head of Sustainability and Quality.
Clarke, who was Beko plc’s Head of Service Operations for six years prior to taking on his new role, brings with him extensive experience within the
household appliance industry and has a clear focus on how the company can support housebuilders, developers and contractors by providing them with high quality, efficient and eco-friendly appliances which have been produced in a responsible and sustainable manner.
Harley Haddow has announced the appointment of Ian Chalk as Director to further strengthen their Manchester offering.
The multi-disciplinary engineering consultancy opened the North West base earlier this year as part of its ongoing UK expansion and recruitment Chalkstrategy.joins
the firm from construction engineering company Hoare Lea with 20 years’ experience in the industry and region. He has worked on an expansive portfolio across multiple projects around Manchester, the North West, and the Middle East; including leading the current St. Michael’s scheme, Manchester Airport, many of the major North West universities, Liverpool Women’s Hospital and multiple Covidrelated healthcare schemes during the pandemic. He also led the Doha Metro Green Line project in Qatar, in preparation for the World Cup being held there later this year.
Within his new role, Ian will be responsible for heading up the Manchester office, business
development and growing the Mechanical, Electrical & Public Health (MEP), Sustainability and Civil & Structural teams.
His appointment adds to a hugely successful period for Harley Haddow, which has been shortlisted for all awards entered so far this year, as well as continuing to hold the title of ACE’s Net Zero Advisor of the Year. These include:
• UKREiiF – Consultancy of the Year and Net Zero Hero of the Year
• London Construction Awards –Engineering Consultant of the Year
• ACE – Engineering Consultancy of the Year
• Building Awards – Engineering Consultant of the Year
Harley Haddow is actively recruiting a range of roles in Manchester to meet growing business development demand.
To find out more about working for Harley Haddow visit the careers page here: careers/https://www.harleyhaddow.com/
In his new role as Head of Sustainability and Quality, Clarke will continue to implement positive changes across the business to improve customers’ experiences, whilst supporting the company’s ambition to achieve carbon neutrality.
Clarke comments, “We understand the significance of sustainability targets within the construction industry and embrace our responsibility as a supplier to support the credentials of the builders and developers we work with. We are proud that Beko plc, and our parent company, Arçelik, are setting the standard for sustainability within the appliance industry with our continuous product innovation, responsible manufacturing methods and ambitious future environmental targets.
“We are determined to achieve our goal of becoming net zero by 2050 and are continuously looking at ways in which we can reach this target. From developing innovative technologies, for example using recycled fishing nets and industrial thread waste to replace virgin plastic in our ovens, to minimising packaging and making our products more energy efficient, we strive to minimise our company’s footprint.”
“We know that home owners are always looking for ways to reduce their living expenses, especially in the recent climate of soaring energy prices. Our focus as a company continues to be around continuously improving the energy and water efficiency of our products, meaning that they produce lower carbon emissions during their use, as well as allowing consumers to benefit from reduced energy and water bills.”
We have built strong foundations in this area and I am excited to be further driving our sustainability agenda.Ian Chalk Steve Clarke
Construction Plant-hire Association (CPA) Chief Executive Kevin Minton has given notice of his intention to step down, and the association has started the process of identifying a successor.
Kevin has been with CPA for 15 years, and will remain with the company until the first quarter of 2023 allowing time for a smooth handover. He joined CPA as Technical and Safety Manager in 2007, before becoming Director in 2014, and Chief Executive in 2018.
In a letter to CPA Members, Kevin said: “I have had the privileges of leading this association, and a great team of professional and dedicated staff, since 2018; and of being part of Colin Wood’s team for 11 years before that.
“The time is right now for a change, and I will be pleased to hand control to a new Chief Executive who can lead the association on challenges the sector will face in the
near future, such as rising costs of doing business, a widespread skills shortage and decarbonisation.”
CPA President Brian Jones said:
It has been a pleasure to work with Kevin over the past 15 years, and we wish him well for his retirement. Thanks to his efforts and those of the CPA team, the association is in a stronger place than ever before.
“We continue to develop our support for Members and to put construction plant hire at the forefront of policy makers’ minds.
Membership is growing, and CPA Council is looking forward to new challenges and opportunities.”
Further details about the CPA Chief Executive job vacancy are available on the CPA website at association-cpaexecutive-construction-plant-hire-uk.net/news/job-vacancy-for-chief-https://www.cpa.
Kevin MintonContractors working on the new Harbour Arch Quay development at Sutton Harbour in Plymouth have begun pouring and forming the first-floor concrete slab, achieving a significant milestone for the project.
Located on Sutton Harbour’s north eastern quay, the Harbour Arch Quay development by Sutton Harbour Group, will offer 12 stylish two and threebedroom apartments in addition to two luxurious penthouses in Britain’s Ocean City and is due to be completed for occupancy in spring next year.
With the core structure of the unique development of elegant waterfront apartments overlooking Plymouth’s historic harbour and marina already completed, it is expected that the new concrete slab for each floor of the building will be formed and poured each between one to two weeks. The roof slab, topping off the ninth storey, is expected to be poured at the end of October.
Philip Beinhaker, Executive Chairman of Sutton Harbour Group was joined by Andrew McGoldrick, Senior Project Manager and Rod Short, Managing Director of Moor Manage, construction managers of the project, at an intimate ceremony to mark the step forward.
Harbour Arch Quay, designed by Plymouth-based ADG Architecture Design
Graphics, will be a striking new addition to the Sutton Harbour waterfront, offering spectacular views over the marina and Plymouth Sound. Sutton Harbour Group and Moor Manage are working with structural engineers Airey & Coles and MEP engineers Hoare Lea on the project.
At ground floor level, there is the lobby entrance and space for a commercial unit, as well as significant public realm improvements outside to enhance the harbourside setting.
Philip Beinhaker, Executive Chairman of Sutton Harbour Group, said: “The development of Harbour Arch Quay is the reawakening of the regeneration of the east side of Plymouth’s historic harbourfront, one of the finest in the UK.
Further development will follow with the Sugar Quay complex, which will transform the city’s famous waterfront, regenerating the long-overlooked east side, enhancing this area of the harbourside and make it more accessible and welcoming for residents of Plymouth, visitors, and tourists, along with the enhanced integration of the residential communities to the east and Plymouth city centre.
Sugar Quay, a £60million, 21-storey landmark building on the eastern side of the harbour, will offer 170 apartments, restaurants, and shops, and was unanimously approved backed by Plymouth City Council’s Planning Committee earlier this year. Work on this project is expected to begin next year.
Harbour Arch Quay will occupy space between Pinnacle Quay, home to apartments and the popular HonkyTonk Wine Library and Daisy’s Tea Rooms on the ground floor, and Salt Quay House, which is the headquarters for leading South West professional services firms such as Foot Anstey and Bishop Fleming.
Apartments will be appointed to the highest specifications and will feature floor to ceiling windows, open plan living spaces and large private terraces, along with the spectacular views to the marina, the Barbican and the Hoe to the south
design is being enhanced with the use of high-quality materials and finishes on the build to add to the distinctiveness of Sutton Harbour’s waterfront and complimenting neighbouring buildings.
For more information about Harbour Arch Quay, visit www.harbourarchquay.com.
As one of the world’s largest sectors the construction industry engages a vast number of small businesses to complete work on projects. As a sector already known for high rates of business insolvencies, inflationary pressures are seeing even greater numbers of businesses failing.
Operating on a ‘project-based structure’, the industry delivers projects involving multiple companies creating complex contractual hierarchies, which makes payments or security of payment, a problem.
To address some of the payments issues created by this complexity, Project Bank Accounts (PBAs) have historically been used, as ring-fenced bank accounts which provide an alternative payment mechanism on projects. They’re used by the UK Government to ensure that main contractors, and subcontractors in the supply chain, are paid and don’t face unreasonable payment delays due to the main contractor not passing on payments.
In fact, the Government has recently recommended that all projects should use a transparent payment mechanism and recommended the use of project bank accounts on all construction projects, public and
are paid directly from the PBA at the same time as the main contractor. But PBAs still have several limitations and flaws which have hampered their uptake and use on building projects. They are difficult to set up and have complex legal requirements. Also, how to effectively implement them is frequently misunderstood and they require significant paperwork and spreadsheet administration.
They tie up the working capital of main contractors and only protect payments for the top tier contractors.
They have also recently been shown on a UK government project to be ineffective in protecting payments to lower level subcontractors when a contractor collapses.
In traditional construction supply chains, main contractors pay subcontractors, who then pay their sub-subcontractors, this can add delays and increase average subcontractor costs for projects of around 5-10%. And if the main contractor’s business collapses subcontractors don’t get paid at all for work completed.
The construction sector is renowned for a vicious cycle of working capital dysfunction. This is created by limited access to affordable working capital due to this contractual chain payment risk resulting in high rates of non-payment and business collapse in the sector - with small and micro businesses most exposed to risks with the majority of their business assets tied up in unpaid invoices.
With the payment risk that the hierarchical payment chain creates, at least 32% of business assets are made up of accounts receivable. This is more than any other industry and further highlights the extent of the counterparty risk faced within the building and construction industry.
This dysfunction is made worse by the power imbalance between large main contractors and the small businesses – who become default financiers on projects. In fact, main contractors often use money owed to small business subcontractors as their free working capital to spend as they please. This provides an incentive to delay payments to small businesses for as long as
this, a new trusted, collaborative and digital way to manage payments has been developed, using secure digital wallets to remove the insolvency risk which results
in non-payment from project payments. These reduce project costs and provide full supply chain payment guarantees well beyond the capabilities of PBAs. By ensuring payment for services performed they remove the financial contagion associated with outstanding accounts receivables impacting the supply chain. This changes the management of working capital without the additional administration and audit compliance costs of project bank accounts (PBAs provided by the major banks) borne by project owners and main contractors.
Project bank accounts require the drafting of complex legal agreements which means they are typically only used on large government projects. But these new platforms allow all parties to quickly sign up to a building project’s wallet, agreeing to the wallet’s terms of use electronically when they are joined to the digital wallet as part of the simple onboarding process - making it easy for them to be used on any size of project big or small, public sector or private. Everyone across the project’s supply chain is joined to the project wallet and can benefit from guaranteed project payments made by the contractually agreed due date or immediate invoice payments if they register for them and agree to the merchant fee.
Primarily, they offer reduced costs for subcontractors in managing working capital, while removing the risk of nonpayment and increasing trust by providing payment certainty. This facilitates lower subcontractor costs, ensuring lower project budgets and freeing up cash to invest in more housing stock.
But they also provide a range of further benefits, including:
• Visibility and control
• Lower administration
• Fully secure, fast payments
• Robust supply chains
• Full compliance
• Reduced risk
So those who typically look at PBAs for certain projects should now look at new project wallet solutions that are becoming available, which address and overcome all the limitations PBAs.
On an industry-wide level this provides a collaborative, scalable and secure payment platform that makes the entire construction project payment process simpler, faster and protected for everyone.
Jones Homes Southern has appointed a senior quantity surveyor who has 37 years’ experience in the construction industry.
Adrian Hall now leads the regional surveying team based at Jones Homes’ South East headquarters in Swanley,
Adrian,Kent. who left Thames Polytechnic with a HND in civil engineering in 1981, started his career in the industry on the Falkland Islands in the South Atlantic.
Adrian, who lives in Bexhill-on-Sea, returned to the UK where, over the years, he took on a number of roles with different companies within the construction industry including senior surveyor, senior quantity surveyor and commercial manager.
For more information about careers at Jones Homes, jones-homes.co.uk/careers.visit
A university graduate who started his career in the construction industry as a labourer has joined Jones Homes Southern as an assistant quantity surveyor.
Jamie Yeo has taken up the role at the housebuilder’s regional headquarters in Swanley in Kent.
The 30-year-old, who lives in Deal, worked as a labourer on a building site after
graduating from Aston University with a degree in computer science and business studies.
“I knew by the time I finished my degree that I wanted to have a career in construction,” said Jamie. “I wasn’t sure how to get into the industry so I got a job as a labourer on a housing development and worked in that role for two years.
“During that time I asked management if I could move to an office-based role and they put me forward for a master’s degree in construction project management at London South Bank University on a day-release basis.”
Jamie then secured a role as a junior quantity surveyor with a construction company but switched to Jones Homes after listening to advice from his father David.
A popular home builder has appointed six new members of staff as the company continues to grow.
As expanding housebuilder Genesis Homes works towards constructing more than 750 new homes across Cumbria and Lancashire, the company has strengthened its workforce to help it meet its ambitious build target.
The company, which was founded in Penrith just five years ago, has grown rapidly and last year acquired south Cumbrian home builder Russell Armer Homes to widen the geographical area it builds new housing developments in.
Its ongoing recruitment drive has resulted in the recent appointments of
six new starters, including experienced site manager Hugh Sneddon, trainee land and technical administrator Josie Scrimgour, IT manager Maciej Misiak, commercial assistant Bethany Bell, technical assistant Josh Halliwell and trainee quantity surveyor Jack Smith.
Hugh has nearly 30 years of experience in the construction industry working at some of the country’s largest house building companies. He has been appointed as site manager at Russell Armer Homes’ Bowland Fold development in Halton, Lancaster.
Just starting out on his career path is 18-year-old Jack who spent two weeks with Genesis Homes in February on work experience while studying a BTEC in Business at Carlisle College. That experience whetted his appetite further to pursue a career in construction.
Genesis Homes is currently operational across seven development, including its pioneering EcoGen project in Calthwaite which will see the construction of 16 homes fully powered by renewable energy - with a further three developments set to start later this year. In total, 757 new homes will be built over the 10 developments.
For construction workers, there are many dangerous risks to face. In fact, the cost of injuries within the industry across the UK has reached more than a staggering £16.2 billion a year, truly emphasising the impact that working on a building site can have.
However, despite the overwhelming findings, there are more ways to offer protection thanks to advanced Buttechnology.howexactly
does this work? Here, with some help from van leasing company, Van Ninja, we delve into five ways technology is helping to improve the health and safety of the construction sector.
While PPE is an essential measure for construction workers to ensure their health and safety, that’s not to say there’s room for improvement; in fact, there are more items that workers can wear to protect
There are many risks that can affect the health of a construction worker, but with site sensors, there’s extra protection in place against these.
With site sensors, which companies like SmartSite and Pillar Technologies have developed, many things such as noise levels, temperature, and dust particulates can be monitored to protect the workers from high exposure. Across the construction site, these sensors can be implemented to inform the employees if they are in danger of passing the exposure limit.
are yet another way that safety can be improved in the construction industry, with many helping monitor vital signs, identify collisions, and keep track of workers who are working unaccompanied. So, if workers are using van leasing to go from site to site, you can keep an eye on them for their safety.
When out and about, especially during rush hours, mishaps can take place at every turn. Even slamming the breaks to avoid colliding with another vehicle or a pedestrian can be harmful. You are likely to suffer an abrupt movement of the head and neck, which may result in whiplash injury.
Susanne McGraw, Head of Personal Injury at Watermans, said: “As part of a team of personal injury lawyers, I support many people who have suffered a whiplash injury when at the wheel of their vehicle. Most of them will recover within days, whereas others have to deal with its effects for weeks or even months.
“My recommendation is to seek medical assistance as soon as possible. This will give you the chance to get the treatment you need and alleviate feelings of discomfort in a timely manner.”
Exoskeleton is one example of wearable technology which assists the workers’ physical support when there is a high risk of injury.
Turning the safety process to digital instead of having a pile of paperwork will not only provide more time to be used elsewhere, but also contribute to the safety process of the construction site. With an ePTW system, safety is ensured while making life easier. Digital signoffs allow for more traceability, and you can rest assured that you have clarity of what’s going on throughout the construction site, thanks to real-time visibility, even if you aren’t on-site. In addition to this, consistent standards can be implemented across various sites, even for different types of construction work. With consistency across teams and visibility over the sites, you can rely on this technology for a safer working environment.
It’s essential for site workers to be aware of hazards to avoid major injuries.
Thankfully, technology can monitor sites to improve workers’ safety.
Drones are excellent for construction companies as they can be used for an aerial inspection of their site, which offers a wide view of the area and the surrounding environment. Given their ability to reach elevated areas and places that may be deemed unsafe, the inspection is much more accurate and efficient. With this technology, any safety hazards can be spotted prior to work being carried out to identify any procedures that need to be in place.
Training is important in any job role for upskilling, but for the construction industry in particular, it is vital due to the many physical health risks like back injuries and the harmful chemicals in
training sessions, all workers across several sites can learn the same information, avoiding miscommunication that could be spread through in-person training through multiple sites. As well as this, sessions can be recorded for workers to revisit to refresh their memory, ensuring excellent safety conditions as employees can become much more familiar with necessary
Technologyprocedures.providesan abundance of opportunities for many different industries, but given the risks for construction workers, the advancements are particularly useful for this sector due to the ability to improve safety.
The new all-in-one platform combines an interactive sales and customer experience centre environment with the latest Samsung touchscreen devices and innovations.
Signtouch, part of the Sign Build group of companies, has launched ‘Signtouch, powered by Samsung’, a pioneering digital sales centre solution offering new home builders enhanced development marketing, sales performance, content management, footfall analytics and customer experience - all via one easy-to-use interactive
want to experience a new home development and ultimately how they want to research and buy a new build home is changing rapidly. As retail data analytics confirms, consumers are no longer tolerating homogenised sales experiences – they expect every step to be personalised, multi-channel and interactive.
‘Signtouch, powered by Samsung’ provides new home builders with an effective way to transition from an uneconomical and environmentally unfriendly paperbased sales centre approach to a digitally driven single, integrated solution. New home builders will now benefit from a customisable and reliable solution to meet the challenges of today’s new home buyers. The Signtouch launch means that centralised sales & marketing teams can now share customised branded content in real-time at group, regional or development level with just a few clicks.
• The Signtouch solution is highly secure and robust and leverages new home builders’ portfolio of marketing, sales, and analytic capabilities, including 3D tours, interactive site plans and behavioural data.
• The Signtouch nationwide hardware service includes touchscreen installation, site maintenance, removals, storage, re-installations, and decommissioning – all supported by Samsung UK’s nationwide repair or replace guarantee.
• The Signtouch software support service guarantees 24/7 uptime and provides remote technical support to new home builders as they transition to a digital, interactive sales centre.
‘Signtouch, powered by Samsung’ includes enhanced new build development marketing and sales capability, ‘one-click’ content management utilising existing marketing assets, footfall and customer experience real-time analytics, and visitor demographic knowledge. All of which will be available to builders of all sizes. These features can be run standalone or integrated with a suite of applications, including leading Customer Relationship Management (CRM) and telephone answering services – ensuring everything works in sync.
Mark Cowin, Managing Director –Signtouch says: “At Signtouch we are focused on making the transition to a digital sales centre effortless for housebuilders and have invested in interactive Point of Sale on behalf of home builders. Bringing together the touchscreen innovation of Samsung with Signtouch’s leadership in new home builder digital sales centre technology, we are giving sales & marketing teams the interactive capabilities they need to meet home buyer expectations, through a single seamless solution. Additionally, our open platform and joint innovation are paving new paths to an enhanced customer experience for UK housebuilders.
Damon Crowhurst, Head of DisplaySamsung Electronics UK says: “We’re excited to be working with Signtouch to bring to market an interactive sales centre solution that meets a real business need. The interface between new build developments and customers is of paramount importance and Samsung firmly believe that Signtouch offers new home builders a managed and cost-effective way to advance this interface and further enhance this complex relationship.” WITH SAMSUNG BRING DIGITAL SALES CENTRE TECHNOLOGY TO UK HOUSEBUILDERS
We’re looking forward to developing this partnership further and deeper in the future.
One of the UK’s fastest-growing construction companies has thrown its weight behind this year’s campaign to encourage more tradespeople and contractors to seek help with a range of issues – from depression to suicidal thoughts – as part of a bid to tackle the mental health crisis that is affecting the UK construction industry.
Huddersfield-based Big Red Construction has become the headline sponsor of this year’s Big Brew campaign, which encourages construction industry workers and tradespeople to come together over a cuppa to support one another and remove the taboo around mental health in the Bigsector.Red
Construction was only founded just over five years ago and already has an order book of more than £20m of projects where it is either a principal contractor or a main contractor. It sees supporting the Big Brew as “absolutely vital” for the UK construction industry, where the suicide rate of workers is estimated to be as high as two people every day. UK construction sector workers are nearly three times as likely to die by suicide than their counterparts in other
“Through partnering with Band of Builders on this remarkable campaign, we hope to not only increase awareness of the mental health support services that are available but to also encourage other construction companies to join us in being part of the change. Big Red, Big Change,” said Mike.
“It is our key focus at Big Red to support all our construction workers, as we recognise the impact that not having the correct support or tools in place can have a detrimental impact on those who may be struggling with their mental health and day to day life. It’s absolutely vital that individuals, businesses and the industry at large do all they can to tackle this crisis.
We are supporting this year’s Big Brew because it’s a brilliantly simple idea to encourage tradespeople and contractors to have a quick timeout over a cuppa and check in with colleagues and friends to just see if they’re OK.
has got the industry talking; and how the first Big Brew raised enough money to fund a new, free, construction industry-only counselling service for two years.”
Peter Cape, the Big Brew lead at Band of Builders, said that this year more than 300 Big Brew events are expected to be hosted – mainly on construction sites and at builders’ merchants – this October, and the campaign is timed to coincide with World Mental Health Day.
“We are delighted that Big Red Construction has been so eager to come on board as a sponsor of the Big Brew and support a campaign that not only shines a light on the mental health crisis within the construction industry but has also put lifelines in place – such as our free counselling service and our new text line (text BOB to 85258) – that tradespeople, contractors and their families can use at any time,” said Pete.
the tie-up, Mike Lomas, Managing Director of Big Red Industries, praised the trailblazing work of the Big Brew and said that Big Red Construction was proud to be a supporter of a “brilliantly simple” campaign that aims to tackle such a systemic issue with a cuppa.
Mike added that a key reason why Big Red Construction is throwing its support behind the campaign is because it wanted to be a driving force in the continued momentum of the Big Brew.
He said: “We have been impressed with the way that the Big Brew has tackled the mental health crisis in construction head-on; how it
Pete added that at a time when the suicide rate of UK construction workers is estimated to be as high as two people every day, and UK construction sector workers are nearly three times as likely to die by suicide than their counterparts in other industries, it’s important that the industry comes together.
“We are proud that the Big Brew is gaining genuine momentum – particularly through the support of organisations such as Big Red Construction – because it means we can reach out to more tradespeople and construction workers who may be in crisis,” he said.
There’s still time to register interest in hosting a Big Brew event at https://bandofbuilders.org, and you can join in the conversation online by using the hashtag #GiveYourselfABreak.
The most effective way to start turning the tide on this is to get tradespeople and contractors talking, and this year we are introducing a tea scale as one way to start conversations – with images of different strengths of a cuppa. So, we are asking tradespeople ‘where are you at on the mental health tea scale?(L-R) Big Red MD Mike Lomas and Richard Croft from Band of Builders.