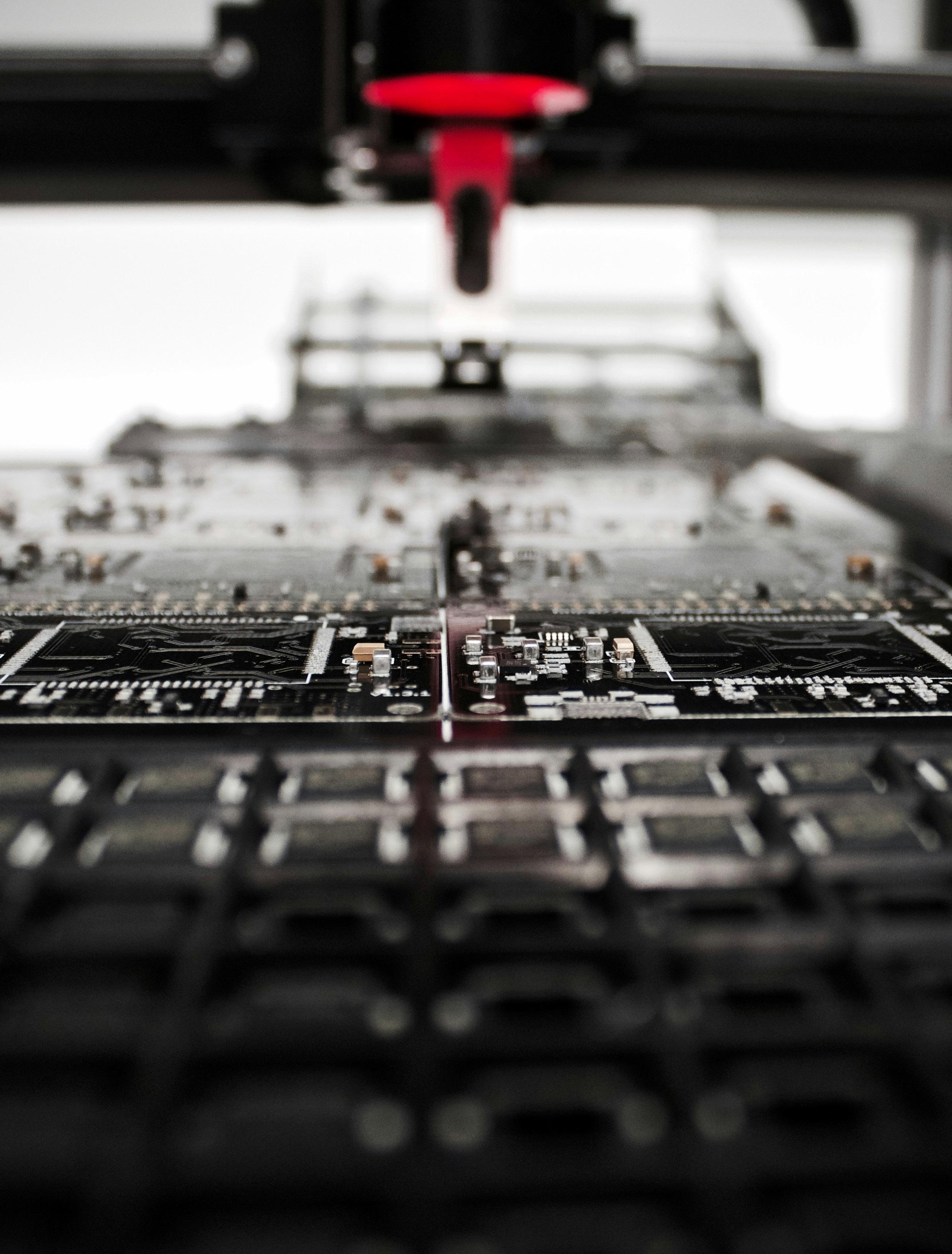
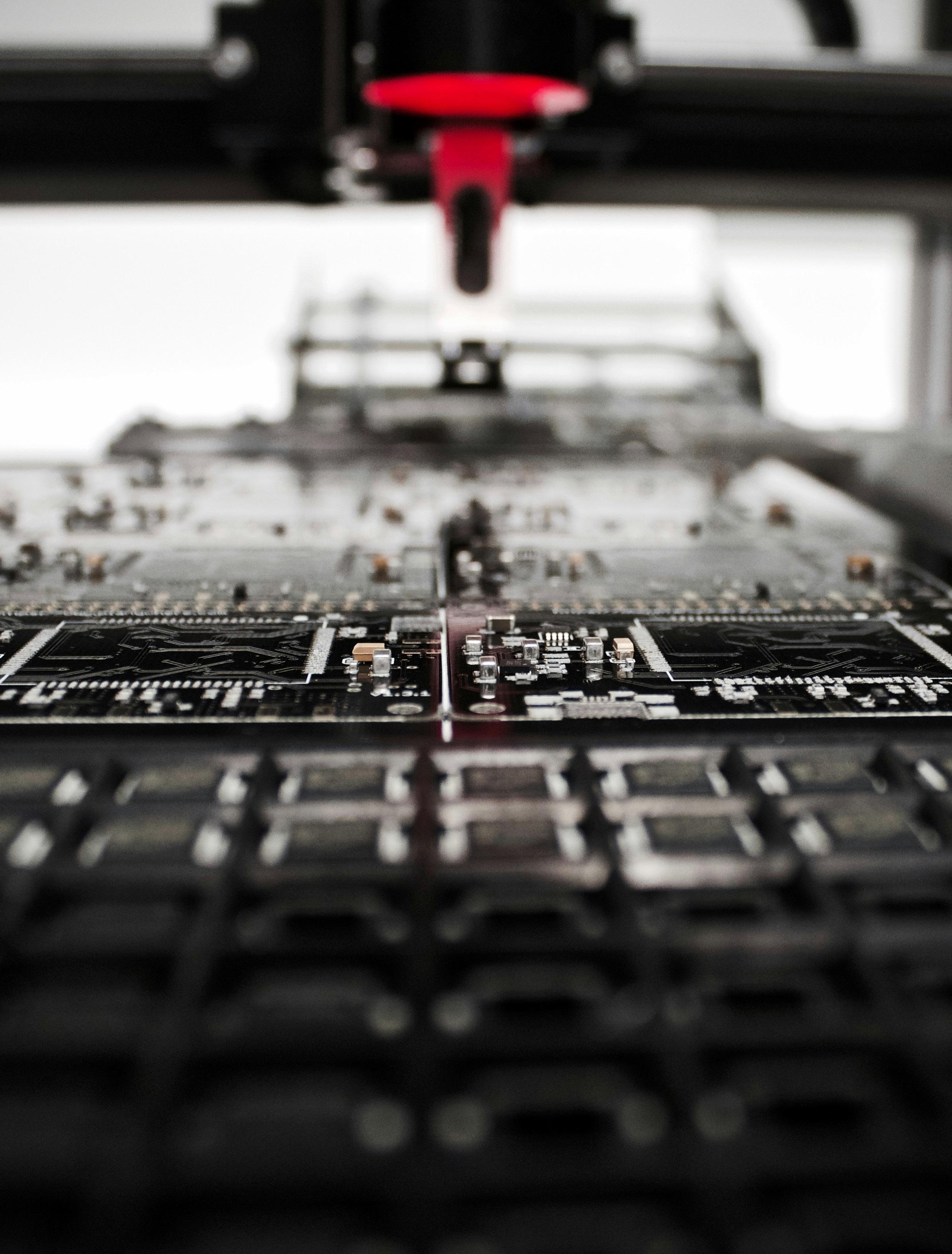
MANUFACTURING PRODUCTION
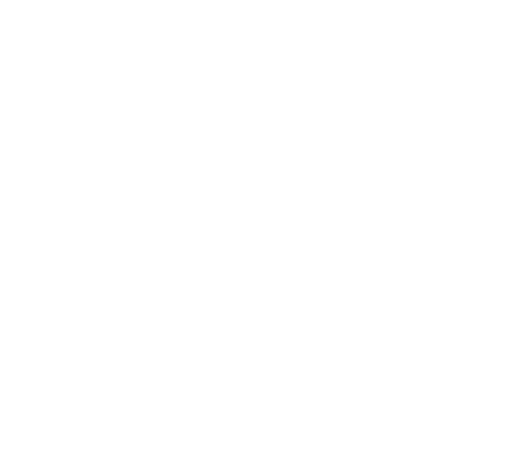
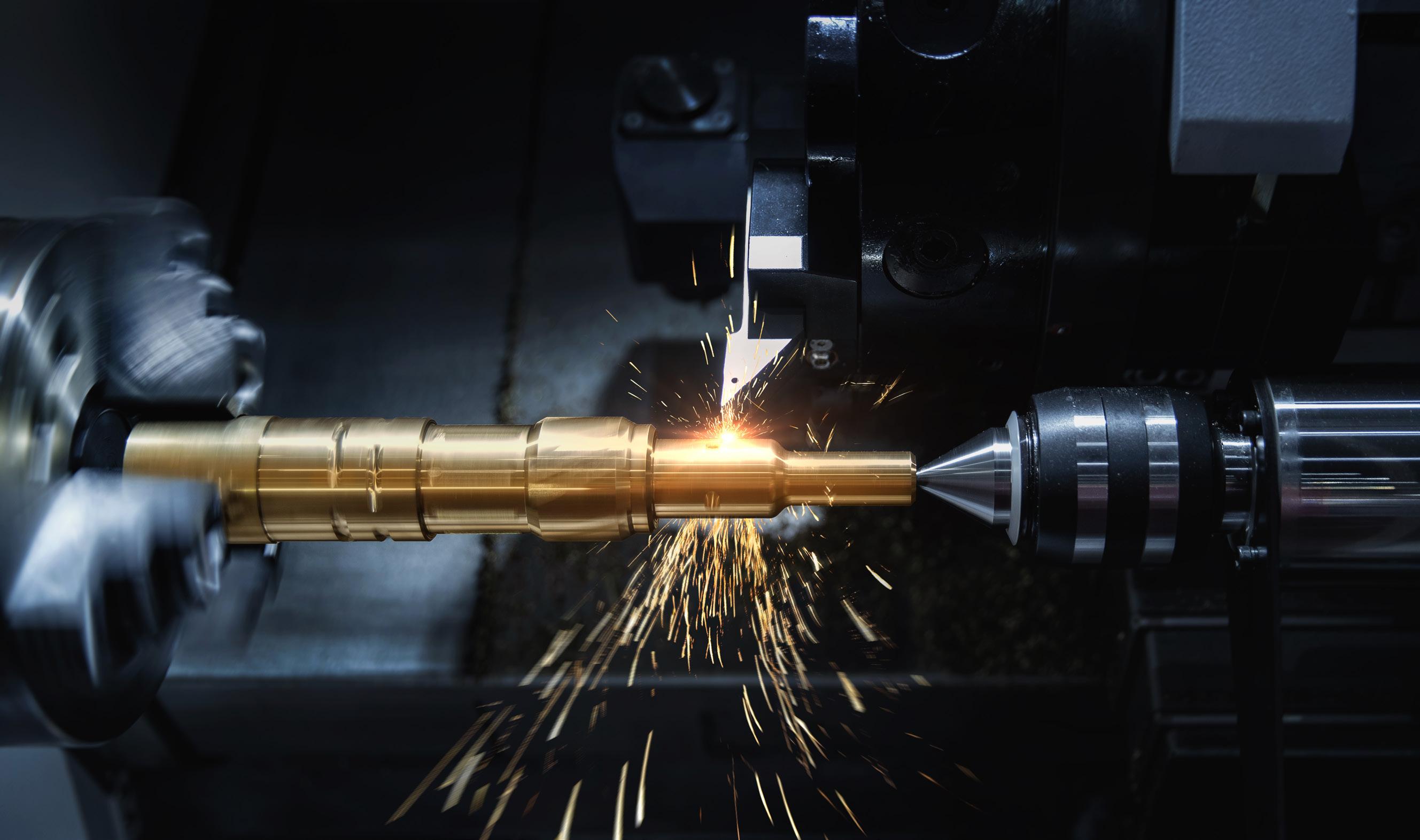
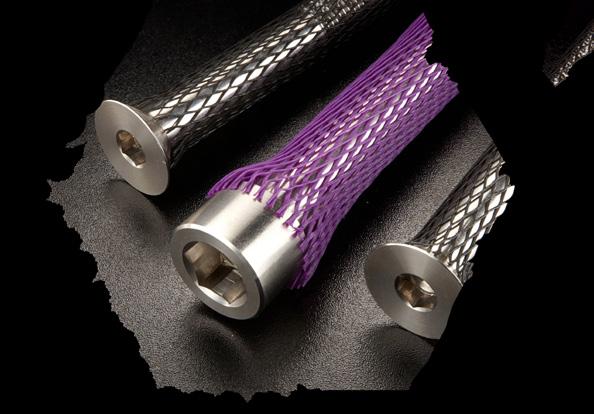

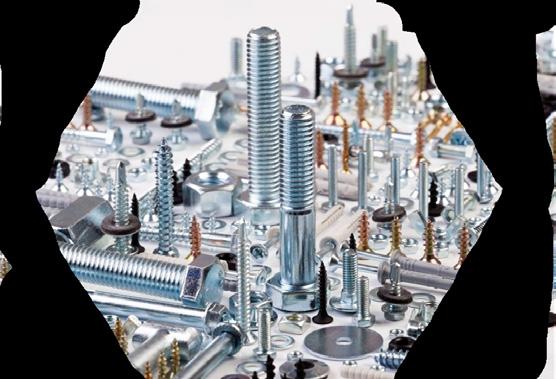
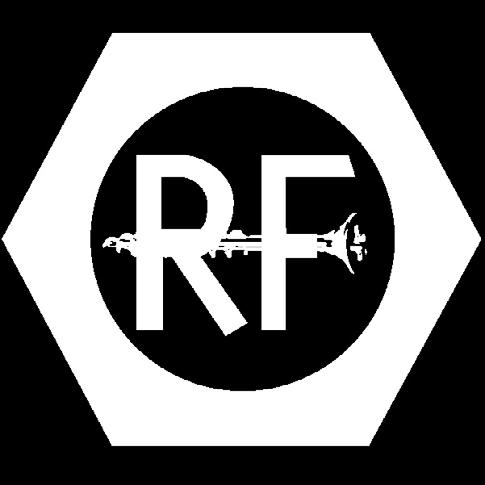
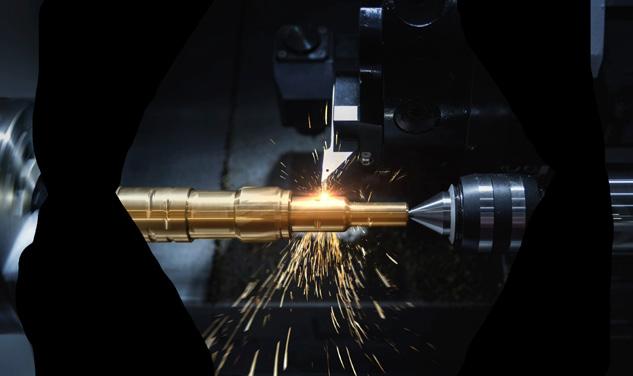
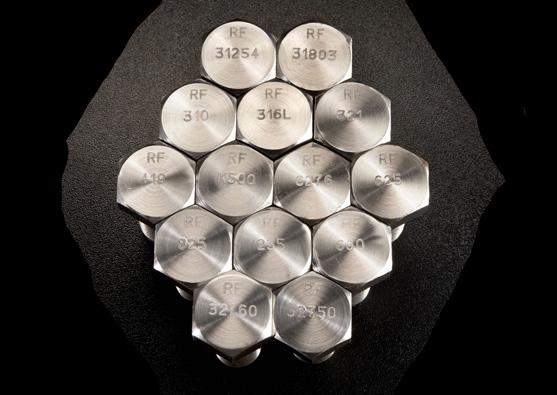
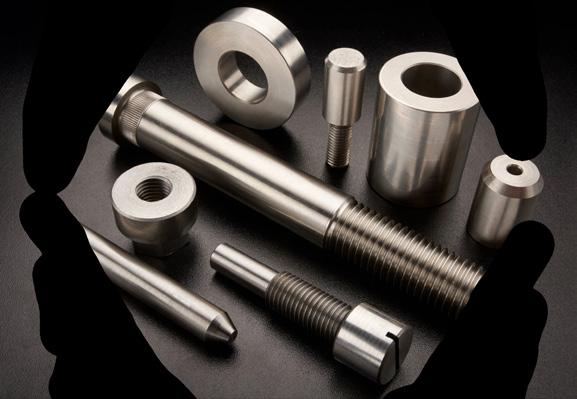
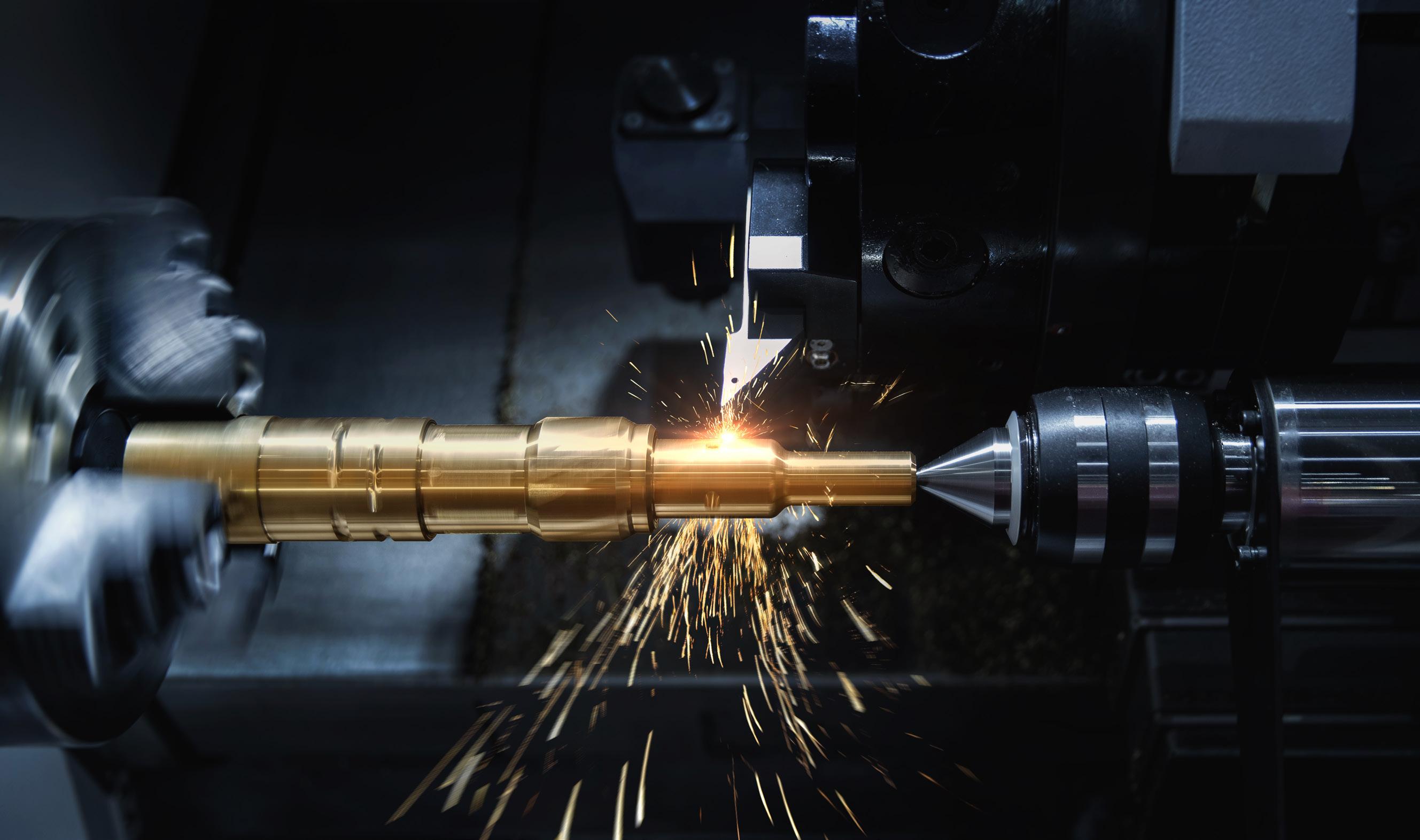
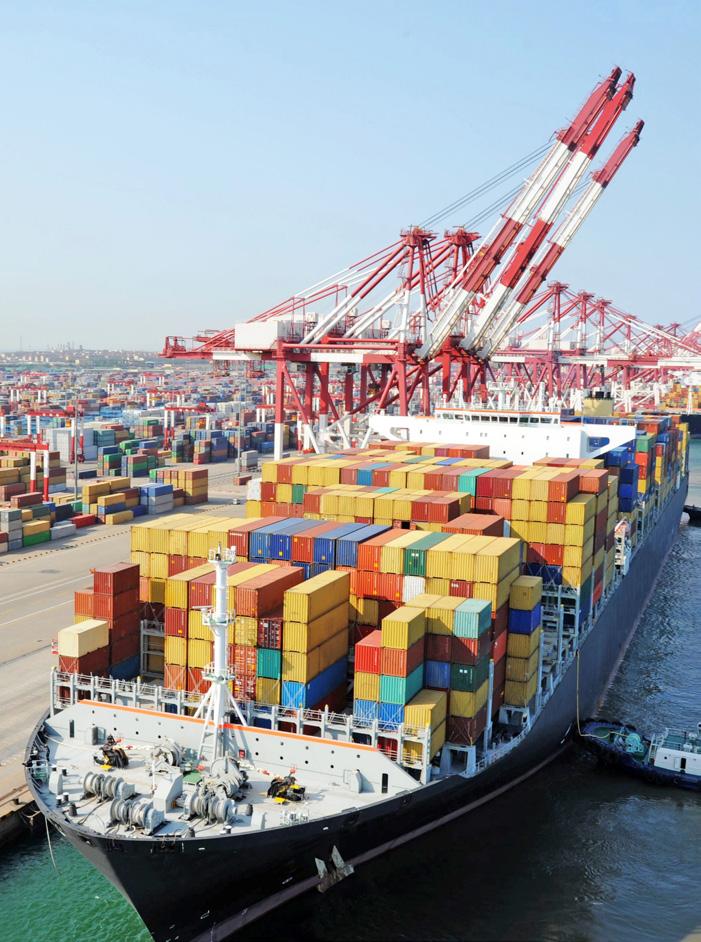
Editor
Paul Attwood editor@mpemagazine.co.uk
Senior Editorial Assistant
Sophie Weir editorial@mpemagazine.co.uk
Features Editor
Harry Peters editorial@mpemagazine.co.uk
Production/Design
Laura Whitehead laura@lapthornmedia.co.uk
Megan Carley megan@lapthornmedia.co.uk
Sales Manager
Charlotte Chapman charlotte@mpemagazine.co.uk
Accounts
Richard Lapthorn accounts@mpemagazine.co.uk
Circulation Manager
Leo Phillips
subs@mpemagazine.co.uk
Publishing Director
Maria Lapthorn maria@lapthornmedia.co.uk
Lapthorn Media Ltd
5-7 Ozengell Place, Eurokent Business Park, Ramsgate, Kent, CT12 6PB
Tel: 01843 808 102
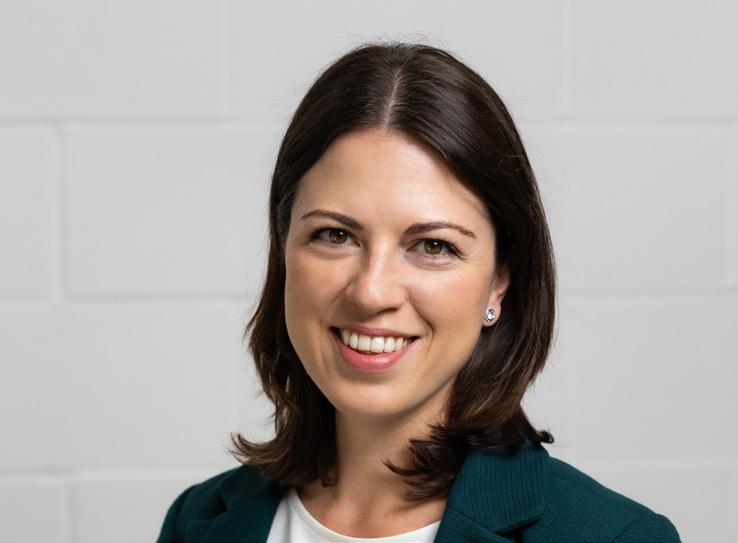
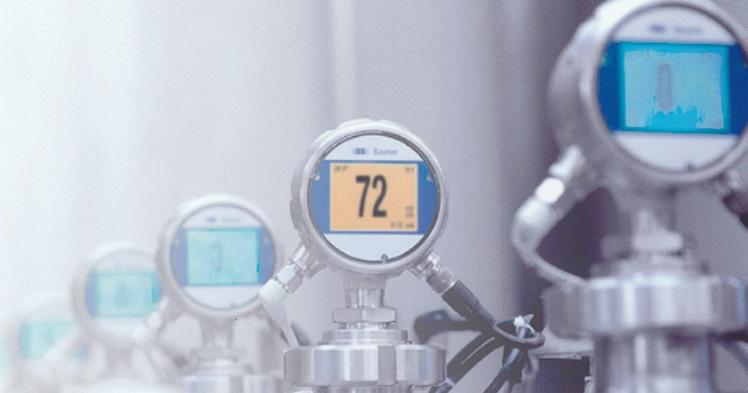
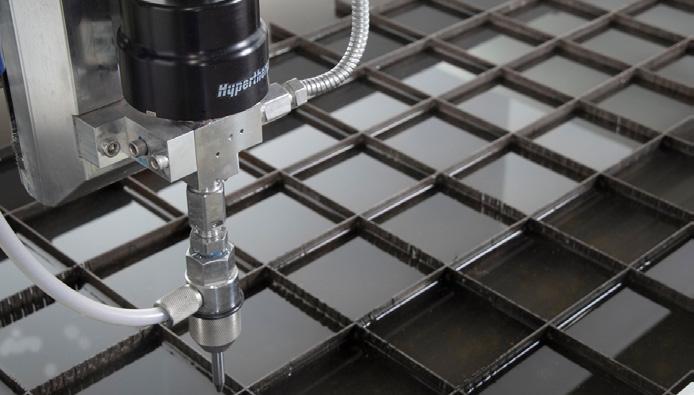
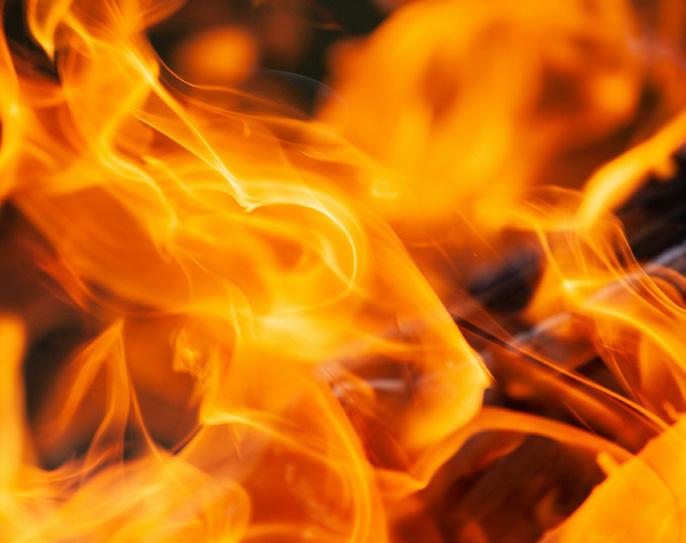
The impact of cargo crime: An insurance perspective
Interview with Oana Jinga, CC&PO and Co-founder of Dexory
Smart sensors- grasping the full potential
A cut above: Edmar brings waterjet cutting in house with Wardjet a-1212
Which fire protection material to choose for an EV battery
Editors Note
Welcome to the April issue of Manufacturing & Production Engineering Magazine.
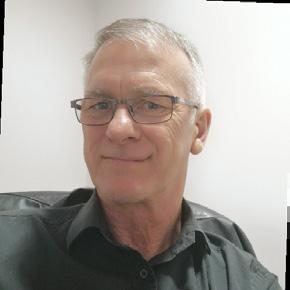
In this issue we have an interview with Oana Jinga, the Chief Commercial and Product Officer at Dexory, a leader in warehouse optimisation through robotics, automation and analytics. She explains and gives examples of how the use of autonomous robots and realtime AI driven data analytics provides increases in profitability by improvements in accuracy and reductions in production delays, stock errors and stock shortages.
We also have an interesting piece by Jon Higson, Managing Director at Titan Manufacturing in Weymouth, who explains how precision engineering is being revolutionised by the next generation of “Smart” CNC machines.
We hope you enjoy this issue and like always, if you have any contributions you would like to feature, please email details to editorial@mpemagazine.co.uk.
Every
Paul Attwood Editor
Commitment to Polymer Ireland Industry Deepens

Sumitomo (SHI) Demag announces its exciting expansion in the Ireland polymer processing market with Kris Thacker appointed as the company’s dedicated technical sales manager in Ireland. As part of this local development phase, the company has also recruited a new service engineer, Cathal Deegan. Offering on-the-ground, responsive support, Kris and Cathal are being supported by global medical specialist Andrew Sargisson, as well as UK and Ireland managing director Dave Raine. The entire team are on hand applying their deep technical knowledge to assist Ireland-based processors in their drive to boost productivity and secure new massmanufacturing opportunities.
Water company leak correlation trials deliver efficiencies
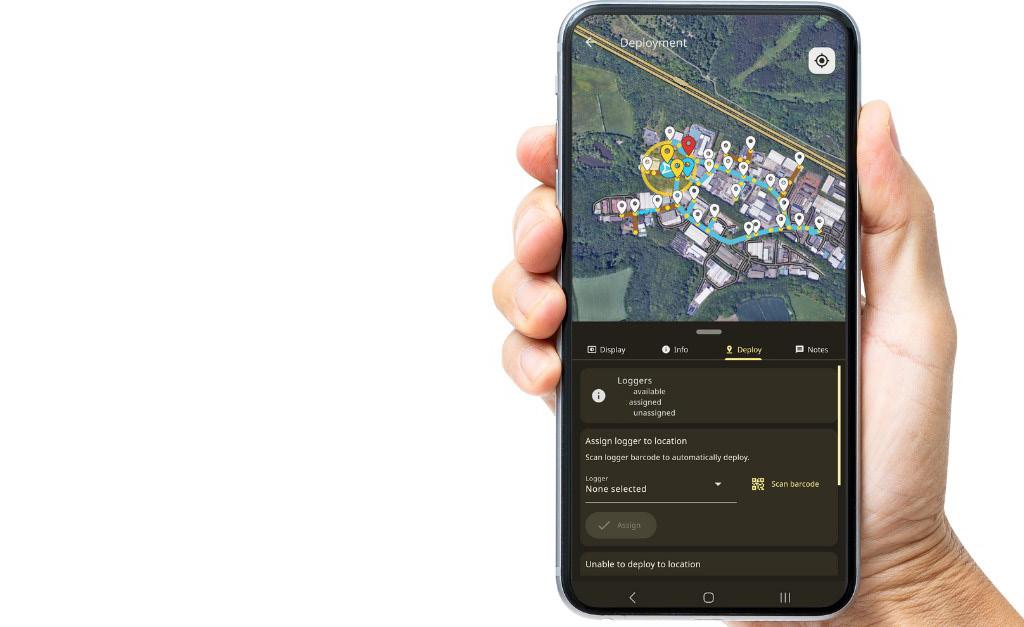
In addition to on-site visits, Kris and Cathal are welcoming processors weekly to the company’s state-of-theart Limerick centre. Here, local and multinational moulders and medical manufacturers are benefiting from having access to state-of-the-art technologies to perform trials and validations. Processors can also access production optimisation training at all levels to help address industry skills gaps.
This latest expansion in 2025 marks the company’s rich history serving processors throughout Ireland.
The Central Statistics Office reports that pharmaceutical manufacturing output in Ireland increased by over 38% in 2023 and has now returned to similar levels documented in 2021. Additionally, manufacturing in Ireland grew 17.1% year-on-year between October 2023 and October 2024.
Sustaining pharmaceutical manufacturing output requires local capabilities and access to dedicated people, tool trial and training facilities; the Sumitomo (SHI) Demag Limerick Centre of Excellence opened in 2023 and combined with the recent appointments, is now fully established and serving the company’s already sizeable customer base in Ireland.
Multiple water companies trialling a new end-to-end leakage detection system from Ovarro have seen significant timesavings and efficiency gains.
EnigmaREACH is an all-in-one correlating kit, comprising 32 or 64 acoustic leak loggers, an app to guide technicians through logger deployment, retrieval and follow-up, and access to Ovarro’s automated data analytics platform.
The managed system supports leakage teams by completing much of the upfront data analysis for users, enabling faster deployment of loggers on a wider scale, and automatically identifying points of interest (PoIs) using advanced correlation techniques. Following the EnigmaREACH launch in July 2024, Ovarro partnered with five UK water companies on trials in targeted district metered areas (DMAs).
For each trial, an Ovarro engineer used the EnigmaREACH deployment tool in the Atrium cloud platform to identify the best locations in
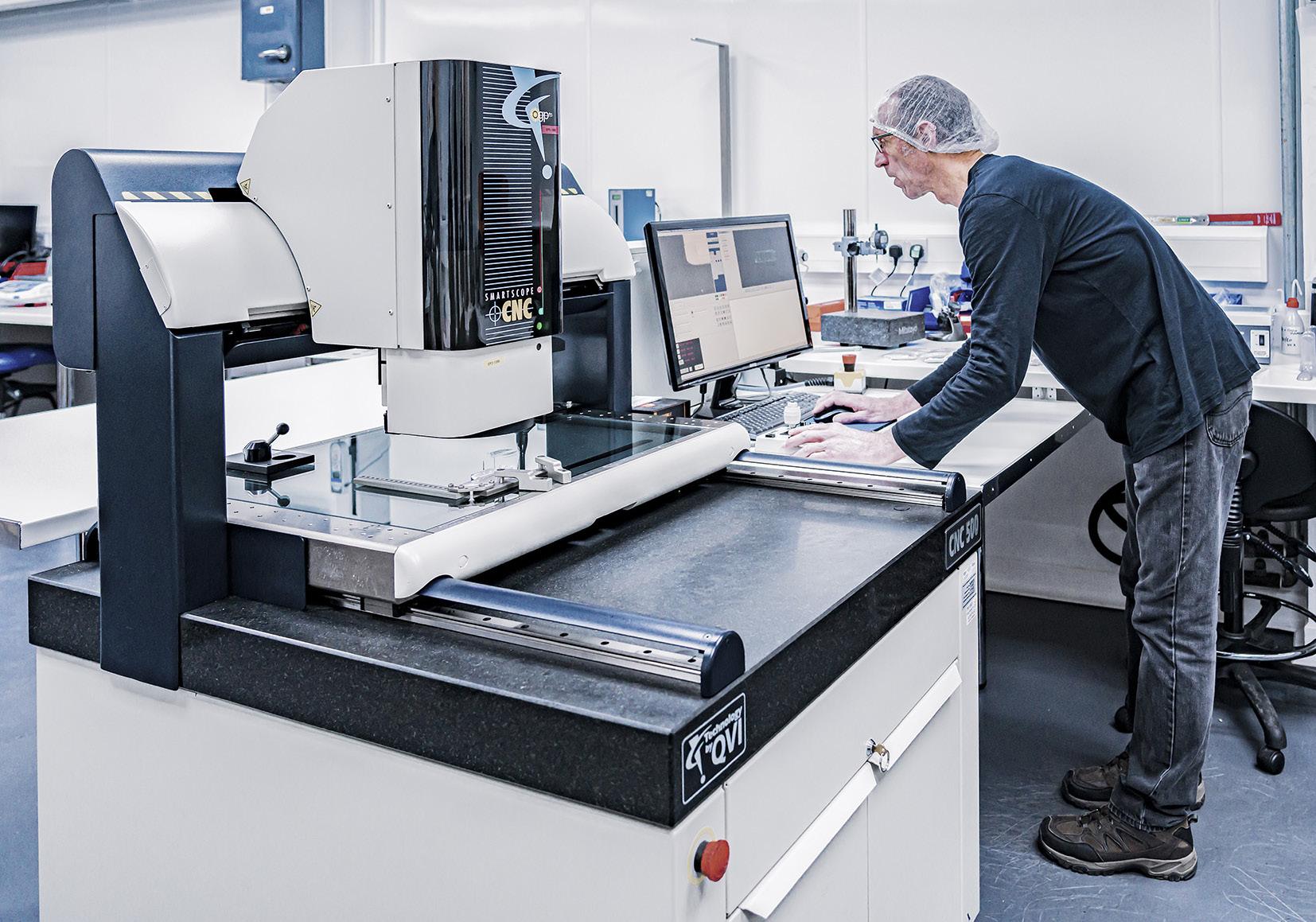
the DMA for up to 32 loggers. The process continues as water company leakage technicians install the loggers and retrieve them the following day using the EnigmaREACH application.
Overnight logger sound files are uploaded to the Atrium platform, which completes the correlation and generates the PoIs for the user to view when they log into the system. The PoIs can then be assigned to technicians to followup directly through the app.
Ofwat’s 2024 price review final determinations challenge companies to cut leakage to the lowest levels since privatisation by 2030, with expected investment of £720m. This is alongside targets to halve leakage by 2050, as part of longer-term water resources management planning.
The targets reinforce the need for companies to capitalise on new technologies and data availability in AMP8, driving the adoption of scalable, end-to-end services.
Europlaz considers acquisition push as 20 new
jobs set to be created
Essex-based Europlaz, which recently launched its own neonatal flow sensor breakthrough, is looking to recruit in customer accounts, projects and production, as it looks to capitalise on a combination of organic growth and a significant rise in its own medical products range.
The family-run business enjoyed a 20% increase in sales to £12.5m in 2024 and is now setting its sights on adding an additional £5m in revenue over the next twelve months, with the management team also hinting at the possibility of embarking on a major acquisition push.
Europlaz, which is ISO13485certified, operates from its stateof-the-art production facility on The Maltings Industrial Estate in Southminster, near Chelmsford.
From here, the business offers injection moulding, assembly, product validation and access to modern cleanrooms, all certified to ISO Class 7 for the manufacture of Class I, Class II and Class III medical devices.
Most of its work is focused on helping medical device and healthcare businesses commercialise new technology, with recent success stories featuring a home dialysis machine, a patient friendly and easy-to-use breath operated inhaler and a bioartificial liver.
The company has invested more than £3.5m into its R&D and production capability to reinforce this reputation and this drives design for manufacturing and industrialisation, ensuring that the product reaches patients efficiently and effectively.
Kavalan and Matic Set New Sustainability Standard in Textile Finishing
Leading manufacturer of low environmental impact PVCfree wide format materials, Kavalan, shares details of its strategic partnership with Matic,
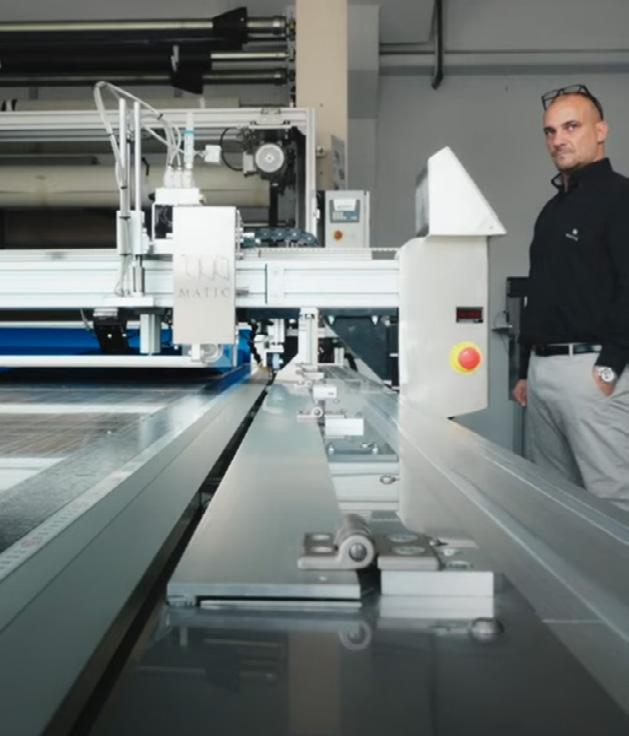
a manufacturer of cutting, welding, and sewing equipment solutions for the textile manufacturing sector. Kavalan and Matic are highlighting the complementary nature of their offerings in a new video shot at Matic’s Barcelona headquarters, which you can watch in full here.
Matic is a business committed to social and environmental goals as well as economic, so when the team discovered Kavalan’s PVC-free materials, it seemed like a perfect match.
Kavalan approached Matic to suggest they trial and evaluate Kavalan’s new industrial textiles, as well as some of the wideformat digital printing materials, a challenge that Matic gladly accepted.
“I am delighted to say the results were flawless,” says Pascal Goiran, Area Manager, Matic.“What impressed me the most was that Kavalan’s innovative textiles welded perfectly with our Perseo 4000 Impulse welding machine in just three seconds, compared to the seven seconds typically required for traditional PVC materials.”
Pascal concludes: “We are proud to partner with Kavalan. I believe their innovative approach aligns closely with Matic’s vision. Their commitment to developing ecofriendly materials sets new industry standards, inspires manufacturers to rethink what is possible, and drives the industry toward better and more sustainable solutions.”
Nova Abbott, Head of Marketing, Kavalan, comments that “Matic’s company principles of symbiosis and shared prosperity are a perfect embodiment of the similar mindset and approach to the market that our businesses have in common, with a strong focus on delivering what our customers need in an innovative and sustainable way.”
BEP Surface Technologies invests half a million pounds on major factory refurbishment
BEP Surface Technologies, a leading provider of surface finishing solutions, has completed a half-million-pound factory refurbishment to drive growth and innovation.
The four-month project dubbed the ‘Black Swan Event,’ overhauled and modernised BEP’s electroplating operations and enhanced its sustainability credentials.
The phased programme, notable for its scale and complexity, involved the removal of large electroplating tanks, with capacities ranging from 4,500 to 15,000 litres, along with all ancillary equipment, including buzz bars, local exhaust ventilation (LEVs), cooling coils, and heating elements.
Over 31,500 litres of chemical solutions, including sulphuric and caustic substances classified as hazardous waste, were extracted and safely disposed of, adhering to strict environmental regulations. The
company retained the chrome tank solutions for reuse, further aligning with its sustainability objectives.
Subsequent phases involved extensive renovation to the pit floor and walls, which was then relined with a robust, chemical-resistant coating. The project concluded with the installation of four newly designed tanks, establishing a foundation for decades of enhanced productivity and reduced maintenance.
Andrew McCluskey, Managing Director at BEP Surface Technologies, commented, “By investing in durable materials and thoughtful design, we have secured a facility that will endure long beyond my tenure at the company. This refurbishment showcases BEP’s commitment to innovation and sustainability, enhancing efficiency and reinforcing our environmental responsibility.”
BEP collaborated with key contractors, including CSG, a
prominent UK waste management firm, for cleaning operations; Arc Fabrications Ltd., for tank fabrication and installation; and Coral Eastern, for concrete and lining services, to ensure the success of this ambitious project.
This extensive refurbishment modernised BEP’s facilities while ensuring compliance with stringent environmental regulations and enhancing long-term operational reliability.
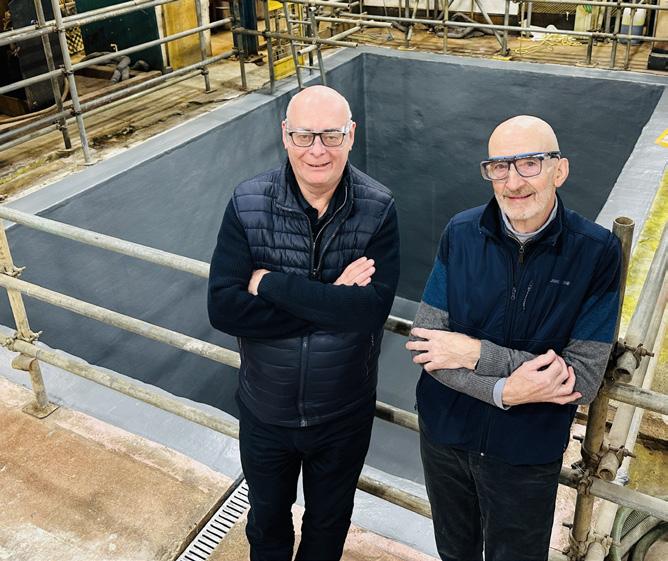
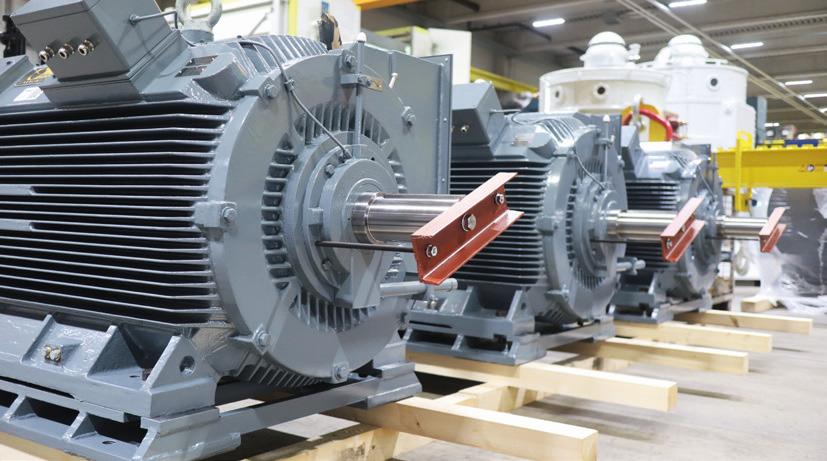
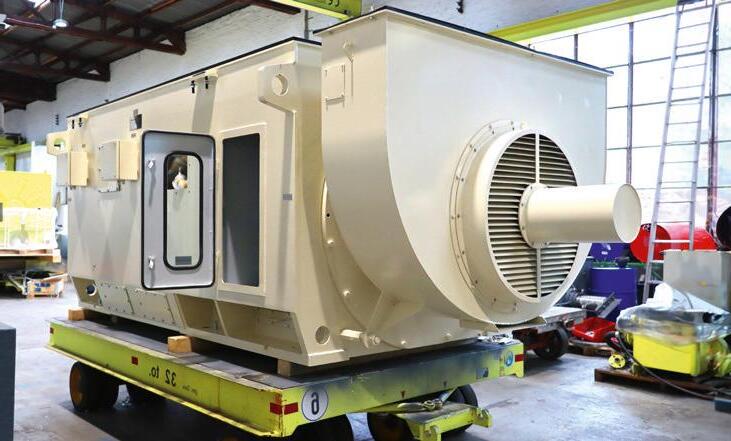

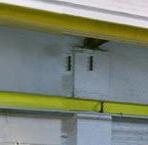
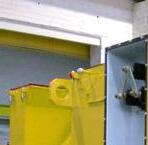

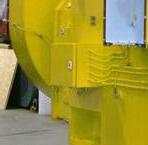


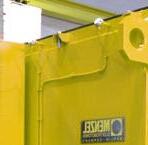
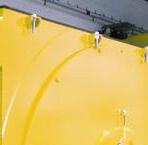
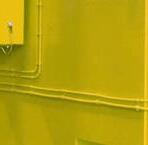

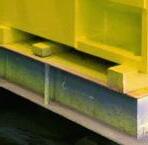
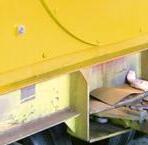
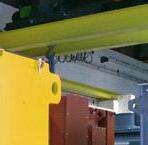
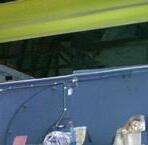

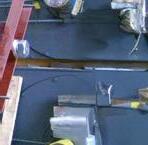
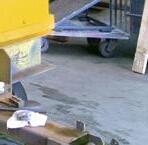
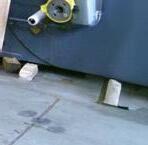
SUPPLIER
SQUIRREL CAGE MOTORS | SLIP RING MOTORS | DC MOTORS
Motors up to 25 MW and 13.8 kV
• Low voltage slip-ring and squirrel cage motors up to 3,000 kW
• Medium voltage slip-ring and squirrel cage motors up to 15,000 kW
• Direct current motors up to 2,000 kW
• Frequency converter-proof drives
• In-house load test facility up to 13.800 V, 2.300 kVA, 120 Hz
Customized special designs
• Custom designs for special applications and operating conditions
• Optimized motor design for higher efficiency
• Mechanically and electrically interchangeable motors
• Commissioning worldwide
MENZEL Great Britain Ltd. | UK Branch Office
Martin Rooney | Tel.: +44 1664 500 844
martin.rooney@menzelgb.co.uk
menzel-motors.com
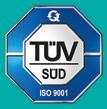
The Impact of Cargo Crime: An Insurance Perspective
Cargo crime is a significant concern in the UK, particularly affecting the manufacturing sector due to the high value and volume of goods in transit. In 2023, the National Vehicle Crime Intelligence Service reported 5,373 cargo theft cases, resulting in an estimated £68 million in stolen goods. This growing threat underscores the necessity for enhanced security measures to protect businesses from financial losses, operational disruptions, and reputational damage.
Key Risk Factors for the Manufacturing Sector
• Geographic Vulnerabilities: Ports, distribution hubs, and transit routes are prime targets for cargo theft due to the high volume of goods passing through these areas.
• Insufficient Security Investment: A lack of robust physical, digital, and operational protection measures increases the risk of theft.
• Insider Threats and Organised Crime: These elements can exploit employees for access to sensitive information.
• Complex Supply Chains: Reliance on third-party logistics providers makes manufacturers more susceptible to cargo theft.
Risk Management Strategies for Manufacturers



Preventative Measures
• Upgrading Physical Security: Investing in GPS tracking, tamper-proof locks, and secure vehicle parking can reduce theft risks. Surveillance systems at warehouses and distribution hubs also deter criminal activity.
• Conducting Supply Chain Audits: Regular audits help identify vulnerabilities, enabling targeted improvements to mitigate risks.
• Employee Training: Training programs raise awareness, guiding workers to recognise and report suspicious activity, thus spotting internal threats early.
Technology Solutions
• Leveraging AI and IoT: These systems analyse real-time data to detect patterns and potential threats, providing early warnings.
• Enhancing Cybersecurity: As logistics systems digitise, prioritising cybersecurity protects against hacking and ransomware. Stringent protocols safeguard the supply chain.
Collaboration and Partnerships
• Working with Logistics Providers
and Experts: Collaborating with logistics providers and risk management professionals ensures consistent security protocols throughout the supply chain. Sharing strategies reduces vulnerabilities.
Insurance and Financial Protection
Comprehensive cargo insurance mitigates the financial impact of theft. Manufacturers should work with risk advisors to ensure policies cover potential losses, including exclusions, coverage limits, and recovery costs.
How Gallagher Can Help
Mitigating cargo crime is crucial for protecting assets and maintaining operational efficiency. Partnering with a risk management specialist like Gallagher provides the expertise and tailored solutions needed to reduce exposure to such risks. We help businesses prioritise security, enhance collaboration, and implement proactive strategies to safeguard physical and financial assets.
Scan the QR code to contact us and explore how Gallagher can help secure your cargo risk.

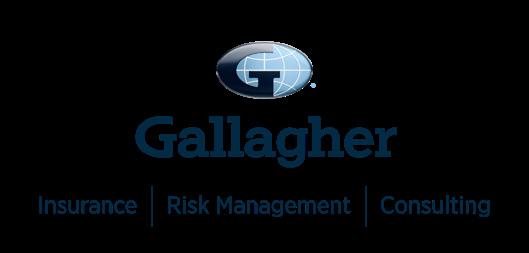


Manufacturing Insurance Designed Around Your Business
Gallagher offers the strength and positioning of a global insurance group, combined with the personalised care and attention of a local UK broker. With a rich history dating back to 1927, we believe we have the expertise and experience to meet your manufacturing insurance and risk management needs. For further information, please scan the QR code. CONNECT WITH A SPECIALIST TODAY.
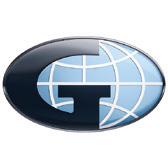
Interview with Oana Jinga, CC&PO and Co-Founder at Dexory
We speak to Oana Jinga, Co-Founder and Chief Commercial & Product Officer at Dexory, a UK-based leader in warehouse optimisation through robotics, data analytics, and automation. In her role, Oana oversees the development of DexoryView, an innovative solution that integrates autonomous mobile robots (AMRs) with AI-driven analytics to create real-time digital twins of warehouses. This technology improves efficiency, reduces errors, and enhances inventory management for industries like logistics and manufacturing.
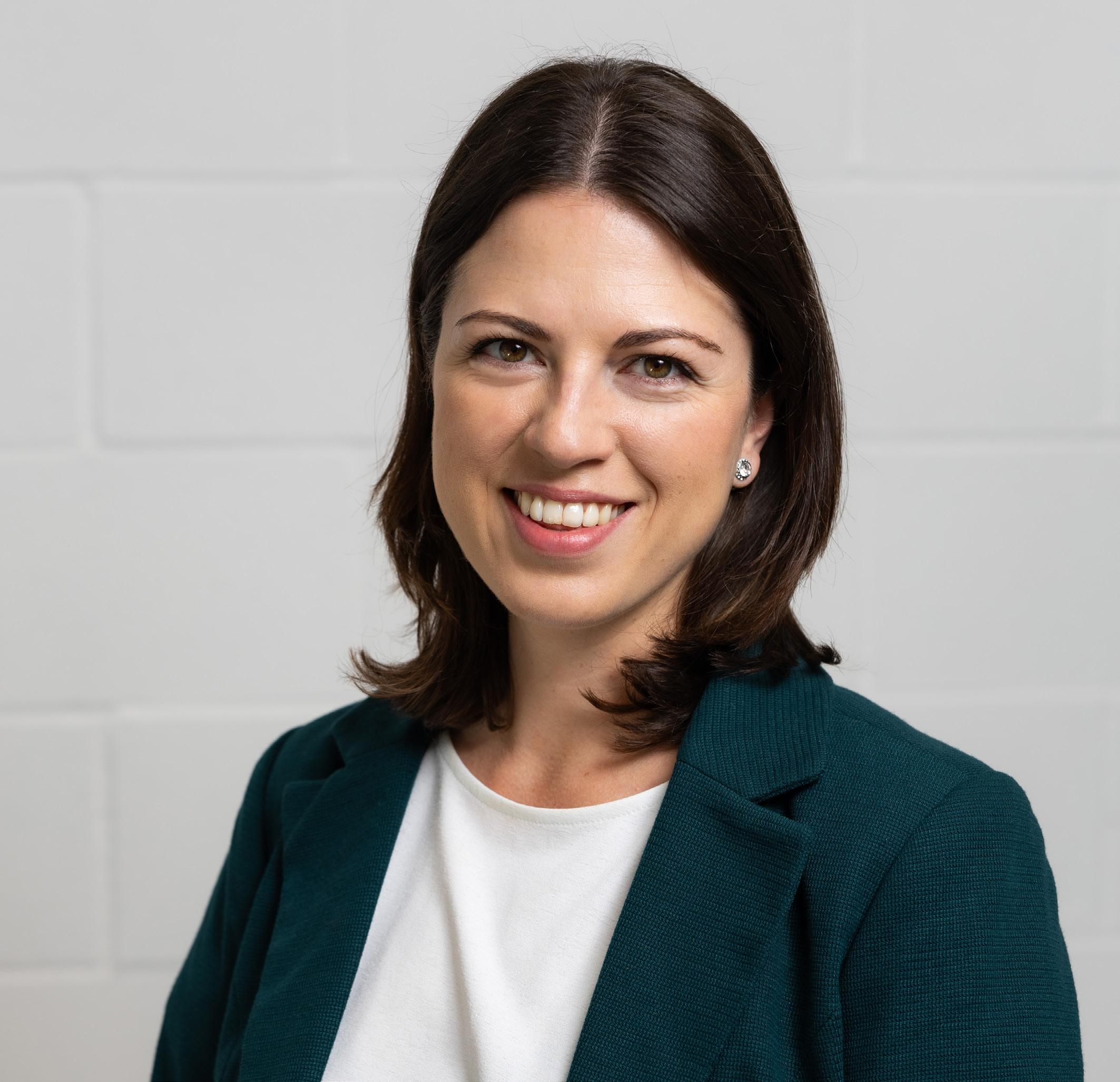
In this interview, Oana shares insights into how Dexory is shaping the future of warehouse automation, addressing industry challenges, and driving sustainable, data-driven operations.
What inspired the creation of Dexory, and how does your approach to warehouse optimisation differ from other solutions currently available in the market?
Dexory was founded with a vision to revolutionise warehouse operations by bridging the gap between realtime data and actionable insights. The inspiration stemmed from recognising inefficiencies in traditional warehouse management—where outdated, static snapshots of inventory and operations often lead to costly delays and underutilised space.
Unlike other solutions that focus solely on partial automation or reactive data, Dexory takes a holistic approach by combining fully autonomous mobile robots (AMRs) with AI-driven analytics. Our technology continuously captures real-time data, creating a complete digital twin of warehouse operations. This enables businesses to make instant, informed decisions, improving efficiency, reducing costs, and enhancing adaptability in a rapidly evolving supply chain landscape.
Could you explain how your DexoryView technology leverages autonomous mobile robots (AMRs), AI, and machine learning to create a digital twin of a warehouse? How does this enhance operational efficiency?
DexoryView is an intelligence platform powered by our fleet of AMRs, which autonomously navigate warehouses to scan and collect high-precision data and images of inventory, storage utilisation, and operational workflows. Using AI and machine learning, this data is processed and visualised as a real-time digital twin, a fully interactive, virtual replica of the warehouse.
This technology enhances operational efficiency by providing continuous visibility into the integrity, health and hygiene of the warehouse, reducing costs associated with lost or misplaced goods. We also enable real-time decision-making, allowing operators to optimise picking routes,
detect bottlenecks and adjust layouts dynamically. We are also enabling our customers to forecast their inventory needs, minimise downtime and allow them to use their labour more efficiently.
By integrating DexoryView, warehouses can move from reactive management to proactive optimisation, ensuring seamless, data-driven operations.
In the context of manufacturing and production, what specific challenges can your solutions address, and what measurable benefits have clients experienced after implementing your technologies?
Manufacturing and production environments face significant challenges, including:
• Inventory mismanagement, leading to production delays and inefficiencies.
• Manual stock checks, which are labour-intensive, error-prone, and time-consuming.
• Lack of real-time insights, making it difficult to optimise workflows and predict supply chain disruptions.
DexoryView tackles these initial issues by providing continuous, automated inventory tracking and real-time visibility into warehouse stock. As a result, our clients have reported:
• Up to 90% reduction in stock discrepancies, leading to fewer production stoppages.
• Fully automated inventory audits, freeing up staff for higher-value tasks.
• Optimised warehouse layouts, improving material flow and increasing throughput.
By digitising and automating inventory and workflow management, manufacturers achieve greater precision, reduced costs, and improved operational efficiency.
Data accuracy and security are critical in automation. How does Dexory ensure the reliability and security of the data collected by its AMRs?
At Dexory, data integrity and security are at the core of our technology.
We employ a multi-layered approach to ensure both the reliability and protection of warehouse data. We have methods in place that secure the data and have implemented processes and procedures that protect our platform. By implementing these measures, Dexory ensures that businesses can confidently rely on secure, real-time data to drive automation and decisionmaking.
As robotics and automation continue to evolve, what trends do you foresee shaping the industry over the next five years, and how is Dexory positioning itself to stay ahead of these developments?
The next five years will see a rapid transformation in robotics and automation, with several key trends shaping the industry:
1. Hyper-automation & AI-driven decision making – AI will become increasingly embedded in warehouse operations, enabling predictive analytics, self-learning systems, and automated decision-making. Dexory is investing heavily in AI development to ensure our platform remains at the forefront of intelligent automation.
2. Interconnected supply chains –Warehouses will move beyond standalone operations to become fully integrated into smart supply chains, with real-time data sharing across stakeholders. DexoryView is designed to facilitate seamless integration with broader logistics networks
3. Labour augmentation, not replacement – Automation will complement human workers rather than replace them, helping to address skills shortages while enhancing productivity. Our solutions are designed to empower teams with better tools and insights.
4. Scalability & flexibility – Modular, plug-and-play robotic systems will dominate, allowing businesses to scale automation gradually. However, DexoryView is built for adaptability and speed of installation, ensuring businesses can expand their capabilities as needed.
5. Sustainability in automation –Energy efficiency will play an increasing role in warehouse and
Interview
logistics operations, especially as companies strive for various Net-Zero targets. This means that organisations will be looking at things like power and electricity consumption, their own supply chains and how.
By staying ahead of these trends, Dexory continues to shape the future of intelligent warehouse automation.
Can you share a success story or case study where your solutions transformed operations for a manufacturing or logistics client? What were the key takeaways from this project?
Customers such as DENSO Manufacturing UK (DMUK) use stateof-the-art technology to operate in a just-in-time environment, DMUK carries out a wide variety of processes to produce plastic mouldings, aluminum pressings, heat exchangers and pipe and hose components. These supply in-house final assembly lines and kitting operations before delivery to internal warehousing and dispatch areas.
DENSO’s day-to-day challenges Ensuring comprehensive oversight of stock and storage operations is critical for manufacturers.
The process of stock-taking is widely recognised as a labour-intensive and time-consuming task that numerous warehouse operations tend to sidestep. Inaccuracies in stock can have an immediate and profound impact on production lines - all the way to stopping manufacturing.
Dexory introduced autonomous robots to scan the entire warehouse, building a digital twin for real-time data analysis and insight into the storage of goods, enabling DENSO to monitor and fix inaccuracies and secure thorough control over stock.
Providing the solution and results Dexory’s fully autonomous robot navigates aisles to check each and every rack location - avoiding obstacles and complying with established warehouse procedures.
The robot scans racks to identify empty locations and locate pallets of components in real-time, quicker and more accurately than when completed manually. By comparing the data collected in the real warehouse environment with existing WMS (Warehouse Management System)
stock records, Dexory reconciles inconsistencies and closes the data loop.
The end goal is to build a warehouse digital twin that offers real-time intelligence to inform and ensure zeroerror procurement, with no disruptions to the production line and the wider supply chain across all DENSO sites.
They have seen remarkable results from the beginning:
• Increase accuracy: Validated accuracy levels above 99%.
• Production delays: Reduced production delays associated with stock inaccuracies to zero.
• Stock errors: Led to zero stock errors throughout the first week of operation.
• Stock outages: Avoided multiple stock outages on parts from day 1 of operation.
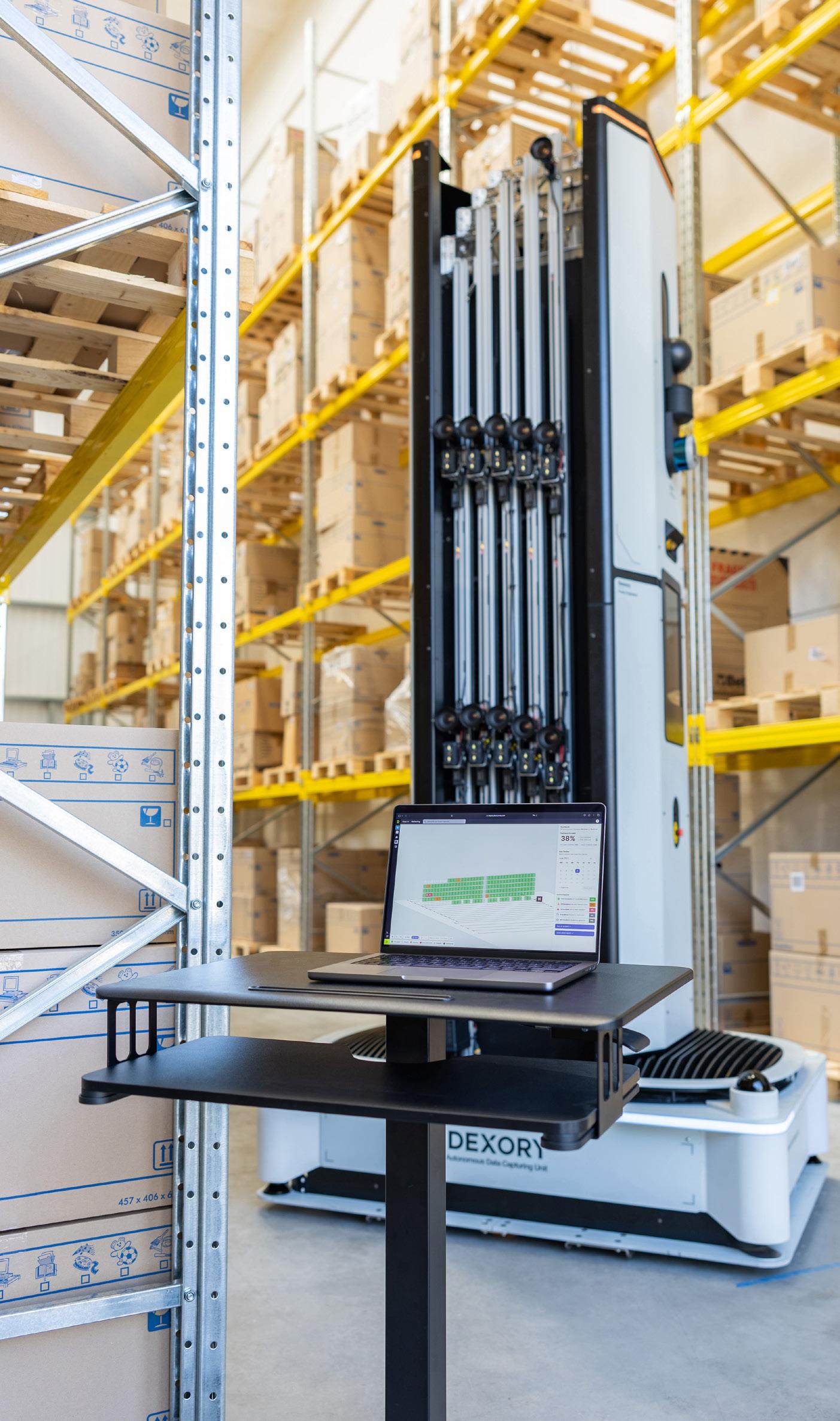
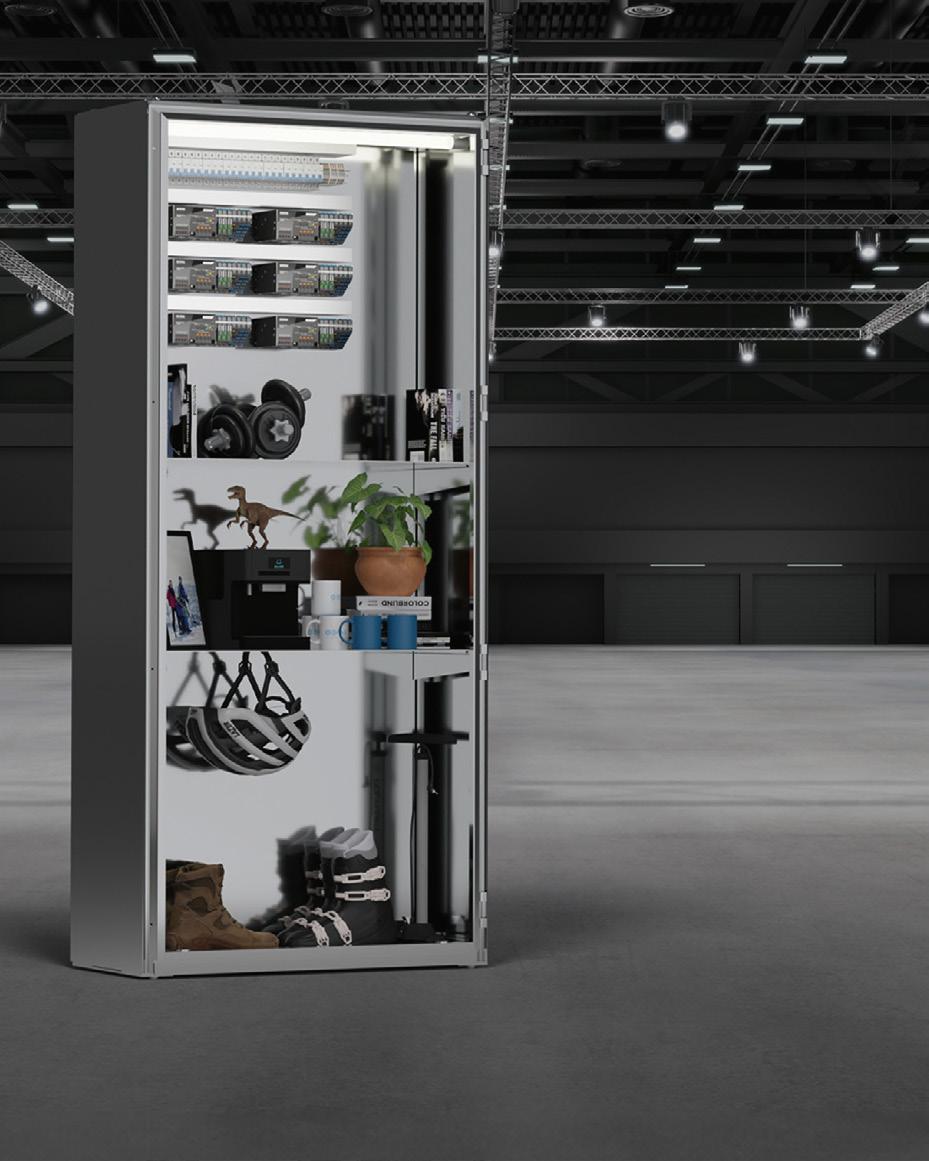
e-t-a.co.uk

Mech a nical Integrity Training with reality built
in…
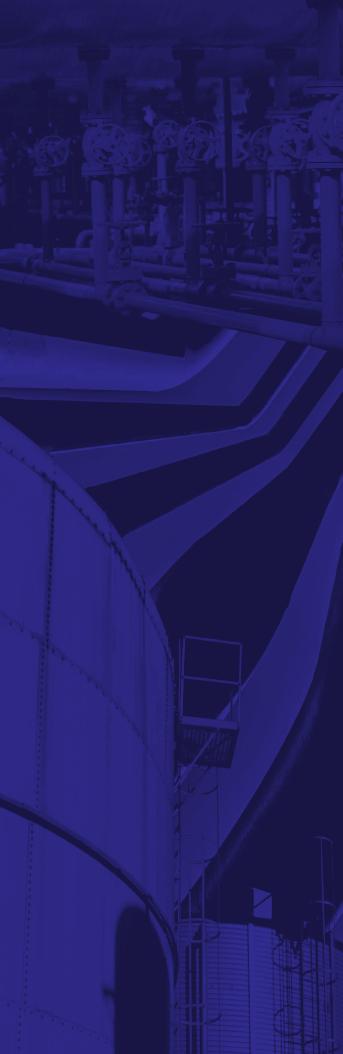
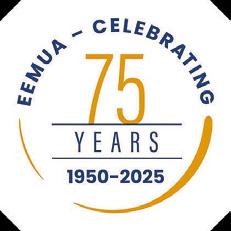
Developed and verified ‘for industry, by industry’, EEMUA 231 Mechanical Integrity courses are for industrial engineers at every competency level in their career. Aiding efficient hands-on work with primary containment (including pressure systems) – to prevent loss of hazardous substances.
• Courses throughout e each year
• Certificated for up to 5 years.
• CPD-approved
• Flexible for learners and companies.
• Cover: * Legislative environment * WSE
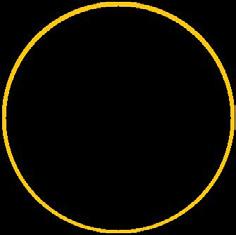

* Industry good practice * ALARP * Asset condition * Equipment design * Operational considerations * Test techniques * Inspection roles, process & reports * Postponement
* Responses to findings * Record keeping
* Audit * Feedback * Operating Limits
* Decision Making * and More.
• Open to all – free or discounted to EEMUA Members.
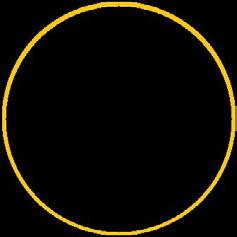

Asset Integrity Leadership Certificate –
Blended, online learning – Leadership level – with a flexible 3 hours of learning per week for 16 weeks – 55 hours' CPD – certificated via exam – tailored to each Learner, company and site/s via a 2-hour induction – next course starts 31 March 2025.
Mechanical Integrity Practitioner
Certificate (MIPC®) – blended, live online learning – on-site or on-call –1:1s and Mentor Support – workbook builds from day-1 for immediate use in on-site application of EEMUA 177, 231 and 232 guidance, and the PSSR ACOP
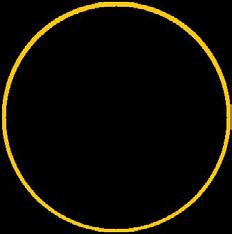

–certificated for 5 years via exam and portfolio assessment – in-depth learning for 27 weeks, flexible 4 hours per week – CPD of 110 hours. The MIPC course adapts to engineering needs of each Learner their company and site/s via a 2-hour induction (made to fit work schedules ahead of the course) –learning starts 20 October 2025.
EEMUA 231 Mechanical Integrity Basics –
Blended, online learning – Basic application competency level – with a flexible 4 hours of learning each week for 3 weeks – 15 hours' CPD – certificated via exam –next course starts 29 September 2025.
EEMUA 231 Mechanical Integrity e-learning –Awareness level – with 1 hour of CPD – immediately available – on-demand
EEMUA 231 Mechanical Integrity In-house training – at the Awareness level – CPD – 1 day or 2 half-days – by arrangement – for your choice of time, location, and method of learning – certificated
Also... EEMUA Conference 2025 Cheshire, UK – 26-27 March 2025
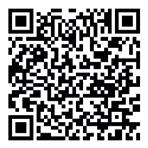
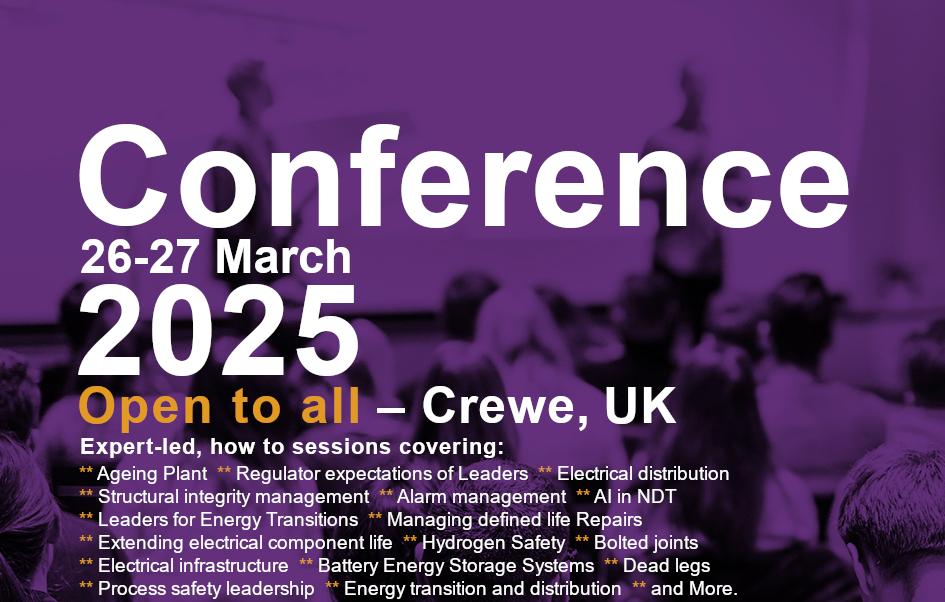
Motor precision is crucial for aircraft electronic expansion valves Mechanical Engineering
Within an aircraft cabin, an Environmental Control System (ECS) is essential, both for safety, as well as the comfort of passengers and aircrew. This technology regulates the pressure and temperature within the cabin, and integral to the system are the valves that control airflow. Particularly for the management of air conditioning and refrigeration, the electronic expansion valve (EEV) is key. With the role of precisely controlling refrigerant flow, these valves enable efficient temperature regulation onboard.
An electric motor actuates the electronic expansion valve via signals received from the ECS controller, which monitors cabin temperature. The motor drives precise valve regulation to control refrigerant flow into an evaporator. While the evaporator is fed by air from outside the aircraft, which is heated by compression or through bleed air from the engine, the blend of refrigerant balances air temperature within the cabin.
The advantage of an electric motor and controls is variable modulation, and it’s this flexibility that is crucial to fine-tune refrigerant flow and optimize passenger and crew comfort. The motor must be able to achieve the required level of precision, and stepper motors are the typical choice. This motor design opens or closes the expansion valve in small, controlled steps; these increments are measured in fractions of a degree, dependent on the resolution of the motor, and this
adjustment achieves precision in valve control.
Crucially, the stepper motor also ensures repeatable control. Since it moves in discrete steps, with each step corresponding to a fixed angular movement, this enforces its precision. Enhancing control repeatability, a stepper motor also provides the higher torque required for the relatively low speed operation of the valve. This means that the stepper motor can generate sufficient holding torque to maintain its position without losing steps when under pressure of the refrigerant.
Although an aircraft’s ECS should include redundancy, protecting against motor failure is vital to minimize the cost and time of maintenance. The design of the stepper motor is inherently durable as it doesn’t rely on mechanical brushes to achieve commutation, and neither does it need a feedback device or a complex closed-loop controller. This simplicity also helps secure a lower cost in procurement. However, when selecting a stepper motor, it’s essential to ensure it can withstand temperature extremes, including temperatures up to 130 degrees Celsius faced by the evaporator, as well as the low temperatures of the refrigerant.
Low weight and size are also important to improve an aircraft’s fuel efficiency and cargo-carrying capability. Stepper motors achieve high torque density for their low-speed operation
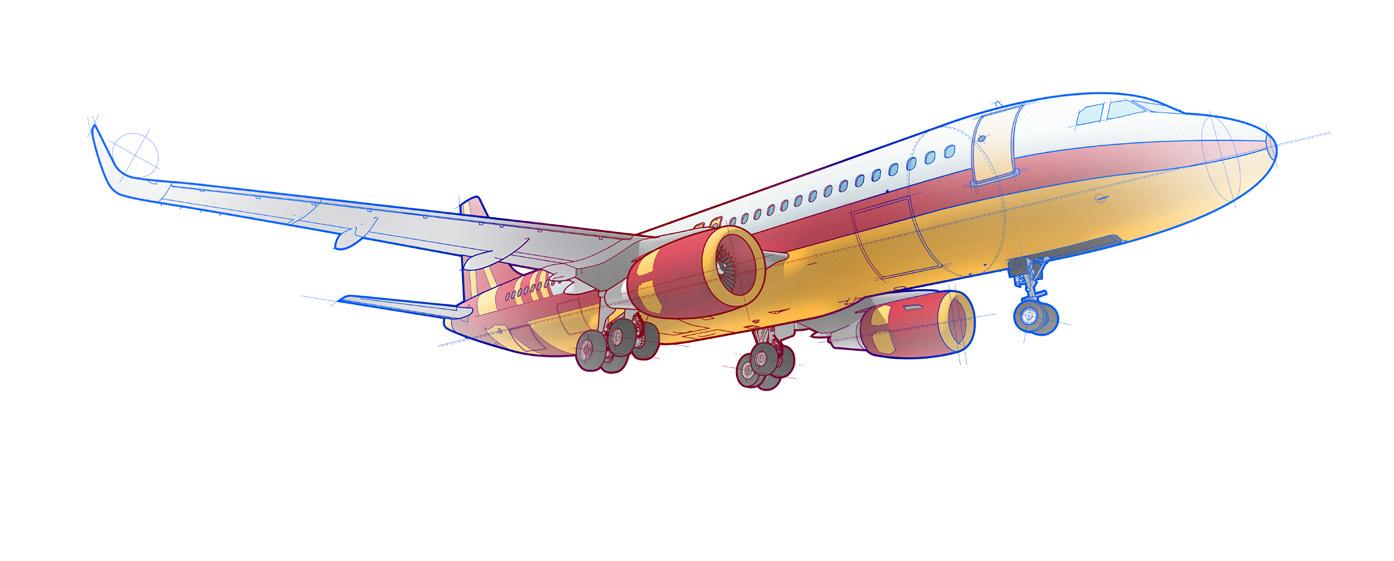
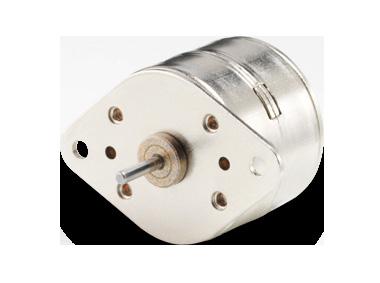
requirements, and as they don’t require complex external electronics or feedback, this advantage reduces the total weight and size of the package. In addition, can stack stepper motors can also be advantageous for some EEV applications. Can stack motion technology focuses on simplicity. This permanent magnet stepper motor uses the simplest of techniques and designs to create an effective solution where reasonable accuracy and moderate torque are required.
As an alternative to stepper motors, brushless DC (BLDC) motors could be used to enhance the speed and efficiency of control, while minimizing form factor and weight. While this design adds cost, alongside the need for external electronic controls, it could provide an advantage for aircraft that need more rapid changes in cabin temperature control. The more efficient operation of a BLDC motor can also add reliability and minimize the potential for overheating when under duress.
As part of motor specification, customization might also be required, particularly to enhance design integration. Features such as customized mounting plates and output pinions might be necessary, as well as modifications to the motor itself. This approach not only minimizes the time and cost of internal development, but the experience in motor customization helps to ensure performance and reliability is maintained.
An ECS relies on valve control to regulate pressure and temperature within the aircraft.
Can stack technology achieves reasonable accuracy and moderate torque.
One of Sheffield’s newest manufacturers is helping to revitalise the city’s industrial capabilities with cutting-edge materials processing technology.
Sheffield Technology is winning a growing customer base, with some key projects being attracted back to the UK from overseas. The company is eager to leverage its ability to rapidly laser-cut materials up to 60mm thick— made possible by the company’s investment in a state-of-the-art 24kW Trumpf 5060 TrueDisk laser.
With fully automated material and part handling, this machine boasts a 6-metre by 2-metre plate capacity and can cut: Stainless steel, armour, carbon, and alloy steels – up to 60mm thick, Aluminium – up to 40mm, Copper – up to 16mm and Brass – up to 12.7mm.
Beyond laser cutting, Sheffield Technology’s extensive fabrication and machining capabilities include a 400-tonne, 5.1-metre press brake and automated cobot welding, allowing the company to deliver fully integrated manufacturing solutions.
Darren Mason, Works Director at Sheffield Technology, explained: “The big advantage for us is that we have truly disruptive technology. Our high-power laser operates at a scale and precision that challenges conventional thinking. While most lasers struggle beyond 30mm, we comfortably cut up to 60mm, allowing us to compete on both quality and cost with traditional heavy-duty processes, such as plasma & profile cutting.”
The company’s rapid expansion is reflected in its workforce growth, scaling from just 10 employees last year to 58 today, including four apprentices. With a firm commitment to developing future talent, Sheffield Technology plans to expand its apprenticeship program to pass on engineering skills that have defined the city for generations.
Looking ahead, Darren commented: “We’re proud to be back in Sheffield,
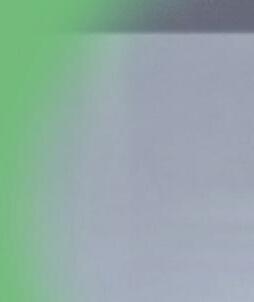
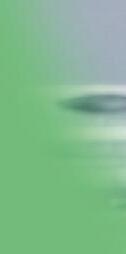
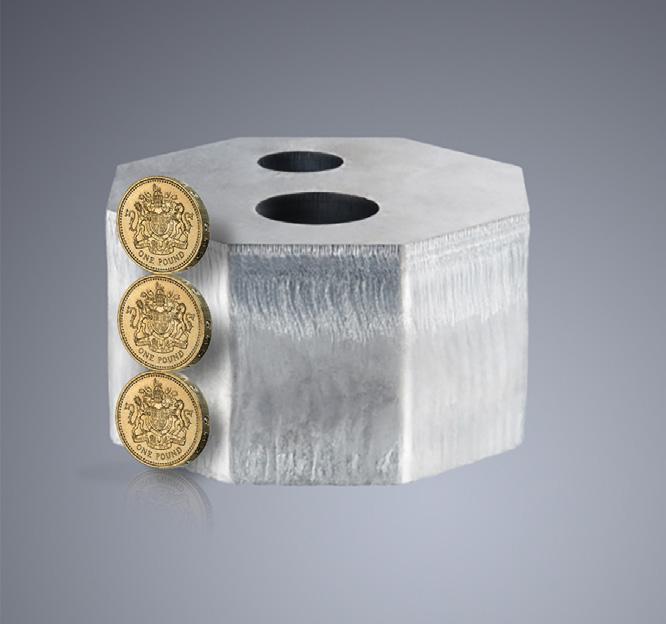
helping to underpin its metal processing history, and we trust the city will continue to attract work from across the country and beyond. Our capacities and state of the art equipment really do support continued competitiveness within the UK in this important sector, underpinning jobs for our young people in the years ahead.”
Sheffield Technology’s innovation and investment in advanced manufacturing can only support the city remaining at the forefront of British materials processing & manufacturing industry.
sheffield-tech.com
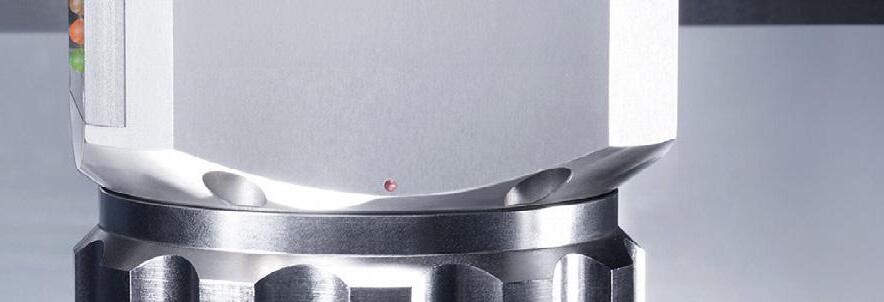
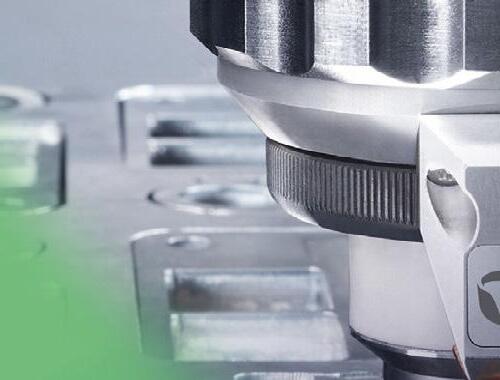
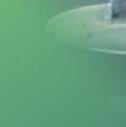
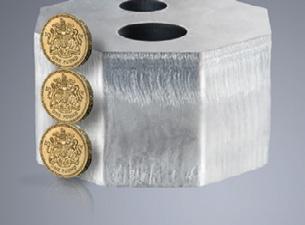
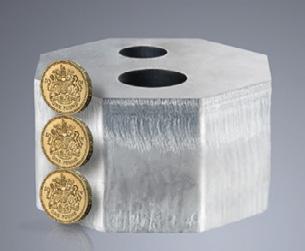
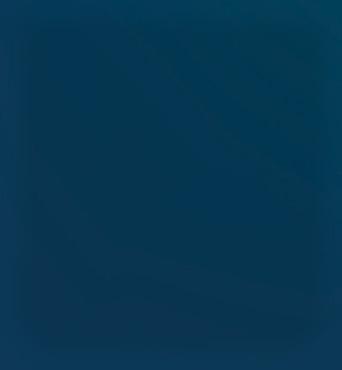
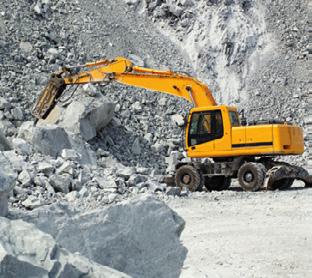
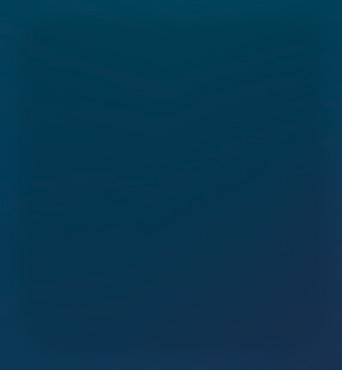
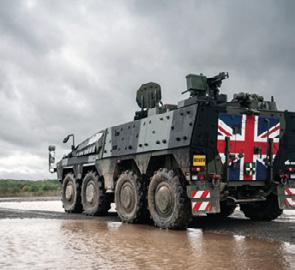

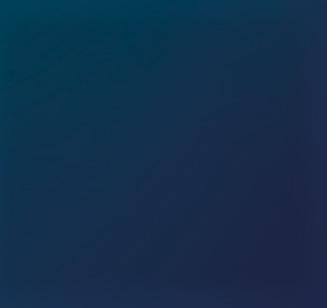
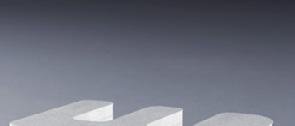
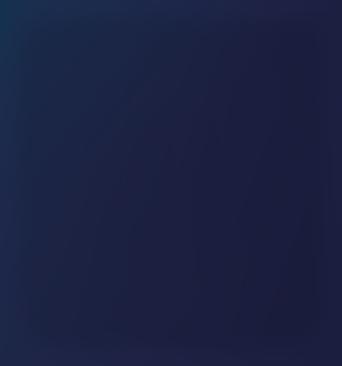
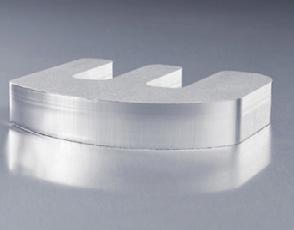
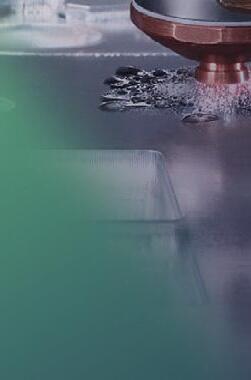
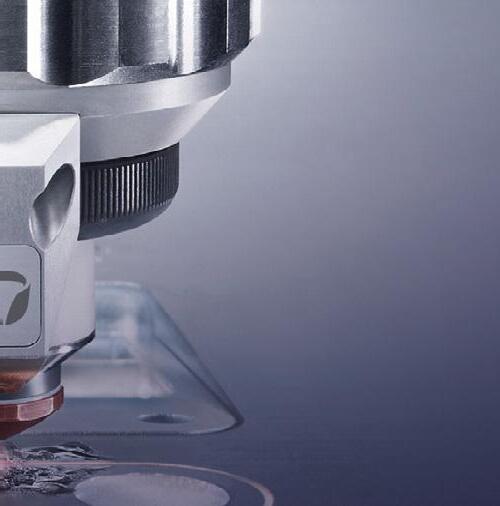
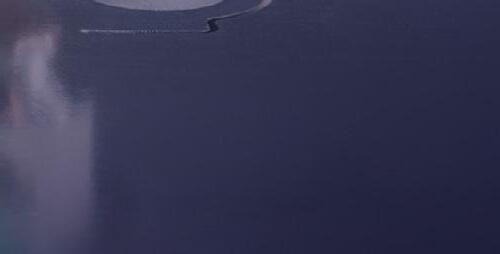
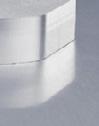
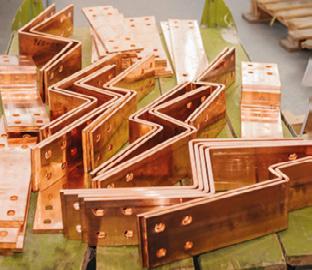
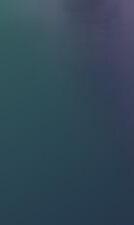

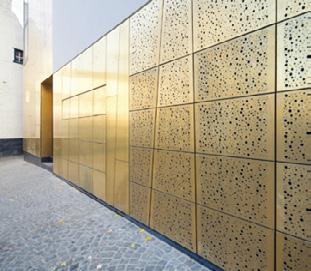

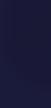

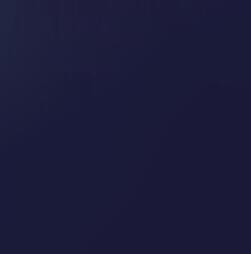
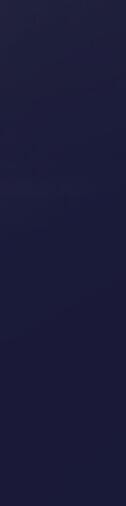
Events & Awards
Celebrating 100 Years of REO : A Century of Innovation and Resilience
This year marks a significant milestone in REO’s history as the company celebrates 100 years of innovation, engineering excellence, and enduring customer commitment.
Founded in 1925, REO emerged at a time when technological advancements were rapidly transforming industry. From early electrical components to the sophisticated power solutions of today, the company has continuously evolved to meet the needs of an ever-changing world. Throughout the decades, REO has navigated global challenges, economic shifts, and the rapid pace of technological progress, maintaining its reputation for reliability and innovation.
One of the defining aspects of REO’s longevity has been its ability to adapt.
As industries evolved, so too did the company’s approach to engineering. Transitioning from traditional electrical components, typically used for lighting control and motor speed adjustment, to specialised solutions in railway, medical, and industrial automation sectors underscores this adaptability. The company’s development of passive harmonic filters, sinewave filters, and chokes is a testament to its focus on ensuring efficiency, safety, and compliance in an increasingly complex technical landscape.
Beyond technological advancements, REO’s success has been built on the dedication of its people. Generations of engineers, designers, and technical experts have contributed to the company’s progress, each playing a role in shaping its legacy. Equally important has been the trust and support of customers and partners
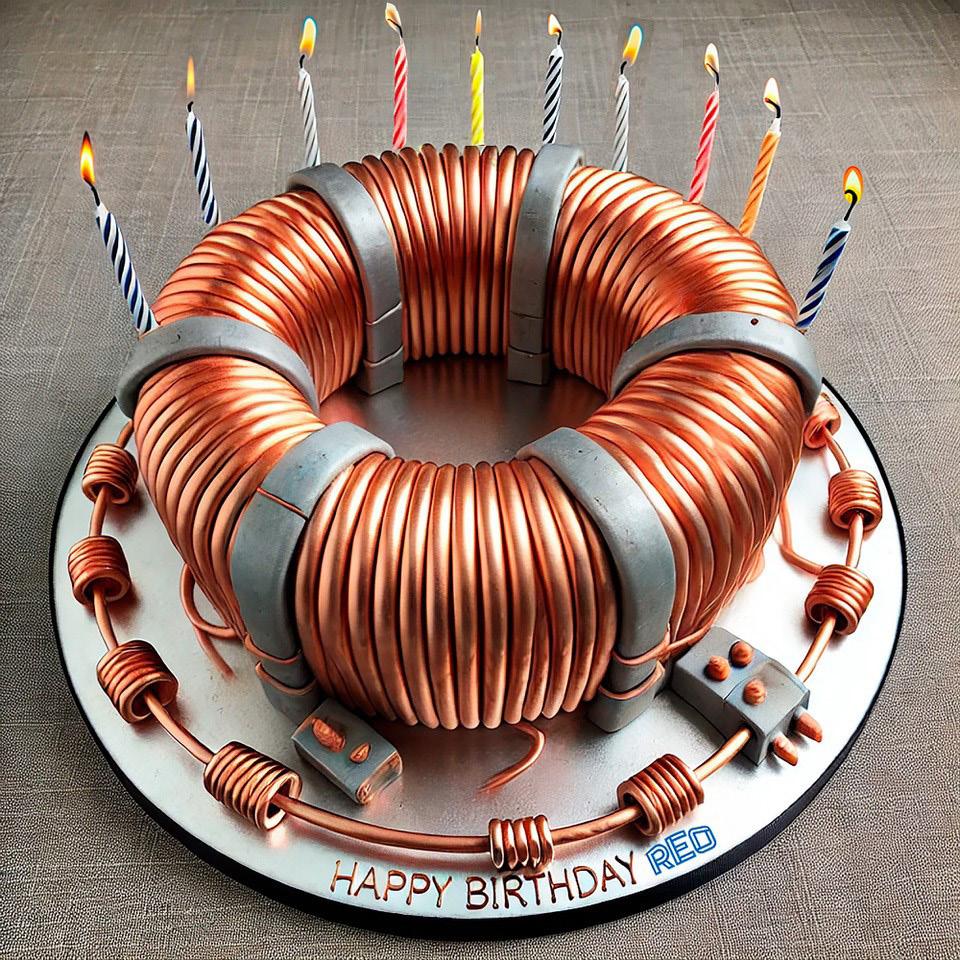
Founded in 1925, REO emerged at a time when technological advancements were rapidly transforming industry.
who have worked alongside REO over the years. Their collaboration has driven innovation and ensured solutions remain effective and practical in real-world applications.
While celebrating the past, it is equally important to look forward. The sustainability, energy efficiency, and digital transformation challenges present obstacles and opportunities. With a strong foundation built over a century, REO is well-positioned to continue its journey into the future, embracing emerging technologies while staying true to its core values of quality, reliability, and customer focus.
CEO of REO Group, Philip Twellsieck, explains ‘this makes me very proud as it means we can compete effectively with our philosophy internationally, even against other companies where there is usually a different corporate culture. That tells us we are on the right path.’
A centenary is not just a measure of time but a recognition of perseverance, adaptability, and vision. As REO marks this momentous occasion, it does so with gratitude for the past and enthusiasm for what lies ahead. The next chapter promises to be as dynamic and impactful as the last, ensuring that REO remains a key player in power quality solutions for many years.
For more information please visit www.reo.co.uk or call 01588 673441

Latest Product Launches
Innovating High Throughput Tube Marking
AFYS3G has announced the launch of Information Marking System
Lambda768, a laser marker designed to optimize sample processing by offering unmatched speed, flexibility, and ease of use, providing laboratories with a highly efficient solution for tube marking.
The new laser marker can mark up to 8 ANSI/SLAS racks simultaneously, and is capable of handling mixed formats in a single run, making it incredibly versatile for laboratories that work with varying tube types, compatible with tubes from brands like Micronic, Azenta, and LVL Technologies.
The Lambda768 offers flexibility in its engraving capabilities, allowing for high-resolution laser markings of images, logos, text, batch IDs, and more, all directly on the tube surface.
Equipped with an intuitive touchscreen interface and userfriendly software, the system allows laboratory staff to operate it with ease, regardless of technical experience. Additionally, an internal camera monitors the marking process in real-
time, ensuring optimal quality control.
Built to meet the evolving demands of modern laboratories, the Lambda768 offers a fast, flexible, and
durable solution for tube marking, whether managing research samples or processing high-volume tubes, the Lambda768 ensures precise, highquality results every time.
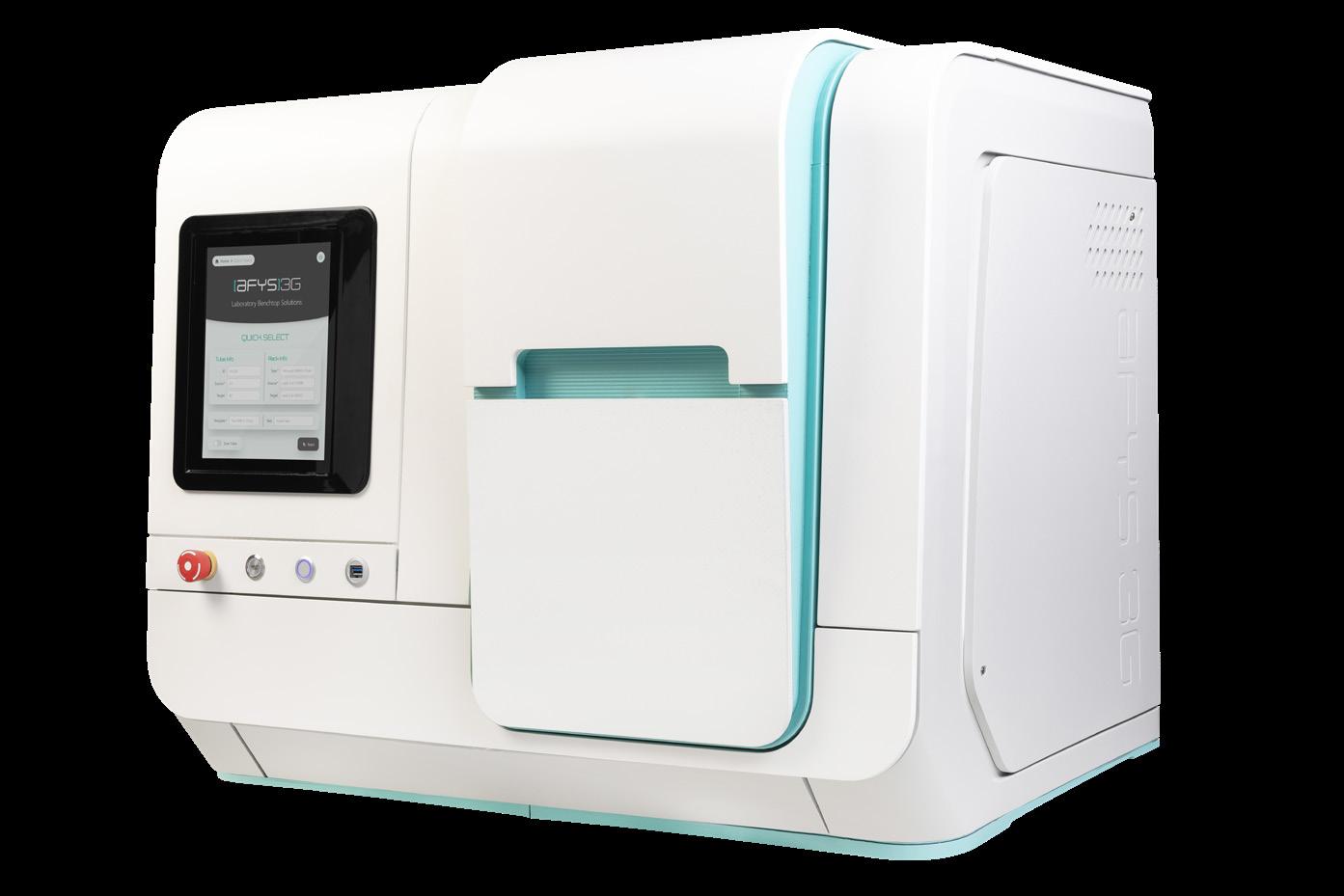
Altus Group Launches New X-ray Inspection Services for Electronics Manufacturers
Altus Group, distributor of production equipment and consumables for the electronics manufacturing sector in the UK and Ireland, has announced the launch of its new X-ray inspection services.
This addition is designed to help manufacturers optimise their production processes and maintain the highest standards of quality
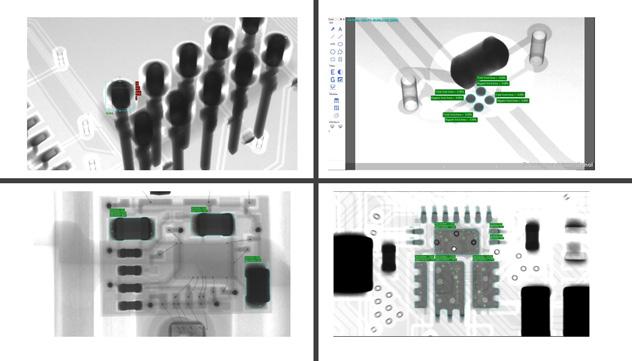
through non-destructive testing solutions where owning a unit outright themselves may be difficult to justify.
Known for its complete turnkey solutions across SMT and THT assembly, back-end processes, and component management, Altus now offers advanced X-ray inspection services using the Xspection 3000 system from Scienscope.
This state-of-the-art 2D X-ray machine features a high-power microfocus sealed X-ray tube, spot sizes as small as 5µm, and a wide range of inspection capabilities for PCBA and final assembly needs. The service supports customers with rapid, high-quality inspections, from initial process validation during NPI to field failure analysis.
The new service offering is part of Altus’ broader strategy to operate as a one-stop shop, providing customers with flexible, high-quality solutions that can help streamline their operations and improve their products.
The
new service offering is part of Altus’ broader strategy to operate as a one-stop shop, providing customers with flexible, highquality solutions that can help streamline their operations and improve their products.
Latest Product Launches
Fast and precise zero cuts without repeated measuring
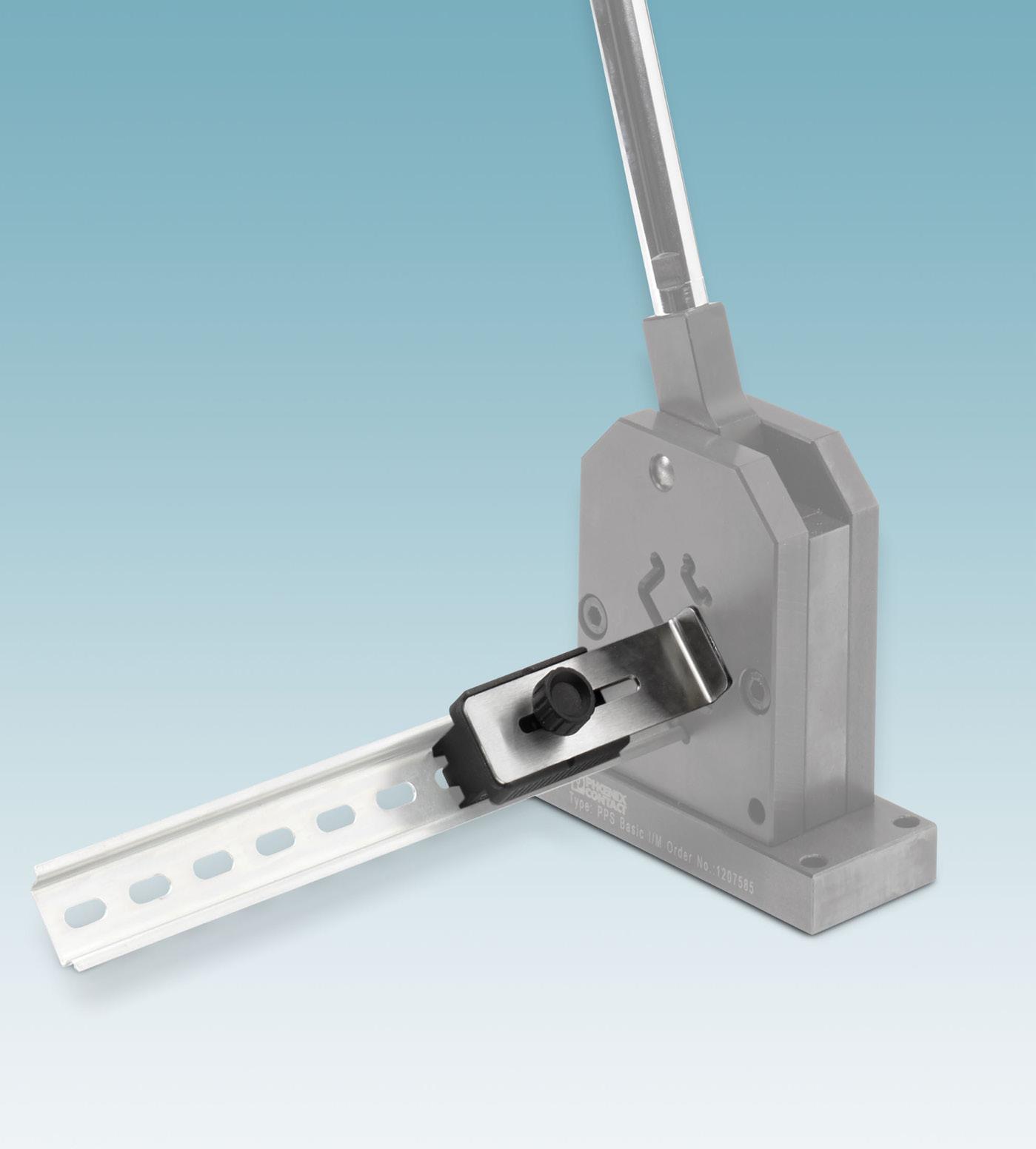
The zero-cut block for DIN rail cutters optimises the manual cutting of perforated DIN rails by enabling fast and reproducible zero cuts, without any need for timeconsuming, repeated measuring.
With the help of an adjustable slide, different zero-cut conditions can be easily set, making the cutting process much more flexible and efficient. This adapter from Phoenix Contact is specially designed for perforated DIN rail types NS 35/7,5, NS 35/15, and NS 15.
The zero-cut block is equipped with a cylindrical pin and magnets for a secure hold. It is fully compatible with the PPS profile cutters from Phoenix Contact, thus ensuring seamless integration into existing systems.
Since repeated measuring and drawing are no longer required, measurement and reading errors are reduced – in turn, saving lots of time.
Different zerocut conditions can be easily set, making the cutting process much more flexible and efficient.
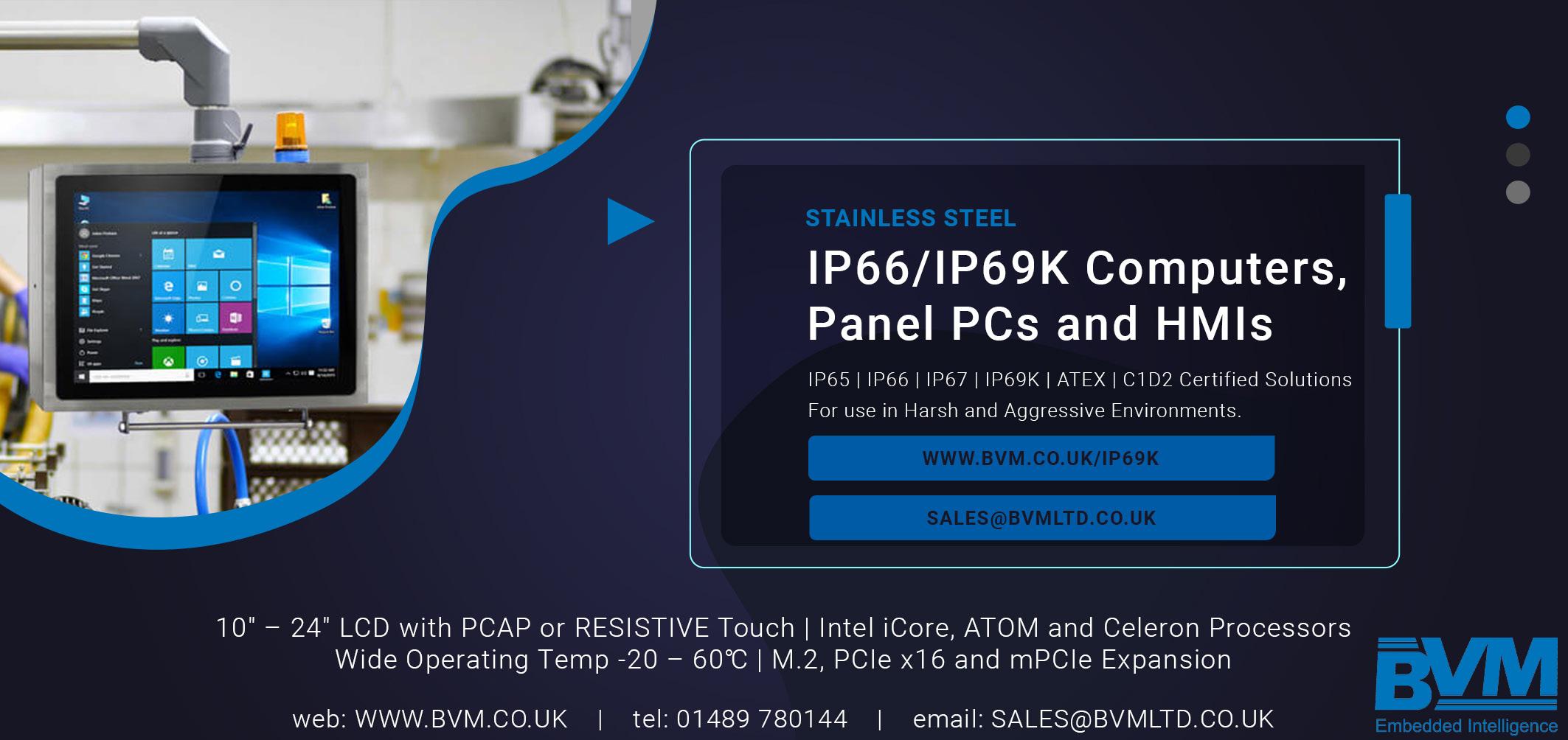
Smart Sensors – Grasping the Full Potential Measurement, Sensors & Monitoring
Clever, intelligent…but more commonly recognised as ‘smart’. A simple definition of an essential component increasingly used in today’s food and beverage manufacturing applications and acknowledged as a bridge to the digital future from analog to IOLink.
A smart sensor is a device that takes input from the physical environment and utilises built-in computer resources to perform predefined functions with detection of specific input and then processes data before passing it on to operators for analysis and action. Or, put it another way, ‘Smart’ sensors allow for ultimate machine performance using powerful measurement technology, innovative design principles and reliable repeatability.
Today, smart sensors are being increasingly used in food manufacturing industries as they reduce resource consumption in some applications by 30% or even up to 50%. CIP (Cleaning-in-place) is one area where smart sensors are helping operators to save time and energy, whilst also reducing water and detergent consumption, without jeopardising process safety.
Also used for faster and more accurate measuring of heat exchangers, these sensors help optimise energy
consumption and cleaning regimes, along with improved inventory management. The result is more accurate production planning based on real-time values helping to optimise safe batch separation, improving production quality whilst minimising material wastage by optimising the emptying of storage tanks and silos.
Inventory Management is another area where smart sensors enable more accurate production planning based on real-time values, ensuring complete material consumption in emptying storage tanks and silos. Also, safer, more efficient batch separation which ultimately improves production quality.
The connected Smart Sensors, like those offered by sensor specialists Baumer, are characterised by precision, miniaturised design and trend-setting functions. Flexible Dual Channel interfaces help operators to switch from analogue to digital output in parallel which means all the IO-Link benefits are accessible. However, sensors can be controlled via 4-20mA analogue output, especially in filling and packaging applications in food and beverage production. The sensors are designed to supply both fast realtime data for machine control as well as acyclic data for status analysis and process optimisation, paving the way to digital 4.0 communications.
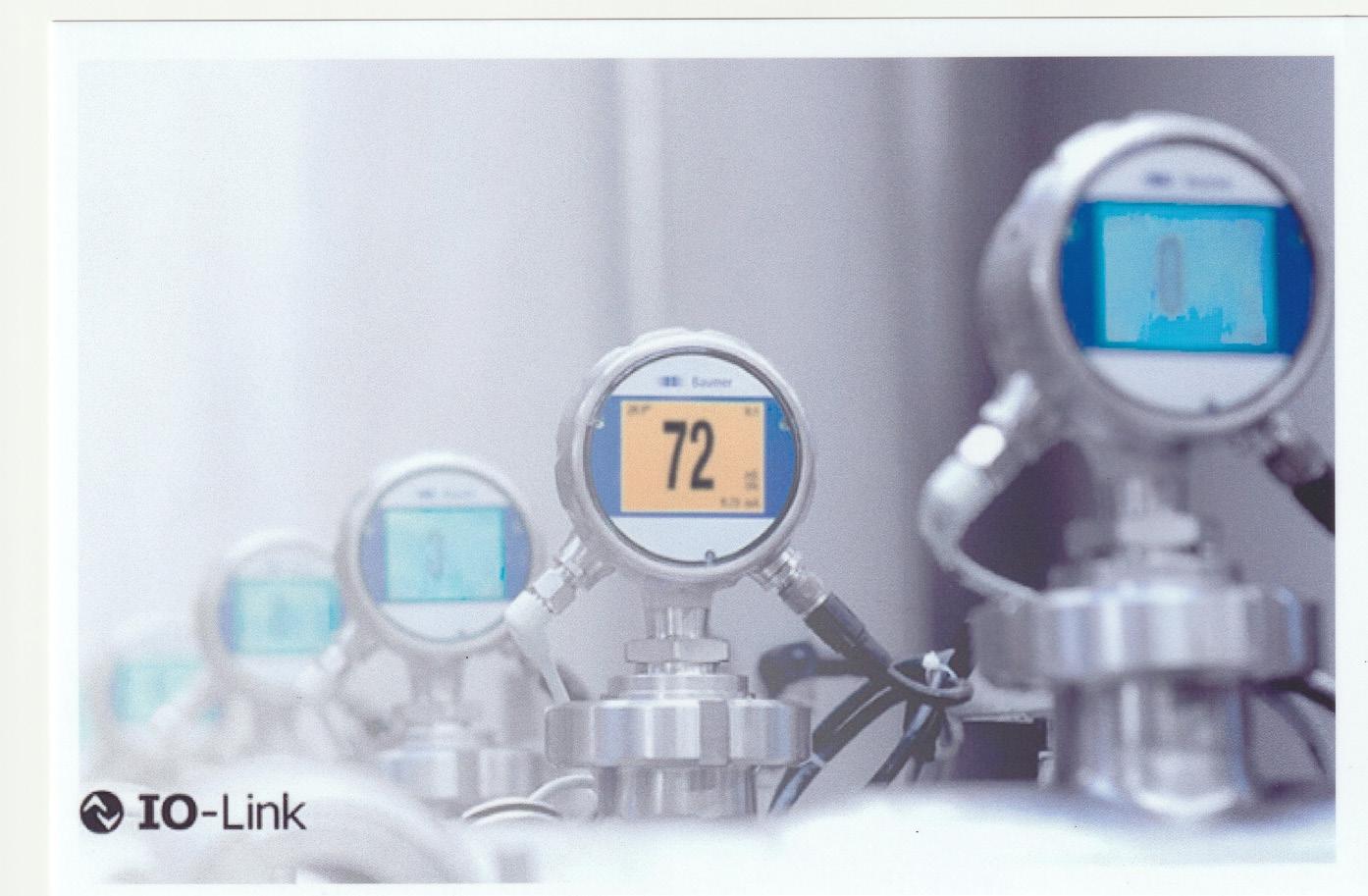
Smart sensor solutions for factory and process automation are helping to pave the way towards smart factories through high-precision thanks to specialists like Baumer.
Most people associate the term ‘smart sensor’ with IO-Link and secondary data for machine monitoring. However, important features like these are just the beginning because with smart sensors integrating freely accessible additional digital services ensures maximum ease of operation. The important questions posed by system designers would typically be; how does the sensor integrate into a machine? How do ‘blind’ areas in the receiver and detection range behave? In most cases users continue to follow the complex, conventional procedures of collecting dimensions and coverage from data sheets for design-in via CAD, but this is time-consuming and prone to errors.
Solutions, like those offered by Baumer, provide a full 3D CAD sensor model with detection area and other relevant information as a digital twin which means designers can easily transfer the supplied data to their models and compare it with the machine design. This means users can see the sensors dimensions, detection range, blind and receiver range and so ensures they can identify the ideal position and parameterisation already on screen.
Smart sensor solutions for factory and process automation are helping to pave the way towards smart factories through high-precision thanks to specialists like Baumer.
Find out more at www.baumer. com/gb/en/product-overview/ smart-vision/c/296
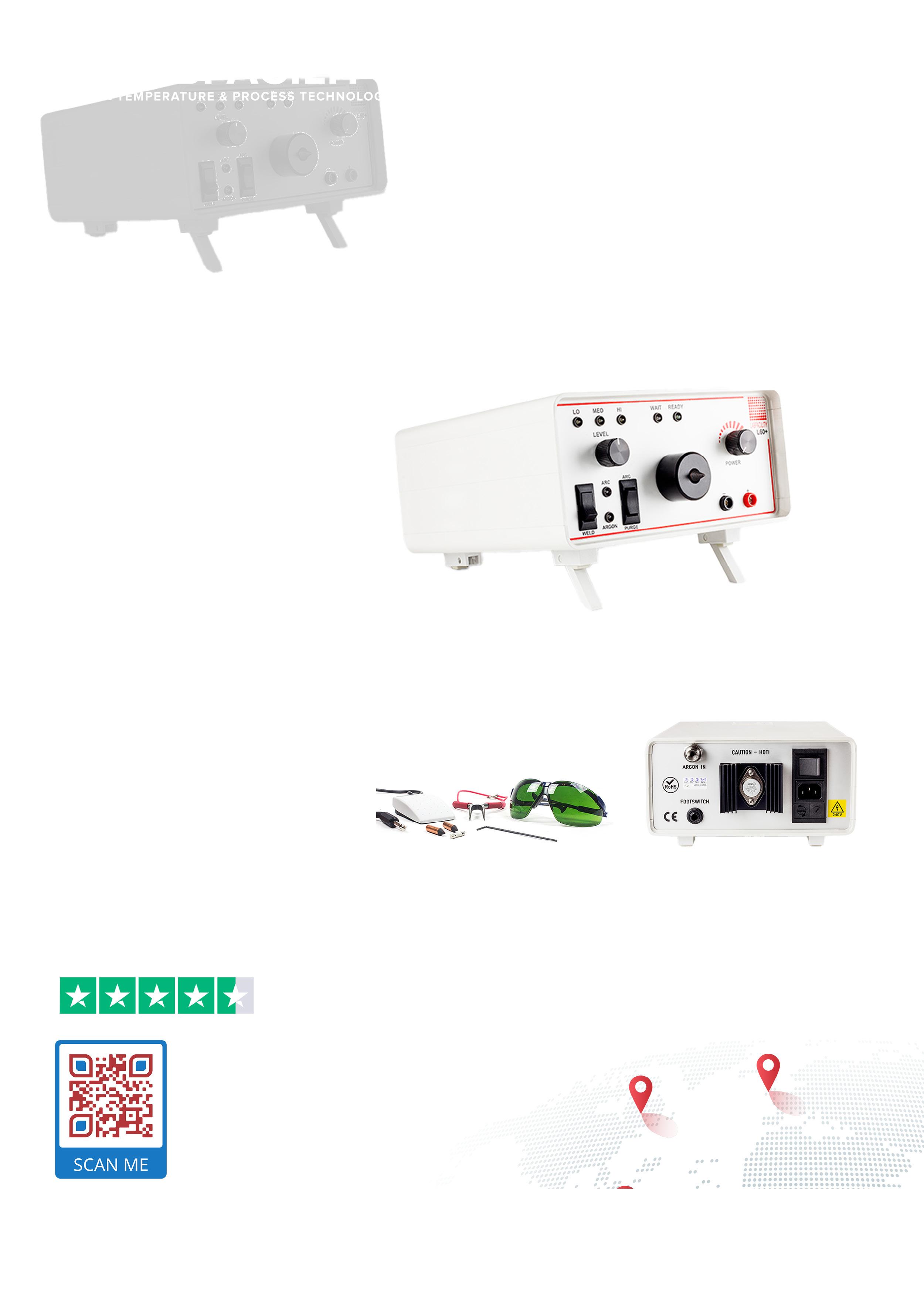

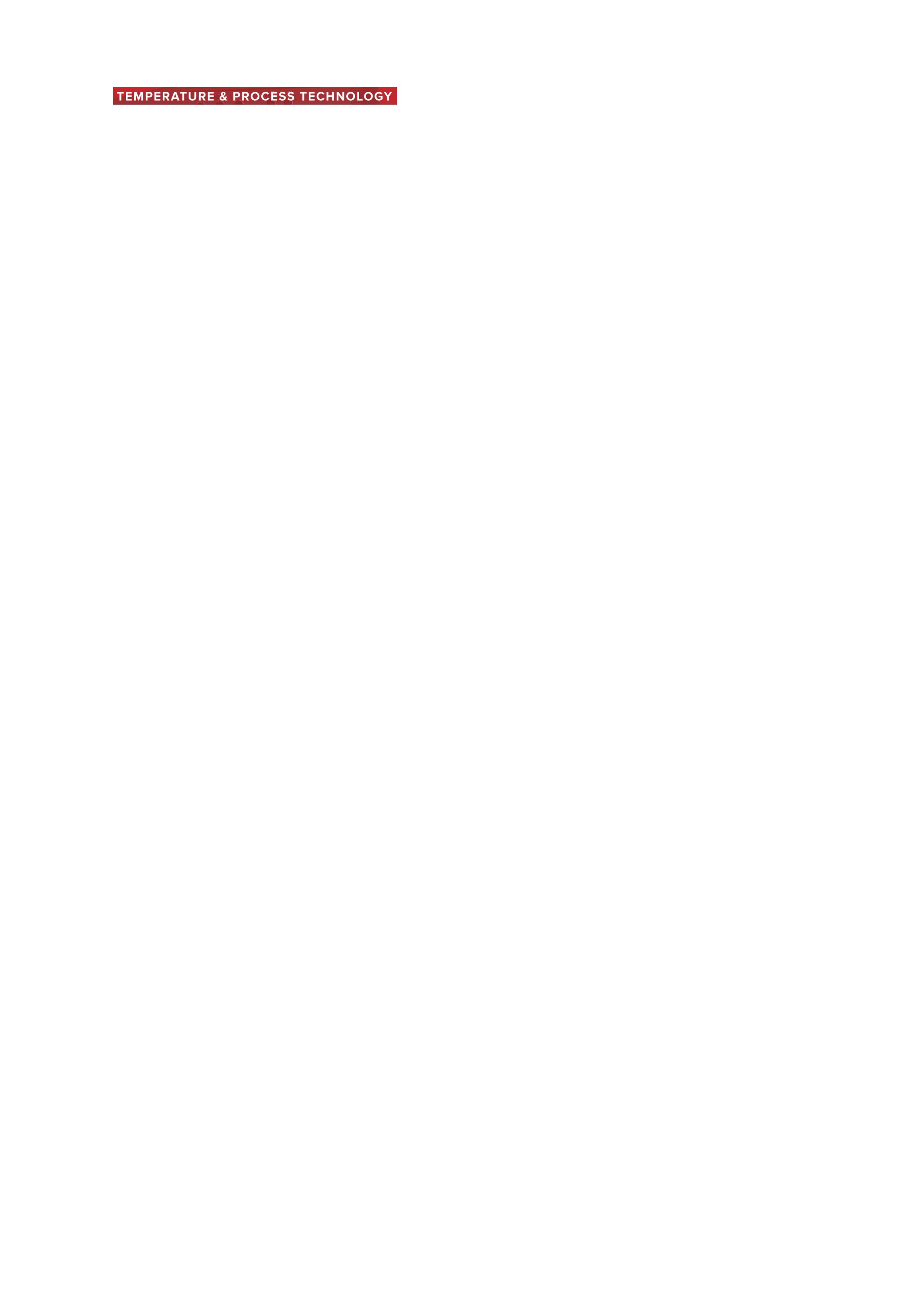
Yokogawa Test & Measurement Releases PBDH0400 Series
Yokogawa Test & Measurement Corporation has announced the release of its PBDH0400 series differential probe with a maximum input voltage of 2000 V and a frequency bandwidth of 400 MHz.
With growing emphasis on measures that will help to achieve decarbonization across all areas of society, there is a need to increase the energy efficiency of motors and inverters used in the transportation and renewable energy sectors. This requirement is particularly acute in the power electronics industry, where the increase in applications for - and production of - next-generation power devices utilizing silicon-carbide (SiC) technology necessitates the ultraprecise measurement of high-voltage and higher speed signals.
This task requires performing measurements from an ungrounded (floating) potential, necessitating the use of differential probes rather than standard probes. Yokogawa Test & Measurement therefore set about
PBDH0400 series differential probes are able to deliver the measurements required for developing the next generation of higher speed power devices that can contribute to the realization of a sustainable society.
developing wide-bandwidth differential probes capable of measuring highvoltage and high-speed signals. The new probes contribute to a more sustainable society through improved energy efficiency.
PBDH0400 series differential probes are able to deliver the measurements required for developing the next generation of higher speed power devices that can contribute to the realization of a sustainable society.
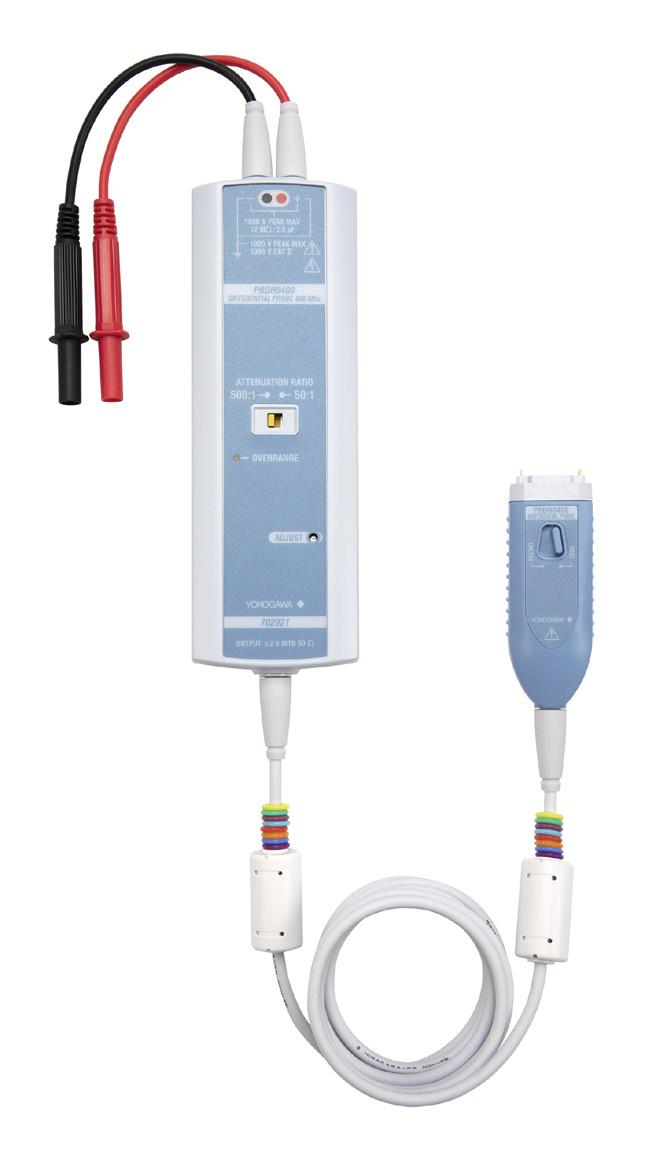
Redefining Precision and Durability in Sample Preparation and Analysis

Micronic has introduced X-Clear Tubes, the first on the market to deliver unmatched optical clarity and optimal light transmittance. These innovative tubes set a new standard in sample preparation
and analysis, making them the perfect solution for laboratories that require accuracy, reliability, and efficiency in sample handling.
At the heart of the X-Clear Tubes is their optical clarity; designed to deliver superior light transmittance, these tubes offer researchers unparalleled visibility of their samples. Their ability to enhance visibility makes it easier to monitor, track, and assess samples, providing labs with a reliable tool for detailed examinations.
Developed for demanding laboratory workflows, the Micronic X-Clear Tubes offer exceptional temperature resistance, withstanding intermittent exposure to temperatures of up to 235°C, ensuring reliability even under extreme conditions.
For more information, visit: www.micronic.com/contact.
Delta Powers Seamless Connectivity for the Westerscheldetunnel in the Netherlands
The Westerscheldetunnel, a vital infrastructure asset managed by N.V. Westerscheldetunnel on behalf of the Province of Zeeland, is the longest tunnel in the Netherlands at 6.6 kilometres underwater.
As a key transportation route, the tunnel ensures smooth connectivity between regions, making its uninterrupted operation critical. A power outage in such an environment could jeopardize the safety of travellers by disrupting critical systems, such as lighting, ventilation, and signalling. Ensuring these systems remain operational, even during power disruptions, is essential to safeguard the lives of those driving through the tunnel.
Delta addressed this vital need by installing state-of-the-art IPT-50kVA Industrial Power Transformer-based UPS systems, showcasing its expertise in delivering comprehensive turnkey solutions for industrial environments.
Innovative Tailored Power Solutions
The UPS system previously used in the Westerscheldetunnel had reached the end of its lifespan and needed to be replaced. The complex logistics of installing a new system within the tunnel presented significant challenges. To address these issues, a solution was needed that could ensure reliable power delivery while optimizing space and operational efficiency.
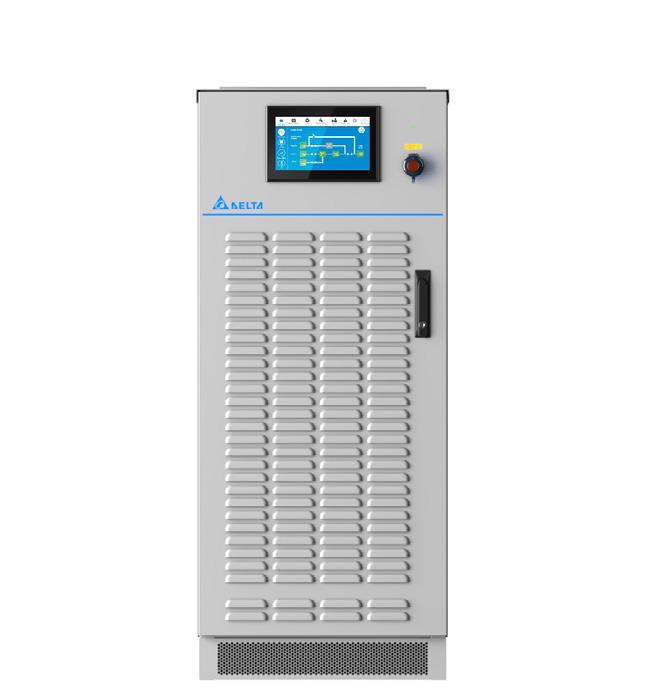
To meet these requirements, Delta supplied its newly launched IPT50kVA UPS units, each with a compact footprint making them ideal for installations where space is limited. These systems feature advanced technologies, including IGBT rectifiers for low total harmonic distortion and inverter-integrated isolation transformers, enhancing shortcircuit capability and load separation. These innovations provided a reliable and manageable power solution that directly addressed the tunnel’s requirements.
In December 2023, Croonwolter&dros, acting on behalf of N.V. Westerscheldetunnel, partnered with e-Power to implement Delta’s IPT50kVA systems during the second phase of the project. Delta’s product management and engineering teams collaborated closely with e-Power to deliver the UPS systems on a tight schedule, meeting the demanding deadline.
The new systems have significantly enhanced the tunnel’s operational efficiency. Features such as a user-friendly 10-inch waterproof touch panel and advanced event analysis capabilities have reduced maintenance time and costs. Additionally, the compact design also streamlined installation, optimizing project and labour management.
Ensuring Safety through Reliable Power
The reliability of the IPT-50kVA UPS systems plays a critical role in ensuring safety within the Westerscheldetunnel. These systems provide seamless backup power, ensuring that essential functions like signalling, ventilation, and lighting remain operational even during power outages. Such redundancy is vital to maintain visibility, air quality, and clear communication within the tunnel, preventing accidents and ensuring the safety of the traffic going through the tunnel.


Overcoming Challenges with Strategic Collaboration
Delta’s partnership with e-Power ensured efficient handling of logistics, installation, commissioning, and ongoing service, adhering to Croonwolter&dros’ high standards for reliability and performance. This collaboration effectively addressed logistical challenges, including extended sea freight times from Delta’s overseas factory to Europe.
A Successful Partnership and Future Prospects
The Westerscheldetunnel project marks the first successful implementation of Delta’s IPT UPS solutions in the Netherlands. Delta’s proven track record, supported by dependable partnerships with Croonwolter&dros and e-Power, has positioned Delta as a leading provider of UPS systems in critical infrastructure. This project highlights Delta’s and its partners’ ability to deliver high-quality, turnkey solutions that meet stringent requirements. Delta looks forward to leveraging this success in future projects, applying the valuable experience gained to continue offering innovative and reliable solutions to its clients.
For more information, visit: www.delta-emea.com
Distinctly Hyster, Built for You Forklifts from 1.6-Tonnes
The Hyster H1.6-2.0A lift trucks replace the current Hyster H1.6/1.8/2.0FT(S) forklift models. They -extend the range of lift trucks available in the Hyster A Series, which also includes ICE
lift trucks with capacities from 2 to 3.5 tonnes. The H1.6-2.0A models share several components and options with the H2.0-3.5A range, delivering many of the same benefits.
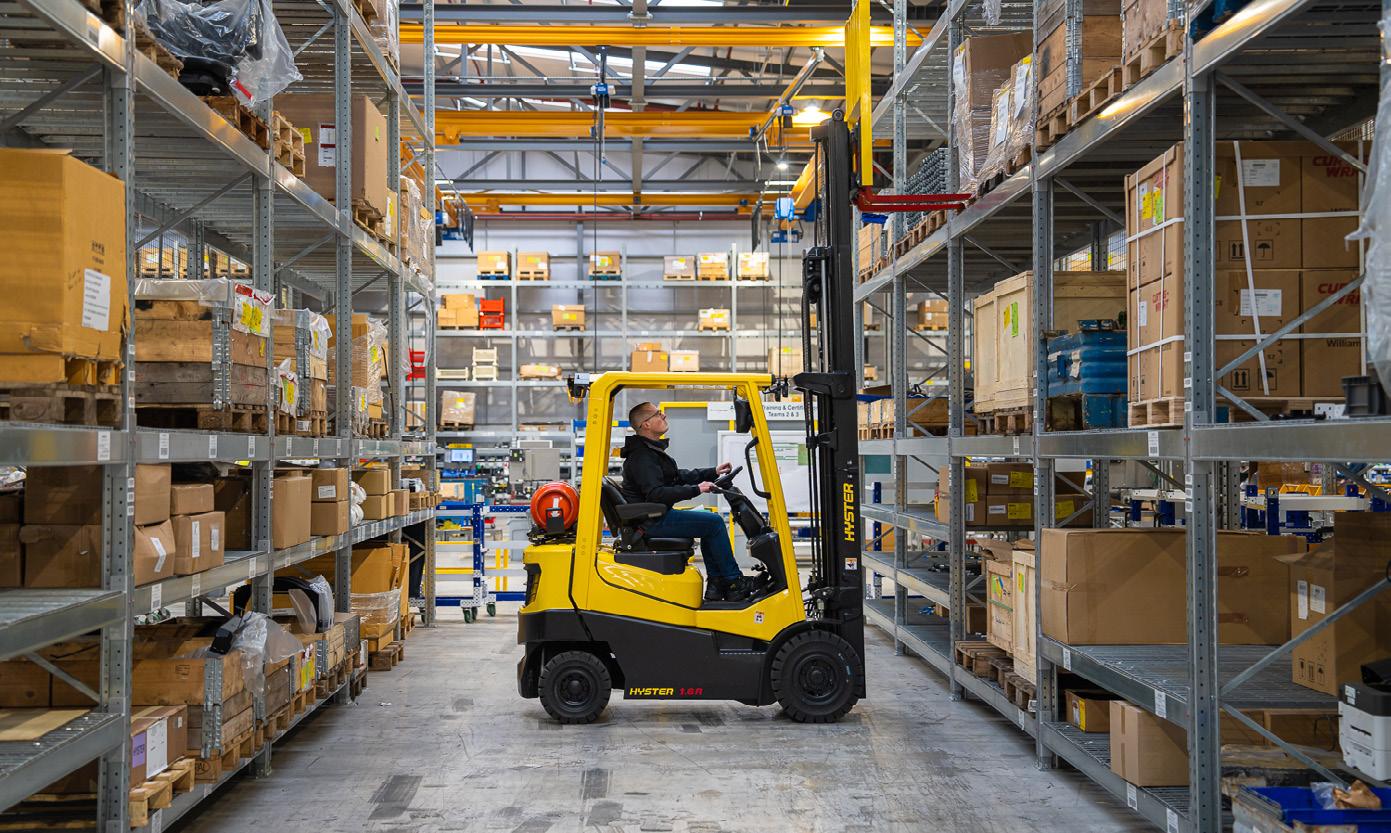
There is a choice of masts that maximise visibility and a range of operator assist options, including lights, fork laser line, and load weight display are also available, helping support accuracy and performance.
The optional Dynamic Stability System (DSS) is also available with the H1.6-2.0A models, reducing the likelihood of tip overs, operating safe practices by monitoring operating conditions and automatically limiting truck functionality when potentially unsafe conditions are detected.
A complete range of overhead guard and cabin options are available, including the clear-view glass roof option, sunshades and more. This operator-centric design helps meet the needs of a range of different industries, including operations handling building materials, metals, and chemicals, and plastics.
For more information, visit www.hyster.com.
Friedheim Packaging Drives Operational Efficiency and Sustainability For Pets At Home
In an era where sustainability and efficiency are paramount, Friedheim Packaging has supported Pets at Home in taking a significant step forward by introducing a state-of-
the-art Beck Packautomaten Paperbag vs machine for direct to customer distribution of online pet pharmacy products.
The new Beck Paperbag vs is designed around processing a wide

range eco-friendly, 100% recyclable paper bags, designed to produce robust, four-side sealed paper bags. This offers an alternative to the previous process of single items packed in a shallow cardboard box, a costlier, slower, and more manual process.
One of the standout features of this machine is its versatility. It can seamlessly accept up to three products and produce a bag length to accommodate the required Royal Mail Large Letter format, due to its automatic product detection system, ensuring a consistent and reliable packaging process.
The machine’s high-speed capabilities - producing up to 1,380 bags per hour – ensure that the demands of a nationwide retailer are met without compromising on quality.
Aluminium expertise for pneumatics
MAPAL harnesses its expertise in aluminium machining, honed through automotive mass production, to produce critical components for pneumatics. Two critical components—a housing for pneumatic valves and a pneumatic cylinder—require
high-precision machining. With millions of units produced annually, they demand process reliability, precision and quality, making them an ideal fit for MAPAL’s capabilities.
The components are aluminium with a small amount of silicon,
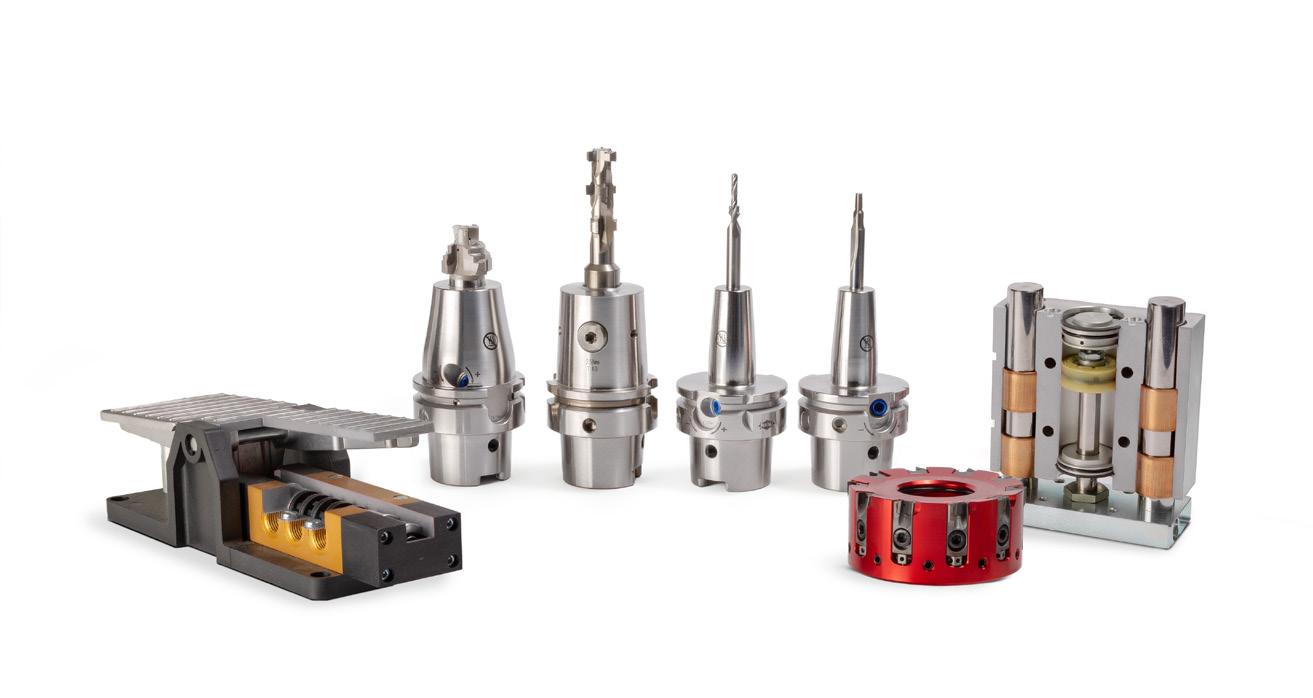
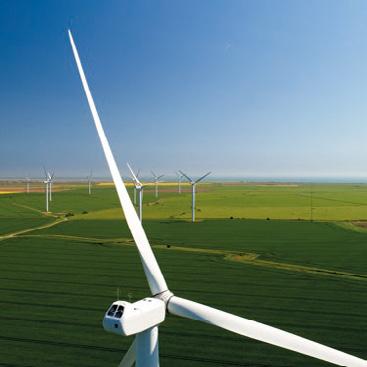
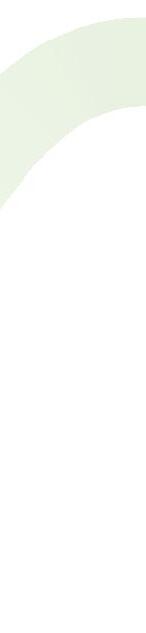
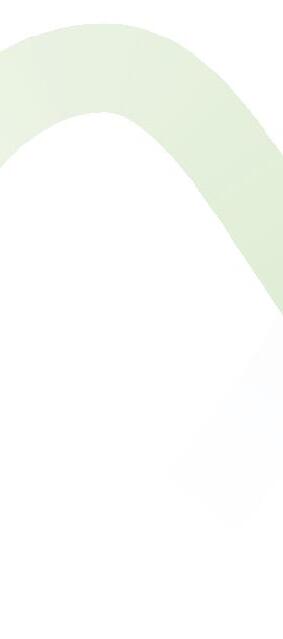
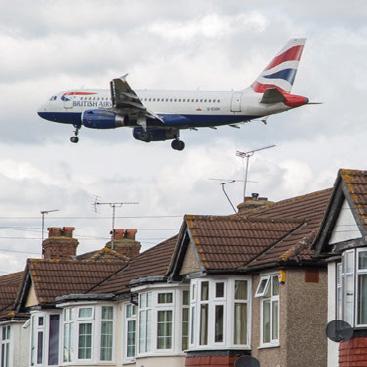
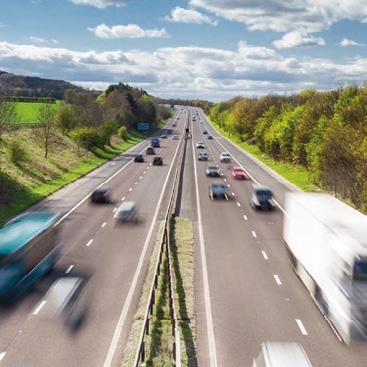
placing high demands on the machining solution requiring careful chip formation and removal. Special attention is given to avoiding burr formation, which can impact valve functionality and even cause it to fail.
For valve housings, MAPAL uses solid carbide tools with multi-cut technology, PCD blades for highvolume production, and combines boring and milling for efficiency. The spool bore is machined with a PCD circular milling cutter, saving time by milling contours in one step. MAPAL also offers the TOOLTRONIC mechatronic system to reduce tool numbers and simplify part variations.
For the pneumatic cylinder, MAPAL employs smart machining and PCD combination tools to maintain high quality despite material hardness fluctuations.
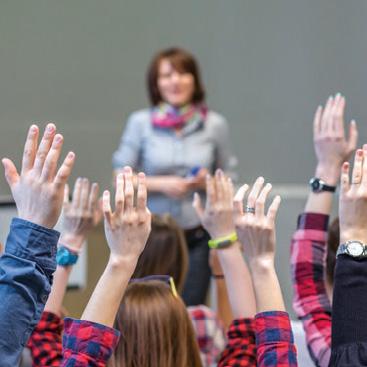

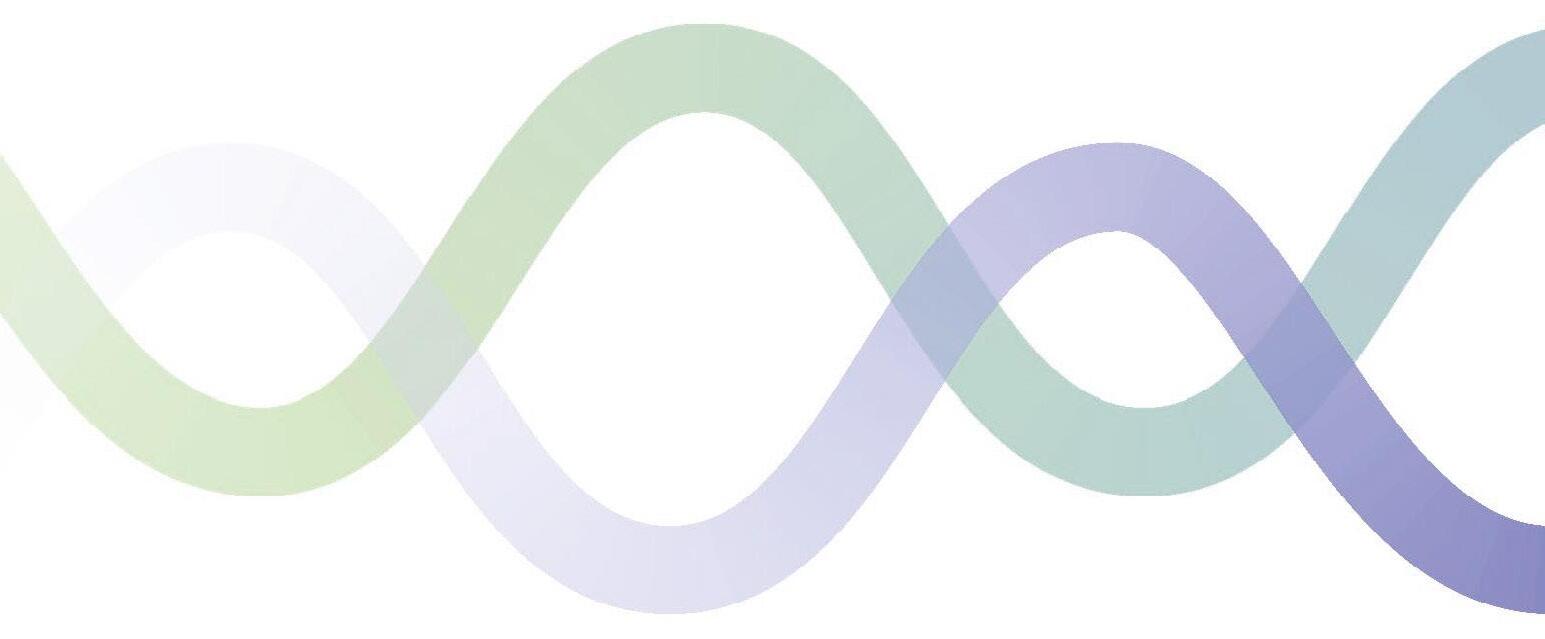
The one year IOA Diploma in Acoustics and Noise Control includes the General Principles of Acoustics, Laboratory and Experimental Methods, a project and two specialist modules chosen from:
• Bui ld i ng Acoustics
• Noise of Assessment nd a Regulation
• Noise: ronmental Envi Measu rement, Pred iction & C ontrol
• Noise a nd Vi bration C ontrol Engi neeri ng
Established for more than 50 years, the Institute provides graduates and those with a proven interest in acoustics, the chance to become a recognised member of a vibrant and active global network with regular UK meetings and CPD.
The Diploma is taught to candidates in centres across the UK and via distance learning tutorials, also facilitating candidates abroad – find out more at: www.i o a .o rg .uk/e d u c a ti o n-t ra inin g
FOR MORE INFORMATION: www.ioa.org.uk E: education@ioa.org.uk T: +44 (0)300 999 9675 Institute of Acoustics, Silbury Court, 406 Silbury Boulevard, Milton Keynes MK9 2AF
A Cut Above: Edmar brings waterjet cutting in house with Wardjet a-1212
Outsourcing processes can be counterproductive, especially when components arrive late or are poor quality. Birmingham-based Edmar Engineering Company Ltd has taken control of its cutting capabilities, splashing out on a A-1212 waterjet from WARDJET – and the business benefits have proved manifold.
Fourth generation family-run business Edmar Engineering celebrates its 80th birthday next year, but its service provision is cutting-edge as ever, thanks to its latest acquisition – a WARDJET A-1212 waterjet machine.
Edmar was founded in 1945 by former Dunlop foreman, Bill Marklew, and partner Mr Edwards. Having been commandeered by the MoD to enlist skilled, local engineers and toolmakers in the war effort, Bill decided to retain his new-found colleagues after the war and set up his own specialised precision engineering company.
Here and now!
Nearly eight decades on and with Bill’s great granddaughters, Anna Hayton and Jayne Sheppard, at the helm alongside Technical Director, Richard Dale, Edmar is still true to its roots. The company specialises in small quantity machining, prototypes, one-offs, jigs, fixtures, and special purpose machines. From its original manufacturing base in Birmingham, Edmar offers expert support to all sectors including automotive, aerospace, utilities, food, and pharmaceuticals, working closely with customers on time-sensitive projects that require tight turnarounds.
“Our engineers love a challenge and creating things for our clients!” enthuses Co-Director Anna Hayton. “To meet their demands, you have to be reactive,” she asserts. “We don’t carry a huge order book going forward, so much of the work we do is reactive – everybody needs it now!”
Prior to purchasing the A-1212, Edmar outsourced their waterjet cutting requirements, but this solution was becoming increasingly problematic for the company, as Technical Director Richard Dale explains: “When you subcontract, you lose control over quality and lead times,” he says.
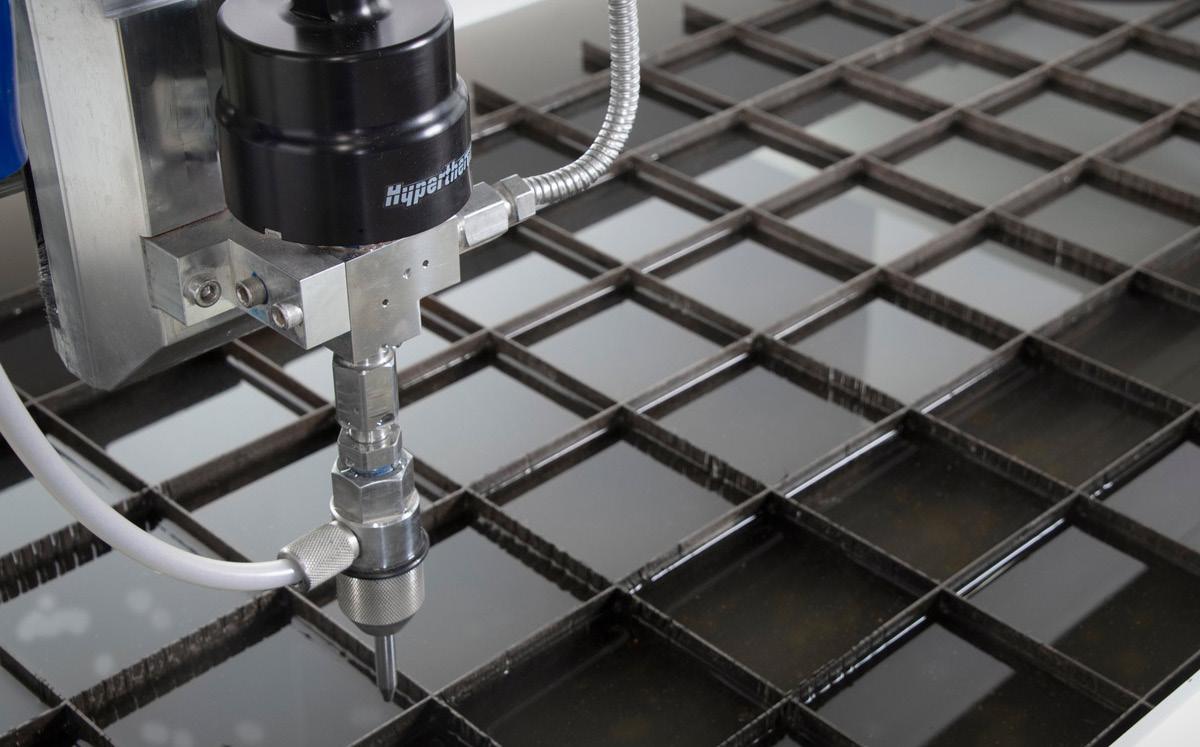
“If you’re relying on parts coming in that have been produced elsewhere, they can arrive late and with a different finish than you wanted. Those parts may then need reworking, which affects everything from timescale to overall quality.”
“By bringing the waterjetting in house, our reactivity and control is much improved. If someone has an urgent requirement, we can manufacture speedily whilst maintaining our high standards. Being able to do that helps us satisfy our existing customer base and has won us new business.”
The waterjet has also helped speed up Edmar’s milling processes by producing profiles prior to milling.
Time-efficient, cost-Effective
The WARDJET A-1212 has not only improved Edmar’s efficiency over the last 12 months; it’s also made the company’s use of materials more cost effective, as Simon’s observed: “We mainly use the waterjet to cut aluminium, and some plastics, which it can do very fast. Previously, we were buying material cut to order, which can incur extra time and cost; now we can buy a sheet and cut the pieces ourselves.”
“We don’t have to wait for materials to arrive on site any more or wait for them
Edmar was founded in 1945 by former Dunlop foreman, Bill Marklew, and partner Mr Edwards. Having been commandeered by the MoD to enlist skilled, local engineers and toolmakers in the war effort, Bill decided to retain his new-found colleagues after the war and set up his own specialised precision engineering company.
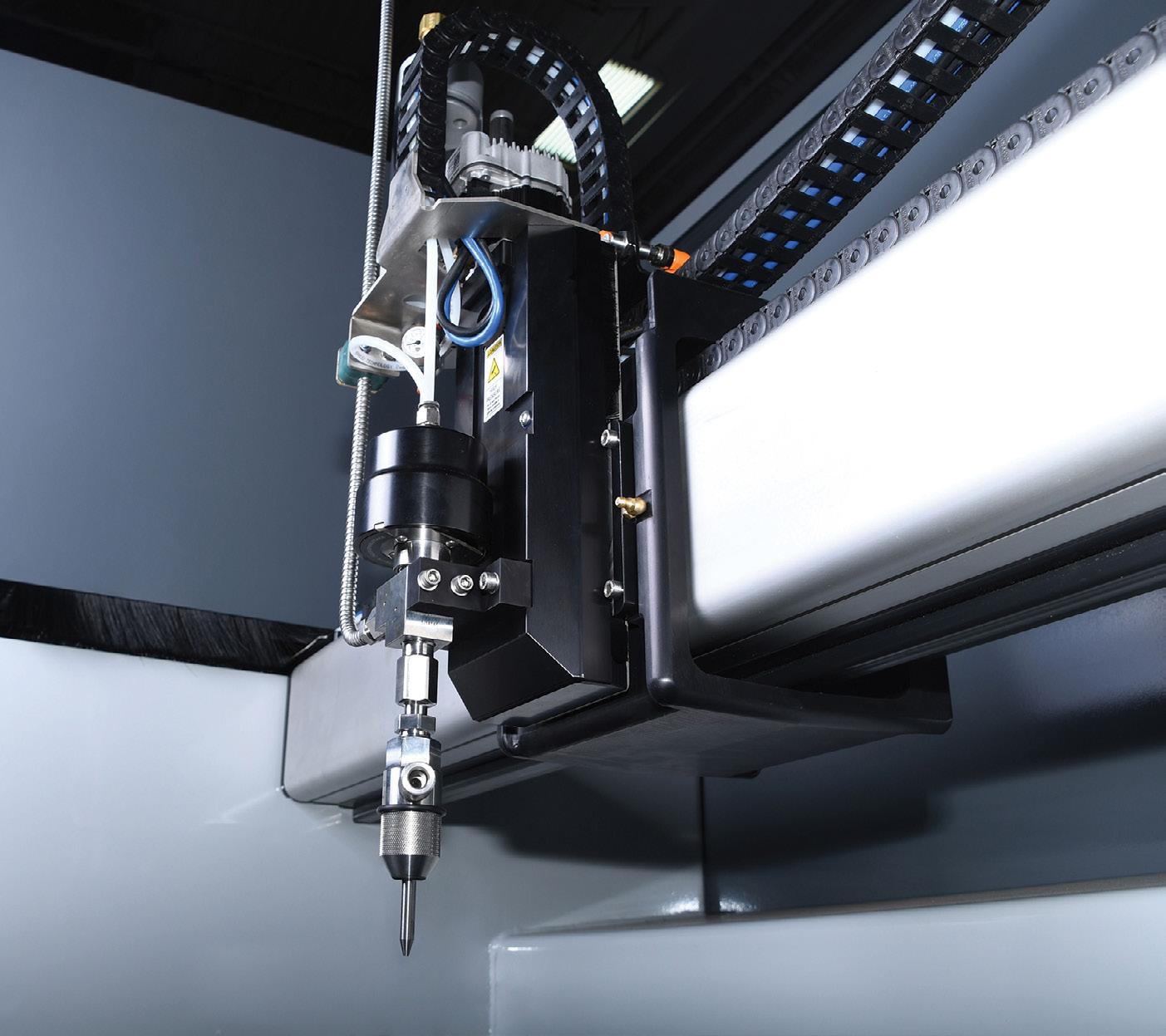
to be cut to size, which has really sped up our processes,” Richard adds.
The right machine
WARDJET’s A-series waterjet is available in two sizes: the A-6012 and A-1212. “We opted for the A-1212 for its generous 1200 x 1200 operating window,” explains Richard. “It has industrial capabilities with a compact footprint and is ample for the work we do.”
Edmar’s Production Manager and machine operator, Simon Danks, also had a hand in choosing the new machine, which features dragand-drop loading and part queuing technology: “It’s a very user-friendly operating system – easy to operate and programme,” he says.
“The dropdown menu of preprogrammed parts is one of the most useful features. If I want a rectangular part, I select ‘rectangle’ from the inventory and the size I want, and the software draws it up for me. It couldn’t be simpler.”
The right partners
After researching the waterjet market, Richard chose Telfordbased WARDJET Waterjets from AAG Tailored Cutting Solutions following an impressive hands-on
demo experience, where he was able to bring his own CAD files to the WARDJET Demo Room and see the A-1212 go to work on his designs. “We had a good look at the operating system and were able to programme and operate the demo machine ourselves,” he recalls.
Positive endorsements from fellow industry professionals, and WARDJET’s proximity to Edmar’s headquarters, sealed the deal. “Although WARDJET machines are manufactured in the US, the UK Telford based-head office is local to us, which means the support and infrastructure is local too.” Richard points out.
“All the training on the new machine was comprehensive and carried out at Edmar. And when we needed extra help with maintenance, WARDJET engineers came out to us to talk us through it. They have a good team of people there. I’m more than happy with the products they’ve supplied and the support we’ve received – I’d recommend WARDJET to anyone.”
Anna adds: “As a small company, the waterjet was a big capital investment for us. We received some grant funding and WARDJET were helpful with the delivery and paperwork requirements of this.
Forterra and Air Products: Generating a cleaner future, hydrogen and brick production trial
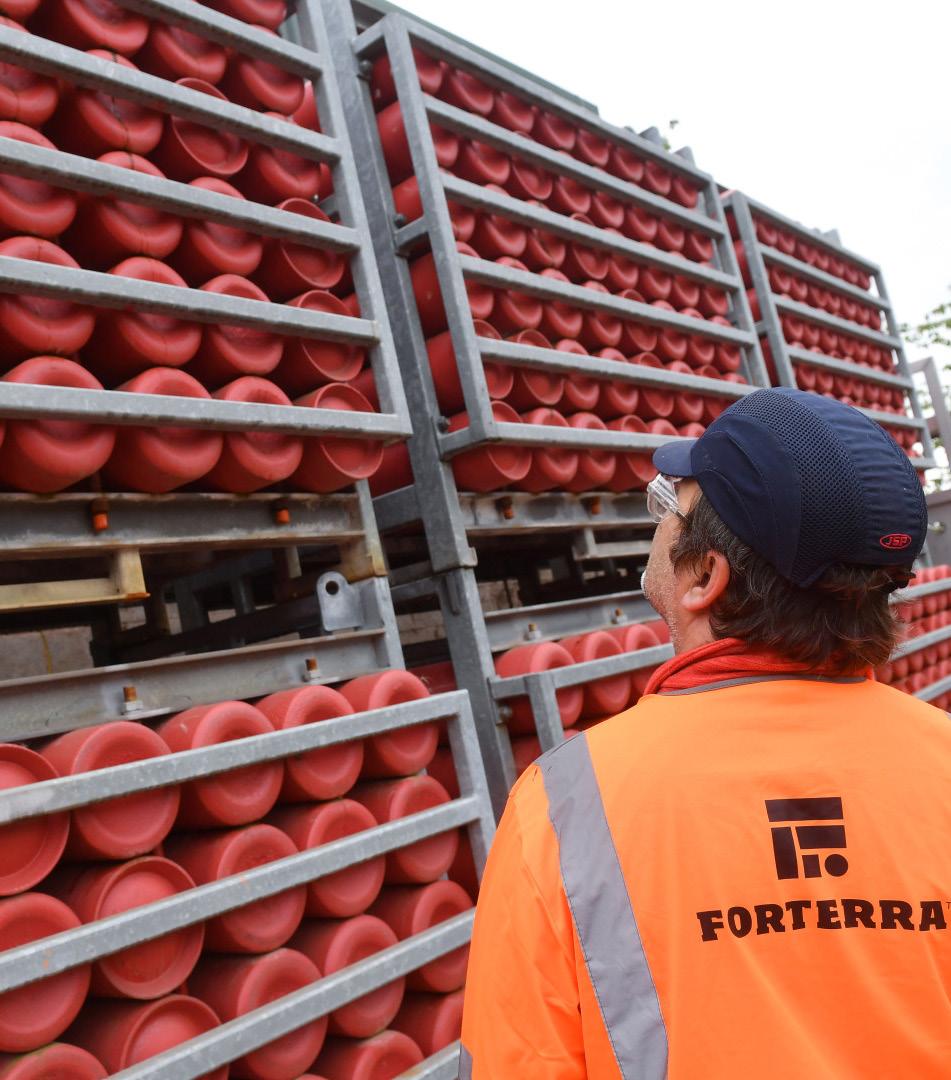
For the construction manufacturing industry, there is a critical challenge on the road ahead –decarbonising its production processes.
So, when Forterra, a leading UK manufacturer of essential clay and concrete building products, published its sustainability strategy in 2022, it set a target to reduce its carbon emissions by 32 per cent by 2030. To do this, it meant tackling the energy mix used to power the company’s brick production kilns – reducing the use of natural gas and increasing the use of hydrogen. Working with Air Products, Forterra has been able to trial exactly that, while protecting the quality of the bricks the company is known for.
Adjusting for hydrogen
Driven by National Grid’s goal to blend green hydrogen into its existing natural gas distribution system, Forterra’s trial with Air Products tested the capability of hydrogen to decarbonise its processes in the longer-term. At its Redbank site, where specialist brick products are manufactured, Forterra has trialled a 20 per cent hydrogen blend with 80 per cent natural gas as an alternative to pure natural gas in its kilns. David Manley, Forterra’s Head of Sustainability, said: “Cutting our carbon emissions is central to our mission, but we need to make sure we’re not compromising on the quality of the products we’re producing.
“When it came to considering how to cut our emissions, we looked at several options including electrification and biomass. Both of these will have a supporting role in our long-term strategy but it became obvious quite quickly that hydrogen is the most effective option for reaching our longterm decarbonisation targets.
“Working closely with Air Products, we’ve introduced gaseous hydrogen storage, together with a blending skid and control system which has allowed us to produce bricks using a mixture of natural gas and hydrogen. The successful use of 20 per cent hydrogen is a game changer given the careful balance we need to strike when it comes to temperature and moisture control in brick production.”
Air Products, with expertise across multiple hydrogen production pathways, guides customers through
the full process. Brick production is a balancing act, and ensuring that product quality is not compromised by changes in temperature and environment within the kiln is essential. How hydrogen could be introduced to the energy mix to protect that balance was vital to Forterra and Air Products’ testing.
Overseeing trials using a 100 per cent natural gas kiln as a control variable, Forterra trialled the use of hydrogen at rates between five and 20 per cent, increasing the volume of hydrogen use as the project progressed. David explains: “Approaching the trials in this way worked perfectly. We were aware what we were doing had the potential to be significant for us and the wider industry, so being careful and testing as we went would allow us to pinpoint to what extent hydrogen could be introduced in the process. Ultimately, at a 20 per cent mix there was no impact on the colour, consistency and quality of the bricks - which is exactly what we were looking for.”
The future is promising too, David continues: “We’re excited by the trial outcome, and it’s proved to be a real success for the introduction of hydrogen into our company. As a result we’re now exploring how we can do a similar trial on a slightly smaller kiln but with hydrogen blends up to 100 per cent, as well as how we would fit out our larger kilns in the future.”
A step change
The trial supports what the wider industry is thinking. In its 2024 Decarbonising UK Ceramic Manufacturing Industry Roadmap, Ceramics UK recommended that deeper decarbonisation of UK ceramic manufacturing requires the urgent development and deployment of lowcarbon hydrogen – and that’s despite its notable absence from the same report only ten years earlier.
But how much impact can a hydrogenenabled furnace have on carbon emissions during brick production? David thinks it could be significant: “If we could operate a kiln on 100 per cent hydrogen, we would be able to reduce our carbon output by 40-45 per cent. That’s significant but there are opportunities with our mobile plants too, where the introduction of fuel cells could further reduce our carbon emissions by 8-10 per cent. That means we could achieve a total
Brick production is a balancing act, and ensuring that product quality is not compromised by changes in temperature and environment within the kiln is essential.
reduction of around 55 per cent of our carbon emissions through the introduction of hydrogen.” This would help make Forterra an industry leader in decarbonisation.
Long-term goals
For both organisations, they are clear that this is just the start, with Forterra looking at expansion plans and uses of hydrogen into the future as they believe it’s critical, and Air Products are well-positioned to provide their expertise. David explains: “As with a lot of businesses working to meet decarbonisation targets, we recognise we need to invest in infrastructure across our UK sites to support a move to hydrogen. But we also want to see wider investment in hydrogen infrastructure come forwards, as well as greater confidence in the market for the supply of hydrogen.”
Considering the use of hydrogen for the manufacturing industry moving forward, Air Products comments, “We know how significant the introduction of hydrogen is to the industry. Working in partnership with Forterra means we can continue to demonstrate feasibility, understand need and respond collaboratively to requirements; most importantly, we can continue to drive forward its goal to reduce carbon emissions by 32 per cent by 2030.”
For companies like Forterra, hydrogen carries huge potential. Not only does it support the move to a netzero economy, but it helps ensure the transition can be done in a way that protects quality – critical for customers. There is more to be done, however, and both Air Products and Forterra will continue to work together to examine how to incorporate hydrogen into the manufacturing process – as they seek to explore the behaviour of the bricks, kiln and hydrogen flame in blends up to 100 per cent.
Which Fire Protection Material to Choose for an EV Battery Health & Safety
Dr James Edmondson, Research Director at IDTechEx discusses the key factors and potential materials that EV battery designers may consider.
Cell form factor
One of the first considerations is the battery cell form factor; IDTechEx found that in 2024 around 58% of the market was using prismatic cells followed by 22% cylindrical, and the rest pouch. The cell form factor may not impact protection at a module or pack level, but will certainly impact inter-cell materials.
It is typical to see sheet-type materials applied between the cells in prismatic or pouch cell systems, with encapsulating foams being a popular choice for cylindrical cell systems. Sheets can certainly be applied to cylindrical cell systems, too, and encapsulating foams can be used for pouch or prismatic; these are just less common.
The failure mode will also vary by cell type, with cylindrical and prismatic cells generally venting through the vents on the top of the cells, making the placement of fire protection materials a bit more predictable.
Thermal management concept
How the temperature of the cells is managed is another critical decision. A popular approach is through a cold plate that sits at the top or bottom of
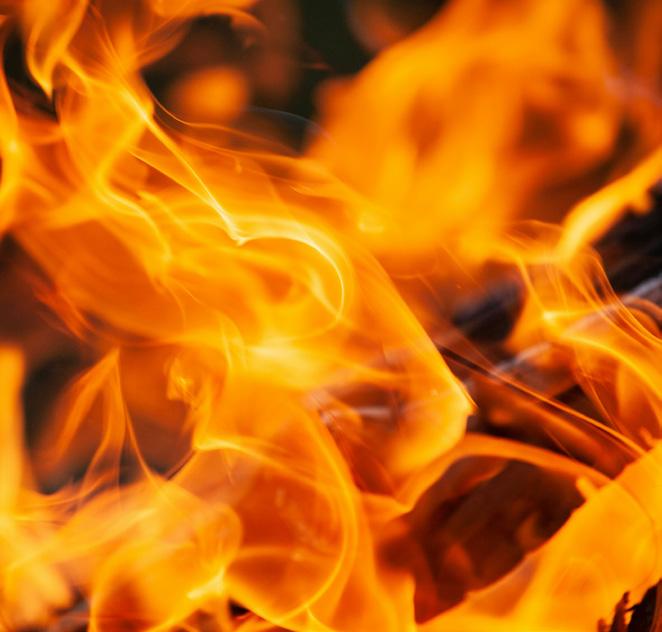
the cells through which water-glycol coolant is passed. Then, the cells are thermally insulated from one another; this aids with maintaining the temperature within the cells in cold conditions but is also beneficial in preventing heat transfer between a cell in thermal runaway and the rest in the pack.
A second option is to cool the sides of the cells too or have heat spreading materials between the cells to transfer as much heat away from the cells as possible. Depending on which approach is taken, this will impact what material or combination of materials are chosen to be placed between the cells.
Material choices
Even once the cell form factor and thermal management strategy are decided, there are a host of different material categories and chemistries that could be valid options.
On key metrics like low thermal conductivity and density, aerogels, ceramic blankets, and encapsulating foams perform well. However, this does not tell the entire story, often, a combination of materials may be needed to meet structural requirements and/or meet UL2596 test requirements. This will typically increase the density required. The UL2596 tests are challenging, with the torch and grit test exposing the sample to an alternating high-temperature flame (1200°C) and alumina particle blasts.
For this reason, material suppliers are generally trying to produce materials that perform multiple functions and can prevent the need for multiple assembly steps. An increasingly popular option from suppliers is polymer/composite components with
fire protective and/or intumescent properties that can be made into structural components of modules, cell holders, or an inter-cell spacer. These may appear less thermally insulating and higher density in normal operation but can replace the need for multiple other materials while providing good insulation at high temperatures. Examples include companies like SABIC, Pyrophobic Systems, Asahi Kasei, and several others.
A primary concern for battery designers is system cost; the addition of fire protection materials increases costs, but the additional cost can vary widely between material options. Part of the calculation is material cost, not just per kg, but by how much is required to achieve the required performance.
Mica has proven a low cost material with strong electrical insulation properties, but is usually required in thicker (and heavier) layers to provide sufficient fire protection. Historically, aerogels have been limited by their costs, but in the right implementation can provide excellent thermal insulation and fire protection. As mentioned above, if a material can provide multiple functionalities, then its additional costs can reduce its impact on overall system cost.
A large variety of factors will go into the choice of fire protection material, and it will include factors like cell form factor, pack design, thermal management approach, material costs, system costs, and regulations to be met. Each material has its own trade-offs and needs to be evaluated for each battery design.
To find out more about this new IDTechEx report, see: www.IDTechEx.com/FPM.
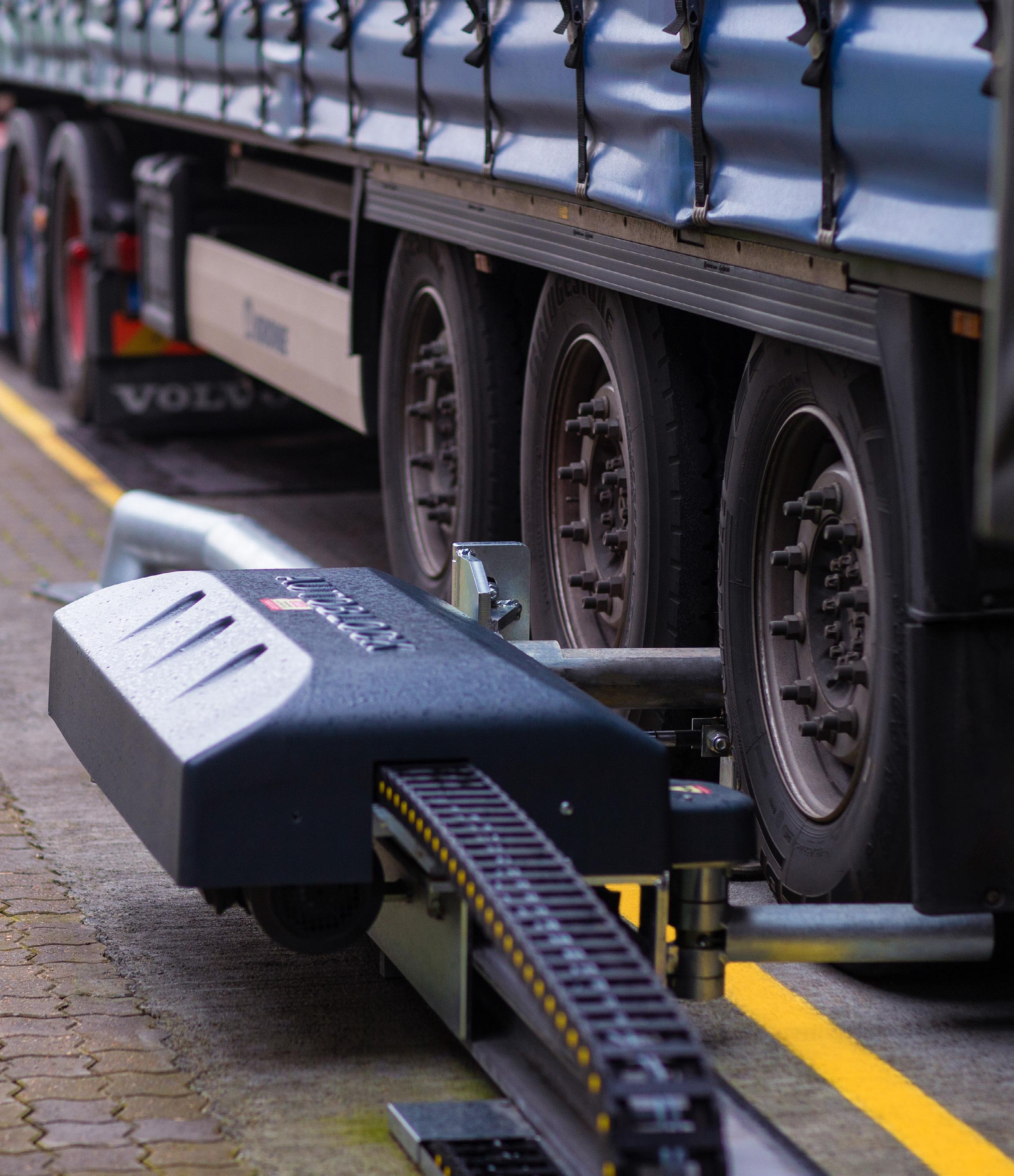
Women In Engineering
Addressing the Gender Gap in UK Engineering
Attributed to Dr Sarah Peers, Associate Professor and Head of Academic Skills at NMITE, and President of the International Network of Women Engineers and Scientists (INWES).
The reasons for the gender gap in engineering are many, and some are global and some UKspecific. UNESCO reports that women have been significantly underrepresented in engineering fields, typically making up only 10 –20% of the engineering work force. Here in the UK, the proportions have dropped recently, from nearly 17% in 2022 to under 16% in 2023.
At entry to engineering, there are beliefs and stereotypes that impact on girls at schools and their own identities. These are due to biases and societal expectations. As individuals, engineers, aspiring engineers and those supporting engineering, we can only be aware of our biases and try to overcome them.
The UK does very poorly in terms of entrants to engineering degree programmes compared to many other countries, because of the specialisation that happens at age 16, and the requirements we set for entry into engineering. This is one reason why NMITE does not expect maths and physics at entry.
We often restrict ourselves though our own mindsets and beliefs. For those who are not sure if they ever could be engineers, remember that the solutions to the big global problems will only be created by engineers and technologists who are creative and problem-solvers, and who care about the future and the world. NMITE firmly believes that we need all sorts of people with a good grasp of technology, but also an even better understanding of what people need.
Structural barriers, that is processes and procedures which stop women
from participating, also have a hand in creating the “leaky pipeline” syndrome where women who have trained as engineers start to fall out of an engineering pathway in their mid-careers. Fortunately, successful companies are beginning to become much more aware of these barriers, and drive programmes and initiatives to support all genders in staying in the workplace. We so need to do much better for everyone’s sake to ensure creative people from all backgrounds to be engineers.
Dr Nadia Kourra (EngD), Associate Professor of Mechanical Engineering at NMITE, provides her personal view on being a female engineer in the UK.
“I was always interested in engineering because I always liked solving problems, especially by using my understanding and knowledge in different fields. I have always admired people who could see the connections between different situations and use their imaginations, technical abilities
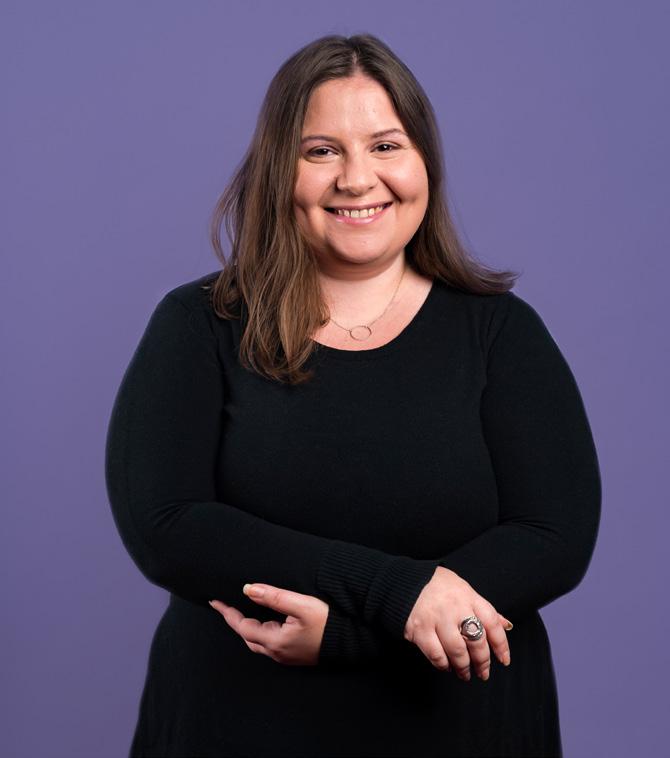
and come up with solutions that were applicable to any specific issue.
I supported an NMITE student during their MEng Project on adjusting refugee shelters according to their cultural and everyday needs. It was a very special project to witness since the student themselves were overcoming their personal experiences in order to deliver the very best they could. It was a humbling experience which reminded me that engineering can bring people and communities closer to overcome very complex and human problems.
The advice I would give to young female engineers is NEVER GIVE UP. All of us are facing different difficulties, gender aside, and we can never let these difficulties get the better of us. Sometimes, that may mean we need to find our voice, or believe in ourselves more, and sometimes it may mean we need to learn how to ask for help. Whatever the difficulty, perseverance is the key to overcome our difficulties.”
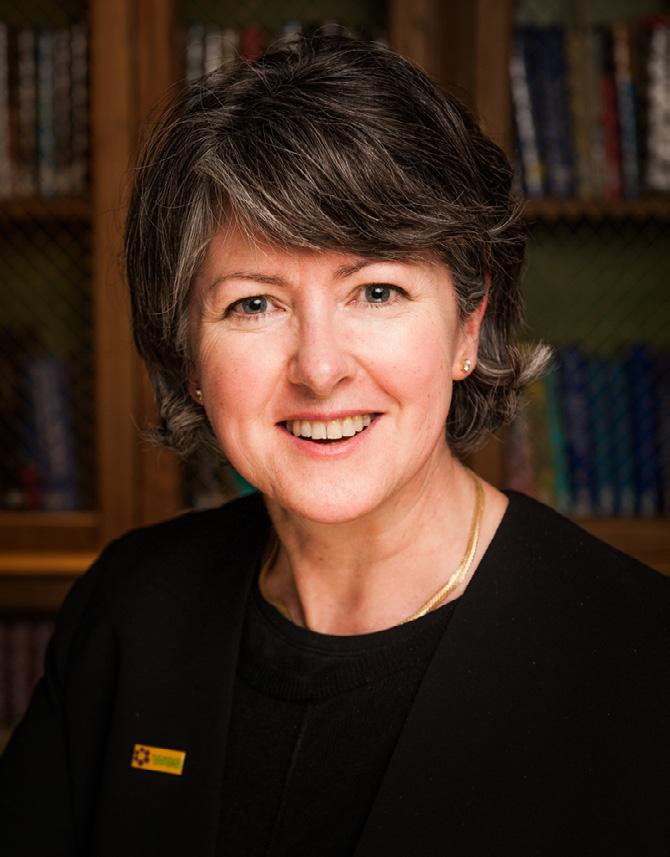
Dr Nadia Kourra (EngD), NMITE
Dr Sarah Peers, NMITE and INWES
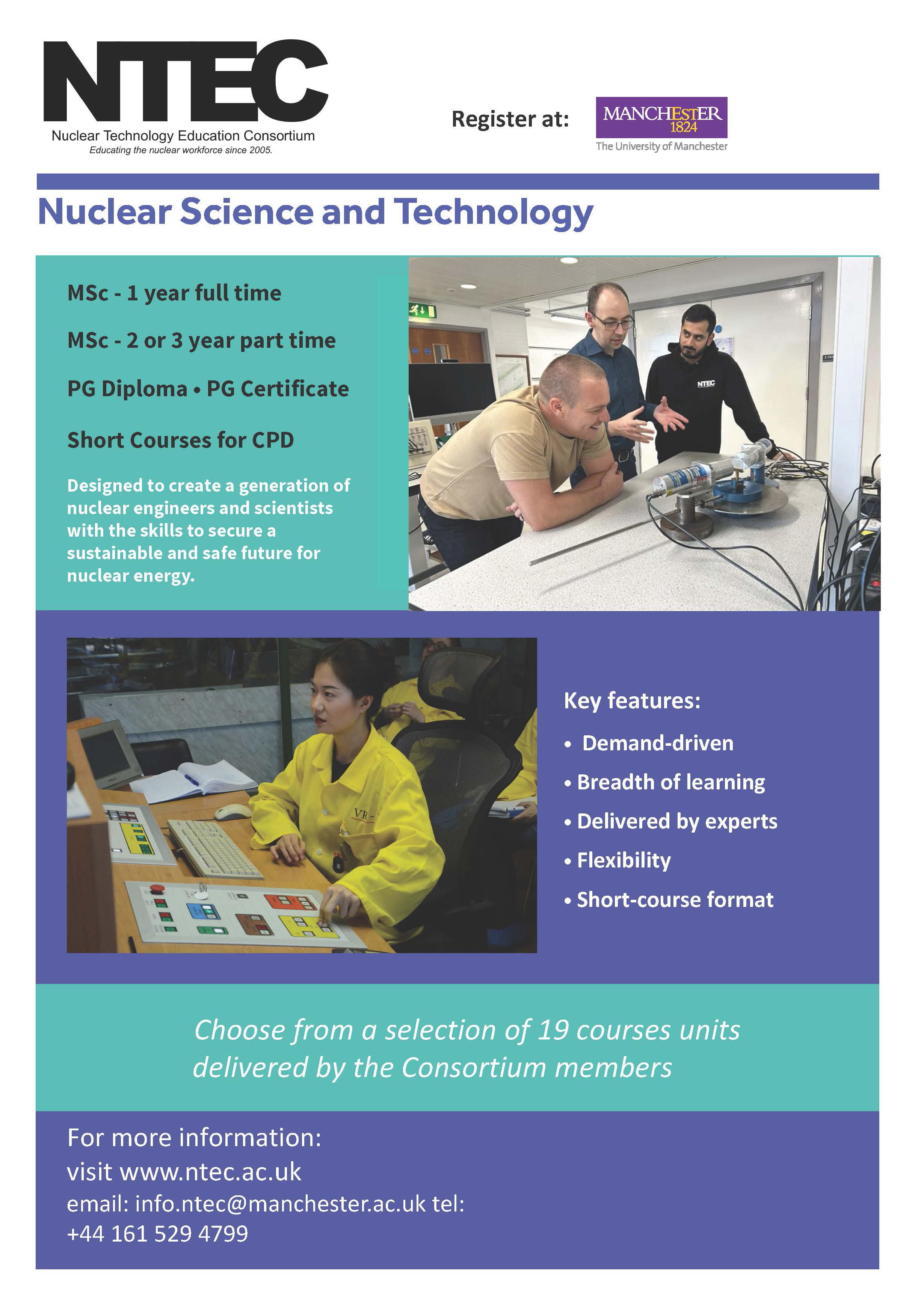
adi Group Shortlisted in Two Categories at Engineering Matters Awards
Multidisciplinary engineering firm adi Group’s commitment to develop its future workforce has been acknowledged by a shortlisting for the 2025 Engineering Matters Awards.
The Birmingham-based business’ apprenticeship programme was entered into the Community and Diversity and Inclusion categories and has made the shortlist for the award ceremony, which will be held at the
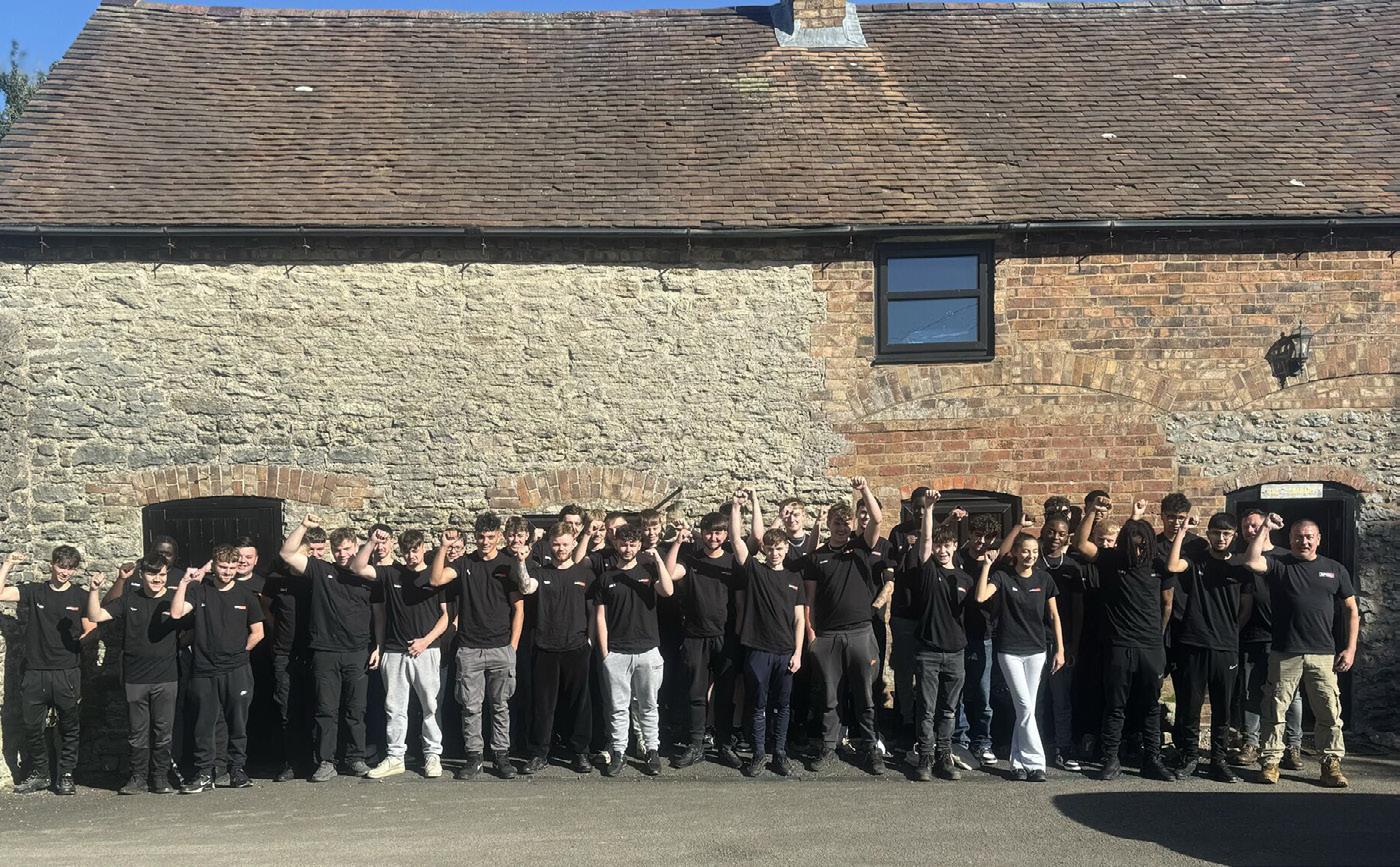
Postal Museum in London on 27th March 2025.
In 2024, adi Group celebrated 10 years of its Apprenticeship Academy by hosting a special two-day event for its apprentices, designed to help improve their communication, teamwork, time management and problem-solving skills, and enhance their engineering know-how.
Throughout the last decade, the firm has seen its staff in earn-andlearn positions exceed 10% of its overall workforce, which has earned it Platinum Membership with The 5% Club, which recognises companies that are making a difference in providing the next generation with work opportunities.
adi is making great strides in developing the next generation of engineers, helping close the widening skills gap by attracting new talent to the profession.
Find out more at adiltd.co.uk/ apprentice-academy
Ideal Heating strikes gold in national manufacturing awards
Ideal Heating’s commitment to employee wellbeing has been recognised in prestigious national awards.
The UK heating industry market leader was honoured with the Manufacturing Matters prize at the Make UK Manufacturing Awards
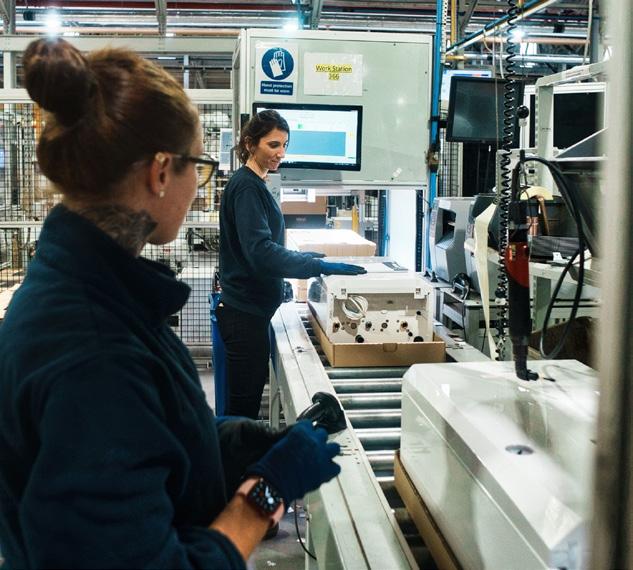
2025, focused on businesses which have had a positive societal impact.
Organised by Make UK, which represents more than 20,000 businesses, the awards celebrate manufacturing excellence and showcase talent across the UK.
Judges noted that Ideal’s investment in staff wellbeing was “one of the most impressive examples they had come across”.
Ideal was recognised for its extensive efforts to support the wellbeing of its staff including the significant upgrading of its manufacturing facility on the Hull site and the provision of physiotherapy and other facilities to aid staff welfare.
As part of its commitment, Ideal also delivered a £1.9m “Physical
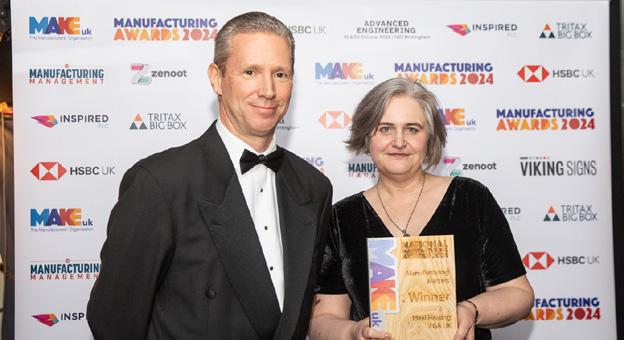
Spaces” investment programme to enhance team facilities at its headquarters site.
The company’s commitments to supporting staff wellbeing are enshrined in its Wellbeing Charter, with other initiatives including the introduction of Mental Health First Aiders and monthly financial wellbeing updates.
For the full list of winners in the Make UK Manufacturing Awards 2025 click here.
Events & Awards
The Princess Royal awards outstanding individuals and organisations advancing gender equity in STEM
Her Royal Highness The Princess Royal, Patron of the WISE (Women into Science and Engineering) Campaign, joined the organisation to award outstanding individuals and companies making significant strides towards gender equity in Science, Technology, Engineering and Maths (STEM).
Her Royal Highness presented two prestigious honours in her name, with digital changemaker Lella Violet Halloum receiving The Princess Royal’s WISE Rising Star Award.
Named one of the most influential women in UK technology, Lella has spearheaded transformative initiatives that empower underserved and underrepresented communities worldwide. A self-taught coder at aged, 8, Lella sat her GCSE in ICT at age 11, and began her professional journey with IBM from there. She now leads global student outreach for IBM Z.
Professor Elena Rodriguez-Falcon received The Princess Royal’s WISE Lifetime Achievement Award for her contribution to the sector. Elena is a globally recognised expert and leader in engineering education, specifically in inclusive and international learning and teaching. She was celebrated for her dedication to making engineering more accessible for underrepresented groups and the way she has challenged and reshaped traditional concepts of teaching.
During the high-profile event, Her Royal Highness met with all award winners, finalists, and sponsors and she spoke with attendees on the importance and ongoing mission for gender parity in STEM.
As Patron since 2000, HRH The Princess Royal has attended many WISE events throughout the years including its 2022 WISE COVID Unsung Heroes Awards, the online celebration of the WISE 1 of the Million campaign
and the WISE conference in October 2024.
This year’s Awards took place at IET London: Savoy Place on Thursday, 20 February, with sponsors including Amazon, BAE Systems, BDO, ECITB, GCHQ, the Institution of Engineering and Technology, Northrop Grumman, Pfizer, STEM Returners and supported by the ERA Foundation.
As well as the WISE Awards and annual conference, WISE’s products include its ‘Ten Steps Programme’ and ‘My Skills My Life Programme’.
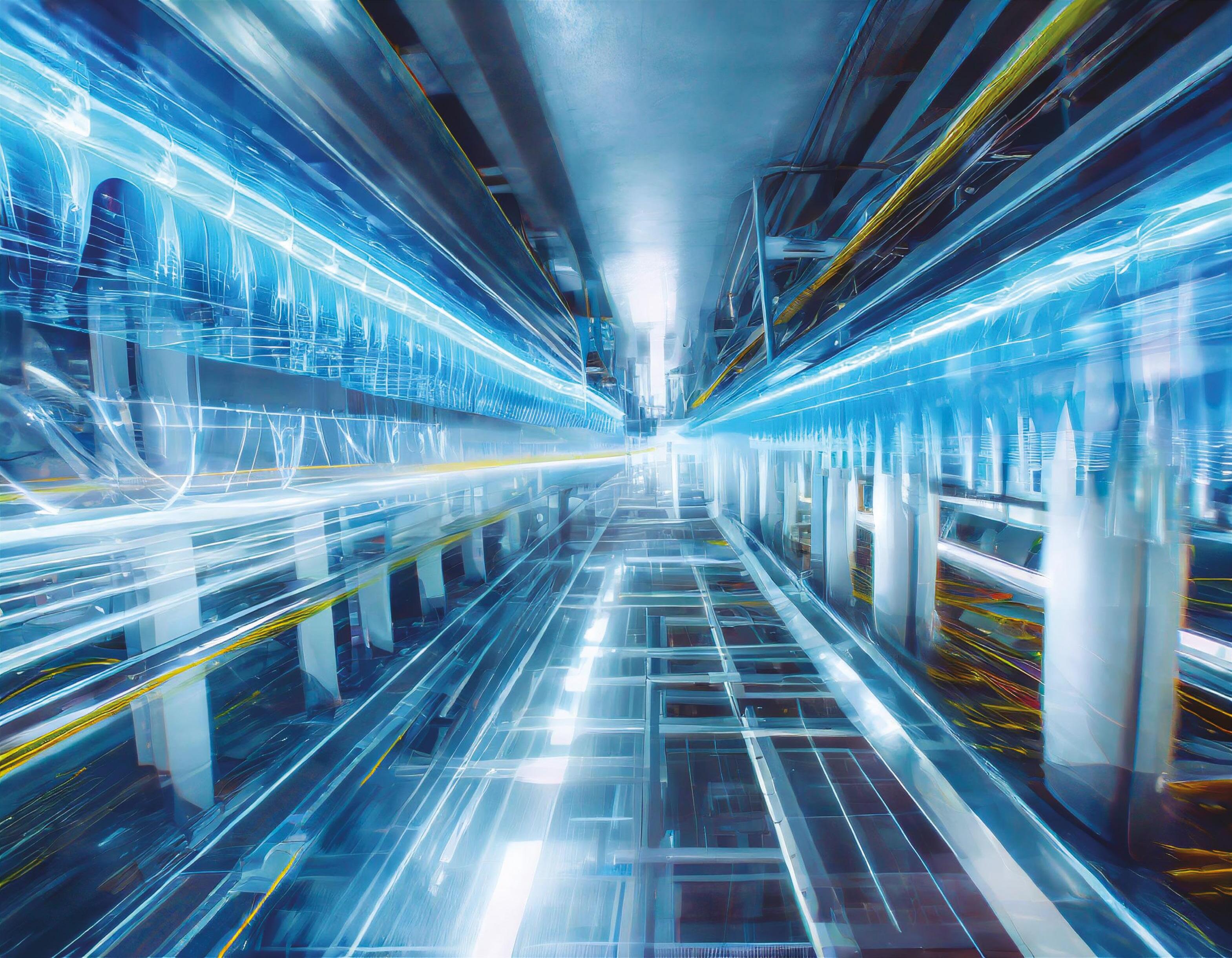
Digital changemaker
Lella Violet Halloum receiving The Princess Royal’s WISE Rising Star Award.
Instant Production Monitoring Powerful Results
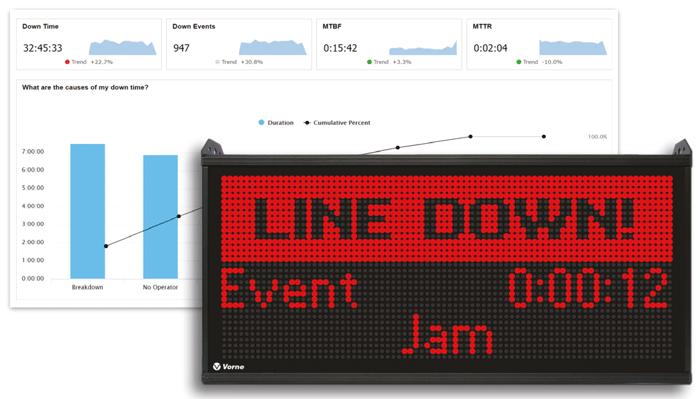
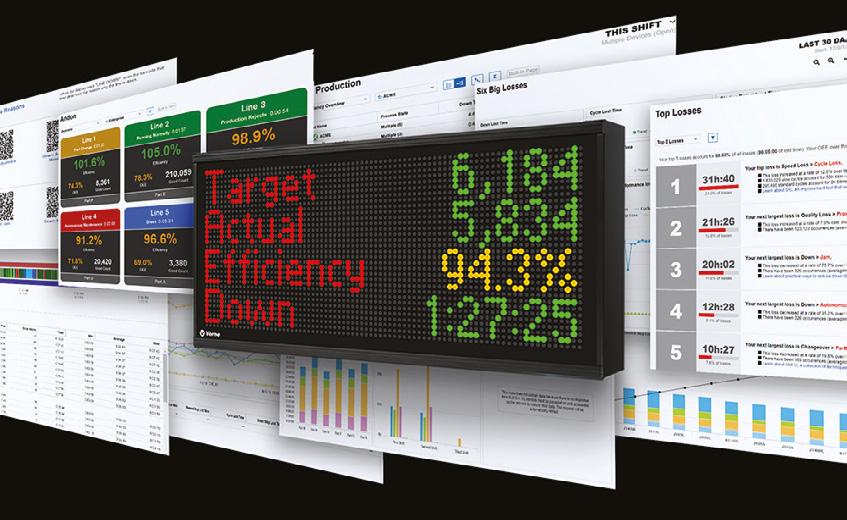
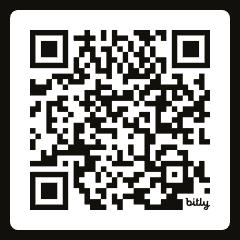
Training & Education News
South Yorkshire’s ‘Get Up To Speed with STEM’ Bigger than Ever
South Yorkshire’s largest STEM careers showcase, ‘Get up to Speed with STEM’, is set to return better than ever with up to 6,000 young people and educators set to take part.
For the first time ever, Get up to Speed will be a two day event, with the first day geared up for secondary school students (11-25 years) and the second day dedicated to primary school (aged 8-11 years) and SEND young people.
Exhibitors benefit by building relationships with young people and educators for the future, raising brand awareness and having the opportunity to engage with attendees in a highly immersive environment.
Get up to Speed offers a unique opportunity for businesses to connect directly with future talent, showcasing their innovations while helping to
bridge the skills gap in STEM. Over the 14 years, this interactive showcase has introduced STEM career opportunities to more than 45,000 young people, parents and teachers.
Beginning with a Business Breakfast, which showcases the region’s current talent and explores the skills and expertise needed in the next 15 years, young people will then have the opportunity to explore and get hands-on with many of the region’s STEM innovations and discover the broad range of exiting careers and opportunities that await them.
To mark the 15th anniversary, GUTS are hosting a special after-show celebration, “The Big 15”, open to all exhibitors, sponsors and anyone who just wants to join in the fun and celebrations.
For more details visit: www.getuptospeed.org.uk/
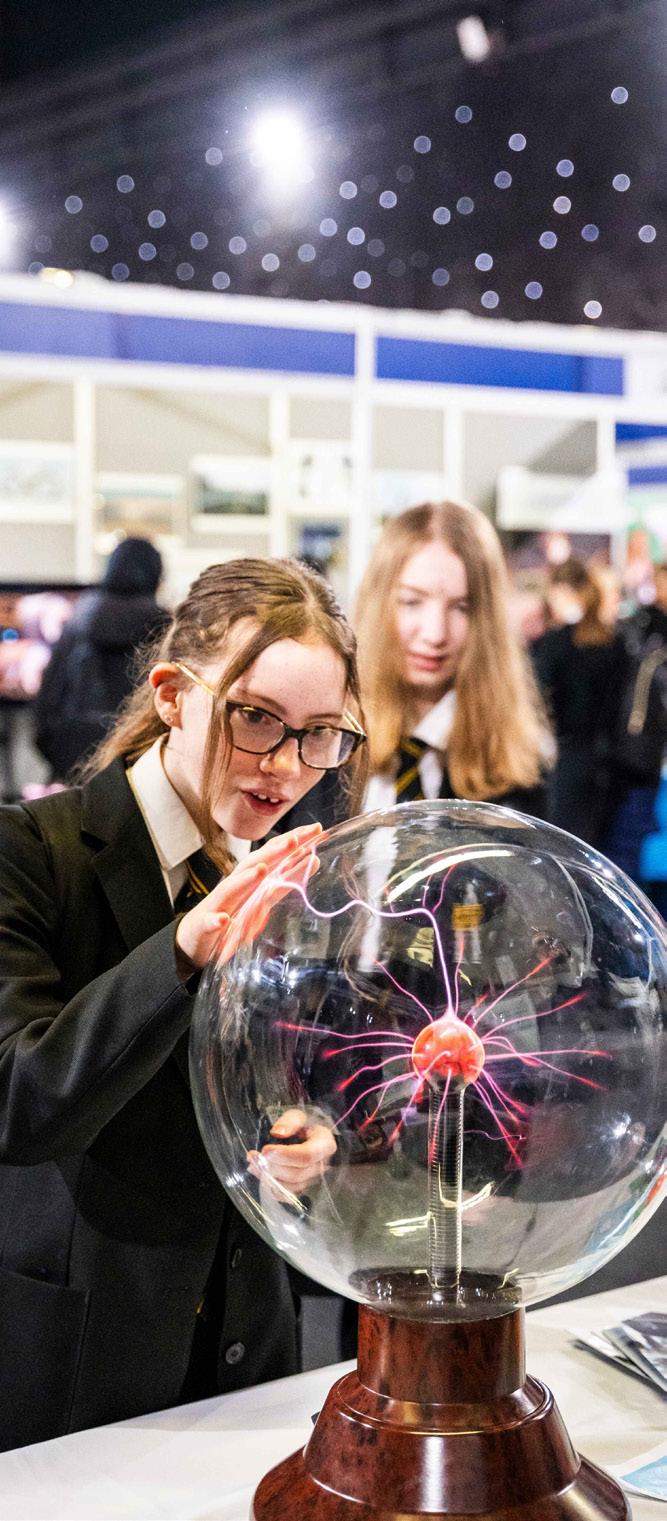
Discovery Education Presents New Resources
Discovery Education, creator of essential K-12 teaching and learning solutions, is offering a new suite of diverse digital resources; immersing students in the future of engineering and
helping create pathways for students seeking engineering careers.
Discovery Education’s curated new collection of standards-aligned, high-quality resources includes
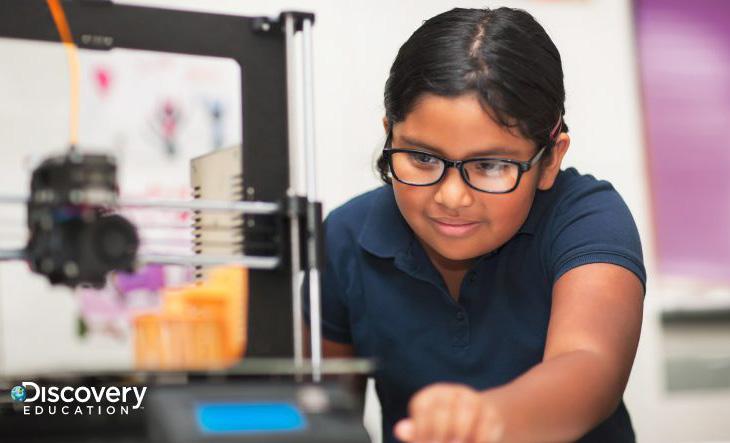
The Engineering Channel, offering diverse content segmented by grade band, Career Connect, promoting student curiosity by connecting classroom learning to real-world applications and potential careers, and Engineering Lessons, available to users of Mystery Science by Discovery Education offering an engaging standardsaligned science curriculum for grades K-5.
The STEM Careers Coalition, an alliance of industries and nonprofit organizations, reaching 11M+ students with equitable access to STEM resources and career connections, also offers a collection of career profile videos spotlighting engineering professionals in STEM. The Coalition will continue to ignite student curiosity and influence a diverse future workforce.
For more information visit www.discoveryeducation.com.
Training & Education
FANUC UK seeks the next young robotics superstars
Leading industrial automation specialist FANUC UK is continuing its commitment to inspire the next generation of engineers by supporting a search to find the UK’s best young robotics talent.
For the fifth year in succession, the company is partnering with WorldSkills UK for the annual Industrial Robotics competition, aimed at giving young people the opportunity to learn how to programme a robot, enhance their engineering prowess, develop valuable workplace skills and earn the chance to represent Squad UK at the international finals in Tokyo.
The competition is open to teams of two young people, who must be within a year of completing a relevant Level 3 Apprenticeship and/or hold qualifications in an engineering-based subject (to a minimum Level 3 or equivalent).
The first stage of the competition takes place online from 22-25 April 2025 and will comprise a virtual task using FANUC’s Robot Simulation Software. Successful competitors
will then be invited to take part in the live Qualifiers Round, where they will complete a timed robot task at the Smart Factory Expo at the NEC, Birmingham on 4-5 June.
FANUC’s team of robotics experts will provide hands-on training to participants ahead of the National Finals, to be held in Coventry on 11-13 November 2025 at FANUC UK’s Open House event.
The current UK champions are Aled Gore and Morgan Leyson, both
aged 21 and studying Mechanical Engineering at Bridgend College, in conjunction with Renishaw.
The contest has been designed to accommodate participants with different abilities and is accessible to those with little to no knowledge of robotic systems, as well as those with a robotics background.
Register in teams of two via the WorldSkills UK website from 3-28 March 2025 here.
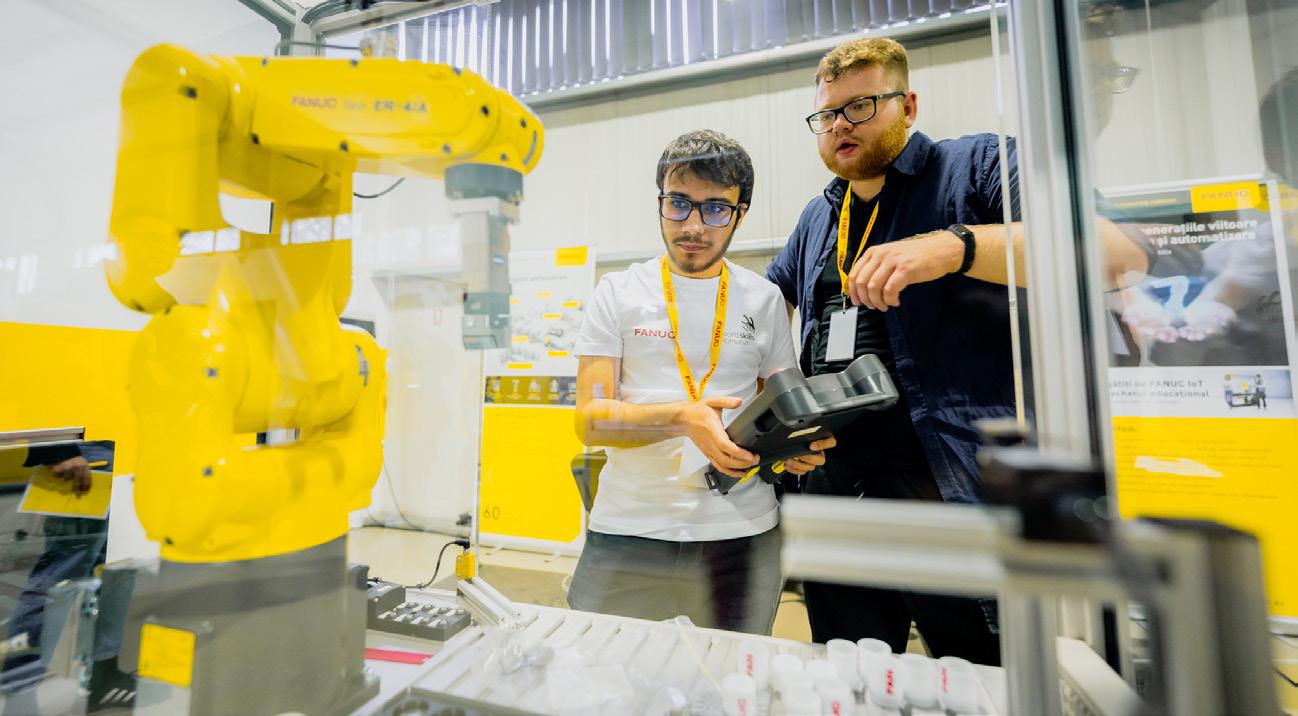
Importance of degree apprenticeships to the manufacturing and engineering sectors laid bare by new study
The findings come from Manchester Metropolitan University, a University Vocational Awards Council (UVAC) member organisation, which conducted the study using data from over 5,000 apprentices and more than 600 employers, highlighting the critical role degree apprenticeships play in driving productivity, social inclusion and tackling the skills gap.
From a recruitment perspective, 93% of firms are investing in higher
and degree apprentices to bolster their talent pipeline, whilst 91% agreed they help address skills gaps within their business.
The report also provides an insight into the potential impact of the government’s proposed changes to the Apprenticeship Levy, which aims to shift funding priorities towards lower-level and new foundation apprenticeships for young people and those at the start of their careers.
The research highlighted the career and earning potential degree
apprenticeships offer, with 63% of qualified apprentices from across a broad range of sectors now earning £40,000 or more. Those completing a degree apprenticeship experienced median salary increases of 44% during the programme, resulting in 70% of employers reporting productivity gains as a result.
The ‘Force for Impact’ report is freely available to view here.
Further information on UVAC is available at www.uvac.ac.uk.
MAHLE Powertrain supports heavy-duty hydrogen combustion engine development
MAHLE Powertrain has entered the testing phase of a key project that will drive hydrogen fuel use in existing heavy-duty truck engines.
Project Cavendish, a £9.8m government-funded programme facilitated by the Advanced Propulsion Centre UK (APC), will deliver fast-tomarket solutions and a clear upgrade path to enable hydrogen combustion using current platforms and
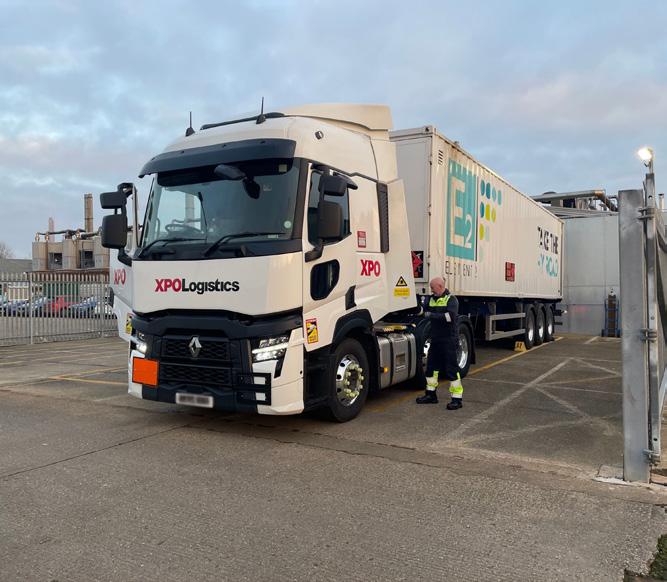
infrastructure, thereby accelerating the decarbonisation of the haulage sector. Crucial to the project is the use of MAHLE Powertrain’s flexible testing facility in Northampton, combined with the company’s experience with alternative fuels such as hydrogen and methanol.
The EU’s recently revised CO2 standards for heavy-duty vehicles, as part of the EU’s “Fit for 55” legislative package, require a 45% reduction in CO2 emissions by 2030, rising to 65% by 2035 and 90% by 2040.
In response to this legislation, the UK Government has committed £8.3bn in Great British Energy to invest in the hydrogen industry and up to £21.7bn for the carbon capture industry to pave the way for large-scale infrastructure projects. The technology will complement fuel cell electric vehicles in driving a common requirement for hydrogen infrastructure that will be used for many decades. The potential
The EU’s recently revised CO2 standards for heavyduty vehicles, as part of the EU’s “Fit for 55” legislative package, require a 45% reduction in CO2 emissions by 2030, rising to 65% by 2035 and 90% by 2040.
for hydrogen use extends beyond highway transport into rail, aviation and maritime applications.
Project Cavendish draws on the experience of a number of partners including PHINIA, BorgWarner, Cambustion, Hartridge and MAHLE Powertrain to develop novel fuelinjection systems and supporting turbocharging technology that can be ready for high-volume production in time to meet EUVII/US27 legislation.
NIS Group secures 500 new jobs with the launch of Transport, Rail and Infrastructure Academy in Aston
NIS Group and City of Wolverhampton College officially unveiled its latest Transport, Rail and Infrastructure Academy (TRIA) site in front of more than 100 people, including Cllr Sharon Thompson, deputy mayor of the West Midlands, with employers from multiple infrastructure sectors pledging more than 500 new jobs for learners.
Delegates heard how the leading training provider has partnered with the college to develop the academy and jointly invested £250,000 into transforming the building into a dedicated facility, offering a 15-metre high-speed slab track, 30 metres of conventional track, one high speed set of points, one level crossing barrier and training
facilities for civil engineering programmes.
Employers including Buildforce Solutions, Linsco, Randstad and Danny Sullivan Group, have thrown their support behind the venture, guaranteeing opportunities for people progressing through the courses to work on a host of existing and future construction and rail projects across the region.
In addition, ISS and NIS Group have launched the official training and employment partnership, which will ensure learners interested in rail career opportunities, will be offered work across the Network Rail infrastructure.
TRIA Aston is the third dedicated academy in the NIS Group’s West Midlands portfolio
and follows its original base at City of Wolverhampton College’s Wellington Road campus in Bilston and the Black Country Innovative Manufacturing Organisation (BCIMO)’s Very Light Rail National Innovation Centre in Dudley.
For further information, visit www.nisgroup.co.uk.
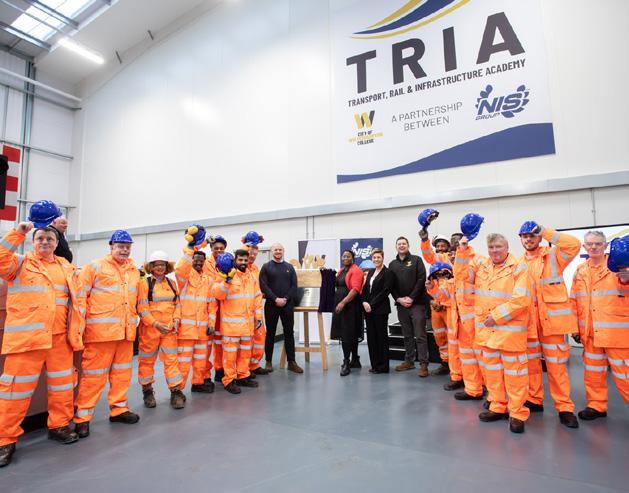
Veolia innovation saves 12GWh of gas use using new distillate product to reduce carbon emissions
The latest innovation from Veolia, a leading resource management company, is now saving 12GWh of gas use per year by using a new distillate product as a fuel for the steam plant that supports the solvent recovery operations at its Garston, Liverpool facility.
By developing and testing the new fuel, and using it as a substitute for fossil fuel, the site now displaces
the equivalent of 1.1 million m3 of natural gas, enough to heat over 1,000 houses for a year. Replacing this gas use with fuel derived directly from the solvent recovery operation means the site is now saving 2,500 tonnes of carbon per year from its own energy demand.
The Garston site takes materials from industry and regenerates these into high quality recycled
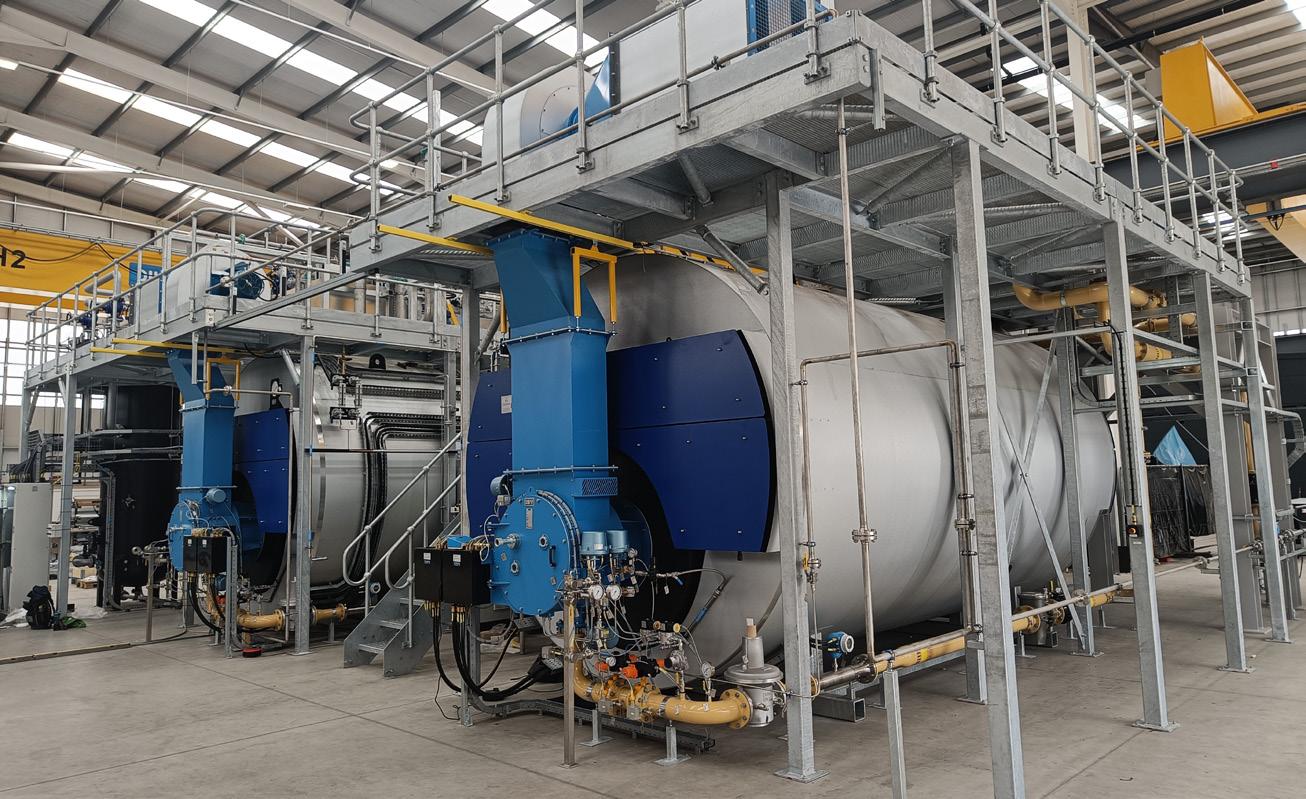
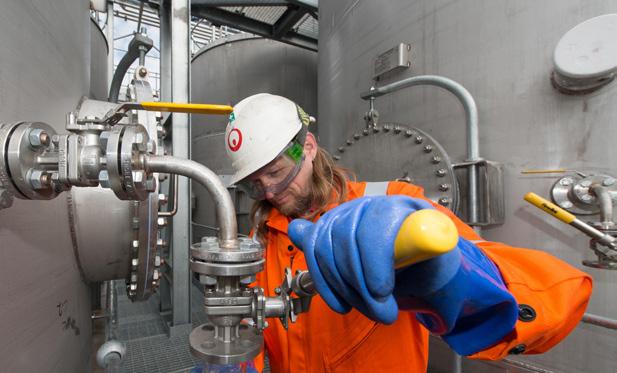
products, displacing virgin materials in the supply chain by using various distillation technologies to make new products for industrial customers. With the growing demand for solvent recovery across the pharmaceuticals, semiconductors, paint and agrochemicals industries, the Garston site needed to expand operations which required a new steam plant to generate the high volumes of steam needed to support production.
To support the operations, Veolia wanted to decarbonise the energy use by replacing natural gas with an alternative greener fuel to reduce the carbon footprint.
For more information visit www.veolia.co.uk
Interest in automated warehouse technology surges as logistics companies look to cut wage bill following Chancellor’s Budget statement
Toyota Material Handling says it has experienced a surge in enquiries for its range of automated and robotic warehouse solutions since the increase in National Insurance employer contributions was announced in the Government’s autumn budget statement.
The hike in the rate at which NI contributions are paid – from 13.8 per cent to 15 per cent – combined with a lower threshold after which employers start paying NI on an employee’s
salary, has added considerably to the wage bill of most companies.
Indeed, it is estimated that for each individual forklift truck driver employed on an annual salary of around £23,400 the NI changes will add in the region of £800 per operator, per year, to a company’s staff costs.
Toyota’s Paul Freeman, Head of Business Development says: “By effectively making it more difficult and costly to recruit warehouse personnel, the Chancellor of the Exchequer has
accelerated the trend for companies in all sectors to introduce automated and robotic solutions as a way of mitigating the impact of the high cost of labour on operating overheads.”
According to Paul Freeman, companies are particularly keen to explore the role that driverless forklift truck technology could play in their intralogistics processes.
Visit https://toyota-forklifts. co.uk/automated-solutions/ to find out more.
Machine Safety Systems Machinery & Machining
Machine safety systems are paramount in today’s industrial landscape, where the integration of advanced technologies poses potential risks. As Industries embrace automation, the demand for tellable machine safety applications continues to grow, driving advancements in this sector.
Robotics
A manufacturing assembly line consists of workstations geographically dispersed within the plant, connected by a mechanised work transport system, transporting parts from one workstation to another. Machinery parts are sequentially added and assembled until the final finished product is manufactured; a continuous, fast, and precise process which must be error-free. Ensuring machine safety is crucial because of the involvement of intricate and high-speed machinery. If not maintained and operated properly, it may lead to severe injuries or fatalities. Additionally, the machinery used in assembly lines can cause harm to products being assembled leading to defects, further emphasising the importance of machine safety solutions. Moving parts of machinery and other potential hazards can also harm to workers; therefore, it is necessary to adopt machine safety measures which involve the use of a shield to prevent contact with the operator.
With technological advancements in the field of robotics, safety regulations for robots are being rewritten with unique specifications. The 1506-6 specification guideline promotes the deployment of a collaborative model that comprises safety-monitored stops, hand-guiding speed and separation monitoring, and power and force-limiting robotic products. Machine safety functions, such as controlling limiting and positioning, are critical for industrial automation, sensing emergencies and preventing robots from damaging effects.
Packaging
Packaging systems also include several parts that are prone to accidents, such as conveyors, flat belt
conveyors, transmission components, and trapping points, increasingly incorporating safety sensors and guarding to prevent these incidents. Among the widely used guarding systems during packaging are safety light curtains and interlocks, which create physical barriers to shield machines from dangerous environmental materials.
The demand for more efficient and automated packaging machines has created a need for enhanced safety measures. As a result, manufacturers have been developing advanced safety technologies to mitigate safety risks associated with packaging machines. Manufacturers are also integrating safety features while designing packaging machines. For instance, emergency stop buttons are easily accessible to workers for quick use in an emergency.
Material Handling
Various process-oriented industries require huge inventories, thereby making material handling crucial. Several types of machinery, robotics, forklifts, and other material-handling equipment require machine safety systems. Moving devices and parts cause potential harm to employee’s machines, and the environment.
Appropriate machine safety such as interlocks, safety guards, and warning signs, are necessary to promote the safe operation of material handling equipment and reduce the risk of accidents. Forklifts are commonly utilised in material handling, and it is crucial to implement safety measures such as conducting operator training, imposing speed limits, and performing regular safety inspections to avoid accidents. Additionally, machine safety measures, such as emergency stop buttons and barriers, protect workers from potential hazards
associated with material-handling equipment. Regular maintenance, inspection and operating equipment within its safe limits also help prevent equipment damage. Compliance with regulatory requirements related to machine safety is essential to maintain worker safety and avoid penalties. Implementing machine safety measures can minimise downtime caused by equipment damage or worker injury, leading to increased productivity and lower costs.
The machine safety market is projected to grow by 2029. Key factors driving the demand for machine safety systems include strict industrial safety mandates and high requirements for reliable safety systems to ensure personnel, assets, and environmental protection. However, the need for high capital investment to install machine safety systems, a lack of awareness, and the complexity of implementation are all key factors restraining the growth of the machine safety market.
Nonetheless, the machine safety presents significant opportunities driven by increasing industrial automation and the need for worker safety. Growing awareness of regulatory compliance, adoption of advanced safety technologies, and the rising emphasis on preventing accidents contribute to a thriving market poised for expansion in diverse industries.
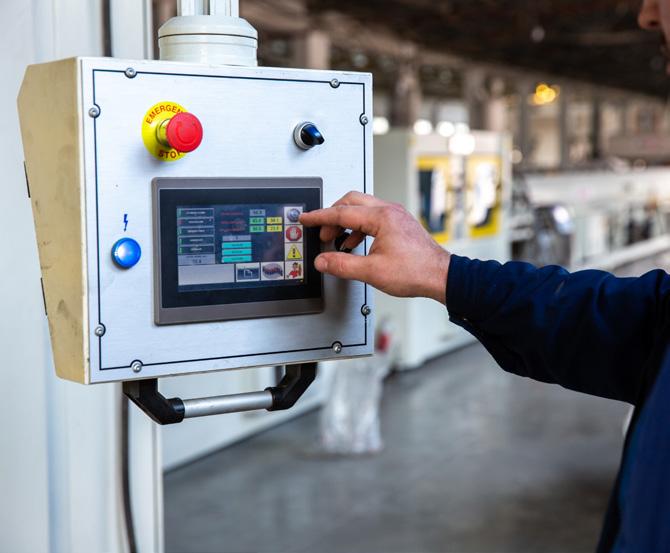
Pentagon, pro-actively supporting you from the early stages of design assistance right through to mould tool manufacture and repeat production of your injection moulding project. Your new or existing plastic injection moulding project will benefit from years of technical moulding experience!
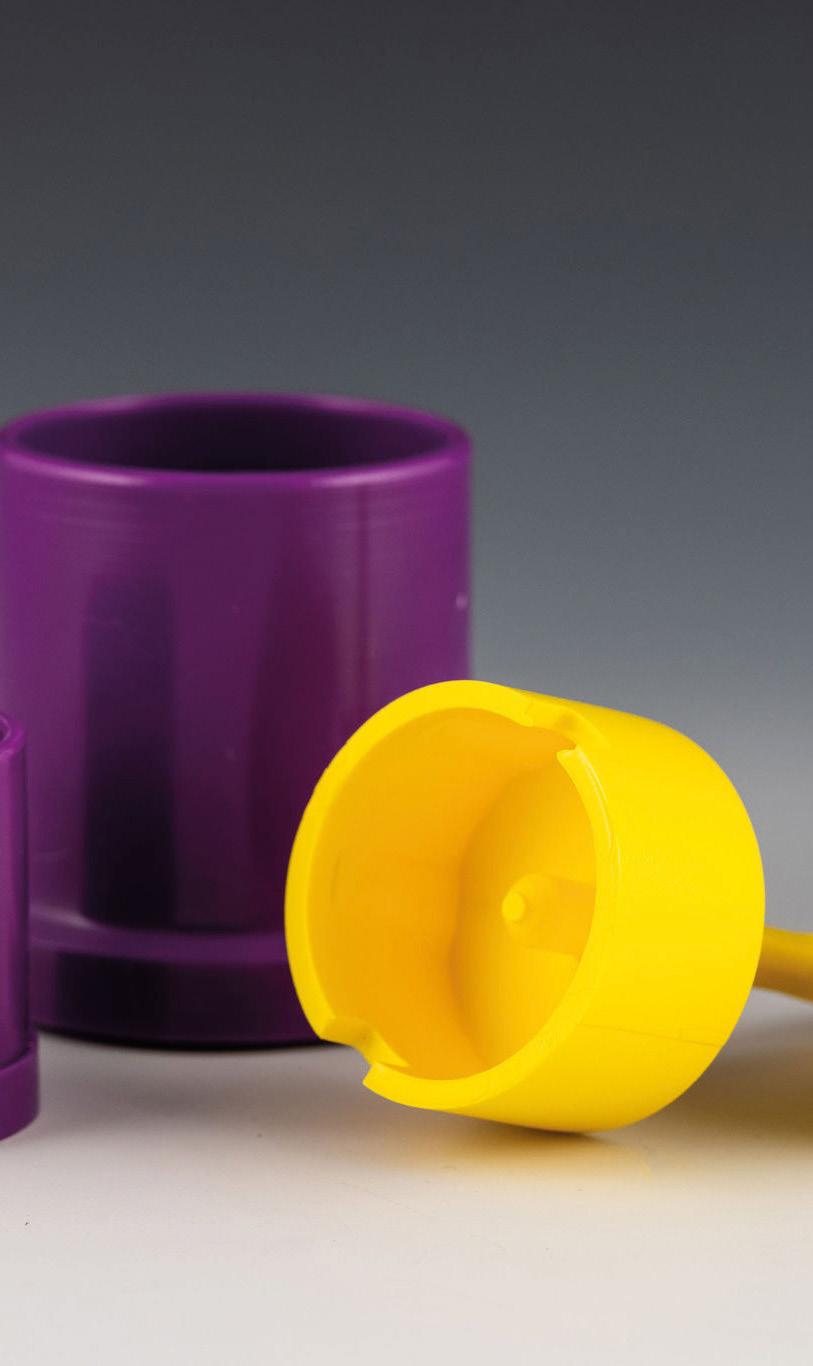
Specialist Equipment & Tools
Working smarter – and harder: How the next generation of CNC machines is transforming precision manufacturing
CNC machines have long been at the heart of precision engineering, but the latest generation has changed working practices and unlocked productivity, explains Jon Higson, MD at Titan Manufacturing in Weymouth.
Historically, CNC machines have been the backbone of precision engineering, enabling the automated control of machining tools. The challenge has always been the need to use G-code to dictate every movement and operation of the machine. For complex components, creating or altering that code often required external CAD/CAM systems (computer-aided design/ manufacturing). This programming process is time consuming to master and to execute. It is also unforgiving; even a small error in the code would lead to waste or even damage to equipment.
But the new generation of CNCs is a game changer - its user-friendly interface is revolutionising how we work, unlocking greater productivity and flexibility.
Conversational Language Instead of Code
At Titan, where we specialise in
CNC precision engineering, within a full-service package, we invested £300,000 in three state-of-the-art Hurco CNC machining centres at our Weymouth facility last year.
They are incredibly easy to work with. Instead of relying on code, these machines feature ‘normal language’ programming, or conversational commands. Operators can input instructions in a more intuitive way, using menus, prompts, and dropdowns on the machine’s touchscreen display, with diagrams and previews of the toolpaths further helping to reduce errors. The models we chose allows even complex components to be programmed directly at the machine, virtually eliminating the need for a CAD/CAM or offline programming.
For businesses like Titan, the integration of next-gen CNC machines have unlocked huge gains. Because we often produce small production runs or custom parts, rapid turnaround is essential. Cutting down the
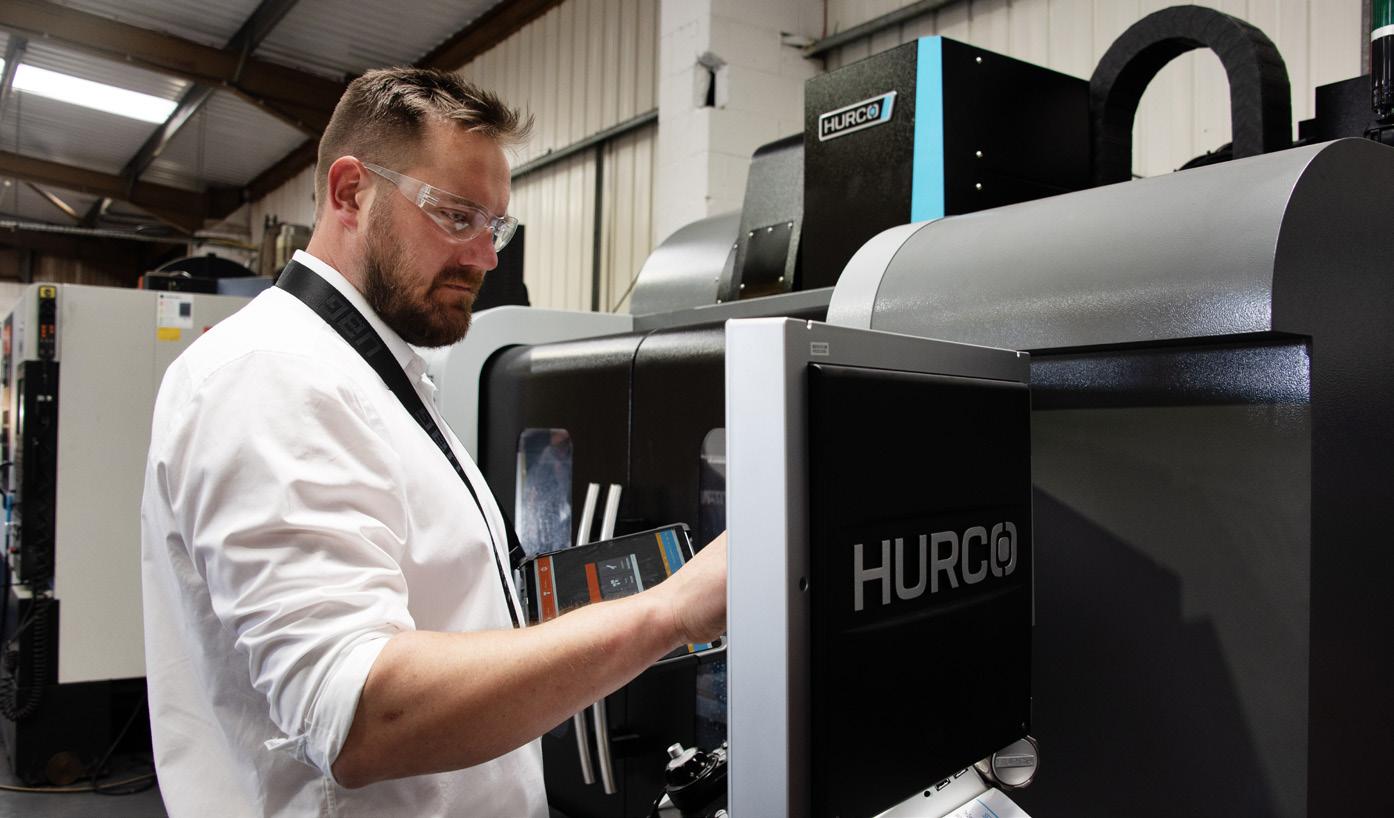
programming time and minimising downtime between jobs means increased production speed and output volume, boosting productivity and profitability.
As well as speeding up the “print-topart” process, the ability to program directly on the machine makes it easier to handle last minute design changes or customisations on the fly – another big plus for our customers.
Smart and Getting Smarter
While an older-style CNC machine can only execute as programmed, even if an error in the code meant that the machine would tear itself up in the process, the new models come equipped with smart-error detection – alerting the operator if they have asked for something impossible or made an error that risks damage or unnecessary wastage.
The new CNC machines can also ensure the machining processes are optimised, again increasing productivity and minimising waste material. Ours are equipped with sensors that monitor parameters such as temperature, vibration, and tool wear, allowing for proactive maintenance and minimising costly downtime.
In short, next-gen CNCs are not only working harder by leapfrogging the hurdle of coding with conversational programming, which is easy to learn and easy to use, they are also working smarter, helping us avoid errors and deliver the precision, speed, and flexibility clients demand.
See https://titanmanufacturing. co.uk/ for more information.
Titan Manufacturing MD Jon Higson
Laser Welding with Max Photonics hand held fibre laser welding equipment Specialist
Wilkinson Star, one of the UK’s largest wholesale welding equipment distributors are proud to be the exclusive partner for Max Photonics handheld laser welding equipment in the UK and Eire.
Targeted at sheet metal fabrication industries, this technology has now been adopted into a growing list of applications including nuclear, aerospace, pharmaceutical and catering to name but a few.
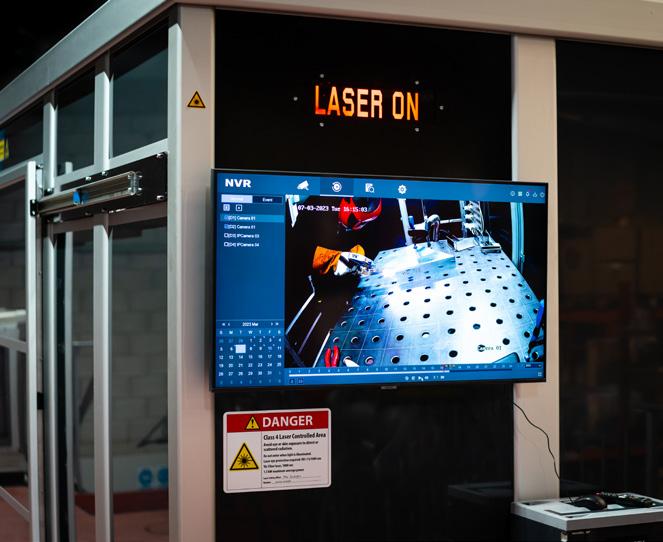
Max Photonics fibre laser technology is a great supplement to conventional welding methods in most fabrication workshops. The technology can offer many advantages over conventional welding methods as below:
• Fast welding speeds
• Minimal heat affected zone
• Minimal heat distortion
• High precision and neat welding seams
• Up to 4 times faster than TIG
• Low consumable usage
• High repeatability
• Minimal training required
• Uniform weld bead
• Ability to weld various metals as well as dissimilar materials
• Improves production efficiency
• Reduced post weld cleaning times
• Easy to use
• Low application costs
• Efficient energy usage
• High welding strength
• Excellent welding performance
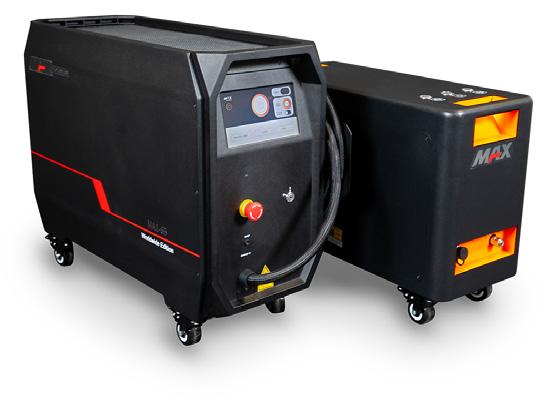
Wilkinson Star Limited are committed to offering safe solutions and guidance to customers and users.
To learn more about our range of available products please visit wilkinsonstar247.com or contact your local welding laser equipment distributor. Demonstrations are available at our training facility in Manchester. For further information please contact 0161 793 8127.
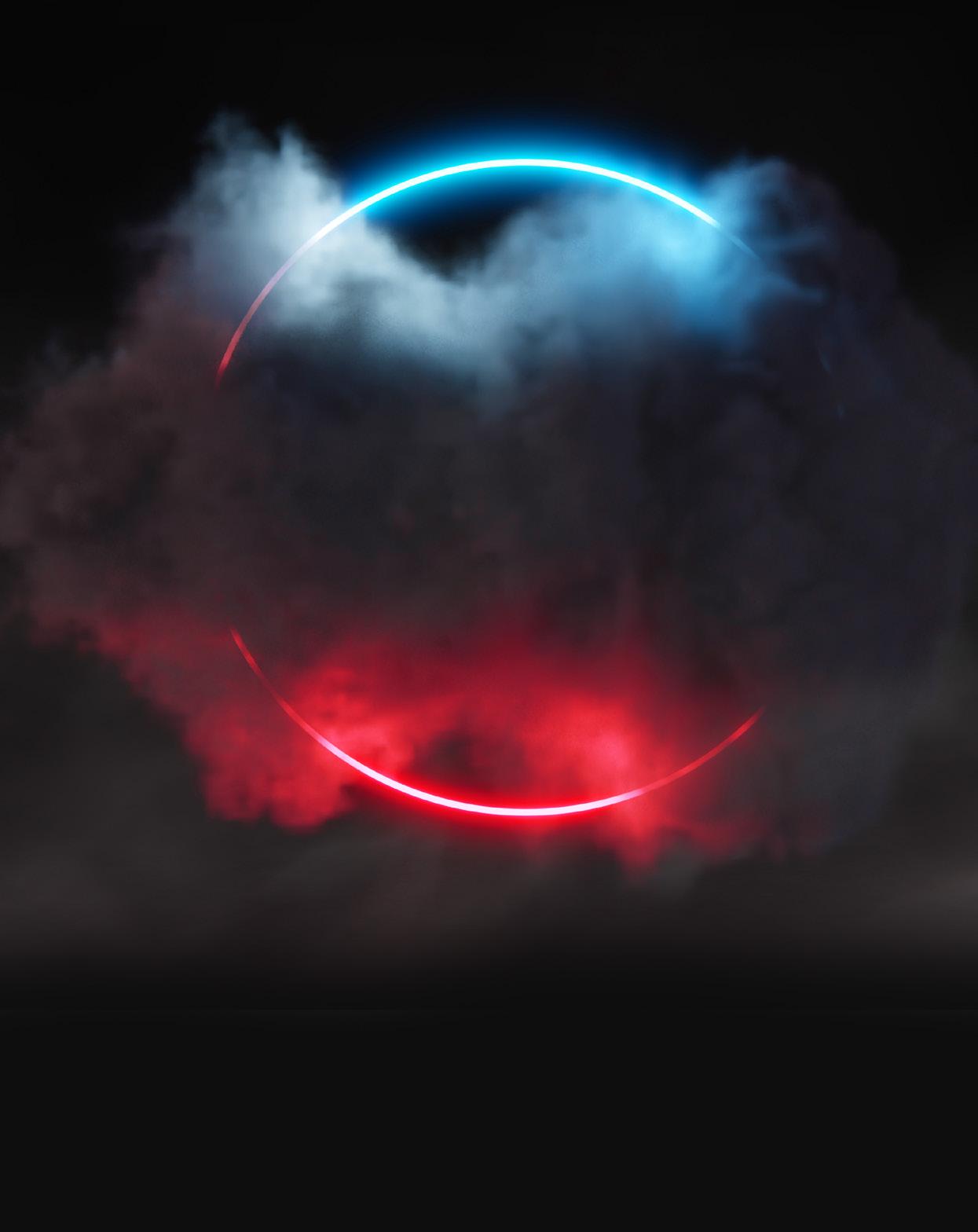
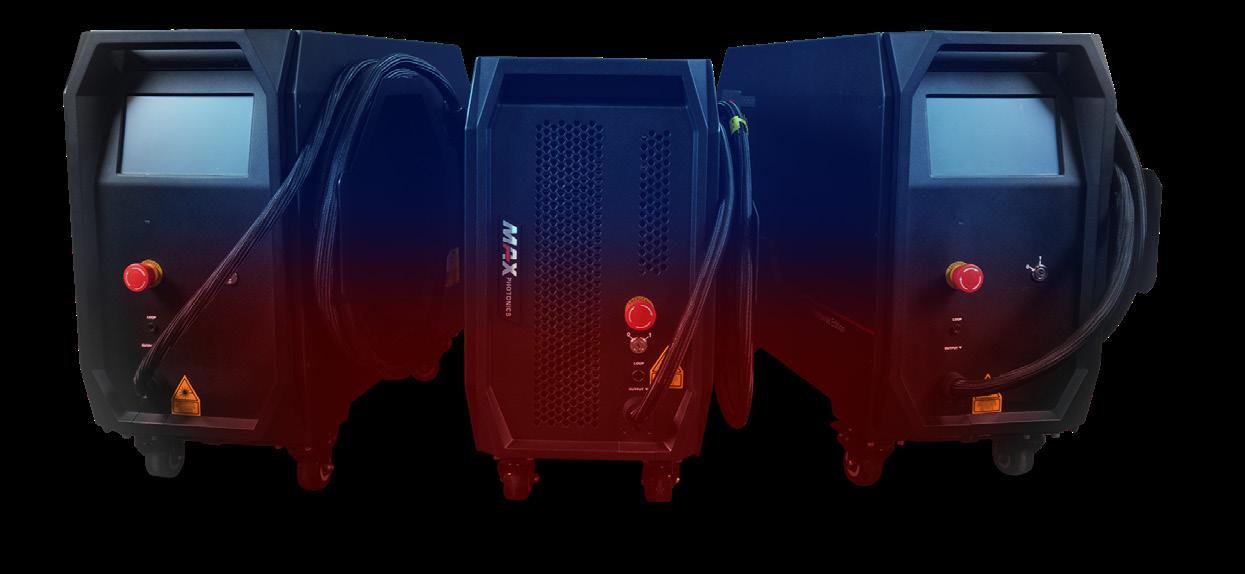
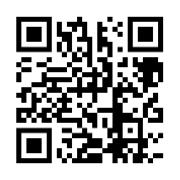
No more cheap labour – it’s time to pack smarter
Jo Bradley, Business Development Manager at Sparck Technologies
If distribution and fulfilment operations ever did benefit from ‘cheap’ labour, a series of recent Government announcements has ensured that era is well and truly over. Controlling labour costs through automation is no longer optional – it’s a question of business survival.
In short order, the Government has first raised the minimum wage by significantly more than inflation to £12.21 an hour for workers over the age of 21, Employer National Insurance contributions are rising from 13.8% to 15%, and in a further twist, this will now apply to workers on annualised pay of as little as £5,000 rather than the previous £9,100.
That last provision in particular hits the many fulfilment operations that are heavily dependent on seasonal or casual employees to cope with peak in activity. This patten of employment is about to be even further challenged by the extension of a range of workers’ rights to ‘day one’ of employment. Details are as yet obscure, but they certainly aren’t going to reduce employment costs.
The response must lie with automation, but particularly in the current uncertain economic climate, few businesses can afford the investment or business disruption required to go ‘full Amazon’ across activities such as retrieval, order picking and internal transport. These tend to be heavily interdependent, and ‘step by step’ approaches can be problematic.
One area that for many fulfilment operations can be treated as a standalone project, with the prospect of significant reductions in labour requirement, and thus an attractively quick Return on Investment, is that of packing and labelling goods into
cartons for transport. Ecommerce operations, in particular, can stand to reap big rewards in terms of savings in labour and material costs, as well as boosting productivity and performance at peak, if the right approach is taken. Our repeated customer experience is that using ‘fit to size’ automation to fold and build boxes around consignments – even of mixed and varied goods – followed by auto sealing, weighing and labelling, can see one or two operators replacing as many as twenty manual packing benches.
But in selecting automated packaging technology businesses shouldn’t focus on labour costs alone. There are other cost pressures looming, and other benefits to be reaped.
On costs, the revised Extended Producer Responsibility regulations are about to come into effect. These are complex, involving fees and credit notes and a significant administrative burden, but at heart they involve a levy on the use of packaging materials. Precise rates are yet to be fixed but the Government’s current mid-point estimates are around £190 per tonne for paper and card, and a deliberatively punitive £425 per tonne on plastic packaging materials.
This is intended to encourage firms to reduce the use of packaging materials. Fortunately for ecommerce businesses the right form of packaging automation can also provide a highly effective solution to this issue too. Sparck’s ‘fit-to-size’ automated packaging systems not only minimise the use of card used, by tailor-making a box for each individual order, but can also eliminate the need for void fillers which are often plastic based.
Those savings can go straight to the bottom line. But there are other less
easily quantifiable but nonetheless real benefits. Well-fitting boxes reduce the incidence of shock or crush damage in transit. They economise on the use of transport space, which can also yield cost savings, on fuel obviously, but also in warehouse labour as there may be fewer roll cages to push around. And right-sizing removes what research consistently shows to be one of consumers’ biggest gripes about e-commerce and home delivery –oversized boxes!
These factors together make a robust case for automation. But as employment costs bite, the laboursaving arithmetic of fit-to-size automation alone will undoubtedly present a fast and sure Return on Investment for many businesses.
More information on Sparck Technologies’ CVP Automated Packaging Solutions can be found at https://sparcktechnologies.com
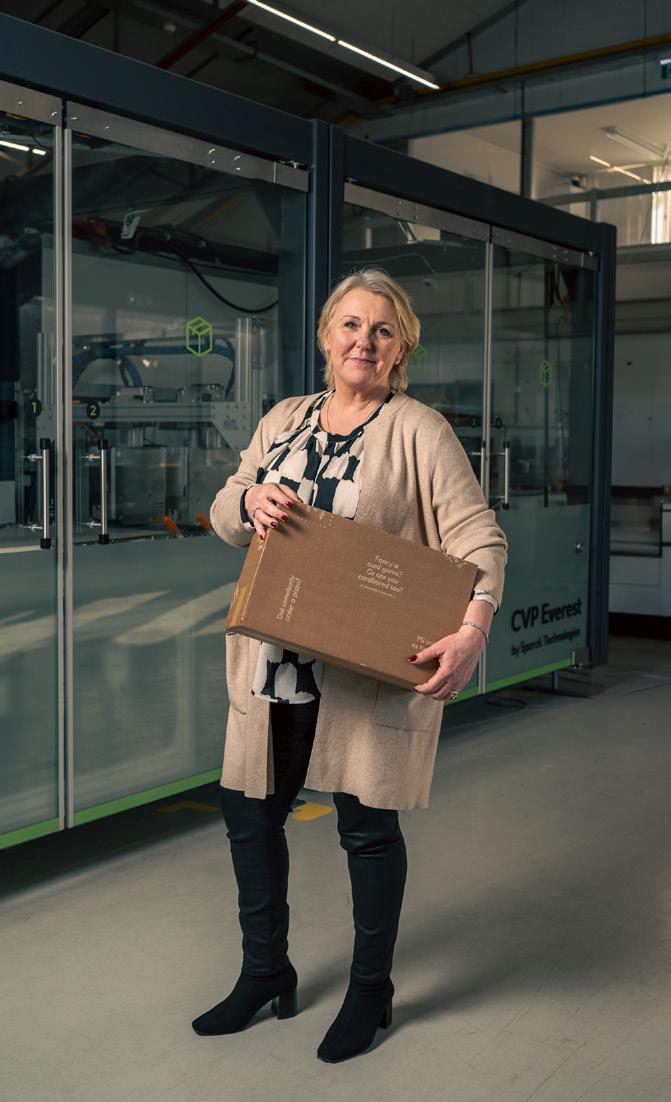

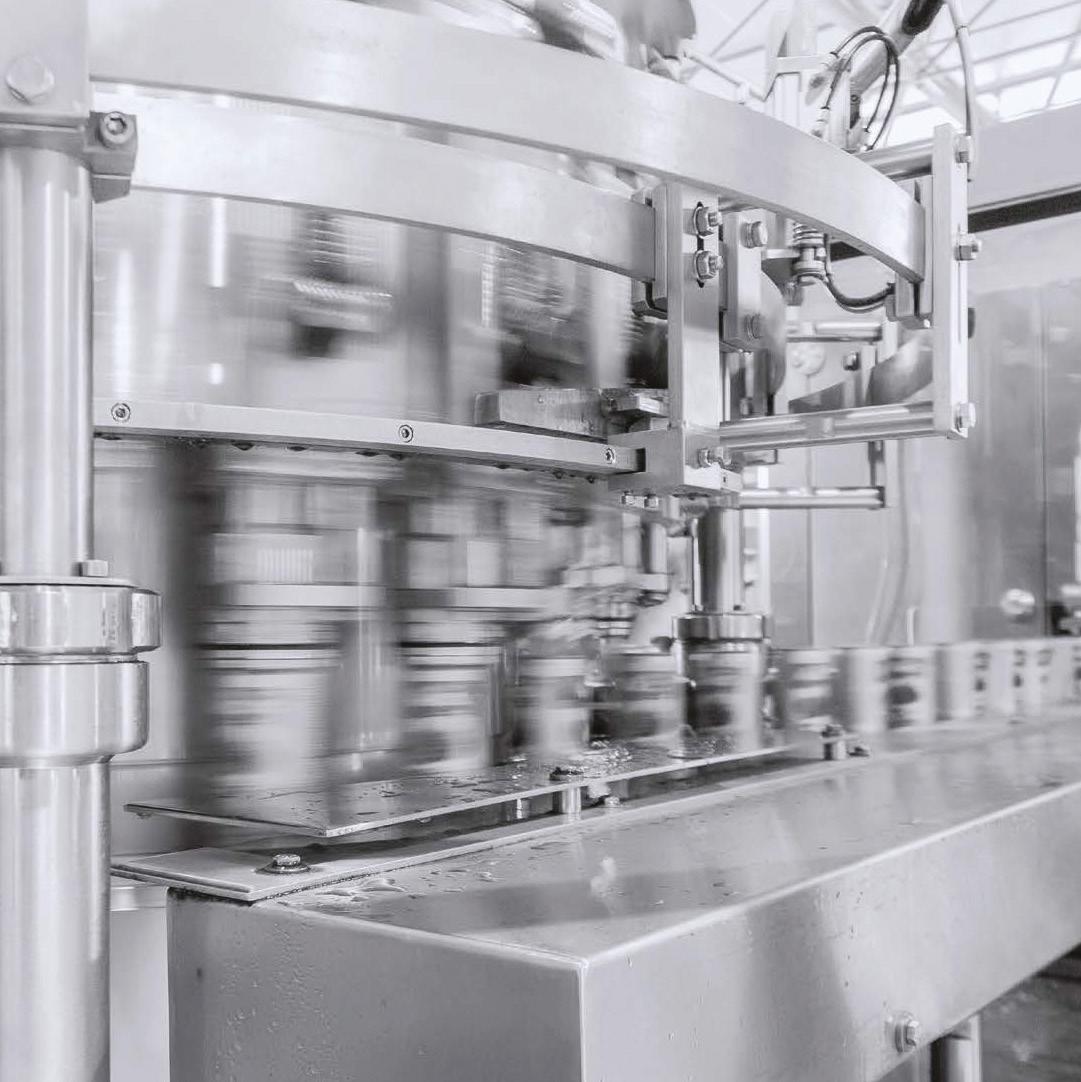
NEW ZQ901 PULL-WIRE EMERGENCY STOP SWITCH WITH STAINLESS STEEL ENCLOSURE
The new ZQ901 pull-wire emergency stop switch by Schmersal is characterised by its robust stainless steel enclosure. It offers optimal mechanical and chemical protection in harsh environments and provides the ideal solution for a wide range of applications.
Thanks to the new housing material, the ZQ901 can be used on transport and material handling systems as well as on large system used in the food processing and chemicals industries. The tried-and-tested technology, used in industrial settings, meets the highest availability standards. The ZQ901 offers an emergency-stop function and manual rest, wire break detection and lengths of wire up to 75 metres.
For more information, scan the QR code to download your free brochure.
SCHMERSAL | Enigma Business Park Malvern, Worcestershire, WR14 1GL
www.schmersal.co.uk
uksupport@schmersal.com
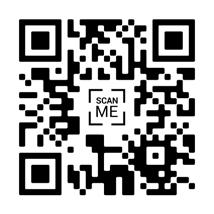
KnitMesh Technologies Appoints Peter Evans and Paul Radford as Directors
KnitMesh Technologies, a leading manufacturer of knitted wire mesh components for industrial applications, has announced the recent appointment of Peter Evans and Paul Radford as Directors of the company.
The company is currently experiencing rapid growth in the automotive, hydrogen production, and oil and gas industries and has a strong presence in international markets.
Peter Evans, who has been with KnitMesh Technologies since 1998, was recently appointed to the position of Managing Director, leveraging his
The company is currently experiencing rapid growth in the automotive, hydrogen production, and oil and gas industries...
26 years of experience and deep understanding of the business. Paul Radford joined the company in 2021 and holds the position of Finance Director and Company Secretary, bringing his expertise in finance and strategic planning to the board.
KnitMesh Technologies is currently working with the world’s leading green hydrogen producers to supply knitted wire mesh for electrolysers. The company has also re-entered the mist eliminator market, rapidly expanding its market share. Peter and Paul’s strategic appointments align with these key initiatives, which aim to accelerate business growth and enhance market competitiveness.
These new changes in the company structure also represent a strategic shift towards effective succession planning, allowing KnitMesh Technologies to capitalise on emerging opportunities while adapting to the changing demands of the global marketplace.

Leading Engineering Firm adi Group Appoints New Chief Financial Officer
Multidisciplinary engineering firm adi Group has announced the appointment of Alex Rudzinski as its new Chief Financial Officer (CFO).
Rudzinski’s arrival is part of adi Group’s ongoing commitment to invest in its leadership and systems,
ensuring the business is wellpositioned to drive performance and align with its ambitious five-year growth plan.
Rudzinski brings over 25 years of experience in both corporate and private equity-backed businesses, where he has played a pivotal role
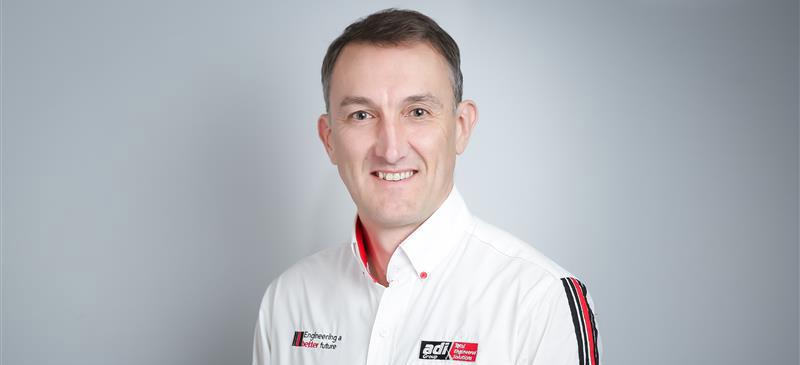
in supporting business growth, enhancing financial performance, and introducing strategic financial insight. Before joining the Group, he held senior financial roles within entrepreneurial and growthfocused businesses across a range of sectors, honing his expertise in managing complex financial structures and supporting business expansion.
As CFO, his responsibilities will focus on strengthening the Group’s financial controls, overseeing accounting functions, and ensuring the business is positioned for long-term success. This includes providing timely, actionable data that supports each of adi’s 17 businesses, and providing forwardleaning insight to the executive to allow them to make the very best decisions.

Process improvement is like cycling. Everything runs more efficiently with the right partner.
Energy optimization is the key to sustainable production. As a strong partner for strategic energy management, we help you cope with rising energy costs and tighter environmental targets. We are at your side –uncovering the ways to save and be resourceful while maintaining safety, quality, reliability, and uptime.