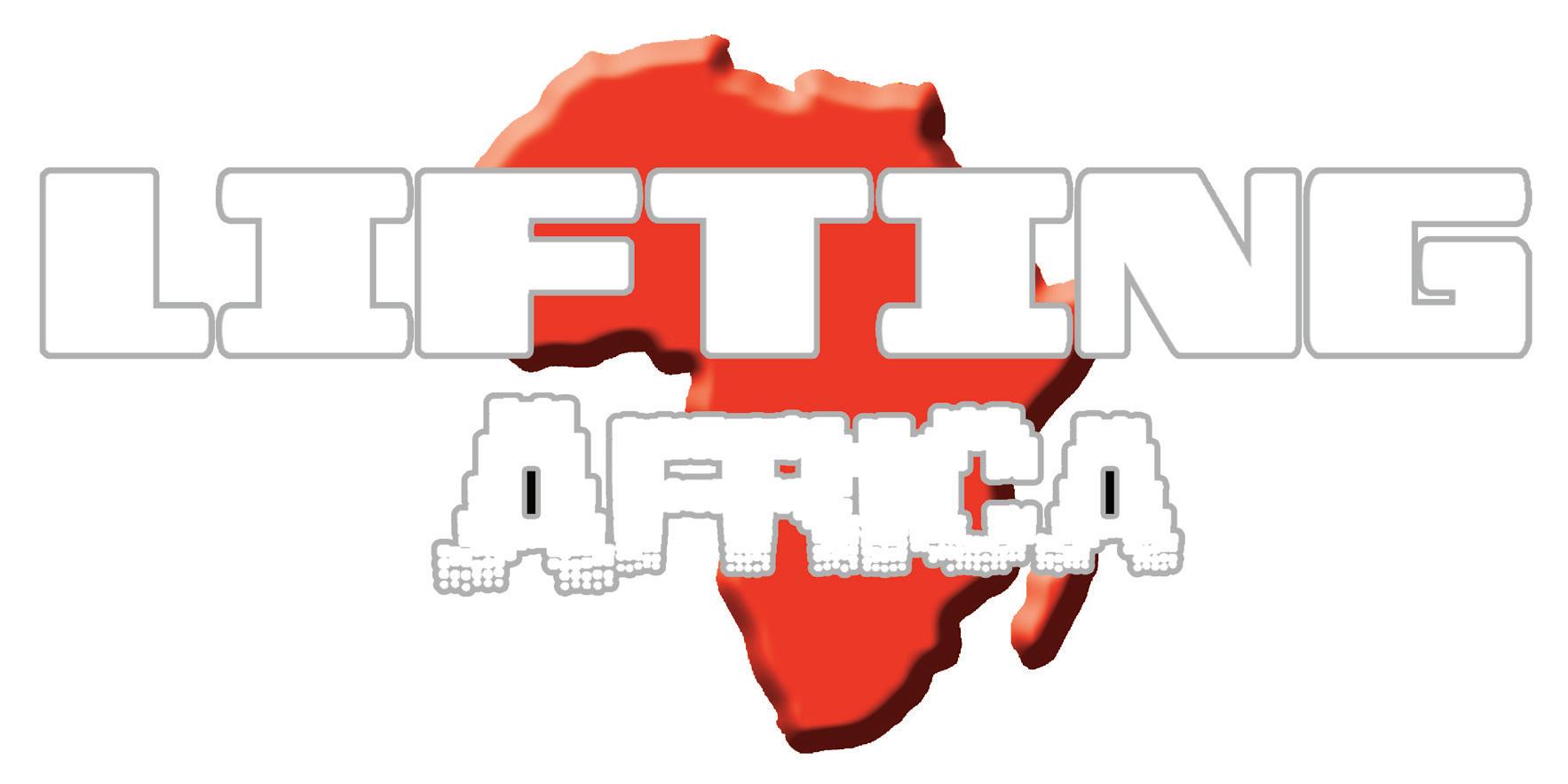
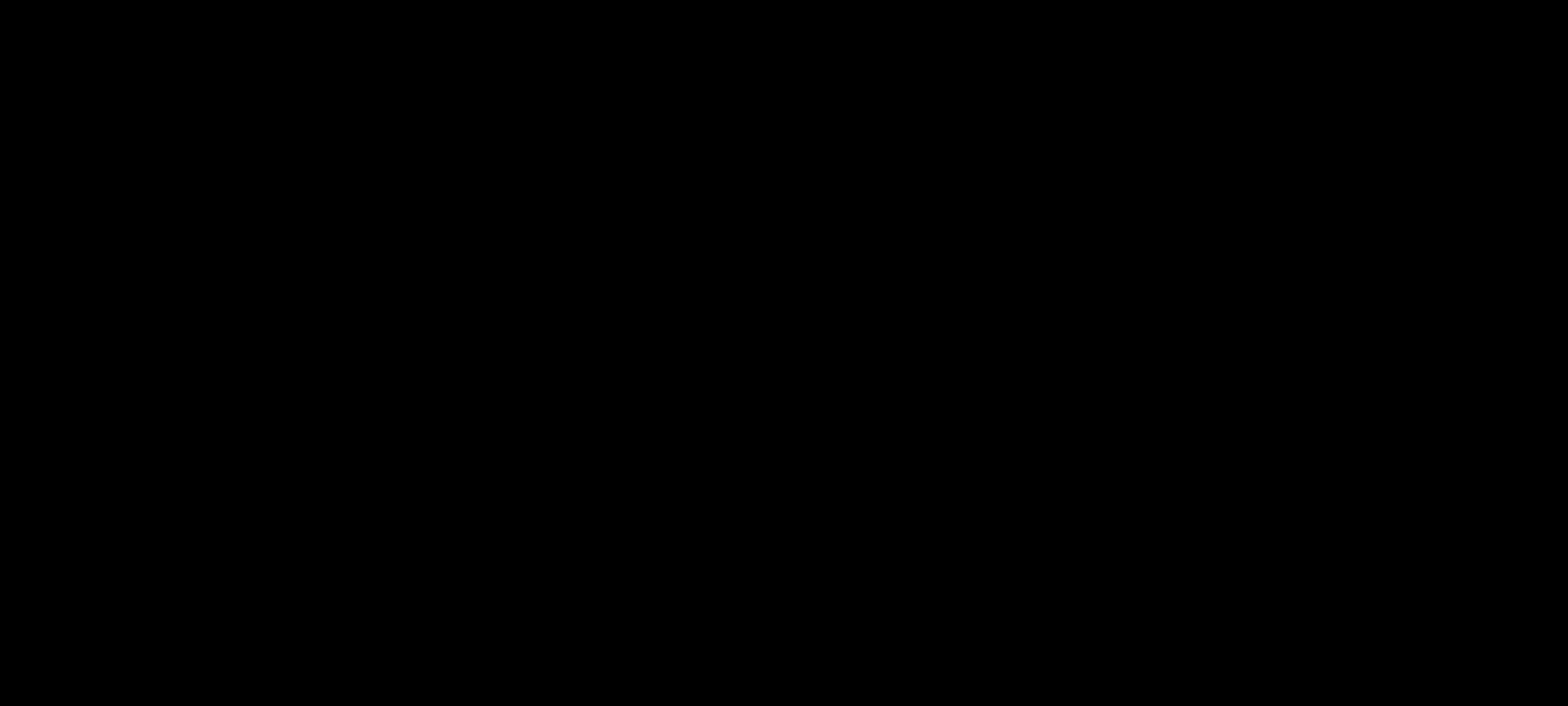
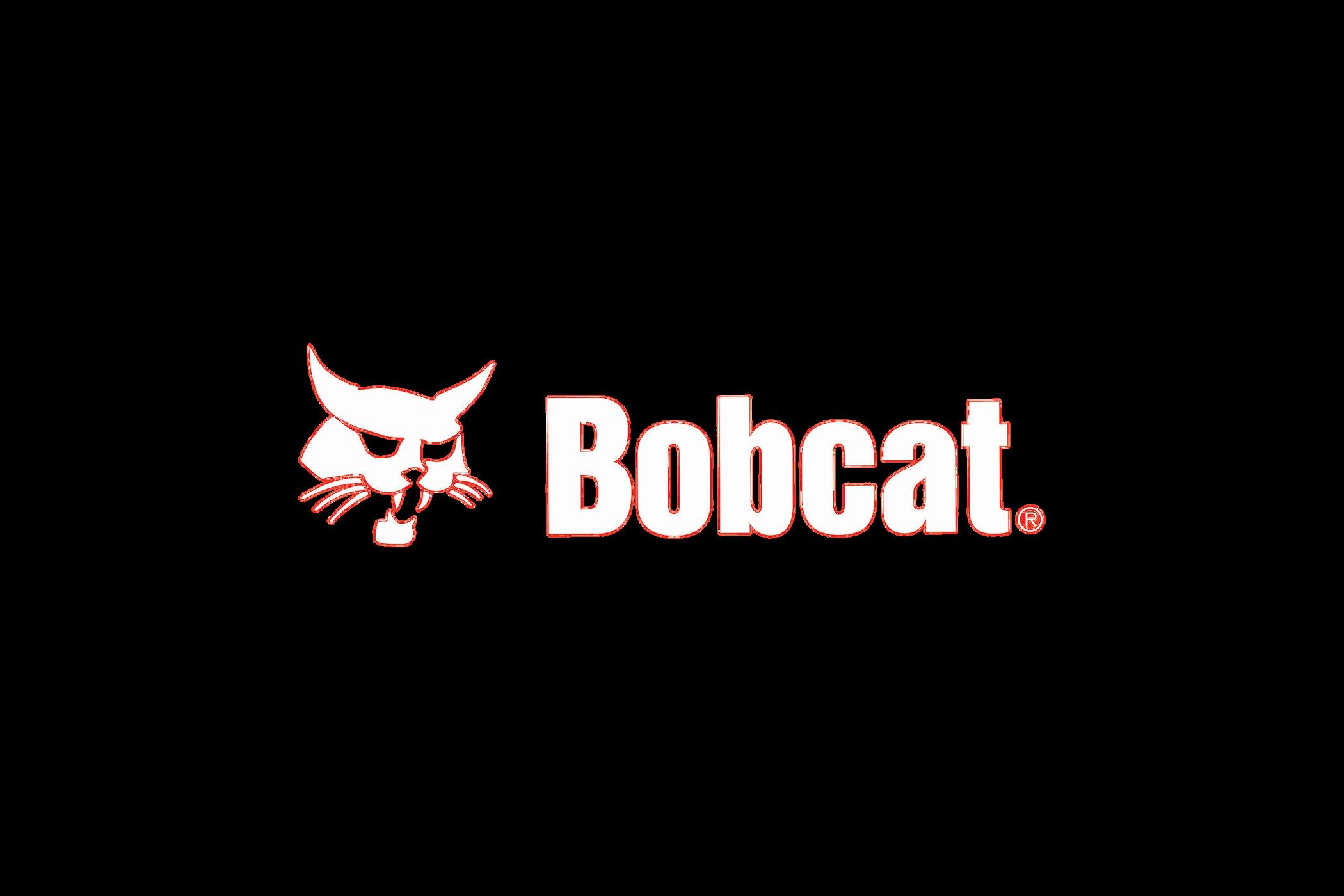

Lifting Africa’s annual Lifting Awards celebrate the outstanding achievements and innovations in the lifting industry, recognising excellence across various categories. These awards aim to highlight the significant contributions of individuals and companies that have set new benchmarks in safety, sustainability, innovation and technical expertise. By acknowledging these exemplary efforts, the Lifting Awards inspire continued growth and development within the industry, fostering a culture of excellence and advancement.
Apprentice / Technician of the Year Award
Excellence in Engineering
Excellence in People Development
Environment Award
Industry Leader Award
Innovation in Service Award
Innovation Award (Manufacturer Product
Innovation of the Year)
Project of the Year
Rising Star Award
Safety and Training Award
Services to the Lifting Industry / Lifetime
Achievement Award
www.liftingawards.co.za
More than a year since the company expanded its material handling portfolio, the Bobcat brand, part of Doosan Bobcat, has firmly established itself in the forklift and warehouse solutions market, not just in Africa, but
all around the world.
Bobcat’s expanded line-up includes all models previously manufactured under the Doosan Industrial Vehicle name, comprising the following product lines:
• Diesel forklift trucks | lift capacities of 2 to 25 tonne
• Liquified petroleum gas (LPG) forklift trucks | lift capacities of 1.5 to 7 tonne
• Electric forklift trucks | lift capacities of 1.5 to 10 tonne
• Warehouse solutions | pallet trucks, reach trucks and stackers
With the resulting incorporation of more than 200 forklifts and warehouse solutions into its product range, Bobcat is committed to becoming a leading player in the global material handling market, mirroring the unparalleled reputation it has developed in the international compact equipment segment.
The addition of the material handling equipment has built on the existing compact loaders and telehandlers from Bobcat, which can be equipped with attachments such as buckets, grabs, bale clamps, dump hoppers and pallet forks, so they can be used in many industries for material handling and logistics work.
Electric Forklift Trucks
With the increased focus on lower emissions and reduced noise levels, the Bobcat range of electric forklift trucks has become increasingly important for both indoor and outdoor applications.
The B20X-7 Plus is part of the electric forklift range. Introduced in 2021, this model is known for its reliability and efficiency in material handling operations. With a nominal load capacity of 2 tonne and equipped with standard tyres, the B20X-7 Plus delivers smooth operation. It is designed with a focus on ergonomics and operator comfort, with the compact turning radius of 1.9 m allowing for excellent manoeuvrability in tight spaces.
The larger B80NS is a model in one of the most recent introductions in the Bobcat range - the NXE series of electric forklift trucks with 4-wheel drive.
This series consists of forklift trucks with a capacity of 6 to 10 tonne, which are suitable for heavy applications in container transport, machine construction and industry.
These zero-emission machines can work an entire day
on a battery charge and are of course very suitable for work in factories and warehouses. Like the smaller electric models, these machines offer excellent visibility and a lot of comfort and features as standard that make operation easier.
Hydrogen Forklifts
Bobcat has recently been showcasing its hydrogen fuel cell-powered forklift prototypes. While these are still in the development phase, the company is exploring hydrogen for use across its forklift range.
Hydrogen fuel cell forklifts offer longer operating times and faster refuelling, making them ideal for applications that require extended use and quick refuelling turnaround.
For warehouses operating multiple shifts, the hydrogen fuel cell forklift is a viable option to reduce carbon footprint while still meeting the operational needs to run longer hours with no charging required.
Doosan Bobcat is the first company to commercialize hydrogen forklifts in South Korea and through the Bobcat brand is now embarking on an effort to expand the reach of hydrogen mobility.
As proof of this, the first Bobcat hydrogen forklift was delivered in August 2024 to Korea Zinc’s Onsan refinery, which received special case clearance in Korea for forklift hydrogen refuelling stations.
In November, Doosan Bobcat announced that it had signed a tripartite Memorandum of Understanding (MOU) with Gwangyang City and Korea Logis Pool (KLP) to collaborate on the ‘Gwangyang Hydrogen City Project’ and expand the supply of hydrogen forklifts.
South Korea’s Ministry of Land, Infrastructure and Transport selected Gwangyang City last year as a Hydrogen City.
The Hydrogen City Project plan for Gwangyang encompasses a hydrogen forklift supply initiative, and through this MOU, Gwangyang City, Doosan Bobcat, and KLP will collaborate on the initiative.
Bobcat, https://www.bobcat.com/mea/en/industry/materialhandling
It’s hard to believe we’re wrapping up 2024 – what a year it has been! The lifting and materials handling industry has faced challenges, from rising operational costs driven by inflation, crime, natural disasters and economic slowdowns to navigating pre-election uncertainties. Add to this the more specific industry issues, such as an ageing workforce, the shortage of registered LMIs and the constant need to stay abreast of evolving regulations. Yet, this resilient sector has proven its dynamism through it all, standing firm as a vital contributor to the country’s economy.
Our cover story spotlights Bobcat, exploring its innovative solutions and contributions to the lifting sector. Bobcat’s commitment to excellence continues to redefine expectations, making it a key player in the industry.
This issue also features highlights from the annual LEEASA Conference, co-hosted by Lifting Africa at Electra Mining Africa earlier this year. The conference underscored the importance of collaboration and innovation in our industry, from thought-provoking discussions to the latest advancements in lifting equipment and standards.
We are also excited to announce that entries for the Lifting Awards are officially open! The inaugural awards ceremony will take place in August 2025, celebrating excellence and innovation across all sectors of the lifting industry. With these awards, we aim to highlight the contributions of individuals and companies that have set new benchmarks for safety, sustainability, innovation and technical expertise in our industry. We encourage you to participate. More information on entering the awards is available at www.liftingawards.co.za
As businesses wind down for the year, we extend our heartfelt wishes to you and your loved ones for a well-deserved break and a joyful festive season. May this time be filled with rest, celebration and quality moments with those who matter most.
As we look ahead to 2025, we encourage everyone to travel safely, return recharged and ready to embrace the new year's opportunities.
feeling rejuvenated and ready for a bumper year ahead. As we enter the New Year, LEEASA has been hard at work planning and developing our service offering, gearing up to give you the best support you may need to achieve your goals.
Regarding the proposed General Manager position, we have reached a shortlist of applicants and feel confident that we will be able to confirm the successful applicant within the next month. This is an important position, responsible for the day-to-day functions of the Association, developing new initiatives and designed to provide the best possible support and communications for our members.
The unique sheave gauge sets that were developed by LEEASA are at last freely available and proving to be popular. This very practical tool enables one to quickly and easily measure sheave groove diameter, which has a significant impact on wire rope service life. These sets cover the full range of rope diameters from 8mm to 58mm. If you wish to purchase a set, please contact Des on admin@leeasa.co.za for details
During this year we will be developing additional inspection tools to assist members to provide efficient and accurate measurement and assessment. Details will be provided shortly. LEEASA has appointed a consultant to assist with the improvement and development of our website during the first quarter of 2025. This will have important features such as easy online purchases. We will advise you as these features become available.
In the last quarter, LEEASA provided training to some of the Department of Employment and Labour Inspectorate. They have a very wide scope of work to cover and our role has been to provide them with the knowledge and information relating to lifting equipment, concerning best practices, audits, documentation of LME’s and LMI’s, conformance with standards and lifting safety in general. We intend to provide this training for DEL inspectors in other areas over the next few months.
We continue to be active on various SABS technical committee
We are committed to giving members better access to, and communication with, LEEASA by rolling out roadshows, meetings and seminars in all provinces during 2025. Our aim is to give all members access to LEEASA services and training, no matter which province they may reside in.
LEEASA has embarked on a concept to produce useful training information in the form of short videos, probably available to members through social media such as Facebook or LinkedIn. Watch this space!
We are engaging with ECSA to address a range of important aspects of the lifting industry, aiming to improve understanding and enhancing safety and efficiency.
Should you have any suggestions or proposals concerning LEEASA or the lifting industry in general please feel free to reach out to any of the board members
We will finalise the LEEASA calendar of events for 2025 to be rolled out by end of February 2025.
Well, the Chairman’s table is pretty full, with an exciting year ahead. May this be a positive and safe year ahead for you, enjoying lifting with LEEASA partnership and support.
Chairman: Kyle Graham: kyle@leeasa.co.za
Vice Chair: Ashley Davis: ashley@leeasa.co.za
Ordinary Members:
Francois Weideman: francoisw@leeasa.co.za
Roger Day: roger@leeasa.co.za
Katiso Mogaki: katiso@leeasa.co.za
Carlos Marques: carlos@leeasa.co.za
Administration: Desiré Davis: admin@leeasa.co.za
Marketing and Design: Xané Roestroff: production@leeasa.co.za
Feel free to reach out to the council members if the need requires.
Yours in SAFE LIFTING, Roger Day and the rest of the LEEASA team.
Mr. Aaldrik Graham Kiewiet
Mr. Akeal Ramraj
Mr. Alan Victor Botha
Mr. Albert Anthony Freeme
Mr. Albert Olof Jansen Van Vuuren
Mr. Alfa Janes Grouws
Mr. Amogelang Gilbert Mmusi
Mr. Amos Tulela
Mr. Ananias Zhou
Mr. Andre Coetzee
Mr. Andre van der Merwe
Mr. Andrew John Ferguson
Mr. Andries Aucamp
Mr. Andries Gordon
Mr. Andries Josias Agenbag
Mr. Antoni Frederik Janse van Niewenhuizen
Mr. Armand du Plessis
Mr. Arnoul Spitsbaard
Mr. Arnoux de Bruin
Mr. Ashley Mark Davis
Mr. Barend Andreas Lubbe
Mr. Bartholomeus Jakobus
Erasmus
Mr. Bless Msweli
Mr. Braam Bezuidenhout
Mr. Brian George Mezieres
Mr. Brian Leonard Meintjies
Mr. Carel Gustavus Potgieter
Mr. Carel Hendrik Ferreira
Mr. Carlos Macuacua
Mr. Challe Andre Bonhamme
Mr. Charl van Heerden Strauss
Mr. Charles Casgoigne
Mr. Chris Lotheringen
Mr. Christiaan Charles Supra
Mr. Christiaan Ernst Gerhard Schutte
Mr. Christiaan Hendrik Van Wyk
Mr. Christo Pieter Barnard
Mr. Christo Van Eyk
Mr. Christo van Huyssteen
Mr. Clifford Mubvuta
Mr. Coenraad Hendrik Heunis
Mr. Collin Kubayi
Mr. Cornelis Henry Cyrus Spamers
Mr. Cyril Raymond Laredo
Mr. Damien Oscar Stephen
Mr. Daniel Ntatenyane Mangwegape
Mr. Darrin Ian Cass
Mr. David Dos Santos Cruz
Mr. David Henry Cooks
Mr. David-Lee Alan Dewelzim
Mr. Dean Edwin White
Mr. Dean Eppel
Mr. Deon Bonthuyzen
Mr. Desmond Errol Lloyd
Mr. Dewald Schutte
Mr. Diederik Arnoldus Dahms
Mr. Dirk Johannes Christoffel
Geldenhuys
Mr. Divan van Zyl
Mr. Donavon Hugh Spamers
Mr. Drean Johannes Kotze
Mr. Dwayne Partridge
Mr. Edius Topera Mashamba
Mr. Edward Kruger
Mr. Edward Nachiwe
Mr. Emile de Koning
Mr. Enock Mugwede
Mr. Ernest Khanyile
Mr. Ernst Cornelius Jansen JNR
Mr. Ernst Cornelius Jansen SNR
Mr. Ettiene Pollard
Mr. Eugene Terence Redelinghuys
Mr. Evans Farai Chabata
Mr. Ferdinand Pieterse
Mr. Francois Dewald Blignaut
Mr. Francois Frederikus Le Grange
Mr. Francois Weideman
Mr. Frank Warrick Saayman
Mr. Frederek Gerhardus Opperman
Mr. Frederick Johannes Jacobus Fourie
Mr. Frederik Wilhelm Stonehouse
Mr. Freedom Nsele
Mr. Funganayi Makhuza
Mr. Garth Vincent Barnes
Mr. Gavin Rayson
Mr. George Cornelius Krafft
Mr. George Khehla Kuhlase
Mr. Gerhardus Jacobus Oosthuizen
Mr. Gert Vos
Mr. Given Nyathi
Mr. Glenton William Rebello
Mr. Happy Tafara Tati
Mr. Harris Naidoo
Mr. Hendrick Rapule Mahuma
Mr. Hendrik de Jong
Mr. Hendrik de Kock
Mr. Henry Oswald Kerr
Mr. Hermanus Barend Dahms
Mr. Ian O’Hara
Mr. Ibrahimo Brento Hassane
Mr. Imraan Moolla
Mr. Irvin Charles Murrish
Mr. Isaac Thupaakgosi Leshotho
Mr. Isidro Ernesto Fernando
Mr. Israel Mooketsi
Mr. Jacobus (Jacques) Mare
Mr. Jacobus Rudolph Kruger
Mr. Jacques Jonker
Mr. Jaen Pienaar
Mr. James Nicholas Hamilton Wells
Mr. Jan Frederick van Niekerk
Mr. Jan Louis Venter
Mr. Janus Jacobus Van Biljon
Mr. Jason Brett Mulder
Mr. Jason James Whitehead
Mr. Johannes Jurgens Marais
Mr. Johannes Mnyameni
Mr. Johannes Roos
Mr. John Carsten Allers
Mr. Joseph Johannes van Huyssteen
Mr. Joseph Mabaso
Mr. Justin Henry Brown
Mr. Karel Johannes Francois Du Toit
Mr. Kebareng Daniel Molausi
Mr. Keith van Vreden
Mr. Kesekang Segole
Mr. Kevin Clive Reckas
Mr. Kevin Keith Godfrey
Mr. Khathutshelo John Phalandwa
Mr. Kobus Van Tonder
Mr. Kyle Graham
Mr. Kyle Streak
Mr. Lake Johane Ndhlela
Mr. Leon Johan Snyders
Mr. Lesiba Willie Sebothoma
Mr. Linton Moodley
Mr. Lodewickus Robert van de Venter
Mr. Louwrens Daniel Basson
Mr. Lukas Petrus Beukes
Mr. Makalele Selwyn Makofane
Mr. Malcolm Ivan Claase
Mr. Malose Kenneth Mabela
Mr. Marius Marais
Mr. Marius van der Merwe
Mr. Mark James Totman
Mr. Mark Leonard Munnery
Mr. Mark Leslie O’Connor
Mr. Mark Warren Minott
Mr. Marthinus Swart
Mr. Matthys Daniel Taljaard
Mr. Matthys Michiel Brink
Mr. Mboshoa Simon Skosana
Mr. Michael Fernandes De Souza
Mr. Michael Henry Hassett
Mr. Michael John Hendry
Mr. Michael Lionel Roberts
Mr. Michael Richard Slabbert
Mr. Michael Varty
Mr. Milton Mhlanga
Mr. Mogakolodi Gregory Thamage
Mr. Mohamed Hoosen Dawood
Mr. Moses Karukwayo
Mr. Mzinhle Leonard Sibenya
Mr. Napo Michael Noosi
Mr. Nathaniel Happy Sambo
Mr. Neil Naude
Mr. Nelson Chaita Moyane
Mr. Nicolaas Benjamin Smit
Mr. Nicolaas Theunissen Wynant
Mr. Nkosinathi Richard Mavimbela
Mr. Phata Simon Mailula
Mr. Philippus Stefanus Kruger
Mr. Phillip Demetrius Kemp
Mr. Phiwayinkosi Manazi Biyela
Mr. Pieter Albert Schoeman
Mr. Ralph Errol Shamrock
Mr. Randy Mmoto Makeke
Mr. Raphael Letsema Shobane
Mr. Reino Schutte
Mr. Rishi Mungroo
Mr. Robert Du Toit
Mr. Robert Wayne Milne
Mr. Jeen-Pierre Groenewald
Mr. Jetro Mzwandile Ngwenya
Mr. Joannes Lugt
Mr. Joao Carlos de Freitas Marques
Mr. Johan Frederick Herselman
Mr. Johan Smith
Mr. Johann du Plessis
Mr. Johannes (Jaco) van Biljon
Mr. Johannes Gideon Kruger
Mr. Johannes Hendrik Snyder
Mr. Nkosini Owen Ngcobo
Mr. Noel Nyamukoho
Mr. Norman David Graham
Mr. Octovias Lebakang Mabelane
Mr. Pastor Noosi
Mr. Paul Pillay
Mr. Paulo Jorge de Freitas Marques
Mr. Peter Abraham du Toit
Mr. Petr Kluson
Mr. Petrus Abraham Bester
Mr. Petrus Lafras Fritz
Mr. Rodney Bassingthwaighte
Mr. Roger Ian Day
Mr. Roland Henry Murray
Mr. Ronald John Laing
Mr. Royden Stewart Turner
Mr. Rudzani Collins Masiagwala
Mr. Russel Henning Boshoff
Mr. Rutendo Job Sadomba
Mr. Ryno Coetzer
Mr. Sarel Petrus Jacobus Dreyer
Mr. Schalk Willem Johannes Burger
Mr. Sello Jacob Sebiloane
Mr. Seth Laredo
Mr. Shadrack Mikel Dlamini
Mr. Shimane Martin Diutlwileng
Mr. Siegfried Schrader
Mr. Sifiso Ngwenya
Mr. Simphiwe Mosito
Mr. Sizwesihle Blessing Ntombela
Mr. Stefan Ivanov Babatchev
Mr. Stephen Andrew McGregor
Mr. Steven Duvenage
Mr. Stuart Mark Love
Mr. Stuart Swart
Mr. Thokazani Bright Mkhize
Mr. Thulani Ndlovu
Mr. Timothy Tatenda Zindi
Mr. Trevor Sefoka
Mr. Tshidiso Isaac Masobeng
Mr. Tshisamphiri Moses Mukoma
Mr. Victor Manuel Batista Ferreira
Mr. Victor Sithole
Mr. Victor Thedor Sargent
Mr. Vincent Smanga Sithole
Mr. Vishay Ramkaran
Mr. Warren Naude
Mr. Wayne Garnett Shaw
Mr. Weddington Chimbane Moyo
Mr. Werner De Bruyn
Mr. Werner Hermann Schroer
Mr. Werner Snyman
Mr. Wesley Horak
Mr. Willem Abram (Bossie) Prinsloo
Mr. Willem Petrus van den Heever
Mr. William Charles Palvie
Mr. William Henry Pepler
Mr. William Peter Park
Mr. Wynand Byleveldt
Mr. Yogandren (Donny) Soobramoney
Mr. Zaheer Shameer Khan
Mr. Zenzele Siphamandla Ntshakala
Mrs. Ruwaida Mahomed
Mrs. Sandile Wyeth Mzimela
Mrs. Surita Marx
Ms. Lynda Lake
“These records are up to date at the time of going to print”
Scania, renowned for its premium trucks, is enhancing it’s presence in Southern Africa with a new state-of-the-art facility in Aeroton. To support their high production requirements, Scania South Africa has placed an order with RGM Cranes for a range of overhead cranes to be installed by mid January 2025.
Scania’s decision to invest in this new facility stems from their significant growth in the region.
Christian Håkansson, head of production at Scania South Africa explains, “Scania is doing exceptionally well in South Africa.”
“Our production volume has increased significantly over the past 7-8 years, and we have outgrown our current plant. This new facility is necessary to meet the increasing demand.”
RGM Cranes, a trusted partner of Scania South Africa, was chosen for this critical project due to their proven track record and expertise in the motor industry.
“We have an existing relationship with RGM Cranes in that they have consistently supported us with servicing our cranes, load testing and lifting tackle inspection. Their ability to deliver quality brands and meet tight deadlines made them the ideal choice for this project,” adds Cornelius Viljoen, Workshop Manager at Scania.
Several factors contributed to Scania selecting RGM Cranes as
their supplier.
“We have a strong relationship with RGM Cranes and have had very productive discussions about development,” says Håkansson. “We did explore the market and received quotes from several companies. Ultimately, we believed that RGM Cranes could meet our tight timeline and deliver the quality we need.”
Viljoen elaborates, “During a site visit to RGM Cranes’ facility, we were highly impressed by their operational structure, extensive stockholding, and technical expertise. The RGM Cranes team have been involved from the planning stages, providing invaluable input and guidance. Their organised approach, availability of spare parts, and deep knowledge stood out compared to other suppliers.”
The new order from Scania South Africa includes a variety of cranes designed to handle heavy-duty lifting requirements essential for assembling bus and truck chassis.
The order comprises eight 125 kg
jib cranes with Planeta Pitch hoist units, four 1.2-ton single girder cranes, one 1.6-ton single girder crane, two 3.2-ton single girder cranes, and four 5-ton single girder cranes.
The cranes will feature top-of-therange equipment from Planeta and Güralp, ensuring they meet the high European quality standards that Scania demands.
“Scania is known for its premium truck offering, and we require premium equipment to support our production,” states Viljoen.
“While there are cheaper options available, we need the reliability and quality that RGM Cranes and their equipment provide.”
One of the standout features of the new cranes is the Guralp hoist units, which come with a crane monitoring system.
This advanced system offers realtime feedback on crane operations, enabling Scania to maintain optimal performance and safety standards. The monitoring unit tracks various
parameters such as motion, load limits, and operational hours, allowing for precise maintenance scheduling and reducing the risk of downtime.
RGM Cranes will also install the necessary DSL system to power these advanced cranes, ensuring seamless integration into Scania’s production processes. “The cranes are a necessity for our operations,” Viljoen emphasizes. “They facilitate the assembly of our trucks and buses, handling engines, axles, and even entire chassis.”
Scania’s new and improved facility in Aeroton, is set to become their operational hub for southern Africa, and beyond, and represents a significant investment in the region’s industrial capabilities.
With the support of RGM Cranes, Scania is poised to enhance its production efficiency and meet the growing demand for its premium vehicles. As this project progresses, the partnership between Scania South Africa and RGM Cranes continues to exemplify the synergy
between premium products and reliable support, driving both companies towards a prosperous future in the southern African market.
RGM Cranes, +27 (0) 11 422 3690, info@rgm.co.za, www.rgmcranes.co.za
BB Cranes is to manufacture its first 30-metre-span overhead crane, a record for this Cape Town-based company and the direct result of improved manufacturing capabilities and a recently expanded factory floor.
The wide-span double-girder electric overhead travelling crane is one of six ordered by boatbuilders Robertson and Caine, the largest manufacturer of catamarans in the Southern Hemisphere and the third largest globally. BB’s 30 metre span, 5-ton capacity crane is for the factory in Montague Gardens, Cape Town.
Robertson and Caine has also ordered two single-girder and two double-girder BB machines, all with 5-ton capacity. They will span 20 metres (two cranes), 19 metres and 18 metres. The sixth crane on order is a 10-ton double-girder machine with a span of 20 metres.
BB will assemble all six from standard components, and fit them with twinned short-headroom Condra hoists – two per crane. There will be variable-speed drives on the long- and cross-travels for precise boat positioning.
Asked to comment, a BB Cranes spokesman explained that three of the six cranes would be manufactured simultaneously with two other wide-span machines ordered by Rovic, an independent agricultural machinery manufacturer that commissioned
three double-girder overhead cranes in the first half of 2024, two of them designed with 28-metre spans just two metres shy of BB’s new 30-metre record.
“Our crane spans are usually anything between 18 and 25 metres, so we see the 28-metrespan machines for Rovic – and especially the 30-metre span crane for Robertson and Caine – as justifying our decision to expand BB’s capabilities and increase our factory floor space,” the spokesman said.
BB has steadily upgraded its capabilities and procedures at Rivergate Industrial Park since 2022, when BB Cranes became a member of the Condra group.
In June 2024, the company increased its factory floor area by 400 square metres.
“All of these cranes represent turnkey deliveries from design through to installation. For us, they are affirmation of BB’s decision to grow,” said the spokesman.
Robertson and Caine has been BB Cranes’ customer for twenty years. Current work for the boatbuilders includes partial on-site automation
of a 16-ton crane used in repetitive applications, control of which will be reduced to the single push of one button to accelerate production and improve productivity.
The BB Cranes spokesman explained that the number of enquiries for automated cranes was increasing.
“We offer automation across our product range, working in collaboration with Condra’s design office,” he said.
“Condra is accumulating automation experience, and is currently automating a crane for use in wrap-and-protect operations in Gauteng. We hope to see more automated cranes among our customers here in Cape Town,” said the spokesman.
Currently equipped with eight BB cranes, Robertson and Caine’s new order will bring its total of BB machines to fourteen. All six of the new cranes will be delivered during November and December 2024.
Condra, +27 (0) 11 776 6000, sales@condra.co.za, www.condra.co.za
Hands-on training sessions that incorporate theoretical and practical lessons. Put your new skills into practice using real equipment, under the guidance of our expert trainersOrganised at a location of your choice.
E-learning + live virtual training + practical training session (optional). The package includes: an individual e-learning session, a live scheduled virtual classroom session with a trainer and an optional practical training session.
Short, interactive, 1.5-hour online sessions that focus on specific topics. Easy to follow from anywhere.
Progress
evolves with the times and new lessons gained from experience. Liebherr has developed its flagship mobile harbour crane over five decades of changing industry demands, standards, and trends.
Upgrades over the years have ultimately served to accommodate larger and heavier cargoes, while maintaining high standards in performance and reliability. This has included updates to the crane’s tower and boom, to modifications in its undercarriage. In recent years, all-electric cranes optimised for energy efficiency and sustainability have come to the forefront. And the newest LHM series focuses on advanced electronics and sensor technology for future automation.
Rostock (Germany), October 2024 – Half a century of innovation. The global market for mobile harbour cranes has seen Liebherr rise to prominence, thanks to the consistent satisfaction of customers who rely on the brand’s dependable equipment and comprehensive service network that extends even to the most remote locations. This trust has been built over years of delivering exceptional performance in the mobile harbour crane segment, making Liebherr
a preferred choice across diverse regions and product configurations.
A legacy of excellence
The legacy and evolution of the Liebherr mobile harbour crane couldn’t be more illustrative than with the LGM 1130 introduced in 1974. Mobile harbour cranes in those times were often used as backup for STS container cranes, positioned under the container crane itself.
This was made possible through a foldingtower design that allowed the LGM to fold its boom, drive underneath the container crane, and erect itself again to then support the STS. The LGM was introduced during a period when containerisation was becoming increasingly dominant, and global trade routes were expanding.
Mobile harbour cranes are renowned for their flexibility and versatility, and this trait was reinforced over time.
Capable of handling various applications such as bulk handling, container handling, and heavy goods transport, these cranes needed to offer more efficiency compared to other port equipment.
The rubber-tired undercarriage provides excellent load distribution, eliminating the need for extensive quay preparation and allowing for easy transition to new projects or ports.
With the introduction of the LHM 250 in 1996, new benchmarks for efficiency and innovation were set. This crane featured an X-shaped undercarriage and individually steerable wheelsets, allowing for improved manoeuvrability in increasingly narrow port environments. The LHM 250 was also the first Liebherr mobile harbour crane to incorporate telemetry, enabling remote monitoring and data transmission. This innovation was crucial as the industry demanded greater efficiency and larger cranes to handle the growing size and capacity of container ships.
“Over the years, Liebherr has continuously adapted to market demands, introducing groundbreaking models that have had an impact on port operations,” says Sebastian Simon, product manager at Liebherr Rostock. “Our commitment to innovation and quality has made us a trusted partner in the maritime industry.”
The LHM 500, launched in 2002, continued this legacy with its robust design and increased focus on environmental sustainability. The crane’s tubular tower and 4-chord boom were designed to enhance steelwork reliability, extending the crane’s lifecycle and reducing its environmental impact. In 2010, innovation saw a shift towards the integration of digital technologies and automation in port operations, with the LHM 550 incorporating advanced telemetry and other features.
Enhancing technical capabilities is just one aspect of improving logistical operations. Maximising limited space is another, and portal crane solutions excel in this area. Liebherr’s LPS cranes have been pivotal in port operations for decades. Their rail-mounted configurations and space-saving portal undercarriage, combined with versatile mobile harbour crane
technology, ensure efficient cargo handling in tight locations. The LPS series, including models like the LPS 420 E, epitomises innovation and practicality, handling containers, bulk goods, and heavy lifts up to 308 tonnes with the LPS 800.
Assistance systems help optimise logistics – SmartGrip, Sycratronic, Pactronic
The assistance systems that launched soon after the LHM 550 came to market helped evolve the logistical capabilities of mobile harbour cranes. SmartGrip, launched in 2014, is an intelligent system that optimises grab filling rates through self-learning. It offers higher performance and nearly eliminates overloads.
Analyses showed that only 70% of the grab’s capacity was typically used due to factors like suboptimal angles and varying material densities. SmartGrip adjusts automatically, recognising bulk density, compression, granularity, and conditions like depth of impression and grab type. It optimises filling to maximum capacity within seven cycles, ensuring the rate exceeds 70% from the second cycle.
The need to handle larger and heavier cargo led to a modification in mobile harbour crane performance. To accommodate heavy-lift project cargo, particularly from the wind industry, two LHMs must work together. Sycratronic
was developed and released in 2004 to maximise performance and turnover by improving the safety and efficiency of tandem operations. It connects two cranes via a Controller Area Network (CAN bus), allowing their Programmable Logic Controller to communicate and synchronise movements. This enables the leading crane to provide input on slewing angle, hoisting height, and load weight to the following crane, which then adjusts automatically. With advanced algorithms and safety systems, Sycratronic allows full utilisation of the cranes’ load capacity, overcoming the typical 75% restriction in tandem lifts. It also enhances safety by monitoring and correcting shifts in the load’s centre of gravity, and eliminates communication errors between crane operators, reducing the risk of accidents.
Hybrid technology is playing a crucial role in modernising port logistics by making operations more efficient and environmentally friendly. Liebherr’s Pactronic system, released in 2010, is a great example of this innovation for mobile harbour cranes. This system uses a special energy storage device that combines gas and hydraulic fluid to store and release energy when needed. This clever setup boosts hoisting speeds without requiring a bigger diesel engine, which means less pollution and better performance.
The Pactronic system is also known for its quick charging, long lifespan, and recyclability, making it a smart and sustainable choice for the future of port logistics. It has a significantly higher energy capacity than conventionally used electrical energy storage devices, such as high-performance capacitors.
Going all-electric for more sustainable port logistics
One of the standout developments in port logistics over the past decade is the increasing demand for a more sustainable infrastructure.
In 2019, the LPS 420 E marked a significant milestone as Liebherr’s first all-electric portal crane. It features permanently excited synchronous motors, significantly reducing energy consumption, especially during idling times. All crane movements – like luffing, hoisting, slewing, and travelling –were done by electric motors, no hydraulics required.
The LPS 420 E was designed for high-efficiency bulk and container operations, reflecting the industry’s increasing focus on reducing CO2 footprints. But it was not the first innovation for electric drives. For more than a quarter century now, Liebherr mobile harbour cranes do not emit any CO2 during operation when their electric prime movers are in operation, according to the Scope 1 GHG protocol, and provided that the port has the corresponding infrastructure for it.
The new LHM series, released in 2022, represents the future of
crane technology with its advanced automation capabilities. This crane is prepared for supervised work cycle automation, preparing ports for the future of datadriven logistics and renewable infrastructure.
As the maritime industry continues to evolve, Liebherr remains committed to leading the way in innovation and sustainability. The company’s focus on data-driven logistics and helping to build out a more renewable port logistics infrastructure through its product innovations ensures that its cranes are prepared for the future.
Liebherr’s vision for the future includes more data-driven logistics, which will improve the operations of maritime crane fleets through mastery over data access and optimization. The company also anticipates a significant growth in renewable infrastructure at ports,
aiming to reduce local emissions and source more renewable energy. Liebherr’s mobile harbour cranes are already prepared for these trends, characterized by low noise, high precision, high speed, and reduced operational expenses.
The extensive sales and service network of Liebherr guarantees that customers receive the support they need, wherever they are in the world. This commitment to innovation and customer satisfaction drives everything Liebherr does, ensuring that its mobile harbour cranes continue to set the standard for the industry.
“The goals for the next half-century are clear: continuous technical enhancements of the cranes, swift adaptation to new developments, and maintaining the agility of a family-owned business with short decision-making pathways,” remarks Andreas Ritschel, General Manager Sales for mobile harbour cranes at Liebherr-MCCtec Rostock GmbH. With a legacy of excellence and a vision for the future, Liebherr’s mobile harbour cranes will continue to set the standard for the industry. That’s why Ritschel adds: “Reliability remains a cornerstone, both in the products and the service expansion. With a steadfast presence for 75 years and 50 years of experience and innovation in mobile harbour cranes, Liebherr is poised to remain an industry leader for the next 50 years.”
Liebherr Africa, +27 (0) 11 365 2000, info.laf@liebherr.com, www.liebherr.com
Polish heavy lift contractor, MS INDUSTRY, has used an Enerpac SBL1100 hydraulic gantry for the installation of transformers at the Baltic Power substation, part of the Baltic Power Offshore Wind development. The gantry allowed precise positioning of the transformers on their respective installation tracks.
The Baltic Power wind farm, located about 23 km offshore Poland, will have a generating capacity of up to 1.2 GW when completed in 2026. Energy generated by the turbines will be transported via export cables to an onshore substation currently under construction.
MS INDUSTRY has delivered and installed two transformers, each weighing 354t, at the Baltic Power substation site. The 13.5m long transformers, measuring 5.3m wide and 4.8m high, were transported to the installation site using SPMTs. To unload each transformer,
MS INDUSTRY used its Enerpac SBL1100 gantry. After lifting the transformer clear of the SPMT, it was skidded along the gantry’s 7m skid track to position the transformer’s wheels in line with a pre-laid installation track. Using the gantry’s Intelli-Lift wireless control system, the operator was able to raise and lower the gantry header beam and side shift units to position and gently lower the transformer onto the installation track.
“Space limitations and the unsuitability of using a crane given
the variable ground conditions made the Enerpac SBL1100 gantry the ideal solution,” said Robert Samczyk, CEO, MS INDUSTRY. “The combination of vertical and horizontal movements using the operator’s wireless control system gave us the precision we needed to place the transformer in the installation track.”
Enerpac SBL1100 – Powerful Lifter
The SBL1100 is Enerpac’s highest capacity hydraulic telescopic gantry. Equipped with three stage lifting cylinders, the SBL1100 lifts up to 12m at the top of the third stage and can handle up to 10,484 kN at the top of the first stage.
As standard the SBL1100 features an Intelli-Lift wireless control system allowing unobstructed views of the load. The wireless system ensures automatic synchronisation of lifting with accuracy of 24 mm and automatic synchronisation of travel with accuracy of 15 mm.
Enerpac, +27 (0) 12 940 0656, africa@enerpac.com, www.enerpac.com
Manufacturing and Modification of Cranes
Erection, Servicing & Load Testing of Cranes
Sling Inspection
Designing of Electrical Panels
Factory Maintenance
Supply, Installation of Standard & Specialized
Radio Control Systems
Hiring of Mobile Cranes and Load Test Weights
A Service That Meets The Requirements of Our Clients
Provide Well Managed, Trained and Motivated Personnel
Meeting any Regulatory and Statutory Requirements
Applicable to Our Business
The Development and Maintenance of a QUALITY SYSTEM
Designed to Ensure Continuous Improvement and Meeting
The Requirements of CertX SA ISO 9001 : 2015
HENRY
DONAVON
Konecranes
has introduced the latest addition to its comprehensive line of explosion-proof equipment with the launch of the Konecranes EX C-series electric chain hoist, designed for Zone 1/2/21 hazardous environments.
Available in the EMEA and APAC regions, this hoist offers the latest technology in safety and efficiency for industries where explosive atmospheres are a concern, such as oil refineries, chemical plants, gas facilities and more.
The Konecranes EX C-series for Zone 1/2/21 is the first EX-proof electric chain hoist to feature invertercontrolled trolley positioning, a significant advancement for smooth, precise trolley movement. With lifting capacities up to 2.5 tons and the ability to operate in the most demanding gas and dust environments, the Konecranes EX C-series is engineered to meet both ATEX and IECEx certifications, providing comprehensive protection in potentially explosive atmospheres.
“At Konecranes, safety is always our top priority. While it’s impossible to eliminate all risks in explosive environments, the right equipment and training can significantly enhance both safety and efficiency. Our extensive experience with explosion-proof products has helped us to develop a comprehensive range of cranes and components that meet strict standards, including our latest Konecranes EX C-series hoist for Zone 1/2/21. The first units are already on their way to customers, who appreciate the fast delivery times and the convenience of having a single EX certification for the entire hoist. Each component is designed to meet the high standards required for certification, and the product is fully supported
by our robust service and parts availability,” states Raine Jussila, Sales Support Manager, Hazardous Environment Products.
Key Features of the Konecranes EX C-series for Zone 1/2/21 include:
• Inverter-controlled trolley positioning: This industry-first feature allows for smooth, precise trolley movement, setting a new benchmark in EX-proof equipment.
• Extended continuous operation: With a Cycling Duty Factor of up to 60%, the EX C-series for Zone 1/2/21 offers longer run times, ensuring continuous productivity.
• Comprehensive certification: One EX certification covers the entire hoist, with compliance for both gas and dust hazardous environments (Zones 1, 2, and 21).
• Enhanced safety features: Safe and easy-to-operate two-speed contactor control technology for hoisting and automatic brake engagement in case of power loss.
Designed for diverse industries
The Konecranes EX C-series for Zone 1/2/21 is built for industries that face demanding explosive atmospheres, ensuring safe handling in both gas and dust environments. This includes oil refineries, chemical plants and gas facilities, where flammable substances are commonplace, and precision lifting with minimal ignition risk is crucial.
The hoist also meets the needs of dust-heavy environments such as paper and textile manufacturing, woodworking and grain storage, all of which are prone to combustible
dust accumulation. Additionally, industries like aircraft refueling, LNG plants and gas pipelines can rely on the Konecranes EX C-series for Zone 1/2/21 for operation in volatile zones.
Manufactured in a carbon neutral factory in Finland
The Konecranes EX C-series for Zone 1/2/21 is produced at Konecranes’ Hämeenlinna factory in Finland, which achieved CarbonNeutral® certification in 2023 in accordance with The CarbonNeutral Protocol. By the end of 2023, the factory has reduced its emissions by 72% since 2019 by using renewable energy and systematically improving energy efficiency through activities like process modernizations and transitioning to electric forklifts. The remaining emissions that cannot be fully eliminated yet are offset by purchasing carbon credits delivering finance to a reforestation project that is reducing emissions now. Efforts to further reduce emissions at Hämeenlinna and other Konecranes factories worldwide are continuing.
Konecranes, tanja.wilson@konecranes.com, www.konecranes.com
The 8-axle crane can complete hoisting work in the 700-tonne class or even higher with ease. It therefore has a nominal lifting capacity of 700 tonnes.
In a lifting capacity comparison, the LTM 1650-8.1 exceeds its predecessor’s capacity by between 15 and 50 percent, depending on its equipment package.
BMG’s dedicated Tools & Equipment Lifting and Rigging division provides solutions for lifting and rigging challenges in all industries, including automotive and tyre manufacturing, paper and pulp, sugar, forestry and agriculture, as well as marine and mining.
“BMG’s dedicated Lifting and Rigging team, supplies and supports a broad range of quality branded equipment, that is enhanced by a technical advisory and support service, designed for simplified,
efficient and safe procedures in every application,” explains Tanita Rousel-Brett, Tools & Equipment Lifting and Rigging, BMG. “An important sector of our service is in offshore projects, which demand
specialist solutions for safe and effective lifting and rigging in arduous conditions.
“BMG’s Kito Crosby product portfolio, which is perfectly suited for dependable use in offshore projects includes wide body and bolt type shackles for heavy and critical offshore lifts, cold Tuff Bolt type shackles for lifts conducted in extreme weather conditions and Crosby SP load monitoring solutions. ROV shackles and hooks are manufactured to withstand the toughest conditions and are suitable for use with a variety of remotely operated underwater vehicles.”
BMG is a sub-distributor in Southern Africa of the Kito Crosby brands and product portfolio, which includes Crosby, Gunnebo Industries, Crosby StraightPoint and Crosby IP clamps.
Included in BMG’s extensive range of tools, lifting and rigging equipment are electric, chain and lever hoists, geared and plain crawls, chain, wire and webbing slings and hydraulic, pneumatic hoists and winches, as well as manual Tirfor winches and
ropes. The range also comprises high-pressure hydraulic tools, mechanical ratchet jacks, jib cranes and eye bolts.
BMG complies fully with the requirements of the lifting machine and lifting tackle regulations of the Occupational Health and Safety Act (OHSA) Act 85 of 1993. The company’s Lifting Machinery Inspector (LMI) is certified in terms of the Engineering Profession Act 2000 (Act no46 of 2000) and is a registered member of the Engineering Council of South Africa (ECSA).
BMG has approval from The Department of Labour in terms of the driven machinery regulations 18
(5) of the occupational and safety Act 1993, for examining and testing of lifting machines and lifting tackle.
BMG specialists consider the safe operation of lifting and rigging equipment, as one of the most critical aspects in materials handling and recommends that customers’ equipment is independently load tested annually, or as per urgent requirements and inspected every three months. The company has a fully equipped trailer and is able to offer an onsite load testing service for customer convenience and peace of mind.
BMG – which celebrates 50 years of business this year - offers complete process solutions to all sectors of
industry, which means customers can access essential quality branded engineering components, technical services and support from one wellestablished, reliable supplier.
The company’s specialist divisionsBearings, Seals and Gaskets, Power Transmission, Drives and Motors, Materials Handling, Agriculture, Tools & Fasteners, Hydraulics, Filtration, Lubrication and Field Services – offers an integrated approach to engineering, that guarantees lower production costs and higher efficiencies.
BMG.
+27 (0) 11 620 7467, tanitar@bmgworld.net, www.bmgworld.net
Genie announces an all-new, future-focused design for its core slab scissor lift product line that further improves performance and lowers the total cost of ownership for Next-Generation Genie® GSTM-1932, GS-2632, GS3232, GS-2646, GS-3246, and GS-4046 scissor lifts.
“Genie’s Next-Generation Scissor Lifts are redefining the standard for slab scissor lifts and moving this classic MEWP category into the future,” said Christian Dube, Senior Global Product Manager. “Our priority when redesigning these lifts was to drive lower cost of ownership, improve serviceability, and enhance the user experience — all while delivering the quality that our customers and the industry expect from Genie.”
Enhanced quality and lowest total cost of ownership
The most noticeable change with the next-generation slab scissor lifts is the industry-leading curved linkage design. This departure from industry standard reduces machine weight, allowing Genie to use right-sized components — including batteries, drive motors and other electrical components — which have a lower replacement part cost. Genie benchmarked its new lifts
against competitors’ machines, and our own E-Drive scissors, to ensure industry-leading performance.
Other intentional design changes also improve quality and add to cost savings.
These changes are the result of an extensive analysis at the beginning of Genie’s design process to identify opportunities to eliminate rust, limit the opportunity for damage, and reduce wear and tear. For example:
• It’s common for water to pool at the top of machine chassis, resulting in rust. Genie designed its new chassis to mitigate stagnant water in these areas.
• Extension decks can be damaged or bent during use; Genie added reinforcement steel in targeted locations to reduce damage.
• During loading and unloading, operators occasionally mis-fork the side pockets, causing damage to the chassis and swing out trays. Genie added steel around these side pockets to reduce the chance for
damage to the chassis.
And these are just a few examples.
“On their own, each individual update is an incremental improvement. But, when considered together as a system, and across the product line, the result is a family of machines that add value by reducing costs while improving performance and serviceability,” Dube said.
Modernized design improves serviceability
Throughout the redesign, Genie focused on increasing service parts commonality and consistency of the component layout across the product line.
Overall, there are fewer serviceable components than with previous generations; of the components that remain, at least 70% have commonality across the product line. This simplifies machine fleet management and should increase uptime. Fleet management is further improved by incorporating a consistent parts layout in easy-toaccess locations; a win for service technicians who work on multiple models.
The most common maintenance item when managing a fleet of slab scissor lifts is the batteries, which were an area of focus for Genie. One example of how Genie is delivering on service parts commonality is through an update that uses just two battery part numbers across the entire slab scissor lift product line. Furthermore, in response to customer feedback and regional preferences, the units are available with commonly used high-quality FLA batteries as standard for customers in North America, and standard maintenance-free AGM batteries for customers in other regions around the world. Lithiumion will be available as an option globally. Finally, Genie developed Battery Guard as an option to help protect owners’ investment recognizing that battery theft is a common problem.
Re-imagined for an enhanced user experience
On the jobsite, operators will enjoy
a completely re-designed platform that improves productivity and comfort when working at height. On the popular GS-1932, standard fixed guard rails allow users to drive through most common doors without the need to pause and fold guardrails down. The platform is 20% larger, offering more room for two people to work comfortably indoors. Across the range, operators will notice other subtle details that enhance comfort at height. When talking with customers, one of the common critiques of products available in the market today is the “flex” that occurs when standing on an extension deck. Genie solved this problem by reinforcing the extension deck across the range, giving the extension deck more structure.
The new Smart Link™ platform controller is completely redesigned
to be 30% lighter than the previous version and incorporates a more ergonomic design.
Additionally, because it is modular, parts of the controller can be replaced without requiring replacement of the whole –another example of reducing parts replacement cost. The control system also has been updated to align to a new ISO standard (ISO 21455:2020).
Lastly, in keeping with regional preferences, Genie® Lift Tools™ Spill Guard hydraulic oil containment system will be standard on nextgeneration scissors offered in North America. Spill Guard is an option for the rest of the world.
Goscor Access Solutions, +27 (0 11 393 6437, accesssolutions@goscor.co.za, www.goscoraccesssolutions.co.za
Agriculture is much more than an economic pillar for countries around the world. It is the lifeblood of communities, shaping futures and sustaining livelihoods across nations. It intertwines with the social and economic fabric of societies, offering both sustenance and security for millions.
When agriculture flourishes, so do the people it supports: families are nourished, children grow healthier, and communities thrive. Conversely, when the sector struggles, the impact extends far beyond the fields.
Insights reveal a troubling reality, with South Africa wasting 10 million tonnes of food annually, equivalent to one-third of its total production1. This significant waste exacerbates food insecurity and underscores the urgent need to enhance food availability, sustainability, and efficiency in the agricultural sector, all while being environmentally conscious.
For over 40 years, Toyota Material Handling has been at the forefront of agricultural innovation, committed to transforming the sector by offering cuttingedge equipment solutions from prominent global manufacturers. Claude Pheiffer, Cape Town New Sales Manager for Toyota Material Handling, a division of CFAO Equipment SA, emphasises the importance of leveraging advanced technologies to drive sustainability and operational efficiency in
agriculture. “Technologies such as Toyota Material Handling’s fork vibration dampeners and hydraulic accumulators are crucial in reducing product damage and maintenance costs. These innovations not only help farmers enhance their operational efficiency, but also contribute to more sustainable agricultural practices by minimising food waste and reducing environmental impact,” Pheiffer explains.
Developed by Toyota Industries Corporation (TICO), the fork vibration dampeners function as shock absorbers for forklifts, reducing the impact of bumps and vibrations. This is critical for protecting sensitive agricultural products such as fruit and vegetables. By mitigating the risk of bruising and damage during transport, the fork vibration dampener helps preserve produce quality and reduces financial losses associated with downgraded or wasted goods. The hydraulic accumulator, on the other hand, optimises the hydraulic system’s efficiency by storing and releasing
hydraulic energy as needed, smoothing out hydraulic flow during operation. This reduces strain on the forklift’s hydraulic system, minimises wear and tear and lowers energy consumption.
“This efficient management of hydraulic power not only enhances forklift performance, but also leads to a more reliable, durable machine. Reduced strain on the hydraulic system results in lower energy consumption, decreased maintenance needs and an extended equipment lifespan,” adds Pheiffer. Given the significant environmental impact of food waste, Toyota Material Handling’s technologies are pivotal in supporting sustainability efforts within the agricultural sector. These innovations conserve resources and reduce the environmental footprint of farming operations. Efficient material handling fosters a more sustainable food supply chain, aligning with broader sustainability goals. Moreover, Toyota Material Handling’s advanced technologies boost financial and operational efficiency for farmers, particularly in
fruit farming. By minimising product damage, these solutions help farmers avoid costs and increase revenue through higher-quality produce.
“Toyota Material Handling is at the forefront of supporting South African agriculture with cutting-edge technologies. By utilising advanced technologies such as these, farmers can operate more effectively and economically, allowing them to focus on improving productivity and profitability while supporting their environmental commitments,” concludes Pheiffer.
By reducing waste and boosting efficiency, Toyota Material Handling’s innovations are not just mere equipment solutions, but set a new benchmark in eco-friendly farming, empowering farmers to excel and lead in sustainable practices.
CFAO Equipment SA, +27 (0) 11 571 0200, info@cfaoequipment.co.za, www.cfaoequipment.co.za
The CSIR’s mechanical testing capabilities may be one of the industry’s best-kept secrets. Riaan Bergh, from the CSIR Mining Cluster, recently shared insights at the annual LEEASA conference, showcasing the organisation’s wide-ranging expertise. He urged industry leaders to tap into these advanced testing services, highlighting the potential benefits for operational safety, compliance, and innovation.
The mining sector, one of the most critical drivers of the global economy, relies on a unique set of testing, analysis and training capabilities to maintain safety, compliance and operational efficiency.
At the forefront of these services is the Council for Scientific and Industrial Research (CSIR) Mining Cluster, a division committed to achieving zero harm in mining
operations and ensuring the industry’s compliance with legislative requirements. Through its comprehensive mine testing and training services, the CSIR Mining Cluster plays a pivotal role in enhancing safety standards and operational performance across the sector, according to Bergh.
“The CSIR’s mandate is clear,” he told conference delegates.
“The objectives of the CSIR are
to foster industrial and scientific development through directed, multidisciplinary research and technological innovation, in fields that it deems a priority.
This is done either independently or in collaboration with private or public sector partners, to improve the quality of life for the people of the Republic. The CSIR is also tasked with any other functions assigned to it by or under the Scientific Research Council Act.”
He explained that the CSIR Mining Cluster provides comprehensive mine testing and training services that support zero harm and ensure compliance within the mining industry.
“We strategically support both the industry and the state through unique capabilities, such as annual monitoring and legislated performance acceptance testing for SCSR. We also conduct bi-annual, legislated destructive tensile testing of mine winder ropes, monitor and analyse industrial air pollution, and offer mine fire and explosion suppression testing. Additionally,
we provide competency-based training that incorporates Fourth Industrial Revolution (4IR) technologies to reinforce the industry’s commitment to zero harm.” One of CSIR’s key assets is its Cottesloe Laboratories, which host state-of-the-art facilities such as the Wire Rope Testing Laboratory and the Mechanical Testing Laboratory. These labs are not just centres of excellence in mining-related testing; they represent the capability to conduct extensive, high-precision testing that spans multiple disciplines, from material strength to environmental monitoring, said Bergh.
“We are exceptionally wellequipped to conduct a broad range of critical testing services,” including proof load testing, destructive testing, load comparison testing, force calibration, wire rope and conveyor belt testing, as well as tensile testing of lifting equipment,” said Bergh.
With a force range from 10 kN to 15 MN, the CSIR laboratories are capable of performing proof load tests on large engineering components, lifting gear, and industrial equipment. The CSIR team also carries out both tensile
and compression testing to assess the failure points of materials and structures. Additionally, the cluster performs load comparison testing and force calibration, ensuring that everything from hydraulic jacks to large crane hooks meets operational and safety standards. Their expertise extends to destructive tensile testing of steel wire ropes and conveyor belt splices, guaranteeing the reliability of mining operations and reducing the risk of premature failures.
The CSIR Mining Cluster also tests various lifting equipment, including webbing slings and round slings, to assess their ultimate strength and verify compliance with safety standards. The laboratories at Cottesloe are designed to accommodate large test specimens, with the 100-ton Universal Testing Machine capable of testing samples up to 2.5 meters in length. For more demanding requirements, the 1500-ton tensile testing machine features an 8-meter test bed and 2-meter stroke length, providing the capacity to test heavy-duty equipment such as crane hooks and structural elements. “We test a wide variety of equipment, from large to small crane hooks. To avoid damaging valuable
assets, we typically perform proof load tests. We also conduct load comparison tests on hydraulic jacks and ultimate strength testing on flat webbing slings, endless round slings, and trestles. Additionally, we test trailing cable splices, lever hoists, and a range of other lifting equipment. Whether for certification or product development, our tests help identify failure points, enabling improvements to enhance performance and safety.”
He mentioned that the cluster recently conducted a wire rope failure investigation, where the incident was initially regarded as a premature failure of a 90mm steel hoist rope. The team was tasked with determining whether the failure was due to a fault in the rope itself or another factor. They carefully examined the rope’s condition at the point of failure, as well as its strength both near and far from that point, to understand the cause of the catastrophic failure. “We are able to handle such investigations internally and can carry out these types of assessments quite efficiently,” he added.
“We also conduct three-point bend tests on welded rail joints, belt clamp tensile tests, and rail car tippler lifting gear load testing. Although we carried out the rail car tippler lifting gear test several years ago, it serves as a strong example of the testing capacities we have in our lab. The tippler structure itself weighed 220 tons, and to accommodate this size, we modified our tensile testing machine. We tested the beam elements for buckling, the tensile elements for tensile loading, and the corner elements with loading in various directions. These tests were designed to closely simulate the actual loads the structure would experience during operation, and the test results were validated when the structure successfully passed the lift test.”
CSIR, +27 (0) 12 841 2911, enquiries@csir.co.za, www.csir.co.za
In the bustling world of warehouse management, every minute counts. That’s why savvy warehouse operators rely on a crucial tool in their arsenal; tow motors. But what exactly are tow motors and why are they so beneficial to have in a warehouse environment? Let’s delve into the essentials in this quick two-minute read.
What Are Warehouse Tow Motors?
Warehouse tow motors, also known as tow tractors or tow tugs, are compact yet powerful vehicles designed to tow heavy loads within warehouse facilities. They come in various sizes and configurations to accommodate different load capacities and operational requirements. Equipped with electric or combustion engines, tow motors are versatile workhorses capable of moving everything from pallets and carts, to trailers and other equipment.
Why Are Jungheinrich Tow Motors Beneficial to Have in your Warehouse?
Efficiency Boost: Warehouse tow motors significantly enhance operational efficiency by streamlining material transport. Instead of relying on manual labour or forklifts for every task, tow motors can efficiently tow multiple loads at once, saving time and labour costs.
Versatility: Whether you’re moving pallets of inventory, transporting equipment between
workstations, or replenishing stock in picking areas, tow motors offer unparalleled versatility. Their ability to navigate through tight spaces and congested aisles makes them indispensable for optimizing workflows in warehouses of all sizes.
Space Optimization: Unlike larger equipment, such as forklifts, tow motors have a compact footprint, allowing them to manoeuvre easily in confined spaces. This makes them ideal for warehouses with limited aisle widths or storage configurations, where maximizing spacial utilization is essential.
Safety: Tow motors are designed with safety in mind, featuring advanced braking systems, ergonomic controls, and built-in safety features to protect both operators and pedestrians. By reducing the risk of accidents and injuries, tow motors contribute to a safer working environment for everyone in the warehouse.
Cost-Effectiveness: In addition to their operational benefits, tow motors offer a cost-effective
solution for material handling needs. Compared to larger equipment, tow motors typically have lower upfront costs, require less maintenance and consume less energy, resulting in long-term savings for warehouse operators.
Jungheinrich, +27 (0) 10 596 8460, info@jungheinrich-shop.co.za, www.jungheinrich-shop.co.za
Pre-checks for lifting equipment are essential to ensuring safety and operational efficiency on any job site. These preliminary inspections help identify potential issues before use, reducing the risk of accidents and equipment failure. Richard Oldknow, consultant at Yoke Industrial Corp and member of the LEEA Technical Committee, emphasised the importance of these pre-checks at the LEEASA conference.
In Europe, where inspections occur every 6 to 12 months, a chain sling operating in an arduous environment could go as long as 180 days without being inspected by a LMI. This underscores the critical importance of conducting pre-checks before use.
Addressing delegates at the annual LEEASA conference, Oldknow explained that while pre-checks are mandated by law in Europe, they are often poorly executed or overlooked entirely.
“We even see this issue in the offshore environment and much of it can be attributed to a lack of training on how to perform prechecks. Yes, there is significant industry discussion around it, and it is legislated, but far too many people simply don’t know how to carry them out.”
Acknowledging that he was not fully
up to date with local legislation, Oldknow noted that it seems to rely more on company policy than strict legal requirements. He emphasised that the issue of pre-checking equipment prior to use is becoming a pressing topic in Europe.
“The reality is that if a pre-check is not formally documented and not required by law, there is little chance that it will be consistently performed.”
Using digital effectively
With evolving technology and the increasing use of RFID chips in products, operators now have the capability to access all necessary information about equipment at the point of use. This advancement greatly facilitates pre-checks, said Oldknow. “These pre-checks are mandatory before every lift by the users of the equipment. They are not formal written inspections
conducted by a LMI.
This underscores the critical importance of training equipment users; if an LMI conducts checks every three or six months and rejects the equipment, it raises concerns if that equipment has been in regular use during the preceding months.”
Oldknow emphasised that the primary goal of pre-checks is to ensure safe working equipment by identifying any faults before use. He noted that digitalisation, particularly through blue chips embedded in products, empowers users to conduct these checks more efficiently.
“The chip can store all the procedures for the pre-check, safe user instructions, necessary certifications, and maintenance programmes, as well as the current status of the product,”
he explained. “In Europe, we adhere to Regulation 8 of the Lifting Operations and Lifting Equipment Regulations (LOLER), which mandates these pre-checks. The operator of the equipment serves as the first line of defence in spotting any faults or damage. These checks should be performed before lifting equipment is used each day or at the start of every shift.”
Oldknow outlined several factors to consider during these checks to ensure equipment safety.
These include assessing operational lifting safety, working under suspended loads, ensuring visibility, properly attaching and securing loads, evaluating the environment and location, managing overturning risks, identifying proximity hazards, maintaining the integrity of the equipment, and conducting thorough pre-use inspections.
More training required He said to enhance pre-use checks, it was necessary to significantly increase training requirements, as people simply haven’t adequately been taught how to perform them.
“Digitally supported pre-use checks can revolutionise this process by integrating specific questions and recommendations from suppliers. Users can simply scan their phone over the product and it will provide
CSIR
answers based on pre-set questions aligned with EU standards, while also allowing for customisation by individual companies.”
This approach, said Oldknow, not only streamlines the pre-use check but also makes it far more traceable and legible, with unambiguous markings on the components.
The ability to retrofit these digital chips incurs minimal additional costs, while the value and power they deliver far outweigh any expenses.
Each check can be tied to a specific date and time, enhancing accountability.
For example, with a shackle, the digital chip can be programmed to ask structured questions tailored to the user’s experience level.
For less experienced operators, questions might include identifying missing ID, checking for illegible Working Load Limits (WLL), pinhole elongation, missing or incorrect pins, and any damage wear exceeding 10%.
Conversely, for more experienced inspectors, the check could be simplified to a straightforward query: “Is it safe to use?”
This adaptability ensures that pre-use checks are effective and relevant, catering to the varying experience levels of users. He
LABORATORY: SERVING THE MINING AND LIFTING INDUSTRIES SINCE 1935.
The CSIR is home to a dedicated world-class and specialised facility, housing some of the largest mechanical testing machines in South Africa, coupled with significant expertise and a track record of supporting local industry. The laboratory offers a host of services that promote the safety and health of workers in mining, manufacturing, and construction industries.
Offering to industry
• Laboratory load testing up to 1000 t
• Ultimate strength testing to international standards
• Load comparison testing of jacks and load cells
• Testing of crane hooks, trestles, lifting gear, and tackle
CONTACT US
+27 79 887 2218
mininglabs@csir.co.za
Corner Menton and Frost Avenue Cottesloe, Johannesburg
emphasised the importance of having a clear understanding of what constitutes equipment failure during a pre-check.
This includes defining what types of damage or defects warrant rejection, as well as determining acceptable wear levels and identifying which wear patterns need monitoring.
Effective recording of these checks is crucial. Operators should document when, where and by whom the check was conducted, along with the equipment’s condition, any defects and any notable features—such as photographs.
Currently, pre-use checks often go unrecorded, but this must change; accurate records are the only way to demonstrate compliance with legal requirements, said Oldknow.
“Implementing a streamlined recording process will allow operators to capture evidence easily, ensuring 100% traceability. It is essential to make this system user-friendly, especially for newcomers to the industry, enabling them to conduct prechecks confidently and accurately.”
YOKE Industrial Corp, info@mail.yoke.net, www.yoke.net
LEEA – a membership worth considering
Being a member of the Lifting Equipment Engineers Association (LEEA) brings numerous advantages. Richard Oldknow, consultant at Yoke Industrial Corp and member of the LEEA Technical Committee, highlighted some of these benefits during a presentation at the annual LEEASA conference.
As a globally recognised body committed to upholding the highest standards of safety, quality and professionalism in the lifting equipment industry members of LEEA have long advocated that it offers a competitive edge for their businesses.
According to Oldknow, YOKE has been a full LEEA member for several years, providing them with unrivalled access to the latest technical, legal and safety information essential for thriving in today’s lifting industry.
“While LEEASA sets the standards and tone from a local perspective - and it’s vital to be an active part of your local industry body - it’s equally important to recognise the advantages of association with an international organisation like LEEA and the additional value it delivers.”
Oldknow says LEEA’s vision is to raise global safety standards and foster sustainable practices in lifting. “Their mission centres on educating, influencing and enabling members to ensure best practices become daily routines. This focus is particularly relevant for companies
in high-stakes industries such as oil and gas, where stringent lifting standards are vital,” he says indicating that through continuous technical updates, accessible training resources and strong industry representation, LEEA ensures its members are always aligned with evolving standards.
Understanding the benefits
According to Oldknow, one of the standout benefits of LEEA membership is the opportunity to engage with a global community.
LEEA’s technical and training committees provide a platform for members to share industry knowledge and experience, offering valuable insights that enable YOKE and other members to stay at the forefront of lifting industry standards.
Membership also opens doors to national and international networks, boosting company visibility and credibility.
“For YOKE, having the LEEA badge signals a commitment to quality and safety, with LEEA’s audit process becoming increasingly
rigorous and even adopted by organisations such as the Associated Wire Rope Fabricators (AWRF). This accreditation has helped elevate YOKE’s industry reputation and given clients confidence in their products.”
Another major asset is access to LEEA’s comprehensive training resources, he says. “LEEA membership provides access to a range of training options beyond what many individual companies might offer. This includes accredited training programmes and participation in the Accredited Training Scheme, allowing member companies to deliver industrystandard instruction under LEEA’s guidance. This ensures that one’s training is aligned with the highest standards, with the added benefit of LEEA certificates upon completion of accredited courses.”
Moreover, the LEEA Connect app is a valuable resource, giving operators quick answers to rigging questions, furthering training effectiveness in a practical, accessible way.
Oldknow said LEEA members also
benefit from ongoing technical advice, with resources such as the chatbot, which quickly provides answers to technical queries and industry standards Monthly technical updates from LEEA’s experts also keep companies informed and able to adapt quickly.
“One of the major benefits, however, is how LEEA membership supports company credentials,” said Oldknow.
“There is growing recognitions from end-users on LEEA membership and it is widely seen across industries like construction and oil and gas, as a sure verification of standards and qualifications that meet safety and regulatory standards.”
Opportunity for membership
Oldknow acknowledged that until a few years ago most of LEEA’s membership was British, but said in the past few years this has expanded significantly and the organisation is now truly global with strongholds in regions such as West Africa, Asia and Latin America.
“With around 1 000 members worldwide, LEEA continues to grow, particularly in high-demand areas driven by oil and gas exploration,” he says. Oldknow notes that while membership costs are considerable, they offer substantial value.
To address these costs, LEEASA has partnered with LEEA, a move aimed at enabling more South African companies to join. Moving
to drive membership growth.
Giving delegates at the conference a taster of the various trainingin programmes available and what they can access through membership, he highlighted the various opportunities for local companies ot grow their international footprint thrugh membership. “Being part of LEEA
membership places us at the forefront of industry standards, giving us access to critical resources, ongoing technical updates and a global network of experts committed to best practices. It’s an opportunity to collaborate, learn and contribute to a community that’s constantly pushing for higher standards and
When it comes to safety in the mining industry, attitude plays a critical role. A proactive mindset is essential, whether driven by compliance to avoid penalties or a genuine commitment to the highest standards. Speaking at the annual LEEASA conference Gerhard van Zyl, Group Operations Director at Professional Group of Companies, underscored this point, emphasising that safety was not only about adhering to regulations but also crucial for operational efficiency.
Mining is inherently dangerous, with workers facing hazards such as machinery malfunctions, collapses and environmental risks. Safety is, therefore, integral to success. “In the mining environment, the stakes are high,” says Van Zyl. “Accidents not only jeopardise human lives but also result in significant financial losses, legal repercussions and a damaged reputation.”
According to Van Zyl, safety must be prioritised for several reasons.
“First, protecting human lives is crucial in this high-risk industry, where effective safety protocols significantly reduce the risk of injury and fatalities. Second, safety is directly linked to operational efficiency, as accidents can disrupt operations, leading to costly downtime. A safe environment ensures smoother, more productive processes.”
Moreover, he says, a strong safety culture boosts employee morale
and retention, fostering trust and confidence among the workforce. Compliance with regulatory standards is equally important, helping mining companies avoid penalties and maintain seamless operations.
Safety in racking and forklift operations
In line with this, safety in racking and forklift operations plays a crucial role in ensuring efficiency and security. In a mining warehouse, where space utilisation is key, Van Zyl emphasises the importance of optimising vertical storage in racking systems. By maximising every inch of space, operations can remain safe and productive, further enhancing overall operational efficiency. However, mining operations pose unique challenges, he says. “Effective racking systems in mining environments must handle the weight and size of stored materials. Ensuring that weight is evenly distributed across levels is essential to avoid overloading, which could
lead to structural failure.”
Regular racking inspections are also crucial. Van Zyl notes that certain materials, like salt, can quickly corrode racking if not properly managed, leading to catastrophic failures. Furthermore, warehouses must optimise the flow of goods, ensuring that fast-moving items are easily accessible. Poor workflow can lead to inefficiencies and accidents.
He says implementing safety measures and maintaining equipment can be costly, but the long-term savings from avoiding accidents and downtime make it a worthwhile investment once the option is available. Another crucial factor in reducing accidents is the continuous training of forklift drivers and material handling equipment.
Advanced solutions for racking and forklift safety
According to Van Zyl, modern mining operations are adopting innovative technologies to enhance safety and efficiency. From advanced racking systems to cutting-edge forklift technologies, these solutions are transforming the industry and include:
• Automated Storage and Retrieval Systems (ASRS): These systems can significantly improve storage efficiency by automating the placement and retrieval of materials.
• Seismic Racking: Built to withstand earthquakes and other disruptions, these systems reduce the risk of collapse, improving safety.
• Dynamic Racking: Automatically feeds the next pallet for easy access, reducing manual handling.
Cutting-edge forklift technology
This is another way mining companies approach safety and efficiency in their operations.
• Electric and Hybrid Forklifts: The shift towards electric and hybrid models reduces emissions and improves efficiency. Hydrogenpowered forklifts are also entering the market.
• Automated Guided Vehicles (AGVs): These autonomous machines can operate 24/7 without
downtime, enhancing material transport and reducing the risk of human error.
• Telematics and Fleet Management: These systems allow for real-time monitoring of forklift operations, ensuring that maintenance and safety checks are always up-to-date.
According to Van Zyl, the Internet of Things (IoT) is revolutionising how operations are managed. IoT-enabled sensors on forklifts and racking systems monitor real-time data, provide predictive maintenance alerts, and reduce downtime.
“IoT sensors, for example, can detect wear and tear before a major failure occurs, ensuring that equipment is serviced in time, while centralised control systems integrate racking, forklifts, and warehouse management systems into one central hub, allowing for automated adjustments and seamless operations.”
Van Zyl said there were numerous examples of technologies being successfully implemented. One such case was in Utah, where Rio Tinto integrated autonomous forklifts and real-time navigation systems at a copper mine. This reduced manual handling and increased material transport efficiency by 25%, leading to improved productivity and cost savings.
As mining continues to evolve, the focus on safety, efficiency and sustainability will intensify. Van Zyl emphasises that AI, machine learning and digital twin technologies will further enhance predictive analytics and real-time decision-making. Virtual models will allow operators to monitor machinery remotely, reducing the risk to human lives in high-risk environments.
But Van Zyl cautioned against the unchecked adoption of automation. “We must be mindful of the high unemployment rates in Africa. Automation should be implemented with the workforce, ensuring we do what’s best for the business without causing social harm.”
He said that by adopting advanced racking and forklift technologies, safety and operational efficiency in mining could be drastically improved. “Companies like the Professional Group of Companies are leading the way by combining cutting-edge innovations with a proactive attitude towards safety. This approach protects lives and ensures long-term sustainability and profitability in the mining sector.”
Professional Group of Companies, +27 (0) 10 594 5417, info@professional.za.com, www.professionalgroup.co.za
Lifting professionals are acutely aware of the intricate complexities involved in crane operations. As vital as they are to many industries, their proper functioning cannot be taken for granted, and meticulous inspection’s significance cannot be overstated. This was the message from Francois Weideman and Juanre Theron from CrEng at the annual LEEASA conference, where they emphasised the need for thorough and frequent assessments of cranes to mitigate risks that otherwise could lead to catastrophic failures.
Cranes, like all machinery, experience wear and tear over time. These machines are subjected to heavy loads, environmental stresses and operational changes, all of which can contribute to their deterioration. “Major inspections are essential to determine if a crane can continue operating safely without posing health and safety risks. The objective is to identify issues such as equipment fatigue, corrosion or mechanical defects before they become a hazard,” said Theron.
Weideman added that inspections are also a proactive safety measure and a legal requirement. Under South Africa’s Occupational Health and Safety Act of 1993, specifically the Driven Machinery Regulations of 2015, crane operators must adhere to strict safety standards. Various frameworks, such as ISO 9927 and SANS 10375, provide the specifications for crane inspections, ensuring they meet safety and operational standards.
Risk management
“One of the key goals of crane inspections is to identify and quantify risk. Each time a crane is inspected, we examine how effectively risks are managed,” said Theron.
Although not always mandatory, safety devices can drastically reduce the likelihood of accidents, making them a crucial part of risk mitigation. However, Weideman noted that the Swiss cheese model was an excellent analogy for understanding how safety controls work. “Every “slice” of inspection— whether daily, frequent or periodic - adds a layer of protection. The fewer gaps (or holes in the cheese) in these layers, the lower the risk of accidents.”
Weideman and Theron shared the critical importance of understanding the various types of inspections for lifting equipment, each serving a distinct purpose throughout the equipment’s lifecycle.
“Daily inspections are typically performed by the crane operator, who utilises a checklist to ensure that all components are in good working order. This routine check is essential for identifying any visible issues before the crane is put into operation daily,” said Weideman.
In addition to daily inspections, experienced technicians conduct frequent inspections quarterly. These inspections involve a more detailed assessment of the crane’s condition and culminate in written reports documenting any findings or recommendations.
By law, all cranes must undergo a thorough inspection once a year, said Theron. This inspection encompasses a comprehensive evaluation of the crane and includes a load test conducted by an LMI, ensuring that the equipment meets safety and performance standards. Exceptional inspections explains Weideman, are carried out under unusual circumstances,
such as after an overload event, a significant failure or any modifications made to the crane. These inspections are critical for assessing the integrity of the equipment and determining any necessary repairs or adjustments to maintain safety and compliance.
Both Theron and Weideman emphasise that, in addition to the various inspections already outlined, all cranes must undergo a significant inspection that goes beyond routine maintenance checks. These are typically conducted every 10 years for serial hoists, tower cranes, and mobile cranes and every 20 years for overhead travelling cranes and portal bridge cranes. However, these intervals can be shortened depending on various factors such as the crane’s operating environment, an increase in load frequency or when a crane approaches the end of its design life.
“A significant part of a major inspection involves assessing the crane’s duty cycle - the amount of work it performs and the loads it handles. This is crucial in determining whether a general overhaul is necessary,” says Theron. “Engineers must build a load spectrum to estimate crane usage without data loggers. High-usage cranes may require non-destructive testing (NDT) to detect cracks and other damage not visible during routine inspections.”
While the responsibility of testing ultimately rests with the equipment owner, the industry must continue educating asset owners about the importance of ongoing inspection. “As expert engineers and LMIs, we have a responsibility to ensure that all equipment is tested correctly according to regulations and standards,” says Weideman. Numerous issues can arise with lifting equipment. We can better identify and quantify risks through ongoing inspection, ultimately controlling failures and avoiding accidents.” The hazards associated with lifting equipment must be managed through various means, including engineering, administrative or behavioural
controls. “The knowledge and experience you possess regarding the relevant controls for a specific crane directly influences the extent of vulnerabilities present. Just as a piece of cheese has holes, the gaps in understanding and application of safety measures can expose the operation to significant risks. Therefore, continuous education and training are vital to ensure that everyone involved in lifting equipment is equipped to mitigate risks effectively, leading to a safer working environment,” says Weideman.
CrEng, +27 (0) 84 740 7875, admin@creng.co.za, www.creng.co.za
In December 2023, the South African Bureau of Standards (SABS) released the revised SANS 500:2023 standard, which governs the inspection, testing, and certification of chain blocks and lever hoists. These handpowered lifting devices are integral to a wide range of industries, including agriculture, construction, and manufacturing. During the recent LEEASA conference in Johannesburg, Piet Otto of Phakamisa Safety Consultants discussed the key elements of the updated standard and its significant implications for chain blocks and lever hoists.
From the start of his presentation Otto highlighted the importance of adhering to the new regulations, noting that, due to SABS copyright restrictions, the SANS 500 cannot currently be shared on public platforms.
He advised LME and LMIs to ensure they obtain their own copies of the standard for reference and compliance. While SANS 500 has been widely discussed in the industry, it has sparked some controversy among professionals, particularly regarding its applicability to older equipment and the increasing complexity of its inspection requirements. The standard introduces specific checklists for inspecting and examining chain blocks and lever hoists, outlining the necessary steps for ensuring these devices are safe for use. However, the updated rules also underscore the challenges faced by those working with older equipment that may not conform to the new standards, particularly in rural areas or small workshops. Otto said one of the key objectives of SANS 500 is to bring inspections in line with the Driven
Machinery Regulations (DMR) 18, ensuring that all components of the hoists are properly examined, and that overloading is avoided. These measures aim to eliminate the shortcut practices sometimes found in the industry, where some inspections and tests are rushed or conducted improperly due to financial or time constraints. In line with this, the standard stresses that testing should not only meet regulatory requirements but also ensure safety.
Otto said it was important to note that in South Africa, there were no locally manufactured chain blocks and lever hoists. “These devices are primarily imported from the East, and their quality and consistency can vary. Some units come pre-chained and sealed in boxes by the original equipment manufacturer (OEM), while others are supplied unchained, requiring further testing and certification by the distributor or OEM agent. Many of these devices are made in the same factories overseas and share the same gear train, operation and individual parts. This consistency in manufacturing, however, does
not always guarantee adherence to the same standards in every country.” He said the OHS Act DMR 18 defined chain blocks and lever hoists as hand powered lifting devices with the requirements for inspection clearly outlined. “The LMI or the user cannot dictate as to how inspection and testing must be done,” said Otto.
SANS 500:2023 offers a framework for inspecting both new and reconditioned hoists. The legislation requires that lifting machines undergo inspections at regular intervals - either 6-monthly for in-house competent persons or annually by a registered LMI. These intervals are crucial for ensuring that hoists remain safe and operational. The standard defines “competent persons” as those with the necessary knowledge, training, and experience to perform detailed visual inspections, without necessarily being a certified LMI. Testing and inspection
According to Otto, a significant change brought about by SANS 500:2023 is the focus on performance testing. In addition
to visual inspections, hoists must undergo functional tests to confirm proper operation under a load. This test involves lifting a 50 to 100 kg load over a distance of at least 10 links of chain. This ensures that the hoist’s gears engage properly without overloading, providing an additional layer of safety. However, the standard’s insistence on testing hoists to 170% of their rated working load limit (WLL) has raised questions, as many believe that testing to 100% WLL is sufficient. One of the issues highlighted by experts is the practicality of the overload limiter test. According to SANS 500:2023, if the overload limiter does not activate or slip at 170% of the WLL, the hoist should not be failed, as long as it has passed the functional test. This stipulation has been met with some resistance, particularly when considering the variability in the performance of load limiters. These devices are designed to prevent gross overloading and are not always precise in their operation, which can be influenced by factors such as temperature, humidity, and wear.
Despite these concerns, the standard places considerable emphasis on ensuring that overload limiters are not the sole method of load determination. The safety of the hoist should be verified through proper testing and inspection procedures, and the overload limiter should never be relied upon as the primary method of checking the load.
The primary concern voiced by industry professionals is the applicability of the SANS 500:2023 standard to older, noncompliant hoists still in use on farms, in workshops, and in rural areas. Many of these devices were manufactured to different standards and may lack the required identification markings or batch numbers. As a result, the comprehensive checklists in the standard may not be fully applicable in all cases. For instance, some hoists do not have legible chain markings or batch numbers, and this raises questions about how to report these discrepancies.
In these cases, it is recommended that such issues be noted in inspection reports rather than discarding the equipment outright. This allows the continued use of older equipment while ensuring that any issues are documented and addressed.
Otto said while the SANS introduced much-needed clarity to the testing and inspection of chain blocks and lever hoists, it was important for industry to understand the challenges it presented as it would be necessary for to adapt to these updated standards.
“The shift towards more rigorous inspection and testing is a positive step towards improving safety, but industry stakeholders must balance regulatory compliance with the practical realities of maintaining and testing older equipment,” he said.
Phakamisa Safety Consultants, +27 (0) 82 372 4595, potto@icon.co.za, www.phakamisasafety.co.za
T: +27 (0) 64 507 6857
E: admin@leeasa.co.za
W: www.leeasa.co.za
Kempston Controls
T: +27 (0) 140 776 2888
E: holyhead@kempstoncontrols.co.uk
W: www.kempstoncontrols.co.uk
Condra Cranes
T: +27 (0) 11 776 6000
E: sales@condra.co.za
W: www.condra.co.za
Elephant Lifting Equipment
T: +27 (0)12 661 6105
E: info@elephantlifting.co.za
W: www.elephantlifting.co.za
Johnson Crane Hire
T: +27 (0) 11 455 9222
E: PeterY@jch.co.za
W: www.jch.co.za
Liebherr Africa
T: +27 (0) 11 365 2000
E: info.laf@liebherr.com
W: www.liebherr.com
Bell Equipment Southern Africa
T: +27 (0) 11 928 9846
E: susanmy@bell.co.za
W: www.bellequipment.com
Bobcat
W: https://www.bobcat.com/mea/en/ industry/material-handling www.bobcat.com
Goscor Lift Trucks
T: +27 (0) 11 230 2600
E: lifttrucks@goscor.co.za
W: www.goscorlifttrucks.co.za
Jungheinrich
T: +27 (0) 10 596 8460
E: info@jungheinrich.co.za
W: www.jungheinrich.co.za
Yale Lifting Solutions
T: +27 (0) 11 794 2910
F: +27 (0) 11 794 3560
E: crm@yalelift.co.za
W: www.yale.co.za
Yale Lifting Solutions
T: +27 (0) 11 794 2910
F: +27 (0) 11 794 3560
E: crm@yalelift.co.za
W: www.cmco.com
GregBev Enterprise
C: +27 (0) 82 854 5143
C: +27 (0) 72 395 4342
T: +27 (0) 53 285 0842
E: admin@gregbev.co.za
W: www.gregbev.co.za
Kanu Equipment South Africa (Pty) Ltd
T: +27 (0) 11 826 6710
E: fransv@kanuequipment.com
W: www.kanuequipment.com
Kempston Controls
T: +27 (0) 140 776 2888
E: holyhead@kempstoncontrols.co.uk
W: www.kempstoncontrols.co.uk
Morris Material Handling SA
T: +27 (0) 11 748 1000
F: +27 (0) 11 748 1093
E: sales@morris.co.za
W: www.morris.co.za
Elephant Lifting Equipment
T: +27 (0)12 661 6105
E: info@elephantlifting.co.za
W: www.elephantlifting.co.za
H&H Specialized Services
T: +27 (0) 82 446 2899
E: werner@h-hss.co.za
W: www.h-hss.co.za
Kiloton
T: +27 (0) 861 707 707
E: sales@kiloton.co.za
W: www.kiloton.co.za
Elephant Lifting Equipment
T: +27 (0)12 661 6105
E: info@elephantlifting.co.za
W: www.elephantlifting.co.za
Yale Lifting Solutions
T: +27 (0) 11 794 2910
F: +27 (0) 11 794 3560
E: crm@yalelift.co.za
W: www.cmco.com
IY Safety & Inspections
T: +27 (0) 82 773 7019
C: +27 (0) 82 956 3176
E: bianca@iysafetyinspection.co.za
Kiloton
T: +27 (0) 861 707 707
E: sales@kiloton.co.za
W: www.kiloton.co.za
Morris Material Handling SA
T: +27 (0) 11 748 1000
F: +27 (0) 11 748 1093
E: sales@morris.co.za
W: www.morris.co.za
W: www.iysafetyinspection.com LOAD TESTING AND RE-CERTIFICATION
3 60 5 Services
T: +27 (0) 72 207 7443
T: +27 (0) 64 687 7270
E: sales@3605services.co.za
W: www.3605services.co.za
Cranecor Africa
T: +27 (0) 10 446 5790
E: info@cranecor.co.za
W: www.cranecor.co.za
GregBev Enterprise
C: +27 (0) 82 854 5143
C: +27 (0) 72 395 4342
T: +27 (0) 53 285 0842
E: admin@gregbev.co.za
W: www.gregbev.co.za
IY Safety & Inspections
T: +27 (0) 82 773 7019
C: +27 (0) 82 956 3176
E: bianca@iysafetyinspection.co.za
W: www.iysafetyinspection.com
Kiloton
T: +27 (0) 861 707 707
E: sales@kiloton.co.za
W: www.kiloton.co.za
Margisia Lifting Solutions
T: +27 (0) 14 763 1849
C: +27 (0) 83 992 2222
E: info@margisia.co.za
W: www.margisia.co.za
Kempston Controls
T: +27 (0) 140 776 2888
E: holyhead@kempstoncontrols.co.uk
W: www.kempstoncontrols.co.uk
Cranecor Africa
T: +27 (0) 10 446 5790
E: info@cranecor.co.za
W: www.cranecor.co.za
Morris Material Handling SA
T: +27 (0) 11 748 1000
F: +27 (0) 11 748 1093
E: sales@morris.co.za
W: www.morris.co.za
Shosholoza Consulting
T: +27 (0) 14 495 1994
C: +27 (0) 79 391 2990
E: info@shosholoza.africa
W: www.shosholoza.africa
Yale Lifting Solutions
T: +27 (0) 11 794 2910
F: +27 (0) 11 794 3560
E: crm@yalelift.co.za
W: www.cmco.com
H&H Specialized Services
T: +27 (0) 82 446 2899
E: werner@h-hss.co.za
W: www.h-hss.co.za
J Express Crane Services
T: +27 (0) 11 864 8402
M: +27 (0) 83 425 5535
F: +27 (0) 11 864 8408
E: jexpress@telkomsa.net
Kiloton
T: +27 (0) 861 707 707
E: sales@kiloton.co.za
W: www.kiloton.co.za
CSIR
T: +27 (0) 79 887 2218
E: mininglabs@csir.co.za
W: www.csir.co.za/mechanical -and-rope-testing-laboratory
T: +27 (0) 84 506 1209
E: ndt@chimaera.co.za
W: www.chimaera.co.za
By Carpel SRL - Italy
T: + 39 (0) 39 532 0952
F: + 39 (0) 39 532 0825
E: info@bycarpel.it W: www.bycarpel.it
Condra Cranes
T: +27 (0) 11 776 6000
E: sales@condra.co.za
W: www.condra.co.za
FB Cranes
T: +27 (0) 11 902 3271
E: info@fbcranes.co.za
W: www.fbcranes.co.za
HP Cranes Consulting
T: +27 (0) 11 740-9725/28/33
F: +27 (0) 11 740 8416
E: admin1@hpcranes.co.za
W: www.hpcranes.co.za
IY Safety & Inspections
T: +27 (0) 82 773 7019
C: +27 (0) 82 956 3176
E: bianca@iysafetyinspection.co.za
W: www.iysafetyinspection.com
J Express Crane Services
T: +27 (0) 11 864 8402
M: +27 (0) 83 425 5535
F: +27 (0) 11 864 8408
E: jexpress@telkomsa.net
Kempston Controls
T: +27 (0) 140 776 2888
E: holyhead@kempstoncontrols.co.uk W: www.kempstoncontrols.co.uk
KL Cranes and Lifting Equipment
T: +267 397 4853
C: +267 71344438
E: annelieze@klcranesbot.com W: www.klcranesbot.com
Morris Material Handling SA
T: +27 (0) 11 748 1000
F: +27 (0) 11 748 1093
E: sales@morris.co.za
W: www.morris.co.za
V & S Automation/Cranes
T: +27 (0) 10 442 7478
C: +27 (0) 82 787 2343
E: victor@vsautomation.co.za
W: www.vandsautomation-cranes.co.za
RACKING &
ACROW
T: +27 (0) 11 824 1527
E: info@acrow.co.za
W: www.acrow.co.za
Lifting Placements
C: +27 (0) 61 063 1687
E: info@liftingplacements.co.za
W: www.liftingplacements.co.za
Kempston Controls
T: +27 (0) 140 776 2888
E: holyhead@kempstoncontrols.co.uk
W: www.kempstoncontrols.co.uk
Giovenzana International
T: +39 (0)39 5951 1277
E: giovenzana@giovenzana.com
W: www.giovenzana.com
Kiloton
T: +27 (0) 861 707 707
E: sales@kiloton.co.za
W: www.kiloton.co.za
H&H Specialized Services
T: +27 (0) 82 446 2899
E: werner@h-hss.co.za
W: www.h-hss.co.za
Kiloton
T: +27 (0) 861 707 707
E: sales@kiloton.co.za
W: www.kiloton.co.za
CB Lifting
T: +27 (0) 22 719 1437
E: info@cblifting.co.za
W: www.cblifting.co.za
Haggie
T: +27 (0) 11 601 8400
E: distribution@haggie.co.za
W: www.scaw.co.za
Umholi
T: +27 (0) 11 914 2210/11
F: +27 (0) 11 914 2209
E: umholi@umholi.co.za
W: www.umholi.co.za
Combi Lift
T: +27 (0) 11 900 8010
E: victor@solutions-4u.co.za
W: www.combilift.co.za
MH Dawood Plant Services
T: +27 (0) 11 496 1007
F: +27 (0) 11 496 1198
E: info@mhdawood.co.za
W: www.mhdawood.co.za
LMI Academy
T: +27 (0) 11 475 5876
Kanu Equipment South Africa (Pty) Ltd
T: +27 (0) 11 826 6710
E: fransv@kanuequipment.com
W: www.kanuequipment.com
Manitou
T: +27 (0) 10 601 3000
E: info.msa@manitou-group.com
W: www.manitou.com
Liebherr Africa
T: +27 (0) 11 365 2000
E: info.laf@liebherr.com
W: www.liebherr.com
E: info@lmi-academy.co.za
W: www.lmi-academy.co.za
MCLS Training
T: +27 (0) 82 506 5899
T: +27 (0) 73 089 0624
E: sinky@mclstraining.co.za
W: www.mclstraining.co.za
Phakamisa Safety Consultants
T: +27 (0) 11 462 9620/1
F: +27 (0) 11 462 9620
E: potto@icon.co.za
W: www.phakamisasafety.co.za
Crane Clinic
T: +27 (0) 11 902 7379
E: reception@craneclinic.co.za
W: www.craneclinic.co.za
Palfinger Africa
T: +27 (0) 11 608 3670/1/2/3/4
E: sales@palfingerafrica.co.za
W: www.palfinger.co.za
Smith Capital Equipment
T: +27 (0) 11 873 9830
E: mail@smithcapital.co.za
W: www.smithcapital.co.za
Dymot Engineering
T: +27 (0) 11 970 1920
F: +27 (0) 11 970 1979
E: pa@dymot.co.za
W: www.dymot.co.za
With over 35 years in the heavy lifting industry, RGM Cranes excels in manufacturing and supplying overhead cranes and gantries across Africa. Understanding the unique needs of various industries, we design, install, and maintain overhead cranes, gantries, and lifting equipment for optimal safety and efficient productivity. Our crane inspections and testing meet SANS 10375:2018 standards, ensuring top safety measures.
We maintain over R30 million in stockholding, enabling quick turnaround times and efficient service. Additionally, our advanced crane monitoring and crane asset management systems showcase RGM Cranes’ significant leap forward in crane technology. This cloud-based platform provides real-time monitoring and comprehensive asset management capabilities. Users can track crane performance, schedule maintenance, and access critical data remotely. Our advanced crane monitoring system streamlines crane operations and maintenance, guaranteeing peak performance and reliability.