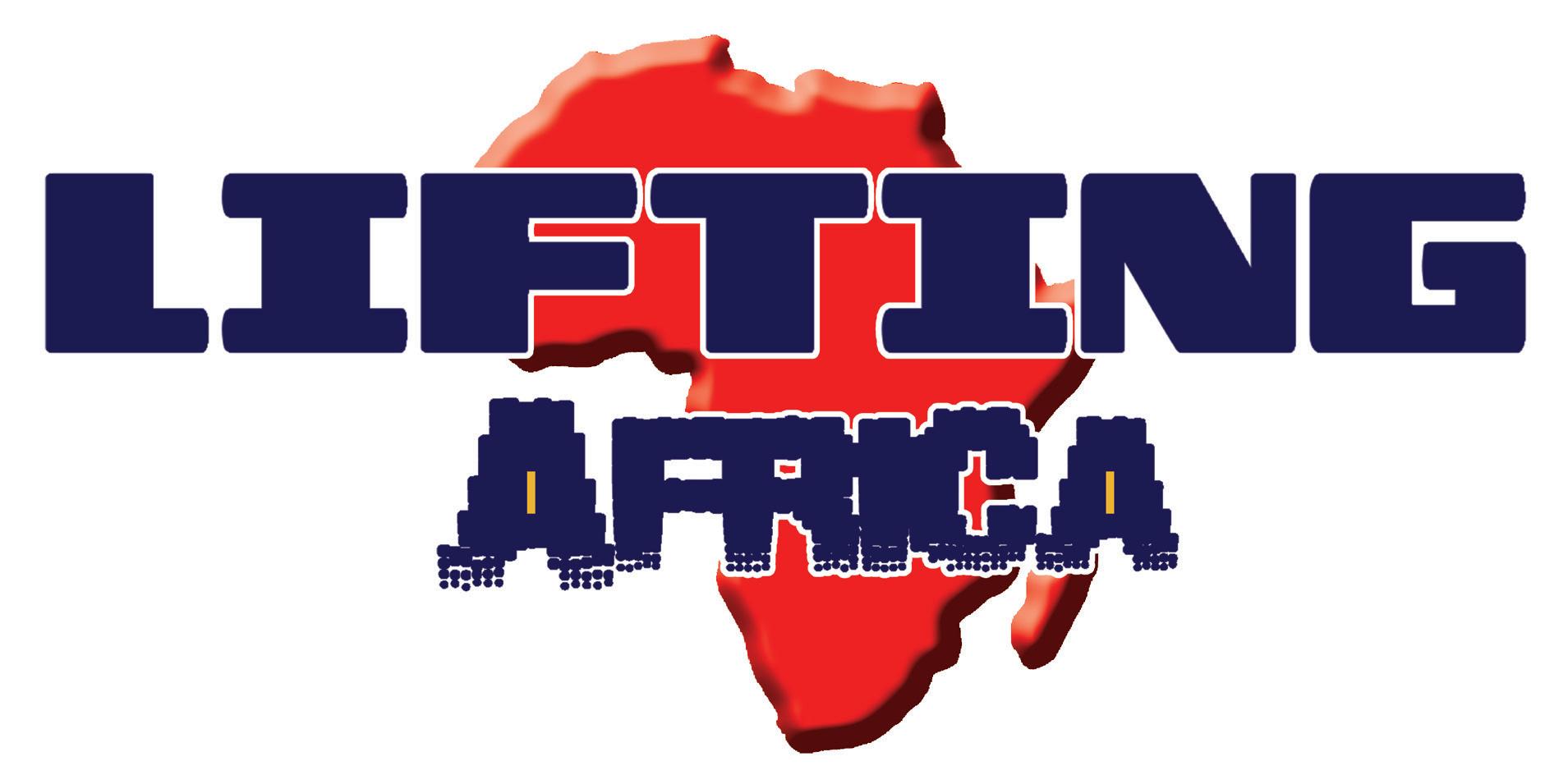



Lifting Africa’s annual Lifting Awards celebrate the outstanding achievements and innovations in the lifting industry, recognising excellence across various categories. These awards aim to highlight the significant contributions of individuals and companies that have set new benchmarks in safety, sustainability, innovation and technical expertise. By acknowledging these exemplary efforts, the Lifting Awards inspire continued growth and development within the industry, fostering a culture of excellence and advancement.
Apprentice / Technician of the Year Award
Excellence in Engineering
Excellence in People Development
Environment Award
Industry Leader Award
Innovation in Service Award
Innovation Award (Manufacturer Product
Innovation of the Year)
Project of the Year
Rising Star Award
Safety and Training Award
Services to the Lifting Industry / Lifetime
Achievement Award
www.liftingawards.co.za
The European machinery industry is undergoing a period of significant transformation as new regulations redefine the landscape and digitalisation picks up speed. Richard Oldknow, consultant at Yoke Industrial Corp and member of the LEEA Technical Committee, highlighted some of the key industry trends and what this means for the local industry during his presentation at the annual LEEASA conference.
With the much-discussed Machinery Directive now formalised into regulation, Europe is focusing on the harmonisation of standards. As global standardisation becomes more critical, this harmonisation is also bringing increased scrutiny, with enforcement bodies across various countries ramping up surveillance to ensure compliance.
“The development and revision of industry standards is a major trend shaping the future of machinery regulations. After nearly 10 to 20 years, new standards are being introduced, and existing ones are undergoing updates. LEEA, which now has representation on the European Standards Board, is actively working on these efforts,” said Oldknow.
Among the key developments is the introduction of the new EN standards, including G100, as well as the revision of older standards like G6 shackles and G8 chains and
components. The G100 standard will be released in two levels, with information being distributed through the European Standards Committee. Meanwhile, the G6 shackle standard, which is 20 years old and currently covers up to 25 tons, is being revised to accommodate greater capacity.
“Another significant update is in the G8 component standard. Until now, there has been no specific standard for hammerlocks or chain connectors. Without a dedicated standard, the industry has had to rely on generic guidelines. However, there is now a strong push for harmonisation across Europe, with a target of having updated or newly written standards in place by 2027 to address outdated or missing regulations.”
Oldknow noted that in discussions with South African colleagues, it became clear that the country faces a significant challenge in transitioning from G8 to G10 standards. While G10 has become the standard in many regions over the past five years, substantial resistance to change persists in South Africa, where reliance on G8 remains prevalent. “The UK has also been slow to adapt, with only 25% of the market currently using G10, and countries like France are similarly lagging.
In contrast, Germany has moved away from G8 completely, while the Scandinavian region is demonstrating an even more dynamic approach to adopting new standards.”
According to Oldknow, the G100 chain and component standards are currently being drafted and will feature two levels: G200C, which is not suitable for use in steel mills, glass factories or high-temperature environments, and X, designed to withstand temperatures up to 400 degrees Celsius. This distinction is crucial, as selecting the appropriate chain for specific conditions can prevent failures. The EN818 standard for G80 chains is under review but has not yet been updated, as it is awaiting the completion of the G100 standards. All new standards are being developed at the European (EN) level, after
which individual countries adopt them, often adding their own acronyms to denote national standards.
The EN13889 standard for G6 shackles has not changed but will be reviewed to include G8 and larger sizes. Similarly, the EN1677 standard for G80 components remains unchanged as it waits for G100 to be finalised. Although G120 is currently not in the planning stages, it remains a long-term consideration for the industry.
“LMIs must be prepared for a wave of new regulations set to be implemented over the next one to four years. Staying informed about these changes is crucial to ensure compliance and maintain safety standards in the industry,” he said.
Embracing digital transformation
One of the most exciting developments, according to Oldknow, has been the introduction of digital chips in products. “Digital technology has taken centre stage at Yoke this year, with the expansion of our RFID product offerings. These chips embed all the product’s key information within it,” explained Oldknow. “The blue chip makes information far more accessible, allowing for faster, easier sharing of critical details.”
amid intensified market surveillance by health and safety officials.
“In South Africa, inspections occur every three and six months, whereas in Europe, they are mandated every six and twelve months. While these inspections are generally conducted effectively, a thorough understanding of the regulations and strict adherence to them is becoming increasingly critical.”
The good news is that these RFID tags can also be retrofitted onto existing products, making the benefits of digitalisation accessible to a wider range of machinery.
“The move to digitliatisation is probably one of the biggest trends we are seeing on a daily basis. It is a critical development to bring in new talent. We must move beyond traditional methods and transfer industry knowledge in ways that resonate with the younger, techsavvy generation. We can no longer be a ‘Cinderella’ industry stuck in the 1950s. As a sector, we need to embrace innovation, with fresh ideas and digital tools driving improved efficiency and operations.”
He said that, similar to South Africa, concerns about an ageing workforce are significant in Europe. “We are witnessing a real loss of experience, and attracting new employees has become a priority. Digitalisation will play a crucial role in this transition.”
How to use digital for pre use chancs and inspection Prioritising compliance
According to Oldknow, another notable trend is the heightened emphasis on compliance, driven by an increasing demand for documentation at the point of use
He said with new industrial sectors emerging, bringing fresh challenges and demands for products, compliance remained central to delivering safe operations.
“Growing industries such as offshore wind energy and wave energy present unique issues, including increased corrosion resistance and the need for enhanced accessibility in harsh environments. It’s essential for us to learn and adapt to these conditions.
“In response to these developments, we are adopting new ways of working, such as leveraging digital solutions and moving away from outdated paper-based systems and hard stamping methods. Traditional hard-stamped shackles can become nearly illegible after just two months, highlighting the urgent need for change. By embracing modern working methods, we can attract new entrants to the industry and ensure we meet the evolving demands of these sectors.”
YOKE Industrial Corp, +27 (0) 64 010 7314, info@mail.yoke.net, www.yoke.net
It’s hard to believe how much has happened in 2024. Here at Lifting Africa, we’ve witnessed countless changes, challenges and exciting opportunities. One of the most significant has been my decision to step down from LEEASA’s Board of Directors. After nine years of dedicated service, I resigned from my role as Director & Treasurer in August. This was not a decision taken lightly. Many have asked why, and while it's a difficult question to answer, I can share that my decision stemmed from differences in the council's direction and concerns regarding specific decision-making processes. Nonetheless, my time with LEEASA has been a treasured experience, and I’m proud of the many initiatives we pursued together to support the industry.
During my tenure, I was deeply committed to LEEASA’s growth and development. It has been a privilege to be part of the association, and I’ll continue to champion its goals from the sidelines. At Lifting Africa, we remain dedicated to serving as the industry’s voice.
And while gently closing one door, I have opened another! I am absolutely thrilled to announce that the Lifting Awards 2025 are officially on! This new celebration of excellence in our industry will feature an inaugural awards ceremony next year, spotlighting achievements, innovation, and safety within lifting. This initiative will recognise the individuals, teams, and companies that are setting new standards and advancing our field. With categories covering operational excellence, environmental responsibility, and individual achievements, we’re creating a platform to honour the skill, hard work, and ingenuity that fuel our industry. Nominations are now open, and we eagerly anticipate revealing the winners at our inaugural ceremony!
Earlier this year, we had the pleasure of exhibiting at Electra Mining, connecting with industry professionals and discussing the latest innovations. We also hosted the Forklift Driver Competition, bringing together skilled operators from across the industry. A heartfelt thank you to all participants for making the event exceptional with their talent and dedication. We are also deeply grateful to our sponsors, whose support made this competition an unforgettable experience. The passion and skill demonstrated by each competitor reinforce the high standards of our industry, and we can’t wait to build on this success in the next competition.
But for now, sit back and enjoy this edition of Lifting Africa, filled with the latest news, insights and innovations across the lifting sector.
LEEASA would like to thank all the Presenters for offering up their time to present at the conference as well as all the delegates that attended, we rely on all of you to make events like this a success.
The conference attracted just under 100 delegates which is back to pre-covid levels and there were some great topics enjoyed by all.
On completion we held a raffle and the first set of LEEASA Sheave Gauges was given away as a prize to a very lucky winner indeed.
These LEEASA Sheave Gauges are now OFFICIALLY available for Sale, and we currently have 18 sets remaining in stock.
A full set comprises of the following
• 37 Pieces (8 – 58 mm DIA)
• Laser Cut Wooden and Perspex Carry Case
• Individually Marked Slots for Easy Identification
• Gauges Can be used to measure
• + 4% Wear
• + 7.5% Wear
• Actual Diameter
Mr. Aaldrik Graham Kiewiet
Mr. Akeal Ramraj
Mr. Alan Victor Botha
Mr. Albert Anthony Freeme
Mr. Albert Olof Jansen Van Vuuren
Mr. Alfa Janes Grouws
Mr. Amogelang Gilbert Mmusi
Mr. Amos Tulela
Mr. Ananias Zhou
Mr. Andre Coetzee
Mr. Andre van der Merwe
Mr. Andrew John Ferguson
Mr. Andries Aucamp
Mr. Andries Gordon
Mr. Andries Josias Agenbag
Price is R 2300.00 per set which includes shipping to your door. Please contact admin@leeasa.co.za to arrange a quotation or invoice to be sent. LEEASA has finalised a one-page procedure on Single Use Lifeline Safety that will be distributed shortly which is the first of many such documents that we are planning on releasing to the industry.
During the last month we have also had a repeat meeting with the DEL, ECSA and COET and are forging forwards with initiatives to relook at ECSA Policy documents that require amending and are ironing out the detail / grey areas within the LMI Candidacy Arena. We currently have two open seats on the LEEASA Board of directors and are inviting nominees to contact us should you wish to be getting involved at this level. Please contact kyle@ leeasa.co.za if you have any questions.
Chairman: Kyle Graham: kyle@leeasa.co.za
Vice Chair: Ashley Davis: ashley@leeasa.co.za
Ordinary Members: Francois Weideman: francoisw@leeasa.co.za
Roger Day: roger@leeasa.co.za
Katiso Mogaki: katiso@leeasa.co.za
Carlos Marques: carlos@leeasa.co.za
Administration: Desiré Davis: admin@leeasa.co.za
Marketing and Design: Xané Roestroff: production@leeasa.co.za
Feel free to reach out to the council members if the need requires.
Yours in SAFE LIFTING, Ashley Davis and the LEEASA team
Mr. Antoni Frederik Janse van Niewenhuizen
Mr. Armand du Plessis
Mr. Arnoul Spitsbaard
Mr. Arnoux de Bruin
Mr. Ashley Mark Davis
Mr. Barend Andreas Lubbe
Mr. Bartholomeus Jakobus
Erasmus
Mr. Bless Msweli
Mr. Braam Bezuidenhout
Mr. Brian George Mezieres
Mr. Brian Leonard Meintjies
Mr. Carel Gustavus Potgieter
Mr. Carel Hendrik Ferreira
Mr. Carlos Macuacua
Mr. Challe Andre Bonhamme
Mr. Charl van Heerden Strauss
Mr. Charles Casgoigne
Mr. Chris Lotheringen
Mr. Christiaan Charles Supra
Mr. Christiaan Ernst Gerhard Schutte
Mr. Christiaan Hendrik Van Wyk
Mr. Christo Pieter Barnard
Mr. Christo Van Eyk
Mr. Christo van Huyssteen
Mr. Clifford Mubvuta
Mr. Coenraad Hendrik Heunis
Mr. Collin Kubayi
Mr. Cornelis Henry Cyrus Spamers
Mr. Cyril Raymond Laredo
Mr. Damien Oscar Stephen
Mr. Daniel Ntatenyane Mangwegape
Mr. Darrin Ian Cass
Mr. David Dos Santos Cruz
Mr. David Henry Cooks
Mr. David-Lee Alan Dewelzim
Mr. Dean Edwin White
Mr. Dean Eppel
Mr. Deon Bonthuyzen
Mr. Desmond Errol Lloyd
Mr. Dewald Schutte
Mr. Diederik Arnoldus Dahms
Mr. Dirk Johannes Christoffel Geldenhuys
Mr. Divan van Zyl
Mr. Donavon Hugh Spamers
Mr. Drean Johannes Kotze
Mr. Dwayne Partridge
Mr. Edius Topera Mashamba
Mr. Edward Kruger
Mr. Edward Nachiwe
Mr. Emile de Koning
Mr. Enock Mugwede
Mr. Ernest Khanyile
Mr. Ernst Cornelius Jansen JNR
Mr. Ernst Cornelius Jansen SNR
Mr. Ettiene Pollard
Mr. Eugene Terence Redelinghuys
Mr. Evans Farai Chabata
Mr. Ferdinand Pieterse
Mr. Francois Dewald Blignaut
Mr. Francois Frederikus Le Grange
Mr. Francois Weideman
Mr. Frank Warrick Saayman
Mr. Frederek Gerhardus Opperman
Mr. Frederick Johannes Jacobus Fourie
Mr. Frederik Wilhelm Stonehouse
Mr. Freedom Nsele
Mr. Funganayi Makhuza
Mr. Garth Vincent Barnes
Mr. Gavin Rayson
Mr. George Cornelius Krafft
Mr. George Khehla Kuhlase
Mr. Gerhardus Jacobus Oosthuizen
Mr. Gert Vos
Mr. Given Nyathi
Mr. Glenton William Rebello
Mr. Happy Tafara Tati
Mr. Harris Naidoo
Mr. Hendrick Rapule Mahuma
Mr. Hendrik de Jong
Mr. Hendrik de Kock
Mr. Henry Oswald Kerr
Mr. Hermanus Barend Dahms
Mr. Ian O’Hara
Mr. Ibrahimo Brento Hassane
Mr. Imraan Moolla
Mr. Irvin Charles Murrish
Mr. Isaac Thupaakgosi Leshotho
Mr. Isidro Ernesto Fernando
Mr. Israel Mooketsi
Mr. Jacobus (Jacques) Mare
Mr. Jacobus Rudolph Kruger
Mr. Jacques Jonker
Mr. Jaen Pienaar
Mr. James Nicholas Hamilton Wells
Mr. Jan Frederick van Niekerk
Mr. Jan Louis Venter
Mr. Janus Jacobus Van Biljon
Mr. Jason Brett Mulder
Mr. Jason James Whitehead
Mr. Johannes Jurgens Marais
Mr. Johannes Mnyameni
Mr. Johannes Roos
Mr. John Carsten Allers
Mr. Joseph Johannes van Huyssteen
Mr. Joseph Mabaso
Mr. Justin Henry Brown
Mr. Karel Johannes Francois Du Toit
Mr. Kebareng Daniel Molausi
Mr. Keith van Vreden
Mr. Kesekang Segole
Mr. Kevin Clive Reckas
Mr. Kevin Keith Godfrey
Mr. Khathutshelo John Phalandwa
Mr. Kobus Van Tonder
Mr. Kyle Graham
Mr. Kyle Streak
Mr. Lake Johane Ndhlela
Mr. Leon Johan Snyders
Mr. Lesiba Willie Sebothoma
Mr. Linton Moodley
Mr. Lodewickus Robert van de Venter
Mr. Louwrens Daniel Basson
Mr. Lukas Petrus Beukes
Mr. Makalele Selwyn Makofane
Mr. Malcolm Ivan Claase
Mr. Malose Kenneth Mabela
Mr. Marius Marais
Mr. Marius van der Merwe
Mr. Mark James Totman
Mr. Mark Leonard Munnery
Mr. Mark Leslie O’Connor
Mr. Mark Warren Minott
Mr. Marthinus Swart
Mr. Matthys Daniel Taljaard
Mr. Matthys Michiel Brink
Mr. Mboshoa Simon Skosana
Mr. Michael Fernandes De Souza
Mr. Michael Henry Hassett
Mr. Michael John Hendry
Mr. Michael Lionel Roberts
Mr. Michael Richard Slabbert
Mr. Michael Varty
Mr. Milton Mhlanga
Mr. Mogakolodi Gregory Thamage
Mr. Mohamed Hoosen Dawood
Mr. Moses Karukwayo
Mr. Mzinhle Leonard Sibenya
Mr. Napo Michael Noosi
Mr. Nathaniel Happy Sambo
Mr. Neil Naude
Mr. Nelson Chaita Moyane
Mr. Nicolaas Benjamin Smit
Mr. Nicolaas Theunissen Wynant
Mr. Nkosinathi Richard Mavimbela
Mr. Phata Simon Mailula
Mr. Philippus Stefanus Kruger
Mr. Phillip Demetrius Kemp
Mr. Phiwayinkosi Manazi Biyela
Mr. Pieter Albert Schoeman
Mr. Ralph Errol Shamrock
Mr. Raphael Letsema Shobane
Mr. Reino Schutte
Mr. Rishi Mungroo
Mr. Robert Du Toit
Mr. Robert Wayne Milne
Mr. Rodney Bassingthwaighte
Mr. Jeen-Pierre Groenewald
Mr. Jetro Mzwandile Ngwenya
Mr. Joannes Lugt
Mr. Joao Carlos de Freitas Marques
Mr. Johan Frederick Herselman
Mr. Johan Smith
Mr. Johann du Plessis
Mr. Johannes (Jaco) van Biljon
Mr. Johannes Gideon Kruger
Mr. Johannes Hendrik Snyder
Mr. Nkosini Owen Ngcobo
Mr. Noel Nyamukoho
Mr. Norman David Graham
Mr. Octovias Lebakang Mabelane
Mr. Pastor Noosi
Mr. Paul Pillay
Mr. Paulo Jorge de Freitas Marques
Mr. Peter Abraham du Toit
Mr. Petr Kluson
Mr. Petrus Abraham Bester
Mr. Petrus Lafras Fritz
Mr. Roger Ian Day
Mr. Roland Henry Murray
Mr. Ronald John Laing
Mr. Royden Stewart Turner
Mr. Rudzani Collins Masiagwala
Mr. Russel Henning Boshoff
Mr. Rutendo Job Sadomba
Mr. Ryno Coetzer
Mr. Sarel Petrus Jacobus Dreyer
Mr. Schalk Willem Johannes Burger
Mr. Sello Jacob Sebiloane
Mr. Seth Laredo
Mr. Shadrack Mikel Dlamini
Mr. Shimane Martin Diutlwileng
Mr. Siegfried Schrader
Mr. Sifiso Ngwenya
Mr. Simphiwe Mosito
Mr. Sizwesihle Blessing Ntombela
Mr. Stefan Ivanov Babatchev
Mr. Stephen Andrew McGregor
Mr. Steven Duvenage
Mr. Stuart Mark Love
Mr. Stuart Swart
Mr. Thokazani Bright Mkhize
Mr. Thulani Ndlovu
Mr. Timothy Tatenda Zindi
Mr. Trevor Sefoka
Mr. Tshidiso Isaac Masobeng
Mr. Tshisamphiri Moses Mukoma
Mr. Victor Manuel Batista Ferreira
Mr. Victor Sithole
Mr. Victor Thedor Sargent
Mr. Vincent Smanga Sithole
Mr. Vishay Ramkaran
Mr. Warren Naude
Mr. Wayne Garnett Shaw
Mr. Weddington Chimbane Moyo
Mr. Werner De Bruyn
Mr. Werner Hermann Schroer
Mr. Werner Snyman
Mr. Wesley Horak
Mr. Willem Abram (Bossie) Prinsloo
Mr. Willem Petrus van den Heever
Mr. William Charles Palvie
Mr. William Henry Pepler
Mr. William Peter Park
Mr. Wynand Byleveldt
Mr. Yogandren (Donny) Soobramoney
Mr. Zaheer Shameer Khan
Mr. Zenzele Siphamandla Ntshakala
Mrs. Ruwaida Mahomed
Mrs. Sandile Wyeth Mzimela
Mrs. Surita Marx
Ms. Lynda Lake
“These records are up to date at the time of going to print”
“Beauty is in the eye of the beholder” - this phrase (and concept) was first penned by Margaret Wolff Hungerford in the late 1870’s. The thought is that beauty is open to individual interpretation. Is competency however open for interpretation?
Are beauty and competency comparable in both being subjective and open to multiple interpretations? Is competency in the eye of the beholder (or instead in the eye of the liable entity) in this case? There is no question that the requirements for competency vary from industry to industry. But is it possible for the prerequisites of competency to vary within a given industry?
In the South African Mine Health and Safety Act 29 of 1996 (MHSA), the following definition of a competent person applies: A ‘competent person’ means a person who-
(a)(i). is qualified by his knowledge,
training, skills, and experience in organising the work and its performance.
(ii). is familiar with the provisions of the Act and the regulations which apply to the work to be performed; and
(iii). has been trained to recognise any potential or actual danger to health or safety in the performance of the work; or
(b) is in possession of the appropriate certificate of competency where such certificate is required by these Regulations; (Chapter1 (4B)).
The South African Occupational Health and Safety Act, 85 of
1993 (OHSA), does not define a competent person; however, the 23 subsequent scheduled regulations provide 11 unique definitions.
All these definitions are essentially “cocktails” made up of the same ingredients (although with different references): technical knowledge, experience, and training.
However, other international publications and research have revealed two additional ingredients often overlooked in the local industry: risk assessment skills and authority.
Here follows a brief overview of each of the attributes mentioned above that constitute a competent person:
• Technical Knowledge: A deep understanding of the specific work or task at hand, including the tools, materials, and processes involved.
• Experience: Practical experience in the field, enabling individuals to apply their knowledge effectively in real-world scenarios.
• Training: Completing formal training programs relevant to the industry and the specific tasks. This might include certification courses, safety training, and continuous education to stay updated on industry standards and regulations. Qualifications are included under this attribute.
• Risk Assessment Skills: The ability to assess and evaluate potential
risks and hazards associated with a particular job or environment.
• Authority: The power to make decisions and enforce safety measures on the job site. This could include stopping work if necessary, implementing safety protocols, and ensuring compliance with safety regulations.
In safety and technical standards worldwide, ‘competent person’ is used as a blanket statement that seems to cover all bases but can cause a false sense of security if not correctly interpreted and applied. As with the OHSA regulations, it is possible for every company or liable entity to have its own “cocktail recipes” or requirements for competence.
Given that the five attributes mentioned above of competency can be demonstrated in several variations by any given candidate, it is often the liable entity’s specific needs and circumstances that determine whether a candidate is competent or not.
When considering competency, the relevant legal entity/appointee should carefully consider which of the five attributes (or cocktail ingredients…) are deemed more relevant within your industry or realm of expertise. The criteria for competence (or a competent person) and how it is enforced can be decisive in any operation.
to consider when appointing a competent person. In conclusion, standards and regulations offer a framework and guideline for what constitutes a “competent person” for a specific role, although it remains the responsibility of the employer or legal appointee to interpret and determine the final criteria for a competent person.
Consider two different companies operating within the same industry. Company A may require a competent person with a diploma and X many years of experience. Company B may require a candidate with a degree and X-3 years of experience. Each of these companies’ respective candidates might be sufficiently competent, but from a third-party point of view, which candidate is more competent?
+27 (0) 64 507 6857, admin@leeasa.co.za,
In the fast-paced and demanding world of the
mining industry, downtime can have severe consequences. Equipment failures, defects, and unexpected maintenance can disrupt operations, leading to significant financial losses and safety risks.
This is where non-destructive testing (NDT) plays a crucial role.
Integrity NDT Projects, a leading NDT services company, offers a comprehensive range of advanced NDT techniques designed to identify defects and potential failures in various materials and components without causing damage.
By proactively detecting issues before they escalate, NDT can help you:
• Prevent catastrophic failures: Identify defects early on, preventing equipment breakdowns and avoiding costly repairs or replacements.
• Reduce downtime: Minimize disruptions to your operations by addressing issues before they lead to unplanned shutdowns.
• Enhance safety: Ensure the integrity of your equipment, protecting your workforce and minimizing the risk of accidents.
• Optimize maintenance: Plan maintenance activities more effectively based on NDT results, reducing unnecessary costs and downtime.
At Electra Mining 2024, Integrity NDT Projects showcased the latest
advancements in NDT technology, including automatic ultrasonic testing. Our experts will be available to discuss your specific needs and demonstrate how our services can benefit your mining operations.
One of our new key offerings is corrosion mapping using advanced ultrasonic technology.
Corrosion and erosion can inflict significant damage upon petrochemical vessels, tanks, and pipework.
By detecting corrosion damage early, you can implement effective maintenance strategies and prolong the lifespan of your assets.
Our corrosion mapping systems provide:
• Accurate assessment of corrosion damage: Identify the extent and location of corrosion in your equipment.
• Condition-based maintenance: Develop maintenance strategies based on the actual condition of your assets.
• Improved RLA and RBI: Enhance your risk life assessment and riskbased inspection processes.
Integrity NDT Projects is a specialist
non-destructive testing company specialising in various types of conventional and advanced NDT methods. We are committed to upholding integrity through honest practices and uncompromising adherence to our principles and values.
As a member of the Two Roads Group, we are part of a network of industrial manufacturing and engineering services companies focused on asset integrity, pressure testing, inspection, and nondestructive testing of pressure equipment, steam generators, pipelines, steel structures, and tanks.
By partnering with Integrity NDT Projects, you can leverage the power of advanced NDT techniques to optimize your operations, reduce downtime, and ensure the safety and reliability of your equipment. Don’t miss this opportunity to learn more about how NDT can save you time and money. Book a preappointment with our team today.
Two Roads South Africa. +27 (0) 11 328 1600, info@2roads.co.za, www.2roads.co.za
Managing director Marc Kleiner says pre-assembled components sold to other manufacturers now account for 12% to 15% of annual revenue. Some 70% of these are sold into South Africa, the rest to export markets.
“We’ve sold end-carriages and other components into England and Spain where the big European crane brands dominate,” Kleiner said, explaining that customers use Condra components to lower input costs and simplify manufacturing processes.
“It saves them the time and trouble of transacting and liaising with many different suppliers, enabling a better focus. We see pre-assembled components as a major growth opportunity despite the high cost of electricity and raw materials here in South Africa,” he said.
Kleiner pointed to Condra’s factory in Bulgaria, which he said is actively pursuing additional opportunities across Europe as it drives component sales into that continent.
He said that there are also opportunities in the Americas. Last month, Condra took an order for a hoist unit from Santiago-based Mantex, a machinery company in Santiago, Chile. Sales through Canadian agents remain steady.
All Condra components are available on short lead times direct from the company’s main factory in Germiston, a 22 000 m2 site with an under-roof area of 8 000 m2. Some 200 different constituent parts are stocked there, ready for assembly into completed components ahead of rigorous testing and despatch.
Local manufacture accounts for about 90 percent of these components, with Condra itself accounting for some 30 percent of the volume. Ropes and electric motors come from Germany, and hook forgings from Spain and Italy.
“We focus on adaptability and robust design,” said Kleiner. “Long production runs keep our prices competitive. Lead times are usually shorter than those of rival firms because of large inventories.”
The majority of Condra’s component sales comprise hoists, end-carriages and cable loop (festoon) systems. There are also crabs, bottom blocks and enclosed conductors. Drives come with single, dual or variable speeds.
Bogies are available with wheel diameters from 125mm to 630mm. Hoists capacities go all the way up to 500 tons.
Component assemblies can be tailored to customer specification. All of them carry a 12-month guarantee.
Condra has a pedigree going back to 1966, when the company was founded as a consultancy and drawing office with general engineering capabilities. Crane manufacture began five years later in 1971.
Today, the company is an acknowledged leader throughout sub-Saharan Africa in robust and enduring overhead and high-lift cranes, portal cranes and jib cranes. There are factories in Johannesburg and Cape Town, with a third facility in Dryanovo, Bulgaria.
Condra (Pty) Ltd, +27 (0) 11 776 6000, sales@condra.co.za, www.condra.co.za
Konecranes launched its flagship Konecranes X-series industrial crane, the successor to its popular CXT model with a new compact design and safe, reliable technology that — thanks to its wireless upgrade capabilities — can adapt to customer needs now and in the future.
“The new flagship crane builds on a quarter-century of success for the CXT, which was launched in 2000 and to date has sold well over 100,000 units globally,” said Jussi Luokomaa, Product Manager, ISE EMEA, Konecranes.
“We expect to see good demand for the Konecranes X-series across multiple industries including general manufacturing, making it a core product for the company for years to come.”
Connectivity for enhanced performance
The Konecranes X-series stands out not only for its lean, state-of-the-art electrical architecture but also for its connectivity.
Designed to be safe, compact and reliable, it can flexibly adjust to future customer requirements, maximizing the investment’s value. This adaptability is enabled by smart, connected components,
allowing seamless software upgrades “over the air”— a first in the standard crane industry.
Customers have the option to initially purchase the crane and easily upgrade to additional Smart Features, enabling seamless incorporation of functionalities as business needs evolve.
Additionally, troubleshooting and software updates can be conveniently conducted from floor level, minimizing potential downtime.
With a focus on user-friendly design, the crane features a new ergonomic CANMAN radio with an integrated display, providing operators with freedom of movement and essential information at their fingertips, while also offering stepless control for safer and more precise lifting experiences. Equipped with TRUCONNECT Remote Monitoring, the Konecranes X-series provides vital insights into crane usage and operation.
This data, combined with maintenance information, empowers businesses to make informed decisions regarding maintenance schedules, safety and productivity enhancements. This innovation in connectivity underscores Konecranes’ commitment to enhancing productivity, reducing downtime, and leading in digital services, reflecting the growing importance of connected equipment in material handling.
To date, Konecranes has 53,600 pieces of connected equipment globally.
A great crane needs a great hoist What further distinguishes the Konecranes X-series crane is the new Konecranes S-series low headroom hoist.
This compact hoist features excellent approach dimensions and smooth stepless lifting with a loaddependent lifting motor, enhancing the user experience and reducing cycle times.
The use of strong, lightweight, durable synthetic rope improves safety and handling compared to steel wire rope.
Commitment to Sustainability
The X-series shows how Konecranes is shaping next generation material handling for a smarter, safer and better world.
Through sustainable design and material choices, such as a more compact and efficient motor and synthetic rope, the X-series drives efficiency improvements.
Features like a thrust rocker reduce steel consumption, and an optimized belt drive reduces wear, minimizing the overall
environmental impact. The optimized design, with synthetic rope and guide rollers, enhances performance and extends equipment lifespan while also reducing maintenance needs.
Additionally, the implementation of inverter lifting technology ensures precise motor speed control, minimizing energy waste.
With the X-series, Konecranes delivers a reliable solution while having an emphasis on sustainability.
The Design for Environment (DfE) approach guided product development, aiming to minimize environmental impact throughout the product lifecycle.
A strong focus on customers and commitment to business growth and continuous improvement make Konecranes a material handling industry leader. This is underpinned by investments in digitalization and technology, plus our work to make material flows more efficient with solutions that decarbonize the economy and advance circularity and safety. Konecranes is now taking orders for the crane and expects the first deliveries to begin in Q4 2024 in Europe, Middle East and Africa, with deliveries in other regions to follow later.
Konecranes, tanja.wilson@konecranes.com, www.konecranes.com
The RL 2600 cranes have been acquired by Dragados Offshore, located in Spain. With a maximum lifting capacity of 35 tonnes and an outreach of 45 metres, the crane is perfectly suited for maintenance and supply operations in the offshore sector.
Its versatility allows it to handle a wide range of tasks, from routine maintenance to supply operations, ensuring that offshore platforms remain productive and wellmaintained. This crane is the most compact one in Liebherr’s offshore portfolio. The well-designed, compact, and weight-optimised crane construction of the RL series ensures optimal utilisation, even in confined spaces. A breath of fresh air from the North Sea with the
offshore allrounder RL 2600 from Liebherr. At Dragados Offshore’s facilities in Puerto Real, Cadiz, a frame agreement has been signed between Liebherr and the engineering, procurement and construction (EPC) contractor. The agreement guarantees the supply of 10 RL 2600 offshore cranes to be used on the platforms that Dragados Offshore will manufacture for European companies and which will be delivered to the North Sea.
Both parties already share a common history. The close collaboration between Liebherr and Dragados Offshore goes back more than a decade, since Liebherr began supplying Dragados Offshore with crawler cranes for the assembly of the impressive structures that Dragados Offshore designs and builds at its facilities in the Bay of Cadiz. “The new deal validates Liebherr’s expertise in the offshore wind sector and is a significant opportunity to strengthen the existing relationships that both companies have in the offshore industry,” expresses Matti Basan, Senior Sales Manager at LiebherrMCCtec Rostock GmbH.
The latest generation of the RL series
The equipment chosen by Dragados Offshore is the RL 2600. Its compactness is underlined by a sleek design. It is therefore an ideal solution for operators where space is limited as it offers a reduced tail radius. With a possible maximum outreach of up to 45 metres and a
lifting capacity of up to 35 tonnes, it is an ideal choice for maintenance and supply work, especially in the wind power industry. This also benefits Dragados’ latest generation of 2 GW platforms, which perform the function of an electrical substation. They collect the energy from the wind turbines, convert it and deliver it to land.
Liebherr Intelligent Maintenance for modern maintenance
Additionally, Dragados Offshore opted in for the sophisticated maintenance system, Liebherr Intelligent Maintenance, or LiMain. It revolutionises maintenance for Liebherr maritime cranes by enabling remote service from shore. This innovative approach minimises the need for onsite visits, reducing costs and environmental impact. Operators can select from various modules to tailor intelligent maintenance to their specific needs. Whether it’s monitoring or maintenance, LiMain ensures efficient, sustainable crane operation, independent of location or time.
Marco Gonzalez, Sales Manager for maritime cranes at Liebherr Ibérica, commented: “We’re proud to close this significant contract with Dragados Offshore. Liebherr is actively collaborating with Dragados Offshore, and Liebherr Ibérica will play a key role in assembling the equipment and providing technical support.”
Liebherr Africa, +27 (0) 11 365 2000, info.laf@liebherr.com, www.liebherr.com
Rusch boasts over 30 years of expertise in crane boom repairs, utilizing certified welders, established welding procedures, and a deep understanding of crane design.
We are equipped to restore any damaged boom back to its original strength, regardless of make or type.
Lattice booms can be repaired on location, while telescopic booms required more specialized attention in our well-equipped Netherlands workshops. This meant that telescopic booms had to be shipped
to the Netherlands for repair, often resulting in significant costs to our clients.
The good news!
To eliminate these challenges and minimize expenses for our clients in Africa, Rusch has opened a workshop in South Africa!
Located in Mossel Bay, our certified
team is now on hand to repair your crane booms to the same highquality standards as our facility in the Netherlands, this resulting in less downtime and reduced transportation costs.
Our certified Rusch team is skilled in various repair techniques and committed to providing efficient and economical repair solutions, ensuring greater time efficiency to you the client.
Reach out to us today for more information about our services!
Rusch South Africa (Pty) Ltd. +27 (0) 44 333 0213, info@rusch.co.za, www.ruschcranes.com
“H&H Specialized Services was formed in 1998 to provide a specialized crane service.”
B-BBEE Level 1 Black Woman Owned Company
Our Services Include:
Custom Manufacturing: New gantry cranes, jib cranes, portal cranes, and lifting attachments tailored to your needs.
Turnkey Solutions: Comprehensive structural steel manufacturing.
Maintenance & Repairs: Expert servicing for overhead cranes and lifting equipment.
Load Testing: Thorough testing of lifting machinery in accordance with our LME standards, covering 11 specific scopes.
Scope of Approval:
Lifting Tackle
Chain Blocks
Lever Hoists
Crawl Beams
Forklifts
Vehicles Hoists
Mobile Cranes
Overhead Cranes
Aerial Platforms
Truck Mounted Cranes
Jib Cranes
Manitou Group, a world reference in the handling, aerial work platform and earth moving announces the expansion of its ME forklift range with five new lithium-ion models named ME LIFT.
Our aim is to provide our customers with ever greater comfort, performance and profitability through more sustainable solutions.
Introducing five new models
Manitou Group presents five new lithium-ion forklift models in the Manitou ME LIFT range, designed for para-industrial and paraagricultural applications (handling bricks, processed wood, viticulture, potato cultivation, etc.). With load
capacities ranging from 1.6 to 3 t, these new models come in two possible configurations, with three and four wheels, and are equipped with a 76.8 V lithium-ion battery. Maximum lifting height is up to 6,5 m.
Among the five new models, the ME 425 LD LIFT boasts a 56% lower total cost of ownership than the MI 25 D diesel forklift.
These figures take into account
maintenance costs, energy consumption and component durability.
The first models will be distributed in Europe from September 2024 throughout the Manitou dealer network.
With their long-standing expertise in the forklift market, they offer a wide range of associated services, such as after-sales service, financing and rental contracts, to provide turnkey solutions tailored to the needs of every type of customer.
new technology
Lithium batteries are extremely durable, with up to 5,000 charge cycles, and can be fully recharged in less than 90 minutes, without having to be stored in a dedicated charging room.
Thanks to their compact size (three times smaller than a conventional battery), the chassis is smaller, enabling operators to use their machine in aisles 30 cm narrower than conventional forklifts powered by lead-acid batteries.
Unlike lead-acid batteries, lithium batteries require no daily or weekly maintenance.
Manitou Group offers a standard five-year warranty on all its lithium
batteries, which are perfectly suited to long-term rental.
With this new design, service intervals are spaced at 1,000 hours or the equivalent of 6 months’ use.
The ME LIFT range offers a high level of performance thanks to a powerful traction system that provides plenty of motive power for fast travel with good grip, even in difficult conditions. In addition, the motor powering the hydraulic pump improves lifting speeds.
All ME LIFT machines boast noise levels below 70 dB(A), making it easier for operators to concentrate on their tasks.
Machine autonomy varies from a few hours to a full day, depending on the requirements and applications of each customer.
Charging time can vary from 1.5 hours to 6 hours, depending on the battery and charger, and the operator’s needs. The ME LIFT 316 model, with an 18 kWh battery, recovers 20% of its range in just 15
minutes with a 20 kW charger.
The safety of operators and their environment remains a priority for Manitou Group.
The ME LIFT range benefits from the latest standards, offering enhanced protection for the operator when negotiating curves or during lifting operations, with cabs that are resistant to falling loads.
To see and be seen, ME LIFT trucks are fully equipped with LED lighting and working lights. Optional blue lights, additional work lights and red warning lines can also be added around the machine for pedestrian safety.
With a centralized LCD display (based on existing models such as the MT 625 e telehandler), you can access all the information you need in one place, and adjust the main settings.
All ME LIFT machines are IPX4*rated and therefore rainproof, ensuring uninterrupted
outdoor use. The easy-to-activate electric parking brake ensures that the machine remains stable on ramps and slopes, preventing accidental or unintentional movement.
Acoustic insulation is considerably improved, with a noise reduction of 6 dB(A) compared to previous series.
The new range also offers greater comfort thanks to a suspended seat and optional heated cab.
The new design of the mast, in fullvisibility duplex or free-lift triplex, clearly enhances operators’ visibility of their load.
The panoramic roof window offers first-rate, FOPS**-compliant visibility, reducing neck and body movements, and also ensures better visibility when storing a load at height.
Goscor Lift Trucks (GLT), a leading provider of forklifts and materials handling solutions since 1984, proudly announces the supply of a fleet of 44 Bobcat Li-ion forklifts to Access World for their Durban operations.
This significant order underscores GLT’s commitment to providing world-class, industry-leading forklift brands at competitive prices with quality guaranteed. Switching from diesel to Li-ion forklifts will reduce Access World’s carbon footprint by 3,080 tons over the rental period, equivalent to planting 50,935 trees.
Access World, a global logistics service provider, has integrated these new electric forklifts to enhance operational efficiency and environmental sustainability. The fleet includes 40 Bobcat Li-ion B35NS and 4 Bobcat Li-ion D50X7 forklifts, all equipped with fleet management systems, and wraparound pedestrian safety lights. These machines will be deployed across three warehouses handling various types of cargo.
Jared Smart, GLT KwaZulu-Natal Area Sales Manager, highlighted the primary reasons for this substantial order: “the decision to switch to Li-ion forklifts was driven by our mutual commitment to reducing carbon emissions and enhancing operational efficiency. We are proud to support Access World in their sustainability goals.”
“Goscor has been an invaluable partner since 2012,” said Peter Hendriks, General Manager at Access World Durban. “Their dedication to providing reliable equipment and exceptional support has enabled us to streamline our operations effectively. The transition to electric forklifts marks a significant step towards achieving our environmental sustainability objectives.”
Access World operates on a global scale, offering comprehensive logistics services, including warehousing, freight forwarding, and supply chain management. Their Durban facility is a key hub in Africa, strategically positioned to provide efficient logistics solutions with state-of-the-art infrastructure, modern warehousing facilities, advanced inventory management systems, and robust security measures ensuring the safety and integrity of stored goods.
The decision to expand their fleet with GLT’s electric forklifts aligns with Access World’s strategic objectives. “Li-ion forklifts significantly enhance our environmental sustainability, reduce
energy consumption, and lower operational costs,” emphasised Hendriks. “GLT’s equipment reliability and minimal downtime support our operations seamlessly.” Access World values GLT as their preferred supplier due to exceptional product quality, reliability, and comprehensive service. “GLT understands our operational needs, offering tailored solutions that ensure optimal performance,” Hendriks affirmed. “Our longstanding partnership is built on mutual trust and reliability, contributing to significant operational efficiencies and cost savings.”
Access World anticipates integrating the new Li-ion forklift fleet smoothly. “We are confident in the positive impact these advanced machines will have on our operations,” Hendriks added. “They will drive efficiency, cost savings, and enhance environmental sustainability.”
Goscor Lift Trucks, +27 (0) 10 594 4339, lifttrucks@goscor.co.za, www.goscorlifttrucks.co.za
With capacity of 3 tonnes (6613 lbs) and lifting height of 5.8 metres (19 ft), the new TH 3.6 combines small size with impressive performance.
In fact, the most compact fixed telescopic handler in the TH range, intended for the construction and logistics sectors and soon also for agriculture, is able to lift its maximum load to a height over 5 metres (17.7 ft), 2,500 kg (5511 lbs) to the maximum height and 1,000 kg (2,200 lbs) to a horizontal reach of more than 3.5 metres (11 feet). Its low-level design makes it ideal for tight spaces, while retaining optimal ground
clearance for uneven terrains. These characteristics, together with a Deutz Stage V engine of 55 kW (75 hp) give it a top speed of 35 km/h (21 mph). The four-wheel drive and steering, with hydrostatic transmission, provide superlative stability and manoeuvrability with 3 steering modes: front, concentric and crab. The cab of the 3.6 model is specially designed to be compact with a new dashboard to optimize the user experience through
ergonomic positioning of the main controls. It also features USB ports (3.0 and c-type) for charging electronic devices and a handy cup holder. The new cab’s standard outfit is completed by the airsuspended seat, adjustable steering column, heating and radio.
Consulted via the 7 inch touch screen, the MCTS (Magni Combi Touch System) on-board software provides complete control of the machine with icon-based navigation. From the main menu, the operator can access the themed screens with the various functions, including load charts.
Unlike competitor models on the market, which have the usual load cell systems, the TH 3.6 is the only machine equipped with a more sophisticated, precise tipping protection mechanism to maximise performance and safety, in line with the entire TH range. This is the LMI (Load Moment Indicator), which enables constant monitoring of the machine’s movements to prevent any kind of overload.
The new RHT 6.31 EC: concentrated efficiency and comfort Magni launches three models derived from the market’s best-
selling rotating telescopic handlers, the RTH 6.22, 6.26 and 6.31, all equipped with elevating cab. This feature is designed to optimise work in conditions that demand greater visibility and to guarantee the very best comfort level by providing the operator with an ergonomic position, especially when handling delicate loads or using specialist attachments.
In these situations, greater visibility means safe, effective movements in even the most complex procedures, such as use of the tree cutting and log handling attachment.
The hydraulic mobile support is able to raise the cab to a height of 1.5 metres (5 ft) and tilt it between 0° and +16° for optimal control in conditions where movements must be exceptionally precise.
Two new attachments: the 3D-Film handler and the tilting rotating forks
At the Paris show, Magni also reveals two new attachments for the RTH and TH ranges: the 3D-Film handler and the 5T tilting rotating forks.
Intended for the movie industry, the 3D-Film handler has a surface fitted to support equipment such as LED light panels or floodlights used during filming in the studio or on location. With a capacity of 2.5 tonnes (5511 lbs) and continuous rotation through 360°, it provides unbeatable manoeuvrability and versatility to offer the optimal response to this specific sector’s needs.
The tilting rotating forks, on the other hand, are designed for handling bulky materials in tight spaces. Unlike standard forks, they rotate and swivel to optimise
movement of the weight during loading and unloading. They deliver frontal lifting capacity of up to 5 tonnes (11,000 lbs), rotated load capacity of up to 2.5 tonnes (5511 lbs), continuous rotation through 360° and positive tilting up to 70°.
With targeted solutions for the demands of a constantly growing sector, Magni TH further extends its range of products to continue its expansion at the global level.
Magni SA, +27 (0) 11 383 2227, info@magnisa.co.za, www.magnisa.co.za
Learn the importance of finding the center of gravity of a load along with step-by-step instructions on calculating the center of gravity (CoG) or balance point of unusually shaped loads.
In material handling, having a wellbalanced pallet can often make the difference between a smooth trip from point A to point B and a costly tipover. Finding this equilibrium is fairly intuitive if you’re moving items that are uniform in shape and weight. However, what do you do when moving objects that don’t
have an obvious middle?
What is the center of gravity of a load?
In physics, an object’s center of gravity, center of mass, or balance point is an imaginary point where there is an equal mass on all sides.
In the context of material handling,
the Center of Gravity (CoG) refers to the single point of the load or object where it can be carried perfectly balanced. To look at it another way, it’s also the point at which all the load’s weight is concentrated.
Finding the location of the center of gravity
While there is always the trial and error method, picking different spots and doing test lifts until you find the right location, there are shortcuts you can take to finding the center of gravity on a load without an apparent midpoint. Here are step-by-step instructions on finding the center of gravity of an object or load you need to move around the warehouse using lift scales, a tape measure, and a calculator:
Determine load weight distribution
Determining weight distribution is where the lift scale comes into play. First, you’ll need to weigh one side of the load, then the other. This will give you the object’s left end weight (LEW), Right End Weight (REW),
then combine them for the total weight of the object. The center of gravity shifts towards the heavier side, so knowing these weights is a critical step.
Divide the heaviest end by the total weight
You only need to calculate one side. Take the heaviest weight between LEW and REW and divide it by the total weight.
The ratio of the total weight of an object with its heavy end determines the pivot point of the load. This is where the CoG resides.
The next step is to measure the span of the load. The span is the distance between the two pick points you weighed on either side.
Using a tape measure, gauge the distance between pick points and apply the ratio from the previous step to calculate where along that span, the CoG lies.
Once you have your CoG measurement, we recommend practice tests where you try lifting the load with a jack or crane a few inches at a time to make sure it’s balanced.
If it doesn’t retain its stability and starts to tip or swing, set it back down, adjust the pick point, and try again.
Example
In this example, we have a load with a LEW of 900kg, a REW of 1,000, and a total weight of 1360kg.
The span is 100 inches. Since the Left End Weight is greater, we divide that by the total weight of 3,000 lbs.
LEW/TW = X
2,000/3,000 = 0.67
Now, take the span of 100 inches and multiply it by the ratio of the weights.
(LEW / TW) x 100” = CoG
(0.67) x 100” = 67”
The CoG is at the 67-inch mark for this load, closer to the heavier side. In summation, finding the center of gravity for an irregular load can be done through trial and error.
Still, some simple math and measurements can significantly reduce the time spent finding that balance.
At Nutting, we engineer our products to seamlessly integrate with your existing operation with carts that can be customized with various features to accommodate different load types. Does your
team produce oddly shapped parts?
We can help provide a solution for your needs, all complete with a calculated center of gravity in your production prints.
Knowing which options are best for your application can save you time and money in the long run.
That’s why it’s essential to consult an expert before purchasing.
Nutting has over 100 years of experience designing and manufacturing high-quality pallet carts, order picking carts, industrial carts, and more so you can be confident that you’re getting the best possible product for your needs. Contact us today to learn more about our pallet carts and how they can improve operational efficiency in your warehouse or distribution center.
Nutting Carts and Trailers, Info@AccoNutting.com, www.materialhandlingsolutions.com
Offering advanced, specialised lifting solutions tailored to industrial applications across the continent, H&H Specialized Services is committed to delivering reliable, high-quality cranes and after services that meets each project’s unique needs.
As a South African crane industry leader, H&H Specialized Services has built a reputation for excellence over the past 26 years, navigating both boom periods and challenging times. The company’s success is rooted in its customer-centric approach, which emphasises clear communication, dependable delivery, and bespoke crane solutions, says Matsakane Lucy Human, Managing Director.
“We’ve always believed that delivering quality solutions on
time is non-negotiable. We are committed to being transparent and dependable throughout every project phase, from initial consultation to ongoing maintenance. It’s not just about selling a crane; it’s about building lasting relationships and ensuring our clients have the best lifting solutions for their specific needs.”
As a Level 1 BBBEEE contributor, this 100% black woman-owned company has established itself as a leader in the crane industry,
providing turnkey solutions for overhead cranes, hoists, and lifting equipment. From design to manufacturing, supply and installation, as well as maintenance, the team at H&H Specialized Services takes pride in building longstanding relationships with customers.
According to Werner du Toit, International Operations Manager, it is about more than just a product or a service; it is about delivering solutions. “Our focus is on ensuring our clients get the right equipment for their specific needs while minimising any downtime and maintenance challenges they might face in the future , hence the crucial part of any supply starts from day one to understand your clients needs.”
With the COVID-19 pandemic bringing the project sector to a near standstill, the world has slowly been returning to normal. “We have seen a significant uptick in project activity, with
demand surging across sectors such as mining, construction, and energy,” said Werner du Toit, International Operations Manager at H&H Specialized Services, in an interview with Lifting Africa. “We’ve experienced a positive rebound. The last two years have been strong. Many projects we tendered during the pandemic have materialised, with previously delayed developments gaining momentum.”
Currently involved in a range of projects across several sectors, both locally and in Africa, the company is seeing an increase in demand for high-quality, cost-effective solutions. “We collaborate closely with our clients from the design stage to maintenance. It is about understanding their specific needs and then working towards finding ways to deliver the necessary solutions for those needs,” he says.
One of H&H Specialized Services’ standout projects is a wind energy development in Jeffreys Bay in the Eastern Cape. The company supplied four 64-ton double-girder portal cranes for this project. Each crane, with a span of 29 meters and a lifting height of 12 meters, plays a critical role in the casting process of concrete towers for wind turbines at the precast yard where they are stationed.
“We were afforded four months for this project, and despite challenges around logistics, we were able to complete it on time and within budget,” said Du Toit. “We also have a dedicated maintenance team on-site to ensure seamless operations throughout the first phase of this project.” The company was also involved in the design, manufacture and installation of the crane rail system and the overhead crane power supply system and supporting structure that runs for 700 meters.
According to Human, several factors contribute to successful project delivery, but transparency and communication top the list. “You have to communicate with clients, keeping them informed every step of the way of the
progress being made while at the same time keeping abreast of any and all issues that arise.” Human credits much of the company’s success to its customer-centric approach. “We are committed to reliability and delivering on the promises we make. Of course, it is not always possible as sometimes factors are out of our control, but clear communication makes all the difference.”
Du Toit agrees, saying the company is renowned for this approach. Just as important, he notes, is the delivery of quality products. “In the lifting sector, there is no room for error. Our products are of the highest quality. At the same time, we also understand the economic environment we operate in, and the need for cost-effective solutions is clear. A lot of time and effort is taken to ensure we meet these market needs in particular,” he says. Another feature differentiating the company is its Factory Acceptance Testing (FAT). “We conduct a full function and load test in our facility, with the client present to witness and sign off before the crane is dispatched to the site,” explains Du Toit. “This establishes the credibility that the equipment is ready for operation and goes a long way in building trust with our customers.”
Existing footprint
“We have grown from 10 staff in 2017 to 75 permanently employed staff members.
We currently run maintenance and project crew members at various developments across South Africa coordinated from our head office in Springs, Gauteng. We are also working on maintenance contracts in the Eastern Cape , Northern Cape, Limpopo and in Northwest,” said Du Toit.
The company has branches across South Africa to ensure they are able to deliver a hands-on service clients. “We also offer a 24/7 breakdown service and are always on call with our standby teams.”
Expanding footprint
While H&H Specialized Services’ primary market remains South Africa, the company is actively
growing its footprint across Africa. “We are the exclusive appointed agent for WorldHoist across the continent,” says Du Toit. “Our African order book value currently accounts for 10% of our business, but we’re seeing a growing demand, particularly in the mining and power sectors.”
Recent projects include structural steelwork and crane installations in Zambia, the delivery of a 3-ton jib crane and monorail hoist system in Mali, and the supply of cranes to a hydropower project in the DRC and a 30m span 5t Store warehouse crane on one of the mines. “We are very active in Mozambique, Zimbabwe, and Botswana, where projects are also being picked up,” says Du Toit.
Locally, the company is currently involved in four major water sector projects in KwaZulu-Natal, Limpopo, and the Northern Cape and 2 projects on one of our mining clients.
According to Human, innovation remains at the core of their operations. “We are constantly finding new ways to add value to our clients. We’re embracing advanced technologies and fostering close collaboration with our clients to ensure we deliver the solutions they need.”
H&H Specialized Services, +27 (0) 11 818 0369, info@h-hss.co.za, www.h-hss.co.za
Despite their seemingly straightforward appearance, wire ropes are highly complex components, integral to ensuring safety and operational efficiency in the lifting sector. Speaking at the LEEASA conference in Johannesburg earlier this year, Roger Day, Director of LEEASA, emphasised the critical importance of understanding the complexities involved in wire rope inspection, highlighting that proper evaluation is key to preventing failures and maintaining safe lifting operations.
In Europe, where inspections occur every 6 to 12 months, a chain sling operating in an arduous environment could go as long as 180 days without being inspected by a LMI. This underscores the critical importance of conducting pre-checks before use.
Addressing delegates at the annual LEEASA conference, Oldknow explained that while pre-checks are mandated by law in Europe, they are often poorly executed or overlooked entirely.
“We even see this issue in the offshore environment and much of it can be attributed to a lack of training on how to perform prechecks. Yes, there is significant industry discussion around it, and it is legislated, but far too many people simply don’t know how to carry them out.”
Acknowledging that he was not fully up to date with local legislation, Oldknow noted that it seems to rely more on company policy than strict legal requirements. He emphasised that the issue of pre-checking
equipment prior to use is becoming a pressing topic in Europe. “The reality is that if a pre-check is not formally documented and not required by law, there is little chance that it will be consistently performed.”
Using digital effectively
With evolving technology and the increasing use of RFID chips in products, operators now have the capability to access all necessary information about equipment at the point of use. This advancement greatly facilitates pre-checks, said Oldknow. “These pre-checks are mandatory before every lift by the users of the equipment. They are not formal written inspections conducted by a LMI. This underscores the critical importance of training equipment users; if an LMI conducts checks every three or six months and rejects the equipment, it raises concerns if that equipment has been in regular use during the preceding months.”
Oldknow emphasised that the primary goal of pre-checks is to
ensure safe working equipment by identifying any faults before use. He noted that digitalisation, particularly through blue chips embedded in products, empowers users to conduct these checks more efficiently.
“The chip can store all the procedures for the pre-check, safe user instructions, necessary certifications, and maintenance programmes, as well as the current status of the product,” he explained. “In Europe, we adhere to Regulation 8 of the Lifting Operations and Lifting Equipment Regulations (LOLER), which mandates these pre-checks. The operator of the equipment serves as the first line of defence in spotting any faults or damage. These checks should be performed before lifting equipment is used each day or at the start of every shift.”
Oldknow outlined several factors to consider during these checks to ensure equipment safety. These include assessing operational lifting
safety, working under suspended loads, ensuring visibility, properly attaching and securing loads, evaluating the environment and location, managing overturning risks, identifying proximity hazards, maintaining the integrity of the equipment, and conducting thorough pre-use inspections.
More training required
He said to enhance pre-use checks, it was necessary to significantly increase training requirements, as people simply haven’t adequately been taught how to perform them.
“Digitally supported pre-use checks can revolutionise this process by integrating specific questions and recommendations from suppliers. Users can simply scan their phone over the product and it will provide answers based on pre-set questions aligned with EU standards, while also allowing for customisation by individual companies.”
This approach, said Oldknow, not only streamlines the pre-use check but also makes it far more traceable and legible, with unambiguous markings on the components.
The ability to retrofit these digital
chips incurs minimal additional costs, while the value and power they deliver far outweigh any expenses. Each check can be tied to a specific date and time, enhancing accountability.
For example, with a shackle, the digital chip can be programmed to ask structured questions tailored to the user’s experience level. For less experienced operators, questions might include identifying missing ID, checking for illegible Working Load Limits (WLL), pinhole elongation, missing or incorrect pins, and any damage wear exceeding 10%. Conversely, for more experienced inspectors, the check could be simplified to a straightforward query: “Is it safe to use?” This adaptability ensures that pre-use checks are effective and relevant, catering to the varying experience levels of users.
He emphasised the importance of having a clear understanding of what constitutes equipment failure during a pre-check. This includes defining what types of damage or defects warrant rejection, as well as determining acceptable wear levels
and identifying which wear patterns need monitoring.
Effective recording of these checks is crucial. Operators should document when, where and by whom the check was conducted, along with the equipment’s condition, any defects and any notable features—such as photographs.
Currently, pre-use checks often go unrecorded, but this must change; accurate records are the only way to demonstrate compliance with legal requirements, said Oldknow.
“Implementing a streamlined recording process will allow operators to capture evidence easily, ensuring 100% traceability.”
“It is essential to make this system user-friendly, especially for newcomers to the industry, enabling them to conduct prechecks confidently and accurately.”
LEEASA,
+27 (0) 64 507 6857, admin@leeasa.co.za, www.leeasa.co.za
As the demands for high-performance ropes escalate across various sectors, Haggie’s renewed focus on Verope underscores its commitment to providing cutting-edge solutions in Southern Africa. Since becoming a distributor for Verope in 2011, Haggie has successfully introduced these high-performance ropes into the market, but a recent shift aims to deepen this relationship and enhance their offerings. Lifting Africa finds out more.
As part of a more extensive strategy to grow its worldwide footprint and presence in Africa, Verope has changed how they approach the local market. This comes as Haggie, which traditionally manufactures its own ropes, has continued recognising the growing need for
high-performance alternatives— something Verope excels at. Verope’s advanced rope technology has become increasingly relevant, particularly in mobile cranes, overhead hoists, ports and other demanding applications.
According to André John du Toit, Technical Sales Engineer at Haggie, who is also at the forefront of this shift, a new venture between the two companies promises largescale benefits to the industry at large. “While Haggie has always distributed Verope ropes, there has never been a permanent focus on these products in the local market. Verope has now asked us to join forces and focus specifically on their portfolio,” Du Toit explains. This collaboration aims to leverage Verope’s high-performance solutions and Haggie’s extensive distribution network to cater to broader market needs. Du Toit has been tasked with growing Verope’s market share in Southern Africa and
actively finding new opportunities to expand the business’s African footprint. Verope has an extensive presence worldwide, with offices in the US, South America, Europe, the Middle East, India, Singapore and China. With growing recognition of the opportunities in Africa, the company intends to develop a footprint on the continent, with Southern Africa as the entry point. “Expanding in Africa is crucial if one considers the growth potential of the emerging markets on the continent,” said Du Toit.
According to Tobias Marx, from Verope’s technical team in Zweibrucken Germany, the company is exploring new opportunities across various industries. These include the mobile crane market, the overhead crane sector, geotechnical applications, ports, and any other environments where high-performance ropes
are essential. “High-performance ropes play a crucial role in driving productivity, enhancing safety and reducing operational costs across a wide range of sectors such as marine, shipping, construction and industrial applications,” said Marx.
Citing Verope’s VeroPro 8 rope, he said it exemplified the advanced technology driving this shift towards high-performance rope. Known for its compacted construction, this rope features reduced pressure between strands and a plastic layer that maintains lubrication, enhancing performance and longevity. These innovations result in longer lifetimes and higher breaking loads, making Verope ropes ideal for high-demand applications.
He said that worldwide, there was a definite move towards increasing the use of high-performance ropes, particularly in high-demand applications. “While these ropes come with a higher cost and involve more production steps, they offer significant advantages. For instance, cranes that require three rope changes a year only need one. This reduction in downtime not only boosts productivity but also results in overall cost savings.”
According to Du Toit, the joint venture will benefit the local market. “Prior to the joint venture, there were limitations that allowed competitors to make headway in the market. With the change now introduced and by focusing on Verope’s advanced products, we
can address market demands far more effectively,” he said.
Ropes that were once exclusive to the OEM are now available locally. “We can also provide socketing end stops tailored to crane manufacturers’ specifications, along with a wide product range for various reeving systems. Our team of trained engineers can supply and fit end terminations in combination with Verope OEM ropes for a broad range of cranes, at our premises. Plans are underway to extend this service in the future to on site. “Thanks to established certification processes, we can offer shorter delivery times, provide necessary support, and, when needed, replace existing end terminations.”
The rope industry is constantly evolving, driven by research and development. Both Marx and Du Toit agree that Verope’s young and dynamic team is at the cutting edge, pushing the boundaries of rope design and application. Their strong material handling background and in-house testing facilities—spanning South Korea and Germany—ensure they remain at the forefront of the industry.
Haggie’s role, on the other hand, extends beyond distribution. Practical stock planning and market demand analysis ensure competitive pricing and timely delivery. “Our goal is to manage stock effectively and offer economical shipment solutions,” said Du Toit. This approach aligns with Haggie’s commitment to delivering value-added services, including training and maintenance.
He said with a legacy of excellence, Verope was an internationally recognised brand that would only improve local operations. The company’s in-house design and manufacturing capabilities, global distribution network, and service centres offer comprehensive support from sale to installation, replacement and maintenance.
“We provide a solutions-based service, tailoring our approach to meet client-specific needs and filling gaps in the market with ropes fit for purpose,” explained Du Toit. Verope’s rope lifetime calculator and specialised tools for lubrication and maintenance further enhanced their offerings, ensuring that clients maximise the performance and longevity of their ropes.
Embracing new opportunities
“The growing demand for highperformance ropes presents exciting opportunities for Haggie and Verope,” said Du Toit. “As new cranes and port facilities integrate these advanced ropes, the market for high-performance solutions continues to expand. Haggie’s focus on Verope’s innovative products positions them to meet these demands effectively and contribute to the ongoing evolution of the rope industry. By aligning with Verope’s technological advancements and focusing on tailored solutions, we are set to significantly impact the market, driving growth and enhancing performance across various sectors.”
Distribution, +27 (0) 83 809 1340, adutoit@haggie.co.za, www.haggiedistribution.co.za
Why does Italian Fassi Group, one of the world’s largest loader crane manufacturers, use so much Strenx® steel in its heavy-duty crane, the F1450R-HXP TECHNO?
Well, Strenx® provides the crane with more lifting power, compact dimensions when folded, and an extended reach compared to comparable cranes in the 119 tm class. The body weight can also be reduced with the advantage of more payload on the truck bed.
The Fassi F1450R-HXP TECHNO loader crane is the first model in their heavy-duty crane line with completely redesigned structural steelwork and electronics. Whether for the crane outriggers or the complete jib system, Strenx® strip and sheet steel grades Strenx® 900 to Strenx® 1100 were used throughout the crane.
“Cranes without compromise” –less material, more strength.
Depending on the starting conditions, Strenx® can allow designers to save 20%, 30% or even more in steel weight while still achieving better performance and longer equipment lifespan.
Fassi’s engineers specified thinner steel dimensions for their heavyduty crane. The results? Increased load capacity, maximum possible
boom length, and an innovative knuckle boom crane that can be mounted on 4-axle trucks.
By leveraging the high strength of Strenx® structural steel, the weight reduction helps to lower the dead weight of the crane.
This plays a major role in improving the overall performance of the crane and vehicle package.
It enables Fassi to stay true to its motto, “Cranes without compromise”, and achieve three goals: to lower fuel consumption, realize operational cost savings, and lower environmental impact through less CO2 emissions.
Towards fossil-free steel production
A truck body that weighs less means more capacity for payload or less moving mass when driving empty, and thus potentially reduced fuel consumption as an extra environmental benefit when using Strenx® steel today.
And in the near future, SSAB intends on eliminating emissions from the use of fossil fuels in its
own steel production. So you can get the same high-performing steel while lowering your environmental footprint.
Strong partnerships and local support for operators
Since Strenx® is designed for areas where structural strength and weight reduction are key competitive factors, the research and development unit at Fassi, in partnership with SSAB, worked together to co-engineer new applications with highly advanced mechanical solutions.
Fassi appreciates SSAB’s expert support, which involves recommendations for high-strength steel grades, welding, forming and tooling recommendations, and advice on production processes.
And their customers not only like the products, but the local support they get.
“Besides a powerful crane, reliable local service was also important to us,” explains Jörg Meyer, a buyer of Fassi’s cranes.
“Our local vehicle builder was a
dedicated partner by our side right from the start. While the crane was still being mounted on the truck, we were able to submit and implement the last adjustment requests.”
“As a construction company specializing in timber construction, the renovation of old buildings and roofing work, we also have to offer our customers a comprehensive service package, so we appreciate this partnership.”
• Extended reach over comparable loader cranes in the 119 tm class
• Reduced body weight, and lower dead weight
• More payload possible on truck bed
• Steel’s high yield strength allows for thinner plate to be used and less steel overall
• Lighter vehicle requires less fuel when driving empty, also providing environmental benefits
SSAB South Africa (Pty) Ltd +27 (0) 11 724 5000, info.za@ssab.com, www.ssab.com
World-class, industry-leading forklift brands are available at competitive prices with quality guaranteed.
Goscor Lift Trucks, the first ISO and OHSAS accredited forklift company in South Africa, have established a powerful reputation of being one of the largest suppliers of forklifts and materials handling solutions to the Southern African market today.
SkyJacks, a trusted leader in powered access, lifting and handling equipment, made a strong impact at Electra Mining Africa 2024, held from the 2nd – 6th of September at the Expo Centre in Nasrec, Johannesburg. The company’s participation highlighted its commitment to innovation, safety, and customer satisfaction.
During the five-day exhibition, SkyJacks introduced a range of advanced equipment that captured the attention of industry professionals. Allistair Bennett, Managing Director at SkyJacks, shared his enthusiasm, “Our latest equipment offerings, such as the Dingli S Series Scissor Lifts, JCPT2212DC electric 22m self-propelled scissor lift, and the FARESIN Telehandler Range, demonstrate our dedication to providing solutions that cater to the diverse needs of our clients in the mining, construction, and industrial maintenance sectors.”
The JCPT2212DC electric 22m selfpropelled scissor lift, for instance, is designed to provide a safe and efficient solution for working at height in tight spaces.
Its compact size and zero-emission electric motor make it ideal for indoor use, while its powerful performance ensures that it can handle demanding tasks with ease.
The S Series Scissor Lift, another innovative offering from SkyJacks,
boasts a range of features that enhance productivity and safety, such as intuitive controls and advanced safety systems.
In addition, SkyJacks displayed other innovative equipment, including the DINGLi BA44RT articulating diesel 44m selfpropelled boom lift, and the DINGLi BA11NE electric 11m articulating boom lift, reinforcing its leadership in the powered access equipment sector.
These products illustrate SkyJacks’ commitment to providing a comprehensive range of solutions that cater to the diverse needs of its clients, from vertical lifts for tight spaces to boom lifts for hard-toreach areas.
SkyJacks also featured the Italianmade FARESIN telehandlers, a valuable addition for customers in industries such as mining, logistics, retail, and construction. These telehandlers offer impressive capabilities, with a load capacity ranging from 2.6 tons to 7 tons and a reach extending from 6 meters to 17 meters including some
full electric models. In addition, SkyJacks showcased the Jekko range of mini-cranes, which can lift between 2.8 tons and 8 tons with superior reach as well as the GEDA 1500 Z/ZP F construction hoist which can move people and equipment to heights of up to 100m.
These versatile machines were enthusiastically received by professionals in construction, energy, mining, and manufacturing, who quickly identified various applications for them in their operations.
A commitment to safety Day three’s focus was Safety and Lifting Day, highlighting the importance of occupational health and safety in the lifting industry—a priority that aligns closely with SkyJacks’ core values. As part of the event, the Lifting Equipment Engineering Association of South Africa (LEEASA) hosted a twoday conference on occupational safety and safe industrial lifting operations, reinforcing best practices in the field. SkyJacks
used Electra Mining to launch their new range of ALR Chain Blocks and Lever Hoists. “Safety remains a top priority for SkyJacks,” Bennett stated. “Our products are designed to meet the highest safety standards. ensuring our customers can perform their tasks with confidence and security.”
Engaging new and existing clients
Keith Freel, Sales Manager at SkyJacks, reflected on the success of the event, sharing insights on customer interactions, “The diverse range of customers we encountered at Electra Mining Africa 2024 underscores the broad appeal of our products. From costconscious clients to those ready to make purchasing decisions, our equipment caters to a wide spectrum of needs. Additionally, it was exciting to introduce firsttime customers to our innovative solutions, opening up new opportunities for their operations.”
Strengthening industry connections
Allistair Bennett further emphasised the strategic value of participating in Electra Mining Africa, “While immediate outcomes may not always be apparent, our presence at the event is a crucial branding exercise. By aligning with trusted partners like Dingli, Faresin, Jekko, GEDA, and ALR, we continue to strengthen SkyJacks’ position as
a market leader and foster lasting industry connections.”
Looking ahead: a future of innovation
Electra Mining Africa 2024, featuring over 950 exhibitors, proved to be a successful platform for SkyJacks to showcase its latest products and services. As the company looks to the future, it remains dedicated to its core values of innovation, safety, and
customer satisfaction. Through continuous investment in research, development and strategic partnerships, SkyJacks ensures that its offerings remain at the cutting edge of the industry, enabling clients to excel in their respective fields.
SkyJacks, +27 (0) 82 300 6537, Alistair.bennett@skyjacks.co.za, www.skyjacks.co.za
Combilift gains further global recognition as it secures awards in 2 categories at the recent UK Materials Handling Association Awards in Birmingham on Saturday the 14th of September.
Up against some of the biggest names in Material handling, they walked away with the coveted ‘Ergonomic Innovation of the Year’ and the ‘Manufacturer Product Innovation of the Year’.
The Combi-CB70E was celebrated for its groundbreaking ergonomic
design. The 7-ton electric-powered, multidirectional counterbalance forklift is the shortest 7-ton capacity truck on the market, making it highly efficient with long loads in tight spaces. The truck’s surprisingly spacious cab, with floor-to-ceiling panoramic glass,
provides operators with excellent visibility and enhanced safety. One of its standout features is the Auto Swivel Seat, which automatically swivels 15 degrees to the left or right, depending on the direction of travel.
This feature significantly reduces driver strain, particularly when reversing.
The CB70E also incorporates a gas strut suspension system, typically found in larger industrial machinery.
This advanced suspension and large super-elastic tyres ensure a smooth ride, even across rough or uneven terrain or during extended shifts.
Combilift’s independent electric traction system -previous Red Dot award winner- provides 100% traction control for all front and rear drive wheels.
This system eliminates the need for a differential lock on slippery surfaces, reduces load swing, and enhances safety and precision when transporting long, heavy loads particularly when navigating sideways, regardless of ground
conditions. Combilift’s second award, the ‘Manufacturer Product Innovation of the Year’, went to the Combi LC Blade, a cutting-edge machine designed specifically to address the growing challenges of transporting offshore wind turbine blades from the manufacturing plant to storage or transportation facilities.
These blades, which can reach up to 115 metres in length and weigh up to 70 tonnes, have long posed logistical challenges due to their size, fragility and complexity.
Combilift’s Heavy Equipment Design Team, known for developing pioneering solutions like the CombiSC Straddle Carrier and CombiMG Mobile Gantry worked hand in hand with Siemens Gamesa, a leading supplier of offshore wind turbines, the LC Blade ensures unparalleled stability and safety during transport.
Now implemented in manufacturing sites across the world, Combilift has transformed the logistics of handling wind turbine blades and set a new industry standard.
Combilift CEO and Co-Founder
Martin McVicar; “We are more than delighted to have won not just one, but two prestigious accolades at this years Archies 2024, making this our 12th Archies to date. Competing against such high-calibre competitors highlights what a fantastic team we have, which are willing to push the boundaries of the material handling industry.”
These awards solidify Combilift’s winning momentum after taking home ‘Design Team of the Year’ for the LC Blade and the ‘Industry Leader Award’ - recognising
McVicar’s transformative leadership at the UK EMA Awards in London, bringing a total of 4 awards for the Irish manufacture within two weeks! As Archimedes once said, “Give me a lever long enough and a fulcrum on which to place it, and I shall move the world.”
Combilift embodies this spirit of innovation, continuously pushing the boundaries of material handling solutions.
Combilift, press@combilift.com, www.combilift.com
LEEASA
T: +27 (0) 64 507 6857
E: admin@leeasa.co.za
W: www.leeasa.co.za
Kempston Controls
T: +27 (0) 140 776 2888
E: holyhead@kempstoncontrols.co.uk
W: www.kempstoncontrols.co.uk
Condra Cranes
T: +27 (0) 11 776 6000
E: sales@condra.co.za
W: www.condra.co.za
Elephant Lifting Equipment
T: +27 (0)12 661 6105
E: info@elephantlifting.co.za
W: www.elephantlifting.co.za
Johnson Crane Hire
T: +27 (0) 11 455 9222
E: PeterY@jch.co.za
W: www.jch.co.za
Liebherr Africa
T: +27 (0) 11 365 2000
E: info.laf@liebherr.com
W: www.liebherr.com
Bell Equipment Southern Africa
T: +27 (0) 11 928 9846
E: susanmy@bell.co.za
W: www.bellequipment.com
Goscor Lift Trucks
T: +27 (0) 11 230 2600
E: lifttrucks@goscor.co.za
W: www.goscorlifttrucks.co.za
Jungheinrich
T: +27 (0) 10 596 8460
E: info@jungheinrich.co.za
W: www.jungheinrich.co.za
Yale Lifting Solutions
T: +27 (0) 11 794 2910
F: +27 (0) 11 794 3560
E: crm@yalelift.co.za
W: www.yale.co.za
Yale Lifting Solutions
T: +27 (0) 11 794 2910
F: +27 (0) 11 794 3560
E: crm@yalelift.co.za
W: www.cmco.com
IY Safety & Inspections
T: +27 (0) 82 773 7019
C: +27 (0) 82 956 3176
E: bianca@iysafetyinspection.co.za
W: www.iysafetyinspection.com
Kiloton
T: +27 (0) 861 707 707
E: sales@kiloton.co.za
W: www.kiloton.co.za
Kanu Equipment South Africa (Pty) Ltd
T: +27 (0) 11 826 6710
E: fransv@kanuequipment.com
W: www.kanuequipment.com
H&H Specialized Services
T: +27 (0) 82 446 2899
E: werner@h-hss.co.za
W: www.h-hss.co.za
Kempston Controls
T: +27 (0) 140 776 2888
E: holyhead@kempstoncontrols.co.uk
W: www.kempstoncontrols.co.uk
Morris Material Handling SA
T: +27 (0) 11 748 1000
F: +27 (0) 11 748 1093
E: sales@morris.co.za
W: www.morris.co.za
Elephant Lifting Equipment
T: +27 (0)12 661 6105
E: info@elephantlifting.co.za
W: www.elephantlifting.co.za
Kiloton
T: +27 (0) 861 707 707
E: sales@kiloton.co.za
W: www.kiloton.co.za
GregBev Enterprise
C: +27 (0) 82 854 5143
C: +27 (0) 72 395 4342
T: +27 (0) 53 285 0842
E: admin@gregbev.co.za
W: www.gregbev.co.za
Kiloton
T: +27 (0) 861 707 707
E: sales@kiloton.co.za
W: www.kiloton.co.za
Elephant Lifting Equipment
T: +27 (0)12 661 6105
E: info@elephantlifting.co.za
W: www.elephantlifting.co.za
Yale Lifting Solutions
T: +27 (0) 11 794 2910
F: +27 (0) 11 794 3560
E: crm@yalelift.co.za
W: www.cmco.com
Morris Material Handling SA
T: +27 (0) 11 748 1000
F: +27 (0) 11 748 1093
E: sales@morris.co.za
W: www.morris.co.za
LOAD TESTING AND RE-CERTIFICATION
3 60 5 Services
T: +27 (0) 72 207 7443
T: +27 (0) 64 687 7270
E: sales@3605services.co.za
W: www.3605services.co.za
Cranecor Africa
T: +27 (0) 10 446 5790
E: info@cranecor.co.za
W: www.cranecor.co.za
GregBev Enterprise
C: +27 (0) 82 854 5143
C: +27 (0) 72 395 4342
T: +27 (0) 53 285 0842
E: admin@gregbev.co.za
W: www.gregbev.co.za
IY Safety & Inspections
T: +27 (0) 82 773 7019
C: +27 (0) 82 956 3176
E: bianca@iysafetyinspection.co.za
W: www.iysafetyinspection.com
Kiloton
T: +27 (0) 861 707 707
E: sales@kiloton.co.za
W: www.kiloton.co.za
Margisia Lifting Solutions
T: +27 (0) 14 763 1849
C: +27 (0) 83 992 2222
E: info@margisia.co.za
W: www.margisia.co.za
Cranecor Africa
T: +27 (0) 10 446 5790
E: info@cranecor.co.za
W: www.cranecor.co.za
Morris Material Handling SA
T: +27 (0) 11 748 1000
F: +27 (0) 11 748 1093
E: sales@morris.co.za
W: www.morris.co.za
H&H Specialized Services
T: +27 (0) 82 446 2899
E: werner@h-hss.co.za
W: www.h-hss.co.za
HP Cranes Consulting
T: +27 (0) 11 740-9725/28/33
F: +27 (0) 11 740 8416
E: admin1@hpcranes.co.za
W: www.hpcranes.co.za
CSIR
T: +27 (0) 79 887 2218
Shosholoza Consulting
T: +27 (0) 14 495 1994
C: +27 (0) 79 391 2990
E: info@shosholoza.africa
W: www.shosholoza.africa
Yale Lifting Solutions
T: +27 (0) 11 794 2910
F: +27 (0) 11 794 3560
E: crm@yalelift.co.za
W: www.cmco.com
J Express Crane Services
T: +27 (0) 11 864 8402
M: +27 (0) 83 425 5535
F: +27 (0) 11 864 8408
E: jexpress@telkomsa.net
Kiloton
T: +27 (0) 861 707 707
E: sales@kiloton.co.za
W: www.kiloton.co.za
Kempston Controls
T: +27 (0) 140 776 2888
E: holyhead@kempstoncontrols.co.uk
W: www.kempstoncontrols.co.uk
E: mininglabs@csir.co.za
W: www.csir.co.za/mechanical -and-rope-testing-laboratory
IY Safety & Inspections
T: +27 (0) 82 773 7019
C: +27 (0) 82 956 3176
E: bianca@iysafetyinspection.co.za
W: www.iysafetyinspection.com
V & S Automation/Cranes
T: +27 (0) 10 442 7478
C: +27 (0) 82 787 2343
E: victor@vsautomation.co.za
W: www.vandsautomation-cranes.co.za
&
ACROW
T: +27 (0) 11 824 1527
E: info@acrow.co.za
W: www.acrow.co.za
Lifting Placements
C: +27 (0) 61 063 1687
E: info@liftingplacements.co.za
W: www.liftingplacements.co.za
Chimaera
T: +27 (0) 84 506 1209
E: ndt@chimaera.co.za
W: www.chimaera.co.za
By Carpel SRL - Italy
T: + 39 (0) 39 532 0952
F: + 39 (0) 39 532 0825
E: info@bycarpel.it W: www.bycarpel.it NON
Condra Cranes
T: +27 (0) 11 776 6000
E: sales@condra.co.za
W: www.condra.co.za
FB Cranes
T: +27 (0) 11 902 3271
E: info@fbcranes.co.za
W: www.fbcranes.co.za
J Express Crane Services
T: +27 (0) 11 864 8402
M: +27 (0) 83 425 5535
F: +27 (0) 11 864 8408
E: jexpress@telkomsa.net
Kempston Controls
T: +27 (0) 140 776 2888
E: holyhead@kempstoncontrols.co.uk W: www.kempstoncontrols.co.uk
KL Cranes and Lifting Equipment
T: +267 397 4853
C: +267 71344438
E: annelieze@klcranesbot.com W: www.klcranesbot.com
Morris Material Handling SA
T: +27 (0) 11 748 1000
F: +27 (0) 11 748 1093
E: sales@morris.co.za
W: www.morris.co.za
Kempston Controls
T: +27 (0) 140 776 2888
E: holyhead@kempstoncontrols.co.uk
W: www.kempstoncontrols.co.uk
Giovenzana International
T: +39 (0)39 5951 1277
E: giovenzana@giovenzana.com
W: www.giovenzana.com
Kiloton
T: +27 (0) 861 707 707
E: sales@kiloton.co.za
W: www.kiloton.co.za
H&H Specialized Services
T: +27 (0) 82 446 2899
E: werner@h-hss.co.za
W: www.h-hss.co.za
Kiloton
T: +27 (0) 861 707 707
E: sales@kiloton.co.za
W: www.kiloton.co.za
CB Lifting
T: +27 (0) 22 719 1437
E: info@cblifting.co.za
W: www.cblifting.co.za
Haggie
T: +27 (0) 11 601 8400
E: distribution@haggie.co.za
W: www.scaw.co.za
Umholi
T: +27 (0) 11 914 2210/11
F: +27 (0) 11 914 2209
E: umholi@umholi.co.za
W: www.umholi.co.za
Combi Lift
T: +27 (0) 11 900 8010
E: victor@solutions-4u.co.za
W: www.combilift.co.za
MH Dawood Plant Services
T: +27 (0) 11 496 1007
F: +27 (0) 11 496 1198
E: info@mhdawood.co.za
W: www.mhdawood.co.za
LMI Academy
T: +27 (0) 11 475 5876
Kanu Equipment South Africa (Pty) Ltd
T: +27 (0) 11 826 6710
E: fransv@kanuequipment.com
W: www.kanuequipment.com
Manitou
T: +27 (0) 10 601 3000
E: info.msa@manitou-group.com
W: www.manitou.com
Liebherr Africa
T: +27 (0) 11 365 2000
E: info.laf@liebherr.com
W: www.liebherr.com
E: info@lmi-academy.co.za
W: www.lmi-academy.co.za
MCLS Training
T: +27 (0) 82 506 5899
T: +27 (0) 73 089 0624
E: sinky@mclstraining.co.za
W: www.mclstraining.co.za
Phakamisa Safety Consultants
T: +27 (0) 11 462 9620/1
F: +27 (0) 11 462 9620
E: potto@icon.co.za
W: www.phakamisasafety.co.za
Crane Clinic
T: +27 (0) 11 902 7379
E: reception@craneclinic.co.za
W: www.craneclinic.co.za
Palfinger Africa
T: +27 (0) 11 608 3670/1/2/3/4
E: sales@palfingerafrica.co.za
W: www.palfinger.co.za
Smith Capital Equipment
T: +27 (0) 11 873 9830
E: mail@smithcapital.co.za
W: www.smithcapital.co.za
Dymot Engineering
T: +27 (0) 11 970 1920
F: +27 (0) 11 970 1979
E: pa@dymot.co.za
W: www.dymot.co.za
been appointed as the
This partnership marks a significant milestone for us, as we bring to our customers this cutting-edge technology and innovation from Hoeflon, a renowned designer, manufacturer, and supplier of compact cranes, Based in Barneveld, the Netherlands.
Hoeflon Compact Cranes, also known as mini cranes, spider cranes, or compact crawlers, are revolutionising the way heavy lifting is done in confined or hard-to-access spaces.
These compact cranes are ideal for tasks such as placing glass with precision or accurately positioning steel beams and pipes. What sets Hoeflon Cranes apart is their exceptional lifting capacity, being the only compact crane capable of lifting more than its own weight. The possibilities with Hoeflon Compact Cranes are truly endless!
Trusted by professionals worldwide, the Hoeflon series perfectly complements our existing range of used and refurbished mobile cranes. This collaboration allows us to offer our customers in South Africa/Africa access to top-of-the-line compact crane solutions that cater to a diverse range of industry and lifting requirements.
At Fastlift Cranes, we take pride in being a leading supplier of quality used cranes in South Africa/Africa. This new partnership with Hoeflon further solidifies our commitment to providing our customers with the best-in-class lifting equipment and solutions.
We are excited about the opportunities that this partnership brings and look forward to serving our customers with the exceptional performance and reliability of Hoeflon Compact Cranes. Join us as we continue to elevate the standards in the crane industry in South Africa/Africa and beyond.
For more information about our range of Hoeflon Compact Cranes and how they can benefit your operations, contact us at Fastlift Cranes. Experience the power and versatility of compact lifting with Hoeflon!
Assuring you of our best service and attention at all times.