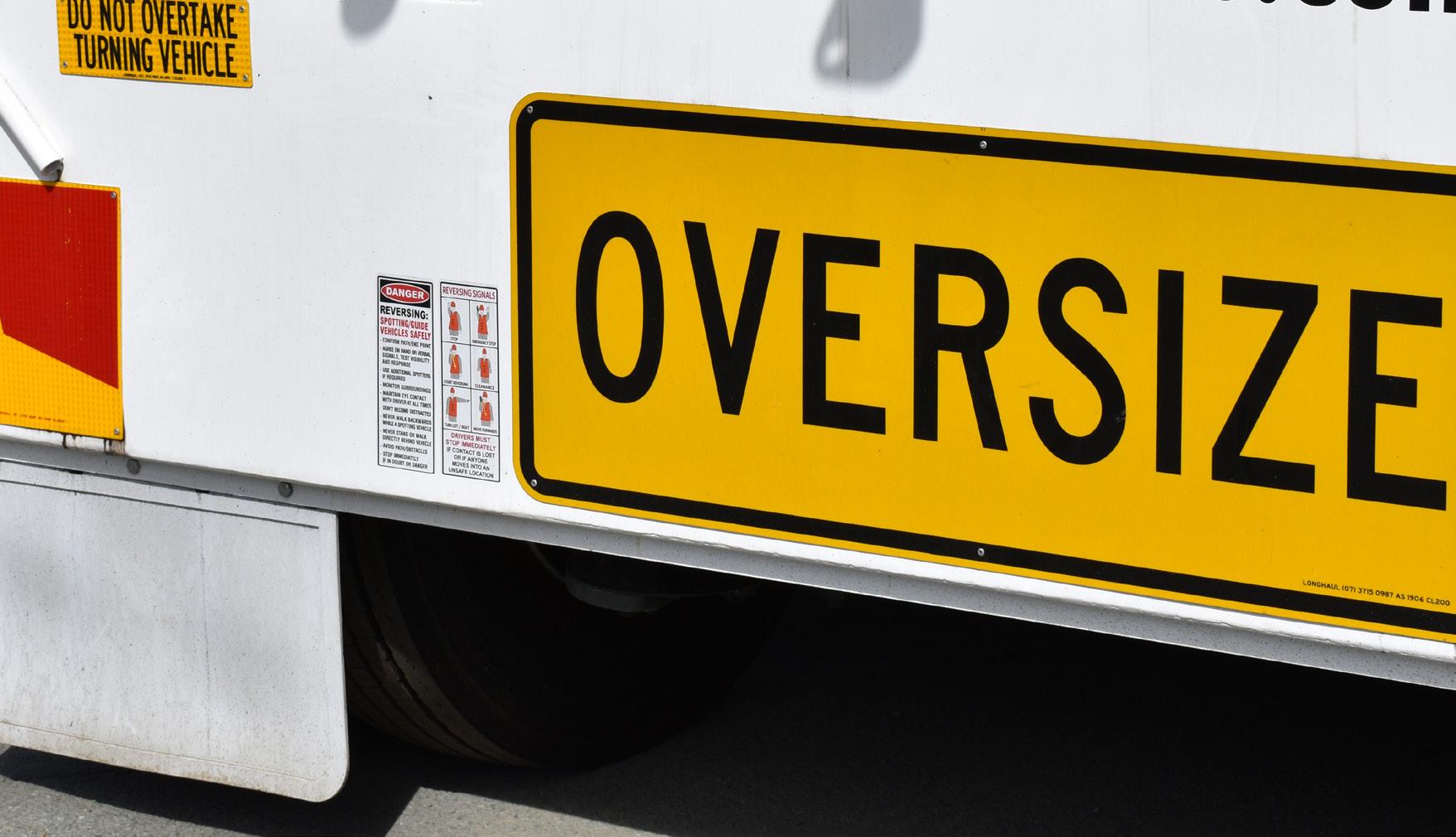
8 minute read
INCIDENT REVIEW
High Potential Incident Review
This issue we look into some examples of ‘near misses’ and high potential incidents (HPI’s).
Advertisement
A High Potential Incident is an incident or near-miss that, realistically, could have under other circumstances caused one or more of the following:
•Fatalities, Lost Time Injuries (LTI’s), injuries involving hospitalisation and injuries likely to cause permanent total work incapacity.
•Significant cost damage
•Significant environmental impact
•All electric shocks
•Incidents likely to result in major Workplace Health & Safety regulatory investigations There is so much to be learned from HPI’s – just as much as those incidents with serious and fatal outcomes. A selection of HPI’s are described below and have been categorised into some common themes that are seen in the crane, construction, transport and mining industries.
POWERLINES
EVENT: TRUCK CONTACTS DE-ENERGISED POWERLINE
DATE: 2020
LOCATION: GUAM, MICRONESIAN ISLANDS
EVENT DETAILS: In September 2020, two operators were making a delivery of aggregate to a residential area. After unloading material, the truck dump box would not retrack. A third party was spotting for the operator and as the operator moved forward, the dump box tray of the truck came in contact with the de-energised power line. This is a HPI as the boom came within 3m of the powerlines – i.e. within the “no go zone”.
EVENT: TOWER CRANE STRIKES POWERLINES
DATE: 2018
LOCATION: QUEENSLAND, AUSTRALIA
EVENT DETAILS: In November 2018, lifting equipment attached to a tower crane servicing a construction project contacted live overhead powerlines next to the site. This caused the power supply within the local area to automatically shut off. There were no injuries and it appears the crane unintentionally rotated over the powerlines under its own power. Investigations are continuing.

POTENTIAL CAUSE FACTORS
• Low hanging power lines • Spotter not paying attention • Additional spotters where necessary • Area not assessed prior to job • Complacency • Potential time factor/cost pressure • Not knowing or understanding the regulations • Crane movements not accounted for
CORRECTIVE / PREVENTATIVE ACTIONS:
• Do site walk and check for ground conditions and overhead obstruction before moving equipment • Review spotter card with third party spotter • Safety talk with the crew on the dangers of working with equipment around energised and de-energised power lines • All powerline incidents have a high potential to injure or kill • Any inadvertent movement may have caused catastrophic damage/death. Crane operator needs to be fully paying attention at all times • Spotters are to remain in place until the job is completed.
Source: https://www.worksafe.qld.gov.au/news-and-events/alerts/incident-alerts/2018/tower-crane-strikespowerlines. Internal
COUNTERWEIGHTS NOT SECURED CORRECTLY
EVENT: COUNTERWEIGHT FELL OFF MOBILE PLANT DATE: 2016 LOCATION: QUEENSLAND, AUSTRALIA
EVENT DETAILS: In January 2016 a 13.4 tonne counterweight fell off the back of a mobile piling rig that was being assembled on a construction site in Brisbane. Two workers were nearby when the counterweight fell, one narrowly missed being struck and the other was injured.
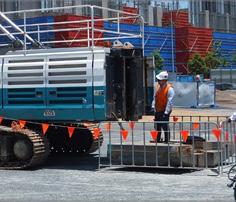
EVENT: COUNTERWEIGHT FELL OFF MOBILE PLANT DATE: 2020 LOCATION: QUEENSLAND, AUSTRALIA
EVENT DETAILS: In October 2020, counterweights were being installed as part of the set up of a mobile crane in Gladstone, QLD. During the set up process, the slings became caught under the base weight. Once all four slings were unhooked, the workers proceeded to rope up when they noticed the counterweight had lifted and promptly began to rope down. It was already too late, the counterweight had lifted too high and then fell backwards off the crane.
Source: https://www.worksafe.qld.gov.au/news-and-events/alerts/workplace-health-and-safety- alerts/2016/ counterweights-on-mobileplant#:~:text=On%208%20January% 202016%20a,injured%20when %20the%20 counterweight %20fell.
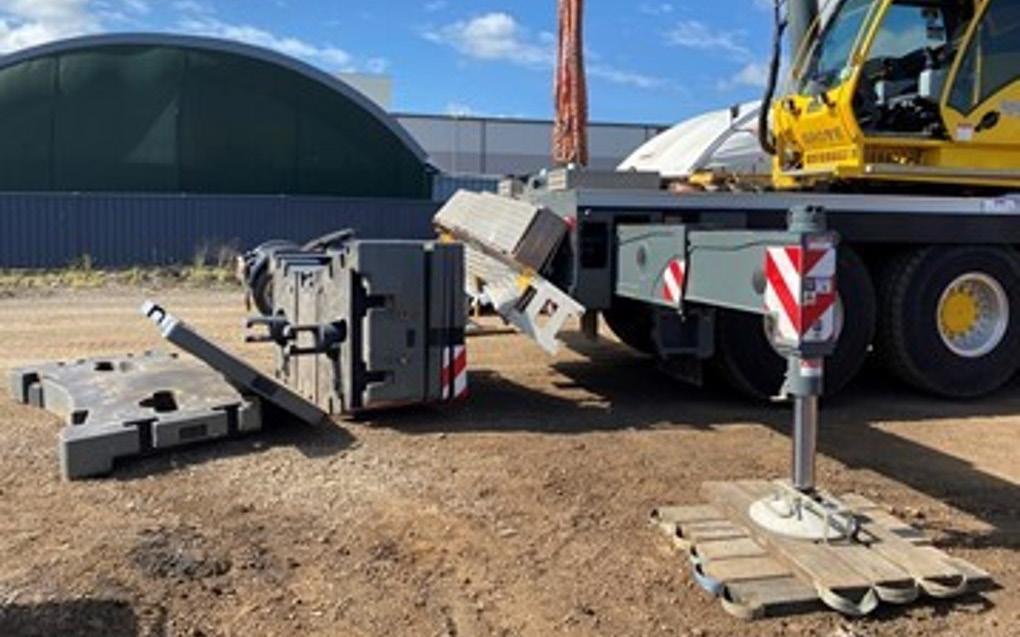
POTENTIAL CAUSE FACTORS
• The counterweight and/or engagement mechanism is not designed to minimise the risk of injuries during rigging and de-rigging operations. For example, when the counterweight is mounted on the rear of the plant, it can fall onto workers positioned behind the plant when the counterweight locking system is being released
• The counterweight was secure while bolts were being installed. There is no effective method to temporarily secure the counterweight in place prior to the bolts being tightened • Workers were in the potential fall zone, behind the counterweight, when installing or removing the counterweight • Possible worker complacency led to the auxiliary equipment not being checked
CORRECTIVE / PREVENTATIVE ACTIONS:
• Counterweights should be designed so a person is never required to be in a position where they have the potential to be struck if the counterweight becomes detached or falls during fitting or removal • The plant manufacturer should document safe work procedures for the fitting or removal of counterweights • Workers involved in the fitting or removal of counterweights on mobile plant are required to hold intermediate rigger HRWL • Workers are to be experienced in this activity or be adequately trained and supervised until they are considered competent
IMPROPER LOAD RESTRAINT CAUSING LOAD TO SLIDE FORWARD INTO CAB OF VEHICLE
EVENT: TIMBER SLIDES THROUGH UTE REAR WINDOW DATE: 2020 LOCATION: QUEENSLAND, AUSTRALIA
EVENT DETAILS: In September 2020, a worker was driving down a steep hill with a stillage of timber in the back of a ute. After stopping suddenly, timber off the stillage slipped out from under the strap and smashed through the back window of the ute cab.
EVENT: STEEL BEAMS SLIDE OFF TRAILER THROUGH TRUCK REAR WINDOW DATE: 2019 LOCATION: OKLAHOMA, UNITED STATES OF AMERICA
EVENT DETAILS: A semi-truck driver survived after a crash in April 2019 in Oklahoma. According to reports, the driver had to stop suddenly causing a load of steel beams he was carrying to shift and smash through into the cab of his vehicle. After the incident, the driver was trapped inside the vehicle and it took rescue crews many hours to remove him. He was taken to hospital for treatment of major injuries, but he was alert and talking after the crash. The incident remains under investigation.
When the driver stopped suddenly, timber off the stillage slipped out from under the strap and smashed through the back window of the ute cab.
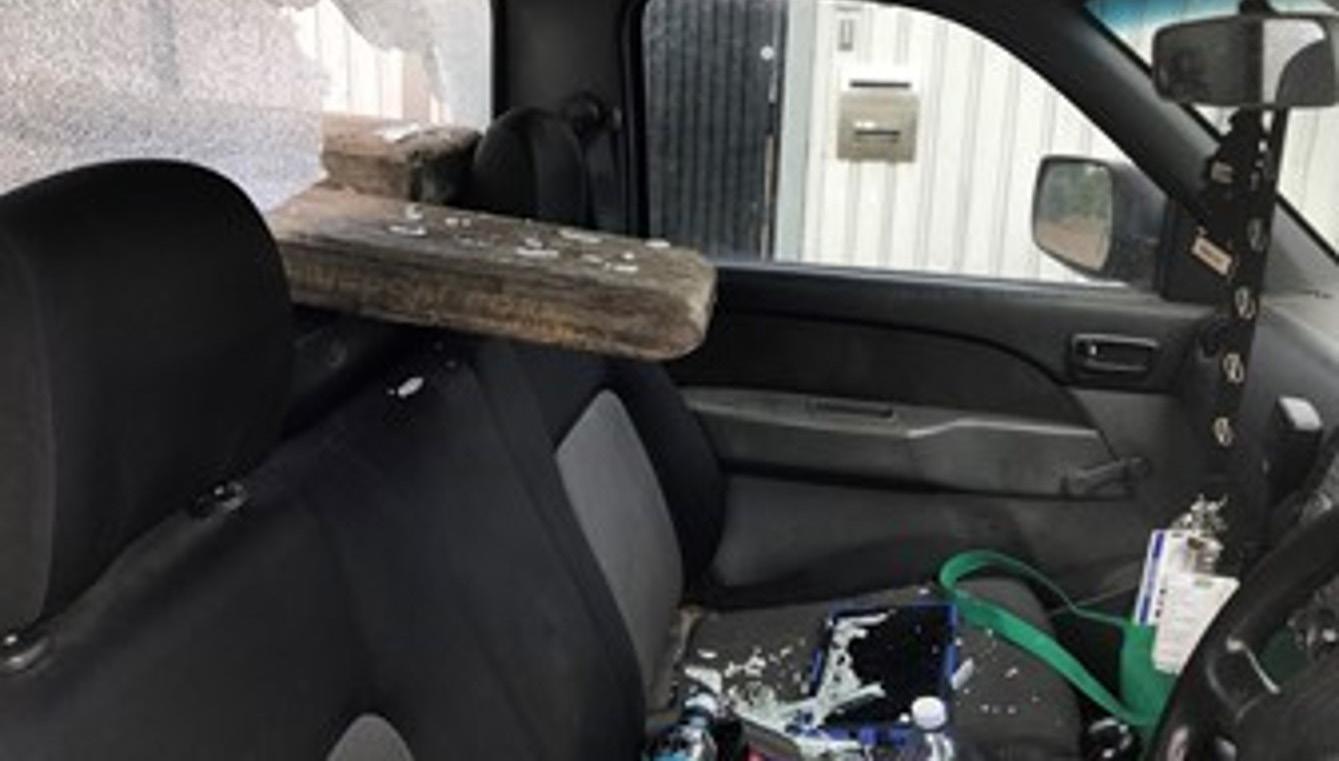
POTENTIAL CAUSE FACTORS
• Load not restrained properly • Load not stacked properly • No protective grill / mesh on back windshield of cab • Stopping too suddenly
CORRECTIVE / PREVENTATIVE ACTIONS:
• Ensure proper load restraint techniques are used and loads are stacked in a proper manner • Ensure all loads are double checked and that the correct form of lashing/ restraints are used
• Install protective grills / mesh or similar to cover cab windows on vehicles • Use of defensive driving techniques to avoid having to break suddenly • Businesses must ensure that safe work practices for load restraint are in place and adhered to
• Businesses to provide additional training to staff on proper load restraint practices
Source: https://cdllife.com/2019/trucker-survives-after-load-of-steel-beams-slams-through-cab/. Internal
DROPPED LOADS
EVENT: MOBILE CRANE DROPS LOAD – STEEL PIPE DATE: 2002 LOCATION: QUEENSLAND
EVENT DETAILS: In 2002 at a job site in Queensland, a mobile crane dropped its load. The crane was used to lift and suspend a 305mm diameter steel pipe vertically in the air so it could be struck with a hammer to remove wet sand that was clogging the inside of the pipe. While the pipe was being struck, the sand came free from the pipe suddenly causing the chain lifting the pipe to come loose and slip off the pipe. Both the crane operator and the worker who was striking the pipe were able to clear the area in time resulting in no injuries, however, the crane sustained minor damage. https://www.rshq.qld.gov.au/safety-notices/mines/mobile-crane-drops-load
EVENT: TOWER CRANE DROPS LOAD OF EXCAVATOR DATE: 2020 LOCATION: HONG KONG
EVENT DETAILS: In October 2020, a tower crane was lifting a large excavator into an elevator shaft of a tunnel development in Hong Kong when an incident occurred. As the tower crane slewed over the top of the shaft, it became apparent the load (the excavator) was poorly rigged and started to slip free. The excavator tilted forward during this movement, as the rigging was set too low around the load causing it to slip out of the slings, flip completely around and then drop down the shaft. There were no injuries, but both the load and the elevator shaft suffered substantial damage. https://vertikal.net/en/news/story/36364/crane-drops-load

POTENTIAL CAUSE FACTORS
• The sand clogged inside the pipe, came out rapidly causing sudden release of about two thirds of the total load of 3t. The sudden release of energy stored in the crane rope and the lifting boom caused the empty pipe to become weightless, bounce upwards and loosen the chain around the pipe. • Instability in the load as the sand was being released. • Instability in the load as the crane slewed due to poor rigging • Centre of gravity of load either not being taken into account or changing during the lift
• The hazard was neither identified nor considered before commencing either of these lifts
CORRECTIVE / PREVENTATIVE ACTIONS:
• A JSA or risk assessment should be conducted by personnel with the appropriate technical and risk management skills before commencing a job/task that is outside the scope of normal lifting operations. • A risk assessment conducted after the incident resulted in a recommendation to cease desanding pipes in this manner. • A lift study should be completed before lifting large, awkwardly shaped loads to account for changes in COG during lifting and slewing • Only qualified and competent personnel should be rigging loads