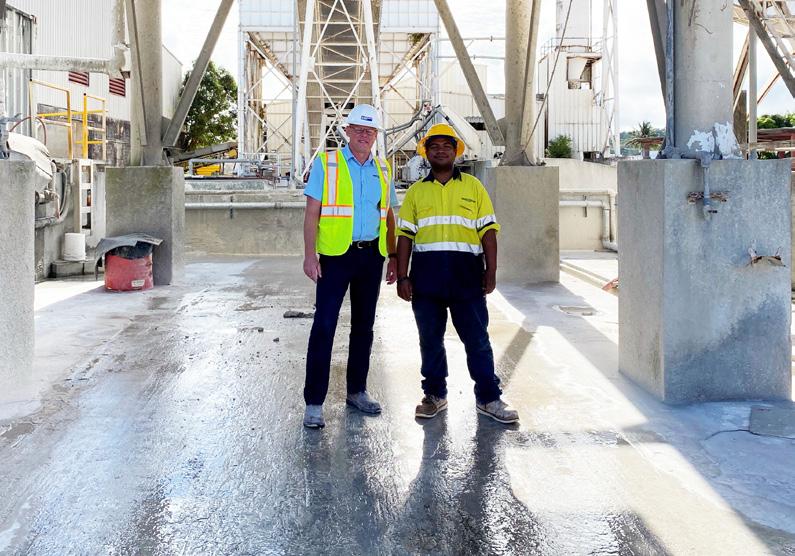
2 minute read
OPERATOR’S OPINION
Rod Hellwig
ROD HELLWIG
Advertisement
CONCRETE DIVISION MANAGER – SMITHBRIDGE GUAM
Rod, pictured left, at the Smithbridge Guam concrete plant.
Rod has recently joined Smithbridge Guam as Concrete Division Manager, bringing with him 20+ years’ experience in business and process improvement roles across a range of manufacturing and service-based industries.
It’s a pleasure to speak with you, Rod. Can you give us a bit of background on yourself?
I have spent the last 20 years working in manufacturing and service-based industries within Australia and overseas. Some of the industries I’ve worked in include engineering plastics, cardboard, plastic bottles, steel, concrete and particleboard manufacture. My main focus has always been people, business and process improvement and I have worked in roles from OHS, logistics and manufacturing manager to customer service, sales and general management. Having 5 years’ experience with Holcim Concrete in Australia with a business improvement focus, I came to Smithbridge Guam to lead the team and build a strong, efficient and well-regarded concrete division within the business. I look forward to the challenges ahead.
What is the most common action or behaviour you witness in the field that leads to high potential incidents or near misses? Any ideas on how we can prevent incidents or near misses in the future?
The most common behaviour is the lack of planning and taking what you do seriously. It is the lack of planning and understanding of the surrounding environment that can (and will) lead to high potential incidents / near misses, or even worse, actual incidents.
We need to take the time to scope, plan, test and then act.
Our industry needs to get better at learning how to say “no” without feeling obligated.
There is no one magic thing that prevents incidents. However, we can train people in planning, processes and thought patterns that will work towards preventing these types of things happening. Spending more time with our people will allow us to truly understand the messages we send about speed and efficiency.
What do you feel is the most important safety issue affecting your particular role in the industry today?
For some reason we still have industries that hold business and profitability over people’s development, safety and training. There is a lack of true mentorship or apprenticeship. For my entire career, one thing has remained true: People trust in those who they respect. We need to bring this core value back to the forefront.
Any final thoughts to share?
I stopped what I was doing today because of the importance of this topic and made sure I spent time to share my experience and concern. We, as leaders, must demonstrate safety, not just talk about it. The trend of blaming complacency for our own shortfalls needs to stop. Just remember, the near miss you walk past could become the next person hurt.
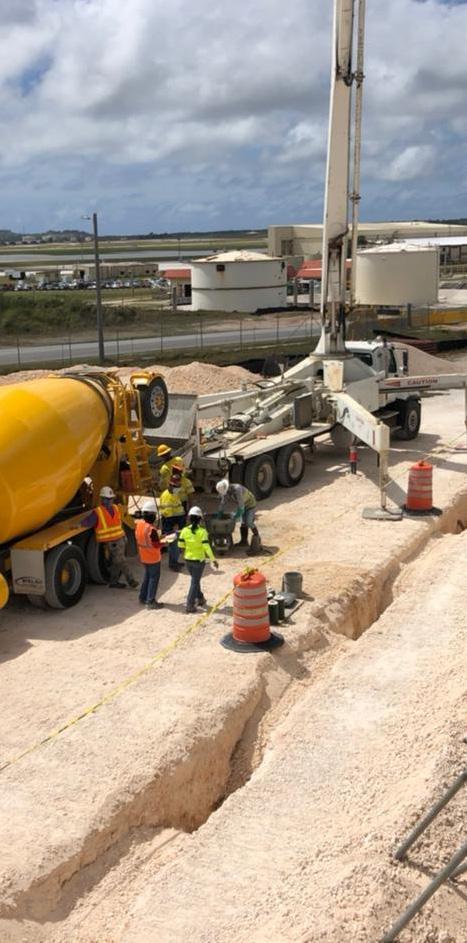