
6 minute read
FEATURE ARTICLE
Driving safety improvements through High Potential Incidents
Article contributed by KEVIN BALL & BETINA DALE – SMITHBRIDGE GROUP
Advertisement
For over 25 years, Smithbridge Group has been known for a commitment to safety across all operations. As an organisation in a high-risk sector, the prevention of incidents and keeping the workforce safe has always been a top priority. For this reason, the Group extended its safety reporting to also focus on the potential of an incident or near miss, rather than just the outcome.
This level of reporting is enabled by Smithbridge Group’s dedicated Safety, Health, Environment and Quality (SHEQ) team, who oversees systems, programs and processes across the global businesses. The team is complimented by locally based SHEQ teams within each business in Australia, New Zealand and Guam.
Defining and Identifying High Potential Incidents (HPI’s)
Through incident reporting and analysis processes, the Smithbridge Group determines the risk its workforce and operations are exposed to when an incident occurs by determining the most appropriate steps to take to reduce risk. This is done by applying a set of control measures consistent with the hierarchy of controls approach, common to risk management processes. As part of this “risk” approach, High Potential Incidents (HPI) are classified where an incident (including near misses) could have resulted in a serious incident if the full potential of the incident was realised. This can occur when
the last line of defence (control) was the only thing that prevented the incident from being more serious, or when it was simply down to luck that nothing more serious occurred.
How HPI’s can drive safety improvements
As Smithbridge has a global reach, it is important the organisation shares the learnings between all locations within the group. Every location within the group has crane hire and specialised transport as integral parts of the business, therefore, the same activities are undertaken throughout the group, just at different locations. Sharing recommendations from incidents that occur in one location with the rest of the group helps Smithbridge prevent the same incident from occurring in the other locations. This is nothing new - lots of businesses with multiple locations do exactly the same thing. However, Smithbridge has a Key Performance Indicator (KPI) for the group of zero repeat HPI’s across the whole group, probably not as common.
How does this work? Universal Cranes Brisbane experienced a HPI last year involving load restraint. Therefore, based on the “no repeat HPI KPI”, the Smithbridge Group as a whole could not have another load restraint incident across the group for that year to achieve the KPI.
Setting a KPI is one thing but maintaining it is another. To help achieve the “zero HPI repeat”, recommendations and actions from the business unit that initially experienced the incident are reviewed at other business unit’s management meetings. The process is by no means foolproof. It does however put the onus on each business unit to actively review HPI findings from all business units, consider the recommendations and key learnings, and adopt the control measures in their workplace. Business Unit’s are encouraged to conduct a gap analysis of existing controls against the recommended controls listed in the report.
The load restraint HPI discussed in the incidents of this Lifting Matters issue led to a number of controls being implemented throughout the Group, including the Universal Cranes Load Restraint Manual.
Load Restraint Manual: Universal Cranes
Reporting on, discussing and rectifying controls for HPI’s lead Universal Cranes to overhaul a critical area of operations, leading to better outcomes for load restraint.
While working as Branch Manager in one of Universal Cranes’ regional depots, Phil Dayman initially had an idea for a safety initiative on Load Restraint as part of his Chain of Responsibility. When he relocated to the Universal Cranes Head Office into an Operations Manager role, Phil developed a Load Restraint Guide. The guide provided a solid foundation for many years but following a string of HPIs, near misses and incidents surrounding load restraints, gaps in load restraint management started to become apparent, even with the Load Restraint Guide in place. The initial Load Restraint Guide released in 2018 was lengthy and very detailed, making it not very user friendly and therefore unused by many in the business. The Guide was therefore again brought to the attention of the SHEQ team.
INCORRECT
coaming rail
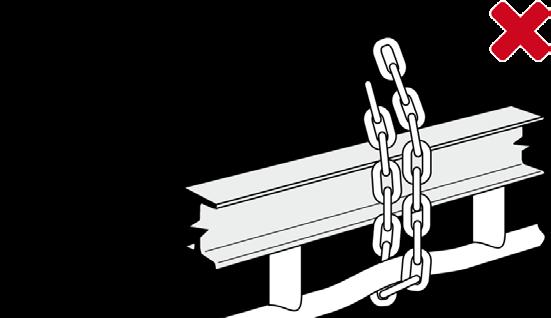
rope rail coaming rail
rope rail
CORRECT
Original source: National Transport Commission Australia, Load Restraint Guide 2018
It was identified the load restraint incidents involved loads quite specific to crane hire and transporting of cranes, either whole or in pieces, complete with their support components like timber pads, mats and wedges, counterweights and boom sections etc. From a recent HPI investigation it was determined Smithbridge needed to develop an internal load restraint manual to cater for the specific loads carried by the business on a regular basis.
Universal Cranes SHEQ Coordinator Julian Carmichael and Smithbridge Group Manager – Safety & Systems Kevin Ball took on the task to work together to revitalise, update and condense the information from the original guide to form a new Load Restraint Manual. The manual is a short and concise 13-page document which details:
•Lashings – placement, type and quantity to be used
•Load restraint requirements (i.e. force required) – downforce principals and angles
•Load restraint methods – specific to different load types • Specific restraint techniques, methods and lashings required for different types of plant and equipment
•Load restraint types – when to use or not use chains, straps and tensioners
The Load Restraint Manual also provides images depicting best practice methods against clearly identified improper practice images. These images provide a clear and easily identifiable visual guide to the do’s and don’ts of proper practice and methods.
The latest version was individually branded and incorporated into the Australian, Guam and New Zealand document management systems. It was so well received it began a wider dissemination journey across the Group. The Manual has now been:
•Adopted as a best practice policy for operations among the Group globally
•Excerpts regularly presented as part of weekly Safety Meetings
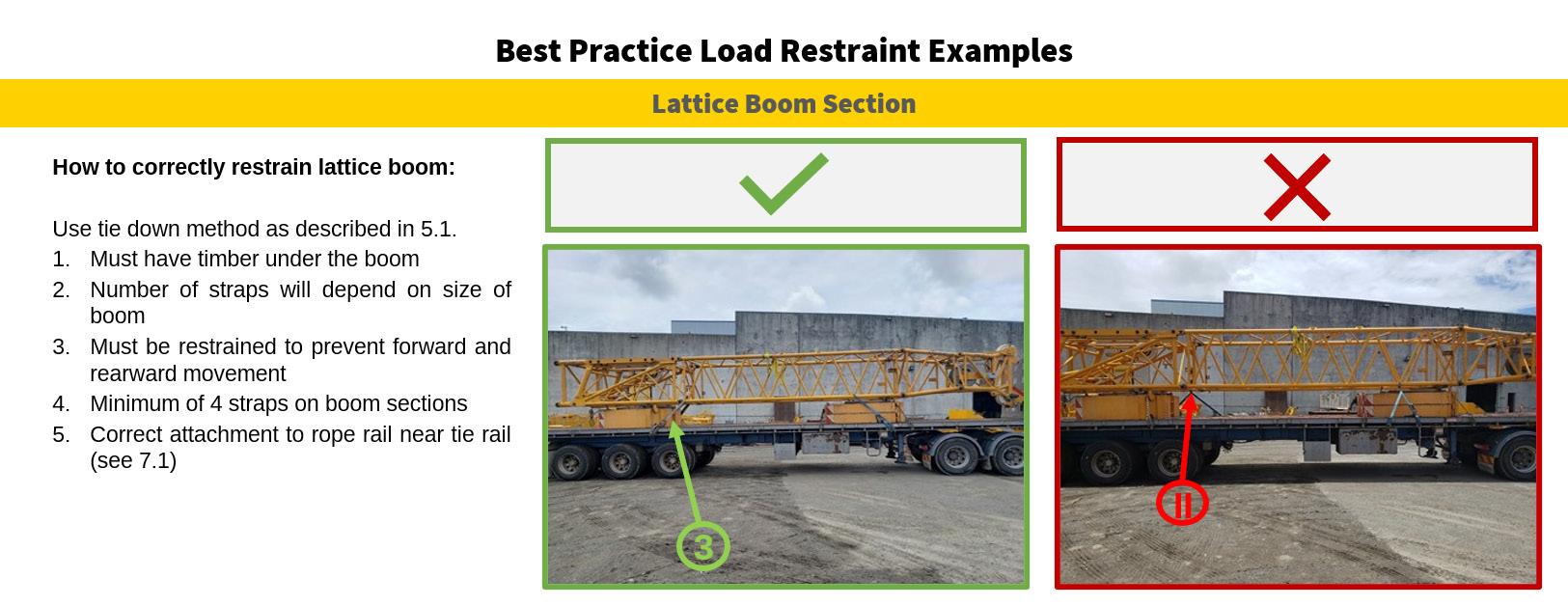
•An online training module is in development with the content
•Used as a best practice guide for Benchmark, KPIs and regular auditing to ensure compliance
•Load restraint types – when to use or not use chains, straps and tensioners
Another example of where a focus on HPIs has enabled the group to make significant improvements to operations is the Dismantle Instruction Guide for a large mobile crane. After an incident in which a specific crane was dismantled incorrectly resulting in minor plant damage, the error was identified a precursor to a potentially catastrophic incident that thankfully never happened.
To mitigate the risks, a team comprised of the Maintenance Manager, SHEQ team, Chief Executive Officer, crane operators and other staff came together to develop an instruction guide. This guide provided step by step instructions including excerpts from the crane user guide and written directives from the operators. This was presented alongside images showing best practice versions of the crane configured in various states of dismantle. After review and approval in Auckland Cranes, the Instruction Guide was then presented to the groupwide global safety committee. Well received, the guide was then rolled out for distribution across the group and has now become a permanent addition to the procedures of that crane.
HPIs – report, discuss, act
Smithbridge Group provides an excellent example of good practice in managing, monitoring and reporting on HPI’s in a high-risk industry. Reporting, investigating and acting on learnings from HPI’s and incidents allows an organisation to change its focus from being reactive, to responding to incidents proactively by examining precursors or the conditions that may lead to events.