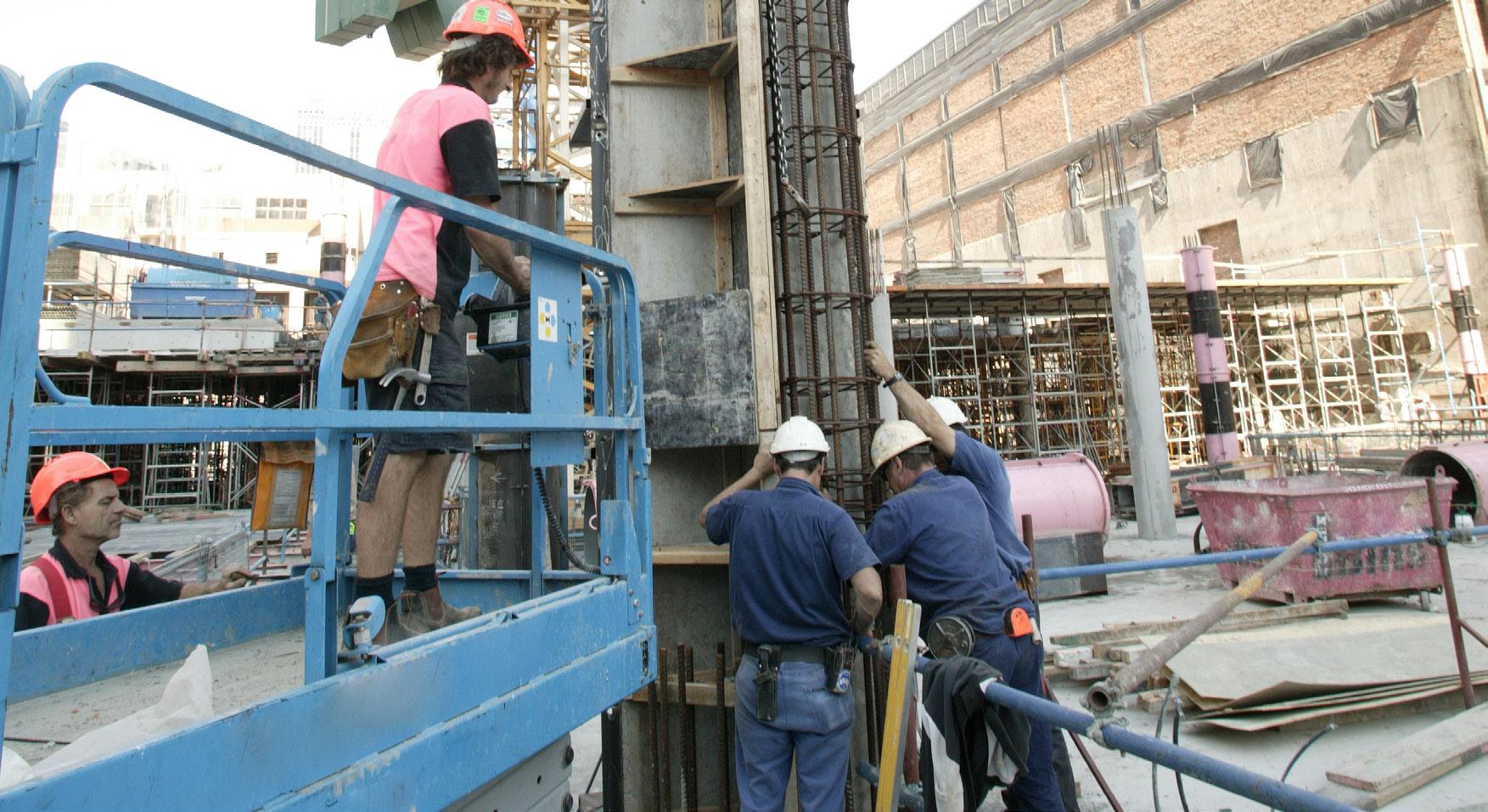
4 minute read
SPOTLIGHT ON
An example of good practice
Advertisement
By Workplace Health and Safety Queensland
The construction division of Workplace Health and Safety Queensland puts a spotlight on safety in cranes and lifting equipment this issue. This article takes a deeper dive into the cause of incidents and discusses safe methods and practices to prevent future HPI's from occurring.
Incidents involving cranes and lifting equipment not only expose the crane crew to a risk of injury, but also have the potential to expose other workers on site and members of the public to being struck by falling objects and overturning cranes.
There have in fact been numerous incidents at Queensland workplaces this year involving cranes and lifting equipment that had the potential to cause serious injury to workers.
The cause of these incidents can be broken into five broad categories:
•failure due to incorrect slinging and rigging techniques
•loose objects falling from loads being lifted
•loads colliding with adjacent structures or plant causing items to dislodge and fall
•cranes not being used in accordance with the manufacturer’s instructions
•incorrect crane selection and siting - for example cranes selected for the task that are not suitable or do not have the capacity for the required lifts.
Shock loads placed on cranes due to lifting incidents also have the potential to cause catastrophic failure of the crane. To manage the risks arising from these types of incidents consider the following measures.
Rigging and slinging techniques
Right from the start, workers should be appropriately trained and verified as competent to perform the tasks, and it is vital that the crane is rigged in accordance with the manufacturer’s instructions, with rope keeper bars fitted correctly. Where practicable, utilise engineered lifting points.
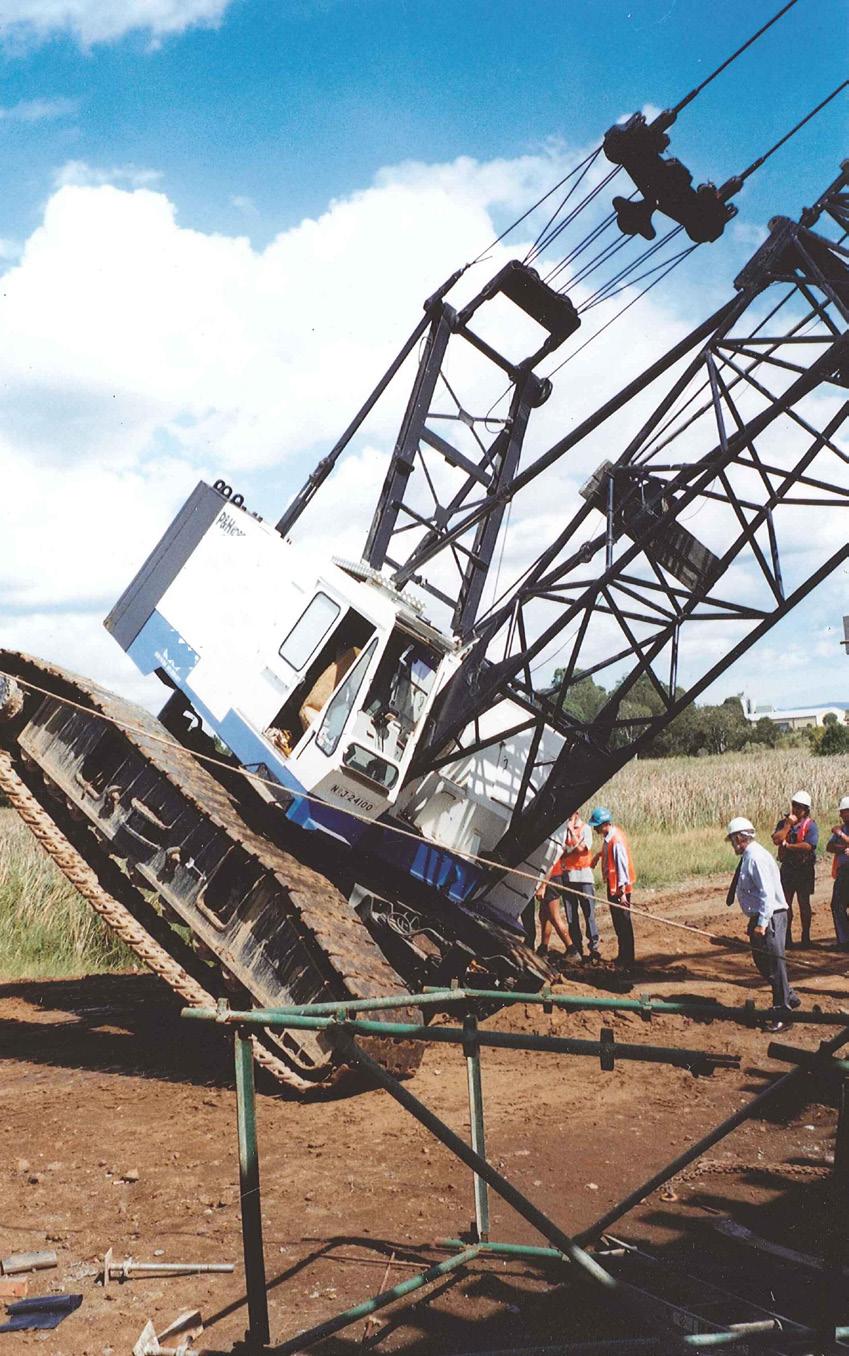
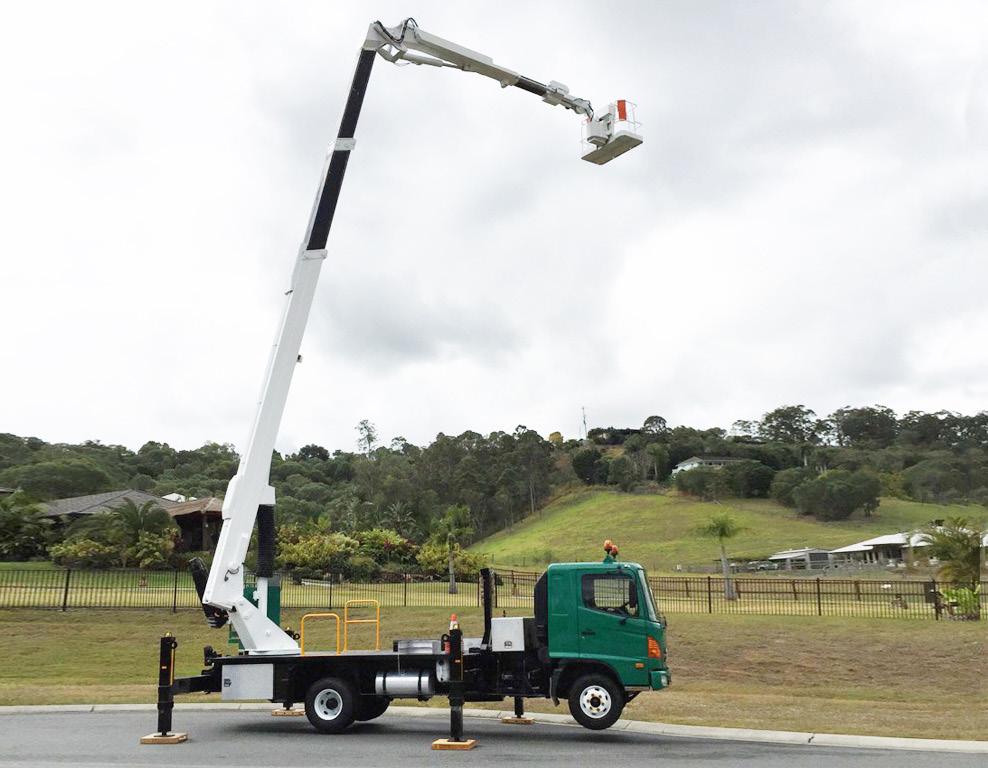
These measures should be complemented by:
•selecting the right lifting equipment, considering the potential for the lifting equipment to slip on the load, ensuring chains/slings have sufficient
WLL for the load. And, when lifting with synthetic slings, use sling protection on the corners of the load unless lifting round pipe. • following guides provided by the designer, manufacturer or supplier and consulting with workers, with pre-start meetings discussing proposed safe methods. • ensuring that the doggers/riggers in control of the load are positioned safely outside of the zone where they could be struck in case of a lifting equipment failure – and implementing exclusion zones to ensure workers not directly involved in the operations are outside the lifting area and made aware of the lifting operations. • ensuring that all lifting equipment is inspected prior to use and is up to date at intervals as specified by the manufacturer. This is outlined in the
Tower Crane Code of Practice 2017 and
Mobile Crane Code of Practice 2006.
Loose objects falling from loads
From the outset, ensure a safe system of work is in place to conduct, inspect and remove all loose items from loads prior to lifting (for example loose z-bar nuts on
formwork shutters, items above the fill line of a skip bin) and do not overfill bins or lifting boxes while avoiding items that may protrude or overhang from the bin or lifting box.
Other measures include:
•Where possible, cover bins and lifting boxes to minimise the risk of loose objects being ejected during lifting.
•Do not rely on plastic wrapping or similar methods to retain objects being lifted in bulk. Loose items should always be captive inside a lifting box/cradle or should be strapped with form ply.
Loads colliding with adjacent structures or plant
Before work begins, design the workplace layout to locate storage and delivery areas away from structures like perimeter scaffolding, so that loads can be lifted free of obstructions. Remember too to use tag lines to stabilise loads where required and monitor wind conditions and only lift when safe to do so.
A vital preventative measure is to ensure that the dogger or rigger has clear sight of the load and can direct the crane operator as needed. Also, mobile plant equipment like concrete placing booms should be well away from the crane or the lifting operations - and if other plant equipment that could collide with the crane or the load is operating on site, develop a safe system of work to manage the interaction.
Cranes not being used in accordance with the manufacturer’s instructions
A basic pre-requisite for safe work of this nature is that all operators have the appropriate high-risk work licence for the type of crane and that familiarisation training has been conducted for the specific make and model of crane.
Procedures also need to be in place to follow the manufacturer’s instructions for use of the crane, particularly during setup and shutdown procedures (including erection and dismantling procedures for self-erecting tower cranes).
Crane selection and siting
Before work begins, ensure the right capacity crane is selected for the lifts to prevent the plant from overturning and at all times focus on the heaviest loads and maximum lift radius.
Consultation should occur to verify the safest site location for the crane to be assembled, with ground conditions assessed and deemed suitable for the crane and load types. The crane operator should also request verification that the ground conditions are suitable.
The above information has been sourced from Workplace Health and Safety Queensland’s construction division. For further guidance refer to the Tower Crane Code of Practice 2017 and Mobile Crane Code of Practice 2006.