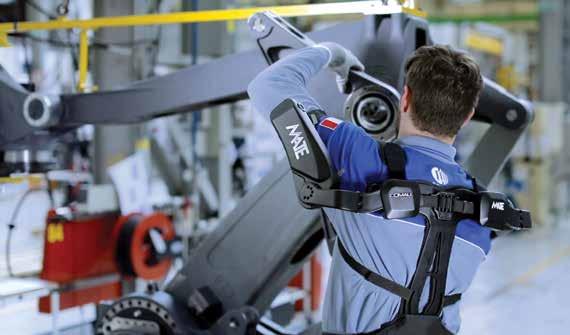
11 minute read
Italian Robotics Enable True Speed and Efficiency
Comau’s MATE is a robotic innovation you wear. Courtesy Comau.
Italian Robotics Enable
Advertisement
By Thomas R. Kurfess PhD, FSME, PE 2018 SME President True Speed and Efficiency W hen Ingersoll International was all but defunct 15 years ago, Tino Oldani saw enough potential in its machine tools division to take a chance on breathing new life into a company that was founded during the Industrial Revolution. He was so convinced, he persuaded the Camozzi Group SpA (Brescia, Italy; www.camozzigroup.com) to invest in Ingersoll Machine Tools, which had been part of one of the biggest companies in Rockford, IL.
“I knew about them, and I knew they had problems, and at a certain point had filed for bankruptcy,” said Oldani, who owned a much smaller engineering company in the same city that competed with Ingersoll. “So, we put together the idea to take over (while keeping the old name).”
Oldani, an engineer by training who’s been Ingersoll’s president and CEO ever since, has taken the company to new levels of success. Under his leadership, Ingersoll makes automated fiber placement machines and integrates them with robots to fabricate composite structures for aerospace. The company has also ventured into making 3D printers for big-area additive manufacturing, along with machinery for the wind power, defense, mining and primary metals processing industries. In 2014, Ingersoll engineered and built the base for the world’s largest solar telescope in its 500,000-square-foot facility.
Ingersoll Machine Tools most recent yearly revenue was $70 million.
“They make massive machines that no other company can make,” said Alex Gary, who was assistant business editor of the Rockford Register Star newspaper at the time of Camozzi’s acquisition of Ingersoll’s machine tool operations, the largest of its three divisions. While Ingersoll International had 4,500 employees in the U.S. and Europe in its heyday, the machine tool division alone now employs about 180 people. 1 in 4 packaging machines worldwide “Made in Italy” SIPA SpA (Vittorio Veneto, Italy; www.sipasolutions.com), a company founded to provide integrated systems for flexible automation, has almost 40 years of experience with making machinery for polyethylene terephthalate (PET) and all other bottle manufacturing and filling technologies. It sells machines to the food/beverage, chemical, detergent and health/beauty aids industries, according to its website. In addition to machinery, SIPA offers life-cycle services that can include data acquisition, line analysis, maintenance management, training and more.
Fluid Forms, Inc. (Colton, CA), recently installed a SIPA XFORM 350 for PET preform injection molding machine to serve its water, food products and carbonated, flavored and alcoholic beverages clients, according to an article in SIPA’s magazine.
Fluid Forms uses its XFORM 350 to make preforms for a 1.75-liter (1.8 qt) margarita mixer bottle and a 12-ounce (0.35 liter) high-pressure processing (low-temperature pasteurization) bottles with an impressive output of tens of thousands of preforms per hour. The company is working with SIPA on making 70-78 gm (2.5-2.75 oz) preforms for its growing liquor bottle business.
In Mexico, the major beverage company GEPP installed a new carbonated beverages bottle blowing and filling line based on a SIPA SFR16 EVO 3 rotary unit in a Sincro Bloc with a 144-valve filling unit at its plant in Celaya. The line also includes SIPA’s Fastlayer robotic system for palletizing. The line produces 17,500 3-liter (0.79 gal) bottles per hour, and 28,000 1.5-liter (0.4 gal) bottles in the same amount of time.
GEPP, which is partly owned by PepsiCo and the exclusive bottler of the company’s beverages in Mexico, already has SIPA bottle-producing units, filling systems and molds in several of its other facilities. SIPA’s machinery is also used to make bottles for non-food industries. Howard Packaging (Corydon, IN) installed a SIPA ECS SP 80 injection-stretch blow-molding machine to switch from PVC bottles to 16-64 oz. (0.47-1.89 L) PET bottles for engine oil, according to a case study on SIPA’s website.
“Our customers see PET as more earth-friendly than some alternative materials, and PET certainly provides a healthier working environment for our operatives than PVC,” said Steve Hawkins, Howard’s maintenance purchasing manager. “Plus, the PET bottles are lighter than versions in PVC, so we save on material. But they still look much better and give far superior results in drop tests—which is particularly important for oil bottles.”
Hawkins also likes SIPA’s local presence, technical support and quick turnaround time on any mold repairs due to the manufacturer’s mold repair and renovation operations in Atlanta.
PET bottles, like the ones Howard Packaging makes with SIPA’s machines, are earth-friendly, indeed.
In Mexico, PetStar, a Coca-Cola-acquired company that operates one of the largest PET recycling plants in the world, has been awarded the Mexican Quality Prize. The Institute of Entrepreneurial Development, which focuses on promoting high-quality standards in the private sector, administers that prize.
The company recycles 100 million PET bottles yearly and converts them into resins to produce new bottles.
Acquired by Coca-Cola Mexico in 2014, according to a Recycling Today aricle, the PetStar facility can process up to 65,000 tons of PET bottles per year. The figure represents a doubling of the facility’s capacity in Toluca, Mexico.
SIPA and more than 100 other companies belong to UCIMA, the Italian Packaging Machinery Manufacturers’ Association (www.ucima.it). UCIMA member companies cover the entire range of packaging machinery production, from the food, confectionery and tobacco industries to pharmaceuticals, chemicals, petrochemicals, cosmetics and end-of-line technologies.
In addition, UCIMA members represent 70% of the total Italian production in its sector and, on average, 80% of Italian exports (with growth of 5.8% in 2016 compared with 2015, representing 5.3 billion Euros [$6.2 billion]). One packaging machine out of every four in the world bears the wording “Made in Italy.” And the U.S. is the industry’s main market for the sector.
In North America, companies have come to value and appreciate the Italian custom-made solutions, which have given them the best quality, flexibility and innovation found anywhere. The major industries that buy Italian machinery are the food and beverage industry (40%), the pharmaceutical/cosmetics/toiletries industry (about 20%) and the chemical/petrochemical field (about 10%).
The latest robotic innovation is one you wear Comau SpA (Torino, Italy; www.comau.com), manufacturer of industrial robots and other automation solutions, recently added a wearable robot to its product lineup.
Comau’s MATE, the wearable, upper-limb robotics exoskeleton, is designed to reduce muscle fatigue and assist the wearer with industrial tasks, such as assembling, packaging, storing and materials handling, along with other jobs whose movements require repeated flexion and extension of the shoulder(s). Activation of some of the muscles in the wearer’s scapular-shoulder area is reduced by half, and due to its patented kinematic mechanism, MATE guarantees all the degrees of movement of the shoulder.
“By decreasing muscle fatigue with MATE, workers have a better quality of work life and the quality of their work can improve,” Martin Kinsella, director at Comau in Southfield, MI, said during a presentation at the Italian Trade Agency’s Innovation Days 2018 in Sterling Heights, MI. MATE is powered by mechanical, pre-tensioned springs located in the torque generator box. The springs provide a torque that reproduces the same physiological curve of the upper-limb flexionextension movement and can be adjusted to give more or less assistance. The power system is engineered to be constant over time. MATE’s compact size and mobility make it different from competitive products, because combining all of its features is difficult. To follow the natural movements of the shoulder, other exoskeletons are generally bulkier. Additionally, MATE is available in a range of sizes to accommodate North American women from size 0-16 (European size 36-52) and men from size 34-50 (European size 44-60), and is adjustable for a custom fit.
“The most challenging point, from a design point of view, was to ensure the functionality of the device in very limited dimensions and with the lightest weight possible, since these were two of the most important requirements to guarantee comfort for the wearer,” Kinsella said.
Development of this novel exoskeleton took about two years, with five different prototypes undergoing testing in the laboratory and in realworld situations. During testing, developers collected feedback regarding the functionality and usability of the device from the end-users. They then integrated that feedback into the final version of the device.
Comau collaborated with IUVO, a spinoff company of the BioRobotics Institute of the Sant’Anna School of Advanced Studies (Pisa, Italy), and Össur (Reykjanik, Iceland), a leader in non-invasive orthopedic devices. In addition to robotics, Comau, part of FCA Group (London, U.K.; www.fcagroup.com), specializes in producing advanced industrial automated solutions that include products, technologies and services to help manufacturers of all sizes increase operational efficiency while lowering operating costs and optimizing returns. It has more than 70 years of experience in the NAFTA countries, with a U.S. headquarters that includes an engineering and innovation center, in Southfield, MI. Comau’s North American presence also includes six manufacturing plants in Southeast Michigan and one in Mexico.
“Italian creativity, a strong engineering mindset and a constant drive for innovation has enabled Comau to become a global leader in the automation industry,” said Kinsella.
Also experienced in designing and configuring robotic automated lines is Salvagnini SpA (Sarego, Italy; www.salvagnini.it), a manufacturer of machines that process sheet metal. Salvagnini’s panel benders (P1, P2Lean and P4Lean), press brakes (B3), punches (S4), fiber-laser punches (SL4) and fiber lasers (L3 and L5) are configured for clients in the HVAC, transportation, furniture, medical equipment and refrigeration industries, and more.
“There are endless variations we can define for our customers, depending on what their needs are,” said Steve Spilak, sales manager for Salvagnini Canada, which was established in 2013. “We perform time studies and usually go through, easily, 12 configurations until we’re certain the customer has what he needs.”
Salvagnini was founded in 1963 and established a presence in the U.S. in 1984. It’s been in Mexico since 2008.
The company is also a leader in Industry 4.0: “Our machines communicate with each other, from the simplest press brake to a complete flexible manufacturing system line,” Spilak said.
Salvagnini’s advanced machinery employs robotics, such as in its RoboFormer and FlexCell, which offers the features of a panel bender and a press brake to let customers get the most out of bending. It’s also vertically integrated, making all components of its machines except for the laser source, dust collection system and robotic arm.
Automation ‘now a given’
In addition to Comau and Salvagnini, other Italian manufacturers have gone in wholeheartedly for automation, too. A recent estimate by Accenture found that 82% of Italian entrepreneurs firmly believe that automation is critical to radically transforming the Italian manufacturing landscape.
The Italian government helps with incentives.
The advanced manufacturing technologies with the best chance of success in Italy fall within the scope of the Italian national government’s advanced manufacturing plan, “Piano Nazionale Industria 4.0.” Among the main features of the plan are tax breaks for the purchase of capital goods, with higher incentives for the acquisition of machinery containing sensors or data transmission software.
Some of the technologies and capabilities eligible for incentives include: Autonomous, cooperating industrial robots with numerous integrated sensors and standardized interfaces; optimization based on real-time data from intelligent systems; a fully automated value chain; Industrial Internet of Things; and cybersecurity.
This plan is among those developed by large European manufacturing countries and is considered by many to be the most advanced and comprehensive. The plan consists of $15 billion in tax breaks for investments by Italian companies by the middle of 2018, to reach $22.6 billion with additional resources by 2020. This strategy is aimed at triggering private investments worth $26.5 billion.
Manufacturers in the Mediterranean country have a long history of automation.
“Starting in the 1960s with the advent of the first numerical controls, the ‘Made in Italy’ machine tool manufacturers have adapted to make their products automation-ready, while also adopting automated processes for their products’ design and fabrication,” said Massimo Carboniero, president of UCIMU-SISTEMI PER PRODURRE - Association of Italian Manufacturers of Machine Tools, Robots, Automation Systems and Ancillary Products (www.ucimu.it). “Automation is now a given.”
Carboniero said UCIMU members have developed the “hardware” necessary for automation, such as devices (sensors, actuators, etc.) that are cheaper, less cumbersome and help increase processing capacity. They also write the software that allows manufacturers to collect and process a large quantity of information—leading to increasingly sophisticated functions of monitoring, control and optimization of processes, and an increase in the quality of processes and products. Worldwide, the industrial robotics market grew by 29% in 2017 over 2016, with 380,550 new robots installed, Bob Doyle, vice president of the Association for Advancing Automation (Ann Arbor, MI) told the audience at the Italian Trade Agency’s Innovation Days 2018.
“Most of what they do is in handling and welding operations,” Doyle said. “The food and beverage industry (like SIPA) is a growing area for robotics.”
The NAFTA countries represent big opportunities for Italian and other manufacturers of robotic arms, cobots, and even Comau’s wearable robotic innovation: The U.S. is the world’s fourth largest market, and Mexico is ninth, according to Doyle’s figures.
The adoption of automation isn’t the only thing that’s changed for Italian machine tools, robots and automation manufacturers. Like Camozzi, Comau and SIPA have, the most successful firms realize manufacturing can be global—and to compete globally, they must invest in a presence in the countries that are their marketing targets.