
14 minute read
Automation: Getting to the Core of Core Materials
Part of an automated Moretto PET processing plant.
Getting to the Core of CORE MATERIALS
Advertisement
When it comes to high-volume products that cry out for automation, you can hardly find a better example than automotive windshields, side windows, sunroofs and LCD back lights. And TYROLIT VINCENT Srl (Thiene, Italy, www.tyrolit.at/en/) is a leading manufacturer of diamond tools for just such applications. TYROLIT VINCENT belongs to GIMAV, the association of Italian manufacturers and suppliers of machinery, equipment and special products for glass processing (www.gimav.it/en/), and all projects of its Glass Division are developed in Italy by the R&D department and carefully followed by the technical and marketing team all over the world.
One such milestone in the automotive glass industry are TYROLIT high-quality diamond pencil wheels for grinding automotive glass at 40 m/min (1,574 IPM). Another more recent development is the “single use” HALO profile wheel. Conventional wheels used for this application must be re-profiled when worn, changing their diameter and forcing the production staff to ship wheels back to the manufacturer, await their return and return them to stock. Not to mention having to track the number of re-profiles, which is usually limited to four cycles. The HALO is designed as a cost-effective “disposable wheel” that can be discarded after use. Because all HALO wheels have the same outer diameter, the operator doesn’t need to adjust for changes in diameter, which contributes to easier setup and automation. And because a worn wheel is simply discarded, the user is spared the logistical challenge of managing re-profiles.
TYROLIT also provides a wide range of single-piece drills and adjustable-countersink drills for the automotive glass industry. They are specially designed and manufactured to guarantee the best hole
A single use auto glass grinding wheel from TYROLIT HALO simplifies setup and logistics.
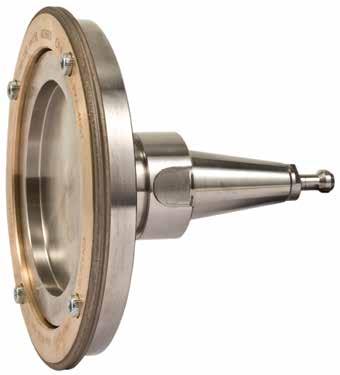
quality at high feed rates of 150 mm/min (5.9 IPM). The sintered diamond drills are manufactured using specific bonds to yield consistent performance over an extended period.
TYROLIT is also a key supplier of dressing sticks for the latest generation grinding wheels and diamond drilling tools. They strike the perfect balance between granularity and hardness. New bonds reduce the frequency of dressing and increase the number of pieces processed per cycle.
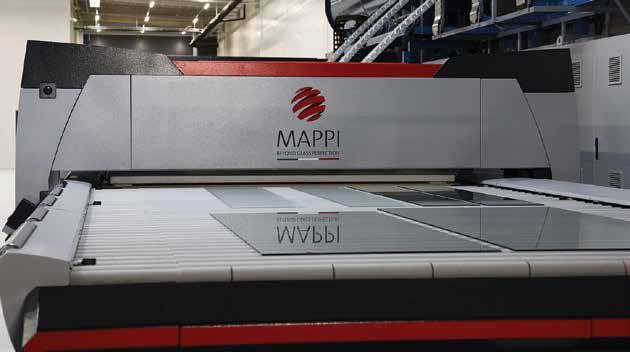
What’s more, TYROLIT has expanded its presence in the U.S. market with a new production and support facility just outside Chicago. The Oswego, IL, site boasts a well-stocked warehouse and a skilled service center for rapid technical assistance and re-profiling, plus shorter delivery times for new products.
Furnace automation for the glass industry
Headquartered in Cisterna di Latina, Italy and with U.S. offices in Naples, FL, Mappi International Srl (Cisterna di Latina, Italy, www.mappi.it) is another GIMAV member helping automate glass making in North America. In Mappi’s case it’s by providing high-tech tempering furnaces, an investment that impacts all other processes in a glass-producing company.
Mappi is able to shorten installation time because the main part of the machine, the heating chamber, comes in a single, preassembled piece and does not require assembly on site. From there, the user enjoys the automation that is the real focus of a Mappi furnace, including an energy-saving, self-optimizing heating system that manages each thermal zone individually through computer control. The complex algorithms behind this feature are made simple to the operator with a friendly human interface.
The computerized system coordinates the heating and forced ventilation to significantly reduce the peak power required by the entire system. It also balances between heating and quench areas to minimize overall peak. In addition, the internal temperature of the furnace is controlled to within 1°C, preventing overheating of the ceramic rollers, as well as avoiding downtime due to delays and waiting for the furnace to reach desired temperature.
A glass sheet emerges from a Mappi tempering furnace.
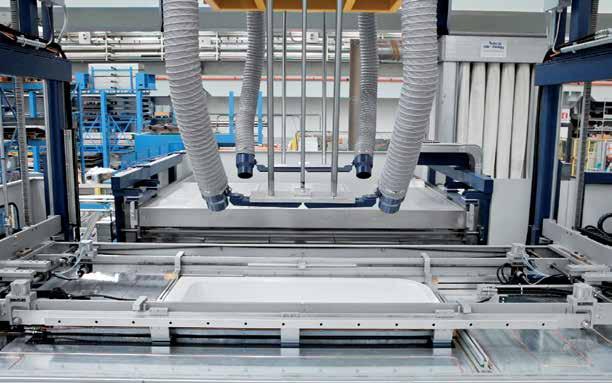
CMS thermoforming machines cool the workpiece with an air flow that’s fully automated and machine controlled.
Every heating element is equipped with an independently managed thermocouple, and the furnace has multiple finely controlled heating zones. And because the system automatically manages the temperature of the furnace through a network of electronically controlled sensors, it can limit its constant and focused heat to areas where glass is present, ensuring thermal and energy efficiency.
Mappi furnaces also have “advanced cooling,” an original design for the blowing system that allows for even more precise control while tempering. This substantially decreases the iridescence of the glass. DC motors drive ceramic rolls with a positional accuracy of 0.001 and use a friction transmission that virtually eliminates gear lash, thereby minimizing any risk of marring the glass. The system also automatically controls the oscillation of the rolls to avoid distortions and damage to the surface of the glass.
A newer innovation from Mappi is its patented GHBS Xtreme Profile Convection System, which enables the processing of all coated glass, including LowE glass with 0.01 emissivity. Sophisticated control and an elaborate array of sensors modulate the intensity of the pressured air in every zone inside the chamber, improving glass quality. The new technology also increases the maximum dimensions of temperable sheets, reduces cycle times and increases productivity.
Mappi prides itself on exceptional customer care: people at your service who understand and are truly committed to MCQ (Mappi Constant Quality). It’s no wonder that in its 25 years Mappi has installed 400 furnaces in more than 50 countries.
Fully automated plastic thermoforming
In the plastics arena, a different set of Italian companies offers a similarly fantastico set of benefits. CMS SpA (Zogno, Italy, www. cmsna.com) point to its BR/5 series sheet thermoforming machines, which enable a single, unskilled operator to run the machine and change production from one mold to another in just a few minutes. The machines can also be equipped with a fully automatic loading/ unloading system, as was the case with an installation at TeucoGuzzini Industrial Group (Montelupone-Recanati, Italy).
Teuco achieved leadership in the field of whirlpool baths by revolutionizing tub manufacturing through the use of acrylics. But its traditional vacuum thermoforming techniques, based on the use of diathermal oil, required bringing oil to the right temperature and maintaining it in operating condition even when the company wasn’t producing anything. Teuco also felt the urgency to use more innovative machinery to comply with contemporary design requirements, especially in improving the thermoforming results in bathtub and shower tray edges. And it wanted to optimize production times by speeding up loading and unloading rates. The answer was a BR5S. Formed workpieces are ejected from the front loader carriage through a motorized vertical unloading system. For negative workpieces, a special width-adjustable support is provided. Digitally controlled servomotors establish the dimensions of the clamping frame and the reduction plate for quick and accurate machine setup change. An extractable mold carrier plate and an automatic plate coupling
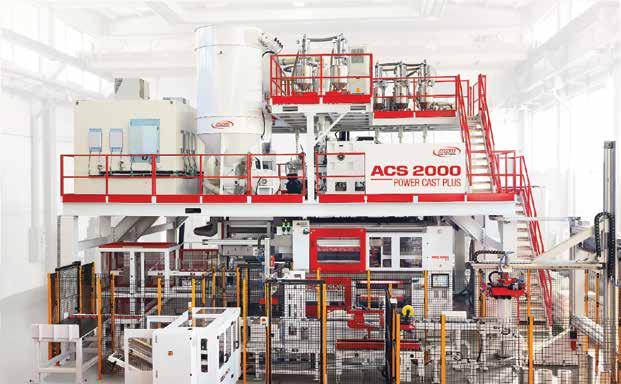
The AMUT ACS 200 can automatically pack and palletize hand, machine, and jumbo rolls of stretch film.
system enable tooling the machine for a new production cycle quickly, safely and handily. The loading station has single-sheet aligning and centering devices to ensure correct positioning in the thermoforming area. Automated fans generate a controlled airflow to cool finished workpieces. And software developed by CMS is both easy to use and comprehensive in its control: It sets the machining parameters, monitors the operation in real time, generates a “history file” and ,if needed, communicates with on-line computing devices and networks.
The machine and its software also enable the processing of unusual and customized products. And the sheets can be made from a variety of materials, to include PC/Polycarbonate, ABS, PE/ Polyethylene, and PP/Polypropylene. In total, the CMS sheet vacuum thermoforming process delivers an aesthetically excellent product that requires no additional machining.
Smart, automated packaging
AMUT Group SpA (Novara, Italy, www.amutgroup.com) also makes thermoforming machines, plus extrusion, packaging film, recycling, flexo printing and converting technology.
One new addition to its line is a packaging system for stretch film rolls. Model 1 can form boxes, fill them with hand rolls of film, close them and put them on a pallet. For machine and jumbo rolls, it can store them on a pallet and insert carton layers in between. In either case, the operator would handle the empty and finished pallets.
Model 2 is the same with regard to packaging the rolls but can also automatically handle and store up to 10 full pallets with a roller
1-888-italtrade conveyor. AMUT’s North American office is in Ontario, Canada. Like CMS, AMUT is a member of AMAPLAST, the Italian plastics and rubber processing machinery and moulds manufacturers’ association (www.amaplast.org/en/).
PET producers cut resin drying energy use in half Moretto SpA (Massanzago, Italy, www.moretto.com), another AMAPLAST member, makes energy-efficient products for the plastics industry. Its latest advance in the injection molding of polyethylene terephthalate (PET) preforms is the EUREKA PLUS resin-drying system. Designed to continuously reduce energy use and improve drying performance, the system immediately grabbed the interest of PET processors, who know every aspect of energy efficiency can make the difference in profitability. Moretto says processors that have adopted EUREKA PLUS drying systems enjoy, on average, a 56% reduction in energy use compared with conventional drying systems.
EUREKA PLUS is comprised of four Moretto-patented technologies: a high performance, resin drying system with an ultra-low dew point; a dynamic airflow management system; drying hoppers with superior mass flow drying characteristics, and a “revolutionary” device that measures polymer residual moisture in-line and adapts the drying system operations. The systems provide processors with a modular, self-adjusting, energy-saving dehumidification system for simultaneously drying plastic pellets and/or regrinds in multiple hoppers.
Each desiccant dryer in the modular dehumidifying system uses an exclusive zeolite desiccant to deliver consistent dew points to -85°F
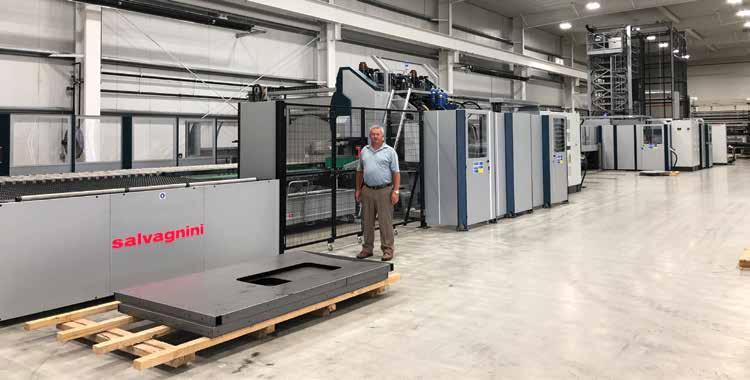
Uni-Fab’s Abe Fehr and his fully automated Salvagnini sheet metal fabrication line.
(-65°C) for uncompromising drying performance. Neither cooling water nor compressed air is required. Strong turbo-compressor blowers provide consistent-but-adaptive airflow to compensate for off-line dryers receiving maintenance or in regeneration.
The airflow management system eliminates traditional valves and automatically delivers optimum airflow to each hopper, based on the hopper size and user input about the material and throughput requirements. The system also ensures the lowest possible energy use (since excess airflow is eliminated) and eliminates the undesirable stress on resin often caused by over-drying, even in reduced or stopped production circumstances, protecting the intrinsic viscosity of the resin.
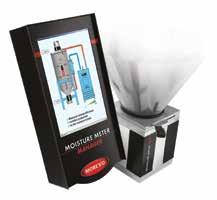
A Moisture Meter Box under the resin drying hopper ensures that dehumidification is successful in Moretto’s efficient EUREKA PLUS.
The advanced drying hopper provides an optimized mass flow of materials for highly predictable resin drying. Each pellet is uniformly exposed to drying air and achieves full residence time in the hopper even though the hopper size is smaller than competing designs, resulting in space savings and energy reduction.
Each hopper is equipped with a convenient control that provides a readout of the temperature and operating status. The control can also be used to program the drying temperature locally, at the hopper. Heating units are mounted directly to the hopper to minimize heat loss. The EUREKA PLUS includes a moisture meter manager (MMM), an in-line, resin moisture sensing and drying control. The MMM reads the moisture content of the resin itself, not the air surrounding the resin, using electromagnetic waves, which change based on the moisture within the resin. Separate sensors read the before and after moisture levels of the resin to ensure dehumidification is successful. The EUREKA rapidly adjusts the drying process based on the readings, which are sensitive from 15 ppm (± 3 ppm) up to 3,000 ppm and operate with resins being dried from 68 to 356 °F (20 to 180 °C).
The innovative EUREKA PLUS thus delivers fully responsive “drying on demand” based on the real drying needs of the polymer at any given time. By managing drying functions in direct response to environmental variables that typically interrupt predictable polymer moisture levels, the Moretto drying system can guarantee production certification and maximum energy efficiency.
Moretto in the last year expanded Moretto USA (www.morettousa. com) to a 30,000 sq ft facility in Western Pennsylvania.
The fluid power ingredient
With 1,700 employees and 24 locations spanning the globe (including a facility in Texas), Camozzi Automation SpA (Brescia, Italy, www. camozzi.com) is a leader in industrial automation. Products include a complete range of actuators, sensors, guides, brakes, shock absorbers, valves, pneumatic couplings and vacuum components—small but critical components in a variety of industrial machinery (e.g. packaging equipment, woodworking machines, printing presses), medical devices and mobile automation.
Camozzi’s strategy is based on helping its customers increase the flexibility and productivity of machinery. That’s why the company recently developed an approach that involves multiple technologies, including pneumatics, electrical actuation and proportional technology, to optimize performance. These smart solutions can be integrated into complex machinery and systems, allowing components to interface and dialogue with each other in order to transmit, receive and reprocess information.
Camozzi also recently created a special applications department to integrate different technologies into more complex systems that
A collection of Comozzi Automation actuators, sensors, valves, pneumatic couplings, and vacuum components.
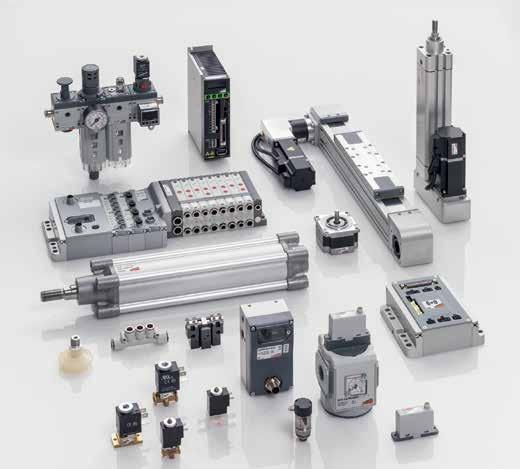
can be customized to offer intelligent solutions that increase productivity and reduce assembly and setup times for automatic machines. Camozzi is a member of ASSOFLUID, the Italian association of fluid power equipment and components (www.assofluid.it/en).
Complex sheet metal parts made in 1, automated line Salvagnini SpA (Sarego, Italy, www.salvagninigroup.com) introduced the world’s first flexible and automatic sheet metal panel production system in 1979, which in turn introduced the now widely applied concept of a flexible manufacturing system (FMS). A member of UCIMUSISTEMI PER PRODURRE - Association of Italian Manufacturers of Machine Tools, Robots, Automation Systems and Ancillary Products (www.ucimu.it), Salvagnini today boasts four manufacturing sites and 23 locations, including the U.S. and Canada.
Salvagnini’s Steve Spilak introduced the technology to Abe Fehr, owner of Uni-Fab, one of the largest metal fabricators in Ontario, Canada. As a job shop that prizes versatility and precision, Uni-Fab saw benefits in what Spilak proposed.
“The Salvagnini FMS line starts with a tower of blank sheets,” Spilak said. “Then depending on what part needs to be manufactured, the machine automatically calls up the appropriate raw sheet and loads it into the queue. From there it moves to the S4 punching machine, which rapidly makes any necessary cuts.” As the S4 completes each panel from the sheet, it shears it off and moves it on to the P4Lean panel bender for automatic bending. But the S4 continues punching the sheet and feeding the bending station while the bending station does its work. “It’s a continuous flow, parts are unloaded and loaded automatically, and there’s zero tool changing.”
Fehr added that Uni-Fab has a lot of experience with laser cutting machines and continues to use them, but the Salvagnini can punch
1-888-italtrade and form components much faster than that technology. Fehr said he could add laser cutting to the line if desired. More importantly, laser cut parts can be introduced to the bender, whether or not they were cut on the line. So, in addition to chasing higher volume work, Uni-Fab plans to move some of the work it is currently doing on laser cutters and press brakes to the Salvagnini FMS because it uses so much less manpower.
Another key point for punching: “We can punch a part and move it on down the line. Whereas with laser cutting you have to cut the entire sheet and then advance it,” Fehr said. What’s more, the machine has 40 tools in the magazine and cuts a variety of shapes with standard punches, simplifying planning. The punch can handle sheets up to 5 x 10 ft, and the panel bender can form sheets up to 4 x 10 ft and 11 gauge (1/8 inch) in thickness.
Another exciting capability is the ability to create radius bends on parts (as long as the bend is within 10 inches high). “It gives us a lot more flexibility,” said Fehr. “We’ll be able to change the way we do machine enclosures from using only square or angled corners to radius corners on panels. It’s the modern look that more and more people require today. In the past we’d have to use a plate or sheet roller for such a feature and now we can do it right in the Salvagnini line.
“Our current market for sheet metal products is mostly machine enclosures and hydraulic tanks for the automotive and oil and gas industries,” Fehr said. “The Salvagnini will make us a lot more efficient in how we do things, putting us into a whole new league of higher volume jobs, whether it’s building materials, transformer covers, or whatever it might be.”
Uni-Fab is off a good start. The line was just installed, and it already won a project to produce 16,000 panels for industrial bins.