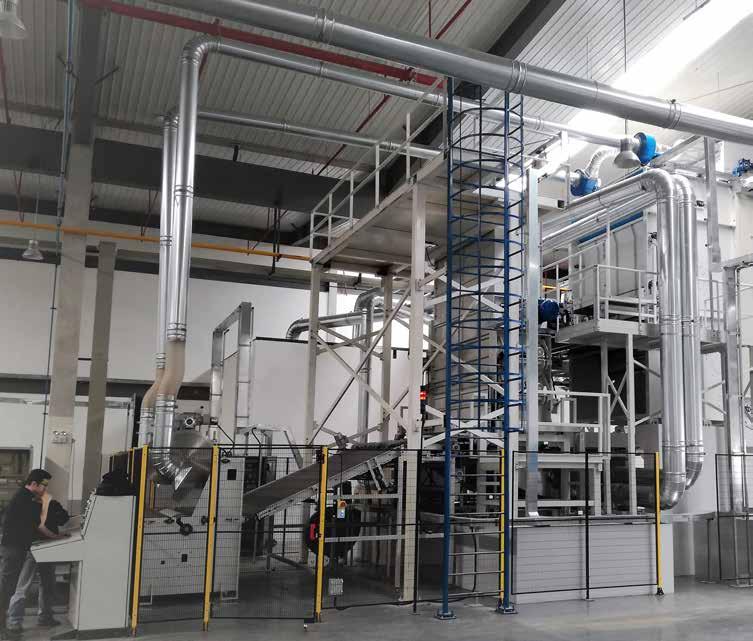
10 minute read
Consumer Products: Italian Machines Produce Things People Want
A Cormatx Airlay thermo-bonding line, which is capable of producing high loft textiles from wool, flax, hemp, carbon, basalt and textile waste, individually or blended together.
Italian Machines Produce THINGS PEOPLE WANT
Advertisement
It should come as no surprise that Italy offers world-class machine technology for making consumer products such as textiles, ceramics and footwear. BUSI GIOVANNI Srl (Botticino Sera, Italy; www.busigiovanni.com) offers a compelling example. Situated in the province of Brescia, Italy’s industrial capital, BUSI, a member of ACIMIT, the Association of Italian Textile Machinery Manufacturers (www.acimit.it), is celebrating 60 years as a family-owned firm specializing in single-cylinder sock-knitting machines for the world’s most discriminating producers—from the classic hosiery of Germany’s Falke and Italy’s Bresciani to the medical compression socks of Gibaud of France. Several factors set BUSI machines apart, starting with unequaled sock quality and versatility, Michèle Castagna, export and marketing manager, said. For example, like other single-cylinder machines, BUSI machines can knit any conceivable embroidery pattern. But they can also produce elegant, true broad-rib socks, which otherwise require double-cylinder machines. And not only can they produce both both terry (up to gauge 22) and classic (200-240-280-320 gauge) knits, they can combine them in the same sock.
BUSI machines are also uniquely capable of producing both sandwich and normal terry in the same sock with just a simple program change, whereas competing machines require extensive mechanical
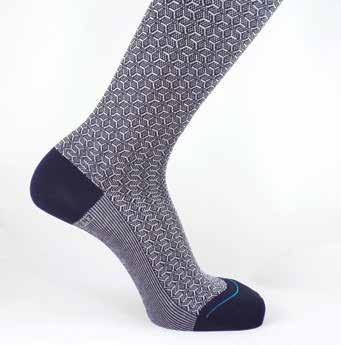

changes. So, for example, you could instantly switch from knitting all sandwich terry socks to a sock that combines a sandwich terry for the leg and top of foot with a normal terry for the sole.
The versatility extends to color, as the machines can knit with six colors plus the background; the competition can handle only three colors. BUSI machines are also capable of knitting double-layer socks and/ or socks with an inside pouch. And you can install a Rimaglio device for automatic, stitch-by-stitch toe-closing with up to 400 needles.
All BUSI machines are custom made in Italy with high-quality materials, and Castagna says they “almost never stop, guaranteeing an incredibly high productivity rate.” And they have outstanding longevity, averaging 25 years.
General Manager Catina Busi joked that after 30 years of making socks around the clock, a customer would give his BUSI machine away only from boredom, not because it was no longer working well. Castagna added that, although the initial investment in a BUSI machine is a bit higher than for competing machines, they are actually more economical amortized over time. In any case, the typical BUSI customer produces higher quality products and targets higher margin business.

BUSI GIOVANNI machines can knit any conceivable embroidery pattern plus elegant broad-rib socks, even combining both sandwich and normal terry weaves in the same sock.
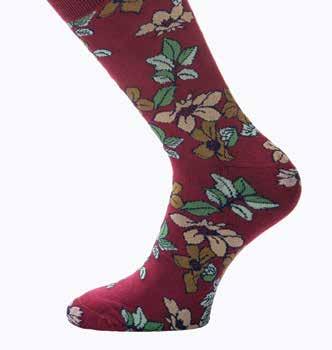
Bonding fibers for everything from filtration to footwear Like BUSI, Cormatex Srl (Montemurlo, Italy, www.cormatex.it) is an ACIMIT member, but with very different technology. Although the company has produced machines for carding and spinning fine knitting yarn since 1938, its recent focus has been on creating machines that produce non-woven materials with a high degree of productivity, flexibility and quality. Called Airlay, these systems use thermo-bonding to produce high loft textiles and other materials, with fiber lengths ranging from 1 to 60 mm in the case of their Lap Formair H model and from 20 to 150 mm with itds Lap Formair V, including powders and granulated matter.
Without modifying any mechanical components, the Airlay systems are capable of processing a wide variety of fibers, including wool, flax, hemp, carbon, basalt and textile waste, individually or blended together. And cleanup is fast and simple. Besides clothing, applications for these materials include packaging and thermal and acoustic insulation, filtration, building construction and home furnishings.
The machines are also highly efficient, owing to their low energy use, low maintenance costs, lack of waste and high productivity (up to 500 kg/hour/each meter width). And, in addition to scheduled
Inside a BUSI single-cylinder knitting machine, capable of producing both sandwich and normal terry in the same sock with just a simple program change.
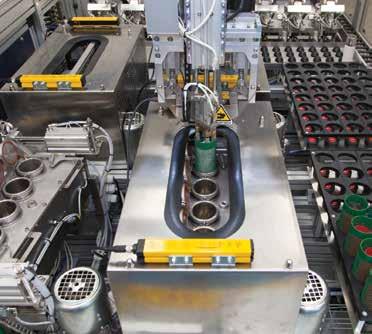
TECNORAMA’s Dos&Dye, a completely automated dyeing system that operates 24/7, unmanned.
maintenance to avoid downtime, they offer on-demand, real-time remote diagnostics via VPN.
Increasing textile dye house productivity Yet another innovative ACIMT member, TECNORAMA (Prato, Italy, www.tecnorama.it) has developed a completely automated dyeing system that operates 24/7 without any manual intervention. Called Dos&Dye, it can manage and perform all laboratory dyeing cycles, increasing the productivity for laboratory and bulk operations. In the lab, it reduces dyeing trials to obtain an exact recipe because it can completely reproduce a dyeing cycle just like a bulk machine, with preparation, dyeing, soaping and washing. And it’s extremely precise. For example, the automatic multi-pipette volumetric system used during the dispensing state is accurate to within 0.01 cc. This offers “right the first time” results, drastically reducing corrections after dyeing and redyeing, cutting the time dedicated to a production batch and increasing the productivity of the entire dye house, TECNORAMA said. Optimizing the production processes and overcoming the limits inherent in manual management of the lab also greatly reduces water and energy use for an environmentally friendly and thrifty approach.
The system consists of an automatic dispensing machine working with one or more automatic dyeing machines. TECNORAMA offers several models of each type, and they can themselves or in combination with others carry out different dyeing programs in the different units, reproducing the same steps used on bulk dyeing machines. One combination of units can dye up to 20 g textiles, such as fabric, knits, yarn (winded or hank form) and flock. Another combination can dye up 500 g textiles.
It’s also important to note that the speed and flexibility of the Dos&Dye systems make them an excellent solution for producing samples, meeting very short delivery times, and for remaining profitable in the face of the increasing trend toward small-batch production in the fashion world.
ACIMIT’s perspective
ACIMIT President Alessandro Zucchi said the biggest concerns for textile machine manufacturers stem from three mega-trends:
1-888-italtrade • Increasing end-user autonomy (i.e. the expansion of e-commerce),
• The constant need for innovation as new products are continuously required (fast fashion), and
• The constant expansion of low-cost trends. “The concern and commitment of Italian textile machinery builders is to provide an adequate response to their customers, who today face the difficult challenge and opportunity of developing new processes and business models that meet the need for fast time to market and just in time production.” Zucchi added that automation and technologies that implement Industry 4.0 are essential in dealing with these trends. This includes embedding sensors on the machine for data acquisition, process monitoring and communications with other divisions—plus collaborative robots (either in the industrial network or interacting with each other to optimize transportation inside a company).
Other common solutions include the use of quality control systems combined with gesture-recognition technologies and 3D printing to rapidly respond to requests.
Companies that produce textile machines are also using intelligent management platforms with mobile devices for monitoring the work and maintenance, if needed, and augmented reality applications to support the operator during maintenance, Zucchi noted.
Smart choice for tableware glass manufacturing
OCMI-OTG SpA (Milano, Italy, www.ocmigroup.com), a member of GIMAV, the association of Italian manufacturers and suppliers of machinery, equipment and special products for glass processing (www.gimav.it), has long been a leading supplier of manufacturing technology for pharmaceutical and consumer glassware. On the consumer side, OCMI has seen steady growth in tableware products in recent years. Its most popular equipment for such applications in the U.S. is the SA sealing and stretching machine, available in versions with 42, 48 and 60 stations. This machine can produce stemware drinking glasses by joining the stem and bowl, a task previously handled by separate pressing and blowing machines. The SA machine can also, if necessary, stretch the stem before unloading.
Processing stemware is an area in which glass forming mixes science with art, OCMI said: “Each operator involved in this sector and working every day with such machines has his particular opinions about the way to work with glass to get the desired article shape.” So developing an SA60 sealing and stretching machine for Libbey Inc. (Toledo, OH) required close cooperation with the customer.
SA60 sealing and stretching machines are usually placed in a production line with a press and a press-blow (or blow-blow) machine to produce stems and bowls, the two items to be sealed together to get the final stemware. And an SA machine typically has two 12-arm loading devices for stems and bowls along with one 12-arm unloading device. These loaders must be perfectly synchronized with the conveyors coming from the previous machines to avoid losses and breakage. They also must of course be synchronized with the rotation of the sealing machine itself.
At Libbey, OCMI also supplied pyrometers to detect the temperature of the bowls and stems on the conveyor and to automatically reject out of tolerance items. Dedicated stoppers that adjust the running time of the articles ensure the synchronisation of the sealing/ stretching machine with previous equipment on the line.
OCMI equipped the loaders and unloaders with 12 mechanical grippers designed for the item shapes specified by the customer. The stem loaders have the option of a vacuum gripping system to handle flat stems that lack a foot. Bowls are loaded in the machine’s lower chucks while the stems go to the upper chucks.
American firms are usually very interested in technological features that contribute to product quality improvements, and Libbey chose OCMI’s self-adjustment system for the upper chucks. A camera mounted immediately after the machine’s loading area checks the distance between bottom of the stem and the top of the bowl before sealing. Then the system uses data coming from the camera to automatically adjust the height of the upper chuck to compensate for any discrepancies. The ultimate goal is to get the same sealing point height in each station and uniform quality for the entire batch.
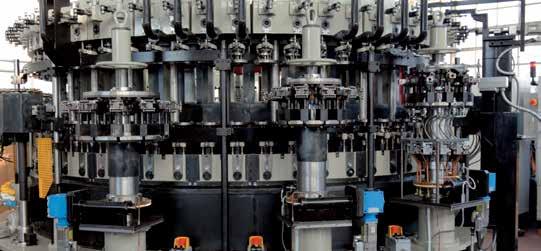
The next working areas are usually equipped with different types of burners, each designed for different operations, such as heating, sealing and cooling. This is one of the most critical aspects of such machines, and the temperature of the flame, the system for orienting the burner and the size of each hole in the burners is often something the end-user prefers to manage himself. In this case, Libbey chose to perform many production tests on the equipment before its installation in the production line.
OCMI developed the main cam that governs the vertical movement of the lower chucks up to the sealing point to match the heating, sealing and cooling points required for each type of article. The section of the cam that controls stretching was a particularly delicate design issue and the resulting cam can be adjusted in slope for slower or faster stem processing.
At the end of the process, an unloading device, also equipped with 12 arms with mechanical gripping hands, picks the finished articles and places them on the exit conveyor going to the moil (exceeding glass) cutting machine or to the annealing lehr.
The OCMI sealing machine produces stemware up to 350 mm in height with a maximum output of about 60 pieces per hour, depending on the type of article processed. The glass bowl can come from a press-blow or a blow-blow machine. The latter option produces a thinner glass and a higher quality item that requires slower rotation of the working station in the OCMI sealing machine. As usual, higher quality products can’t be produced at the highest speed possible.
Likewise, more than in other types of automated glass production, the machine cannot be responsible for everything affecting quality, so the operator must be very accurate in regulating the levels of gas, oxygen, and air feeding the burners and in adjusting the cam height in the sealing and stretching zones. But, Libbey tested the process thoroughly with OCMI technicians, and the tremendous success of the project testifies to the outstanding partnership between these two leaders in the glassware industry.
A stemware-sealing machine from OCMI. Part of an automated line for manufacturing fine glassware.