
5 minute read
Dankzij Additive Manufacturing naar een circulaire economie?
CECIMO ziet in politieke agenda’s toenemende aandacht voor AM als enabler voor duurzaamheid
Is Additive Manufacturing een enabler voor een duurzame samenleving? Zelfs voor een circulaire economie? Duurzaamheid is in elk geval een thema dat politieke agenda’s steeds meer beheerst. CECIMO bracht daarom onlangs een aantal voorbeelden hoe AM duurzame productie mogelijk maakt, bijeen. Om de aandacht te vestigen op de rol die Additive Manufacturing kan spelen in het verduurzamen van de samenleving en economie.
Advertisement
Stewart Lane, die de AM-werkgroep bij de koepelorganisatie van Europese werktuigmachinefabrikanten leidt, denkt dat de Europese Green Deal kansen aan de sector biedt. Want uitgerekend additive manufacturing draagt bij aan het realiseren van de ambities van de Europese Commissie om tegen 2030 bepaalde klimaat- en energiedoelen te bereiken. “We weten dat de samenleving hiernaar kijkt. En dat in een groeiend aantal overheidsagenda’s additive manufacturing gezien wordt als een enabling technology om de agenda te realiseren”, aldus Lane bij de aftrap van de conferentie over Sustainability.

Een van de door Aidro 3D geprinte kleppen die bijdragen aan een fors kleinere CO2 voetafdruk in de olie- en gasindustrie.
Downsizen voor minder CO2 emissie
Wie hiermee bezig is, is Additive Industries. De Nederlandse fabrikant van industriële 3D metaalprintsystemen, is betrokken bij twee interessante projecten op het vlak van duurzaamheid. Het eerste project wordt samen met een bedrijf uit de olie- en gasindustrie gedaan. “Daar worden onderdelen ontworpen voor bepaalde prestaties. Maar in de olieproductie zie je de volumes verminderen”, aldus Harry Kleijnen, key accountmanager. Voor een van de klanten uit de olie-industrie heeft Additive Industries een impeller voor een pomp herontworpen voor 3D metaalprinten. Dit keer niet om de productiviteit verder op te drijven, integendeel. “We hebben met het redesign de output van de pomp omlaag gebracht om energie te sparen.” Het gaat hier om een pomp met een continu vermogen van 150 kW. Door de impeller te herontwerpen, is Additive Industries erin geslaagd om het energieverbruik van de pomp met 70% te verminderen. Dat scheelt 770 ton CO2 uitstoot per jaar. Weliswaar is de output lager, maar het oliebedrijf heeft de hoge output niet langer nodig. De gekozen oplossing kan volgens Harry Kleijnen alleen maar geprint worden. Deze impeller past in de bestaande behuizing, zodat dus daaraan geen wijzigingen nodig zijn. Het alternatief zou zijn geweest een compleet nieuwe pomp installeren, wat echter materiaalverspilling zou hebben betekend, hogere kosten en een langere stilstand van de installatie.
Van schroot tot poeder
Het tweede voorbeeld dat Harry Kleijnen aanhaalde, is het al enkele jaren lopend project Scale4Series met SMS Group in Mönchengladbach. De fabrikant van apparatuur voor de staalfabrieken, ontwikkelt met Additive Industries een gesloten poeder supply chain voor de MetalFab1 printer. SMS heeft nu een test gedaan met het gebruik van schroot uit de metaalproductie als feedstock voor de poederinstallatie. Harry Kleijnen zei in een toelichting dat een eerste test is geslaagd. Schoon afval uit een persstraat is gereinigd en daarna in de installatie van SMS verwerkt tot poeder. Als het om spanenafval uit de CNC productie gaat, zal dit waarschijnlijk meer voeten in de aarde hebben, omdat dan verontreinigingen door onder andere koelsmeermiddelen, grondiger aangepakt moet worden. “We hebben eerst het idee geverifieerd. Het is haalbaar. Nu moeten we verder gaan onderzoeken.” Additive Industries heeft de eerste batch poeder die SMS van schroot heeft gemaakt, inmiddels verwerkt op de MetalFab1.
Lokale gedistribueerde productie
Het thema duurzaamheid kun je vanuit meerdere invalshoeken aanvliegen, zo werd tijdens het CECIMO seminar duidelijk. Alessio Lurosso, oprichter en CEO van de Italiaanse printerfabrikant Roboze, ziet vooral het gedistribueerd 3D print netwerk van de fabrikant als een oplossing om de CO2 uitstoot omlaag te brengen. “Het verschepen van onderdelen over de hele wereld is goed voor 7% van alle CO2 uitstoot in de wereld”, aldus Lurosso. Hij heeft het dan met name over producten die in Azië worden gemaakt en elders in de wereld worden gebruikt. Het aanhouden van magazijnen hiervoor kost nog eens elk jaar $300 miljard. En de transport- en logistieke kosten bedragen $1,6 triljoen. Hij zegt dat Roboze bezig is om naar een circulaire economie te gaan. De sleutel hiervoor is de herhaalnauwkeurigheid waarmee de Roboze printers werken. “Nauwkeurigheid en repeatability zijn essentieel”, zegt Alessio Lurosso. Want alleen met printers die in Singapore hetzelfde resultaat printen als in Europa of de VS kun je echt naar een distributed manufacturing netwerk toe, waardoor het verschepen van onderdelen vervalt. Lokaal en gedistribueerd produceren levert volgens hem 50% kostenbesparing op. Het 3D printen met hoog temperatuur materialen is de tweede cruciale factor. Daarmee kan Roboze aluminium onderdelen vervangen door 3D geprinte kunststof delen.

Additive Manufacturing kan een rol spelen in de transitie naar een circulaire economie, met een veel kleinere carbon footprint van producten. (foto: Gerd Altmann / Pixabay)
Lagere CO2 emissie dankzij AM
Niet alleen Additive Industries en SMS Group onderzoeken de mogelijkheid om van schroot metaalpoeder te maken. Valeria Tirelli, CEO van Aidro, is met enkele partners in een project met hetzelfde idee bezig. Zij richten zich op 316L. Als dit lukt, slaat Aidro een dubbele slag: de manifolds die met additive manufacturing worden gemaakt zijn lichter en vergen dus minder energie in de gebruiksfase en worden in een materiaalefficiënt proces gemaakt. Als je dan ook nog eens afval of de componenten aan het eind van de levensduur kunt verwerken tot metaalpoeders, schuif je op richting een circulaire economie. Aidro heeft overigens samen met de Noorse energiemaatschappij Equinor onderzoek gedaan naar de betekenis van het printen van een manifold op de CO2 emissie. 60% gewichtsreductie betekent 80% minder CO2 uitstoot. “De impact is dus echt indrukwekkend”, aldus Valeria Tirelli.
Huizen 3D printen: duurzaam maar nog ver van grootschalige inzet
Tijdens het CECIMO seminar zette Jakob Jørgensen, CEO van de Deense fabrikant van betonprinters Cobod, iedereen met de voeten op de grond. 3D betonprinten heeft een grote potentie om de al 60 jaar afnemende productiviteit in de bouw te doorbreken. Hij verwacht dat binnen twee tot vijf jaar per uur per werknemer 10 tot 13 kubieke meter beton geprint kan worden. Dit cijfer ligt gemiddeld in de bouw momenteel tussen de 1,3 en 1,7 kubieke meter. Om echt een deuk in een pakje boter te slaan, moet een veel groter deel van de woning geprint kunnen worden. Nu schommelt dit rond de 25%, dat moet naar 60%. Ook de kosten moeten omlaag. Want volgens de Cobod CEO kloppen veel verhalen op internet over het 3D printen van woningen niet. “De technologie is nog nergens rijp.
We gaan daar wel binnen twee tot vijf jaar naar toe.” 3D betonprinten is vandaag de dag nog altijd een moeilijk proces, dat echter wel een bijdrage levert aan lagere CO2 emissies in de bouw. met hetzelfde idee bezig. Zij richten zich op 316L. Als dit lukt, slaat Aidro een dubbele slag: de manifolds die met additive manufacturing worden gemaakt zijn lichter en vergen dus minder energie in de gebruiksfase en worden in een materiaalefficiënt proces gemaakt. Als je dan ook nog eens afval of de componenten aan het eind van de levensduur kunt verwerken tot metaalpoeders, schuif je op richting een circulaire economie. Aidro heeft overigens samen met de Noorse energiemaatschappij Equinor onderzoek gedaan naar de betekenis van het printen van een manifold op de CO2 emissie. 60% gewichtsreductie betekent 80% minder CO2 uitstoot. “De
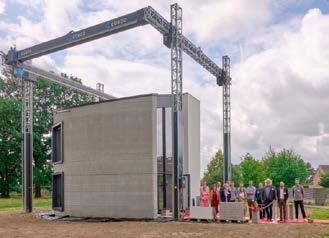
De woning van twee verdiepingen die bij Kamp C in Westerlo is gebouwd is een voorbeeld van waar we naar toe gaan met 3D betonprinten. In het Belgisch project is eveneens een Cobod printer gebruikt.