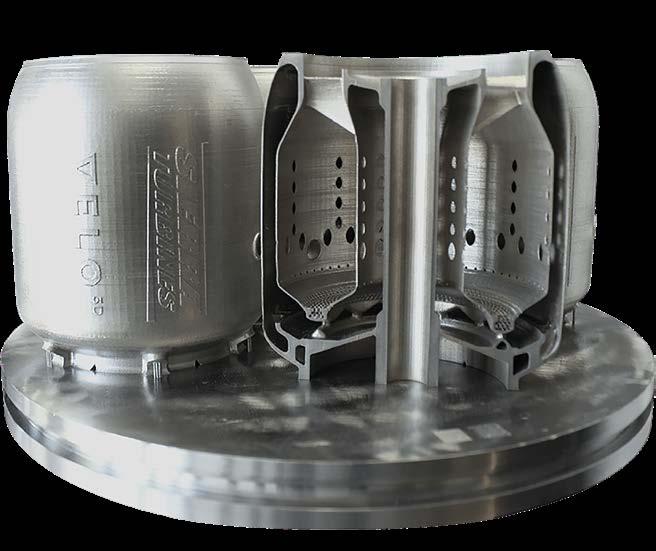
6 minute read
Multilaser systemen voor lagere kosten
Aantal lasers in 3D metaalprinters neemt sterk toe, maar is dit de oplossing?
Is multilasertechnologie de oplossing om de kosten per 3D geprint metalen onderdeel drastisch te reduceren? Ja, denken sommige fabrikanten van laser poederbed metaalprinters. Gemakkelijk is het echter niet. En je moet niet de designkant uit het oog verliezen. Ook daar zit veel potentieel als het om kostenreducties gaat, meent Velo 3D CEO Benny Buller.
Advertisement
Vier lasers is tot nog toe het maximale dat je in de AM-machines voor metaal tegenkomt. Maar dat heeft zijn langste tijd gehad, lijkt het. Velo 3D kondigde enkele weken voor Formnext Connect de Sapphire XC aan. Deze 3D metaalprinter beschikt over een bouwhoogte in de Z-richting van 1.000 mm en krijgt straks 8 lasers van elk 1 kW. Wat dit betekent liet Benny Buller, oprichter en CEO van Velo 3D, tijdens de presentatie zien. Het 3D printen van een nozzle voor een raketmotor kost niet langer $ 100.000, maar nog slechts $ 40.000. Voor kleinere delen betekent de nieuwe machine dat je er in één batch 66 kunt produceren en geen 19 zoals nu. Benny Buller: “Je mag kostprijsreducties per onderdeel verwachten met een factor 3 tot 5.”
Procescontrole luistert nog nauwer
De grootste hordes die het R&D-team van Velo 3D heeft moeten overwinnen, is het kalibreren van de lasers en het voorkomen dat te veel warmte in het werkstuk komt als de lasers elkaars pad kruisen. Volgens Benny Buller is Velo 3D erin geslaagd om een universeel ‘recept’ te ontwikkelen, waardoor men nu kan opschalen. “We weten hoe we het eindresultaat kunnen sturen via de kalibratie.” De bijkomstigheid als je naar 8 lasers gaat, is de interactie tussen de laserstralen. “Dat is een extra element dat het complex maakt: het ontkoppelen van de lasers met wat er gebeurd is. Eerlijk gezegd is dat al iets dat we kennen van de bestaande Sapphire”, legt de CEO van Velo 3D uit. Waar hij op doelt, is dat de laserstraal ook de omgeving van een bepaalde positie in de laag beïnvloedt. Hou je daar geen rekening mee in de opbouw van de volgende lagen, dan zou je zo de mechanische eigenschappen op die plaats in het werkstuk kunnen beïnvloeden. Volgens Benny Buller hebben dit type machines doorgaans last van een soort geheugeneffect. Door in situ te meten wat de laser op welke positie doet, kan men dit ontkoppelen “Doordat wij van elk punt de invloed van een vorige belichting kennen en die van de omringende delen of van de andere lasers in het systeem, kunnen we een zeer consistent eindresultaat halen.” En omdat Velo 3D in staat is vanuit de besturing exact elke laserstraal
Dynamisch uitlijnen
Velo 3D heeft ook een eigen methode ontwikkeld voor het uitlijnen van de lasers. Dat gebeurt dynamisch in elke laag met een nauwkeurigheid van 20 micron. Deze techniek wordt ook toegepast in de Sapphire XC. Het derde aspect waarmee Velo 3D in de nieuwe metaalprinter denkt te scoren, is het free floating concept, alhoewel Benny Buller dit niet de belangrijkste oplossing vindt voor kostprijsreductie. In tegenstelling tot andere fabrikanten heeft Velo 3D bij de werkstukken minder support nodig. Bij kleinere producten vaak zelfs helemaal niet. Hierdoor kan men in de Sapphire XC duizenden onderdelen per batch printen. Buller vindt het echter belangrijker om het design te optimaliseren voor de mogelijkheden van Additive Manufacturing. “Dat is een belangrijk vehikel om de kostprijs per stuk omlaag te brengen.”

Multilaser in industriële toepassingen Buller ziet de single laser machines in de toekomst met name in de healthcare industrie, bijvoorbeeld de dentale laboratoria, omdat het daar veelal om kleine onderdelen gaat. Ook om als bedrijf vertrouwd te raken met de metaalprinttechnologie zijn de kleinere single lasersystemen geschikt. “Het industriële segment van de AM-markt gaat zeker gedomineerd worden door de multilaser systemen, tenzij er een paradigmashift komt qua energiebron. Velo 3D wil de single en multilaser systemen dan ook naast elkaar blijven verkopen. De nieuwe grootformaat metaalprinter komt eind 2021 op de markt als een all-in one machine, zo bestempelt de CEO.
Farsoon: groot volume printer volop in bedrijf
Het Chinese Farsoon heeft op dit vlak een voorsprong, want het vlaggenschip de FS621M large frame metaalprinter, is al uitgeleverd aan Falcontech, een van de toeleveranciers voor het Chinese passagiersvliegtuig van Comac. De Farsoon metaalprinter heeft in de Z-as een hoogte van 1100 mm, het bouwplatform meet 620 bij 620 mm (X-Y). De machine is voorzien van vier lasers. Xu Xiaoshu, oprichter en CEO van Farsoon, gaf tijdens de Formnext persconferentie het voorbeeld van een cilindrisch product dat op de machine wordt geproduceerd om het effect van meer lasers te illustreren. Het onderdeel meet 620 bij 800 mm. “Op een single laser machine zou de productie 30 dagen vergen, op het 4 lasersysteem wordt het in 11 dagen geproduceerd.”
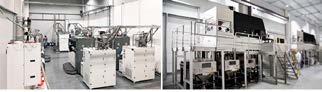
Bij de Chinese luchtvaarttoeleverancier Falcontech zijn al meerdere
Falcontech heeft ondertussen 24 metaalprinters gekocht van Farsoon, die in de AM Super Factory staan die de luchtvaarttoeleverancier momenteel opbouwt. Hieronder zijn meerdere FS612M systemen. Momenteel loopt er nog een order voor de levering van 10 metaalprinters. Falcontech slaagt erin om over een lengte van 800 mm met een maatnauwkeurigheid van 0,5 mm te printen.
SLM Solutions: 12 lasers printen 1.000 cm3 per uur
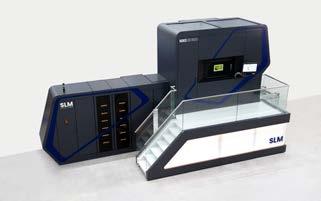
De nieuwe NXG XII 600 van SLM Solutions beschikt als enige AM-machine over 12 lasers.
SLM Solutions heeft tijdens Formnext Connect de nieuwe multilaser machine gepresenteerd. De NXG XII 600 beschikt over 12 lasers van elk 1 kW en een bouwvolume van 600 bij 600 bij 600 mm. De aanleiding voor de ontwikkeling van deze machine is de verschuiving van additive manufacturing van prototypes en enkelstuks naar series en grote onderdelen. Volgens Sam O’Leary, COO, kunnen de kosten per onderdeel gereduceerd worden doordat deze machine vijf keer sneller is dan het huidige topmodel van SLM Solutions met 4 lasers. “Hierdoor zijn we in staat om de cost per part significant te reduceren.” De hogere productiviteit komt ook door het tot 40 procent verminderen van de zogenaamde ‘skywriting’ time, de tijd dat de lasers niet effectief ingezet worden om metaalpoeders te smelten.
Patenten
SLM Solutions heeft patent gekregen voor het opdelen van het scannerveld, dat ervoor zorgt dat de werklast van de 12 lasers gelijkmatig verdeeld wordt over de bouwkamer. Hierdoor kan men de 12 lasers maximaal benutten. “Voor het eerst in de geschiedenis van additive manufacturing kunnen we echt naar serieproductie gaan.” Een andere innovatie in deze machine, is de zoomfunctie. SLM Solutions bouwt voor elke laser twee optieken in zodat de diameter van de straal kan variëren. Hierdoor kan men de materiaaldepositie verder opvoeren op plaatsen waar minder details of nauwkeurigheid vereist zijn. De diameter kan variëren tussen 80 en 400 micron. Sam O’Leary: “Deze functie helpt om meer laservermogen in het poederbed te krijgen. We schatten in dat we bij sommige materialen tot 1.000 kubieke centimeter per uur kunnen opbouwen.” Het design van de machine is aangepast om thermische drift te vermijden. Omdat 12 lasers tegelijk tot veel rook en vonken kunnen leiden, is voor deze machine een nieuw systeem voor de gasstroom ontwikkeld in combinatie met een nieuw ontwerp van de bouwkamer. Per jaar kan, afhankelijk van de legering en het product, de nieuwe metaalprinter 10 ton aan onderdelen produceren. Ook SLM Solutions kan met de nieuwe technologie overhangen tot een hoek van vijf graden printen zonder support. Het Duitse concern mikt onder andere op de automobiel- en vliegtuigindustrie, O’Leary wijst er verder op dat de NXG XII 600 geïntegreerd kan worden in een complete workflow, geautomatiseerde wisseling van cilinder, voorverwarmen en ontpoederen. Hiervoor wordt onder andere met Siemens samengewerkt.