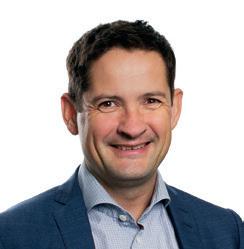
4 minute read
NIRAS: Aspects of future food factory design
Aspects of future food factory design
Production capacity expansion projects in the food industry is a multi-disciplinary exercise that requires experience and industry insight. Food productions meet increasing demands for cost-efficiency, quality, hygienic production environments and sustainable supply chains from authorities, consumers and owners. Hence, food factories are often complex facilities that are designed with a set of important requirements as well as being ready for smooth expansion possibilities and opportunities to change product mix according to market developments.
Advertisement
At NIRAS, we have developed an industry-unique methodology to evaluate your future food factory project. Whether your company is looking at building a new greenfield production plant or making improvements to existing sites, NIRAS provides a full range of evaluation and decision support that will enable your organisation to take the best possible course of action from feasibility study to factory layout, and budgets in the initial project phase to complete design and project execution.
Feasibility Study
Our evaluation and decision support studies assess the practicality of your plan and evaluate how best to deliver your project goals. Using expertise, we produce an entirely independent, well-considered document that examines the concept, technologies, cost-to-achieve, time frame and programme in enough detail to inform investment decisions. A feasibility study can also be a crucial document for securing funding. It allows both clients and their funding sources to know what the project will look like, the level of risk, how much it will cost and what it will deliver in great detail.
Current state
We create a model that considers the process, the required ingredients, the time scale and the techniques. This model will devise how to achieve the desired end result by setting out facts and numbers based on current operations and future projections. By comparing the current state to the future state, we can define business objectives, identify improvement areas and scope out the necessary changes. We can then prescribe scenarios for the future state of products, processes, and demand in order to achieve the project goals.
Creating an effective & efficient layout
Whether your project requires an entirely new factory or whether it necessitates an expansion of an existing facility, the layout of the new areas will need to be planned out with careful attention to numerous important factors. Establishing an effective factory design requires consideration of equipment solutions, the flow of production, processes and people, manning requirements, and health and safety regulations. It will also need to take note of other factors such as shift patterns, changeover times, energy requirements, technical requirements and utilities and services.
With all of these factors in mind and a wealth of skill and experience, we create drawings to design the most efficient and cost-effective layout possible.
Creating a phased master schedule
Considering all operational requirements from beginning to transition right through to optimisation, we create a master schedule with a phased implementation programme for your project going forward.
BY MORTEN AAE OLANDER, MARKET DIRECTOR AT NIRAS, MOOL@NIRAS.DK
Main phases in NIRAS capex project model. The Evaluation phase secures the good project foundation for the later project phases.
From initial feasibility to operational food plant
EVALUATE DESIGN IMPLEMENT
TRANSITION OPTIMISE
Calculating the cost to achieve
Many budgets focus exclusively on the big elements of a project, such as the cost of buying land and building a factory. Although these are crucial components, budgets that focus solely on these elements runs the risk of escalating considerably once the realities of achieving a project are encountered. Which is why we develop a ‘cost to achieve’ budget, including capital expenditure costs, operational expenditure costs, one off transition costs and future state profit and loss analysis. Essentially, every cost within the process is accounted for to create a highly detailed budget.
Food Factory design
We develop concepts into detailed designs that will enable the project to progress efficiently through to the implementation stage. We manage and coordinate all integral elements of the design development aligned to a procurement strategy. A specially selected design team is matched to the specific delivery requirements.
Project Execution & Management
Our experienced team take ownership of the implementation process to ensure that your project is delivered. We ensure that implementation is a robustly planned process. By controlling and coordinating all project activities and communicating with internal and external parties, we lead the process to ensure successful delivery.

innocent’s new factory in Rotterdam, the Netherlands, soon to be in operation with a capacity of 400 mill. bottles annually
Let’s talk about your food factory project
Come to NIRAS’ booth (D3158) at the IFC exhibition in Herning and talk about your next food factory project. We are looking forward to meeting with you.
Fakta
i
NIRAS employs 2300 people of which more than 250 experts are dedicated to project in the Food and Beverage industry. We execute project on all continents and have been main consultant in 100+ greenfield projects globally. Current projects include Oatly’s new factory in UK with the capacity to produce 300 mill. liter oat drink annually, and innocent’s new factory in The Netherlands with the capacity to produce more than 400 mill. bottles juice annually. Under different brands, NIRAS has designed the majority of Danish dairies in operation today.
Let’s talk future food factory design
Sustainable Food Production – Process & Packaging Design Utilities – Warehouse Design – Industrial Architecture Informed Decisions Through Factory Simulation Health & Safety – Project Management