
5 minute read
EFI COVER STORY
EFI ARE YOU GETTING THE MOST OUT OF YOUR DIGITAL PRESS INVESTMENT?
By John Henze of EFI
If your company is looking at adding a digital press or acquiring one for the first time, I’m sure you have spent a fair amount of effort on due diligence to make sure you know what the latest digital press bells and whistles are and how they can help your business continue to grow.
But often overlooked is the value that adding a digital front end (DFE) can bring. Gone are the days when it is sufficient to simply File/ Print. That can still be done, but there are so many advantages to the built-in automation and workflow an effective DFE can offer.
Electronics For Imaging (EFI) recently interviewed a number of printing companies about how they choose a DFE, how they decide what configuration is best, and what they expect to gain from this choice. We were surprised at how many of the respondents indicated they just accepted the recommendation of their chosen printer manufacturer or dealer, and how many of them actually did not know about the many productivity tools a good DFE includes!
We also learned that when companies were offered options, many of them chose the least expensive configuration. These companies are missing out on significant ways to improve both quality and productivity, highly important in today’s competitive marketplace. Here’s why.
LABOUR SHORTAGES
It’s no secret that hiring and retaining talent in today’s marketplace is a challenge. The ability to easily design automated workflows not only enables companies to utilise less skilled workers, it also speeds work through the shop and reduces opportunities for costly errors. Workflows can simplify a wide range of activities that can be labour intensive, require special skills and impact productivity. These can encompass everything from job submission and prepress to make-ready, colour management and finishing.
PAPER SHORTAGES
Another challenge most companies are facing today is shortages in paper stocks. After struggling to get sufficient paper stock of the right types to meet customer needs, the last thing you want is for any of it to be wasted unnecessarily! By using automated workflows and specialised tools to ensure an accurate order-to-ship process, your production operation will see fewer errors, higher quality, and thus less of that precious paper supply is wasted.
PROFITABILITY
How many jobs do you process each day? 10? 20? 200? More? If you can save even 15 minutes of prep time per job, how much more capacity does that give you with your current staff? Speeding up the process by 15 minutes per
job is completely doable, and probably at the low range of possibility. Then think about how much time you could save per job if you are able to process the print ready files faster, especially when they include complex — or not even that complex — variable data, an offering for which demand is high.
Carefully track all jobs through your shop for a week. How long does it take to intake a typical job? How much hands-on time is required by the sales rep or CSR? What about prepress? And once the job is print ready, how much of the time is your digital press running at rated speed? Now take a look at finishing. Are your bindery staff manually setting up the equipment for each job, and how long does that take on average? Also take a close look at waste — makeready waste, finishing waste and waste due to rework required because you catch errors or colour anomalies, or, heaven forbid, the customer rejects the job? Add that up and imagine reducing that time and waste by 10% … by 30%. What would that mean for your bottom line?
FACT BASED MANAGEMENT WITH REAL TIME DATA
Once you understand where you are today, think about where you would like to be next week, next month, next year. And then consider how choosing the right DFE can help get you there. Now, let’s take a look at each step of the process to see how choosing the right DFE configuration can help. We’ll start with job submission and prepress. Other areas of production will be covered in Part Two, appearing next month! Using a web-to-print solution like MarketDirect StoreFront from eProductivity Software makes job submission fast and efficient. While it is not part of the DFE, a web-to-print solution can be integrated with Fiery DFEs to make the job flow seamless. Then using Fiery JobFlow Base, you can automate the job submission process and batch processing of multiple files with the same print settings. Think business cards, as an example.
PREPRESS
The Fiery Workflow Suite offers a number of applications that deliver more accurate print ready files with much less prepress time. For example, Fiery JobFlow automates job preparation steps in prepress workflows to produce ready to print files. It performs essential job processing tasks such as image enhancement, imposition and preflighting, and then submits files to the proper location. It can also automatically archive jobs at various processing stages for later use. The free version, JobFlow Base, is included with most Fiery external DFE configurations. We were surprised at how many of the customers we spoke to during our study have never used JobFlow Base, and some did not even know it was available. That’s just one of the many productivity tools available as part of the Fiery Workflow Suite.
MAKE-READY
Here, too, there are a number of tools available to make this a more productive process, including Fiery Impose, offering fully visual page layout for ganging and booklet imposition. When combined with Fiery JobFlow, multiple operations may take only a few seconds instead of 15 to 20 minutes each.
Or consider Fiery JobMaster, offering intuitive make-ready including media assignment, chapter definition, advanced page numbering, fully visual tab insertion and design, finishing, scanning and powerful late stage editing features. Each of these steps, done manually, takes time and can be error prone. One respondent to our recent study cited a recurring job that has benefited from Fiery and Fiery Command WorkStation, saying, “We do a book every year that has 13 different colour stocks, so I load six colours in the machine, use Command WorkStation to designate which pages go on each colour, then run the other four and three, then assemble. We can do 300 spiral comb bound books in a day or day and a half.” He noted that trying to run this job any other way would take significantly longer and make it difficult to meet customer delivery requirements.
FOR MORE INFORMATION …
Be sure to check out all of the resources available at EFI.com, including Learning@ EFI and our Fiery community when you are ready to make your next digital press investment — or if you are looking for ways to make your current operation more productive and profitable. And watch for Part Two of this article next month! www.efi.com
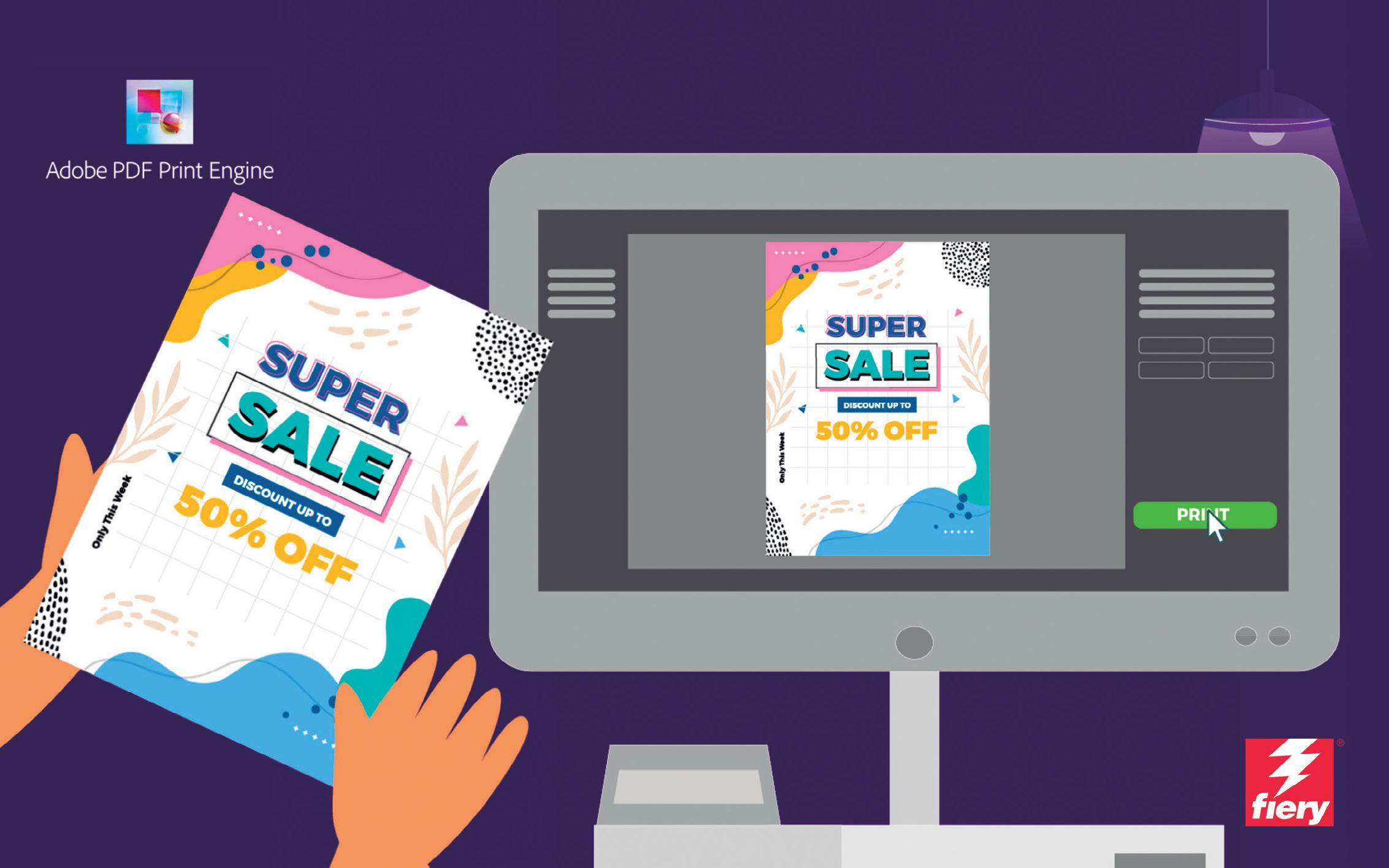