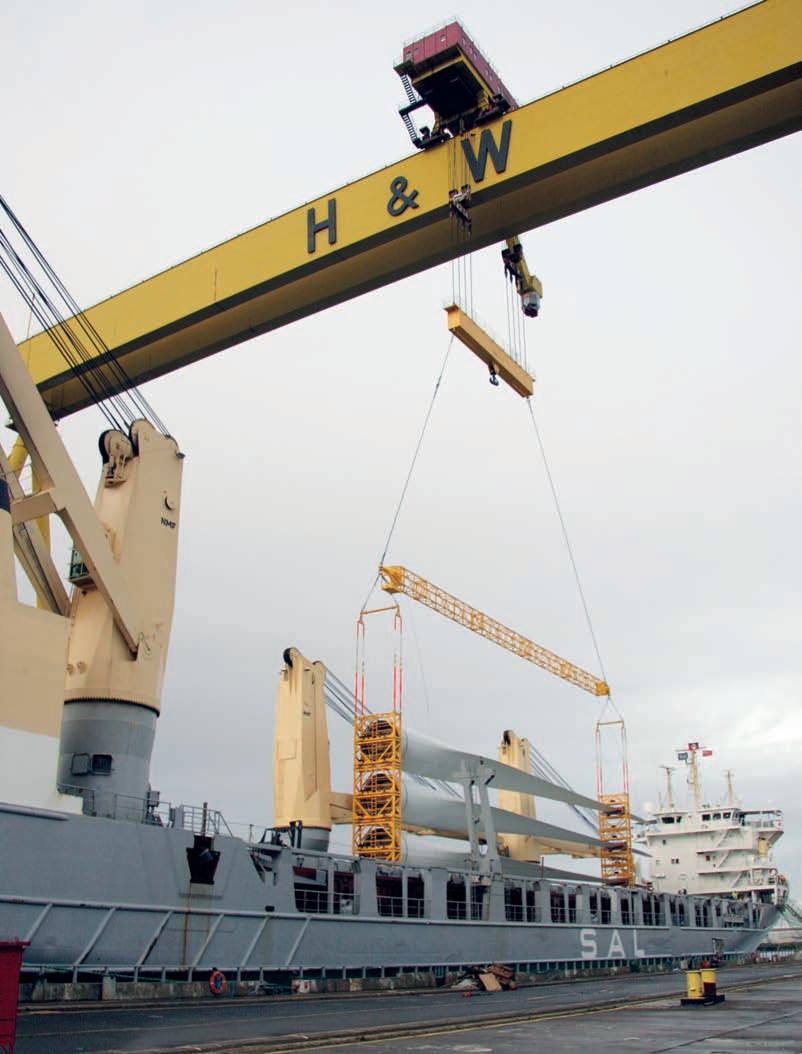
4 minute read
Ready for the ride?
As the AwAreness of climAte chAnge grows, so do the demAnd for renewAble energy, And the heAvy lifting solutions required to accommodate the rise in construction of offshore windfarms.
All photos courtesy of Modulift.
According to a report by rethink energy the offshore wind industry is set to grow significantly within the next 10 to 20 years, with forecasts predicting an increase from 25GW to 418GW by 2040. to put it in context, a GW = 1,000MW and a MW = 1,000KW. one average wind turbine with a capacity of 2.5 - 3MW can produce more than 6kWh million in a year, enough to supply 1,500 average eu households with electricity. so, the sheer magnitude of these projects and what they will do for the fight for greener energy is extremely impressive. With the offshore wind industry taking off: are companies ready for the ride?
A prime example the scale of windfarms is really taking off and an example of this is the proposed dominion energy’s Virginia offshore Wind Project. this could end up being the world’s largest, with estimates suggesting it could produce up to 2.64GW. the Walney extension, located in the irish sea is another good example, as it boasts impressive stats of 189 turbines with a capacity of 659MW. investment in highly-skilled design engineers will be required in both the offshore wind and heavy lift industries to enable the forecasted industry figures to become a reality. Modulift is a prime example of a company that is adapting their strategies in line with the changing industry needs. their highly-skilled team of in-house engineers was recently commissioned to work on a custom solution, designing a 43m lattice spreader Beam for a company needing to lift 150t wind turbine blades.
Technical expert partner “the project plan was highly demanding due to the complexities and timescales involved”, explained Harshal Kulkarni, Modulift’s engineering Manager. “each critical step required stringent third-party certification sign-off before progressing to the next step. these included a design review, a review of weld procedures and welder qualifications, a manufacturing survey, as well as live testing and witnessing of the lattice with a 800t crane and 165t test loads. With a live lift there are many factors to consider: the product delivered on site and on time is one, as well as arranging the crane hire, and the weather being on our side too. from start to finish the project took just under twelve weeks to complete. efficient project planning from the outset was key and ensured that the project was kept on track and the tight deadline was met – proof of why Modulift is viewed as the technical expert partner with which to work in the lifting industry”, Mr Kulkarni states.
Exiting milestone Another example of how Modulifts’ expert team of engineers have worked with the >>
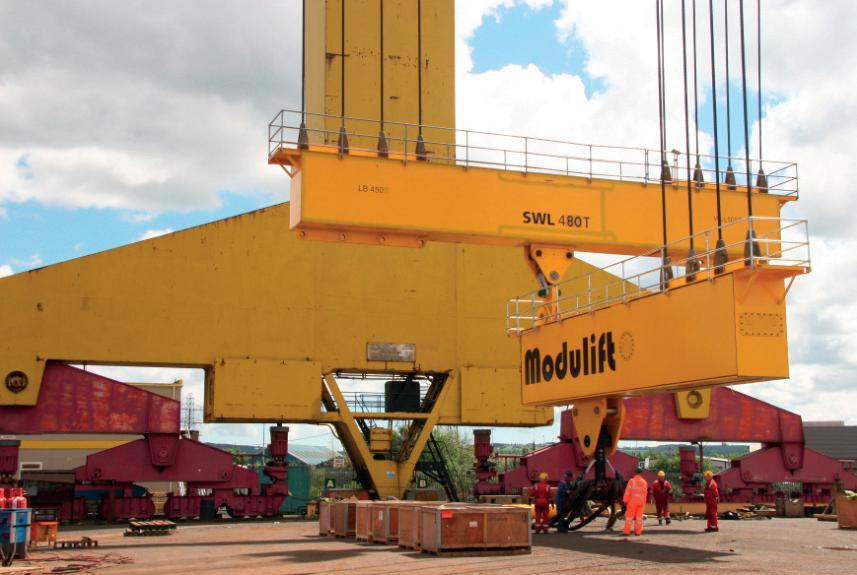

Meet people who can take your business further
Book your stand now.
For Repower, Modulift designed a rig which could not only lift the individual turbines and towers separately and assembled, but also lift three wind turbine blades in one go enabling the blades to stay in their calibrated sets for each turbine.

The beam was an exciting milestone for Modulift. off shore wind industry was the giant lift ing rig they designed and manufactured for the fast and effi cient lift ing and assembly of repower’s 5MW wind turbines at the Harland and Wolff shipyard in Northern ireland. Modulift ’s remit was to design a rig which could not only lift the individual turbines and towers separately and assembled, but also lift three wind turbine blades in one go, enabling the blades to stay in their calibrated sets at all ti mes, for each turbine. Modulift designed a rig consisti ng of two elements which could be used in various confi gurati ons for the transportati on and installati on process of the various wind turbine components. the fi rst element was a giant 500t, 16m long lift ing beam. due to the nature of the lift and the need for minimising the overall weight of the rig itself, Modulift had to design and build the beam to weigh less than 40t without compromising its capabiliti es. the lift ing beam was also designed to include inspecti on hatches and was built to ensure that these hatches would not compromise the structural integrity of the beam. the beam was an exciti ng milestone for Modulift , proving their technical achievements in designing highly engineered lift ing equipment to provide the ulti mate soluti on for lift s of this size. the second element was another feat of engineering for Modulift in the design and fabricati on of a 48.5m spreader that weighed no more than 9.6t to maximise the capacity of the cranes. the beam had to be easy to assemble in situ and capable of lift ing the wind turbine blades, which in their set of three weighed 75t and spanned 61.5m.
Adaptable to change the pressure is on companies in the energy and lift ing industry more than ever to diversify their strategies in line with the changing needs, and, in the words of darwin: “it is not the strongest of the species that survives, nor the most intelligent that survives. it is the one that is most adaptable to change.”