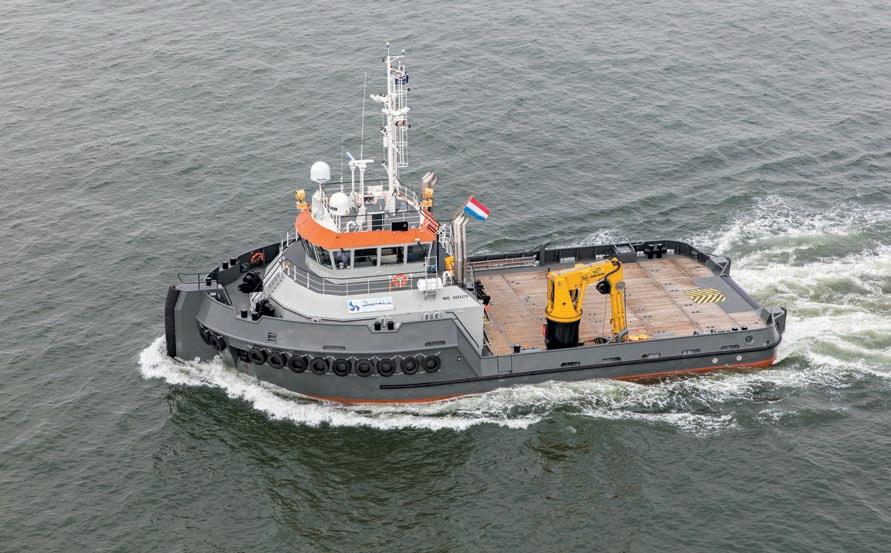
3 minute read
Hybrid Propulsion Systems
Verhoef EMC has installed a hybrid propulsion package on a DP2 tugboat.
Verhoef eMC has deVeloped a hybrid propulsion paCkage suitable for a wide range of Vessels. as the greatest advantage of hybrid systems is achieved with variable operational sailing profiles, the system is particularly suited to Dynamic Positioning Vessels. Inhousedeveloped automation allows the system to select the most suitable energy source for delivering the required propulsion power as efficiently as possible.
All imAges Courtesy of Verhoef eMC.
The environment is 2020’s hottest topic of discussion, both in general and in shipbuilding. Energy transition is a mayor part of the development of new construction projects. Verhoef EMC recently completed a project for the construction of a DP2 hybrid tug. The vessel was built to satisfy the latest environmental, safety, and quality standards. This will enable her to undertake a wide variety of offshore and nearshore duties. Verhoef EMC supplied the entire electrical system integration for this vessel, including the hybrid propulsion system. “We supplied and installed the main engines and the generator sets”, says Verhoef EMC’s General Manager Stephan Kempen. “The complete electrical system and controls were designed, drawn, produced, and thoroughly tested inhouse, before installation on board. This also included the engines and
gearboxes with permanent magnet motors/ generators (pM machines) for the hybrid system. Sister company RH Marine supplied the dynamic positioning system.”
Hybrid System the hybrid system design has been developed to fit into any hybrid, diesel electric or fully electrical vessel with a variety of power sources. Verhoef EMC has experience in DP2 Hybrid propulsion systems from 1MW up to 9MW of propulsion power. The company can, for instance, supply a propulsion package of two 970kW diesel engines, two PM machines of 200kW, as well as a propulsion package of a 8MW main engine with a 2MW electric motor driving a 9MW propeller. Each PM machine is linked to its own switchboard. “The reason we install two completely separate switchboards is
because it is important to ensure that the dynamic positioning system can function at all times”, comments Pascal van der Es, Lead Engineer at Verhoef EMC. “We previously provided the electrical system for a similar tugboat with three main engines. In the hybrid tug, we have replaced one of the main engines with two electric pM machines.”
Different Working Modes The user-configurable power management system offers different working modes (diesel-hybrid-fully electric) in DP1 or DP2 to match client requirements with the weather and sea-state, with an optimal combination of performance and fuel consumption. when the diesel engines and electric drives are used together, a power boost enables increased speed or bollard pull for towage operations. Mr Van der Es adds, “It is also possible to run the main engines and use the pM machines as a generator to save fuel.” The beauty of Verhoef EMC’s system is that the vessel’s operators do not have to choose which machines to use. “We have developed an automation package that will work in the
background to select the most suitable energy source to deliver the required power as efficiently as possible”, explains Mr Van der Es. “Top of mind in the system’s development was that sailors have to operate the vessel, rather than electrotechnical people. this means it will be operated based upon operational instead of technical decisions.” Verhoef EMC works closely with shipyard and client to provide the right system. Mr Kempen elaborates, “We have a lot of experience with integrating electrical systems on board. Each time we provide a tailor-made solution based on our standards. The hybrid tug’s engine room has a height of 1.80m, which means space is very limited. It was a puzzle to get all the equipment in there, but it was a great challenge, which we were happy to accept.”
Interchangeability Verhoef eMC specialises in developing and building electrical systems customised to each customer’s needs. With new developments and technology rapidly emerging, choosing the right option can be a challenge at times, comments Mr Van der Es. “Customers are wondering about the best solution for their application or what happens if they choose one option today and a better solution becomes available tomorrow. The answer is modularity; ensuring that systems are interchangeable when developments offer better alternatives, when energy requirements change or when the application is modified. It is essential that systems have universal connections and controls, which simplifies exchanging a generator module for a battery module or fuel cell. And Verhoef EMC systems are, as a result, future-proof.”
i. verhoefemc.com
