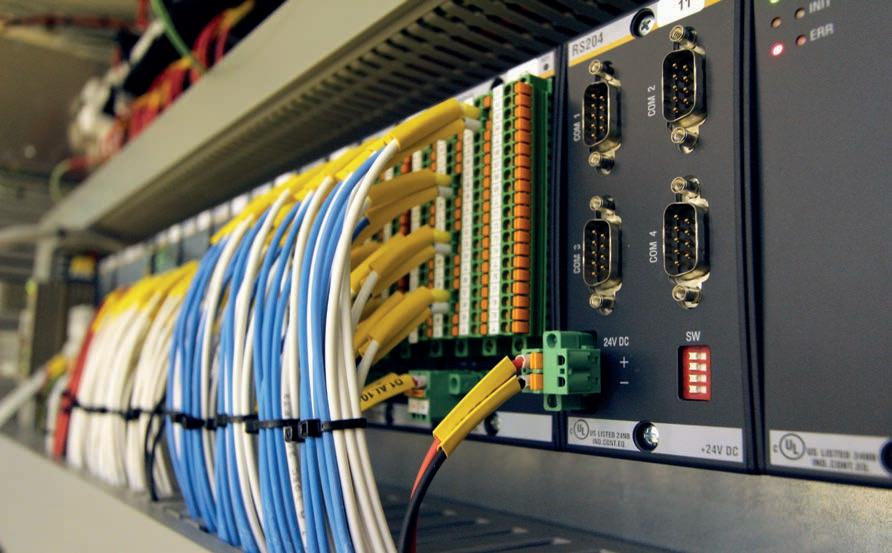
4 minute read
Hybrid LNG ship propulsion – First in the world
M1 controller fully wired in the cabinet
SEMBCORP MARINE IN SINGAPORE IS CURRENTLY BUILDING THE WORLD’S FIRST HYBRID LNG-POWERED TUG FLEET. IT WILL REPLACE THE EXISTING diesel-powered one in the coming years. The Hybrid Control System (HCS) is provided by Invertek Drives Far East. For this purpose, the company relies on the M1 system components from Bachmann electronic.
ALL IMAGES COURTESY OF SEMBCORP/INVERTEK DRIVES. The drive control of tugs is demanding, because this type of ship requires very variable power ranges, high manoeuvrability, and immense force: The new harbour tugs have 65 tons of bollard pull to handle the huge ships and tankers in Singapore. With the new ships, Sembcorp wants to contribute to decarbonization, and, above all, to reduce the air pollution. In the tugs, two 16-cylinder engines powered by liquefied natural gas (LNG) are supported by electric motors. “Depending on the desired operating mode and required performance profile, the electric engine can be used for propulsion (Power Take-In, PTI) or as a generator (Power Take-Off, PTO),” says Henry Beh, Managing Director of Invertek Drives Far East Pte. The two gas engines deliver an overall output of almost 3,000kW. They do not emit any sulphur oxides and only very small amounts of nitrogen oxides. Therefore, the exhaust gas aftertreatment can be dispensed with. In contrast to the dieselpowered counterparts, the particle number is negligible.
Efficient use of resources
The hybrid system has five drive modes: In the ‘Harbour’ operating mode, propulsion is purely electric and emission-free, as the gas engine is switched off. In ‘Transit’ mode, without towing or pulling vessels, the tug is powered by the gas engines. Generated excess power is stored in the battery. When pulling ships to or from the port, the tug is
operated in ‘Towing’ mode and is powered by the LNG engines only. Then, when high bollard pull is required, the captain can activate the ‘Boost’ mode where both gas and electric motors are used in parallel to deliver maximum power. Finally, a special feature is being implemented to use the tugs for firefighting operations: One motor is reserved to operate the firefighting pump, the other one is used to keep the ship in position. “Our control system ensures that both motor and generator are always operated in the optimal load range, to achieve maximum fuel efficiency and lowest possible carbon emissions”, emphasizes Henry Beh.
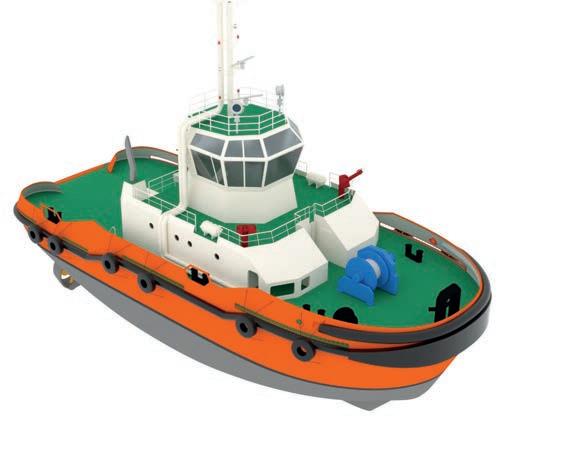
Demanding automation
In Singapore, the combination of LNG motor and electric drive is being used for the first time worldwide for tugs, and the control is complex: “The power management of the two motor types, the batteries, and the converters require completely new approache”, explains Henry Beh. High maneuverability of the ships must be guaranteed for all performance requirements, and at the same time, the least possible impact on the environment must be assured. Therefore, the Hybrid Control System is one of the most critical subsystems of a hybrid vessel.
Maximum reliability and operational safety
“It can be seen as the brain that coordinates and controls the various propulsion system components on board, such as engine, electric motor, battery and thruster”, as Henry Beh underlines. “The components must work in perfect harmony
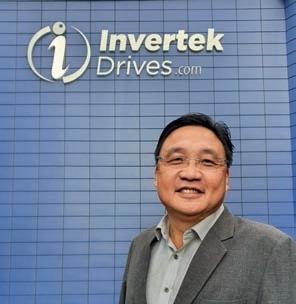
Sembcorp Marine in Singapore is currently building the world’s first hybrid LNG-powered tug fleet.
BOOTH NO. 1512
EUROPORT 2021
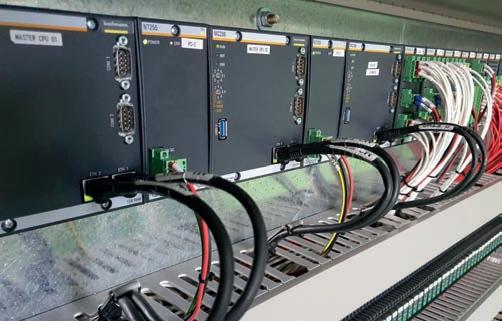
Redundant setup HCS system.
to achieve the desired operating objectives in terms of efficiency and resource-saving.” Together with Bachmann electronic, the Invertek engineers developed an appropriate automation solution. Controls and network in ring topology are completely redundant: The two master CPUs are operated in hot standby, automatically synchronized, and can be transferred bumpless. “Thus, the ship operator gains maximum reliability and operational safety,” emphasizes the general manager.
Challenges mastered
The frame conditions due to the corona pandemic were anything but easy. The entire project – from tender, kick off meeting, system design, and project coordination – had to be executed completely online without a single personal encounter. Beh praises the cooperation with the Bachmann electronic engineers: “They were available to us at any time and were also a great help to our customers.” When he opted for Bachmann electronic, he was convinced from the start by the company’s extensive experience and impressive references in the maritime industry. “It is important for us that all components are approved for such demanding applications in accordance with stringent marine and offshore standards”, adds the Invertek manager. To ensure full compliance in meeting the stringent criteria of marine classification, the design and operation procedure including FMEA was reviewed by ABS. ABS also surveyed the final factory acceptance test. Henry Beh is pleased: “Thanks to Bachmann electronic, we were able to create an excellent basis for expanding the fleet with a total of twelve tugs.”