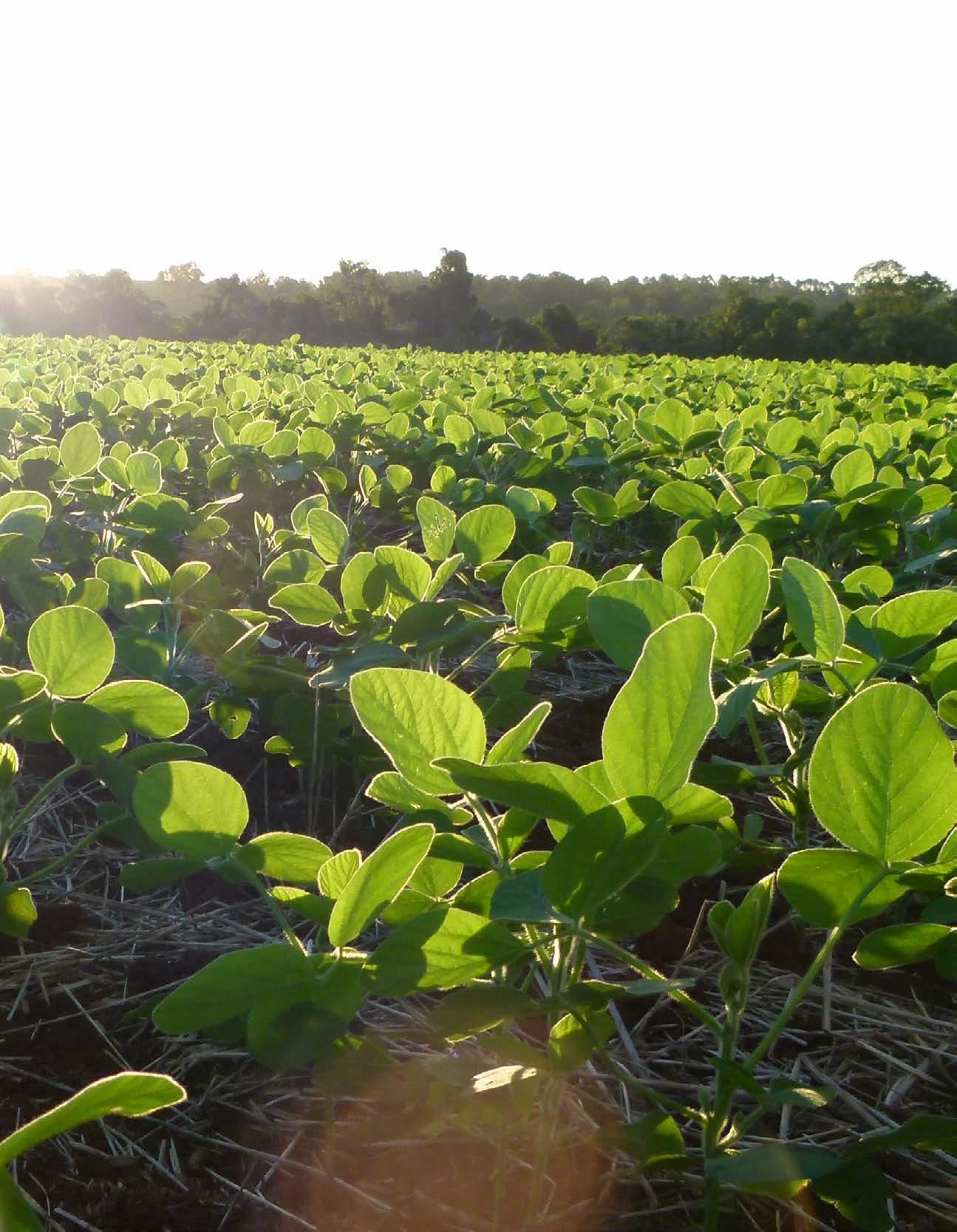

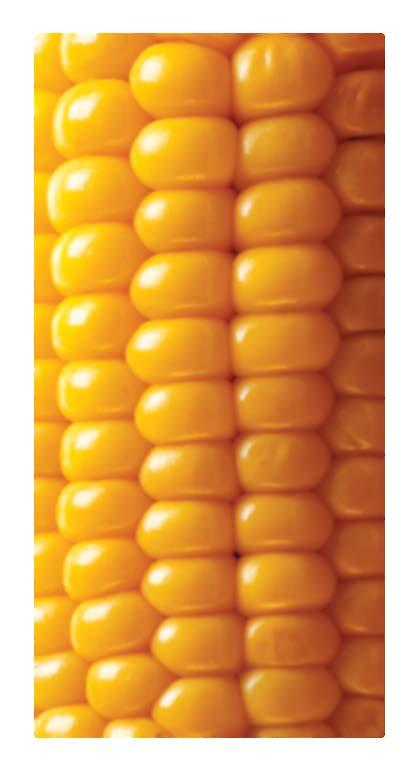
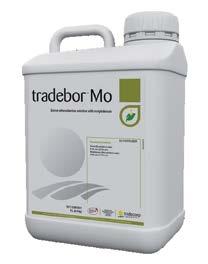

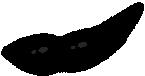

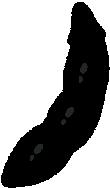
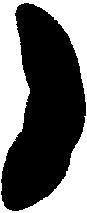
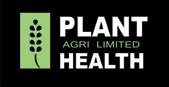
Syngenta is at the forefront of delivering innovations that help farmers adapt to changing growing conditions. Syngenta recently introduced Soyastarter+. Read more on page 3 how your soya bean crops can benefit from Soyastarter+.
No. 10 Tito Road Rhodespark, Lusaka +26 (0)97-769-9786 www.proagri.co.za
I
t is that time of the year again when farmers are anxious about the rains as we get ready to plant. Decisions are being made on what needs to be planted, where to get the seeds, and other farming inputs.
Good news to start off the plant ing season is the SARCOF 26 forecast, stating that the bulk of the SADC Region is likely to receive normal to above normal rainfall for the October, November and December period.
Farmers are not only food produc ers, but they are also guardians of our natural resources, soil, water, biodiver sity and seeds. As times are changing, farmers also need to adapt, change, create new methods of working the land and endure weather fluctuations.
Our farmers are stalwarts who tackle every new season with faith and hope, regardless of what nature and life throw their way.
In the cover story of this month’s edition of ProAgri Zambia, we take a look at growing soya beans in Zam bia the Syngenta way. We had the honour of seeing LEMKEN’s Juwel 8 plough in action; read more about it on
page 6. And for the poultry farm ers, there are several informative articles, from vaccination tips, the importance of biosecurity, and how Novatek plays an important role in the success of poultry farmers of the Zambian community.
At ProAgri, we hope to arm you with the knowledge you need to face the challenges when approaching this new season.
We remain committed by providing our readers with informative articles and agricultural related news, help ing farmers to reduce downtime and maximize productivity.
Sign up for our monthly newsletter, and make sure you visit our websites www.proagri.co.za , www.proagrimedia.com and www.agri4all.com for all your agricultural news and needs.
We wish all farmers success for the coming season.
Editor Bianca Henning
Reporters
Benine Ackermann
Maryna Steyn
Natasha Kruger
Specialist Writer
Annemarie Bremner
+27 82-326-2572 bianca@proagri.co.za
+27 73-105-6938 benine@proagri.co.za +27 82-261-9177 maryna@proagri.co.za +27 81-736-4236 natasha@proagri.co.za
+27 82-320-3642 annemarie@proagri.co.za
Senior Production Manager
Zainab Pandor
+26 (0)97-769-9786 zainab@proagri.co.za
Client Relations Manager
Carin Swartz
Marketing Manager
Diane Grobler
Marketing Xander Pieterse
Johan Swartz
Tiny Smith
Lynette van Tonder
Creative Director
Christiaan Joubert
Design Michelle Kruger Enquiries
Engela Botha
+27 84-233-0123 carin@proagri.co.za
+27 82-555-6866 diane@proagri.co.za
+27 79-524-0934 xander@proagri.co.za +27 71-599-9417 johan@proagri.co.za +27 82-698-3353 tiny@proagri.co.za +27 74-694-4422 lynette@proagri.co.za
+27 72-419-3990 christiaan@proagri.co.za
+27 12-803-0782 engela@proagri.co.za
Distribution and subscription
Nita Volmer-van Zyl
Accounts Ronel Schluter
Business Manager
George Grobler
+27 79-515-8708 nita@proagri.co.za
+27 12-803-0782 accounts@proagri.co.za
Soya beans (Glycine max) is a crucial food legume crop being cultivated extensively in our country Zambia on large and small-scale farms.
Growers must follow basic agronomic principles when growing soya beans to maximize yields and get a higher return on investment: They must know when to plant, which latest robust varieties to plant, which fertilisers to apply, how to manage pests and diseases, and many other factors. This article deals with some of our new in novations, crop protection, and seed treatment from Syngenta.
Syngenta is excited to introduce Soyastarter+, a seed treatment combi pack consisting of APRON® Plus Beans and Atuva. Apron® Plus Beans is a fungicide seed treatment that protects your soya seed from important seed and soil diseases. By protecting the seed from plant ing, APRON® Plus Beans gives you optimum emergence with a stronger stand for maximum quality and yield. ATUVA® is an inoculant formulated with Osmo Protection Technology to strengthen the bacteria against harsh conditions for maximum nodulation and biological nitrogen fixation (BNF). It gives the grower a greater treatment
window, hence more flexibility and op erational efficiency during the planting season (up to 7 days).
It is critical to keep the soya beans weed free for optimum yields. Chemi cal control measures can be either pre-planting - TOUCHDOWN Forte ® Hitech or pre-emergence - DUAL MAGNUM®
Once the soya beans have germi nated, any weeds that emerge can be controlled using selective herbicides. Depending on the type of weeds, Syngenta has two solutions: FLEX® for broadleaf weeds and FUSILADE FORTE® for grasses. Herbicides should be applied when weeds are young and actively growing. Always read the la bels before applying and obtain all the necessary guides. Adhere strictly to the application rates as shown on the product label.
Soya beans can be attacked by pests at any stage from seedling to harvest, hence the importance of regular crop scouting cannot be overstated. Many pests have a major impact on yield and quality, and intervention with pesticides is frequently unavoidable. Syngenta has an excellent insecticide
by Admore Nyaguze - Head of Commercial Syngenta Zambiarange for the pests common in soya beans; CRUISER® 600F S is a seed treatment insecticide, while AMPLIGO ® and DENIM FIT® are foliar solutions.
Soya beans can be affected by diseases throughout the growing season. Seed treatment fungicides such as the previ ously mentioned Apron® Plus Beans do a good job in controlling seedling diseases from planting.
During the season, many leaf diseases are common on soya beans, and Syn genta has introduced the MIRAVIS™ Duo, a new unique fungicide that deliv ers the promise of consistent long-last ing broad-spectrum disease control.
This is powered by ADEPIDYN® Technology for superior performance and consistency. We have AMISTAR Top ®, powered by AMISTAR® Technology, a reliable technology with a proven track record amongst other Syngenta fungicides that are registered for the use in this crop.
more information contact:
Admore Nyaguze
Admore Nyaguze
Commercial Sales
Admore.Nyaguze@syngenta.com
Admore.Nyaguze@syngenta.com
If required Post Em Herbicide can be sprayed only up to 3rd Trifoliate ONLY Scout Fields for Weed Growth Stage 2LF not older than 4LF READ Label for effective control of weeds
If
read product label
read product label
Syngenta wishes you the best sea son ever as you reap the rewards of quality products from your Innovation Powerhouse Partner, Syngenta!
For centuries you have cultivated the land. We trust in you Today you provided to millions. We thank you You innovate for tomorrow, today. We support you John Deere salutes you!
Golden opportunities were opened for farmers when, in June 2021, Tata Zambia and John Deere partnered and expanded their footprint within the Zambian community to support a fast growing agricultural and construction market.
“We are committed to providing our services in Africa and the Middle East, allowing customers continued access to agricultural solutions, as well as new construction solutions from John Deere,” says Cobus du Toit, Business Head for agricultural and construction equipment at Tata Zambia.
Cobus adds: “The past year we have seen exceptional growth and we are excited for what the future holds for us at John Deere, while we plan to expand our footprint even wider in Zambia as well as the rest of Africa.”
John Deere’s exceptional service
“We understand what our communities need and only supply equipment created and designed for African condi tions. We always put our farmers first. It is important for us to build a trusted relationship with the farmers. We know the importance of time on a farm; therefore, we want to limit downtime to the minimum by ensuring that we always have enough parts available and reassuring the farmers that we are only a phone call away,” says Cobus.
“Our wide network of platforms also ensures that farmers can easily get ac cess to our branches and technicians. We have an exceptional team of tech nicians ready to assist farmers with their specific needs. We currently have
four branches based in Lusaka, Kitwe, Mpongwe and Mkushi,” Cobus says.
In Zambia, you will find John Deere’s 5E Series Tractors from the north to the south. Once you have seen it on your neighbour’s farm, faithfully work ing year after year, you will decide to get one on your farm.
Cobus explains his opinion on the reason why John Deere 5E Series Tractors are so popular: “John Deere’s utility tractors are built to give you the best performance while saving you money on fuel and maintenance. These tractors are designed to perform in the harshest conditions; John Deere trac tors always show up ready to handle any task you give them.
“The 5E tractors are built to work longer and smarter, they are designed to provide a low cost of ownership through reduced fuel consumption and less maintenance costs compared to others in their class.
“We ensure that there is at least one or two 5E Series tractors available at
each branch. Once you have seen it, you will not be able to say no. Every farmer needs a 5E workhorse tractor on his farm,” Cobus concludes.
“Not only are the 5E tractors a hit in Zambia, we have recently introduced the 5D series tractors to the market, They are also doing exceptionally well, especially amongst the new-era farm ers. Our 6B, 6M and 8R tractors are also becoming very popular.
“Not only do we provide top class agricultural equipment, but also con struction equipment for all segments of the industry, from TLBs to bulldozers, from small excavators to large ADTs, our machines work hard to help you succeed,” states Cobus.
Customers wishing to finance either agricultural or construction equipment can reach out to John Deere Financial for tailor-made financial solutions for purchasing John Deere products.
John Deere’s goal is to provide supe rior customer care and quality prod ucts. They are always ready to handle any task. John Deere’s utility tractors, machinery and equipment are just what you need for a job well done.
For more information, visit their Facebook page (www.facebook. com/TataZambiaEquipment), or LinkedIn profile (www.linkedin.com/ company/tata-john-deere-zambia), or send an e-mail to jd.zambia@ tatainternational.com. Contact them on (+26)076-217-2412, or visit them at Plot 26593, Kafue Road.
The John Deere Zambia team.
John Deere’s 5E tractors: Your ultimate workhorse.
John Deere: Ready for any job on the farm!
Where this blue team operated, the field is ready for planting.
The LEMKEN Juwel 8 in ac tion with the furrow press roller ensuring an even and perfect seedbed afterwards.
L
EMKEN is well known for their mul tipurpose equipment such as the Karat, Rubin and Heliodor, assuring you a firm seedbed for the planting season. When ploughing needs to be done, LEMKEN also stands ready with its Juwel range.
Greenway Farms originated 34 years ago – in 1988. They are located in the Tarlton area, and also have properties in Christiana and Naboomspruit. The main crop produced by Greenway Farms is carrots (800 ha) and cash crops which include wheat (350 ha), sugar beans (300 ha) and soya beans (300 ha).
Greenway Farms is a family farm
owned by two families, under the man agement of Vincent Sequeira senior and Vito Rugani.
"I grew up on the farm and have always had a love and passion for what we do. Since I was five years old, I have helped out on weekends and holidays on the farm wherever I could. For the past four years, I have been on the farm full-time, where I started as General Farm Manager for the Tarlton farm, and after two-and-a-half years I was appointed as Senior Production Manager, where I am now responsi ble for the management of all three farms," says Vincent Sequeira junior.
Nowhere in the world is a set of equipment that can compare to LEM KEN. This is also precisely why Green way Farms chose LEMKEN. They have been using LEMKEN equipment for the past three-and-a-half years.
They have four LEMKEN implements on the farm, including two 3,5 metre Karat 9s, a 5 metre Rubin 12, and they recently acquired the LEMKEN Juwel 8 plough.
"Over the past five years, farmers all over the country have made a mental shift, and increasingly realised the importance of good soil structure. Our need on the farm was to improve our soil structure and soil moisture," says Vincent.
Marco Tijssen, Co-Director of Genius Landbou and LEMKEN Sales Repre sentative for the Tarlton area, confirms that LEMKEN was the best solution to improve the soil structure of Greenway Farms.
"They were looking for a reliable implement, and parts that are easily available. I recommended the LEM KEN Juwel 8 plough together with the furrow press roller, which is ideal for reconsolidating soil and provides farm ers with the best results," he says.
The LEMKEN Juwel 8 is a mounted plough attached to the three-point hitch of the tractor. The furrow press roller is pulled behind the plough. At the end of the field, the furrow press roller is unhitched, whereafter the plough is hydraulically turned around in the air, to plough the next section of the field.
“After I did some thorough research, Marco recommended the Juwel 8 to me,” says Vincent. "I had seven re quirements: durability, a user-friendly
machine, low maintenance cost, good working depth, safe and quick hydrau lic overturn, availability of parts, and lastly a method of tillage that breaks the clods and creates a level soil sur face. The Juwel 8 met all my require ments, which made my choice easier.”
Good soil structure is of utmost importance to allow water and air to move freely through the soil, ensuring healthy plant growth.
Vincent adds: "Because carrots are a root crop, our soil structure is extremely important to ensure that we produce the best quality carrots, and also reduce diseases of the crop by ensuring you have the best possible drainage in your field.
“Over the years we have always ploughed our fields, although we always had to do extra tilling for the seedbed preparation. With the Juwel furrow press roller attached, it is a two-in-one operation. We save on fuel, labour, wear and tear, and an addi tional tractor and implement. With all these factors considered, we are more efficient in what we do.
"One of my favourite and unique features of the Juwel 8 is the Optiquick adjustment system. The Optiquick adjustment system allows for easy and efficient adjustment of front width and tractor or plough pull line, independent of each other. This precise and specific adjustment has brought us great im provements in our fuel consumption. The tractor pulls the plough with less effort, resulting in improved efficiency and cost savings.
“The LEMKEN Juwel 8 plough has a ploughing depth of anything up to 350 mm and a working width of up to 50 cm
per mouldboard. The plough needs a tractor power ranging from 80 to 150 kW depending on the number of furrows.
The furrow press roller is acquired apart from the plough. It is attached to the plough using a hydraulic pin. When the plough reaches the end of the field, the pin releases the roller, whereafter the plough turns over. It then re-engages the roller to work the next row," Marco explains.
Vincent adds: "We use a 130 kW tractor to plough. Our Juwel has al ready worked 400 ha, and now we only had to replace some of the shares for the first time."
Marco says: "Several farmers return to ploughing because it is a tillage method that offers the most for the farmer. You have a better soil struc ture, and better weed and pest control on your fields, which ultimately results in a better crop and harvest."
"All LEMKEN's implements are reli able and built to last. With LEMKEN, you get 100% value for your money, and you're assured to get what you need and more," Vincent concludes.
In Zambia, poultry farming serves as a major source of income and nutri tion for more than one million farmers and households who keep chickens. Novatek is committed to maintain both quality and quantity in the Zambian community. In this article we look at some important factors to keep in mind on your poultry farm.
Heat stress can result in poor returns for farmers. It is important to re member that whilst we enter into the warmest time of the year, that we keep our birds comfortable by ensuring ad equate ventilation. By removing heat, you allow your birds to be comfortable and productive.
Thermoneutral zones promote overall health and performance of animals. Thermoneutral zones are the tempera ture ranges within which the animal does not display symptoms of heat stress. It is in this zone that the animal can maintain a constant body tempera ture and where the animal displays normal behaviour.
Thermoneutral zone for laying hens is between 19 and 22 °C. Thermoneutral zone for broilers is be tween 18 and 22 °C.
Biosecurity is a farm’s first line of defence and should always be in place on a farm; from the access of vehicles to foot dips and personal protective equipment. Access to the right quality of feed and cool, fresh water is key for a production cycle that benefits both the farmer and the birds.
An increase in the humidity of a poultry house can decrease heat loss from the lungs of a bird, exposing the bird to heat stress. It is important to monitor the humidity levels in a poultry operation.
Air flow allows for managing the heat through a poultry house and allows for removal of heat from the house.
Most often, birds will consume the
by Riyashna Rampersadhmost feed in the mornings. This puts the animal at risk of heat stress in the afternoon. It is important to monitor bird behaviour. Active and happy birds are comfortable birds.
Birds usually increase their water intake 2 to 4 times during heat stress conditions. Sufficient cool, fresh water and drinkers should be provided to en courage water intake. Lines should be flushed out regularly to ensure that the water is cool enough for consumption.
Addition of electrolytes into water prior to heat stress conditions also en sures that the mineral loss experienced during heat stress, is reduced.
Supplemental vitamins added into feed, for example Vitamins A, D, E and B are effective to reduce heat stress mortalities in broilers. Vitamin C is another key in layer production as it moderates warm temperature declines relating to egg production and eggshell quality.
Novatek is glad to announce the promotion of Nelia Mbewe from the position of Feed Formulator to the role of Junior Nutritionist.
Novatek has added two new mem bers to their Technical Team, namely Everett Pieterse (Nutritionist) and Riyashna Rampersadh (Technical Manager). The team will ensure that the quality of feed produced meets all regulatory and industry standards. Together, they each hold a wealth of knowledge and are willing to support you as a farmer.
Dr Oscar Blanco (Phibro) visited the team to present training on coccidiosis. Theoretical and practical training form part of the backbone in developing teams, and Novatek aims to equip their team members in providing the best customer service experience.
Infectious bronchitis virus (IBV) infects exclusively birds, with different clinical presentations depending on factors such as the virus variant and the age of the birds (see ProAgri Zambia issues 69, 77, and 79). IB virus (IBV) is known for being highly sensitive to different environmental factors; for example, it is easily destroyed by common disin fectants, UV radiation, high tempera tures, and extreme pH.
Such sensitivity to external factors is not only verified in field viruses, but also in vaccine strains. This means that, by nature, live IBV vaccines could be easily destroyed if certain preventa tive measures are not put in place dur ing their transport, storage, prepara tion, and administration.
IBV enters the birds by colonising the upper respiratory tract (nasal cavity and upper trachea) and the mucous membrane of the eye (conjunctiva). Such structures constitute the portals of entry from which the virus reaches the circulation and spreads to different organs, such as the kidneys.
In young broilers, in which their im mune systems are still developing, the application of IB live vaccines aims, mainly, to locally protect of the portals of entry. Immediately after vaccina tion, the IB vaccine virus colonises the surface of the upper trachea, nostrils, and conjunctiva, avoiding the attach ment of the field strain (competitive exclusion). This is followed by the generation of local immunity at the portal of entry, increasing the number of immune cells in the area and the secretion of immunoglobulin A.
Considering the objectives of early im munisation with live vaccines, as well as the sensitivity of the IBV to environ mental factors, different strategies can be practiced increasing the chances of delivering viable IB vaccine virus to the portals of entry.
Below we discuss some procedures that, when performed correctly, can help to improve the immunisation of young birds against IBV field strain.
The highest level of immunisa tion against infectious bronchitis is reached when live vaccines are applied in a spray form.
As mentioned above, IB vaccina tion in early life aims to increase the immunity at the portal of entry (upper respiratory tract and conjunctiva). This can only be achieved if live vaccine vi rus reaches the portal of entry in spray form. Vaccination in drinking water against IB has erratic and suboptimal results, so it should be avoided.
2. In our region, it is recommended to use coarse spray (droplet size between 100 and 200 microns) (Figure. 1).
Firstly, in our frequently hot and/ or dry environmental conditions, coarse spray reduces the chances of vaccine being evaporated before reaching the chickens.
Secondly, very fine spray would reach deep down the respira tory tract. In our region, where mycoplasma positive flocks are common, this may result in the reactivation of the mycoplasma infection.
3. Use 25 to 30 ml of water for every 100 birds when preparing the vaccine for spray application.
4. Apply a coloured water sta biliser to the vaccine water before vaccine preparation.
Before vaccine preparation, com mercial water stabilisers should be added to the water, with the objec tive of dechlorinating it and improv ing its pH (the ideal pH range is between 5.5 and 7.5). Some of those products are also able to reduce the negative effect of water hardness and bind heavy metals. The addition of a stabiliser is key to a successful immunisation.
Furthermore, the blue dye contained in these products helps to monitor the vaccine distribu tion. When appropriate vaccinating technique is performed, the areas around the eyes and the nostrils of the broilers are blue (Figure. 2).
5. The ideal temperature of the water for preparing and apply ing IB vaccine is between 6 and 10° C (Figure. 1). Studies have demonstrated that, beyond 10 °C, there is a 3.2% reduction on vac cination effectiveness per degree Celsius of temperature increase. For example, in cases in which the wa ter is at 25° C, there will be a drop of almost 50% in effectiveness.
In Zambian field conditions it may be quite difficult to reach the ideal thermal range, but effort should focus on bringing the water temperature as close to the ideal range as possible.
Chilling the water with ice packs before vaccine preparation and
m
9. Vaccinate with the lights ON (Figure. 1). This would result on the chickens looking at the moving sprayer, improving the chances of the vaccine reach ing the eyes, nostrils, and trachea.
10. Crowd the birds on one side of the house, to reduce their movements and improve vaccine distribution (Figure. 1).
11. Walk up and down the house, spraying 50 to 100 cm above the chickens (Figure. 1).
12. Wear protective gear, especial ly goggles and mask (Figure. 1)
13. Open the curtains and restart ventilation 15 to 20 min after the end of the vaccination.
14. Make sure the vaccines are properly scheduled.
There should be a minimum interval of, at least, 12 to 14 days between 2 doses of live infectious bronchitis vaccine, to avoid inter ferences between them. Shorter periods may compromise the effectiveness of the second vac cine, rendering sub-optimal local protection.
15. In order to reach the highest immunisation against IB variant 2, use homologous vaccines.
Homologous vaccines are those that have, at least, 95% similarity with the field strain. The utilisation of the only homologous vaccine against variant 2 (TAbic IB VAR206) has showed the highest protection in laboratory and field trials.
For more information on this and other poultry topics, please visit https://academy.pahc.com/ and register for free.
5. maintaining the low temperature with ice packs inside the sprayer is of great help. Do not add ice cubes on their own since they will dilute the vaccine as they melt. Finally, control periodically the integrity of the ice packs before refreezing them since the leakage of their content into the vaccine solution will be detrimental.
6. Minimise the interval between the preparation of the vaccine and its application.
This will increase the chances of the IB vaccine virus to remain alive by the time it reaches the portal of entry.
7. Vaccinate the birds during the cooler parts of the day.
8. Before spray vaccination, switch off the fans or close the cur tains (Figure. 1). This will reduce the chances of the vaccine being dispersed away from the birds.
Figure 2. Blue stain around the eyes and nostrils, showing successful vac cination (Udi Ashash, 2022).
Figure 1. Good practices for coarse spray vaccination in broilers.Stock feed is the feed manufactured for livestock animals to meet the requirements of a certain species. It can be produced in a mash, crumble, or pelleted form.
Livestock is an investment, so proper feed storage is an integral part of pro tecting the health and safety of your animals. If feed is not stored in the
correct environment, it becomes prone to pests which may aggravate the spread of diseases, the chemical com pounds in the feed may change leading to the growth of bacteria, fungi and mold, and the nutritional value of the feed may be reduced. This in turn will affect the performance of your animals and hence your return on investment.
Points to consider when you store your feed:
• Provide a secure warehouse or storage area
• The area needs to be cool and well ventilated
• The feed needs to be away from direct sunlight and should not be exposed to the rain or any moisture
Store the feed on pallets that keep the feed off the ground. This is done to prevent condensation and mold growth.
Proper feed storage helps to pre serve the quality and nutritive value of the livestock feeds you purchase, and helps save money by preventing spoil age. Feed is approximately 70% of the cost on your livestock enterprises, so make sure you look after your profits by looking after your most expensive production investment.
For more information, contact Brian Sitali Tiger, Feeds Techni cal Advisor on (+26)96-794-62-15 or send an e-mail to Brian.sitli@ tigerfeeds.com.zm.
smoke and spices such as mustard and black pepper, and sweeteners such as sugar or molasses.
• 350 ml brown sugar
• 350 ml ketchup
• 120 ml red wine vinegar
• 120 ml water
• 15 ml Worcestershire sauce
• 35 ml dry mustard
• 10 ml paprika
• 10 ml salt
• 7,5 ml black pepper
During barbecue style cooking, barbecue sauce is used as a flavouring sauce, marinade, or basting for pork, beef and chicken. Barbecue sauce is a ubiquitous condiment that can be used on many other foods as well.
The ingredients of barbecue sauce vary de pending on the recipe, and may even vary within different coun tries. The usual accept ed ingredients, however, are vinegar, tomato paste (or mayonnaise or both) for the base of the sauce, and then liquid
Combine the brown sugar, ketchup, vinegar, water and Worcestershire sauce in a blender. When properly combined, season with mustard, paprika, salt, and pepper and continue blending until smooth.
Choosing the appropriate cheese: Not all cheeses melt in the same way when heated. Some will in fact not melt at all, but instead become stiffer and drier when heated. On the other hand, some good melting cheeses are not suitable for sauce making, as they do not fare well in liquids. Avoid cheeses that are manufactured using acid instead of rennet. These cheeses include most fresh goat milk cheeses, ricotta, queso blanco and Indian paneer.
Cheeses manufactured with rennet have a soft, malleable structure that melts when heated, whereas cheeses manufactured using acid, allows the water in the cheese to be repelled when the cheese is heated. This in turn causes the proteins to stick together and form hard lumps.
The age of the cheese also plays a major part in how the cheese will react in a sauce. As a cheese is aged, the ag ing process adds flavour enhancement, but also causes the fats and proteins to break down into shorter strings. When an aged cheese is then melted, is has less ability to blend, which results in a sauce that is grainy. One way of bypassing this grainy texture while still adding the flavour that an aged cheese will impart to the sauce, is by blending aged and younger cheeses.
This will ensure a cheese sauce with a good flavour profile and a rich, vel vety consistency.
Factors that influence the quality of a cheese sauce:
• When making a cheese sauce, it is important to always add the cheese last and then only heat the sauce long enough for the cheese to melt. The less the cheese is heated, the better. Never let the sauce boil as this will cause the cheese to be come tough and curdle. It is advisable to use the residual heat from the pan to melt the cheese.
• While the whole cheese is cold, break it down as small as possible by shredding, crumbling or dicing the cheese. Small pieces will be quicker and easier to incorporate into the sauce, and working with the cheese while it is cold makes for easier handling.
•
After the cheese has been reduced to smaller pieces, allow it to sit at room temperature, as this will al low the cheese to melt faster when added to the hot liquid.
• Keep stirring to a minimum to prevent the cheese proteins from forming globs.
• Use a thickener (corn-starch or potato flour) to prevent the cheese from curdling.
• Adding lemon juice or wine (in other words an acidic ingredient) will prevent the cheese from be coming stringy. Sprinkle the acidic agent over the shredded cheese before heating.
• Reduced-fat cheeses take longer to melt and are tougher. Shred reduced-fat cheese very finely and melt it over very low heat.
• Do not substitute milk or half-andhalf when a formulation calls for cream, as the higher fat content in the cream will help prevent curdling.
• Do not add too much cheese. Although the flavour of the cheese will improve the taste of the sauce, there also needs to be enough moisture to hold the cheese in suspension.
Steps for making a roux and béchamel sauce:
1. Measure equal amounts of butter and flour.
2. Dice butter into small cubes and melt in saucepan over low heat.
3. Once the butter has melted, begin whisking in the flour.
4. When all the flour is incorporated, continue stirring and cooking the sauce for a few minutes to activate the starch granules.
5. If making a white or light-coloured cheese sauce, keep the heat low enough so the roux does not brown.
6. Add milk. If the roux is hot, the milk should be cool, but if the roux is cool, the milk should be hot. Combining the two ingredients at different temperatures ensures they will heat up at a moderate rate, in other words not too fast or too slow, creating a smooth sauce.
7. Whisk the mixture until smooth; add seasonings as required.
8. Allow the sauce to simmer until it has lost its “floury” taste (approxi mately 20 minutes). Strain out any seasoning or lumps.
9. Remove the pan from the heat and gently blend in the cheese. If the cheese appears not to melt, return the pan to very low heat. Watch it carefully and remove as soon as the cheese is melted.
10. Avoid high heat. Temperature abuse can coagulate the proteins in the cheese and cause a separa tion of fats and solids.
Cottage cheese is categorised as a cultured dairy product. Cottage cheese is the product obtained from a co agulated milk, cream, partly or wholly skimmed milk, reconstituted (pre pared) milk, or a combination of these products. Cottage cheese is a soft, unripened cheese containing about 80% moisture. Cottage cheese can also be made with various additions such as herbs, pickles and spices.
white blood cells and cells of ud der tissue) from milk, prior to further processing. Clarification is achieved through filtration. Milk may be filtered through a perfo rated strainer, fine-wire mesh, or woven cloth (melkdoek) in small dairies. Medium and large dairies use replaceable in-line filters situ ated before the heat exchanger.
Cottage cheese. (Image Source: healthline.com)
Cottage cheese is classified as follows:
• Full fat cottage cheese may also be named cottage cheese, full cream cottage cheese, and creamed cottage cheese with the fat in dry matter content of at least 45%, but not more than 60%.
• Medium fat cottage cheese with the fat in dry matter content of at least 25%, but not more than 45%.
• Low fat cottage cheese with the fat in dry matter content of at least 10%, but not more than 25%.
• Fat-free cottage cheese may also be named skim milk cottage cheese, with the fat in dry mat ter content of at least 10%. Yield: 1 kg full fat cottage cheese from approximately 4,74 kg of whole raw milk and 1 kg low fat cottage cheese from approximately 7,48 kg of whole raw milk.
Milk is a highly perishable prod uct that may turn sour if left at room temperature. Milk is cooled to improve its quality and stabil ity. Milk leaves the cow at ± 37 °C and must be cooled within three hours to 4 °C. During cold storage, the milk must be stirred gently to prevent a cream layer from form ing on top (cream separation by gravity). Raw milk is thus kept in large vertical tanks at the factory or processing plant (2 500 to 150 000 litres) fitted with one or more propeller agitator(s) until further processing proceeds.
2. Clarification of milk
Clarification is the removal of solid impurities (dirt particles,
Clarification of milk. (Image Source: dairyfoods.com)
Prior to separation, the milk is heated to 45 to 60 °C to ensure ef fective separation of the skim milk and cream phase. Heating also in activates the enzyme lipase that is responsible for the development of rancidity in fats. Pre-heating guar antees the highest possible cream quality, that is the lowest amount of free fat in skim milk. Heating takes place in a batch vessel or in a plate heat exchanger.
4. Separation and standardisation of milk for cottage cheese
Standardisation involves the ad justment of the fat content of milk to obtain a product with a defined, guaranteed fat content. Cottage cheese products are classified ac cording to their fat content. The fat content of milk must therefore be adjusted and standardised ac cordingly since the fat content of raw milk varies. Standardisation is preceded by separation of the milk and cream, and then re-mixing the two fractions in the desired proportions.
Take note: Fat-free cottage cheese is made from skim milk and does not require remixing but only separation. Separation: The cream fraction of raw milk is separated from the skim milk by passing pre-heated raw milk (45 to 60 °C) through a conventional or hermetic centrifugal separator.
A centrifugal separator consists of a stack of conical disks kept apart by strips of metal to form separation channels. The milk is fed into a central inlet tube into the bowl and enters the channels
at the outer edge at the bottom of the clarifier. The centrifugal force separates the fat and water phase of the milk. Any solids that may be present are collected at the bottom and discarded. Centrifugal separators thus aid the clarifica tion process.
Conventional separators: Con ventional separators operate at atmospheric pressure and air is therefore present in the product.
Hermetic separators: Hermetic separators on the other hand are airtight and operate under pres sure, thus reducing the air present in the product. The skimming efficiency is increased by 0,01 to 0,02%. Hermetic separators treat the milk gently and with minimum damage to the fat globules.
Standardisation: Standardisation follows directly after separation. Various standardisation methods are available. The method depends on the size of the processing plant and the amount of automation em ployed during the processing.
Batch standardisation: This method is mostly used by small processing plants. It entails the mixing of a calculated quantity of skim milk, cream or full fat milk with the incoming batch of raw milk to obtain a product with a specific fat content. The quantities of the various fractions needed for batch standardisation can be calculated using Pearson's Square. To be able to do this, the fat content of the various fractions must be known.
Continuous or direct standardisation: Large proces sors can afford to invest in auto matic, in-line equipment for con tinuous standardisation. The raw milk is first skimmed (separated) by passing through separators in an in-line system. The fat content of the skim milk and cream frac tions are determined and auto matic standardisation takes place by re-mixing the required amount of cream with the skim milk. The remaining cream or skim milk is diverted and the standardised milk is ready for further processing.
5. Homogenisation of milk for cottage cheese (optional) Homogenisation is the process where the fat globules in the milk products are finely distributed to reduce “creaming”, that is the separation of the cream and skim milk. Homogenisation can be seen as a special type of emulsification process. It is an expensive process that is usually not performed on
small scale by batch operators. Large-scale processors include homogenisation as part of the continuous pasteurisation process. Homogenisation is performed after pre-heating the milk (regenera tive heating step of continuous pasteurisation) because homog enisation is most effective when the milk is slightly heated (60 to 70 °C).
Homogenisation is accomplished by forcing the milk through a small opening at high velocity to cause disruption of the large fat globules to form small, stable fractions. The pre-heated milk enters the homogeniser at 60 to 70 °C, and is homogenised at a pressure of 15 to 25 MPa (150 to 250 bar). A twostage treatment is recommended. Two homogenising heads are used in series. The homogenisation head consists of a high-pressure positive pump that forces the milk through a narrow gap in a specially designed valve. The high pressure on the inlet side causes the fat globules in the milk to break up. Homogenisation takes place at the first homogenising head. The sec ond head operates at a lower pres sure and is used to break up any remaining clumps of fat globules. Homogenisation is an optional pro cess. It has advantages for cheese processors, but also disadvan tages. The processor must decide which is more important.
• The uniform distribution of the fat globules,
• producing a smooth and creamy cottage cheese,
• a whiter coloured product.
Disadvantages include the following:
• the milk cannot be separated (cream and skimmed milk),
• increased sensitivity to sunlight leads to the development of a me tallic taste,
• increased sensitivity to lipase (en zyme), and
• low stability of the protein to tem perature variations.
A. Pasteurisation of milk for cottage cheese
Pasteurisation is a milk heat treat ment that destroys all vegeta tive pathogens and heat sensitive enzymes so that the phosphatase test gives a negative result.
Pasteurisation thus improves the keeping quality.
Although cottage cheese can be made from unpasteurised milk and is considered to have a better fla vour and aroma, the milk is usually pasteurised to eliminate microbial
competition for the starter culture. Various pasteurisation methods are available, depending on the size of the processing plant.
Batch pasteurisation: This method is suitable for small opera tions with less than 2 500 litres of milk per day. The milk is pumped into an open vat or jacketed vat fitted with an agitator where it is heated. The milk is held at least 30 minutes at 65 to 73 °C followed by cooling within 30 minutes to 30 °C.
Continuous pasteurisation: Large processing plants use a continuous high-temperatureshort-time (HTST) method. Milk is heated quickly to 72 to 75 °C for 15 to 40 seconds in a plate heat exchanger.
Five stages of heat exchange can be identified:
A. Regenerative heating: The incoming milk is pumped to the regeneration section of the heat exchanger where it is heated to 60 to 65 °C by heat transfer from freshly pasteurised milk. Up to 92% of the required heat can be recovered in this way. Milk may leave the pasteuriser at this stage to be homogenised and return to the next section.
B. Heating: Milk is further heated indirectly with hot water, vacuum steam, or saturated steam at atmospheric pressures to the re quired temperature (75 to 85 °C).
C. Holding: The hot milk is held at the required temperature in a chamber or a holding pipe for 15 to 20 seconds. The dimensions of the holding pipe must be sufficient to ensure the required residence time and flow rate of the milk. The stainless steel holding pipe slopes upwards and excludes trapped air. The temperature at the end of the pipe is continuously monitored to ensure sufficient pasteurisation. If the required temperature is not maintained for long enough, the
milk is returned to the heating and/or holding sections via the flow diversion valve.
D. Regenerative cooling: The hot milk from the holding section goes to the regeneration section where it is cooled to 10 to 20 °C by heat transfer to the incoming milk.
E. Cooling: Milk is further cooled to 30 °C, first with cold water and finally with chilled water or refriger ant (brine or polyalcohol solutions). The higher the fat content of the milk, the higher the final tempera ture of the cooled milk will be. This prevents the milk from thickening, resulting in clogging of pipelines and filling problems. The mechani cal action involved in pumping and filling thick, cold milk could also cause damage to the fat globules.
Take note: It is required by law in South Africa that processors keep thermo-graphic recordings of the temperature of pasteurisation for at least four weeks; and that ap paratus used must be calibrated monthly to ensure the correctness of the pasteurisation process.
7. Inoculation and incubation of milk for cottage cheese
Inoculation is the addition of start er cultures to a food substance to initiate fermentation reactions. The warm milk (20 to 22 °C) is pumped into the fermentation tank and inoculated with a 0,75% starter culture mixture containing Streptococcus lactis.
The milk and starter culture are mixed thoroughly to ensure even dispersion of the culture in the milk. The inoculated milk is incubated at 21 °C for 14 to 16 hours to allow fermentation to take place until the pH is reduced to 4,5. Fermentation is defined as the conversion of the milk sugar (lactose) into simpler substances such as acids by the action of the starter culture and enzymes. The fermentation tanks are insulated to ensure that an even tempera ture is maintained throughout the incubation period. They are also fitted with rotating stirrers.
8. Rennetting of milk for cottage cheese
Rennetting aids the coagulation of milk proteins to produce a coagu lum or curd that traps the milk fat. This is achieved by the addition of rennet to the fermenting milk. Rennet is an enzyme preparation that was once isolated from the fourth stomach (abomasum) of a calf. Today rennet can be culti vated microbiologically. The rennet is a liquid to which salt, propylene
glycol and a preservative (sodium benzoate) may be added. This preparation is stored at 4 °C and diluted with cold water prior to ad dition to the milk. Between 1 and 2 ml of rennet is added to 450 litres of milk to aid coagulation of the milk. The milk is stirred with the rotating stirrers of the incubation vat to prevent fat separation. The temperature of the milk is raised to 30 to 32 °C and the rennet added. It is then left to set (coagu late) and must remain undisturbed to ensure that a 'gel' is formed.
9. Cutting of coagulum for cot tage cheese
The coagulum is then cut with vertical and horizontal knives into small cubes of between 0,5 and 1,2 cm. This eases the whey separation or syneresis by increas ing the exposed surface areas. The cubes of curds and whey are gently stirred to prevent lump forma tion. Some whey may be removed at this stage. The curd is then left to rest for about 15 minutes.
10. Scalding of cottage cheese curds
Scalding is a heat treatment given to cheese curds to regulate the texture and acidification of the curd. The curds are slowly heated to 55 °C to accelerate the whey separation. Slow heating is neces sary to prevent case hardening. The curd-whey mixture is stirred as soon as the required tempera ture is reached to ease separation.
11. Draining of whey from cottage cheese
Draining aims at removing excess free moisture from a product by gravitation force to obtain partial drying of the product surface. The whey and the curd have separated due to cutting, stirring and scald ing. The whey is drained off either through a tap or by gravity separa tion.
12. Washing of cottage cheese curds (optional)
The curds can be washed 2 to 3 times with potable water at 30 to 32 °C, 14 °C and 4 °C, respective ly. This cools the curds, removes excess acid and lactose and thus inhibits further acid formation through fermentation.
Cottage cheese. (Image Source: healthline.com)
13. Draining of washed cottage cheese curds
The water is removed from the curds by draining it off either through a tap or by gravity separation.
14. Seasoning of cottage cheese (optional)
Salt and other optional seasonings such as peppercorns and herbs may be added at this stage.
15. Filling and sealing of cottage cheese
The containers are filled by au tomatic injection nozzles in large processing plants. Small proces sors can hand fill and seal the containers. Suitable containers include plastic tubs with foil and/ or plastic lids. The containers should be hermetically sealed and stored at 4 °C. A hermetically sealed container is an unopened container that cannot be opened without breaking or damaging the container, seal, adhesive tape or any other attachment which may protect the contents against the entry of micro-organisms.
16. Labelling
Cottage cheese containers are labelled or pre-printed with the necessary information. The label information and presentation must be in accordance with the requirements set out in the Label ling and Advertising Regulations (R2034/1993). Also take note of regulations relating to Dairy Prod ucts and Imitation Dairy Products
R 2581 of 20 November 1987 (as amended by R 1059 of 3 June 1988; R 2141 of 6 October 1989 and R 1465 of 26 August 1994).
Published with acknowledgement to the ARC Agricultural Engineer ing for the use of their manuals. Visit www.arc.agric.za for more information.
Highly pathogenic avian influenza (HPAI) is one of the deadliest dis eases for poultry throughout the world, and some strains may affect humans, who might die from it.
AI, or bird flu, has resulted in the death and mass slaughter of more than 246 million birds worldwide between 2005 and 2020, with peaks in 2006 and 2016. During these two years, about a quarter of the world's countries was affected.
Up to now, several humans have been infected with subtypes of H5N1 and other subtypes, about half of which have succumbed to the disease. There
are no specific vaccines for preventing Influenza A (H5N1) in humans. Because the strains evolve, it is of great impor tance to keep this disease at bay.
Biosecurity and vaccination are fun damental to successful health man agement of poultry. Vaccination helps prevent endemic diseases that are already there, while biosecurity helps prevent the introduction of disease from elsewhere.
A biosecurity programme must take into consideration three factors, name ly location, farm design and operation al procedures, which are all designed
Migratory wild water birds have been proven to spread bird flu. (Source: Pixabay)
Left: Whole flocks of ostriches had to be culled because they were suspected of being infected with avian influenza, and farms had to be quarantined. (Source: Pixabay)
by Tisha Steynto keep pathogens or disease-causing organisms away from the flock.
Isolate farms from other poultry, live stock, and other animals and birds, and keep poultry of the same age and from the same supplier in a poultry house to prevent cross-contamination.
Create a barrier by erecting a fence to prevent any unauthorised person or animal to have access to your poultry house. Design the farm to have a sin gle entrance/exit that can be controlled to keep out humans and animals alike.
Poultry houses must be designed to facilitate proper cleaning daily and dis infecting between flocks. The poultry house must be proof against insects, rodents and wild birds to prevent these unwanted critters carrying disease from sneaking in.
In some areas where ostriches are farmed, no poultry species, includ ing chickens, ducks and geese, were allowed in case they spread AI to the ostriches. (Source: Pixabay)
Prevent the introduction and spread of disease with procedures that control the movement of people, feed, equip ment and animals on the farm. Enforce strict rules to ensure that contamina tion is prevented.
The following procedures must be followed:
Humans
Commercial poultry farmers reduce the risk of humans bringing diseases into their production systems by fencing in their poultry houses. You must enter through a reception area where you sign in, so that, in case of an infec tion, it can be traced to the person who entered at a specific time.
In addition, there is often a walk-
The movement of wild birds cannot be contained, so poultry farm ers must ensure that they protect their birds from random visiting birds. (Source: Pixabay)
Wild birds, like seagulls, are susceptible to bird flu. (Source: Pixabay)
through shower where everybody – farmer, veterinarian, workers and visitors – must have a shower and put on clean clothes and shoes before they are allowed to enter the premises.
Where people are not required to take a shower every time, there must at least be a footbath with disinfectant that they must step into before enter ing the production area.
No clothes or shoes that were worn outside the poultry units are allowed inside, because it has been proven that clothes, dirty hands, and even human hairs can carry the disease. Cloth ing used inside the premises must be washed on the premises to ensure it remains disease-free.
It is not always possible to have all these precautions on your small-scale
Hundreds of sea birds died as a result of AI during a recent out break in the Western Cape. (Source: Pixabay)
farm, but you can insist on restricted entrance, and make sure that you have special clothes, like overalls and boots that you wear only inside the poultry house. Personal hygiene is also impor tant: wash your hands before and after handling chickens.
All farming equipment, as well as poul try feeding and drinking equipment, should be cleaned on the premises to prevent a build-up of bacteria, and pre vent diseases from spreading from one house to the other, or from one bird to another. Any item that is removed from the poultry house must be disinfected before it is returned.
Rodents, like mice and rats, carry lice, mites and flies that can cause disease in poultry. (Source: Pixabay)
It is most important to prevent ve hicles from bringing disease onto your farm. Vehicles that transport chickens, feed, or new litter to your farm, must be sprayed with disinfectant before being allowed onto your property. Their movement must also be restricted to a specific area.
Feed can also contain contaminants, such as mould, which can produce tox ins. To reduce the risk, farmers must buy only the best quality feed from a reputable supplier. For a small poultry farm, it is best to buy feed in small quantities and not in bulk. Feed must be properly stored in a dry, cool place with a lock and where no other people, birds, or rodents can get in. Discard old, mouldy food.
The chickens are kept in houses to limit their contact with all other animals, including other chickens.
It is good practice to group your birds in batches according to the time they arrive and their age. In this way one batch from a specific supplier arrives and leaves at the same time, limiting the possibility of contamination from other suppliers’ farms.
It is essential to clean and disinfect poultry houses and the area surround ing them after a batch has left and before a new batch arrives.
Also, any sick or dead birds must be removed immediately and either buried or burned some distance from your farm.
Keep wild birds away from your chickens. Wild birds, especially migrat ing waterfowl, are known to be carriers of pathogenic avian influenza (HPAI), also known as bird flu, which is highly contagious and deadly. The droppings of wild birds, or dead wild birds, may also pollute drinking water, which may cause disease outbreaks.
Rodents, like rats and mice, are a big concern, because not only do they eat the feed, break eggs and kill young chickens, they also carry diseases and parasites like lice, mites and flies. Poul try houses and food storage facilities must be rodent-proof, and baiting or trapping programmes must be in place to keep their populations in check.
Pets must also be kept out of the production area.
A community must work together to promote biosecurity, because no farm can do it on its own. It is practically impossible to contain disease when chickens are allowed to scavenge around the community for food.
Unless a barrier between these freeranging birds and your poultry house can be erected, it is essential that the community work together to remove sick or dead birds from the rest of the flocks.
Every farmer must buy poultry only
Personal hygiene is of utmost importance, and washing your hands before and after handling chickens is the first step in preventing the spreading of diseases. (Source: Pixabay)
Remove old litter, dirty bags and any rubbish from your poultry houses and yard, and dump it far away from your farm, but in such a way that it does not contaminate the environment.
• Discard old, damp feed as it can also make your birds sick.
Small-scale farmers should not buy feed in bulk, but only in smaller bags to prevent the food from be coming mouldy and making your chickens sick.
Pixabay)
from a reputable source, and keep new birds separate from existing flocks for a few weeks to ensure the new birds are not a health risk, bringing disease to the community.
It is important to inform authorities of any disease outbreak.
It is also important to keep contact with buyers of chickens to a minimum, especially if they are known to travel from farm to farm to buy birds.
Do not eat sick birds or those that have died because of disease.
• It is most important to keep your poultry farm clean in order to keep it free of disease.
• Place a footbath with disinfectant outside the door and use a special pair of shoes for working inside the poultry house. Wash your clothes and keep your body and especially your hands clean.
• Clean and disinfect the poultry houses between batches of chick ens, and leave them empty for at least a week to get rid of diseases that need a host to survive.
• Do not overcrowd your poultry houses. Make sure the birds have enough clean water, fresh air and light – preferably sunlight. Damp, dark and mouldy conditions breed disease.
• Wash your hands before and after handling chickens!
Resources Arbor Acres broiler management guide. (2009) Aviagen https://eu.aviagen.com/assets/ Tech_Center/AA_Broiler/AABroilerHandbook2018-EN.pdf High pathogenic avian influenza (HPAI) situation report. (2022) World Ani mal Health Information System of
World Organisation for Animal
Influenza A (H5) - United Kingdom of Great Britain and Northern Ire land. (2022). World Health Organi sation
Kriel, G. (n.d.) Biosecurity in Poultry
Poultry Farming in South Africa
Sussex cattle are one of the oldest and purest English breeds and are popu lar in Southern Africa's beef industry. The breed descended from horned red cows once found in Sussex and Kent in southern England. These cattle were draft animals for years before ultimate ly being slaughtered for beef at the age of 6 years.
The Sussex is a medium-sized, early maturing beef animal with a smooth, hereditary red coat and a white tail. The breed's easy-to-handle tempera ment has earned it the nickname "trou ble free." The breed is a part of the Bos taurus group.
The cows' maternal instincts, abun dant milk supply, high calving rates, and excellent fertility demonstrate their versatility. Cows’ average weight is 520 to 620 kg; bulls have muscle and depth, and their average weight is 850 kg.
Breeders must dehorn naturally horned Sussex animals. Breeders use polled bulls to introduce polled genet ics into their herds. Polled bull sperm has been imported, and polled genetics are available.
Sussex cattle mature early, so they can be sold right off the veld or pas tures. It is a good converter of concen trate feeds and gains weight quickly, so feedlot operators like them.
hardy, show a good weaning weight, and excellent post-weaning growth. Sussex bulls add weaning weight to crossbreeding programmes.
Sussex bulls with the $X brand mark on their left shoulder have been visu ally inspected by a senior inspector of the Society. When using Sussex bulls, farmers should make sure they have the $X brand.
A Sussex stud breeder gives com mercial beef producers high-quality bulls that work well to improve the quality and profitability of beef.
The Sussex breed produces high-qual ity meat.
African cattle are categorised by humps. Zebu cattle have humps on the thorax, while Sanga cattle have them on the neck. According to DNA tests, Tuli cattle are part of the Sanga group, which dates back over 2 000 years. Migrating tribes brought these early animals to Southern Africa, where they thrived south of the Zambezi. The Tuli is "fertile, profitable, range cattle", ac cording to the Society's logo.
This pure indigenous breed has quali ties that beef farmers value. It has a
medium body size, high fertility, is mostly polled, has easy birthing, lon gevity, hardiness, and adaptability that have been bred into it over at least 2 000 years by natural selection. This makes the breed naturally resistant to both internal and external parasites.
Scientific selection recently focused on economic value, resulting in the modern Tuli. Never has the breed’s har diness and adaptability been compro mised. They tend to have solid white, red, brown, and yellow coloration.
Tuli cows have good fertility, milk production, and low calf mortality with an average weight of 400 to 500 kg, and Tuli bulls have a good feed conver sion ratio and carcass quality with an average weight of 750 to 850 kg. The breed is a part of the Bos taurus afri canus group.
Southern Africa produces the Tuli breed because of its adaptability, hardiness, and capacity to produce high-quality meat from even the worst quality grazing.
The breed does well in sandy, semidesert areas like Namibia, Botswana, and the Northern Cape. It also does well in hot heartwater bushveld areas like Zimbabwe, Limpopo, and the Lowveld of Mpumalanga, as well as
In South Africa, Namibia, Zimbabwe, and Botswana, Sussex Stud breeders can meet the demands of commercial cattle farmers.
Sussex animals can tolerate the harsh cold of the Drakensberg and Eastern Cape mountains as well as the sands of the Kalahari Desert and the warm bushveld of Africa. This demon strates their extraordinary adaptability and superior heat resistance.
Purebred and crossbred Sussex cattle perform well. Bulls are pre-potency,
in high rainfall, sour veld, and highaltitude areas of Mpumalanga, and in KwaZulu-Natal, where redwater, gall sickness, and cold conditions with snow are common.
The Tuli is particularly effective in crossbreeding programmes due to its distinctive genetic make-up, which produces good hybrid vigour and a high proportion of polled calves. Addition ally, compared to many other breeds, Tuli steers and Tuli-cross calves finish quicker on the veld.
Of all the breeds in the world, the Tuli has the highest rib-eye to carcass ra tio. Due to the hardiness of the breed, their meat can actually be labelled as "grass fed" because it can be "fattened up" on the land.
The name Wagyu refers to two Japa nese cattle breeds and means "Japa nese cow". Buddhist leaders strictly forbid eating meat, so these cattle were chosen for their strength. Mar bling is the succulent, flavourful inter muscular fat. Wagyu beef used to only be eaten by royalty and samurais in Japan because it was so good.
International production accounts for 0,2% of premium meat breeds. Raising awareness of the excellent meat qual ity will continue to increase demand. South Africa produces both red and black wagyu. Akauishi has excellent marbling, fertility, and growth. They resemble South African red cattle. The Japanese black has even more mar bling than the Akauishi, and is ideal for the "boutique" meat market and exports. The cows weigh an average of around 450 to 560 kg and bulls can weigh up to 950 kg. The breed is a part of the Bos taurus group.
Due to their high adaptability, Wagyu
cattle are raised all over Southern Af rica. The Wagyu Society encourages its use in crossbreeding with native breeds like the Nguni, Bonsmara, and Beefmas ter, which are primarily British and in digenous, in order to improve the meat quality and fertility of these breeds.
In accordance with the breed defini tion, the term "Wagyu" may only be applied to cattle that are first-line crosses with a minimum of 50% breed content or to registered full-blood or purebred bulls. Farmers must follow a number of moral and animal wel fare rules, keep accurate production records, and castrate bull calves not intended for breeding before they are five months old.
The meat must be hormone-free and have a marbling score of at least three.
Ankole cattle are raised for beef in South Africa. This breed dates back to ancient Egyptian hieroglyphs and has been part of the longhorn cattle tribes for over 6 000 years. The breed migrated down the Nile to Uganda, the Pearl of Africa.
The Banyankole people of Western Uganda, after whom the Ankole was named, believe God created the breed and gave it to the Ankole Kingdom's founders. The Ankole are "Kings' Cattle".
Dual-breed cattle are known for their lean meat and high-quality milk. They have majestic, ivory-looking horns that point to the African sky. Horns con nected to airways help cattle regulate their body temperature.
Roan, strawberry, dark to light brown, and red are some of the coat colours. In the past, Ankoles were managed by their coat colours, body types, behaviour, and horn shapes. The cows weigh an average of around 400 to 540 kg, and bulls can weigh an average of 450 to 720 kg. The breed is a part of the Bos taurus group.
The breed can do well in most of Southern Africa because it can adapt to different climates.
They have the capacity to acclimate to harsh and extreme weather, from cold and rainy to hot and dry desert climates. They are a strong and use ful breed because they can survive on low-quality forage and have a high level of disease and tick resistance.
The breed may be used alone, but due to its extensive use in crossbreeding programmes in Uganda, it has come under threat over time. Lots of milk are produced by the cows, which are val ued in Uganda and is reportedly both tastier and healthier than milk from traditional dairy breeds.
The meat is tasty, lean, low in choles terol, and rich in omega-3 and ome ga-9 fatty acids. According to the An kole Cattle Breeders Society of South Africa, it will undoubtedly attract the attention of customers and markets who are concerned about their health.
Ankole cow and calves. (Source: Facebook by Ankole Cattle Breeders' Society of South Africa)
Southafrica.co.za. (2022). South Af rican Beef Breeds. [online] Available at: https://southafrica.co.za/southafrican-beef-breeds.html
Loubser, A., Schutte, N. and Hofmeyr, I., (2007). Cattle breeds of South Africa. Pretoria, AgriCon nect, Pages 97-165.
W hen discussing textiles, the term "angora" by itself always and exclusively refers to the hair of Angora rabbits.
The hair of Angora rabbits is one of five keratinic textile fibres of animal origin that have significant economic value. Sheep's wool, at over 1,3 mil lion metric tonnes annually, is by far the most important fibre. The other four, mohair, angora, cashmere, and alpaca, each produce between 5 000 and 30 000 tonnes annually, and their unique fineness, lustre, and feel make them ideal for use in high-end luxury goods. In the textile industry, angora is ranked among the "noble" fibres.
• down: shortest hair (6 cm), rounded point, barely visible, very fine body (14 µ). Thermic insula tion undercoat has 60 guide hairs. Angora hair's length allows thread cohesion, giving it textile value. Because of the slight relief in the cuticle, rabbit hair has a low friction coefficient. This results in softness but also slipping. Angora hair is twisted and stays in the thread because of its length. Using ordinary rabbit hair to replace angora produces low-quality threads that spread everywhere. This is a fraudulent process that harms the Angora industry.
Although Angora rabbits can be found in a wide range of colours, only the albino variety is currently bred for commercial use.
The animal's pure white fur is ideal for the process of dying. In many countries, breeders of Angora rabbits of various colours raise the animals so that the breeders can make undyed artisanal fabrics with subtle colour pat terns.
All of the hairs are medullated, mak ing them less dense than wool (1,1 versus 1,3) while still providing excel lent warmth. They share every quality of keratin, including insulating proper ties, a high water-holding capacity, and a favourable reaction to dye.
Curing: tanning skins with hair. Shearing: separating implanted hair from skin.
Knife marks: skinner's knife slits or perforations.
Skinning: removing animal skin from a carcass.
Brushing: gently repositioning hair during the curing process.
Pellicle: thin collagenous film on flesh.
Length - Angora hair is unusually long due to a prolonged active phase of the hair follicle cycle. It grows for 14 weeks, whereas ordinary (short) rabbit hair grows for only five weeks. Angora rabbits have a recessive gene that is responsible for the long hair. Aside from its length, the coat contains the three classic rabbit hair types.
• guide hairs: longest (10 to 11 cm), roughest; they guide the coat;
• guard hairs ("barbes"): shorter than guide hairs (8 cm); their rough points lie on the coat and seal it (covering hair); four per guide hair;
Fur: rabbit hair and skin. Glossing: dyeing cured fur. Moulting: hair follicle reactivation. Former hair is hydrolysed to make way for new hair.
Moulting zone: area of skin with ac tive hair follicles. Dark blue patches on the pelt's skin. Slaughter interrupts hair growth, making it easy to shed or shorten.
The hair is collected every 90 to 100 days, when the follicles are in the rest ing stage and before the hair starts falling out and causes felting that reduces value. The hair is cut with scis sors, or electric or manual shears, or collected by depilation.
Depilation is the method of pluck ing the loose hair, but using shear products make shaving rabbits faster, easier, and less stressful.
French-type Angora rabbit hair is better collected by depilation than by shearing or scissors. Their genotypes differ in how quickly hair follicle growth resumes after collection.
Angoras really do not like heat over 30 °C. Low temperatures (below 10 °C) are a problem after hair collection. Open-air production has long been the norm, but denuded rabbits must be protected, especially when depilation is used. Breeders use two-stage depila tion, leaving a "back" that is later removed; body-coat, warmers, postdepilation boxes, et cetera.
Angora rabbits have specific dietary needs that differ from those of meat rab bits. When an Angora is at the height of its productive capabilities, it resembles a normal adult rabbit. They will reach their full size and can only reproduce with a select few animals at a time.
However, they must produce more than 2 kilogrammes of dry proteins per year, including more than 1 kilo gramme of keratin (hair) and the same quantity from the internal sheath of the hair follicle. This is roughly the same as having 7 or 8 kilogrammes of lean muscle mass.
Adult Angoras tend to die in the days following hair collection because they have trouble regulating their body temperature. They are much more likely to get sick from a cold or the flu (pasteurella, coryza, et cetera). There fore, the breeder needs to be vigilant about maintaining a clean environment (frequent litter renewal, cleaning, dis infecting).
Because first-year Angora output is noticeably lower, 650 g compared to 1 kg, replacing working females with young does reduce average production levels. The average yearly renewal rate is between 25 and 35%.
The interval between collections is the most important, based on weight. This effect is attenuated when considering annual output.
Shearing reduces adult doe produc tivity by 30% in the (depilated) French strain. For French strains, the first four hair collections represent 11%, 60%, 81%, and 93% of adult production. It seems that the German strain is more advanced, as the fourth and even the third collection show that it has reached its full potential.
Male French rabbits have 20% less hair than females. Literature reports a difference of 0 to 15% for the German strain, with most citing 10% less for male rabbits. Live weight is irrelevant, except during growth, but should cor relate with collection number (first, second, et cetera).
Winter collections are always 4 to 30% heavier than summer collections.
Higher strain productivity reduces the seasonal effect.
Other factors like birth season have been studied, but more data is needed to confirm these findings. Diet (defi ciencies), temperature, and comfort all affect hair growth.
Non-genetic hair production factors
Length, down fineness, guard-hair di ameter, fur structure, and composition are Angora hair quality parameters. Last, woolly fur differs from guardhaired fur. The latter include those with over 70% full guard hairs (that is pointed ends) and less than 1% of fibre shorter than 15 mm, according to the 1992 Corvallis Convention.
A quality parameter is felting or dirty fur. The time between haircuts affects hair length. The collection method distinguishes guard hair from woolly hair. At least for the first harvest, the number of collections is important for all rabbit strains, and for the second and third collections in French strains, where young rabbits still produce woolly fur after depilation.
The sex factor is weaker in the Ger man strain than in the French strain, but males tend to feel it more. Live weight and season have less effect on adults; the length ratio of underfur to guard hair is less in summer than in winter: 55% in summer versus 65% in winter.
The information provided in this
Lebas, F., Coudert, P., de Rocham beau, H. & Thébault, R. (1997). The rabbit - Husbandry, health, and
92-5-103441-9.
Jute Mallow and Ethiopian Kale are two ancient African plants that are used as leafy green vegetables.
Jute mallow (Corchorus olitorius) Jute mallow belongs to the Malvaceae family, one of the important leafy veg etables in most parts of Africa, includ ing Southern Africa.
Its origins are unknown because it has been around for ages in tropical and subtropical regions all over the world.
Leaves and young shoots are nor mally harvested when about 20 to 30 cm long. These are boiled with locust beans (Parkia biglobosa), lemon or olive oil, steamed and pureed, and added to soup or chicken dishes. Young leaves are also added to salads.
The leaves are also dried and used to make tea or to thicken dishes. When pounded into flour, it can be stored for quite some time. The seeds are also edible.
In India, Bangladesh and China, the plant is cultivated for its fibre. The stem is the main source of jute used in sack cloth and paper, among other uses. The wood is light and soft and is used in making sulphur matches.
The plant is easily propagated from seeds. Soak the seeds in warm water for 24 hours for the best germination results before sowing directly in the soil.
Seed can be scattered into seed beds containing fine soil. Mixing the seed with sand makes it easier to sow evenly. Seed can also be planted in rows 20 to 30 cm apart.
Sow seeds in full sun at the begin ning of the rainy season. If planted in rich soil, no fertilisers are needed, but nitrogen will enhance rapid growth. If planted in the dry season, controlled manual watering is necessary as the plant suffers when the soil is water logged or too dry.
Four to six weeks after planting, when the shoots are 10 to 20 cm long, they should be transplanted. The first harvest is ready for cutting when the shoots are between 20 and 30 cm long. This cutting stimulates the develop ment of side shoots. If you cut every two to three weeks, a total of up to eight cuttings is possible.
Brassica carinata and B. juncea, which are often confused because they are so similar, are the two most widely used leafy vegetable species in Africa.
tive potential. Researchers pointed out that in general, the consumption of B. carinata should be encouraged as part of chemo-preventive measures to combat prevalence of aflatoxin-induced diseases. The seeds are used to relief stomach aches.
The species tolerates a wide range of climatic conditions and can be grown in temperate to tropical zones. In cool regions it is suitable as a leaf crop, but in other areas it can also be grown for the seed.
The plant grows best in areas where annual daytime temperatures are be tween 10 and 25 °C, but it can tolerate 5 to 35 °C. It is successful in full sun when planted in well-drained, fertile, and preferably alkaline soil. The plant grows in almost any soil, but prefers a pH in the range 5,5 to 8.
Flowering is delayed when the leaves are regularly harvested. Seedlings of varieties with larger leaves like those found in West Africa and Tanzania, must be planted at a spacing of about 75 x 50 cm.
Varieties with smaller leaves found in Zimbabwe, can be planted with a spacing of 50 x 35 cm. Once the plant is established, the leaves can be fre quently harvested. The smaller-leaved varieties are often collected in the form of shoots.
The leaves contain almost all the nutrients needed by humans, includ ing lipids, protein, and carbohydrates. They are rich in beta-carotene, iron, calcium, and antioxidants, as well as micro-nutrients such as potassium, magnesium, iron, copper, and manga nese. It is an essential as a source of energy in human and animal nutrition.
All parts of the plant have been used as medicine to treat various illnesses, including aches and pains, fever, dys entery, enteritis, pectoral pains, and tumours. It contains iron and folate that are useful to avoid anaemia. The leaves are also used to treat cystitis, gonorrhoea, and dysuria or painful urination. The seeds are purgative. The high fibre content makes the leaves fill ing and good for weight loss.
B. carinata, also known as Ethiopian or Abyssinian cabbage, is grown in East African, West African, Central and Southern African countries, as well as Madagascar, Asia, and India.
The waxy stem, light-green stalked leaves, and immature flowering stems with their yellow flowers are edible. Aviation biofuel for jet engines have been developed from the plant.
Leaves and young stems are harvest ed when they are 30 cm tall. They are eaten raw or cooked, and have a mild and pleasant cabbage flavour. Young growth can be finely shredded and used in salad, while the older leaves are cooked like cabbage leaves. Im mature flowering stems are cooked and used like broccoli, and the seed can be crushed and used as a condiment.
B. carinata has proven cancer preven
I
n pig farming, optimum management is essential as this determines the success of the venture.
The general production cycle of pig farming begins with a sow mating with a boar, or the fertilisation of ova through artificial insemination. The average gestation period of a sow is 114 days, after which it gives birth to a litter. Weaning is usually under taken at three weeks, after which the weaners are taken to a nursery after having their tails docked, ears notched, needle teeth clipped, navel disinfected, been castrated, and receiving their iron shot.
From the nursery, the pigs are moved to a grower-finisher facility where they may be slaughtered or sold upon reaching the desired market weight or size. At the end of the cycle, the gilts/boars can be replaced, and the cycle starts afresh again.
To ensure that the Life Cycle As sessment (LCA) is proficiently undertaken, key farm activities will be centred on the management of:
• the use of direct energy and water;
• manure and waste,
• upkeep of the breeding herd,
• nursery pigs,
• growers/finishers and pigs for slaughter;
• feed production, and
• feed processing.
This model of functionality is common ly applied to an all-round integrated pig farming system.
Managing animals that are newly introduced to the breeding herd should be a high priority if maximum reproductive efficiency is to be achieved. Good repro ductive and nutritional management pays
dividends through an increased number of pigs farrowed live and weaned.
For reproductive soundness, boars should be at least seven and a half months of age and should be evaluated on:
• mating behaviour,
• libido,
• mounting,
• mating, and
• their quality of semen.
When it comes to the sow, the energy intake of selected gilts should be restricted to prevent overweight conditions. Moving gilts to new pens, increased exercise, and daily exposure to boars beginning between 160 and 180 days of age, will help encourage the onset of oestrus (a recurring period of sexual receptivity and fertility).
Breeding should be delayed until the second or third oestrus to increase the probability of large litters and prevent dystocia (difficult farrowing).
Gilts that do not conceive after mat ing at two oestrous periods should be marketed. Likewise, gilts that have not expressed heat by nine months of age should be culled. During gestation, gilts should be fed to gain about 34,1 kg and not become overly fat.
Farmworkers must ensure the piglets are able to suck from the udder as soon as possible after birth. Sucking of the piglets stimulates the sow to let down her milk. Weak piglets may need to be aided during this period. It is important that the piglets immedi ately take advantage of the first milk (colostrum) and the colostrum should be taken by all the piglets on the same day they are born. This is because the colostrum aids immensely in boosting their immune system and defending them from diseases.
Boars should be replaced when they become too large to serve most of the sows on the farm.
Boars usually have a maximum
working life of between 18 to 24 months, meaning replacement should be under taken when they are 30 to 36 months old. It is very important to keep record of the boars' use so that infertile ones can be detected and replaced as soon as possible.
A low sex drive (libido) can also be a problem. Some boars are slow workers and are sometimes reluctant and only now and then willing to work. Such boars may need to be substituted.
If replacement gilts are not available when needed or if they do not comply with the requirements, gilts should be bought. It is desirable to buy the gilts from the same farm where the boars come from, because in this way the previous owner can advise you on the breeding policy for a small pig farm.
The overall project management system for a piggery looks at:
• conception and initiation of the project,
• definition of farm objectives
and planning,
• launch/execution of project,
• performance and control, and
• piggery project closing.
The conception was explained in the previous article about piggery. The definition and planning will look at ele ments such as scope and budget, work breakdown schedule, the Gantt chart, communication plan, and risk manage ment of the project.
The launch and execution cover the project status and tracking, key performance indicators (KPIs), quality maintenance and project forecasts. Performance and control include aspects such as the project objec tives, quality deliverables, effort and cost tracking, and the piggery project performance.
Project closing seeks to ensure that the project punch list was achieved and the processing of a report for fu ture reference and record-keeping for the project.
want to make decisions that improve your yield and bottom line. Valley® Irrigation is here to provide you with the equipment and technology you need to achieve maximum productivity and profitability. No matter your field size or budget, we have the best irrigation solution for you.
Whether you’re installing irrigation equipment for the first time, replacing an aging pivot or upgrading your current equipment, there’s no question that it’s a big investment
and a significant commitment. Determining exactly what you need is crucial to the way you farm.
us to help you design a customized solution
your operation.