ENVIRONMENTAL PORTFOLIO
STUDENT: ZACH BARKIN INSTRUCTOR: MARY POLITES TSM2001
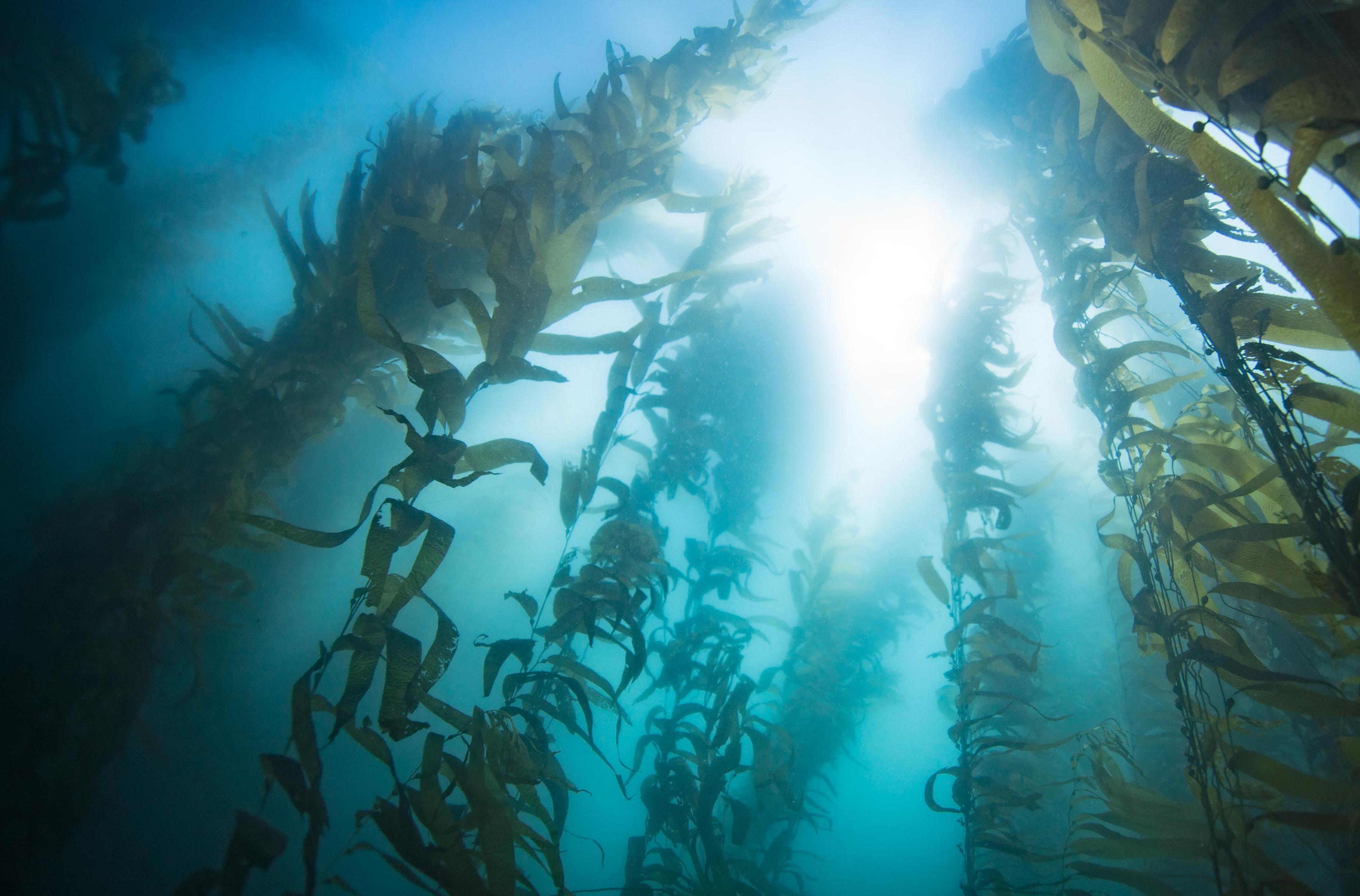
IMAGE: Custom House Wharf

Courtesy of Benchmark Real Estate
COVER IMAGE: Pagniello, C. (2018)
CUSTOM HOUSE WHARF| ZACH BARKINIMAGE: Custom House Wharf
Courtesy of Benchmark Real Estate
COVER IMAGE: Pagniello, C. (2018)
CUSTOM HOUSE WHARF| ZACH BARKINLOCATION SALEM, MA
BOSTON ARCHITECTURAL COLLEGE, MASTER OF DESIGN STUDIES REAL ESTATE DEVELOPMENT, EXP. 2022 CERTIFICATE: SUSTAINABILITY
UNIVERSITY AT BUFFALO BACHELOR OF SCIENCE BUSINESS ADMINISTRATION, 2014 MINOR: URBAN PLANNING
• FLY FISHING
• AGRICULTURE AND GARDENING
• WILD LIFE
• PAINTING
I am a real estate professional who is passionate about making the built environment more sustainable and ecologically proficient.
Financial Analyst at multi-family residential real estate firm Berkshire Residential Investments. This mix of professional experience has allowed me to become very proficient at data analytics.
BERKSHIRE RESIDENTIAL SENIOR FINANCIAL ANALYST- 4 YEARS
THE MENTOR NETWORK FINANCIAL ANALYST -2 YEARS
• KELP FARM
• COMPOSTING
• RECYCLING
• SUSTAINABLE CONSUMPTION
• REDUCED MEAT INTAKE
• PUBLIC TRANSPORTATION
I received a Bachelors of Science in Business Administration from the University at Buffalo in 2014. In addition to my degree concentrating in Finance, I pursued a minor in Urban Planning and participated in a projected documenting the spoken word history of the Commodore Perry Municipal Housing Project in Buffalo, NY.
After school I worked at several different companies in order to establish a base of professional experience. These included an Underwriting Assistant for Hanover Insurance and Financial Analyst at the Human Services company the Mentor Network. Currently, I work as a Senior
In 2020 I decided that in order to move my career in a direction that could have a positive impact of the planet, I would need to expand my education. I began pursuing my degree at Boston Architectural College in Real Estate Development with a concentration on Sustainability. While at school I have participated in a 3i Home consulting project, laying the groundwork for a non-profit to develop a semi-assisted living housing development. Additionally, I have begun to develop a kelp and mollusk farming venture on the north shore of Massachusetts.
A survey of my ecological footprint illustrates that even while being relatively conscious about my environmental impact, I still take up a very large amount of ecological space. My biggest consumption category is from shelter. I live in a single family home, that is old and difficult to heat and am not surprised to see that having a major impact on my ecological impact. This
exercise has made me strive to improve the aspects I can of my home to lessen it’s environmental impact. My carbon Footprint is predominantly driven by the energy generated by my home.
IF EVERYONE LIVED LIKE ME THERE WOULD NEED TO BE: 3.6 EARTHS
streamline the process of submitting for the COTE Top Ten award, this tool will allow easy, consistent calculation and evaluation of project performance metrics and benchmarking.
Other Climate Zone(?):
Note: This version is not compatible with Excel 2016 or older. For questions email cote@aia.org, we are looking to improve the tool, and appreciate your feedback!
COTE
Reasonable
PROJECT INFORMATION
Development team
Corey Squire, AIA Bora Architects, Portland, OR
Z Smith, FAIA EDR, New Orleans, LA Billie Faircloth, FAIA KieranTimberlake, Philadelphia, PA
Janki A Vyas, AIA KARMA co/lab, Philadelphia, PA
Ryan Welch
KieranTimberlake, Philadelphia, PA
Total Building Area(?) 31,276 Gross sf Site Area(?) 37,414 sf Regularly occupied space(?) 28,148 sf Avg daily occupancy(?) 113 People Peak occupancy(?) 133 People FTEs(?) 100 People
Annual days of operation(?) 260 Days Avg. daily hours of operation(?) 12 hours Total Construction Cost(?) 39,821,250 USD FAR 0.84
Program Breakdown(?) % of Building Area
Building Program #1 Warehouse 35% Building Program #2 Office 20% Building Program #3 Laboratory 40% Building Program #4 Services - General 5% Building Program #5 Building Program #6 Building Program #7 Building Program #8 Total must equal 100% 100%
The project is the development of industrial and labs space. The site is located on a 150 year old wharf in Portland Maine in the center of the city’s working waterfront zone. This restricts the buildings program to uses that support the cities working waterfront,, including it’s shipping and fishing industries.
The proposed program would support aqua-cultural production as it becomes more prevalent in the region’s economy.
This includes the incorporation of shellfish and kelp processing space as well as laboratory and hatchery space on the buildings upper levels. The buildings location on the wharf allows for easy boat access for farmers as well as the potential for the hatchery to leverage the salt water below.
In addition to the benefits, the site also creates immense design challenges. The building's resiliency to storms and rising
seas has to be factored into any design considerations. Additionally, rain-water runoff and pollution concerns must be carefully addressed. As the proposed program includes laboratory and hatchery spaces there is additional concern for the waste management system in place.
The building is the final piece in the renovation of several structures occupying the historic wharf. For decades the restaurant and seafood industry has made
the wharf a community destination and has supported Portland’s rich maritime history. It is essential that the design of the space continues to contribute to the allure and character of the city serving as a community center.
The city of Portland has experienced a renaissance over the past 20 years. The maritime charm and creative presence of the citizens has created a prosperous and unique place along the eastern seaboard. Portland enjoys a multitude of unique high quality restaurants, breweries, artisans and shops. The working waterfront at the center of the city is rare among those of this scale on the east coast and remains a focal point of it's character.
As the jump off to the natural beauty of Maine, the city enjoys a heavy amount of tourist activity year round. It is well known for its seafood industry and the site of boats filled with lobster, scallops and oysters draws in travelers from around the world. In the summer a cruise ship and ferry terminal, located only a quarter mile away from Custom House Wharf, regularly delivers thousands of people to the shops and restaurants of the famed Commercial
Street and the cobbled alleys of the city’s Old Port district. The acquisition of Custom House Wharf provides a unique opportunity for investors to become part of the fabric of this unique and vibrant city.
After a period of over-commercialization of the cities waterfront Portland acted to conserve the city’s maritime industrial center. They created the Waterfront Central zone to “protect and nurture: waterdependent and marine related support
uses”. The zone prioritizes marine uses and demands that the first floor of every building be predominantly occupied by a direct marine use as indicated on the permitted uses to the right. The zone supports the use of a variety of “non marine commercial uses” as long as they do not interfere with marine supported uses.
A CONNECTION NODE FOR THE CITY OF PORTLAND
Over the centuries the wharf has served as a center for fishing and maritime industries. It housed the Casco Bay and terminal, in the building that now holds Gilbert's Chowder House. The terminal served as a major transportation link for the city of Portland for decades, connecting the residents of Casco bay to the city via Steamboat. Today there are still several ferries that go out of the adjacent pier. The wharf includes a marina for fishing vessels to unload their
catch to a processing facility, as well as, a recreational marina for boaters to dock their boats onto restaurants.
A bike path surrounds the perimeter of the peninsula and runs all the way to the eastern end of the city. Portland supports a bus system with multiple stops downtown with service reaching the surrounding suburbs. The WCZ zone of the city supports minimized parking requirements however this could be supplemented
by the density of the downtown and the favorable walkability of the city.
Interstate 295 runs along the western bay of the city and connects to the adjacent towns including Scarborough, Westbrook and Freeport. From the project site commuting times to large car accessible residential communities range from about 5 minutes to 20 minutes. Portland features its own Jetport and is an hour and a half drive from Boston (Walk Score, 2022).
Average Daily Occupancy 113
No. of occupants commuting by single-occupancy gas vehicle(?) 75
Percent of occupants commuting by single-occupancy vehicle 67% 76% Weekly Avg.
One of the oldest in Portland, Custom House Wharf was built in 1807. It was purchased by the proprietors of Custom House Wharf in 1836, and kept under family ownership until earlier this year, when it was put up for sale.
A landmark on the wharf is Harbor Fish Market. Since the late 1800’s the fish market has been a premier destination for fresh seafood. Harborfish is staple of the working waterfront zone and a
crucial element to the character of the property. Likewise, Boone’s Fishhouse & Oyster Room dates back to 1898, and has continued to serve the myriad of locals and tourists that flock to their deck every year since. The history of the wharf is what truly makes this property special and it is imperative that the maritime tradition and character of the property is upheld in our design and development.
In addition to the fishing industry,
Maine enjoys a rich history in the timber industry. Forests in are regularly harvested for supplies of both pine and hardwoods. This industry was the driving force of the region’s shipbuilding prowess, and also left an indisputable impact on the cities built environment.
Portland has a rich collection of architecture from the Victorian Era after a fire destroyed the majority of the city’s original buildings in the 1860’s. As such,
many of the buildings in the area, include dramatic mansard roofs and ornate architectural details.
The historic Old Port of Portland is predominantly composed of historic brick buildings with several institutional Granite buildings such as the Custom House and City Hall. This is largely due to the large supply of granite available on New England’s coast line. Imagery below provided by Benchmark Real Estate.
The project is part of a redevelopment plan focused on the fusion of Portland’s maritime industry and recreational benefits water can provide. The plan is to develop a mix of commercial and lab space to reinvigorate the wharf. It paves the way for a new era of seafood processing that supports conventional fishing economies and space for higher tech jobs. The pier acts as a node for both fisherman and science. It’s location in the center of the city helps bolster the local economy and while residents of the city can easily walk to their place of work.
Maine has long been a center for the fishing industry supporting not only New England, but the entire United States. As we move into the 20th century however the availability of wild caught seafood and the impact demand for these products has on the natural ecosystem is considerable.
These problems are now generating interest in the aquaculture industry throughout the world. As a result the sector is foretasted to grow immensely over the next ten years, leading to potential subcontinental increased demand throughout this industrial sector. Aquaculture is a delicate balance between fishing, farming and hard science. In order to support the continued growth of this industry, buildings will need to be well equipped to handle not only the processing of the product, but also to house the hard science research that supports nursery operations.
The site faces the south east towards the Atlantic Ocean. A design should account for winds coming off of the sea, as well as weather moving in from the west. The sun faces the south easterly facing wall of the building.
As the building is on the ocean there is substantial storm risk to the building. Average tides fluctuate around 12 ft daily, with variability depending on the tidal cycle. The depth of the ocean reaches 24’ off of the south east end of the wharf.
Wharfs on the east coast carry substantial opportunity to support marine life to due the natural structure and shelter they provide. A variety of flora including kelp, oarweed and irish moss can set to the wood supports. Invertebrates such as crabs and starfish scavenge waste and fish can rely on the structure for shelter.
The south east facade of the building requires a 40° sun shade
The south east facade of the building requires a 30° sun shade
The south east facade of the building requires a 10° sun shade
The south east facade of the building requires a 30° sun shade
CLIMATE CONSULTANT -ASHRAE STANDARD 55-2004 USING PMV
The Psychometric Chart is a tool developed by climate consultant that allows for the review of approximate site climate data and applies it to a building’s potential for human comfort.
Due to the Maine’s variable and cold climate the natural amount of time that lends itself to human comfort is minimal at just 489 hours or 5.6% of the total time throughout a year that a building could meet ASHRAES comfort standards.
Due to the challenging conditions the environment provides there are a multitude of steps that can be taken in the design of the structure. The addition of outside heat and de-humidification are a necessity for the site and accounts for 59.5% of the building comfort range or 5,212 hours. This analysis concludes that an external heating system would be required and passive design elements would only allow for the mitigation of energy usage.
It is essential that the building includes internal heat gain design elements that would account for approximately 20.9% or 1,833 hours with the standard. The incorporation of additional passive solar direct gain and passive design measures can provide approximately a 13.4% or 1177 hours of comfort.
Due to the building’s location on the coast the addition of a dehumidification system would provide the the building
an additional 5.2% or approximately 454 hrs of comfort, while dehumidification for cooling accounts just 1.9% of the anticipated comfort or just 165 hours.
Solar glazing is a design element that emits direct sunlight into a space to passivley heat buildings in colder months. The technology could be applied to the southeast facade oriented no more then 25º of the building. The building has been designed to include a large glass facade on the southernly side to help maximize the impact of winter sun exposure and passive solar heat gains. The thermal
energy would store a portion of the heat gained during the day. Due to the site’s northern location and particularly harsh winters of the northern Atlantic the incorporation of movable insulation over the glazing in the evenings could be an effective way to heighten the impact of the glazing.
The majority of sunlight admitted into the space during the daytime will be stored inside the space for release in nighttime hours. The incorporation of concrete tiles into the design can absorb and store thermal heat. Floors are a minimum thickness of 4 inches. Floors exposed to solar glazing will be more capable of storing the absorbed thermal energy.
In Maine where temperatures often fall outside of the ASHRAE comfort zone due to cold temperatures the storage and maintenance of heat in the day is incredibly valuable. An exposed surface area to a solar glazing are should range from 3:1 to 9:1. The higher the ration the more stored heat ant the more stable the indoor temperature will become. Floors that are a dark color will absorb more heat,
Due to the site’s location on a wharf and the proposed program in aquaculture t there is significant opportunity for the building to become an ecological node on a dense urban area. The site will have a large green roof as well as tanks to help support the aqua cultural nursery operations. The living roof will incorporate native shore plants that can help support and shelter sea birds that will be in the area. As the last building on the wharf the site can become an ecological haven
for a diversity of wildlife that populates Penobscot Bay. In addition to greenery on the roof the addition of plantings along the building will help buffer runoff from the building with the slanted roof on the south east side of the building draining into raised native planters. The wharf itself provides significant shelter and opportunities to bolster ecological life. The addition of fuzzy ropes and the planting of sea plants in between pylons could support and foster marine life.
Green roof area 2,854 sf - sf
31,276
18,000
19,414
37,414
A wharf, like a reef, can provide critical shelter for species of fin fish and other marine creatures. (Lawrence, 2020)
An idea first conceptualized by Scape Studios in the Gowanas Canal, stringing ropes and netting between pylons can help create a more natural environment for life such as sponges, plants and mollusk to gain a foothold (Scape Studio, 2017).
The building will support aquacultural development through the cultivation of kelp, mussels and oysters. These species are all native to the waters surrounding the project. The introduction of these species under the wharf can provide numerous ecological benefits including water quality improvements and the reduction in nutrient excess (Greenwave, 2022)
As a seafood processing building, water use will be an important factor when considering the buildings overall sustainability objectives. Water is used to rinse and process seafood. In addition, ice making plays a crucial role in the preservation and logistics of the building operations. On top of this the building needs to be able to support a substantial amount of FTE's from industrial and lab operations.
The primary use of water for irrigation is a living roof and planters that will flank the southeast side of the building. As mentioned, in the ecology section of the analysis the plants w ill be native plant's to the coast Maine Ecology. This will reduce the amount of water requited for irrigation to nearly nothing.
Like wise the structure's living roof will be grasses and plants that can help to support ecological corridors on the wharf. The structures sloped roof provides rain water collection that could be used in the establishment of these native plants on the roof or planters.
Is potable water used for irrigation? No Proposed Design Baseline #1: All Turf Baseline #2: All Native Irrigated Area (potable or non-potable) 4,000 sf 4,000 4,000 Summer Evapotranspiration Cool Humid 3.8 3.8 3.8 Plant Quality Factor (Qf) Water stress 0.4 0.4 0.4 Type of plantings (Plant Factor) Native plants 0.2 1 0.2 Irrigation efficiency Drip Irrigation 0.9 0.75 0.9 842 5,050 842
Month Irrigation Co. gal 83% 0%
January 31% 260.9 February 38% 319.9 March 60% 505.0 April 77% 648.1 May 88% 740.7 June 99% 833.3 July 100% 841.7 August 100% 841.7 September 77% 648.1 October 60% 505.0 November 38% 319.9 December 30% 252.5
Annual Irrigation Water Use 6,717 gal / yr
Rain water collection was a focal point of the roof design, particularly it's slant over the loading bays and seafood processing facilities. Likewise collection of seawater will be used in the hatchery operations, pumping water from Penobscott Bay.
A cistern to collect and process the rain water is included in the spatial planning of the interior structure. The location of the building on a wharf provides additional challenges but as the building features a
large industrial footprint storage tanks and treatment can be placed near the buildings loading docks. As identified in the climate analysis, Maine receives a high amount of precipitation. This is a resources that can and should be included in the overall design considerations of the project
In addition to this the plan calls to increase vegetation on the site minimizing using raised planters. The amount of runoff headed directly into the ocean should
2 - Account for Rainwater and Reclaimed Water (Grey/Black)
therefore be minimized. This can have an immediate positive impact on the building's ecological impact all while beautifying the site.
Predicted gal/mo Measured gal/mo
Month Demand1 Potable Rainwater3 Reclaimed grey/black3 Potable2 Rainwater3 Reclaimed grey/black3
January 10,986 4,417 6,569 0 3,533 5,255 0
February 11,045 4,728 6,317 0 3,783 5,053 0
March 11,230 2,989 8,241 0 2,391 6,593 0 April 11,373 3,579 7,794 0 2,863 6,235 0 May 11,466 4,100 7,366 0 3,280 5,893 0
June 11,558 4,542 7,016 0 3,634 5,613 0 July 11,567 4,997 6,569 0 3,998 5,255 0 August 11,567 5,464 6,103 0 4,371 4,882 0 September 11,373 4,201 7,172 0 3,361 5,737 0
October 11,230 1,765 9,465 0 1,412 7,572 0 November 11,045 1,463 9,582 0 1,170 7,665 0 December 10,978 3,164 7,813 0 2,531 6,251 0
Total (gal) 135,417 45,410 90,007 0 36,328 72,006 0
Total Annual Potable Rainwater Grey/Black Total
Predicted 135,417 33.5% 66.5% 0.0% 100.0%
Measured 108,334 33.5% 66.5% 0.0% 100.0%
Water Use Summary
Total Annual Potable Water Use (gal / yr) Water Use Intensity (gal / sf / yr)
Total Annual Water Use per Occupant (gal / occupant / yr)
Benchmark Predicted Improvement Measured Improvement 3,085,065 45,410 99% 36,328 99% 30,851 454 363 98.6 1.5 1
Being on the coast storm water is a particular area of concern. The site leverages rainwater collection from roof runoff. In addition the incorporation of rain garden collection boxes will help mitigate the impact of storm runoff.
Type of Storm Event 2yr-24hr Storm Event 3.4 in Storm Event 0.28 ft Stormwater Storage 0 cf
Surface Runoff Co. Area (sf) Stormwater (cf) Total Runoff (cf) Roof 0.9 31,276 8,862 7,975 Impervious 0.9 3,284 930 837 Turf 0.2 0 -Native Plantings 0.05 2,854 809 40 Semi-Pervious 0.5 0 -Sub Total 37,414 10,601 8,853 After Storage 8,853 Percentage of Stormwater Managed On-site 16.5%
BEFORE
The initial calculated circulation on the first floor of the projection was 7,896 out of a gross square footage of 14,659 sqft. That equals a circulation ratio of 53% which is well above and industry standard of 25-40%. This is partially driven by the large amount of logistics required in the nature of intended use. The loading and unloading of seafood requires substantial space outside of processing and takes up 4,660 sqft of the space dubbed "circulation". Though this space is technically not assigned to production it is essential for the operations of seafood processing.
The initial calculated circulation on the first floor of the projection was 7,896 out of a gross square footage of 14,659 sqft. That equals a circulation ratio of 53% which is well above and industry standard of 25-40%. This is partially driven by the large amount of logistics required in the nature of intended use. The loading and unloading of seafood requires substantial space outside of processing and takes up 4,660 sqft of the space dubbed "circulation". Though this space is technically not assigned to production it is essential for the operations of seafood processing.
Upon revisiting the layout I noticed there there was substantial space in the center of the building that was not being fully utilized. I reduced the building's footprint by approximately 2,000 sqft contributing to a new circulation ratio of 40% , more in line with industry standard, especially when factoring the building's intended use. The additional space on the exterior wharf could be utilized by fisherman for unloading or temporary storage. The reduced footprint should have a positive impact on the plan's potential energy use.
Upon revisiting the layout I noticed there there was substantial space in the center of the building that was not being fully utilized. I reduced the building's footprint by approximately 2,000 sqft contributing to a new circulation ratio of 40% , more in line with industry standard, especially when factoring the building's intended use. The additional space on the exterior wharf could be utilized by fisherman for unloading or temporary storage. The reduced footprint should have a positive impact on the plan's potential energy use.
Mechnanical 11 Atrium12
Room4 Supervisor1 5 Supervisor2 6
Mens7 Womens 8
Hall9 Stair10 42' 1 3/8"
Production 1 Conference2 2 Conference1 3
FIRST FLOOR BEFORE FIRST FLOOR AFTER
Mechnanical 11
Mechnanical 11
UP UP DN
Room4 Supervisor1 5 Supervisor2 6
Mens7 Womens 8
Hall9 Stair10 42'2 3/8"
Production 1 Conference2 2 Conference1 3
The bulk of movement on the first floor of the structure involves the processing and production of sea food and administrative functions to support operations. Additionally circulation is increased in common space as FTE's utilize these spaces to reach the 2nd and 3rd floor lab space.
Focus of circulation is more on logistical movement, or loading and unloading product. There is still considerable anticipated movement around exits and entrances, with less focus on circulation up to the 2nd and 3rd floor containing lab space, most likely used in 9-5 business hours.
Room4 Supervisor1 5 Supervisor2 6
Mens7 Womens 8
Hall9 Stair10 42' 1 3/8"
Production 1 Conference2 2 Conference1 3
-
UP UP DN DN DN-
Mechnanical 11 Atrium12 UP UP DN
Mechnanical 11 Atrium12
Hall9 Stair10 42' 1 3/8"
Room4 Supervisor1 5 Supervisor2 6
Mens7 Womens 8
Production 1 Conference2 2 Conference1 3
DN
Cross laminated timber is beginning to make a presence in Maine, long known for it's role in America's lumber industry. The average cost for Cross Laminated Timber construction is $60 per square foot, or approximately 50% less then comparable traditional construction methods. Two mills for cross laminated timber are in Maine, with the first large scale commercial building completed in 2021. The proposed plan currently includes 3,040ft of required timber for supports and 30,675sqft of flooring material. The estimated cost of this material for the project is $1,840,500. (Image: Mayr-Melnhof Holz, 2022)
Maine has access to several steel suppliers including American Steel and Aluminum Company. Steel makes up the majority of the flooring support of 538 ft and 1,189ft of additional structural beams. The cost per 40ft beam is approximately $500. The estimated cost of steel required for this project would be approximately $21,588. (Image: American Steel & Aluminum., 2022)
New England Gypsum is a manufacturer and supplier of Gypsum wall board with a location in South Portland Maine. Gypsum is a large part of the interior finishes for the project. The price at New England Gypsum for a 4x12 sheet is $20. Based on the required volume for gypsum board the project would require 1,448 4x12 sheets. This means the total projected cost for this material is $28,977. (Image: NE Gypsum, 2022)
The proposal for the building and the proposed program was developed fully with the maritime economy of Portland in mind, tapping into sustainability with a focus on the local aquaculture market. Thie building falls in what is called the Waterfront Central Zone (WCZ), with the goal of keeping Portland's maritime industry alive. The building was very much so developed with this in mind with the intended use to provide supportive services for the fishing and aquaculture
industries. The plan includes a first floor processing and logistics space, as well as space for businesses to operate their businesses. The top two floors bolsters the economic activity in the building by offering lab space, with at least one floor supporting the operations of an aquaculture nursery.
Not only does the intended us look to bolster the industrial center of the city, the design of Cross Laminated Timber
will help support a burgeoning industry within Maine. Long a timber center, the state's mills have faced increasing hardship. The promise of mass timber offers hope of a resurgence in the industry with two CLT plants going into the greater Portland area in 2021. Not only does this reduce the buildings embodied carbon impact, and offer an attractive price point, the building is also helping to support another developing industry within the city's economy. CLT is favorable from a
maintenance stand point as well providing less operational costs throughout the buildings life cycle.
The use of efficient systems and the incorporation of a solar array on the south east facing side of the building generates operational savings through out the buildings life, increasing its economic potential.
In order to estimate the cost of a comparable building we leveraged the tool RS Means. This provided a realistic cost of construction for a building in Portland of the size and class. The assumptions generated by this analysis were applied to the Cote Super Spreadsheet and used in the design for the Economy sections. In addition these factors were included in the revised proforma of the structure, increasing the validity of assumptions used to model the project's potential return on investment
The building was designed with thought to it's energy usage. In comparing to similar energy benchmark the estimated performance of the building is relatively favorable. As this is a processing and lab space the lighting power density of the building is high to ensure a safe and efficient work environment. The design includes a great deal of windows to allow natural light helping the building to just out perform the benchmark. The intended lighting source will be LEDs throughout the
entirety of the building to their increased efficiency. The placement and scale of the windows allows sun to enter on the southern side of the building, maximizing solar heat gain. This side of the building has a 63% window to wall ratio to ensure that the maximum amount of heat is let in. Like wise, where appropriate windows are heavily included on the southwest facing facade with a WWR of 23%. In totality the building has a Window to Wall Ratio of 30.1%, falling within the optimal range.
Relative to other building classes the program of the design leads to relatively high energy consumption. Food service and lab space benchmarks highly at 527 kBTu/ sf and 312 kBtu/ sf. Additionally due to the size and climate of the building there are substantial anticipated Natural Gas costs. Savings are created by efficient passive design methods such as solar screening, utility systems as well as the
previously mentioned solar array, which is capable of generating energy on-site. The size of the roof and the location allows for an estimated 45,000kWh.
January 190,832.1 45,000.0 162,207.3 - 45,000.0 February 190,829.8 45,000.0 162,205.3 - 45,000.0 March 190,832.9 45,000.0 162,207.9 - 45,000.0 April 190,827.5 45,000.0 162,203.3 - 45,000.0 May 190,826.7 45,000.0 162,202.7 - 45,000.0 June 190,826.7 45,000.0 162,202.7 - 45,000.0 July 190,826.7 45,000.0 162,202.7 - 45,000.0 August 190,826.7 45,000.0 162,202.7 - 45,000.0 September 190,842.2 45,000.0 162,215.8 - 45,000.0 October 190,826.7 45,000.0 162,202.7 - 45,000.0 November 190,826.7 45,000.0 162,202.7 - 45,000.0 December 190,826.7 45,000.0 162,202.7 - 45,000.0
The building lends itself to a significant operational carbon impact as a result of energy consumption. The primary reason for this is the planned program, which historically is highly energy intensive to power the machinery required. The anticipated kg-C02e per year per is ~15M. This leads to a total annual cost of $468K, in operational energy costs.
Energy
Predicted Measured Operational Carbon
Gross Annual Consumption (kBtu / yr) 7,813,634 6,641,589
Gross Annual Generation (kBtu / yr) 1,842,556 1,842,556
Net Annual (kBtu / yr) 5,971,078 4,799,033
Percent of Total Energy from Renewable Energy 23.6% 27.7%
Gross Energy Use Intensity (kBtu / sf / yr) 254.7 216.5
Predicted Measured
Annual (kg-CO2e / yr) 705,841 1,002,911
Annual Intensity (kg-CO2e / sf / yr) 23 33
Percent Reduction from Benchmark 10% -29%
Percent Reduction (Inclusive of Renewables) 33.5% 46.6%
Cost
Net Annual Cost ($) $263,994 $222,775
Predicted Measured Net per Area (kBtu / sf / yr) 194.7 156.4
A program called Tally allows us to look at the embodied carbon impact of material choices in the design. Using two different flooring assemblies we can look at the direct impact of material choices all the way down to the granularity of suppliers with a determined radius of the a project.
As a base case a structure designed with traditional concrete construction is compared to Cross Laminated Heavy timber construction to demonstrate the
advantages of leveraging that technology. The global warming potential for concrete is significant with 1.3M kg of C02.
Product [A1-A3] 03 - Concrete 05 - Metals 06 - Wood/Plastics/Composites 09 - Finishes
Transportation [A4] 03 - Concrete 05 - Metals 06 - Wood/Plastics/Composites 09 - Finishes
Maintenance and Replacement [B2-B5] 03 - Concrete 05 - Metals 06 - Wood/Plastics/Composites 09 - Finishes
End of Life [C2-C4] 03 - Concrete 05 - Metals 06 - Wood/Plastics/Composites 09 - Finishes
Module D [D] 03 - Concrete 05 - Metals 06 - Wood/Plastics/Composites 09 - Finishes (TALLY, 2022)
Broken out by life cycle, the assembly's material impact it is clear. Concrete has the highest Global warming impact in the production of the product at 76% of the entire carbon impact. There is marginal credit for concrete in it's end of life, relative to wood due to the greater opportunity for the byproduct of concrete to be reused or recycled. Concrete composes 81% of the building's Global Warming potential embodied carbon impact.
When compared to the life cycle analysis of concrete, it becomes apparent that wood's production provides as significant advantage when analyzing the embodied carbon potential. As trees grow carbon is sequestrated. When used as a building material such as in Cross Laminated timber that carbon is trapped creating a net positive gain. When itemized by division wood's carbon impact can help offset the global warming potential of other materials such as finishes or metals.
A total carbon impact of 822kg of Co2 is a significant reduction from the base case concrete study.
545,562
4/26/2022
- Metals
- Metals
- Metals
- Metals
The primary carbon impact for wood comes at the End of the building life. If the material is dissembled, as an organic material is difficult to recycle. As it decays carbon will make its way back into the terrestrial carbon cycle and potentially the atmosphere. Wood's global warming impact, though still negative provides significant advantages when compared to the amount of carbon generated by concrete.
When looking more in depth at the suppliers of cross laminated timber a clearer picture of the carbon potential for each product emerges. There is significant variability in each manufacturer's measured carbon potential, likely due to the process or the associated credits with the material. As a product the kgCo2 per cubic yard ranges from an average of 53 Kg Co2e to -343 kg Co2e driven by the impact of tree sequestration.
The charts to the right compare the product by manufacturer and specific plant in which the material is fabricated. This allowed us to really hone in on specifics factoring the location of the products as well as a comparison of the different manufacturer's practices.
Coffeyville XLAM is showing only 1 EPD of -343 kg C02e per yd3. When compared to the mean of the other manufacturers
this product, could be an outlier. Red Stag Timber seems to contain the most EPDs all within a fairly contained range. A conservative estimation for Red Stag Timber's material's impact still remains well below the overall material's baseline of 153 Co2e per yd3.
(EC3, 2022)
The chart below demonstrates the importance of sourcing and the impact that can have on the total carbon impact of a project. In the baseline assembly of concrete the variability of the source can have a significant impact (29%) on the carbon impact of the project. This
diagram demonstrates how a granular look at the product composition can have a measurable impact relative to respective industry baselines. The choice of manufacturer and source for the cast in place concrete had a measurable impact. The graph also again demonstrates the
relative impact of materials relative to one another. Concrete clearly represents the bulk of the carbon impact on this project's floor assembly.
(EC3, 2022)
Similarly, the bar graph below can demonstrate the variability of material choices relative to a baseline project. Using the program EC3 projects can reduce their overall carbon impact by material. Though wood has a significantly less impact than concrete as a construction material, it's overall impact can be reduced even greater by the wood selected and the manufacturer's process. In this case relative to the
base line, the total realized kgCo2e per sqft is approximately 2.4 less then the benchmark. For concrete the selected product is 3.7 kg Co2e per sqft less than the benchmark.
This sankey diagram takes a more holistic look at the materials planned to be in the design, based upon the data available in EC3. The same principals used in the baseline comparison of Concrete versus CLT are applied and the amount of embodied carbon based upon specific
material selections has the potential to be reduced by 35% relative to material baselines.
In all with conducting a rough Tally and EC3 analysis I predict a total Embodied Carbon impact of 1.5M kg CO2e or ~50kg C02e per square foot. This is on the lower side of the range for industrial buildings driven predominantly by the incorporation of cross laminated timber into the building design. In all the analysis included several
Predicted Measured Annual (kg-CO2e / yr) 16,997,333.7 14,850,679.3
Annual Intensity (kg-CO2e / sf / yr) 554.1 484.1 Percent Reduction from Benchmark -2078% -1803% Was embodied carbon modeled? Yes Total Predicted Embodied Carbon
(B1-B5)
(A4-A5)
of Life (C1-C4)
Beyond (D)
When selecting materials the design put an emphasis on regional EPDs to not only reduce the overall carbon impact but also provide economic activity supporting the project's region. Cross laminated Timber can be sourced 400 miles away at a mill in Quebec, bordering Maine. Even closer are steel plants in Boston and Concrete sourced from within greater Portland. All and all we estimate that regional material make up over half of the cost of the project.
of
Due to the coastal nature of the project an emphasis was placed on resiliency in the planning process to minimize the impact of coastal flooding. This site is located in a V3 Flood zone and therefore we anticipate coastal flooding to impact the structures. In order to address these concerns we are looking to raise the slab foundation of industrial buildings to provide additional elevation in flooding, incorporate a structural support system in which flood walls can be easily installed in the event of a storm surge, providing additional elevation from water. The incorporation of solar panels provides a secondary energy source and due to the lab and industrial program generators will be required as further back up for essential systems.
The importance of transparency will be paramount when analyzing the measured performance of the building. Communicating with users, owners and designers is critical to ensure that the planned systems are working as intended. We intend to be transparent throughout the building life and continue to monitor building performance.
Measure 2: Design For Community
THE BIG IDEA: Walk Score
Transit Score
100% The project is the construction of industrial and labs space off of a large wharf in the working waterfront of Bike Score
Measure 3:
Percent of Site Vegetated - Post-Development
Percent of Site Vegetated - Pre-Development
Percent of Site with Native Plantings
Potable water reduction
Lifespan Commute/year Energy/year Building Materials Total 1 Year 80,304 1,002,911 1,525,197 2,608,412
Embodied carbon intensity (kg-C02e / sf) 20 Year 1,606,084 20,058,214 1,525,197 23,189,496 Total embodied carbon (kg-C02e) 100 Year 8,030,422 100,291,072 1,525,197 109,846,692
Net energy reduction from Benchmark
Embodied carbon modeled No (0) Yes (1) 200 Year 16,060,843 200,582,145 1,525,197 218,168,186 Biogenic carbon considered? No (0) Yes (1) Design 50 Year 4,015,211 50,145,536 1,525,197 55,685,945
Percent of reused floor area 0%
Percent of construction waste diverted 0%
Total Percentage of Carbon Dioxide Equivalents from: Percent of recycled content of building materials
Lifespan Commute/year Energy/year Building Materials Total Percent of regional materials
Percent of installed wood that is FSC Certified 0%
1 Year 3.1% 38.4% 58.5% 100.0%
20 Year 6.9% 86.5% 6.6% 100.0%
Measure 9: Design For Change 100 Year 7.3% 91.3% 1.4% 100.0% Local Hazard Research Score
Lifespan Commute/year Energy/year Building Materials Total 1 Year 80,304 1,002,911 1,525,197 2,608,412
1,606,084
Very High Performance
Overall the building is performing relatively well when compared to benchmarks. Going through the Cote Super Spread Sheet, increased the sustainability of the building.
The incorporation of a rain water collection system will reduce the building's overall reliance on external water. The embodied carbon of the building was also greatly reduced by leveraging technology tools such as Tally and EC3 and incorporating
sustainable materials such as cross laminated timber. The design improved expected performance by incorporating passive design strategies such as the placement of the windows on the based on environmental conditions. Additionally, greater care was put into the integration of the project within the ecology of Penobscott Bay. The steps taken to analyze the systems could make the building a true beacon of sustainability on Portland's working waterfront.
The energy per year is the greatest percentage of the building's energy use. Though a significant percentage this is driven by the savings from the buildings embodied carbon, as well as the energy intensive building use.
These factors stress the importance of the passive strategies we implemented for the building's design, as well as the incorporation of renewable energy sources such as the building's array.
THE BIG IDEA: 100% 100% The project is the construction of industrial and labs space off of a large wharf in the working waterfront of Portland Maine. Due to the zo 100% 100% 100% 100% 100% 100% 100% 100% 100% No (1) 100%
Overall this exercise made the building more efficient and will reduce the overall global warming impact of the project.
CARBON OVER TIME: 100% >50% >50% 105% 100% 100% 75% 100% 100% 100% 100% Yes (1) Yes (1) Carbon Calculations 10+ Total kg of Carbon Dioxide Equivalents from: 10+ Lifespan Commute/year Energy/year Building Materials Total 1 Year 80,304 1,002,911 1,525,197 2,608,412 20 Year 1,606,084 20,058,214 1,525,197 23,189,496 100 Year 8,030,422 100,291,072 1,525,197 109,846,692
Cumulative carbon over building life
Commute/year 3% Energy/year 38% Building Materials 59%
Building Materials 3%
Cumulative carbon after 1 year occupancy Commute/year 7% Energy/year 90%
Actual construction cost $192 Dollar (USD) / sf
Benchmark Construction cost $257 Dollar (USD) / sf
Construction cost Reduction from the Benchmark 25%
Efficiency Ratio Achieved 40% Net to Gross
Efficiency Ratio Percent Improvement -25%
Net site EUI 194.7 kBtu / sf / yr
Gross site EUI 254.7 kBtu / sf / yr
Predicted Measured
Net Energy Use Reduction from Benchmark 33%
Operational Carbon Emissions per Area 23 kg-CO2e / sf / yr
Percent from Renewable Energy 24%
Percent Operational Carbon Reduction from Benchmark 10%
Net site EUI 156.4 kBtu / sf / yr
Gross site EUI 216.5 kBtu / sf / yr
Net Energy Use Reduction from Benchmark 47%
Operational Carbon Emissions per Area 33 kg-CO2e / sf / yr
Percent from Renewable Energy 28%
Percent Operational Carbon Reduction from Benchmark -29%
Lighting Power Density 1.33 W/sf
Lighting Power Density % Reduction 2%
Window to Wall Ratio 3010%
American Steel & Aluminum. (2022). Beams. Retrieved from American Steel & Aluminum: https://americansteelandaluminum.com/product-line/#Beams%20&%20Channels
Architecture 2030. (2022). Direct Glazing. Retrieved from 2030 Palette: http://www.2030palette.org/direct-gain-glazing/
Babin, M. (2018, March 2). Best Places for Waterfront Dining. Retrieved from Old Port: https://www.oldport.com/best-of-portland/best-places-waterfront-dining/
Bonanza. (2021). Bonanza. Retrieved from Coastal Golden Rod: https://www.bonanza.com/listings/Organic-Native-Plant-Seaside-Goldenrod-MonarchButterfly-Fo/31309261
EC3. (2022). EC3. Retrieved from Building Transperency: https://buildingtransparency.org/ec3/buildings/own
Envornmental Protection Agency. (2022). Carbon Footprint Calculator. Retrieved from EPA: https://www3.epa.gov/carbon-footprint-calculator/
Global Footprint Network. (2022). Footprint Calculator. Retrieved from Global Footprint Network: https://www.footprintcalculator.org/home/en
Green Wave. (2021). Green Wave. Retrieved from Green Wave: https://www.greenwave.org/
Higgins, S. (2019). 40 Things To Do In Portland. Retrieved from Out of Office: https://outofoffice.blog/40-things-to-do-in-portland-maine/
Hooper Island Oyster Co. (2020, June 25). Nursery Tank Spat on Shell. Retrieved from Hooper Island Oyster Co.: https://hoopersisland.com/oyster-seed-production-2020/nursery-tankspat-on-shell/
Lawrence, M. (2020). NOAA. Retrieved from NOAA: https://www.pewtrusts.org/en/research-and-analysis/articles/2015/04/20/noaa-warns-new-england-fishery-council-not-to-weakenocean-habitat-protection
Mayr-Melnhof Holz . (2022). CROSS-LAMINATED TIMBER. Retrieved from Mayr-Melnhof Holz : https://www.mm-holz.com/en/products/clt-cross-laminated-timber
New England Gypsum. (2022). Drywall. Retrieved from New England Gypsum: https://negypsum.com/content/drywall-products
Pagniello, C. (2018, December 17). Could fish sounds help scientists monitor ocean health? Retrieved from California Sea Grant: https://caseagrant.ucsd.edu/news/could-fish-soundshelp-scientists-monitor-ocean-health
Piconi, P., Veidnheimer, R., & Chase, B. (2020). Edible Seaweed. Rockland, ME: Island Institute .
RS Means. (2022). Retrieved from RS Means: https://www.rsmeans.com/ Scape Studio. (2021, October 12). PARTICIPATORY HABITAT. Retrieved from Scape Studios: https://www.scapestudio.com/ideas/ Tally. (2022). Tally. Tally. Building Transparency, KT Innovations, thinkstep, and Autodesk.
Walk Score. (2022). Portland, Maine. Retrieved from Walk Score: https://www.walkscore.com/
Williamson, B. (2017). Welcome to Portland. Retrieved from Down East: https://downeast.com/issues-politics/welcome-to-portlyn/