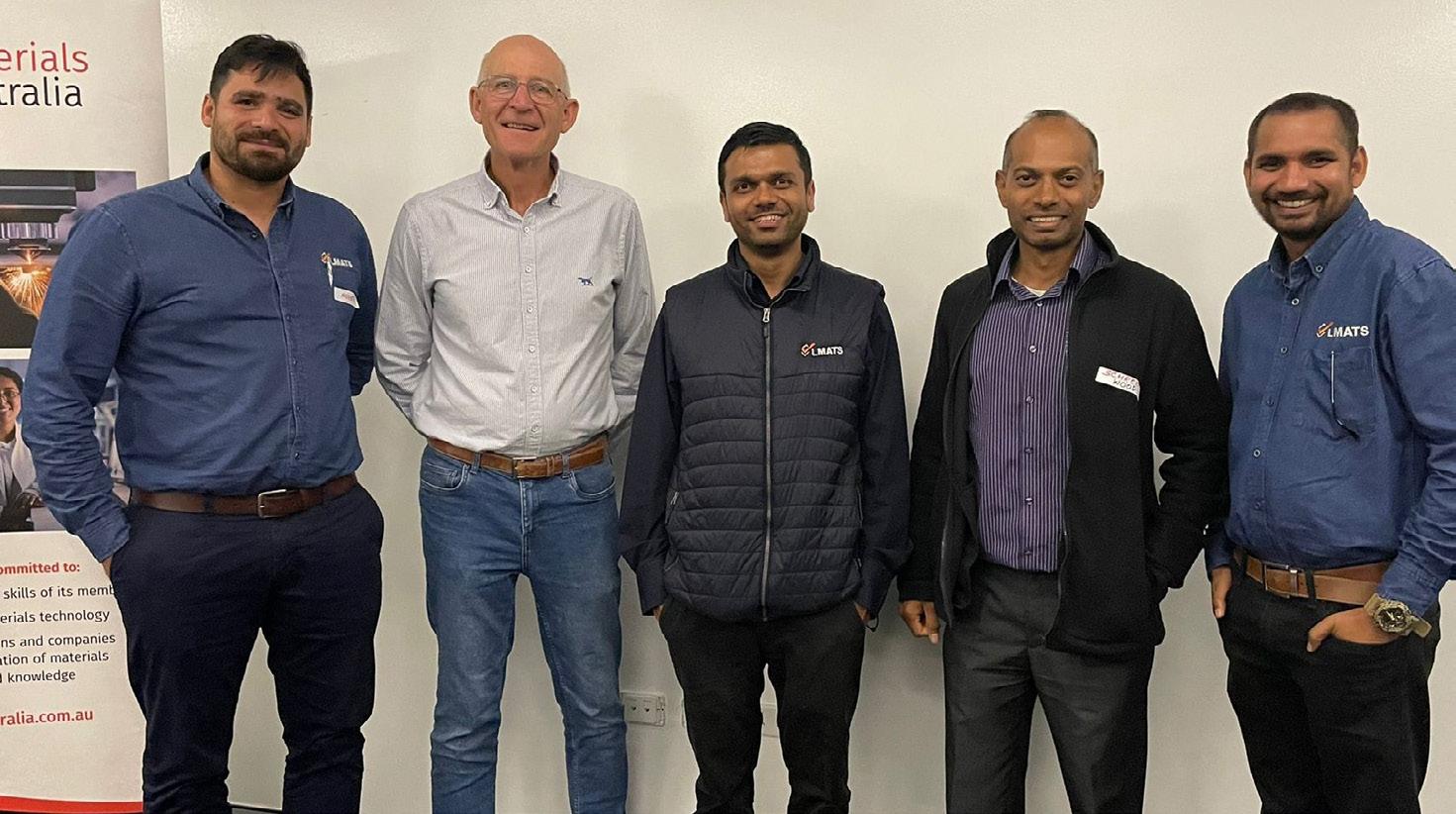
3 minute read
WA Branch Meeting Report - 14 November 2022 Update in Non-Destructive Testing (NDT) and Factors Affecting the Selection NDT Methods
Source: Jigneshkumar Dhimar, Branch Manager, LMATS Perth.
Jignesh Dhimar is a mechanical engineer with more than 15 years of experience working in NDT application industries. He has been actively involved in asset integrity inspection, refinery EPC projects, and pipeline corrosion mapping using conventional and advanced NDT techniques.
In NDT during manufacturing, requirements are often prescribed in specifications, codes and standards. With in-service NDT, the methods used depend on the component (e.g. structure, pipe, tube, pressure vessel, above ground storage tank), the material and the condition (e.g. surface condition, insulation, access, surface temperature). Jignesh emphasised the point that the choice of the right NDT method is crucial, and proceeded to outline recent advancements in NDT and to provide insights on their applicability in various industries.
He set the scene by reminding the audience of the main types of conventional NDT:
• Radiography – mainly internal discontinuities, sensitive to volumetric discontinuities
• Ultrasonic – mainly internal defect, sensitive to planar discontinuities
• Eddy Current – surface discontinuities, only conductive material
• Dye Penetrant – open-to-surface discontinuities
• Magnetic Particle – surface and subsurface discontinuities, only magnetic material
Advances in electronics, computing, and information and telecommunications (IT) have led to the development of advanced forms radiography, ultrasonic testing (UT) and eddy current (EC) testing techniques:
• CRT – Computed Radiographic Testing
• PAUT – Phased Array Ultrasonic Testing
• TOFD – Time Of Flight Diffraction Ultrasonic Testing
• GWT – Guided Wave Testing
• ECA – Eddy Current Array testing
• PECT – Pulsed Eddy Current Testing
• LFEC – Low frequency Eddy Current Testing
Improvements in electronics allow more sensitive data capture, for example, replacing single-use radiographic film with a reusable cassette containing a scanned phosphor plate. Greater computational power has been instrumental in allowing more complex signal processing and data analysis. Improvements in IT apply across all testing methods, notably enabling traceable, paperless results to viewed by clients anywhere in the world.
The application of these improvements to UT has greatly expanded the scope of the method. In its original form, detection is limited to planar discontinuities directly under the combined source and detector. PAUT creates a steerable UT beam using interference between the ultrasound waves produced by an array of piezoelectric transducers. Steering the beam at angles either side of the through-thickness axis allows detection of non-planar defects and visualisation of data on a volumetric basis. This method has a high detection rate and is well suited to weld inspections, corrosion mapping, and monitoring and sizing defects for baseline data. TOFD, which can be used in conjunction with PAUT, detects discontinuities regardless of their orientation and is regarded the best NDT method for through wall sizing of defects. The tips of a crack that lies between a transmitter and a separate receiver (on the same surface) diffract waves that arrive at the receiver at different times, allowing the defect to be located both laterally and on the through-thickness axis.
A further extension of UT from throughthickness to axial defect detection is achieved with guided wave long- range UT (GWUT). In this method, the ultrasonic wave travels axially, with defects located normal to the longitudinal axis being detected by the energy they reflect to the transmitter/ receiver. This allows their distance from the transmitter to be determined. This method is well suited to identifying relatively large defects, such as loss of wall thickness, in inaccessible locations, such as buried pipelines.
Eddy current testing has also advanced. Eddy Current Array (ECA) testing uses the same basic principles as simple eddy current testing. The difference is that electronics and signal processing area applied to allow a large number of exciting coils to be used simultaneously to cover a large area at once, and with greatly improved signal to noise ratio and reproducibility. This method can detect surface defects, far-surface corrosion and shallow subsurface defects. It can be implemented with flexible probes for complex shaped geometries.
Another of the improvements to eddy current testing made possible by improved signal processing is pulsed eddy current testing (PECT). In this method a step-function voltage is applied, producing a spread of frequencies. Because the different frequencies penetrate to different depths, this allows simultaneous collection of information from a range of depths. This makes the method particularly useful for thickness measurement without removal of insulation (e.g. for corrosion under insulation), for measuring thickness of steel embedded under concrete or asphalt, and for detection corrosion of steel submerged in water.
Low frequency eddy testing (LFET) is applied to gather information deeper below the surface, though with relatively low resolution. Jignesh explained how LMATS applies this method for scanning for defects in boiler wall tubes.
Jignesh proceeded to describe factors affecting the selection of NDT methods, taking as an example inspection of heat exchanger tubes. He summarised the applicability of various methods in relation to tube material and tube form (e.g. with or without fins), and explained how the choice is further governed by the type of defect to be detected and the required sensitivity of detection. This was a comprehensive update, highlighting the range of techniques that are available locally.