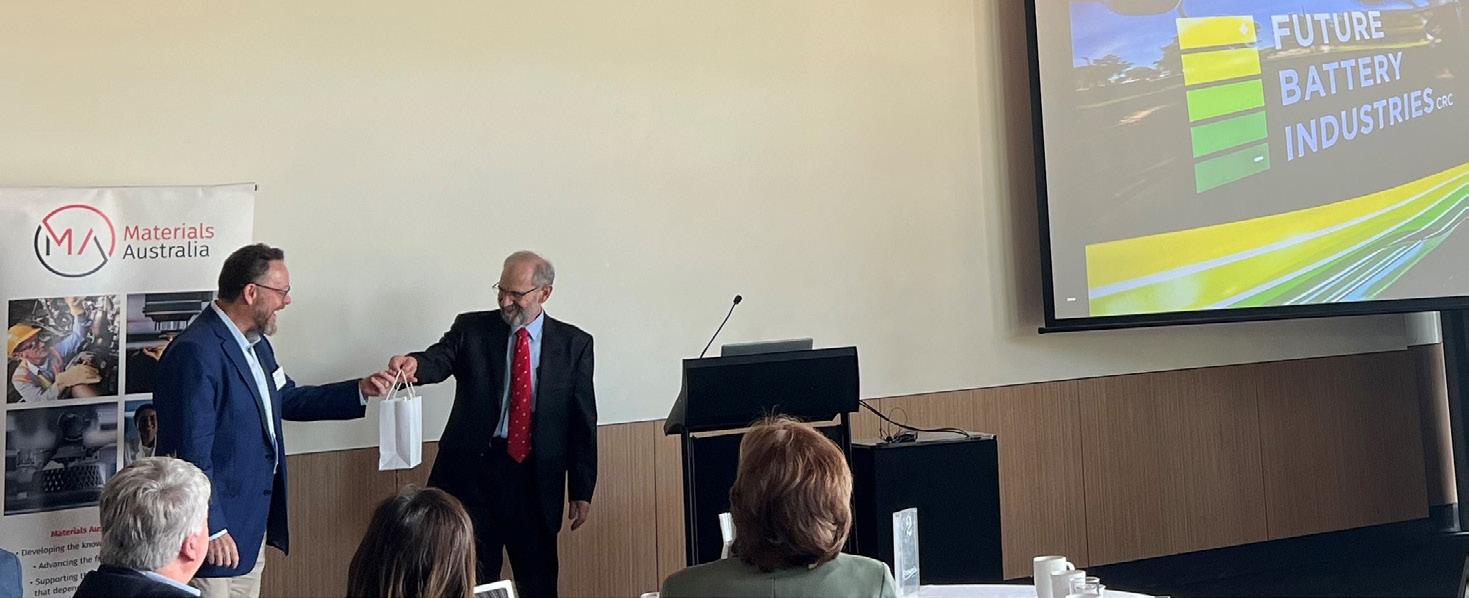
4 minute read
Perth Branch Annual Sir Frank Ledger Breakfast Challenges with materials selection for lithium-ion battery cathodes
Source: Dr Richard Macoun, Research Manager, Future Battery Industries CRC
Dr Richard Macoun studied physical and polymer chemistry (University of Sydney) before completing his PhD in nanotechnology and chemical engineering (UNSW). Richard also holds an MBA (UWA) and has worked in product and process innovation for over twenty years at CSIRO, BHP and BASF (Mining Solutions). He has had a long involvement in collaborative innovation efforts as Program Manager at AMIRA, and as Research Director at the Future Battery Industries CRC (FBICRC).
The FBICRC has been planned to have six-year life, “to live fast and die young” with a mission to help develop a vibrant battery industry for Australia before the window of opportunity closes. Richard reminded the audience that while Australia possesses around half the world’s known reserves of battery materials, mining and chemical processing makes up only around 3 percent of the battery value chain.
While the centre is undertaking 15 projects across the value chain, Richard singled out one, the National Battery Testing Facility, for special mention. It is vital for providing certification for shipping lithium-ion batteries (LIBs) batteries. The point is that, unlike lead- acid batteries, end-of-life LIBs present a significant hazard, which will soon be encountered in increasing volumes as electric vehicles (EVs) become eight to ten years old. The LIBs they contain will have to be processed somewhere, which will involve collection, storage, and transport, in addition to the processing.
The fundamental reason why LIBs are different is that they operate on flow of lithium ions between two electrodes (anode and cathode) neither of which is consumed in a chemical reaction (the way lead is consumed in a Pb-acid battery). Rather, the two electrodes act as ‘sponges’ which can contain mobile lithium ions at differing energy states. Richard likened charging and discharging LIBs to ‘sopping up’ ions with the virtual sponge, and then ‘squeezing and wringing them out’. Extending the analogy, the basic problem is that the harder the sponges are squeezed and wrung out the greater the damage accumulated in each cycle. Unfortunately, internal failure of LBIs, particularly when being charged, can lead to runaway discharge with the potential for practically inextinguishable fires, which are now all too common.
The way LIBs work is not intuitively obvious. Indeed, the award of the 2019 Nobel chemistry Prize is an acknowledgment of their development as a triumph of materials science. The initial scientific breakthroughs, starting in the 1970s, were the discovery of materials that could accommodate lithium ions intercalated within layered crystal structures. Subsequently, the key to the development of LIBs into practical and widely used portable energy sources has been in finding electrode materials that allow higher capacity (for a given size and weight) and faster charging and discharging rates (power output), combined with adequately long life and affordable cost. The first LIBs had lives measures in hundreds of charge-discharge cycles, now they can withstand thousands, but the goal is for them to be able to withstands tens of thousands.
Currently, the most common anode material is graphite, typically ‘five nines’ purity, though graphene (single-layer graphite), lithium titanate and silicon are also options. Cathodes are mostly based on metal oxides, with several competing technologies in common use. Three of these five formulations contain cobalt, and the high cost of this element is driving the development of alternatives. alternative energy palladium catalysts glassy carbon thin lm screening chemicals surface functionalized nanoparticles zeolites
Richard outlined the production process for cathodes starting with manufacture of the cathode precursor material, which is the oxide structure that can hold the lithium ions. Lithium ions are subsequently introduced through combining the oxide with lithium carbonate and calcium, in powdered form. Details of the manufacturing processes are closely held trade secrets.
The third component of the cell is the separator and the fourth is the electrolyte, commonly lithium hexafluorophosphate. The flammability of electrolytes is a significant factor in LIB fires, which are made worse by the propensity of cells to explode and spread burning material for up to several metres, in all directions.
Richard briefly touched on manufacture of batteries, with a focus on the common small cylindrical-form cells that are the active components of most LIB packs. A rechargeable LED torch might typically have three such cells, while 18V power tool battery packs typically have five. However, battery packs for EVs contain 5000 or more of these small cells, connected electrically and structurally, together with cooling and power management modules.
The manufacture of the individual cells starts with preparing slurries of anode and cathode materials. These are used to form a three-layer sheet with a separator between the electrode layers, using processes like those in paper and film production. The spooled sheet is then rolled to form the cylindrical cells, a bit like forming a like a Swiss roll cake. The next step is to fill the cells with electrolyte and then apply a series of charge and discharge cycles to transport the lithium ions into the electrodes. Currently this final ‘formation’ process can take up to three weeks, resulting a considerable inventory of cells in production. The results of formation are not guaranteed, so cells are individually tested and graded before sale and subsequent assembly into battery packs.
Richard remarked that while EVs received the top-grade cells, the lower graded cells often end up in consumer products such as cheap scooters and power tools. It would appear no coincidence that such devices have been the cause of many house fires. Returning to his analogy, Richard’s advice was to treat an LIB like a sponge and not to wring it out too hard! He recommended keeping LIBs between 60 and 80 percent capacity, and not to leave them on-charge out of sight and out of mind.
The audience reception showed that Richard’s presentation maintained the established reputation of the Sir Frank Ledger Breakfast as a highlight of the WA Branch year.
99.999% ruthenium spheres diamond micropowder janus particles nickel foam buckyballs gold nanoparticles
III-IV semiconductors organometallics nanogels metal carbenes ITO bioactive compounds nano ribbons nanodispersions
3D graphene foam osmium
MOFs isotopes ultralight aerospace alloys
Nd:YAG cermet epitaxial crystal growth drug discovery quantum dots transparent ceramics spintronics mesoporous silica sputtering targets
MBE indicator dyes macromolecules silver nanoparticles enantioselective catalysts rhodium sponge pharmacoanalysis spectroscopy anode excipients superconductors chalcogenides rare earth metals cryo-electron microscopy
CVD precursors deposition slugs laser crystals calcium wires platinum ink tungsten carbide refractory metals optical glass graphene oxide
The Next Generation of Material Science Catalogs
h-BN MOCVD metamaterials
Fe3O4 uorescent microparticles cisplatin shift reagents ferro uid dielectrics
American Elements opens a world of possibilities so you can Now Invent!
Over 30,000 certi ed high purity laboratory chemicals, metals, & advanced materials and a state-of-the-art Research Center. Printable GHS-compliant Safety Data Sheets. Thousands of new products. And much more. All on a secure multi-language "Mobile Responsive” platform. www.americanelements.com biosynthetics dysprosium pellets process synthesis metallocenes conjugated nanostructures