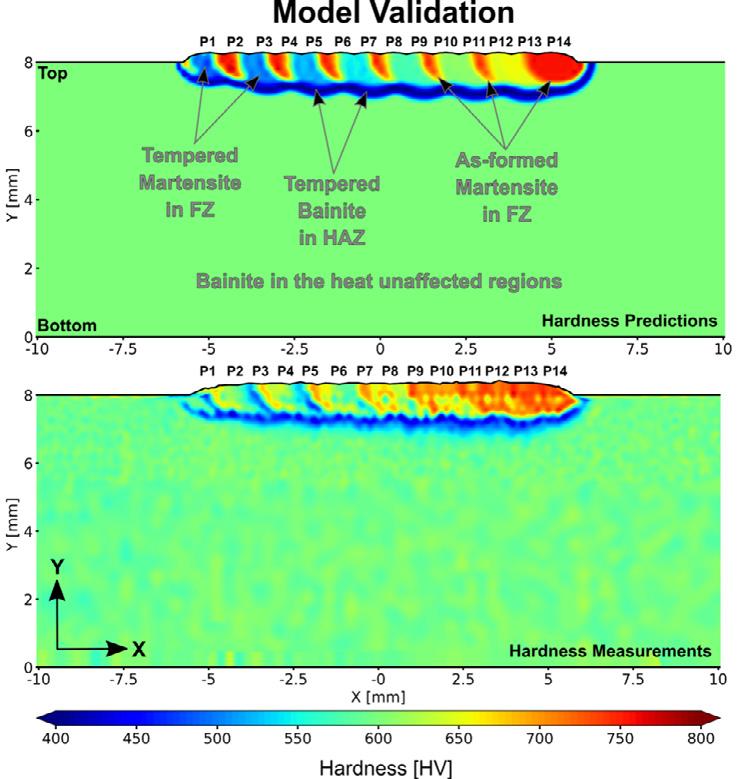
4 minute read
Revolutionising Repairs: Optimising Laser Metal Deposition (LMD) with High-Fidelity Multi-Physics Numerical Simulations
Laser Metal Deposition (LMD), also known as laser cladding, is an innovative additive manufacturing (AM) technique that injects metal powder into a laser beam to create a new, strongly-bonded layer on top of a substrate. This technology has gained significant attention recently as a cost-effective and time-efficient repair method that can sometimes enhance material properties in the repaired area.
However, LMD can result in residual stresses and intricate microstructures that may negatively affect the performance of repairs. To tackle these challenges, the Australian Nuclear Science and Technology Organisation (ANSTO) has partnered with leading institutions, including the Royal Melbourne Institute of Technology (RMIT), Swinburne University of Technology (Swinburne), Defence Science and Technology Group (DSTG), and Rosebank Engineering, under the auspices of the Defence Materials Technology Centre (DMTC), to develop advanced numerical models that capture the development of residual stresses and microstructure during the LMD process. These high-fidelity multi-physics numerical models can significantly enhance the optimisation of the LMD process and thus ensure the fatigue life of repaired components.
ANSTO's previous research on stainless steel and nickel alloys showed that thermo-mechanical models could predict welding-induced residual stresses accurately. However, modelling residual stress development in lowalloyed steels requires accounting for metallurgical and transformationinduced plasticity strains and heat treatment (tempering) of the material during the deposition process. To address these challenges, ANSTO has developed a high-fidelity thermometallurgical-mechanical numerical model for predicting the microstructure and residual stresses associated with a multi-pass (14-pass), single-layer LMD repair.
ANSTO’s numerical model, developed using the SYSWELD finite element package, takes into account the kinetics of solidstate phase transformations (SSPTs) and tempering (heat treatment) that occur during the low-alloyed steel powder deposition on a matching low-alloyed steel substrate. The validity of the developed numerical methodology was assessed by comparing numerical predictions with experimental measurements. Microstructure predictions were indirectly validated through hardness measurements (Figure 1), while residual stress predictions were directly validated using X-ray measurements (Figure 2).
The comparison between hardness predictions and experimental measurements depicted in Figure 1 shows a good agreement, confirming the numerical model's accuracy in capturing the resulting microstructure consisting of bainite, martensite, and their tempered equivalents. The model correctly predicts the initial formation of martensite in the fusion zone (FZ) and its softening in the earlier LMD passes (P1 – P4) due to tempering from heating during subsequent material deposition. Later passes (P5 – P12) show higher hardness, suggesting a limited amount of tempered martensite, while in the absence of further deposition, the final two passes (P13, P14) remain in the as-formed (untempered) martensite condition.
When it comes to the prediction of residual stresses, the numerical model reveals a relationship between residual stresses and the formed microstructure. Regions with higher hardness containing more significant amounts of untempered martensite experience compressive residual stresses (P5 – P14), while softer regions with higher amounts of tempered martensite are under tensile residual stresses (P1 – P4). Similarly, the heataffected zone (HAZ) containing large amounts of soft tempered bainite is under tensile residual stresses. The modelling results demonstrate that martensite formation is associated with the development of compressive residual stresses, which is a result of the volumetric expansion of the crystal lattice upon cooling during the austenite-to-martensite (AtM) SSPT. The AtM SSPT counteracts the formation of tensile stresses, which is a common residual stress inducing mechanism in materials without AtM SSPTs. The model also shows that subsequent tempering of the formed martensite leads to the relief of compressive residual stresses, leaving tempered martensite regions under tensile residual stresses. The presence of residual stresses in components can significantly impact their life under operating conditions, as these stresses may either enhance or diminish the component's overall resistance to crack nucleation and propagation. Tensile residual stresses at the surface of the deposited layer can initiate crack nucleation and accelerate its propagation, potentially undermining the performance of LMD repair in realworld operating conditions. The current fatigue crack growth analysis indicates that cracks originating in regions of high tensile stresses of earlier passes (P1 – P4) grow considerably faster and deeper than those that form in regions of compressive stresses (P12 – P14). However, it is important to note that although the compressive residual stresses are often preferred, the presence of untempered martensite in the material can result in brittle characteristics that may not be desirable for all applications. It is, therefore, crucial to consider the benefits and drawbacks when optimising the LMD process for specific repair applications.
Figure 1: The developed model predicts the formation of complex microstructure containing martensite, bainite, and their tempered equivalents. The accuracy of the microstructure predictions is performed indirectly through hardness measurements. The excellent agreement between the predicted and measured hardness values validates the applied methodology, confirming the model's accuracy in predicting the resulting microstructure in an LMD repair.
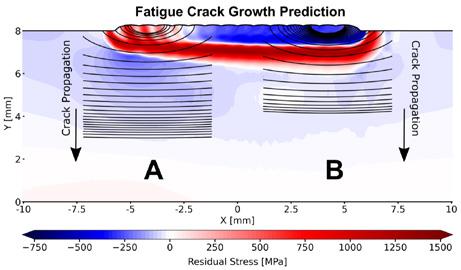
The high-fidelity, multi-physics numerical model of the LMD process developed by ANSTO can effectively capture the evolution of microstructure and residual stresses during the material deposition process. Hence, validated numerical simulations have the potential to revolutionise the LMD process by providing a faster method of testing a wide range of processing parameters with the aim of obtaining an optimal microstructure and residual stress distribution within a repaired component. As a result, the numerical simulations can reduce costs, shorten turnaround times, and improve material properties in repaired regions, making LMD repairs an increasingly attractive option for industries seeking cost-effective and reliable repair technologies.
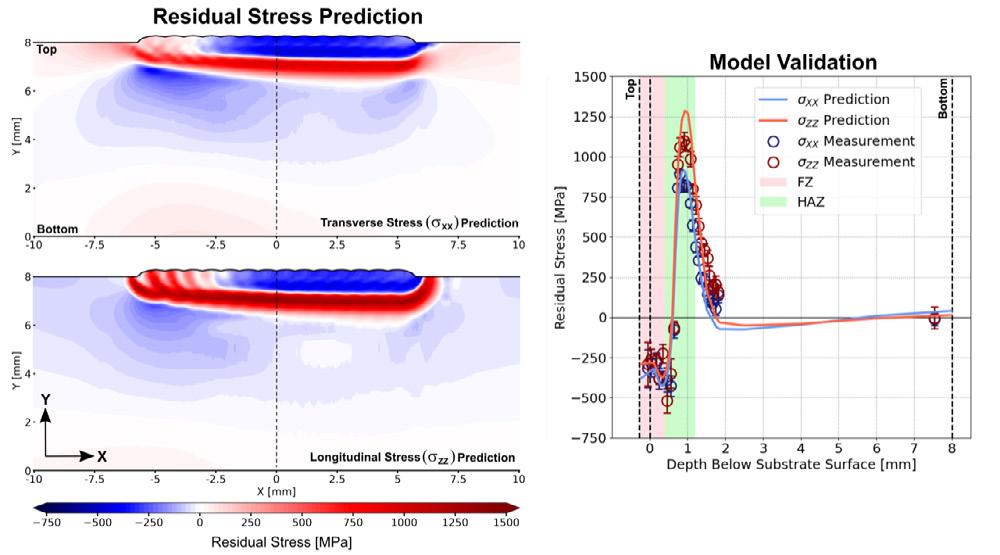
With the ongoing advancements in numerical modelling and additive manufacturing technologies, the future of LMD repairs is poised to become even more promising and transformative for the manufacturing and repair sectors. As research and development efforts continue to push the boundaries of LMD technology, industry stakeholders can expect further improvements in the efficiency, reliability, and performance of LMD repairs. By harnessing the power of high-fidelity numerical simulations, the collaborative efforts of ANSTO and its partners are paving the way for a new era of advanced repair solutions that cater to the diverse needs of various industries.
As LMD technology becomes more prevalent, industries worldwide will continue to benefit from the advancements driven by ANSTO and its collaborating partners. The high-fidelity numerical simulations developed through this collaboration have the potential to leave a lasting impact on the way repairs are conducted, leading to more efficient and reliable solutions for a broad array of applications. By continuing to refine and enhance the high-fidelity, multiphysics simulations, researchers and engineers will unlock new possibilities for the LMD process, ultimately resulting in a more sustainable and innovative manufacturing landscape for years to come.
In summary, the collaborative research undertaken by ANSTO, RMIT, Swinburne, DSTG, and Rosebank Engineering has yielded valuable insights into the complex interplay of factors that influence LMD repair performance. This work has shown that by leveraging high-fidelity multi-physics numerical simulations, researchers and engineers can better understand these factors and develop more efficient and reliable repair techniques tailored to specific applications, ultimately benefiting a wide range of industries, from aerospace and automotive to energy and infrastructure.