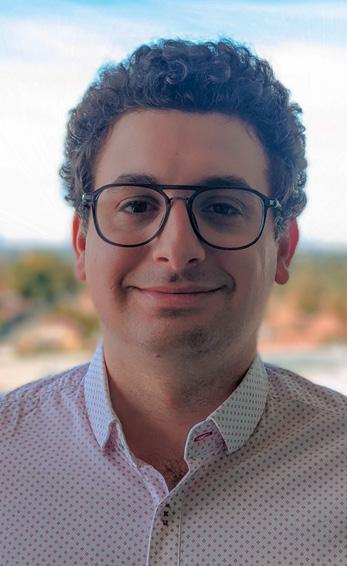
5 minute read
CMatP Profile: Deniz Yalniz
Deniz Yalniz is a Quality Engineer at Weld Australia—the peak body representing the welding industry in Australia. Deniz commenced his career at Jacon Technologies, first as a Design Draftsman, before progressing into various positions, including Technical Sales Engineer, Design Engineer and Quality Control Engineer. Prior to joining Weld Australia, Deniz was a Service Support Coordinator at Jacon Equipment. With an adaptable nature and in-depth understanding of quality assurance and Australian Standards, Deniz holds a Bachelor in Metallurgical and Materials Engineering, as well as a Graduate Diploma in Master of Engineering.
Where do you work? Describe your job.
I work at Weld Australia as a Quality Engineer. Weld Australia offers a broad range of services including, company certification according to a range of Australian and International Standards. These certification processes enable fabrication businesses to improve their technical knowledge, bolster productivity and profitability, and reduce the risk of failure and rework. services that provide professional development and career advancement opportunities for welders, as well as greater quality assurance throughout the welding industry. Weld Australia offers a broad range of engineering services that help substantially increase the operational life of plants and equipment and reduce the maintenance and repair overheads. We are the Responsible Member Society of the International Institute of Welding in Australia.
My role is to make sure that our entire system complies with Australian and International Standards, and IIW technical guidelines. I also advise Weld Australia team members and engineers regarding procedures and processes. Materials engineering is an integral part of my role as welding is closely related to materials science. It is a dynamic, exciting and a challenging role.
What inspired you to choose a career in materials science and engineering?
I was very familiar with materials engineering from an early age. That’s why I pursued it as a profession. My first job was as a Design Engineer at a materials engineering company, so I decided to switch my focus more to quality as I found this area fascinating.
Who or what has influenced you most professionally?
My professors when I was studying my bachelor’s degree. They showed what a great area the materials engineering field is. Their technical expertise provided me great knowledge to become a materials engineer.
Which has been the most challenging job/ project you’ve worked on to date and why?
To be honest, when I was working as a design engineer, every project I worked on was a challenge—each project had its own unique requirements and material needs. One particular project was more challenging than the others. As a design team, we were working on new machinery for coal mines. After the brainstorming stage, the critical components of design and material selection for the structural elements were vital to ensure the mechanical integrity of the product. Selecting the correct material with the right mechanical properties and behaviour under statics, dynamics, vibrations, wear resistance and fatigue was a challenge—we always have to consider the environment in which our design will operate. However, the mine regulations and Australian Standards were limiting us to design freely. After we started to design our machinery in computer aided design software, our stress analysis calculations and FEA results were showing structure failure. Therefore, we had to approach our design from a new perspective completely. After the new design and few steps of design optimisation, our new machine design had no problems. As a result, our customer was more than happy.
What does being a CMatP mean to you?
Being a CMatP means recognition that I have achieved a high professional standard as a materials engineer in Australia. It is the only professional qualification in the world, of which I am aware, that is specifically for materials people.
What gives you the most satisfaction at work?
As a quality engineer in the materials field, I get a great deal of satisfaction by navigating the systems and processes to achieve the correct outcomes, thus providing others with the tools and knowledge to become more independent throughout the quality journey.
What is the best piece of advice you have ever received?
For me, the best advice comes in the form of encouragement and acknowledgement—where someone has recognised your contribution in making a pattern of work better, or improving something for others. However, everyone makes mistakes. You learn more from your mistakes than from your successes. The important thing is, never make the same mistake twice.
What are you optimistic about?
I have a great interest in metal additive manufacturing. It is a growing scientific area in industry. It has greater benefits than the conventional traditional manufacturing methods. Hopefully, in the future, we will see more about metal additive manufacturing in every industry.
What have been your greatest professional and personal achievements?
My greatest professional achievement was my bachelor thesis: Sub-zero treatment on Tool Steels and its effects on microstructure and mechanical properties. I had the chance to work with scanning and transmission electron microscopes. Also finishing my master’s degree at UTS was a challenge. I also studied at Istanbul University’s Conservatorium of Music for seven years and can play three musical instruments. I believe improving yourself in other areas is as important as improving yourself in the professional arena. I have always had an interest in languages. Therefore, in 2012, I moved to Munich for a year to learn German. I had great experiences there, while becoming fluent in German.

What are the top three things on your “bucket list”?
> To become more fluent in other languages than I currently speak, which are Italian, German and Russian.
> To travel the world, once these dire times end.
> To improve myself in my professional area even more. Currently, I am undertaking the International
Welding Engineer course, which is the highest qualification engineers can obtain in the welding area.
Tritex Multigauge 6000
A Drone Ultrasonic Thickness Gauge
Specifically designed to mount onto drones and transmits live measurements up to 500 meters. Features include:
• Measures through coatings up to 6 mm thick using Multiple Echo. • Remote-controlled gel dispenser. • Lightweight. • No zeroing required. • Single crystal soft-faced probe for curved surfaces. • Intelligent Probe Recognition (IPR). Available with or without a drone.
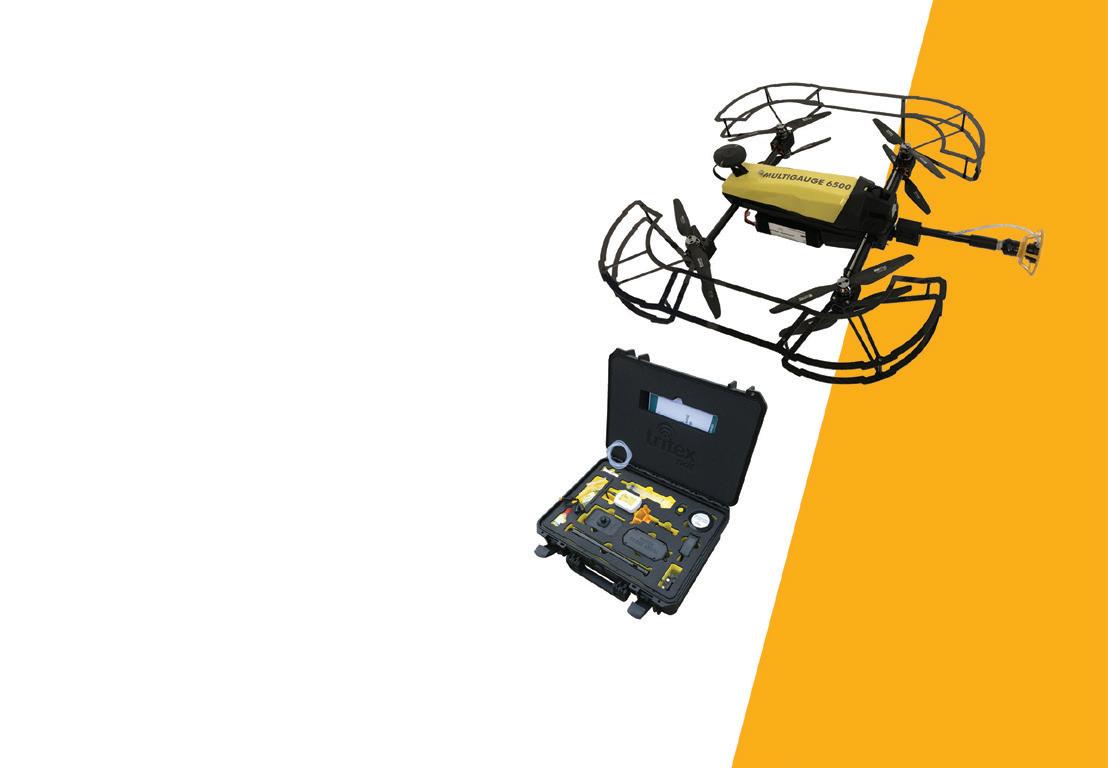
For further information please contact: NDT EQUIPMENT SALES: UNIT 21, 3 BOX ROAD TAREN POINT NSW 2229 TEL: (61-2) 9524-0558 • FAX: (61-2) 9524-0560 • Email: ndt@ndt.com.au • Web: www.ndt.com.au
www.streamlinecreative.com.au