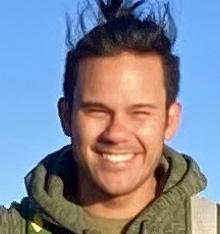
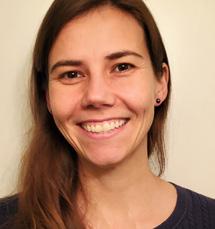
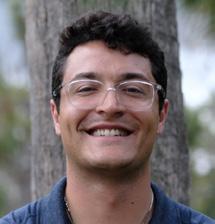
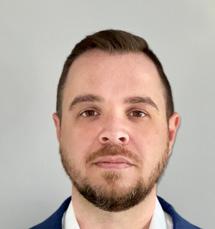

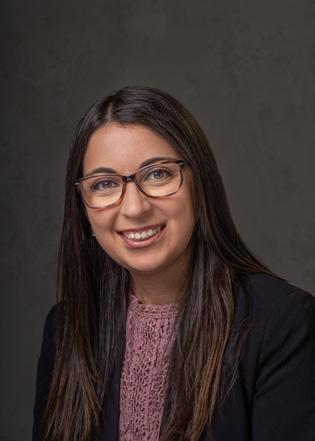
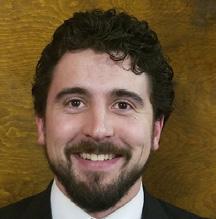
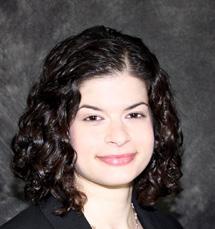
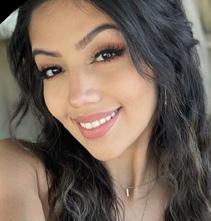
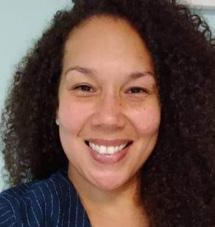



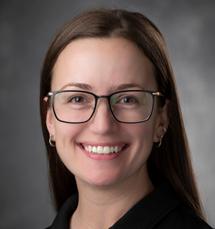
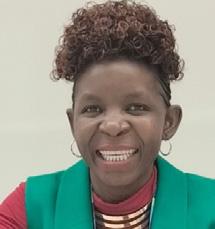
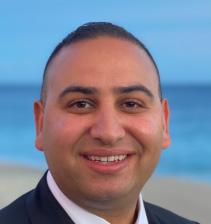
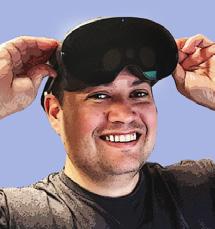
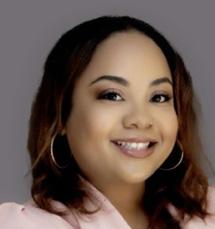
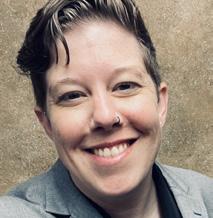


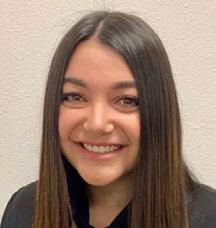
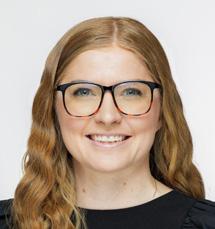
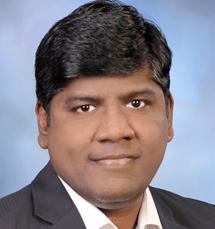
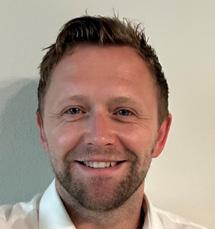
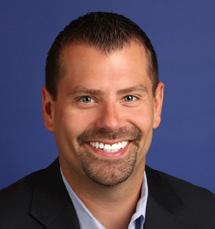
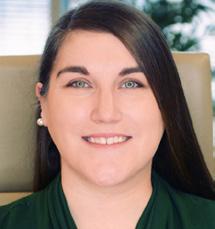
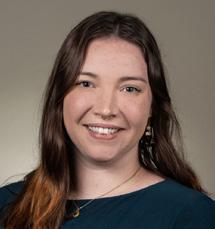
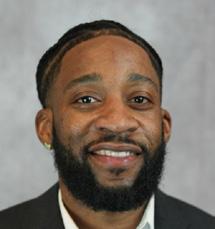

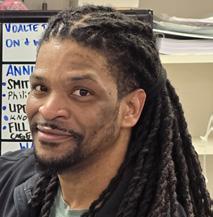
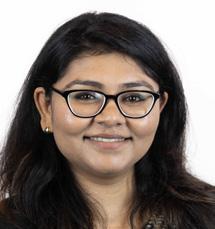
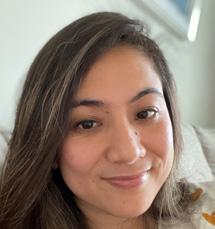

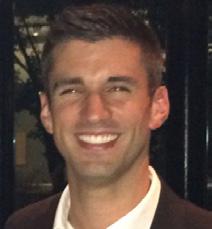


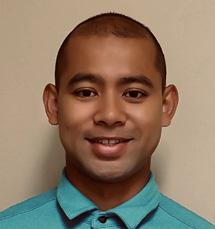
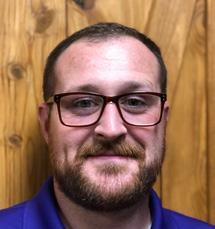
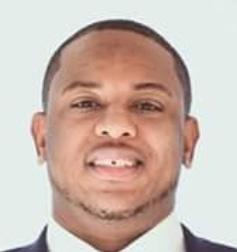

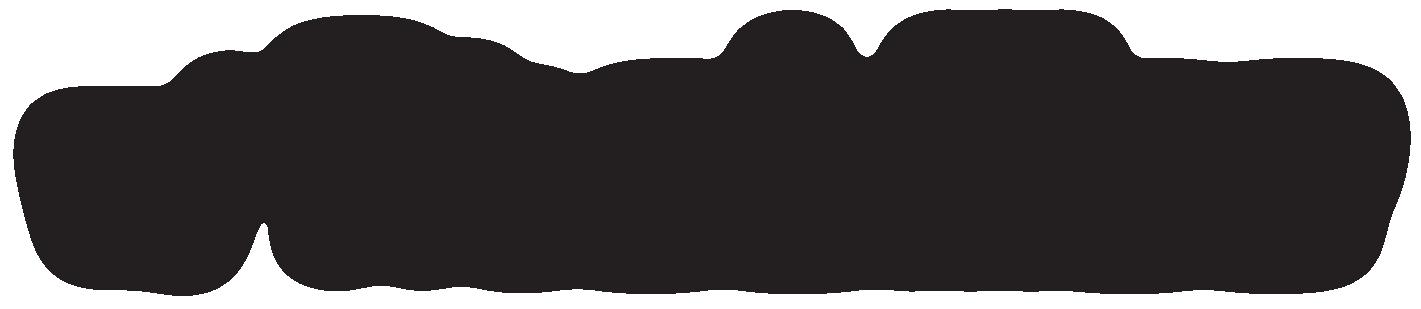
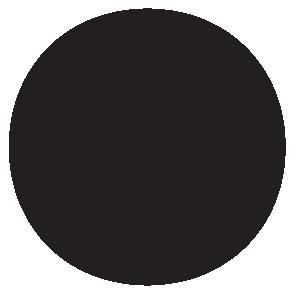
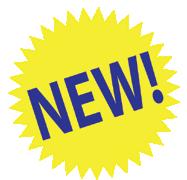
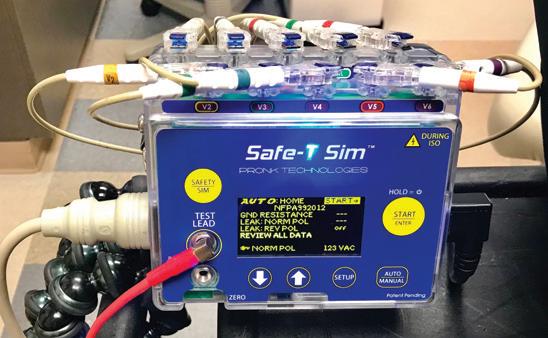
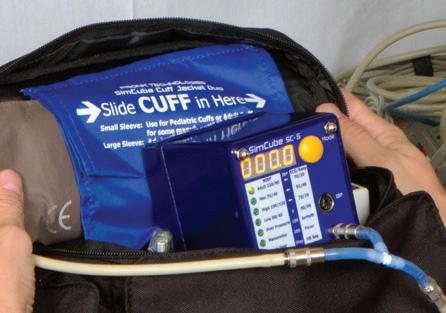
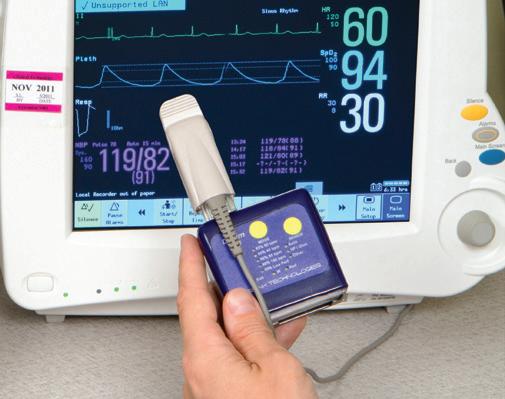
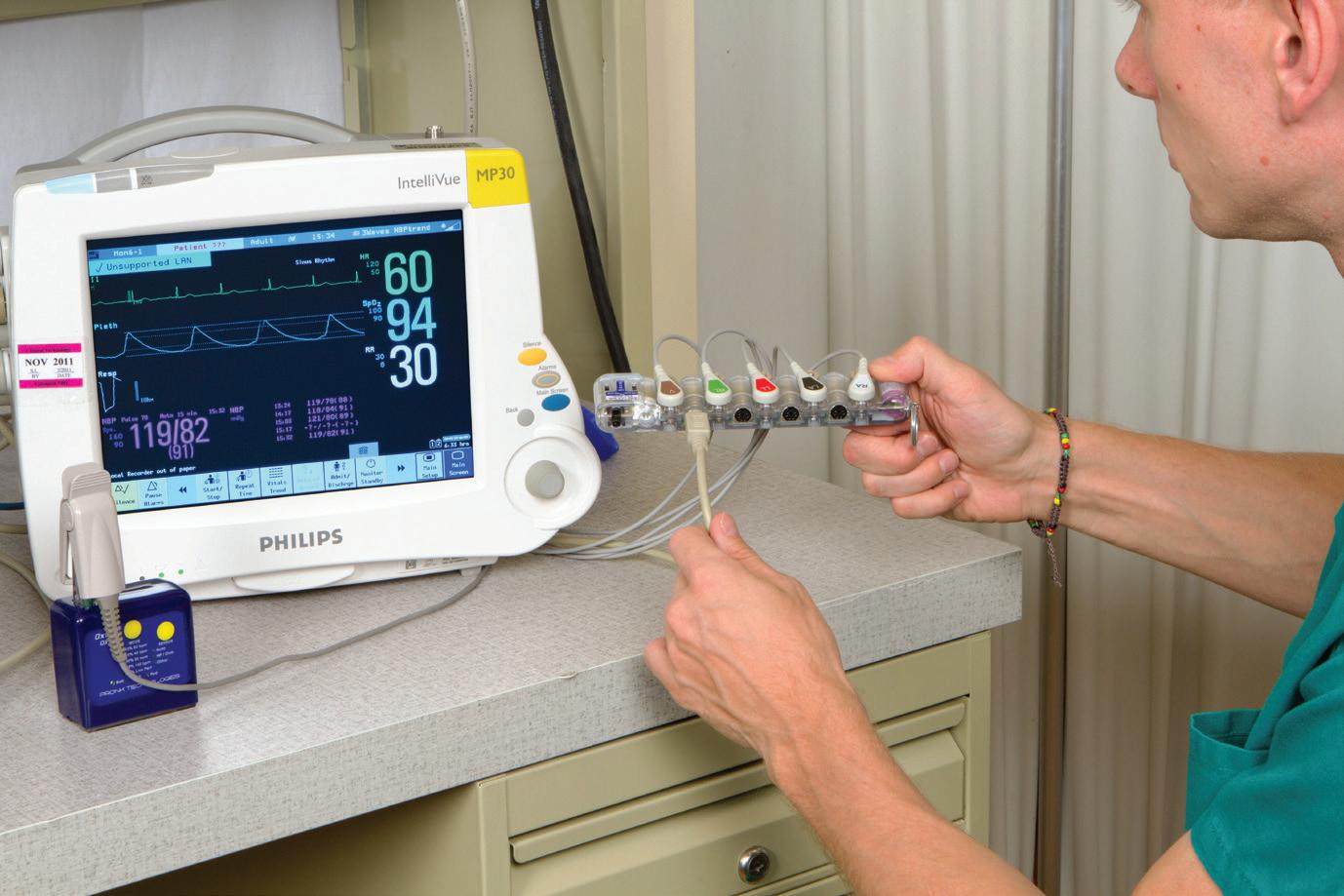
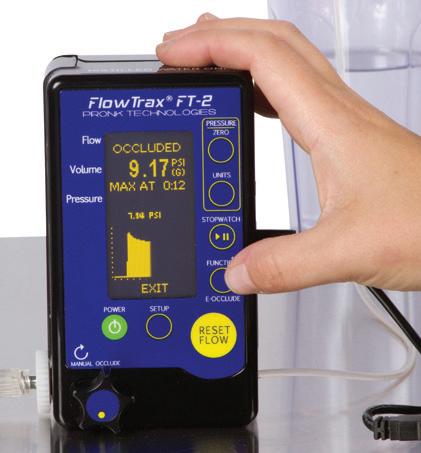
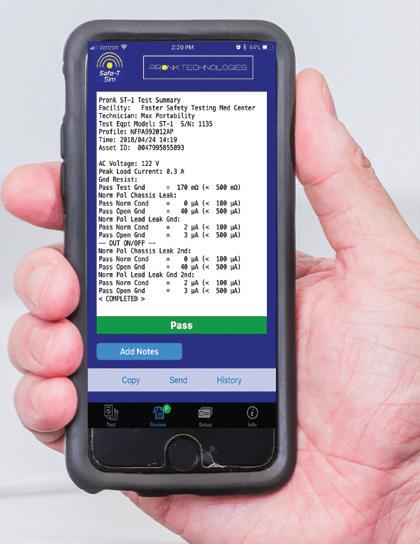
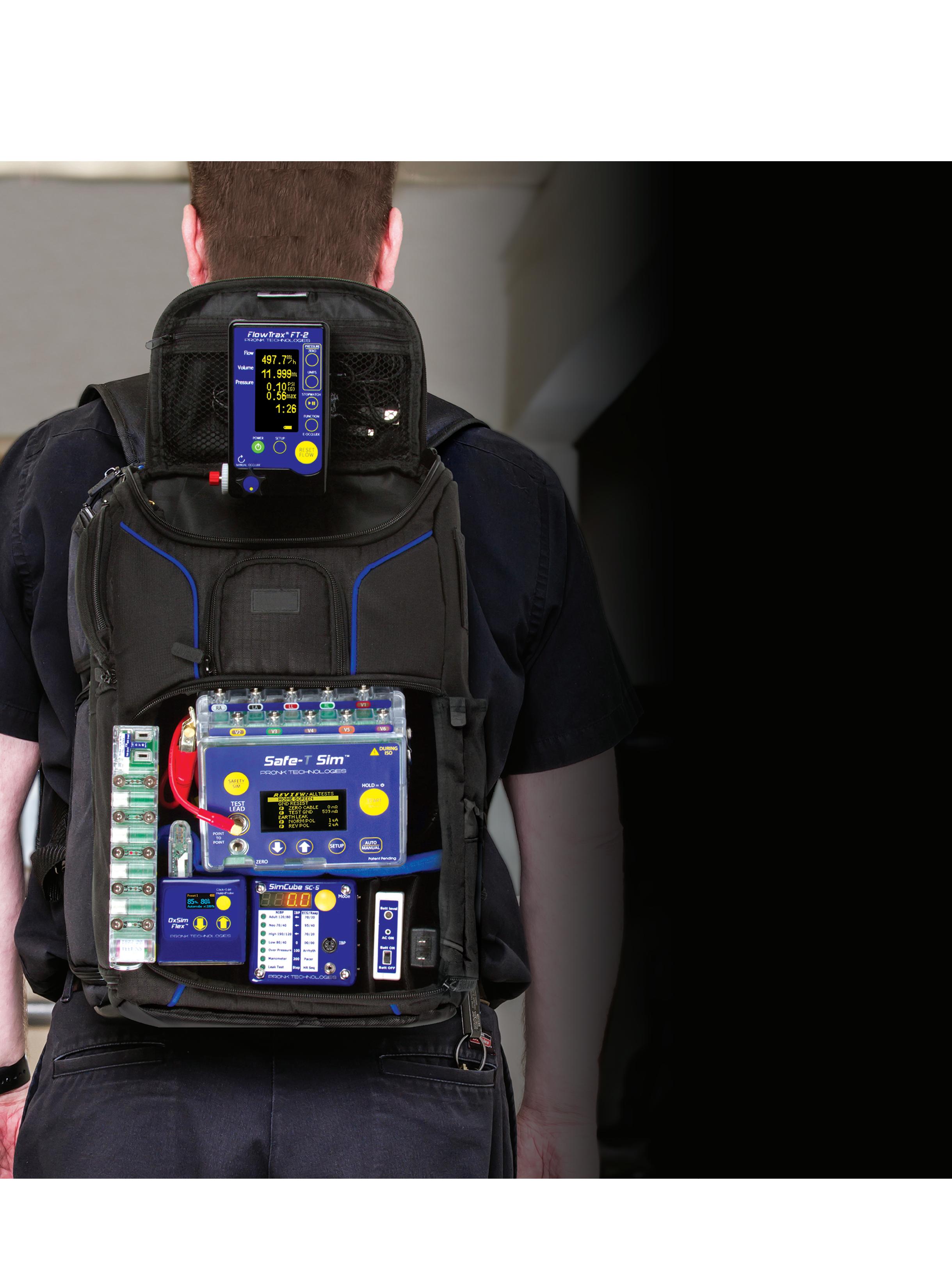
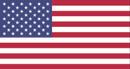

Your Ultrasound Partner
Your Ultrasound Partner
FREE TECH SUPPORT
FREE TECH SUPPORT
QUALITY, TESTED PARTS
QUALITY, TESTED PARTS
ULTRASOUND SERVICE TRAINING
ULTRASOUND SERVICE TRAINING
PROBE REPAIR WITH FREE LOANERS
PROBE REPAIR WITH FREE LOANERS
NEXT DAY RENTALS
SERVICE ACROSS THE US
SERVICE ACROSS THE US
Mention this ad for 10% OFF your next part or repair.
Mention this ad for 10% OFF your next part or repair.
HAVING PROBLEMS WITH YOUR ULTRASOUND PROBE?
HAVING PROBLEMS WITH YOUR ULTRASOUND PROBE?
Scan the QR code and get an instant quote by using our free ultrasound probe evaluation tool.
Scan the QR code and get an instant quote by using our free ultrasound probe evaluation tool.
A.M. Bickford is the authorized US distributor and calibration service provider for the FI-8000P Riken Gas Indicator.
• The all-in-one solution for measuring gas concentration of Sevoflurane, Isoflurane, Desflurane, and Halothane.
• Updated software and firmware.
• Approximately 50% faster than previous model.
• Intuitive user experience.
• One-touch switching between gases.
Chad Senior Technician
LEASE OR BUY!
Monitors | Modules | Telemetry
Infusion Pumps | Defibrillators | ESU
You need to know it’s right. Who’s in your corner?
Our technicians know what’s at stake and are trained on a wide variety of OEM equipment. Our rigorous standards and inspections ensure that pre-owned equipment meets final approval before being labeled “T.Certified” and heading out the door. We understand the needs of healthcare professionals and work to provide the most efficient, detail-oriented solutions.
We’re in YOUR corner. Call today to schedule repairs, purchase parts or lease equipment.
Regardless of the make, model or field strength, we have the team and infrastructure to get almost any MRI coil back up and running.
Quickly
With over 35 years of experience and more than 45,000 successful repairs, you can trust your devices to be repaired to their original design.
Yes! We can repair your Philips dStream™, GE Air™ coils, and Invivo coils, and we can fully rebuild your coil’s system cable. All covered by a 6-month warranty.
Setup a repair or arrange for a loaner today 844-687-5100
customercare@innovatusimaging.com
Let's meet in-person at the CABMET and Heartland Biomedical Conferences in August!
P.12 SPOTLIGHT
p.12 Department of the Month: JPS Health Network Clinical Engineering Department
p.14 Professional of the Month: Donald Sims
p.16 Next Gen: Peyton Thomas
p.18 Association of the Month: The North Carolina Biomedical Association (NCBA)
P.20 INDUSTRY UPDATES
p.20 News & Notes
p.26 SPONSORED: Crothall Healthcare
p.28 AAMI Update
p.31 Ribbon Cutting: Hospital Sisters Mission Outreach
p.32 ECRI Update
p.35 Welcome to TechNation
P.36 THE BENCH
p.36 Biomed 101
p.39 Tools of the Trade
p.40 Webinar Wednesday
P.42 FEATURE ARTICLES
p.42 Roundtable: Training & Apprenticeships
p.46 Cover Story: Training Can Accelerate Your Career: Biomeds Have Choices
p.52 40 Under 40
P.70 EXPERT ADVICE
p.70 Career Center
p.72 SPONSORED: Innovatus Imaging
p.74 The Future
p.76 Cybersecurity
p.78 Networking News
PUBLISHER John M. Krieg
VICE PRESIDENT Kristin Leavoy
VICE PRESIDENT Jayme McKelvey OF SALES
EDITORIAL John Wallace
CONTRIBUTORS Roger Bowles
K. Richard Douglas
Jim Fedele
Joie Marhefka
Manny Roman
Steven J. Yelton
ACCOUNT Megan Cabot
EXECUTIVES Emily Hise
ART DEPARTMENT Karlee Gower
Taylor Hayes
Kameryn Johnson
DIGITAL SERVICES Cindy Galindo
Kennedy Krieg
Haley Harris
EVENTS Kristin Leavoy
WEBINARS Linda Hasluem
HTMJOBS.COM Kristen Register Sydney Krieg
ACCOUNTING Diane Costea
CIRCULATION Joanna Manjarrez
Rob Bundick, Director HTM & Biomedical Engineering, ProHealth Care
Carol Davis-Smith, CCE, FACCE, AAMIF, Owner/ President of Carol Davis-Smith & Associates, LLC
Jim Fedele, CBET, Senior Director of Clinical Engineering, UPMC
Bryant Hawkins Sr., Site Manager, Children’s Hospital of New Orleans
Benjamin Scoggin, MBA, MMCi, Director, Clinical Engineering | Biomedical Operations, Equipment Distribution, Clinical IT, DHTS, Duke Health Technology Solutions
Allison Woollford, Biomedical Equipment Specialist at Duke University Health System
Bryant Hawkins Sr., HTM on the Line, Trimedx Site Manager at Children’s of New Orleans
Dr. Brian Bell, HTM Workshop, Faculty Biomedical Engineering at St. Petersburg College in St. Petersburg, Florida
Carlos Villafane, BMET Latino, Certified Biomedical Engineering Technician III, Baycare Health Systems
Chace Torres, Bearded Biomed, Lead Technician SPBS, Dallas-Fort Worth Metroplex
Discover the perfect balance of quality HTM education and flexible learning with CBET. Programs designed to cater to the busy schedules of working adults, whether entering the HTM career field or seeking professional development, our 100% online courses offer convenience without compromising on excellence!
Experience innovative VR lab training integrated into select courses, crafted to enhance HTM technician education. Take your career to new heights with the College of Biomedical Equipment Technology.
BY K. RICHARD DOUGLAS
In January of 2016, TechNation highlighted the JPS Hospital clinical engineering team. As is the case with most biomed departments, a lot has changed in eight years. The pandemic was one big catalyst for change, but there were more common ones as well.
That was the case when the future mayor of Fort Worth, Texas, John Peter Smith deeded five acres of land in the downtown area in 1877. The hospital got its official name in 1954.
Today, JPS Health Network, in Fort Worth and the surrounding communities, includes a hospital on Main Street, a five-story Patient Care Pavilion, a facility providing psychiatric services and an outpatient care center. There is also an Oncology and Infusion Center, the Center for Pain Management and a number of clinics.
“We do have two technicians that are anesthesia trained and we do all anesthesia in house. We are also in the process of servicing all washers and sterilizers in house as well,” Betancourt says.
The CE team manages medical equipment for a level one trauma center supporting 550 beds, as well as a separate outpatient surgery center and supports 25-plus community clinics in the area.
The JPS CE team is balancing its responsibilities to serve its clinical colleagues and the patients in Fort Worth.
The Clinical Engineering Department at JPS Hospital has a different director than in 2016 and the team has grown by four members. Management is outsourced to Agiliti Health.
The team is made up of a staff of 29 members, including Director Mike Betancourt, a manager, a capital planning manager, a finance manager, biomed leads and an imaging lead, eight BMET IIs, seven BMET Is and four imaging engineers.
“We work closely with IT in the capital acquisition process gathering the MDS2 forms from a security perspective for new purchases. We just participated in a cybersecurity audit and are in the process of developing a network segmentation for medical equipment,” Betancourt says.
Service contracts are managed by the director who uses that as the basis for a training plan.
“We look at expiration dates and determine if we can get training completed. Our goal is to perform as much in house work as we can so that response time to issues is minimal and less disruptive to patient care,” Betancourt says.
He says that the department CMMS system, Vityl, keeps track of inventory.
In the problem-solving category, the CE team has organized its PM efforts into a methodical and organized
system which will create new levels of efficiency.
“We just level loaded our PMs in the whole system to put devices and departments into monthly schedules. This allows us to shift resources a lot easier and we can plan for vacation coverage since work is now more centralized versus going into all the departments every month,” Betancourt says.
He says that they took a look at the PMs that were due and realized that they needed to rebalance the work load.
“We have added staff to the department, and this was the right time to take a holistic look at our monthly PM workload. I put together a PM balancing team and they would help short cycle departments to get them in the correct month for the new schedule. We would then report out on our monthly EOC meeting the results from our prior month’s work and what departments were coming due so they could prep for our visit,” Betancourt says.
He says that some operations needed the biomeds to come in after hours so they did not interrupt patient care.
“Balancing our PMs allows us to also concentrate on getting corrective work orders turned around quicker. With us not having to go to every department each month, we turned our corrective work order turn-around time from 10 days to 7.1 days. Not resting on our laurels, we are shooting for 6.5 days in 2024,” Betancourt adds.
The team is involved in AAMI and three of its members have earned the BMET certification.
“I am looking to increase those numbers in the near future,” Betancourt says.
The JPS CE team is balancing its responsibilities to serve its clinical colleagues and the patients in Fort Worth.
BY K. RICHARD DOUGLAS
Baylor University Medical Center is a part of the Baylor Scott & White Health System. It has 1,025 licensed beds and is a major health care provider in North Texas.
Many of the biomeds who manage medical equipment at the medical center went through formal biomed training curriculums to become biomeds.
But the biomed profession has feeder professions; similar professions that include overlapping skill sets. Some biomeds take this route to an HTM career.
Donald Sims, biomedical equipment technician II in the Healthcare Technology Management Department at Baylor University Medical Center, is among those who took an indirect route into HTM.
“I went to ATI (ATI Tech Training Center) to learn electronics,” Sims says.
He graduated in 1995 with a 4.0 GPA, a major in electronics and a minor in computers.
“I started my studies of basic electronics, followed by an in-depth study of digital and analog, in late 1993. Although the school was difficult because of my dyslexia, I still graduated third in my class. The course also covered computer repair and basic networking, which I found to be the most fun. I still
enjoy working with computers and networking when I get the chance,” Sims says.
He says that he switched from working with just nurse call and intercom systems to working on medical equipment because the company where he worked for 20 years went bankrupt.
“If it weren’t for that, most likely, I would still be working there. I was never the type of person who jumped from job to job. However, now, I see it as the best thing that ever happened to me. Because the manager of biomed at that time believed in me and wanted me to join his team. I have been learning and experiencing new things,” Sims says.
He says that he worked on nurse call, intercom and RTLS systems for 20 years, which provided him with a good understanding of computers and networking.
At a major medical center, it is understandable that biomeds would be called upon to pitch in for major projects. One of the projects that Sims was involved in was helping to complete the PMs, battery replacement and a drug library upgrade on 2,800 IV pumps.
“This was incredibly challenging because of the size of our hospital and the time that we had. We had to touch the pumps three different times to accomplish this. Each time we thought we were completed, something else came up,” Sims says.
He says that each pump had to be found and returned three times to complete the PMs and projects
in three months.
“I know it’s an old saying, but imagine digging through a pile of needles to find a needle three different times. We first had to find pumps with an outdated PM label and then pumps without a battery replacement sticker. After that, we started using tie straps to identify pumps with the updated drug library. If I did my math right, we were doing all of this in a hospital that has seven buildings and 57 floors,” Sims says.
When not working at the medical center, Sims enjoys outdoor pastimes.
“Doesn’t matter if I’m working or doing other things like hiking or camping. Well, when I was younger, I enjoyed hiking in the woods and camping out with my friends on their land. But now, because of limited personal time, I enjoy walking around the neighborhood with my wife and kids. I also work in the yard most weekends just to keep up with the yard work. I know that sounds like not much fun, but like I said, I enjoy being outside and working,” Sims says.
He is married and has two kids; a son and daughter.
Sims recalls the sequence of events that led to joining the HTM profession.
“I have been working on electronic equipment for the last 29 years. My first job was as a bench tech repairing PC monitors and refurbishing computers. After five years, I went to a company that sold and maintained nurse call, RTLS, intercom and other systems, until the company went bankrupt in 2019,” he says.
For a short time, he worked for the nurse call system manufacturer and became a certified systems integrator.
“In May 2020, I was offered a job and I started my career in HTM,” Sims says.
In his first year, his HTM peers voted him to be the employee of the month. He was awarded 1,500 points by the vice president.
Sim’s nominator said, “As Baylor University Medical Center’s nurse call specialist, Donald is often called upon to assist with nurse call replacement efforts. He is always happy to assist with regional facilities when they are having nurse call issues. He has even gone to other facilities like Plano to troubleshoot and fix the issues.”
In a short time, Sims has proven his value to his team and showed the value of his years working on electronic equipment.
FAVORITE BOOK: “Lord of the Rings”
FAVORITE MOVIE: Marvel movies
HIDDEN TALENT:
I’ve been told I’m good at troubleshooting.
FAVORITE FOOD: Italian
FAVORITE PART OF BEING A BIOMED?
Working with new technology and my peers.
Peyton Thomas earned his associate degree in biomedical engineering technology from Howard Community College and holds certificates in electronics technology and biomedical engineer specialist. He is currently a biomedical equipment technician at WellSpan Chambersburg Hospital. TechNation found more about this promising HTM professional in a recent Q&A session.
Q: WHERE DID YOU GROW UP?
A: I grew up in Chambersburg, Pennsylvania.
Q: WHERE DID YOU RECEIVE YOUR HTM TRAINING/ EDUCATION?
A: Howard Community College in Columbia, Maryland.
Q: HOW DID YOU FIRST DISCOVER HTM?
A: A family member worked in health care, and said biomed would be a field I may be interested in.
Q: HOW DID YOU CHOOSE TO GET INTO THIS FIELD?
A: I was enrolled in a mechatronics/electromechanical vocational program in high school. A background in electronics and a desire to be in health care led me to a career in HTM.
Q: WHAT DO YOU LIKE MOST ABOUT YOUR POSITION?
A: I enjoy making an impact. You know going into every day that you are making a difference.
Q: WHAT INTERESTS YOU THE MOST ABOUT HTM?
A: Every day is an opportunity to learn something new.
Q: WHAT HAS BEEN YOUR GREATEST ACCOMPLISHMENT IN YOUR FIELD THUS FAR?
A: I am certified on our dialysis and CRRT units and keep the department running smoothly.
Q: WHAT GOALS DO YOU HAVE FOR YOURSELF IN THE NEXT 5 YEARS?
A: I would like to get my CBET and CCNA certification.
FAVORITE HOBBY: Watching sports
FAVORITE SHOW OR MOVIE: “Unsolved Mysteries”
FAVORITE MEAL: Smoked brisket with mac & cheese
WHAT WOULD YOUR SUPERPOWER BE? Teleportation
1 THING ON YOUR BUCKET LIST: Visit the Maldives
SOMETHING YOUR CO-WORKERS DON’T KNOW ABOUT YOU:
If biomed wasn’t an option for me, I would’ve gone to school to be an aviation mechanic.
The Insulation tester, Leak Tester Tester, Shaver Leak Tester and Cable Continuity Tester are easy-to-use devices for verifying the functionality of equipment for safety
McGan Insulation Tester
Detect & locate defects such as pinholes, cracks and bare spots in the jacket or coating of laparoscopic and bi-polar electrosurgical instruments
Test the functionality of automated & handheld endoscope leakage testers with healthmark’s new Leak Tester Tester.
Test the quality of monopolar and bipolar cords with this user-friendly, durable device. A green light noti es the user that the cable passed testing.
Shaver Leak Tester
Designed for pressure testing arthroscopic shavers to help identify leaks caused by failing seals that degrade over time from repeated use and processing.
For more of Healthmark’s intelligent solutions for instrument care & infection control, visit hmark.com hmark.com | 800.521.6224 | healthmark@hmark.com
BY K. RICHARD DOUGLAS
From Cape Hatteras and the Outer Banks on the Atlantic coast to the Blue Ridge Parkway and Ashville in the west, the state of North Carolina offers diverse scenery and plenty of outdoor activities.
The state’s biomed association may be as storied as the state itself. The North Carolina Biomedical Association (NCBA) has been a model for other biomed associations in many ways.
“The NCBA was originated in the late 1970s by a group of giants in our industry. Our founding members met and developed our by-laws. While being massaged and updated over the years many other organizations around the country established their by-laws based upon what these founders developed. November 5, 1980 was the first election for the NCBA board of directors,” says NCBA President Mike McAuliffe.
There are several people who made the organization possible.
“We all owe our founding board of director’s a giant dose of gratitude,” McAuliffe says.
Those founders include President Patrick K. Lynch, CBET; Vice President W. Glenn Scales, CBET; Secretary Wes Cormac; Treasurer Eddy G. Whisnant; and Directors Jim Downing; Frank Forrest, CBET; Dave Curry; Dr. J.C. Boone; Clint Crites, CBET; and Bob Strickland, R.H.Ed.
The current NCBA Board of Directors meets once a month.
“Our meetings are not simulcast; however, they are open to all members of the association. We publish our meeting dates, times, and locations on our website (ncbiomedassoc. com),” McAuliffe says.
The association offers multiple scholarships.
“We offer three different scholarships – Eddy Whisnant, Norman Reeves and the W. Glenn Scales. The Eddy and Norman are both for students in North Carolina biomedical programs. They are both a $2,000 scholarship. The Glenn Scales scholarship is for a NCBA member who is pursuing an
advanced degree. It is $5,000,” McAuliffe says.
He says that the group works closely with higher education. A few of the board members are on advisory boards for the colleges.
“We offer a drastically reduced rate for students enrolled in area colleges to attend our annual conference,” McAuliffe adds.
The group’s annual conference is at a new venue this year.
“Our annual conference will be held in Cherokee, North Carolina, at the Cherokee Resort and Casino this August 19-21st. Registration opened March 1. This is our first of at least two years at Cherokee. The symposium has been held in Pinehurst for several years, however this year Pinehurst is hosting the U.S. Open, and we simply could not afford to have our show there,” McAuliffe says.
He adds that the NCBA had maxed out its vendor booth space in Pinehurst.
“It was hard to tell vendors that we don’t have room for them. Now moving to Cherokee, we have expanded our vendor hall and class space. We can offer a better room rate to our members. This is the first time the NCBA has hosted an event in Western North Carolina,” McAuliffe says.
He says the group hopes to draw some attendance from Eastern Tennessee, Upstate South Carolina and Georgia.
“The NCBA has always drawn attendance from across the country and we expect this year to be no different. It will be nice to have our entire meeting under one roof. There are multiple food and entertainment options available for all ages so once you arrive, there will be little reason to leave,” McAuliffe adds.
He says that the association’s conference last year was its 45th annual symposium.
“We had awesome attendance and the feedback received about our education; [it] was very encouraging. Our vendor hall was filled to capacity with over 80 unique vendor booths. That said, we always want to do better and advance our field. Our 46th annual symposium is shaping up to be our biggest and best show ever. Space for vendors or educational classes should not be an issue. We had excellent door
prizes last year; everything from a BBQ smoker to an ultrasound system was given away. The NCBA vendors spare no cost for prizes and opportunities. It’s almost like they one up each other to create excitement. The board of directors loves the enthusiasm this brings to the show,” McAuliffe says.
He adds that the golf tournament is always sold out.
“Of course, its typically at Pinehurst, so there is a mystique about playing there. I myself am not a golfer, however Aaron Watts, our golf coordinator, assures me that Sequoia National in Cherokee is a much nicer course than what we historically play at Pinehurst. So, bring your clubs and register early for golf. Cherokee is also surrounded by several beautiful creeks and streams. People come from all over to trout fish these waters. If you can stay an extra day to fish; I don’t blame you,” McAuliffe says.
He says that highly sought after classes will be a part of the symposium with an emphasis on hands-on training whenever possible.
“The last thing we want is death by PowerPoint or a sales pitch. The NCBA offers multiple tracts of education. We have BMET classes geared towards beginners or basic BMETs. Advanced BMET for those who have been in the business a few years and need more advanced training. Imaging for both seasoned imaging personnel or those advanced BMETs who are looking for a way to advance. IT tract which helps everyone across the board do their job better, from working with MS Office to setting up a PACS network,” McAuliffe says.
He says there are even management classes for managers and advanced technicians.
“We even host a roundtable with area hospital C-suite
leaders to discuss pain points and help BMETs work with and understand this group’s needs better. And finally, safety and regulatory; we work with Joint Commission and DNV to understand the ever-changing landscape of regulations,” McAuliffe adds.
With the experiences brought by the pandemic to biomed associations, McAuliffe says that NCBA became a little more cautious about their money spend.
“We were able to negotiate a better deal at Cherokee for both us and the hotel due to COVID. I see this slowly going away. We have always run the NCBA with a razor-thin budget so we weren’t negatively affected to bad. We also keep a couple rainy day CDs to protect the association. Having a few dollars in the bank allows us too keep moving forward. Our show basically pays for itself and our scholarships. We treat every dollar like it’s our own and don’t waste a cent. Last year, we had a company not able to fund one of our scholarships until after the deadline. The NCBA vendors stepped up big time! With donations from $250 to $2,500, we had more than enough money to cover the scholarship in a matter of hours. We plan ahead a little more thoroughly now, but otherwise it’s business as usual for us,” McAuliffe says.
There is little doubt why NCBA, and its 40-plus year history, have been the model for many other biomed associations.
Scholarship information: https://ncbiomedassoc.com/scholarships-awards
TruAsset CMMS software is continually evolving to meet the ever-changing needs of its customers in health care. As changes occur in the industry, TruAsset continues integrating with the products its customers are using to streamline the process for HTM professionals. The addition of the integration with Equiptrack will allow efficiency in the processing of FDA recalls and streamlining patient safety processes.
Equiptrack integration will allow clients to receive notifications for FDA recalls within the CMMS and open work orders to address the recalls that are relevant to their asset inventory. This adds value in remaining on top of patient safety and efficiency.
Equiptrack started with an overall idea – to be the leading source of analyzed FDA Recall data and maintenance reports for buyers and resellers of used medical equipment. Today, Equiptrack continues to build the equipment buyer focused
medical equipment maintenance report database available with Equiptrack Reports, online medical equipment store apps and FDA Recall API services.
TruAsset is a CMMS solution that was created specifically with independent service organizations, HTM, and plant operations/ maintenance teams in mind. There was a prevalent need for a system capable of centralizing and running all aspects of maintenance management, so the TruAsset team decided to build it. Understanding how essential it can be to have immediate access to asset data, TruAsset is available wherever you have Internet access for everyone whether through a computer, tablet or smartphone. No matter where jobs take you, the TruAsset computerized maintenance management system (CMMS) is at your fingertips.
FSI, a health care CMMS/EAM provider, has announced two new integrations with PartsSource and Cynerio.
The strategic partnerships are seen as an opportunity to alleviate current challenges for health care facilities and HTM professionals as they manage across siloed software platforms, according to a news release announcing the partnerships.
“Our product constantly needs to evolve and bring our customers value that not only meets their expectations, but exceeds them,” said Zachary Seely, CEO of FSI. “We are thrilled to partner with Cynerio and PartsSource, two leading software providers in the health care space, creating a seamless experience for the end user.”
In a hospital setting, the need for several software solutions that address IoT cybersecurity, compliance and supply chain are required to support business operations. The FSI, PartsSource and Cynerio integrations save departments time and resources as tools can communicate across the business, the release adds.
FSI’s PartsSource integration allows users to launch PartsSource from within a work order to seamlessly order parts and materials as part of their CMS WO workflow.
“This partnership and workflow integration with FSI is instrumen-
tal in supporting our evolving ‘facilities & workspace solutions’ modality here at PartsSource and bringing even more value and efficiency for our mutual customers,” said Butch Ellis, senior director/ general manager-facilities. “We are very excited about the partnership and what it offers our health care customers.”
The Cynerio integration focuses on the management of connected medical devices – a challenge at the forefront for many within the HTM industry. Using FSI’s Public API (Application Programming Interface), the integration automates the creation of work orders for the identification of vulnerable assets and their proper assignments within CMS solution’s normal workflows.
“We are excited to integrate our advanced cybersecurity solutions with FSI’s comprehensive CMMS,” said Leon Lerman, CEO and co-founder of Cynerio. “This partnership allows us to enhance the security posture of health care facilities by seamlessly incorporating real-time IoT data into their maintenance workflows, ensuring that vulnerable medical devices are quickly identified and secured.”
Each integration will connect with FSI’s CMMS/EAM suite of products (CMS) to offer a streamlined approach to cyber-threat and parts management.
Hospitals along the Gulf Coast and Eastern Seaboard are intensifying their preparation efforts to ensure they’re ready for any patient surges during hurricane season. As storms threaten to test the resilience of health care facilities, US Med-Equip – a provider of medical equipment rentals, sales, and services – is helping clinicians across the country continue their vital work, no matter what the weather brings.
With the increased frequency and severity of tropical storms, hospitals in hurricane-prone areas face the daunting task of ensuring they have sufficient medical equipment to handle potential surges in patient volume, power outages and supply chain disruptions.
“US Med-Equip is trusted by hospitals, in part, for its equipment rentals and team’s ability to respond quickly to urgent needs,” according to a press release. “The health care company has strategically located service centers and a vast inventory of medical equipment, including ventilators, infusion pumps, and patient monitors, ready for immediate deployment. This rapid response capability is crucial during hurricane season when hospitals may face sudden equipment shortages.”
“Our goal is to support health care heroes who are on the front lines no matter the circumstances,” Greg Salario, CEO of US Med-Equip, said. “US Med-Equip was founded on the Gulf Coast, and for the past 20 years our team has helped hospital partners brace for hurricanes and supported them afterwards so clinicians could focus on what they do best every day – save lives.”
In addition to its extensive inventory, US Med-Equip offers rental agreements that allow hospitals to scale up their resources quickly and cost-effectively, according to the release.
“This flexibility is particularly beneficial in the face of unpredictable natural disasters, enabling hospitals to maintain high standards of care without the burden of high-capital or long-term commitments,” the release states.
As hurricane season looms, US Med-Equip is also providing biomedical support services to ensure that hospitals’ rented and purchased equipment is maintained to the highest standards. The company’s certified technicians are on standby to perform on-site repairs and maintenance, ensuring hospitals can rely on their equipment when it’s needed most.
Sodexo has announced its achievement of the ISO 13485:2016 certification for its Quality Management System. This certification, issued by NSF International Strategic Registrations (NSF-ISR), underscores Sodexo’s commitment to maintaining the highest standards in the management and maintenance of medical equipment for healthcare delivery organizations. ISO 13485 is the quality management systems standard for the medical device industry.
This milestone places Sodexo among the elite in the healthcare technology management industry, recognizing the organization’s dedication to meeting rigorous quality standards. The ISO 13485 certification reflects Sodexo’s substantial investment in quality management and operational excellence, marking a significant achievement in the company’s ongoing mission to enhance healthcare services.
“We are very happy to have earned our ISO 13485 certificate,” said David Franklin, Sodexo Vice President. “This achievement demonstrates the strength of Sodexo quality and regulatory compliance.”
The 2024 GBIS Technical Conference is set for August 16-17 at the Piedmont Athens Regional Medical Service Building (242 King Ave, Athens, GA 30606).
This year’s conference is dedicated to GBIS co-founder Horace Hunter – a true pioneer and promoter of GBIS until his passing.
HTM professionals are invited to attend the conference. It will offer multiple technical and management classes. Educational sessions include one on project management along with classes on surgical table service, basic PM training and more.
Attendees can expect the following:
• professional development opportunities
Electrical test and measurement specialist Seaward Electronic Ltd has appointed a senior executive to oversee its global brand and business development as it invests further in international operations.
Amy Lyons joins as international business development manager at the Peterlee-based firm in a move that will see her working alongside the senior management and sales teams to open up new routes and markets for the company’s range of multi-function industrial and production line electrical testers, notably the HAL series.
A key brief will be to continue to develop Seaward’s presence and reach across Europe and Asia, where there is significant opportunity to build additional brand awareness and market share among electrical product manufacturers and suppliers requiring high quality test and measurement technologies. She will also oversee the opening of new routes to market and provide support for the company’s network of international sales and distribution partners while showcasing Seaward products and network building at international industry exhibitions, seminars and events.
“We commend Sodexo on prioritizing quality in medical devices by achieving certification to ISO 13485,” stated Sameer Vachani, Senior Director of NSF-ISR. “Companies certified to the ISO 13485 standard show they are actively implementing quality management systems in their organization, supporting the health and safety of their workforce, customers, and end users.”
The scope of Sodexo’s certification includes the management and maintenance of medical equipment for healthcare delivery organizations. This certification confirms that Sodexo’s Quality Management System meets the stringent requirements set forth by the ISO 13485:2016 standard, ensuring the highest level of safety and efficiency in healthcare technology management.
“The certification represents a major investment,” said Franklin. “And it demonstrates Sodexo’s unwavering commitment to excellence in healthcare technology management.”
• health care product demos
• equipment service training
• networking opportunities
• vendor showcase
A final AAMI-certified class schedule will be provided later.
GBIS will host a “Meet N Greet” on Friday, August 16 from 6-9 p.m. at the Athentic Brewing Company (108 Park Ave, Athens, GA 30601) with two free drink tickets per person. There will also be a food truck on site with great food options.
For more information, visit gbis.wildapricot.org.
Bringing 20 years’ experience and expertise in sales and marketing, product management and electrical engineering to the position, Lyons rejoins Seaward in an expansive role that will also see her develop new opportunities and commercial ventures with parent company GMC’s global network of customers, suppliers and partners.
“We are committed to hiring the best industry talent to support our growth and ambitions. It’s fantastic to have Amy back on board with her strong experience, sector knowledge and track record in international business development work and corporate brand building,” CEO Chris Callan said.
Intermountain Health has been ranked the top large health system in the nation by Fortune magazine and PINC AI, as a part of their annual evaluation and rankings of the nation’s best health systems for 2024.
This is Intermountain Health’s second consecutive year on the prestigious list – and the first time the health system has been ranked number one.
The Fortune magazine analysis found that if all health systems in the United States performed like Intermountain Health and leading systems on the list, it would result in 220,000 fewer patient deaths and 196,000 fewer patients experiencing complications during their hospital stays.
“I’m beyond proud of our entire team of caregivers who have put in the work to make this possible,” said Rob Allen, president and CEO or Intermountain Health. “This ranking is a tribute to their expertise and dedication to helping people live the healthiest lives possible.”
Intermountain continues to be a national leader in health care thanks to its outstanding clinical outcomes, cutting-edge
medical research to enhance patient care, telehealth capabilities to enhance access, and focus on preventive care and overall wellness.
Headquartered in Utah with locations in six states and additional operations across the western U.S., Intermountain Health is a nonprofit system of 33 hospitals, 385 clinics, medical groups with some 4,600 employed physicians and advanced care providers, a health plans division called Select Health with more than one million members, and other health services. Helping people live the healthiest lives possible, Intermountain is committed to improving community health and is widely recognized as a leader in transforming healthcare by using evidence-based best practices to consistently deliver high-quality outcomes at sustainable costs.
The Fortune/PINC AI ranking is based off publicly available health data from 355 health systems across the country. The study looked at eight performance indicators including clinical outcomes, inpatient mortality, average length of hospital stays, and overall patient experience.
MD Publishing, the parent company of TechNation and MD Expo, is excited to announce that an HTM Mixer is coming to Lexington, Kentucky.
The HTM Mixer Lexington, proudly supported by KAMI, will start on Friday, November 15 and conclude on Saturday, November 16 at the Marriott Resort Griffin Gate (1800 Newtown Pike, Lexington, KY 40511).
An HTM Mixer has everything an MD Expo offers HTM professionals just on a smaller scale. Think of it as a hybrid event that combines the best of a state association annual meeting and an MD Expo. The two-day conference includes an exhibit hall, educational opportunities and networking events.
MD Publishing President John Krieg is excited to partner with KAMI and add this educational and networking event to the 2024 calendar.
For more information, visit HTMMixer.com.
HTM Week 2024 went by too fast! However, five lucky biomeds took home a $100 Amazon gift card via a TechNation contest sponsored by Healthmark Industries.
HTM Week is a week that promotes awareness and appreciation of professionals who manage and maintain a variety of medical devices and health technology in hospitals, clinics and throughout health care systems.
The 2024 HTM Week Contest winners are:
• Lowell Pitman, HTS Manager
• Smitha Krishnan, BMET II
• Jody Booth, Biomed Technician
• Joel Coffman, BMET
• Alexis Hayley, Biomedical Engineer
TechNation magazine continues to promote and applaud the men and women of HTM with the second annual Tech Choice Awards. The Tech Choice Awards (also known as the Wrenchies) shine a spotlight on the heroes of HTM.
“We are excited to carry the Tech Choice Awards into 2025,” MD Publishing Vice President of Sales Jayme McKelvey said. “TechNation is constantly looking for ways to celebrate the hard work and innovations of the biomedical and HTM industry. These awards give us another opportunity to recognize individuals, departments and organizations for their contributions and achievements. But, my favorite thing about the Tech Choice Awards is they make people feel valued and inspired, which can lead to increased productivity and engagement. When that happens, we all win!”
The Tech Choice Award categories are:
• Professional of the Year, sponsored by 626 Holdings
• Department of the Year, sponsored by USOC Medical
• Young Professional of the Year, sponsored by Prescott’s
• ISO Employee of the Year
• Director/Manager of the Year, sponsored
by MW Imaging
• Military BMET of the Year, sponsored by College of Biomedical Equipment Technology
• Lifetime Achievement Award, sponsored by Renovo Solutions
• Humanitarian Award, sponsored by Pronk Technologies
• Women in Leadership Award, sponsored by Avante Health Solutions
• Industry Influencer of the Year, sponsored by Soma Tech Intl
• Outstanding Vendor of the Year
• Association of the Year, sponsored by MultiMedical Systems
• Educator of the Year
The deadline to submit a nomination is August 16, 2024. Visit 1technation.com/techchoiceawards to nominate yourself or someone else.
BY RICHARD ELIASON, SENIOR DIRECTOR OF QUALITY & COMPLIANCE, CROTHALL HEALTHCARE
Few words strike fear in the hearts of hospital employees like “Surveyors are in the building.” Unannounced, a group of strangers just entered your place of work to evaluate your operation, they will probably be there several days, and everybody’s stress level is high. Vacations may be canceled, meetings put on hold, and general day-to-day operations are upended.
As an Independent Service Organization, Crothall’s Healthcare Technology Solutions (HTS) team has participated in and helped hundreds of hospitals successfully prepare for these accreditation surveys. In 8 years, 2016-2023, our HTS division supported over 220 successful surveys and 14 already in 2024. Our team of Quality & Compliance specialists is well-versed in the complexities of the hospital accreditation process. Drawing on a wealth of knowledge from each successful survey, they gather and analyze extensive data, providing crucial insights that greatly benefit our hospital partners. This expertise enables these hospitals to understand precisely what is required to prepare effectively for accreditation surveys. By tapping into this resource, facilities can enhance their readiness and compliance, ensuring they meet the rigorous standards set by accreditation organizations (AOs).
Some hospitals may not have the resources to maintain a large technology staff like an ISO; however, this should not hinder their ability to successfully pass accreditation surveys. It’s crucial to recognize and utilize all available tools and support systems, perhaps including external expertise and streamlined processes, to ensure thorough preparation. By leveraging these resources, even hospitals with small in-house teams can navigate the complexities of AO compliance effectively and ensure they meet the high standards required for accreditation.
Here are four recommendations that can help you prepare for your next accreditation survey:
It is essential not only to identify the key Accreditation Organizations governing your Medical Equipment Management program but also to understand the emphases and expectations of each accrediting body and its surveyors. Deemed status organizations such as DNV and The Joint Commission (TJC), in addition to
addressing CMS “conditions of participation” also have unique focal points and criteria that they use to measure compliance.
The Joint Commission, which accredits over 4,000 hospitals, has emphasized infection control in recent years, closely linking it to the environment of care and the quality of medical equipment performance and maintenance. This highlights the importance of not just meeting the baseline requirements, but also prioritizing areas of heightened scrutiny.
Understanding an AO’s expectations enables you to proactively address areas of concern. This involves tailoring your internal audits and compliance checks to anticipate these areas of interest, thereby enhancing your preparedness, and ensuring that your facilities meet both the letter and the spirit of the standards. This strategic approach allows you to prepare thoroughly for inspections and address issues before they arise during accreditation surveys. Ultimately, this leads to better compliance outcomes and smoother accreditation processes, ensuring that your facility meets the highest standards of care and safety.
We’ve found in recent surveys that they also focus on the accuracy of the medical equipment inventory including the number and percentage of medical devices designated as “Unable to Locate.” They also focused on scheduled maintenance completion rates for High-Risk devices, Alternate Equipment Management (AEM) devices, Alternate Equipment Management Exempt (AEM-E) devices, and the qualifications and competency of HTM personnel.
HTM departments need to understand and be able to interpret all the information in their Computerized Maintenance Management System (CMMS). Surveyors will ask HTM staff to run reports covering a wide variety of topics, such as their inventory of key pieces of medical equipment.
Staff must be ready to discuss the details of their Medical Equipment Management Program (MEMP) and the related policies, procedures, work instructions, and program processes. We have found surveyors will ask HTM staff to explain the details of specific program processes, such as AEM methodology risk assessment and even the cybersecurity measures used to protect key medical equipment.
Just as important as providing documentation, hospitals need to demonstrate the safety and effectiveness of their MEMP. The surveyors will want to know an HTM department’s goals, objectives, and performance improvement initiatives; whether
they are meeting those criteria, and how they measure success. In effect, you will need to provide a comprehensive explanation with objective evidence of the entire Medical Equipment Management Program.
Do you know the difference? Hospital staff must also work with their healthcare technology management partners before the survey to delineate certain responsibilities for key elements of the MEMP. Some AO medical equipment management standards may be out of the HTM department’s direct control and managed and documented by other departments.
For example, some HTM departments may be responsible for maintaining dialysis equipment while not necessarily responsible for managing the RO system and conducting the requisite biological/chemical water testing. However, they are still held accountable for these tests being performed under the medical equipment management standard. Therefore, it is important to know who and which entity within the facility is ultimately responsible for managing, conducting, and documenting these tests to remain compliant.
To ensure a smooth survey process, both the hospital and the HTM department need to collaborate and clearly understand which party is responsible for each activity under the medical equipment management standards. Knowing who your resources are and where they can be found enables you to provide accurate and confident responses to surveyor questions. Instead of saying “I’m not sure,” you can confidently state, “I will consult with [name] in our [department] and provide you with an answer promptly.”
The best way to prepare for a survey is to never stop preparing for a survey. Be survey-ready every day. There’s no better way to prepare than by conducting an honest assessment of your medical equipment management program and identifying any
potential gaps. As part of this exercise, an HTM department should assess the following Medical Equipment Management Program elements (among others):
• Inventory accuracy including the ability to readily identify HR, AEM, AEM-E equipment
• Staff qualifications and technical competency
• Properly documented maintenance activities
• Staff understanding of the MEMP
• All AO-specific MEMP standards and requirements have been addressed in your MEMP and associated policies/procedures
• Routine evaluation of MEMP safety and effectiveness
• Monitor and communicate AO standard changes After your assessment, it is essential to review the results and create an action plan that details the key focus areas scrutinized during the assessment. This action plan should offer an evaluation of the findings, identify areas where compliance was achieved as well as where it fell short, and propose actionable recommendations for improvement. By systematically addressing each critical aspect of the survey, the action plan serves as a valuable tool for ongoing quality assurance and helps to ensure continuous alignment with accreditation standards.
To effectively prepare for an inspection in the HTM department, especially considering the anticipated retirement of seasoned staff, it’s essential to implement a comprehensive knowledge transfer and succession planning program. By pairing experienced engineers with emerging talents through mentorship or formal training initiatives, your HTM department can preserve invaluable institutional knowledge and technical expertise. This strategy not only facilitates a smooth transition of responsibilities but also signals to TJC and other deemed status AOs your commitment to maintaining excellence and operational stability, regardless of staff turnover. This proactive approach ensures that the department remains well-equipped to meet rigorous standards, safeguarding its readiness for any AO scrutiny.
Effectively preparing for an accreditation survey requires a multifaceted approach that encompasses understanding the expectations of your accreditation organization, being aware of your resources, clearly delineating accountability from responsibility, conducting Quality Assurance Assessments, and ensuring continuity amid change. By integrating these strategies, organizations can navigate the complexities of accreditation compliance with confidence and precision. This comprehensive preparation not only enhances the likelihood of a successful accreditation outcome but also strengthens the overall operational integrity and resilience of the organization in the face of ongoing changes and challenges.
For those seeking additional support, feel free to contact me at Richard.Eliason@Crothall.com. For more information about Crothall Healthcare, visit our website at Crothall.com.
Day three of the AAMI eXchange featured an open forum on whether medical device servicing should be subject to additional regulations. This debate comes hot on the heels of the “Final Guidance to Clarify ‘Remanufacturing’ of Devices that Need Maintenance or Repair,” issued by the U.S. FDA this past May, 2024.
While AAMI does not take a stance for hotly contested issues of policy, the association does provide a neutral forum for conversations among members. The session featured Dr. Binseng Wang, vice president of program management for healthcare technology management at Sodexo and G. Wayne Moore, founding partner at Acertara Acoustic Laboratories. Larry Hertzler, chief operating officer at The InterMed Group, moderated the event.
Moore took the floor first, indicating that right-to-repair issues are best resolved between stakeholders rather than by government intervention. Also, “my position is that third-party servicers … should be regulated, actively regulated, by FDA,” even if HTM professionals in hospitals should be allowed more leeway.
Wang strongly disagreed, stating that given FDA’s statutory authority to regulate, “everyone under the sun should be regulated equally.”
Hertzler then pressed on, presenting the pair with a number of questions to discuss.
IF THE RIGHT TO REPAIR LEGISLATION FORCES THE OEMS TO RELEASE SERVICE MATERIALS, WOULD THIS REQUIRE OEMS TO REVEAL TRADE SECRETS AND INTELLECTUAL PROPERTY (IP)?
According to Moore, “not necessarily.” State and federal right to repair legislation has stated that OEMs will not have to give up trade secrets or intellectual property. Right to repair legislation
is likely to result in OEMs compartmentalizing service-related software and moving away from the integrated software approach. But if the right to repair were made retrospective, it could create vulnerabilities to cyberattacks.
Wang concurred, stating, “the answer is definitely no.” Trade secrets will remain safe, and there are plenty of legal remedies to protect intellectual property, such as NDAs. Further, international manufacturers have not faced this issue and software compartmentalization is a valid option.
IF THE THIRD PARTIES ARE NOT REGULATED BY THE FDA, HOW CAN ONE BE SURE THAT THEY ARE NOT EXCEEDING SERVICING LIMITS AND VENTURING INTO REMANUFACTURING?
According to Wang, the lack of available information on remanufacturing is comparable to a local government issuing speeding tickets without posting a speed limit. Also, the EU has explicit requirements for manufacturers to provide information, and America should do the same.
Moore stated, “I don’t believe in unintentional manufacturing.” He believes that FDA provides sufficient information to HTM professionals. It is their responsibility to look up available specifications. “Go find the information or don’t do it.”
Per Moore, the fact that OEMs are required to be registered and third-party services are not creates a “blind spot” for FDA of between 15-20 thousand non-registered entities. Registration requirements for third-party services would create welcome clarity. Further, FDA registration would apply only to third-party ISO and OEM servicers, rather than hospital employed HTM workers. Notably, Moore did not see any major concerns that he would place in the “con” category.
Wang, however, was concerned with how in-house hospital employees and federal employees are unregulated. Good patient care should be the North Star, and Wang noted that OEMs were more cooperative during the pandemic. Even minor delays from OEMs can accumulate and result in harm to patients. Wang also expressed skepticism that FDA intervention
would be effective, noting that there are still challenges for medical device manufacturers that current regulatory intervention does not always solve.
SHOULD SERVICING INFORMATION FROM OEMS BE AVAILABLE TO ANYONE WHO WANTS IT?
“The short answer is ‘no,’” said Wang. He elaborated, suggesting that the U.S. should follow the EU’s example, and have manufacturers release information to buyers or owners of equipment.
Moore kept his remarks even more brief. “I agree.”
IN ITS FINAL VERSION OF THE REMANUFACTURING GUIDANCE, THE FDA STATED THAT “CONSISTENT WITH PROMOTING AND PROTECTING THE PUBLIC HEALTH, FDA ENCOURAGES OEMS, AS AN INDUSTRY BEST PRACTICE, TO PROVIDE SERVICING INSTRUCTIONS THAT FACILITATE ROUTINE MAINTENANCE AND REPAIR OF THEIR REUSABLE DEVICES.” WOULDN’T THIS STATEMENT PREEMPT THE NEED FOR A NEW REGULATION OR RIGHT TO REPAIR LAW?
Moore noted that FDA encouragements are not legal requirements. If FDA established requirements this would create clarity, but the agency uses language such as “routine,” that are open to interpretation. He suggested that panel attendees check out an FDA training held on June 27 related to the issue.
Wang, however, reiterated his point about the speed limit. Without the right information, device servicers cannot know the right course of action. Wang would prefer equal treatment for hospital employees and third-party services alike. After all, they are “under the same pressure” and a distinction based on which entity disburses the paycheck is “really absurd.”
WHAT’S YOUR TAKE ON THE OPTIMAL WAY TO MOVE THE RIGHT TO REPAIR ISSUE FORWARD TO A “FINAL” CONCLUSION?
Wang noted that the 2018 FDA Report on Device Servicing included no evidence of major public health concerns. In fact, more widespread inspections would tax FDA’s limited resources. In Wang’s words, full FDA regulation would amount to solving a cockroach problem with a nuclear missile. Instead, memoranda of understanding among OEMs and servicers is the best possible outcome.
Moore concurred that he would rather have third-party services and manufacturers solve this issue among themselves. But he believes that having third-party services registered with FDA would give the agency vital information. While FDA did not find evidence of a public health risk, “the absence of evidence isn’t the evidence of its absence.”
The debate over this key issue is far from over, and longtime AAMI members will recognize the arguments and personalities on both sides. But watch this space, as any FDA action on remanufacturing will immediately impact AAMI’s members and AAMI will be sure to cover future developments.
For more information, visit aami.org.
LOOKING FOR A CMMS THAT IS DESIGNED FOR HTM BY HTM
EQ2 HEMS: A "Smart CMMS" that Makes Everything from Managing Work Orders to Maintaining Compliance, Reporting, and Capital Planning Easier
Numerous integrations, to streamline workflows
Superior regulatory compliance reporting included
Mobile app designed for offline and online work means you can always access what you need when you need it
Data and information in the format that fits the needs of all levels of management and the hospital as a whole
All webinars, podcast, and product demos are eligible for 1 CE credit from the ACI.
ON-DEMAND:
CITREX H5 Gas Flow Analyzer and MultiGasAnalyser OR-703
Combating Ransomware in Healthcare with Network Detection and Response (NDR)
LIVE:
AUGUST 7 | Claroty
Tools of the Trade live demo
AUGUST 14 | Cognosos
Save the date for this live webinar.
AUGUST 28 | GE HealthCare
Save the date for this live webinar.
Demo of Kontakt.io”s Asset Tracking Platform
TUNE IN TO ANY LIVE WEBINAR TO WIN AIRPODS!
PODCASTS: sponsored by MMS
Insights on HTM Community Building
Hospital Sisters Mission Outreach is a medical surplus recovery organization (MSRO) focusing on improving health care access to people in low- and middleincome countries (LMIC) through responsible donation of medical supplies, equipment and support services. Mission Outreach exists to strengthen and build health systems in LMIC, to support surgical mission teams and to prevent and recover during a crisis.
Hospital Sisters Mission Outreach Biomedical Engineer Ratish Kumar, M.S, recently shared more information about the organization.
Q: HOW DOES YOUR COMPANY STAND OUT?
A: Mission Outreach adheres to best practices in medical donations and follows the WHO standards to solicit and provision of medical supplies and equipment donations to LMIC. We are among the very few in the MSRO industry to have a full-time biomedical engineer on staff. My responsibility is to develop and conceptualize the biomedical equipment program with a goal to advance and sustain the biomedical infrastructure in LMIC health systems with quality medical equipment donations and support services.
A: We are reimagining how we provide support services to our international partners and identify measurable health care outcomes through the donations we provide. In 2023, we established a long-term partnership with St. Joseph hospital in
Moshi, Tanzania, part of the Sisters of Our Lady of Kilimanjaro, and committed to equip their current hospital and the new mother/baby hospital which is under construction. Mission Outreach sent the first shipment in February 2024 with equipment and supplies, then later in June, I along with our executive director followed the shipment for on-boarding and installation assistance of equipment and to evaluate the impact of donations. It was a successful visit as we were able to replace some of their old equipment and bring in new equipment that was not available before. We also realized it is just the beginning and a lot more needs to be done in the future. One of the primary goals for me in this project is to establish solid biomedical operations in the hospital by working with their biomedical technician and equipping them with biomedical test equipment, tools, workstation and standard operating procedure. The overall goal for us as an organization is to play a key supporting role to St. Joseph hospital’s vision to reduce the infant mortality rate of the Kilimanjaro region with necessary equipment, supplies and support services.
A: The theme of our organization is “Global health is local health” – we as an organization are always grateful to our volunteers, product donors, financial donors, our founders for paving us the way to do this global health work. As a biomedical engineer myself, I would like to take this opportunity to tell my clinical engineering community that there is lot that can be done to support our neighbors through responsible medical equipment donations, volunteer your valuable time to support the local nonprofit organization who does global health work, or connect with me to be part of many other projects we do.
For more information, visit mission-outreach.org.
ECRI’s annual Health Technology Excellence Award competition provides insight into exceptional technology management initiatives undertaken at health care organizations around the world. ECRI bestowed the 2024 Award on Clínica Imbanaco (Cali, Colombia) for its multiyear effort to improve how health technology is managed at its facilities, with the goal of becoming a pioneer of health technology management best practices in its region.
“For our organization, it is essential to learn every day from the best global practices in patient safety.” Those words from Karent Muñoz Salazar, head of clinical engineering for Clínica Imbanaco S.A. (Cali, Colombia) – combined with her organization’s demonstrated commitment to facilitating better strategic management of health technology to improve patient safety, enhance processes and reduce costs – illustrate why ECRI selected Clínica Imbanaco as the 2024 winner of its Health Technology Excellence Award.
Clínica Imbanaco has implemented multiple initiatives over the past several years to expand the capabilities and upgrade the quality of its health technology management function.
“What struck us about the work being done at Clínica Imbanaco is that the projects weren’t just one-time efforts. They reflected a culture of wanting to continuously improve how health technology is managed,” explained Scott Lucas, ECRI’s vice president of device safety. “Their work shows a real desire to elevate the health technology management function within their region to meet or exceed international standards.”
The following are a few examples of their work.
Corrective maintenance is a reactive measure. A problem
occurs, then staff need to identify the cause and restore the equipment to normal operation. This approach can be costly in terms of time and money, and it can put patients at risk, subjecting them to harm if the problem is not discovered before the device is used in their care.
The proactive management of medical technologies, by comparison, is intended to help prevent future device failures. Clínica Imbanaco implemented several measures to reduce its reliance on corrective maintenance (repairing devices after they’ve failed) in favor of a more proactive approach.
This initiative included the following measures:
• Identifying and classifying medical equipment risks, the probability of failure, and the potential impact of failure, and then using that information to define maintenance and training strategies for the equipment. For the risk assessment process, the organization developed a “heat map” to classify the probability and impact of device failures for various clinical processes, ranging from acceptable risks (low probability, low impact) to unacceptable risks (high probability, high impact).
• Training users on the safe use of medical technologies and, importantly, evaluating the effectiveness of that training (using the Kirkpatrick methodology).
• Adhering to a robust preventive maintenance program. Regular device inspections and maintenance (e.g., lubricating and adjusting components, replacing worn parts) can prevent failures and breakdowns.
Collectively, these efforts helped reduce corrective maintenance expenditures, increase preventive maintenance compliance rates, and improve patient safety.
An inaccurate measurement from a medical device can lead to inappropriate care decisions. So access to a timely and reliable source for medical equipment calibration is a key technology management consideration for any care provider.
In many regions, health care organizations can contract with an outside organization to perform this
function. That can be a challenge in Colombia. According to Muñoz, only four health entities in Colombia have accredited metrology laboratories. Further, calibration services are expensive, are not readily available in all locations, and can be of inconsistent quality (or not conducted in accordance with the country’s regulations).
Clínica Imbanaco reports that it repeatedly experienced delays in the process, resulting in medical devices not being available.
To address this challenge, Clínica Imbanaco established, and achieved accreditation for, an in-house metrology laboratory. This effort required a significant investment, as it involved infrastructure adjustments, equipment maintenance, proficiency testing, internal audits, consulting and training for the team of professionals formed. Achieving accreditation from ONAC (Organismo Nacional de Acreditación de Colombia) under the guidelines of ISO/IEC 17025:2017 was key to providing assurance that medical devices would be calibrated according to the organization’s standards and available when needed.
Consideration of an intracranial and extracranial surgery system for treating cancer patients illustrates the organization’s embrace of an evidence-based technology assessment process. A multidisciplinary technology assessment team was formed to establish selection criteria, evaluate the prospective models against those criteria and make an evidence-based selection decision.
Clínica Imbanaco’s assessment followed the GRADE methodology to evaluate the certainty of the evidence; this approach helped the organization make clinical practice recommendations and decisions about new or emerging technologies systematically. Questions were
framed in the PICO format, defining the population, intervention, comparator and outcomes to be studied. (The comparator, in this case, involved comparing the technologies under consideration with the alternatives currently available for managing the health condition.) The team’s analysis considered factors such as the system’s ability to fulfill a clinical need, the features and capabilities of the systems under consideration, preinstallation conditions and testing, and economic and operational factors (e.g., cost, warranty information, expected life, service schedules). This process helps the organization identify new or emerging technologies that will meet clinical practice recommendations in a cost-effective manner.
Following are a few of the additional projects that Clínica Imbanaco has implemented in recent years to improve how health technology is managed:
• Establishing a clinical alarm management program. Efforts included assessing clinical workflows, adopting a patient assessment process to facilitate early detection of patient decompensation, and upgrading medical technologies and alarm communication systems.
• Implementing smart infusion pumps with dose error reduction system technology to reduce medication errors.
To apply for the 2025 Health Technology Excellence Award, which is open to members of any ECRI program, visit https://ly.ecri.org/HTE_Award. Applications consist of a short essay describing an initiative that improves patient safety, reduces costs, or otherwise facilitates better strategic management of health technology. ECRI will accept applications through the end of January 2025.
Q: WHAT PRODUCT, SERVICE, OR SOLUTIONS DOES YOUR COMPANY PROVIDE TO THE INDUSTRY?
Bio-Medical Equipment Service Company (BMES) is a healthcare technology leader specializing in patient monitoring and telemetry repair for over thirty years. We recognize the challenges faced by biomedical professionals and aim to streamline the repair process, ensuring you can return to full service swiftly and efficiently.
Q: TELL US WHAT DIFFERENTIATES YOUR COMPANY FROM THE COMPETITION?
What sets BMES apart from the competition is our commitment to excellence. We continuously refine our processes, understanding that stagnation can be the downfall of any
Ed Evans, CEO
company. By staying at the forefront of new technology and services in the biomedical repair industry, BMES ensures unmatched turnaround times and warranties. Contact us today to experience the BMES difference.
Q: WHY DID YOU CHOOSE TECHNATION FOR ADVERTISING?
BMES selected TechNation for advertising due to their significant influence in the biomedical community. Whether in an office or a repair depot, it’s rare not to find an issue of TechNation available. Their unparalleled industry reach made them the obvious choice for our advertising needs.
For more information, visit bmesco.com.
BY BRIAN BELL
iomedical equipment technicians (BMETs) are faced with a growing number of medical devices, but the same basic electrical troubleshooting methods still prevail. Most electronic issues can be traced back to a handful of common problems.
Issues with the power supply or power delivery can cause various symptoms in an electronic device. Understanding how to troubleshoot power issues is essential for BMETs. It is good practice to start at the wall (line voltage) and work your way to the device power supply. Check outlets first, then cables and finally board supply inside a device. You will need to measure voltage as you go to determine the start of the problem. However, more often than not you will visually see the issue (i.e. a loose connection or damaged cord)
Electronic components can fail due to age, misuse, or manufacturing defects. Identifying and replacing a failed part is often the solution to electronic problems. Using your senses can help you locate the issue. For instance, you can smell burnt resistors, see a burnt fuse, feel the heat from a component or hear an out-of-place noise.
Signal integrity problems can lead to issues like noise, distortion or signal loss. These problems can often be traced back to electromagnetic interference from other devices, broken or poor insulation, long cables or cords, poor network connectivity or bad electrode contact.
Fuses are essential to electrical circuits, protecting the system from excessive current and potential damage. Fuses are designed to protect devices, not people of
course, there are some safety benefits to having a fuse; however, a fuse is not designed for that purpose. Fuses are designed to cut off power (or “blow”) when the current exceeds its rated value, interrupting the circuit and preventing any harm to the connected devices or wiring. During the process a fuse is destroyed. A fuse sacrifices itself to save the device (quite the hero). In this section, we’ll explore the critical aspects of troubleshooting fuses, including how to identify fuses, methods to confirm their functionality with a multimeter and the process of replacing fuses when necessary.
Before you can troubleshoot a fuse, you need to locate it within your electrical system. Fuses are typically housed in a plastic or ceramic casing, often cylindrical in shape. The casing can be clear or opaque, allowing you to see the fuse element inside. Fuses are labeled with their amperage rating, indicating the maximum current they can handle before blowing. The fuse rating is often printed on the casing or on the metal end caps of the fuse. In Figure 1, you can see a blown fuse.
When you suspect a fuse might be the source of an electrical problem, confirm the fuse status before proceeding with any replacements. A multimeter is a valuable tool for checking
fuses. Here is how to use a multimeter to test a fuse. First, turn your multimeter on and set it to the “Ohm” or “Resistance” mode (or if you prefer continuity mode). Next, ensure the circuit you are testing is de-energized. Then, remove the fuse and touch the multimeter probes to the metal end caps of the fuse. A working fuse should show low resistance, typically near 0 ohms. If the multimeter reads “OL” (Over Limit) or a high resistance value, it indicates a blown fuse. If your meter is in continuity mode, you will hear an audible sound indicating low resistance. Alternatively, if you are uncertain about the fuse’s status and do not have a multimeter nearby, you can switch out the suspected fuse with one you know is working (ensure the fuse is of the same amperage rating). This can help verify whether the fuse is indeed blown.
Finally, once the new fuse is in place, reconnect the power to the circuit or device. After restoring power, test the circuit to confirm that the issue has been resolved. If the problem persists, there may be an underlying issue that needs further investigation. Troubleshooting and replacing fuses is a basic but essential skill for anyone dealing with electrical systems.
In summary, troubleshooting electronic issues often revolves around understanding common problems such as component failure, power issues, signal integrity
problems and faulty fuses. By using your senses and basic diagnostic tools, you can identify and address these issues effectively. Key takeaways include the importance of systematically checking components, verifying power, maintaining signal integrity, and correctly identifying and replacing blown fuses. Mastering these fundamental troubleshooting techniques will enhance your ability to diagnose and resolve electronic problems, ensuring the longevity and reliability of your devices.
Brian Bell, Ph.D., is a member of the TechNation Digital Advisory Board, founder of HTM Workshop and teaches courses in engineering technology with a focus on biomedical engineering technology.
Basic Electrical Troubleshooting is based of a section from the book “Essentials of Biomedical Engineering Technology and Healthcare Technology Management” and is used with permission from the author.
Claroty xDome is the industry’s leading health care cyber-physical systems protection platform – enabling health care organizations to safely deliver connected care while enhancing efficiencies across the clinical environment. Claroty xDome spans the entire health care cybersecurity journey regardless of the scale or maturity of your environment through asset inventory, exposure management, network protection, threat detection and operational efficiency.
As a modular solution, Claroty xDome is suited for organizations at any stage in their health care cybersecurity journey, regardless of their scale, staffing or program maturity. The solution consists of platform essentials, offering foundational capabilities across all core areas mentioned above, as well as advanced modules that provide increased value and enhanced programmatic capabilities.
For more information, visit claroty.com.
All webinars, podcast, and product demos are eligible for 1 CE credit from the ACI.
Webinar Wednesday’s recent presentation “Navigating the Asset Lifecycle: From Standardization, Maintaining Compliance to Capital Planning” sponsored by FSI is eligible for 1 CE credit from the ACI.
FSI’s Director of Product Experience Joe Stockman, Vice President of Product and Strategy Chris Lang, and Solutions Engineer Kevin Lund teamed up for an excellent webinar.
The presenters discussed how HTM professionals juggle a robust workday with several challenges on their radar: incomplete asset inventory systems, regulatory compliance, cybersecurity risks as well as staffing and retention issues. So, what is at the core of a well-oiled, successful HTM/biomed department? An asset management strategy that considers the entire lifecycle, from standardization to capital planning and everything in-between.
The presenters also fielded questions from attendees including queries about service contracts, software, compatibility with testing devices and more.
The webinar was popular among HTM professionals with 149 registered for the live presentation. A recording of the session is available for on-demand viewing and 1 CE credit from ACI at WebinarWednesday.live.
Attendees were asked “Excluding CE credits, why do you attend Webinar Wednesday?”
“Learning about what and who is shaping the technology and direction of the HTM industry.”
- Brian Synder, BS, CBET, BMET III, Franciscan Health East. “To learn more about the importance of having all of the proper information and documentation for PMs.”
- Valerie Piontek, Dispatcher, UPMC.
“I attend Webinar Wednesday because it gives me a chance to connect with people in the HTM field outside of my immediate geographical region.”
- Adam Ruppert, Biomedical Technician, St. Luke’s Hospital. “The title of this webinar caught my attention and when I attended the webinar, everything was great and it was very helpful.”
- Jesus Velazquez, Field Service Specialist 2, CHI St. Luke’s Hospital. “To try and stay abreast of changes in the HTM field.”
- David Kennedy, Medical Technology Advisor, CommonSpirit Health.
University of Tennessee Medical Center’s Daniel Griffin won a $100 Amazon gift card during the session as Webinar Wednesday continues to celebrate its 10th anniversary. Register and attend a future webinar for a chance to win a prize.
The Webinar Wednesday session “Building for the Future: Trends and Recruiting Strategies for Healthcare Technology Management” sponsored by Agiliti is eligible for 1 credit from the ACI.
The HTM workforce and the candidate market is continuing to change. Agiliti Vice President of Clinical Engineering Bill Mannes and Talent Acquisition Supervisor Erica Cuthbertson shared how to set your team up for long term success. They shared market, workforce and candidate trends with webinar attendees. The duo also discussed strategies for addressing market challenges and how to position oneself for success.
It was a popular webinar with almost 100 individuals registered for the live presentation. An on-demand recording of the session is available for viewing (and 1 credit from the ACI) at WebinarWednesday.live.
Andrew Nedolast, BMET, with Avita Health Systems in Ohio was the lucky winner of a $100 Amazon gift card as Webinar Wednesday continues to celebrate its 10th anniversary. Prizes will also be given away during future webinars.
Attendees were asked, “How much new information did you receive from today’s webinar?”
“I have a better idea how to approach someone and encourage them to take the HTM path.”
- Joel Coffman, CBET, Chambersburg Hospital.
“It was good to hear what’s going on in the industry. Been at my position for 15+ years now so it is nice to know stuff.”
- Glenn Fraser, Certified Biomedical Technician, Stanford Children’s Healthcare.
The recent Webinar Wednesday presentation “An Introduction to Computed Tomography” is eligible for 1 credit from the ACI. The session was sponsored by AllParts Medical.
James Freeman, Multi-Vendor Modality Manager, CT-PET/CT-Nuclear at Phillips Healthcare, discussed computed tomography, including functionality and system components, advantages over traditional radiology and a system overview. He also provided insights regarding service including cost to serve elements to consider. Finally, in the comprehensive webinar, Freeman shared information about CT training and CT support at AllParts Medical.
The webinar was a homerun with almost 200 professionals registered for the session. Laura Kroger, a CBET with Prairie Lakes Healthcare System in South Dakota was a big winner. She took home Apple AirPods as Webinar Wednesday continiues to celebrate its 10th anniversary by giving away amazing prizes!
Attendees were asked, “How much new information did you receive from today’s webinar?”
“I liked the information on the CT Data Acquisition System and how it transmits and processes the information received. It makes me want to learn more.”
- Michael Skelton, Student, Bates Technical College. “Learned about the beginning of CT and its growth to what it has become today.”
- David Esquivel, Biomed, Providence St. Joseph.
GE Innova x100
GE Innova IGS/Discovery
Siemens Axiom Artis
Siemens Artis Zee Cath Lab Mini C-Arm Hologic & Orthoscan Family
OEC 9800/6800/9900
OEC Elite CFD (pre-req - OEC 9800/6800/9900)
GE Logiq 9/Vivid 7 UL
GE Logiq E9/Vivid E9 UL
GE Vivid E80/E90/E95 & Logiq E10
VIRTUAL - GE Logiq P3, P5, P6, A5
GE Logiq-Voluson Midrange Training (P7/P9/S8/E8/F6/F8
Voluson S6/S8/P8/S10/P6)
VIRTUAL -GE Laptops with Venue 40/50
GE Vivid Midrange Training (S60/S70/S5/S6/T9/T8)
GE Voluson E6/E8/ E10
Siemens S1000-S3000 SC2000/ Antares UL
Siemens Sequoia UL (Older Version)
Siemens Sequoia II UL (NEW CLASS)
Siemens Mid-Range UL (X700,X300, X150, NX3, G40,)
Sonosite Family (VIRTUAL)
Samsung Family
Toshiba Aplio - Xario (Aplio 300-400/i600-900/Xario 100200/A450-A550)
Siemens
Siemens
Siemens
Participants are:
ealthcare technology training, including apprenticeships, remain a common topic of discussion. It is an especially important topic because of the growing number of open positions being created by the retirement of an aging workforce. TechNation reached out to HTM professionals to find out more about the current state of training in the industry.
• Brian Bell, Ph.D., Faculty Biomedical Engineering Technology, St. Petersburg College, and Founder of HTM Workshop;
• John Drew, Tri-Imaging Solutions, Vice President of Operations;
• Stephen Maull, Owner of Maull Biomedical Training
• Glenn Schneider, MHSA, CRES, Chief Service Officer, Elite Biomedical Solutions; and
• Matt Tomory, Vice President Sales and Marketing, Innovatus Imaging.
Q: WHAT ARE THE BENEFITS OF AN APPRENTICESHIP?
BELL: An apprenticeship offers the benefit of employer-sponsored training, providing hands-on, and up to date industry-specific skill directly related to the employer’s strengths. Apprenticeships strengthen the relationship between employee and employer, fostering mutual trust and better communication.
DREW: I can talk to our program here at Tri-Imaging. We are having great success bringing new engineers into the field with our program. To date, we have had approximately 60 apprentices complete our program. It is a great way for a new HTM candidate to enter our industry with more than just a class under their belt. The program offers them a submersion into working with us day to day diagnosing, repairing, testing and calibrating diagnostic imaging systems in a controlled environment. The result of this is twofold. First, the engineer is far more comfortable when they enter the workspace. Having been exposed to multiple modalities such as X-ray, mammography, mobiles, C-arms, cath lab and CT. Second, the employer is confident that they are hiring someone who has been vetted and has more than just a basic understanding. We also work with our customer to tailor the training need of the apprentice to meet their needs.
SCHNEIDER: Since we are a manufacturer, we have positions that require low-skilled labor to perform. Our apprenticeship program provides opportunities for employees in those positions to develop a career in the HTM field, if they show an interest and the necessary aptitude. We already know their character and work ethic, so investing in them is an easy decision.
TOMORY: Apprenticeships have many benefits beyond the individual apprentice. Of course, the individual receives the accumulated knowledge and years of experience of the mentor, but the mentor also benefits. Over the years, I have taught hundreds of classes and trained countless individuals and the one constant is that even though I was the subject matter expert, I learned something from each class and person. The industry also benefits; there is a dramatic shortage of new personnel in the HTM field and every day, knowledge is lost. Apprenticeship brings new blood into the industry and provides them with an excellent foundation to build upon and become the next generation of this essential workforce.
Q: HOW CAN A BIOMED BE SURE TO OBTAIN QUALITY TRAINING FROM AN OEM, ISO, SCHOOL, TRAINING CENTER, CONFERENCES AND WEBINARS?
BELL: To ensure quality training, a biomedical engineer should verify the experience and past performance of the trainer when possible. Also, seeking feedback from biomeds who have previously attended the training is another great way to confirm the quality of the training. Additionally, the value and opportunities for networking provided by the training should be a part of the consideration when evaluating its quality – not just technical skills.
DREW: I would say it’s critical for several reasons, but I will just give a couple.
• Personal growth. Engineers today are looking for continued growth with an employer, and educating and expanding skill sets is one piece of that plan.
• Due to the shortage of engineers, employers are requiring employees to cover more and varied systems. Continuing education is essential to make this successful for both the employee and employer. Once there is a base established, it can be the launching pad for other specific areas.
• Degrees are another way to distinguish yourself from another as well.
MAULL: In our industry there are basically two types of training courses; concept courses and actionable courses. A concept course is what we often get at tradeshows; introduction to X-ray, introduction to contrast injectors, or infusion pumps or ventilators, etc. When you take a concept course you are going to learn generalities and lingo about that particular type of equipment. An actionable course is one where you are going to learn how to operate, maintain and/or repair a specific type of equipment. A quality course is one where you actually
learned what the course curriculum said you were going to learn. If you went to school to learn how to do a PM on a ventilator and you can actually do a PM on a ventilator when you get back to your medical facility, then you received quality training.
SCHNEIDER: Like many things, you get out what you put into training. I’ve attended training in the past where students did only what was necessary to complete the course and others asked a lot of questions and really tried to get the most out of it. I think you’ll find most instructors love to teach the subject matter and like questions from students that challenge them and the other students to better understand the device or subject matter. Don’t try to multi-task while listening to a webinar. You’ll get very little out of the presentation if you’re not paying attention. You’ll be surprised by the number of people who have the same questions you do.
TOMORY: There are many channels for biomedical training available today with a wide variety of outcomes. The questions to be asked include: What limitations will I have to comprehensively service and maintain XYZ device after this training? What barriers will remain including diagnostics/passwords or software? I recommend a mix of sources for training as well as continuing education to grow your knowledge base. Conferences such as AAMI and MD Expo are excellent events for a wide variety of complimentary or inexpensive education. The OEM training can be a great source as well although usually expensive. It is best to negotiate for OEM training at the point of purchase when they are the most flexible. ISO training (my previous specialty) can be excellent with pragmatic, real-world applications and situations as long as the instructor has the experience and training materials to fully equip you to service XYZ device.
BELL: New technologies like remote learning and VR are significantly enhancing training in biomedical engineering tech by providing flexible, accessible and immersive learning experiences. Remote learning kits from HTM-Workshop.com or virtual training from NVRT labs is a great way to build confidence for technicians alongside more traditional live training and labs.
DREW: Training is continuing to evolve thanks to technology. Remote classes continue to increase as an alternative to traditional in-person courses. This really seemed to grow during COVID of course. This could not have been effective without the technology to deliver the courses getting better. Although offering courses online has shortened the amount of time an engineer has to be away, it has not eliminated the need for hands-on training. VR is awesome and has its uses but I believe Augmented Reality (AR) is where we will see great strides made. Having the ability to work in the real world and virtual world together is the key.
Faculty Biomedical Engineering Technology
MAULL: The adoption of remote training is a slow-moving tortoise, but it is moving forward. We started our remote training options in 2015 and it was slow to catch on. Being a relatively new concept in our industry, BMETs were unsure of the effectiveness of training you didn’t have to attend in person. But, like all legitimate technological advancements, it slowly picked up steam. Now, many companies are offering a form of remote learning; some are dedicated specifically to it (NVRT for example). Our first year offering remote training we had around 20 students choose that option. Now, it’s close to 10 times that. With VR, AR and AI, the training will only get more and more effective (both in practicality and cost), which is making it easier on budgets and personally to the students who don’t have to leave home to get the training they need. Geography and lack of manpower are being eliminated as obstacles to attending training, and that’s huge.
SCHNEIDER: VR and remote learning make access to training so much easier. The video quality and availability of VR has improved exponentially over the last 5 years. For any remote training, I still believe hands-on for labs is necessary. Partnering with a hospital or medical device repair facility for required hands-on training is essential to the student’s success.
TOMORY: Remote training can be valuable, however I view it as a complement to in-person training. When in-person, people are dedicated to the class and attention, proficiency, and knowledge retention is apparent to the instructor. When remote, people tend to “multitask” (I say this euphemistically) and are not fully focused on the task at hand. With technical training, nothing compares to hands-on, in-person interactive instruction.
BELL: Earning a certification such as CBET, CABT or CRES offers several benefits. It validates expertise and knowledge in biomedical engineering, enhancing
professional credibility and career prospects. Certification often leads to better job opportunities and higher salaries, as employers recognize the value of certified professionals. However, each employer is different and it’s important to understand each employer’s perception of each certification. There are great technicians that are not certified, certification is more of a badge of accomplishment and a statement of career commitment to continual education. Your reputation is your most powerful tool and certification is just one part of your overall brand and reputation as a technician.
DREW: I will answer this leaning to the diagnostic imaging space specifically. Certifications lend to credibility or competency in a specific area or a general knowledge. If someone is entering into this space and has completed our BMET to Imaging courses, an employer can be confident they have a base of knowledge that can be built upon. Certain certifications for specific specialties may be required, but we have not seen much of that just to enter the field.
SCHNEIDER: As an employer, I see the certification as a minimum knowledge base for that technician. It tells me that the certified technician had to invest their own time, most likely their own money, and effort above and beyond the normal job duties to pass the exam. If comparing people during the hiring process and everything else is equal, I’ll always choose the certified technician. Also, the certification is nationally recognized, so it provides the technician with the possibility to earn more and work anywhere.
TOMORY: Certifications are important for a variety of reasons. Having the discipline to complete a program such as CBET demonstrates commitment as well as proven proficiency in the program materials. Each program has a curriculum students must complete and pass exams to earn that certification. The certification in turn opens doors to
new or additional professional responsibilities opportunities and associated financial benefits. Certifications may also be a requirement for certain positions or career paths.
Q: WHAT ELSE DO YOU THINK TECHNATION READERS NEED TO KNOW ABOUT TRAINING OPPORTUNITIES?
BELL: TechNation readers should know that training opportunities are continually evolving, offering more flexible and diverse options than ever before. It’s essential to stay informed about industry trends and updates, as new certifications and specialized courses are regularly introduced. Networking through training programs can be invaluable, offering connections with industry experts and peers that can enhance career growth and development.
DREW: We have been talking to people for years about the need for new engineers in our industry. The early warning signals are long gone, and we are deep into a severe shortage of diagnostic imaging engineers. I would encourage anyone who is interested in a career field that has great pay, a good work environment, and longevity to visit our website, www.triimaging.com, and inquire about our programs to get started.
MAULL: There is a well-known adage about growing old: “When you stop moving, you die.” This basically means as you age and retire, don’t become complacent and lazy about your physical activity. Whether it’s running, bike riding or walking or whatever, keep active … keep moving every day and enjoy a long, healthy life. In our industry, the same can be said about training. This career field is, by its nature, always on the cutting edge of technology. The medical industry moves technology forward as fast as nearly any other industry in the world, so when someone decides to become a BMET, you are committing to a life of never ending learning. The equipment is always evolving, so the BMET needs to constantly keep up with these technological advances.
SCHNEIDER: Being asked to attend training is a privilege. It’s an investment by the employer that should not be taken lightly by the student. There are intangibles like quicker turn-around times. The value training brings to an HTM department favors the employer, student and, ultimately, the patients. Effective training provides a department with the ability to keep equipment in the hands of the caregivers for longer periods of time.
TOMORY: Training is essential for ALL of us regardless of the field you are in. Stasis in any business means no growth while others are growing around you – leaving you behind. I am fond of saying that staying still means going backwards. Whether your current position is technical, managerial, executive it does not matter – continuing education ensures professional growth or, at the very least, ensures you are not passed by your peers.
BY K. RICHARD DOUGLAS
iomeds will always benefit by leveraging the training, networking and other resources available through national biomed organizations, local and state biomed organizations, professional organization expos and conferences and technical training through OEMs and ISOs.
Along with the approximately 24 state and local biomed associations and societies in the U.S., there are organizations like AAMI, ACCE, MD Publishing and the VA that all provide training, educational sessions and webinars. The military has its own training to advance a biomed’s vocation as well.
This supplemental training can help boost a biomed’s career by a value-add formula and the potential for specialization. Also, with the advent of hybrid-type positions in the field, additional training allows a biomed to move into a more specialist area, including IT, cybersecurity or networks. This can allow biomeds to gain certifications in these areas.
The training available includes degrees, certifications, continuing education credits and other credentials. For rookie biomeds, this can also include the BMET training that leads to the CABT certification, issued through AAMI.
Additional training, along with experience, can allow a BMET I to work their way to a BMET II and continue on a career progression. Certification also aids in career advancement.
biomeds. This sub-set of course offerings will continue to gain more momentum.
The New England MD Expo in October will offer many educational opportunities. Check out the education at MDExpoShow.com.
MD Expos have included a broad cross section of training topics from the testing of gas modules and anesthesia monitors to service contract management strategies and certification preparation. The course content has taught biomeds soft skills, technical skills and prepared them for management positions.
The benefits for career growth from participating in these educational sessions, and in continued training in general, became the topic for one course offering.
The presentation “Role of Professional Organizations in Promoting Your Biomedical/Clinical Engineering Career” addressed the importance of professional organizations in the life of a biomed and the role they play in career growth. It was presented by Arif Subhan, MS, CCE, FACCE, AAMIF, chief biomedical engineer with the VA Greater Los Angeles Healthcare System.
Attendance and training at these events can be very beneficial to a biomed’s foundation of knowledge as well as for career development.
Some of the most valuable training for a biomed is technical training, often hands-on, which has an immediate real-world application. While much of this training has been provided by the OEMs and ISOs, as mentioned previously, there are opportunities for technical training at expos, conferences and state biomed symposiums.
Attendance and training at these events can be very beneficial to a biomed’s foundation of knowledge as well as for career development. More technical training at these events would supplement OEM and ISO training and provide those in the HTM profession with more opportunities for growth.
Some of the offshoots of biomed require additional training.
While most any form of training provides benefits, it is the technical training with the most direct application for
His session also pointed to the many benefits of participation in professional organizations like AAMI, ACCE, BMES, CMBES IFMBE, AIMBE and IEEE-EMBS, as well as state organizations. Subhan says that participation in professional organizations aids in the promotion of the HTM profession.
He also pointed out that participation in these organizations can help promote a biomed’s career. Subhan’s message was that professional organizations provide valuable resources for career development by providing access to networking, professional development, advocacy and resources.
One of the primary providers of training opportunities in the HTM realm is AAMI.
The 2024 AAMI eXchange offered over 80 training sessions and workshops. The eXchange included three sessions devoted to technical training with the promise of more in the future.
“Yes, given the positive reception that AAMI technical trainings had at last year’s eXchange and the number of registrants for technical training at the upcoming 2024 eXchange, we intend to offer training courses next year and expand our offerings into new areas,” says Danielle
The opportunities for a biomed to grow their career are plentiful and the offerings for technical training, soft skills, specialist knowledge and management training come from many sources. These organizations, conferences and special events can play a big role in advancing a biomed’s career.
McGeary, CHTM, PMP, vice president of HTM at AAMI. (Note: She was interviewed prior to the 2024 eXchange.)
She says that at the recent eXchange in Phoenix, there were technical training sessions highlighting infusion pumps, ultrasound and MRI.
“We thank Fluke Biomedical, RSTI and Innovatus Imaging Corporation for working with us to offer these trainings at a very low cost,” McGeary says.
It has been ISOs who have been the traditional providers of technical training, along with OEMs, for thousands of biomeds. The benefits of technical training can include career advancement and specialization.
AAMI has certainly seen this with attendees of its courses.
“Feedback from the HTM professionals who have taken our technical training courses has been overwhelmingly positive. The hands-on experience and access to industry subject matter experts were both cited as positive aspects of the training. HTM students also love our technical training offering as it gives them the opportunity to gain additional skills and work with industry experts,” McGeary says.
She says that since AAMI’s technical training is offered at a very low cost, it gives BMETs access to training they may not have otherwise had.
“Service schools can be cost prohibitive to healthcare delivery organizations; especially given the economic climate the health care sector is facing. Our goal was to ensure technical training was as accessible as possible.
Additionally, by making the technical trainings separate events, folks can just come to a specific class and not have to commit to being at the entire eXchange,” McGeary says.
She says that additionally, AAMI’s technical trainings offered at the eXchange come with a pass to the expo hall so attendees can stay and explore the latest and greatest technologies being showcased by AAMI’s exhibitors.
With more emphasis being put on the practical benefits of technical training, AAMI will continue to offer it among its course offerings.
“The goal of AAMI technical training is to ensure that HTM workers have access to cost-effective, hands-on courses that provide the latest information and strengthen their ability to perform in their roles. It is also an opportunity for HTM professionals to earn CEUs to maintain their certifications,” McGeary says.
She says that with the ageing HTM workforce, AAMI is committed to making sure new and mid-career HTM professionals are well trained to ensure the field’s workforce of the future is strong.
“Given this goal, expect new offerings in the future based on hot topics in HTM and feedback from course attendees. AAMI is always open to suggestions. Please email HTM@ aami.org with feedback or questions,” she suggests.
STATE ASSOCIATIONS AND THIRD-PARTY PROVIDERS
In addition to the many course offerings through AAMI and MD Expo, there are continuous training opportuni -
ties available through state biomed associations or third-party providers.
There are approximately two dozen state biomed associations in the continental U.S. Those state biomed organizations are supplemented by student organizations and organizations affiliated with the American Society for Health Care Engineering (ASHE). These organizations provide training opportunities to their memberships also.
State biomed associations offer members a laundry list of benefits. Besides the camaraderie and the relationships established through these organizations, training is often a centerpiece of each group’s offering. This training is most often offered through ISOs or third-party providers.
Recent symposium course offerings through the North Carolina Biomedical Association included “Learning from Cybersecurity TTE as an HTM/CE-IT Professional to Achieve 3C’s Effectively,” “Using Augmented Reality (AR) to Virtually Disassemble CARESCAPE ONE” and “Alaris Pump Repair.” The group’s 2024 symposium offers a number of classes for the advanced BMET, imaging professional, management, IT and regulatory.
On the opposite coast, the California Medical Instrumentation Association’s 2024 Connect Conference included “Challenges of Providing Remote Support Outside of a Hospital Setting,” “From Tech Expert to Inspirational Leader: Mastering the Art of Confident
New England • October 8-10, 2024
Leadership” and “Using Artificial Intelligence (AI) in Health Care for Health Technology Managers and Biomeds,” as just some of the day one conference course offerings.
This sampling of courses points to the enormous cross-section of topic areas provided through biomed association symposium sessions and seminars. Continuing education credits are often the icing on the cake.
There are many other organizations solely focused on training. These organizations include private schools, technical training schools and formal college courses.
Third-party training sources have always played an important role in specialized training. There are companies like Avante Solutions, College of Biomedical Equipment Technology (CBET), Elite Biomedical, Fluke Biomedical, FSI Inc., Maull Biomedical Training, NVRT, Richardson Healthcare, Rigel Medical, RSTI, Tri-Imaging Solutions, USOC Medical, and others; known for their training courses.
The opportunities for a biomed to grow their career are plentiful and the offerings for technical training, soft skills, specialist knowledge and management training come from many sources. The incentive to become a part of many industry professional organizations is due, in large part, to the ongoing training opportunities available. These organizations, conferences and special events can play a big role in advancing a biomed’s career.
TechNation magazine has announced its 2024 class of 40 under 40, powered by Young Professionals at MD Expo (YP at MD). The 40 professionals in this feature were nominated based on their professional achievements, earned merits and the positive influence they bring to the HTM industry.
YP at MD influenced the idea of starting the TechNation 40 under 40. Established in 2019, the purpose of the YP at MD networking group is to provide a space where younger professionals can network with their peers to share ideas, build relationships, and feel empowered to grow in their professional roles.
“Our first 40 under 40 class was announced in 2022 and was a huge success. TechNation is excited to keep our 40 under 40 an annual spotlight feature in the August issue. The 2024 40 under 40 class is made up of hardworking and dedicated HTM professionals who have done amazing work in our industry. We look forward to celebrating their achievements!” YP at MD Founder Megan Cabot said.
For more information on YP at MD, visit our site!
Thank you to TechNation’s 40 Under 40 sponsors for recognizing the up-andcoming talent in the HTM industry. Your support of our young professionals will ensure the future of HTM is bright!
HOW HAS THE HTM INDUSTRY IMPACTED
YOU? Josh started out his earlier life in IT. He is a former Best Buy Geek Squad member. He has a college IT degree. His parents work in health care and he saw an opportunity for himself. Since making his career decision to work in HTM, he has been on an upward trajectory. I see a bright future ahead for him.
FUN FACT: Josh is a huge Kansas City Chiefs fan. All of us co-workers like to give him a hard time about that. He enjoys snow boarding, hiking, mountain biking and is a member of an Ultimate Frisbee team when off the clock. He is one of the nicest people you will ever meet and will instantly be your friend. He has started his own HTM business outside of work. It is called Elevate Biomed.
HOW HAS THE HTM INDUSTRY IMPACTED
YOU? Katie has always been passionate about supporting health care teams in the delivery of safe, high-quality patient care. Throughout her 12plus years at Providence, Katie has partnered closely with clinical engineers and HTM professionals at all levels of the organization to ensure medical device safety, security and functionality.
FUN FACT: When she’s not working, Katie can be found curled up with a good book, walking her dog, dancing at an outdoor concert, or exploring the mountains, lakes, rivers, hot springs, and small-town rodeos throughout western Montana. Katie is an avid traveler who hopes to one day visit all 50 U.S. states and all 7 continents.
HOW HAS THE HTM INDUSTRY IMPACTED YOU? It has provided me with a platform to leverage my skills and expertise in technology for the betterment of health care systems and also advocacy for building the right ecosystem on technology.
FUN FACT: Despite my busy schedule in the tech industry, I still carve out time to capture moments through photography and videography and often share them with my followers on social media.
HOW HAS THE HTM INDUSTRY IMPACTED YOU? The HTM industry adds to the fulfillment of my passion in health care. When I began my career, I always envisioned myself in a role that would be instrumental in assisting our clinicians in providing excellent patient care to our communities. HTM has provided me the platform to drive strategy that directly impacts and facilitates patient care in our hospitals and, ultimately, our communities.
FUN FACT: I enjoy spending time outdoors with my family and our two dogs. My wife is also in health care, working with blind and visually impaired veterans in our community.
HOW HAS THE HTM INDUSTRY IMPACTED YOU?
The HTM industry has positively influenced me by offering a platform to combine my passion for health care and technology. Through my work in HTM, I have been able to contribute to the improvement of patient care by leveraging technological advancements and ensuring the safe and efficient operation of medical devices and equipment. The industry has also provided opportunities for me to innovate, collaborate with experts, and make a meaningful impact in the health care sector, ultimately shaping my career path and driving my passion for HTM.
FUN FACT: My passion for deep-sea fishing is unmistakable. The thrill of battling powerful fish beneath the waves is exhilarating. Deep-sea fishing is more than a hobby; it is an embodiment of adventure, perseverance and excitement. I love it.
HOW HAS THE HTM INDUSTRY IMPACTED YOU? HTM experience and knowledge are a premium in the medical field. Jessica’s “let’s get it right the first time” attitude has made it easy for her to merge cross-functional teams under one successful vision.
FUN FACT: Jessica is an animal lover. She has rescued and adopted several pets and previously worked in veterinary medicine.
HOW HAS THE HTM INDUSTRY IMPACTED YOU? I have been a patient that had to rely on OR equipment with my own initials on it. There is not much more personal than being worked on with the very equipment that you work on.
FUN FACT: I have tattoos from head to toe, literally.
HOW HAS THE HTM INDUSTRY IMPACTED YOU?
The HTM industry brought me purpose. Knowing that, at the end of each workday, my work positively impacts patient safety and improves quality is a game changer for me and the reason I truly love my job!
FUN FACT: I have a need for speed! Once, I drove a Formula 3000 car for half an hour at the Yas Marina Circuit (where the Formula 1 Abu Dhabi Grand Prix happens). I reached the car’s top speed (170 mph) several times, and it was one of the best days of my life.
HOW HAS THE HTM INDUSTRY IMPACTED YOU? Elizabeth began her professional career in HTM and has steadily and continuously grown both professionally and personally. From the outside looking in, she isn’t missing any opportunities to take the road less traveled and isn’t afraid to lean on experts when needed! A focus on patient care has been the impact from the industry that drives her limitless potential!
FUN FACT: Elizabeth is a devoted and immense lover of animals. She will care for, foster, and take in any animal in need. She is also a huge coffee aficionado and even continued to work at Starbucks part time for many years just so she could continue to hone her barista skills and stay in touch with all things coffee related.
HOW HAS THE HTM INDUSTRY IMPACTED YOU? It is no industry secret that the HTM field is aging and we are coming to a period in time where we will need to be experiencing significant growth to back fill retirees. I think there is something to be said for those truly inspiring young BMETs who are eager and willing to fill those ranks and make their predecessors proud. Jo-Jo is this and more, and the HTM field is truly lucky and blessed to have her in this career field while she is also cheerleading and championing for the HTM field daily. She is someone the younger female BMETs can look up to and aspire to be.
HOW HAS THE HTM INDUSTRY IMPACTED YOU?
Martin Cornea started his career as a BMET I and has excelled to a system director role in less than 10 years. He has a strong passion for coaching, teaching and developing the new generation of BMETs entering our industry.
FUN FACT: When Martin is not working, he enjoys relaxing with his wife and two beautiful children on the sunny beaches in southwest Florida.
FUN FACT: Jo-Jo and her wife enjoy fine art/ museums and you can oftentimes find them at a local museum/gallery enjoying the beauty and history that one can find there.
HOW HAS THE HTM INDUSTRY IMPACTED
YOU? The HTM industry has profoundly impacted me by fueling my sense of purpose and commitment. As a passionate advocate for health care technology, I’ve witnessed firsthand how our work directly influences patient care. Whether it’s ensuring the seamless functioning of critical medical devices or guiding the next generation of BME professionals, I find fulfillment in contributing to health care excellence.
FUN FACT: My wife and I are avid Nerf enthusiasts with multiple standard and custom Nerf shooters through the house. This includes a handmade remote-controlled shooter!
HOW HAS THE HTM INDUSTRY IMPACTED
YOU? A tireless contributor, this nominee has served on every focus group for Acumatica implementation for the biomed sales team, both in module development and successive training for her peers. With an abrupt departure in west region management, she proactively approached senior leadership for team support and was able to mentor a young and hungry sales team to a solid close for the year. A subject matter expert in the patient monitoring modalities, every contract opportunity and strategic patient monitoring engagement is vetted by this professional, utilizing her vast market and competitive knowledge to provide direction for the organization. Her ultrasound market growth and strategic contracting allowed for the ultrasound field service expansion into the Pacific Northwest market, paving the way for additional business in the zone and region. Similarly, her DI market growth and contract closures has prompted numerous resource allocations to the Western market in support of covered assets.
FUN FACT: Aline is a first generation American and speaks 3 languages – a proud dog Mom to Lexie, Aline is recently engaged and is busy planning her wedding in 2025!
HOW HAS THE HTM INDUSTRY IMPACTED
YOU? The HTM industry has profoundly shaped Mitch’s career, providing him with over 15 years of invaluable experience in both sales and operations. His deep immersion in this sector has equipped him with a wealth of industry-specific knowledge and expertise, enabling him to navigate its complexities with finesse. Through his dedicated involvement in HTM, Mitch has honed his skills, forged meaningful connections, and consistently delivered impactful contributions, solidifying his reputation as a standout professional in the field.
FUN FACT: When he’s not navigating the waters of the HTM industry, you can find him exploring the waves of Lake Erie during the summer months or jetting off to various destinations in pursuit of his bucket list fish. But Mitch is also a culinary wizard. So, whether he’s mastering operations, mastering the perfect cast, or mastering a new Walleye dish, Mitch always brings his A-game.
HOW HAS THE HTM INDUSTRY IMPACTED
YOU? Being in HTM for (a very fast) 6 years has taught me lessons in business and in life that could fill a book. Surrounded by overly talented leaders and mentors, I have been given an opportunity of a lifetime learning from individuals like these; developing skill sets in operational execution, crisis management, sales and marketing, branding, customer relations, new market development, entrepreneurship, strategy, positioning and so much more. Beyond my internal team of champions, I have been able to develop relationships and friendships throughout this industry that I will treasure forever. As my good friend Thomas Seiler recently said to a group of us at a CMIA event in California, “You know what? When you look around a trade show and see colleagues, and even competitors, giving out more hugs than handshakes, you know we’ve got a pretty special thing going.” I completely agree with him and could not sum up working in this field any better than that.
FUN FACT: Two truths and a lie...
1) I was a state champion swimmer in high school (having peaked then)
2) I was once featured in an episode of Nashville, sharing stage time with Christina Aguilera.
3) I can bench press over 500 pounds
HOW HAS THE HTM INDUSTRY IMPACTED YOU? Shortly before I joined HTM, my family’s life was turned upside down when my oldest son, Jaxon, was diagnosed with Ewing’s sarcoma. As a Mayo Clinic employee at the time, my lens of the hospital operations were strictly through the lens of both a clinical and research laboratory as well as a patient. Living essentially in and out of a hospital for 7 months while my son was being treated exposed me to so many different challenges from the provider/practice side of the hospital. Pumps that don’t stop beeping, equipment that isn’t working, equipment that isn’t available, and the frustration that this causes with the clinical staff (and the patient!) that are trying to treat every patient as their number one priority, while also trying to navigate equipment issues and every other challenge that they are facing. While my son is in remission and doing fine today, other than being a typical 16-year-old :), the experience we lived through drives me to continually improve what we can do to better support our patients and our clinical staff.
FUN FACT: I have 5 kids and 4 dogs! When I am not working, I enjoy running, helping to coach youth baseball and ice fishing (when we actually have good ice).
HOW HAS THE HTM INDUSTRY IMPACTED YOU?
The HTM industry has taught me how to be a self-starter, accept challenges and to be adaptable. I have learned to work efficiently but with the most integrity. I have met many people along the way and made friends, some that I will have for life. I have learned from senior techs who were so kind to share their knowledge with me, and I now pass it along to those that I mentor. Yet, I still have so much to learn as I continue in my career.
FUN FACT: I love birds. I am a licensed falconry apprentice.
HOW HAS THE HTM INDUSTRY IMPACTED YOU? Early on in Mallory’s career at Aramark, she had the opportunity to visit several hospital sites to see what BMETs do on a daily basis. These visits had a profound impact on the direction of her career. Blending her academic experience and HR knowledge with technical training has driven her to success.
FUN FACT: Mallory has worked from a young age. She has been a barista, horse trainer/stable worker, bartender, ballroom dance teacher, and even counted coupons for Applebee’s corporate office, among other odd jobs!
HOW HAS THE HTM INDUSTRY IMPACTED YOU? Though I stumbled into the HTM field (as many often do in our field), it has provided me a fulfilling career, where I know I make a difference for other biomedical engineering staff, hospital technical staff and clinicians and, most importantly, patients. I love being able to find solutions for our hospital network, particularly when our team comes together with other technical teams to do it.
FUN FACT: I love spending time with my family, especially hiking and traveling. We have a family goal to visit all U.S. National Parks. I also enjoy Palestinian tatreez (cross-stitching) and reading (anything and everything).
HOW HAS THE HTM INDUSTRY IMPACTED YOU? Rebecca was grateful to be a past recipient of an AAMI scholarship. This scholarship assisted with college costs and demonstrated the HTM industry’s commitment to young HTM professionals. Rebecca is always looking to share the HTM industry with students and professionals looking for a career change. Outside of work, she is an active member in the New England Society of Clinical Engineering’s (NESCE) new outreach committee which partners with New England-based vendors and is focused on sharing the HTM profession with high school and college students.
FUN FACT: For Rebecca, baking is not just a hobby. It’s a therapy session in the kitchen where she can whisk away stress and create sweet masterpieces. In her spare time, Rebecca also enjoys crafting with her cricut! She has a knack for finding creative solutions to everyday problems, thanks to her imaginative and resourceful mindset.
HOW HAS THE HTM INDUSTRY IMPACTED YOU? The HTM industy has given Kaleb an opportunity to grow and thrive in a career. It is a place where a technical mindset and problem solving meet helping people and society. This is something that Kaleb is great at. He has the mind to overcome challenges and oversee tasks that ultimately better the lives of the people around him and in his community.
FUN FACT: Kaleb has a passion for travel. He lived abroad and backpacked Australia for a year and is always trying to go to new and exciting places like Machu Picchu or the historical sites in Israel or exploring state and national parks in the U.S. He was also a competitive water-skier in college for the University of Missouri.
HOW HAS THE HTM INDUSTRY IMPACTED YOU? In the face of incorrect diagnoses and incompatible treatment plans for debilitating wrist pain, Julie researched and designed a wrist splint that allowed her to continue her musical studies, and win some high school science fairs in the process! She’s been hooked on biomechanics and bioengineering since then and has dedicated her career to improving safety for patients and health care workers alike through careful understanding of the interplay between the safe use and implementation of medical technologies in a variety of health care settings.
FUN FACT: Julie has been playing violin for nearly 30 years and is an award-winning baker!
HOW HAS THE HTM INDUSTRY IMPACTED YOU? It’s been thrilling for me to observe the influence of the HTM industry on the U.S. health care system. You would be surprised by the levels of appreciation for this sector in comparison to other regions. The critical role of ensuring the safety of medical equipment is often overlooked. I have also loved witnessing the technological advancements from companies and individuals within the field.
FUN FACT: When I was younger, I spent a couple of weeks cycling from my hometown in England to Northern Spain.
HOW HAS THE HTM INDUSTRY IMPACTED YOU? Growing up I always had interest toward life science and mathematics. HTM is a perfect blend of medicine and engineering that gives me the opportunity to pursue a career in health care. The people who are directly impacted by my work are spread across the world which is immensely rewarding for me day in and day out. People in low- and middle-income countries lack access to quality and safe medical equipment, through my work I help to bridge the resource gap. I also had the opportunity to travel to countries like Tanzania, Togo, Haiti and Peru to share my knowledge and advocate for HTM.
FUN FACT: I enjoy playing badminton, watching cricket and long drives. In my free time, I like to cook and take care of house projects.
HOW HAS THE HTM INDUSTRY IMPACTED YOU?
I ’ve found my purpose, and my home, within the healthcare technology management community. The connections I’ve made, the skills I’ve learned, and the lessons I’ve learned have all helped me become a better, more well-rounded HTM professional. I know that I will never find this same sense of community or passion in another field or industry, and that is what makes getting up and going to work each day so easy.
FUN FACT: I lived in Panama for three months in 2017 working with the Panamanian National Water Utility Company (IDAAN) to help bring clean water infrastructure to informal communities.
HOW HAS THE HTM INDUSTRY IMPACTED YOU? Matt has extensive knowledge in the ultrasound community. He has worked for MW Imaging for 10 years and has helped grow the company immensely. Matt has made many connections within the industry.
FUN FACT: He is from a tiny town in Ohio.
HOW HAS THE HTM INDUSTRY IMPACTED YOU? I found a career that I enjoy working in and I feel like my work makes an impact on those around me. I like that every day is different and challenging in a good way.
FUN FACT: I enjoy spending time with family and friends.
HOW HAS THE HTM INDUSTRY IMPACTED YOU? Yessenia operates within a bustling three-person shop, and she has recently begun attending conferences to cultivate crucial connections with her peers. The role of healthcare technology manager resonates deeply with Yessenia’s skill set and temperament. She exhibits keen attention to detail, ensuring tasks are executed flawlessly, and embraces a servanthood mentality, deriving fulfillment from assisting others. For Yessenia, HTM isn’t just a job; it’s a career that aligns seamlessly with her inherent qualities and passions, making it the ideal professional path for her.
FUN FACT: Yessenia is a devoted mother to her two lovely daughters, showering them with constant affection and attention. Beyond her role as a mother, she nurtures her creative side as an aspiring artist, finding solace and expression through painting and drawing.
HOW HAS THE HTM INDUSTRY IMPACTED
YOU? The HTM industry has allowed me to become part of an amazing group of professionals. Giving me purpose and allowing me to do what I love – serve others.
FUN FACT: I played the Alto saxophone in middle school and high school. Earning second chair in concert band.
HOW HAS THE HTM INDUSTRY IMPACTED
YOU? HTM has brought my passion for health care to an even higher level since I discovered this side of the industry. Working in several different facilities has given me a broad perspective on how vital our role is to patient care. I have a true passion for HTM and hope to one day affect the industry on an even larger scale.
FUN FACT: I was a CNA for 4 years prior to my time in HTM.
HOW HAS THE HTM INDUSTRY IMPACTED YOU? Isis has dedicated her life to the field of healthcare technology management (HTM), following in the footsteps of her father, who is an engineer in Cuba. From a young age, Isis knew that this was her calling. Her impact extends beyond her technical expertise; she exudes professionalism while remaining approachable and fostering collaboration with everyone she meets. Fluent in multiple languages, Isis adeptly navigates the diverse community of Miami, enhancing her ability to connect with people from various backgrounds. While Isis’s foundation lies in biomedical technology, she has also cultivated strong leadership and managerial skills, emerging as a beacon in her field.
FUN FACT: Isis was destined to pursue a career as a biomedical technician. Following in her father’s footsteps, who was also a biomedical technician in Cuba, Isis embarked on her professional journey in the same field. She has practiced as a biomedical technician in three different countries: Cuba, Argentina, and the U.S. Alongside her professional endeavors, Isis is a devoted wife and mother to a newborn son, and she also shares her home with a beloved dog. Her passion lies in engineering, evident from the mechanical drawings of vintage medical equipment adorning her office. Her commitment to her craft and her innovative spirit make her a true engineer, and her achievements make her a deserving candidate for recognition among the “40 under 40” achievers.
HOW HAS THE HTM INDUSTRY IMPACTED YOU?
The fusion of engineering and design thinking has long captivated Priyanka’s interest. Witnessing the unwavering dedication of the HTM industry to prioritize patients’ safety continually motivates her. She is driven to enhance health care safety and assist hospitals in making informed patient safety and technology decisions through her efforts in research, education and consulting.
FUN FACT: Priyanka is a trained classical singer and enjoys traveling in her free time.
HOW HAS THE HTM INDUSTRY IMPACTED YOU? Haskins has found a meaningful career and his purpose at Children’s Healthcare of Atlanta. During the transition period from the military to civilian life, Haskins struggled with feeling connected/ engaged in his newfound civilian life as he did while in the military. Since being at Children’s Healthcare of Atlanta, Haskins has a renewed meaning and purpose. His dedication and quality of care has proven how much HTM has turned his job into a career. Haskins’ hard work is a labor of love.
FUN FACT: Haskins is husband and a father of 3. He has a love for projects and carpentry. Recently, Haskins has designed and constructed a Jon boat where he enjoys spending time on at Sweetwater Creek State Park. Haskins has established himself as a Navy Captain in his own right.
HOW HAS THE HTM INDUSTRY IMPACTED YOU?
Ranjita’s goal as a biomedical engineer is to help improve the quality of health care for our esteemed veterans. HTM is expanding and healthcare technologies are being more integrated and more expensive. With the increasing cost of health care, biomedical engineers can play a pivotal role in planning for a sustainable healthcare technology without compromising on the quality of health care.
FUN FACT: Ranjita enjoys hiking and traveling in her free time.
HOW HAS THE HTM INDUSTRY IMPACTED YOU? Tyler is very passionate about his business and the impact the company has on the medical equipment industry. It has provided him a way to make a great living and to grow/mentor technicians into the HTM industry. In 2017 and 2018, Tyler realized that TBS was larger than himself and the impact that the business has on the people around him. Tyler truly enjoys mentoring the people in our business.
FUN FACT: Tyler loves summertime and being on the water. He enjoys spending his summer days boating on a lake and being outdoors, spending time with close family and friends.
HOW HAS THE HTM INDUSTRY IMPACTED YOU? The HTM industry has been a part of my life since I was 18. With almost 20 years in the field, I feel this industry has taught me humility with understanding new technology but also it has strengthened my knowledge of devices from the past. In my career so far, I have worked with over 200 biomed technicians, biomedical engineers, BESS IT, supervisors and managers from the technician level, biomed engineer level, manager level, chief level and director level. It is such a great field to be in.
FUN FACT: I have been to all 50 states already, either because of military training, biomed training and work and road trips to visit many friends nationwide. I have played fantasy football with a league started from coworkers, military and college friends and have won 7 years in a row. Great at analytics, stats to keep me going.
HOW HAS THE HTM INDUSTRY IMPACTED YOU?
The HTM industry has been a tremendous part of my daily driving force which I have tried to provide the same impact that those who came this way before me helped to carve out such as the likes of Pat Lynch, Paul Mills, Binseng Wang, etc. Coming from an area of economic disparity due to the overall decline of coal energy, the HTM industry has provided my family with the opportunity to seek a lifelong career without the need to climb into a deep coal mine! Coal keeps the lights on, but HTM keeps the hospitals operating.
FUN FACT: I am a board member for my community center which hosts the Longest Running Square Dance in Kentucky.
Service Engineer I at Sysmex America Inc.
HOW HAS THE HTM INDUSTRY IMPACTED YOU? Her customer service is outstanding. Her innovative ideas advance the trust that the customers have in the engineers and the instruments.
FUN FACT: Knows 13 languages
HOW HAS THE HTM INDUSTRY IMPACTED YOU ?
The way that HTM has impacted Phillip is in two ways. First, he has the opportunity to learn a disciplined way of education in the biomedical technology industry. By personally being a Navy vet BMET himself, he knows the importance of detail. The second impact is that HTM industry teaches how to communicate effectively with staff and health care clinicians. The importance of detailed communications is necessary because lives are at stake.
FUN FACT: Phillip is always the life of the party. He enjoys meeting and talking to people … what a great attitude!
HOW HAS THE HTM INDUSTRY IMPACTED YOU? I have been greatly impacted by the HTM industry, from humble beginnings as a co-op to a national cybersecurity specialist. I have learned the significant role the HTM industry plays in the health care infrastructure. It has taught me a lot about integrity from the diligence needed when making physical repairs on medical equipment and understanding you may have a loved one using the device you repaired. It has also given me a greater appreciation for my family as I have moved into a remote position and simultaneously support hospitals across the country and my family.
FUN FACT: I’m a great bowler!
YP at MD is a group of young professionals in the HTM industry. Gather with your fellow up-and-coming colleagues at our MD Expos, HTM mixers and on social media to network, share ideas and discuss our bright future in the HTM industry!
BY KATHLEEN FURORE
often hear “Gen Z doesn’t want to work.” I’m always surprised when I hear people make that comment, because it isn’t something I’ve witnessed in the young people I know. If someone is managing a team that includes members of several generations, how can they bridge any divide that might be occurring because of a misunderstanding or misperception about how this younger generation approaches work?
Professionals I reached out to acknowledge that there’s a “Gen Z doesn’t want to work” movement out there – but they aren’t jumping on that bandwagon.
“I’m always surprised when I hear comments suggesting that Gen Z doesn’t want to work, as this contradicts the dedication and enthusiasm I’ve witnessed in our young team members,” says Daud Grewal, CEO of Tripshepherd.
Laurie Cure, Ph.D., CEO of Innovative Connections, whose expertise is in change management and culture evolution, echoes Grewal.
“I am struck by the negative terms currently used to describe this ambitious group of young employees — words like superficial, unresilient, unmotivated, lazy, entitled and narcissistic,” says Cure, who notes that negative perceptions of younger generations are nothing new. “For decades, generations have been defined, labeled and judged. What strikes me most is how these same words were often used to describe previous generations at this same stage of their careers.”
The truth, Cure adds, is that Gen Z works differently – “and that is neither better nor worse,” she stresses.
Cure offers this take on the topic: “What appears as laziness is actually a healthy view of mental health and work-life balance. What comes across as rigidity is actually an adaptability arising from new technologies that they were raised learning, virtual environments that became commonplace and entrepreneurship that
was critical for their survival. What might be viewed as safe and non-risk-taking comes from a generation, not unlike others, who have borne the repercussions of economic uncertainty, social changes and increased violence. What is seen as overly sensitive is the rightful extension of the civil rights movements and other social causes that occurred for decades and have been valued across the generational continuum.”
With five generations currently in the workforce –“from the silent generation to Gen Z,” Cure explains – it is essential to navigate team dynamics in a way that is respectful of each one.
Here are a few tips business pros recommend:
• Encourage open dialogue.
“Promote an open and respectful communication culture where team members can share their expectations, work preferences, and motivations,” Grewal says. “This helps in understanding each other’s perspectives and fosters mutual respect.”
• Structure intentional ways to build relationships.
That step, which Cure suggests, can be done in several ways.
She advises forming cross-generational project teams, adding time on the agenda to recognize members from several generations, and hosting team development sessions “that consciously bring people together in meaningful ways.”
Grewal’s advice is to implement mentorship programs that pair younger employees with seasoned mentors, which can bridge knowledge gaps and build strong, collaborative relationships.
“This helps both generations appreciate and learn from each other’s experiences,” he explains.
Julia Lozanov, chief editor at Verpex, also suggests developing reverse mentorship programs that match junior staff members with more experienced colleagues.
“Gen Z is able to exchange ideas, viewpoints and digital fluency regarding changing market trends. [These mentorships] also provide students with a stage
on which to showcase their ambition and work ethic,” Lozanov explains.
“This reciprocal knowledge exchange fosters respect for one another in addition to dispelling misconceptions. It demonstrates how eager Gen Z is to participate and pick up knowledge from more seasoned colleagues, fostering a collaborative atmosphere where all generations are treated with respect and understanding.”
mental health reasons as they secure healthy workplace boundaries. The more teams can respect individual needs, the better they can appreciate and meet those needs.”
• Highlight common goals.
“Emphasize shared goals and the collective mission of the team,” says executive coach Smita D. Jain. “When team members focus on common objectives, generational differences become less significant.”
BY TED LUCIDI, CBET
If you work in or support a metropolitan health care facility or one that specializes in cardiology, most likely, a good portion of your ultrasound support costs are consumed by addressing TEE probe failures. OEM replacement costs for the latest high-tech 3D TEE probes from Philips, GE and Siemens can range from $20,000 to $30,000. Believe it or not, some facilities are replacing one TEE probe every month.
Every year, Innovatus repairs about 1,800 TEE probes. We have a massive database that enables us to investigate and cross reference failure analysis data and determine root causes. Believe it or not, over 60% of all TEE probe failures are a result of flooding, or what’s called “gross fluid invasion.” With most of these failures, some type of physical damage or worn and missing seals breaks the physical integrity of the fluid-proof components of the probe. TEE probes are high-level disinfected via immersion or automated reprocessor between every use. The process of high-level disinfecting a TEE probe with a break in physical integrity permits water and chemical disinfectants to enter the probe and cause massive damage to the electronics.
You have several options for supporting TEE probes. Like most support models, the cost of each is offset by the amount of risk you are willing to accept.
1. You may have a full-service contract on your ultrasound consoles that covers ALL of your TEE probe failures, no questions asked. These types of contracts are extremely costly; however, they eliminate
all risk for your facility. Based on our data, they are most likely not the best use of your budget.
2. You also might have a shared-service or event-based contract that covers x-number of TEE probe failures, no questions asked. Once the number of events would be consumed, you would have the option to purchase an OEM exchange/replacement at 50% list-cost. Even using this model, you would still be outputting over $11,000 to $15,000 per failure, on top of what the contract is costing you.
3. A third option is to support your TEE probes via time and materials (T&M), addressing each failure as it occurs. Repairs on TEE probes can begin as low as about $900 and might top out at about $11,000.
Based on our data, this scenario can provide the largest savings to your budget.
4. There is a fourth option that blends options 2 and 3 together. Some facilities choose to maintain their event-based contract but augment it with option 3’s repair model. In this scenario, you would always begin by utilizing the T&M repair model. If the probe would be repairable, you would pursue the low-cost repair option, realizing significant savings. If the probe would happen to be catastrophically damaged beyond repair, you would use an event on your contract to replace that probe. In this scenario, you would realize significant savings to your budget and make the most of your contract.
No matter which model you have chosen, there are other items that need to be considered, such as downtime, patient throughput, uninterrupted workflow and customer satisfaction. Believe it or not, there were several occasions over the last few years when OEM-contracted customers could not obtain replacement TEE
probes due to supply chain challenges and manufacturing shutdowns. There was no, or extremely limited, availability and it affected the ability for some health care providers to perform TEE studies. And there is no guarantee that it will not happen again. All the more reason to consider options 3 and 4 as the most viable solutions.
The path to success begins with minimizing your risk for preventable TEE probe failures. By having the proper controls in-place,100% of all preventable TEE probe failures can be eliminated. That is a powerful claim, but it is true. By understanding how your facility’s TEE probes are stored, transported, staged, used, cleaned, and disinfected, you can very easily reduce, if not eliminate, the need to replace a TEE probe due to preventable damage.
OEM user manuals are filled with lists of Do’s and Don’ts. Based on over 10 years of data, we can confidently say that many items on those lists are not in-practice in today’s health care facilities. Surprisingly, with only some very minor updates to the processes in each clinical area, costly catastrophic TEE probe failures can be eliminated. Also remarkably, the solutions are very low-cost and would add very minimal time to the existing processes.
In about an hour’s time, the clinical experts at Innovatus Imaging can train one or more members of your HTM team to be TEE probe experts. We will provide them with the knowledge and our proprietary tools to capture the current care and handling practices for TEE probes at your facility. Our experts will review your facility’s current
practices and consult with you and your clinical teams to implement industry best-practices that have been proven to eliminate the potential for replacing TEE probes due to preventable damage.
Some of the items include if, when, and how clinical teams visually inspect a TEE probe; and what occurs if any concerns arise. Is leakage testing performed? When in the process; and, what is the process if a failure occurs? Are the proper chemicals in-use, and are they being used according to the instructions. How are TEE probes being stored as well as how are they transported from point A to point B?
Innovatus Imaging is not just a repair provider, we are your service partner. We are here to assist you and your customers with obtaining the maximum lifespan for your ultrasound probes and MRI coils. Our SafeTEE program is designed to help you, your facility, and your customers reduce and even eliminate preventable TEE probe failures. For questions, assistance, or more information, please reach out to safetee@innovatusimaging.com. If you have a failed TEE probe, we can help! We have some of the most-comprehensive repair capabilities on standard and 3D TEE probe models, and we would appreciate the opportunity to assist you.
Ted Lucidi, CBET, is the director of commercial operations and business analytics at Innovatus Imaging.
BY STEVEN J. YELTON, P.E., AAMIF
Ihad the privilege of attending the AAMI eXchange this year, in Phoenix. Every year I return from the eXchange with a renewed excitement about the HTM field. It is like a reunion to get to see so many colleagues year after year. The eXchange provides a great forum for reconnecting with old friends and connecting with new ones. It provides us with a time to run ideas past people who are likely pondering ideas like our own.
As always, we are looking at how we can best educate our students. I always return from the eXchange with great ideas. One topic that I seem to run by my AAMI “family” is how to attract more people into our field and further, innovative ideas to help provide our local employers with enough co-operative education (co-op) students and graduates. We currently, and almost always, have more demand for co-op students than we have supply. This is generally true for graduates also.
We have always been a co-op school where our students are required to complete cooperative education assignments to graduate. As such, we have co-op coordinators for each program. They recruit and place students, search for positions, but teach classes on interviewing skills, resume writing, job responsibilities and communications. In conjunction with our other faculty, industry advisors and employers, our co-op coordinators also provide advising to students to make sure early on that they are in the field that best fits them. Our faculty work closely to provide a well-rounded education for our students. Even with all of this, we are challenged to attract enough students into our field.
I mentioned in my last column that many of our hospital-based employers are supporting home healthcare within their HTM departments and have been doing so for many years. As such, our co-op
students who can work in these areas are receiving experience in areas previously not possible. Our students are getting experience in Internet connectivity within the home as well as connection speeds and stability of the connection. Our co-op students are working alongside technicians who go into the patient’s residence to assure that the medical equipment placed within the home is working and communicating properly. The technicians have learned many skills “on the job” that were previously unnecessary. Our graduates with co-op experience are likely hired full time by their co-op employers.
Along with my position as professor emeritus, I also work as a senior consultant for a hospital network in Cincinnati, Ohio. We are challenged to work within our human resources framework to be able to hire non-full time employees. We have hired co-op students for many years and still hire them when available.
We are trying to be innovative and think within our available framework. We are in the process of attaining approval for a new position within the HTM department. This is an equipment technician position that is entry level and does not require a college degree, however it does require the employee to be pursuing their degree. This would be similar to a “parallel co-op arrangement.” The student would work and attend school at the same time. The traditional “alternating co-op arrangement” would have the student spending one semester in school, then the next semester they would work in a related job placement. Traditionally, there are two students who pair to fill the openings. At this time, we are not able to find enough students to fill these traditional alternating positions. The equipment technician position is attractive to the person who needs a full-time position but does not have the qualifications for a full HTM technician position.
We are hoping that our equipment technicians would sit for the Certified Associate in Biomedical Technology
(CABT) exam. A CABT is an individual who is new to or planning to enter the HTM field and looking to earn an entry-level certification to kick-start their career. We would like them to pursue full certification as a CBET.
Since we are exploring innovate ways to fill HTM roles, I always like to give a shout out to the apprenticeship program within AAMI. This program has been very successful and has helped fill the need for HTM technicians. The following statement is from the AAMI Array website, “Because of the shortage of qualified healthcare technology management (HTM) professionals in the hiring pool, some hospitals and other employers are training their own biomedical equipment technicians (BMETs) from the ground up with no formalized way to ensure these BMETs are trained consistently or to a minimum standard. This apprenticeship program will bring structure to that process and contribute to a solution for bridging the current skill gap in the field for entry-level employees. The intent is that the availability of a formalized BMET apprenticeship that offers formalized training in a real work environment will attract new professionals to the field.”
Steven J. Yelton, P.E., AAMIF; is a senior HTM engineer for a large health network in Cincinnati, Ohio and is a professor emeritus at Cincinnati State Technical and Community College where he teaches biomedical instrumentation (HTM) courses.
BY NADIA ELKAISSI, CHTM, AND JANE LACSON, CCE, CHTM
You are troubleshooting a medical acquisition workstation, but you do not have the correct password. On a whim, you decide to search online for the default local account credentials. To your surprise, you find a document with full login credentials and instructions on using them to remote into your company’s workstations and servers. This document was meant to be an internal tutorial/ training handout, not publicly accessible online. You realize the severity of the situation because it included many internal procedures and default vendor-provided users and passwords. You work with your company to immediately remove the document from the web-hosted repository and begin searching your network for other workstations and servers that might be affected. You contact the vendor to change the default password, but they advise against it, citing potential configuration issues.
Aware that the public credentials pose a security risk, you continue to work with the vendor to update the default logins for all the workstations and servers. As a healthcare technology manager, you also begin to think, is the local passwords required for the device? What are some security measures we should develop to protect these local passwords? Are there alternatives to using local passwords, such as centralized authentication methods? The following article will review security risks local passwords present and some best practices that can mitigate or lower the risk.
The health care industry is increasingly reliant on advanced medical devices for patient care, ranging from pacemakers to CT scanners. While these devices have revolutionized technology, they also introduce new potential vulnerabilities. One significant security risk that is often overlooked is the use of default passwords, which are typically set by the manufacturers and not changed by HTM or clinical staff during implementation. Proper password management and implementation education are crucial. When evaluating and managing medical
equipment procurements, HTM staff must prioritize password policy. When not managed properly, health care facilities could be exposed to the following potential risks:
Local passwords, especially if they are left as the default manufacturer password, are one of the main targets for attack. Many vendors provide the passwords online in manuals or troubleshooting guides. Once attained, these credentials can provide unauthorized users with full control over critical devices.
2. Lack of strong password practices
Even if a local password is modified during implementation, the passwords are often replaced with simple passwords that can be easily guessed. “Root”, “password” and “biomed123” are some of the most common passwords for medical equipment. While it may be inconvenient to have long and unique passwords, weaker passwords are an easy target for attacks, leading to compromised device security.
3.
During the procurement of medical equipment, one area that is not scrutinized as much is the evaluation of the medical devices’ logging capabilities. Unfortunately, many medical devices lack a robust method for logging credentials. Although this should not be the reason to reject purchasing the equipment, HTM staff need to discuss and find ways to monitor the devices after they are implemented. Without a way to monitor/audit passwords, unauthorized access to medical devices can go unnoticed, complicating the investigation of security breaches.
Depending on the HTM’s implementation process, password management is another critical area that can be overlooked. Often, during the procurement and implementation phases, vendors are not asked if their devices support multi-factor authentication (MFA). Consequently, health care facilities end up managing numerous local passwords. A common approach to managing these passwords is to use an Excel spreadsheet, which can come with its own security risks and limitation. Typically, if passwords are stored in a document, it
may not be encrypted which leaves them vulnerable to unauthorized access if the file is compromised. In addition, the document does not offer features such as secure sharing or synchronization across devices, which can make it less efficient for managing passwords securely. Without a proper way to manage the passwords, passwords may be forgotten, written down in unencrypted/unsecured documents or shared inappropriately among staff. Such mishandling of passwords can pose significant risks to the security of the medical devices.
These potential risks can be mitigated by following some simple best practices.
1. Regularly change default credentials
Changing default user logins and passwords is essential upon installing or deploying any device or system. This helps eliminate the risk of unauthorized access using default credentials. A good practice is to develop implementation checklists with an area focused on password management. This will ensure all devices implemented are following the same process. You may find vendors insisting on keeping default passwords unchanged due to system configurations. However, it is not advisable to comply with this requirement. To ensure a smooth transition during password changes, it is essential to inquire about details such as, “What configuration adjustments are required when changing the default password?” and “What are the steps and complexities involved in changing the password?” Even if it is a complex password, the security can be compromised if the password is included in any service manuals or troubleshooting guides. Therefore, changing the default password is one of the initial steps to mitigate the risk.
2. Enforce strong passwords
In addition to changing default passwords, it is important to ensure all passwords follow strong password policies. Strong passwords are characterized by their length, complexity, and uniqueness, incorporating a mix of uppercase and lower-case letters, numbers, and special characters. The length should be a minimum of eight characters; however, it is recommended to try to push the limit to 16 characters or more. It is not advisable to include any personal information or use common words. If the device is unable to automatically require users to change the password periodically (every 90 days), then HTM should develop a tracking sheet to ensure the passwords are changed consistently. Health care facilities should implement policies that mandate password lock outs after a certain number of failed login attempts to prevent bruteforce attacks. Lastly, it is important to also provide constant training on the importance of creating and safeguarding strong passwords. By enforcing these practices, the risk of unauthorized access can be significantly reduced.
3. Monitor and audit default credentials
Monitoring and auditing default credentials is essential to reduce the risk of the medical systems. Often, medical
devices will not have the capabilities to monitor and audit logs. However, it is imperative to ask during the procurement and implementation of the equipment what possibilities are available. In addition to ensuring the system has monitoring capabilities, it is recommended to have policies that require periodic reviewal of default credentials. This could include ensuring default credentials are promptly identified and ensure there are no suspicious login attempts. This proactive approach can help detect and rectify oversights in changing default logins and passwords.
Effective password management is essential in a strong cybersecurity program. Leveraging password management tools enhances the capability to streamline and centralize password management across an organization. The benefits of using these tools can help to automate processes and allow for storing and encrypting passwords. Prioritizing inquiries with vendors about MFA support for their device is strongly recommended. MFA offers enhanced security compared to local passwords by requiring multiple forms of verification, significantly reducing the risk of unauthorized access. The goal should always be to minimize local passwords and maximize the use of MFA wherever feasible, thereby reducing the quantity of passwords that need management. Unfortunately, many medical devices still do not support MFA. Therefore, for local passwords, embracing password management is essential to safeguard sensitive information, promote efficient access control, and ensure compliance with security policies.
Default password management plays a crucial role in cybersecurity within the health care sector. Through timely modification of default passwords, adherence to robust password protocols, staff education, and deployment of effective monitoring tools, health care organizations can significantly mitigate the risks associate with default passwords. Just know that anything is better than nothing. HTM professionals should recognize the significance of password management and strive to integrate it into the implementation and sustainment of medical equipment withing health care environments.
Nadia ElKaissi, CHTM, is a biomedical engineer in the Healthcare Technology Management VA Central Office (19HTM).
Jane Lacson, CCE, CHTM, is a biomedical engineer in the Healthcare Technology Management VA Central Office (19HTM).
BY GARRETT SEELEY, MS, CBET
Ab out one-third of an HTM imaging technician’s service calls will be related to connectivity or DICOM communications. This is part of the reason why the field, in general, advocates strong networking skills for all technicians. I recommend everyone build up these skills to be more successful at their jobs and to help the overall health of society.
For TCP/IP troubleshooting, please refer to previous Networking Notes articles. Keep in mind tools like ping and other command line troubleshooting techniques. For wiring issues, please remember to use a port scanner. Be mindful of the potential for firewall and ACL issues and refer to previous articles for the building blocks of these skills. These techniques will help to repair a communication using non-DICOM related tools. However, these are not the only problems that imaging equipment faces. Unfortunately, these problems can often be non-critical issues, and thereby take a back seat in maintenance to overall operability of the imaging modality. It can be a point of contention that involves not only a radiology department, but information technology, manufacturers, and independent servicers as well as PACS administrators. Therefore, let’s discuss how to tactfully troubleshoot a DICOM issue if there is not a TCP/IP problem.
The first place to look is in the settings. The settings can cause basic communication issues and they can be overlooked or even changed over time. Recall from the previous article that the setup of DICOM requires an IP address, port number and an AE title. Keep in mind that in DICOM, the settings need to be in the right place on both ends. Double-check the settings both at the SCU (source)
and SCP (destination). It is amazing how many times these settings change. This happens particularly after another technician has completed a repair, or after an update resets the settings to defaults. I want to caution against finger-pointing if either of these situations is suspected. Just fix the problem and do not look for blame. When completing a repair, triple-check to make sure a port number or AE title did not mysteriously change. This happens a surprising number of times. Additionally, be aware that there is a setting for what is called a promiscuous mode. In this mode, the SCP is set to not care about the AE title of the SCU. Sometimes this setting gets changed to “on” for security reasons. Again, do not accuse people at this point, simply ask if this change occurred. This can cause an AE title mismatch and the association will be refused. To make matters worse, occasionally both server and client software prefer a reboot. This is usually due to cache memory filling up on either of the ends of the DICOM communication, called an association. Sometimes, turning it off and on again is the answer and there is no clear cause to this issue. These systems may require daily reboots. If the error is related to intermittent failures, check the timeout settings. I suggest a larger timeout setting, for example, 120 seconds for worklists or off-site PACS applications. If the timeout is set too low, it will abort during network congestions. After correcting these settings, remember to always finish a repair with a DICOM echo (also called DICOM ping or DICOM validation). This will verify the solution and it’s one of the easiest things to check. If these suggestions do not provide a resolution, check the error logs for possible errors. Nearly all server software has a debug mode for logging DICOM data. Some clients will also list the error in their association logs. In such logs, the individual DICOM steps are sometimes observable. Lines that contain “A-” refer to the starting and stopping of an association. Lines with the
“C- “statement are commands with data, such as “C-echo”, which is a DICOM validation command. These are the individual protocol data units, or PDUs, of the association. In this way, a complete DICOM error log will show the start, command with data exchange, and the stopping of the association. Advanced troubleshooting is best done by examining such logs. An error of “refused” points to a setting issue with IP, port or AE title. A “timeout” error is usually a firewall or ACL issue, or a timeout set too low. If any log states require header element or syntax errors, I suggest looking up the error in the conformance statement, which is a great troubleshooting tool.
A conformance statement is one of the best resources for advanced troubleshooting of DICOM. It will tell exactly how a device was intended to be used, what type of networking and settings are required, and the header elements needed for a DICOM file to be accepted. A conformance statement is supposed to be available on the web. It is ideally evaluated for compliance with an existing network before purchasing a device, however these statements are usually over 50 pages long. Because of this complexity, some details can be overlooked when installing new devices on a network. There may be a feature that a device was purchased to do that the rest of the devices on the network do not know how to work with. In this situation, a PACS admin will usually have to help resolve the information if it is a PACS system issue. The
manufacturer will usually have to help if the problem exists on the SCU side of the association. Keep in mind to avoid assigning blame. The best way to do this is by presenting the documentation both from error logs and from the conformance statements to all relevant parties.
This brings me to my final point. These types of repairs are best documented as they can involve a lot of different servicers from several different organizations. No manufacturer wants to admit that they had a hand in an issue. No in-house HTM tech wants to admit when they are wrong. No admin or engineer wants to cause an issue. However, all these things can happen. Solutions to these conversations are easier with documentation. For that reason alone, I suggest preserving all information. Screenshots (being mindful of PHI), conformance statements, and downloaded logs go a long way in preventing emotional reactions. This is ultimately the spirit of advanced troubleshooting. My suggestion is to use management and better judgment to diplomatically present what these tools will help you find. This will help make a difference in your facility’s operations.
Garrett Seeley, MS, CBET, is a Biomedical Equipment Support Specialist-Imaging with VISN 17: VA North Texas Health Care System.
•
If your ultrasound transducer is deemed beyond repair at any point, you will not be charged for the repair attempt.
The 2024 edition of the AAMI eXchange was held in Phoenix, Arizona from June 14-17, 2024.
With a schedule packed with speakers, training sessions and expo hall events, AAMI eXchange 2024 was a must-attend event for anyone involved with HTM.
Leading up to the event, AAMI
President and CEO Pamela Arora said, “It’s always a joy to bring together members and friends from all corners of the healthcare technology community for our annual AAMI eXchange conference. eXchange 2024 will provide the training, comradery, and spectacle of years past, while equipping us all with the knowledge necessary to drive safe and effective healthcare toward a brighter future.”
The 2024 eXchange attracted 2,000 attendees, provided 100 educational sessions and 31 presentations via in-booth theaters on the expo floor.
AAMI eXchange 2024’s keynote focused on “hospitals without walls,” and discussed how home healthcare is increasingly the responsibility of HTM professionals.
As the keynote wrapped up, the audience heard that workers can no longer use “that’s not our job” as an excuse, because soon enough, it will be.
Speakers included Ryan Bertram of Chartis, Mike Busdicker, System Director of Clinical Engineering Shared Service at Intermountain Healthcare, Cherie Pardue, AVP/ACIO Clinical Technology at Children’s Hospital of Philadelphia, and Diane Wurzburger, Executive, Regulatory Affairs and Quality, GE
HealthCare.
Another session of interest was “How Paperwork Speaks Louder Than Words,” delivered by Maggie Berkey of Bio-Electronics, Colleen Haugen-Ortiz of GE Healthcare, and Holly Kollman of Booz Allen Hamilton.
They presented their findings from a survey of HTM professionals regarding the state of documentation practices in the industry. Both training and auditing are effective at improving documentation practices. According to Berkey, “We don’t have the tools we need to be successful when it comes to documenting.”
They also announced a forthcoming whitepaper on their findings, and a “Fuel to Thrive” guidebook that will compile existing resources on documentation. These products are meant to help demonstrate the need for future guidance documents.
eXchange also featured a debate session between Dr. Binseng Wang and G. Wayne Moore on remanufacturing and right to repair. AAMI is a neutral convener, but was more than happy to facilitate conversations among members with different perspectives.
Attendees also heard from Erin Sparnon regarding AI’s impact on health equity. “If you don’t know who your AI governance committee is in your facility, you might need to start one,” she said.
Herman McKenzie of the Joint Commission delivered the closing keynote. He spoke about ongoing priorities and what can to expect during an inspection.
Other activities included the second annual golf tournament at the Legacy Golf Club, AAMI Party at Phoenix-area venue The Duce and more.
The 2024 AAMI eXchange in Phoenix, Arizona included a schedule packed with educational talks, training sessions, networking opportunities and an exhibit hall filled with leading HTM companies. The AAMI eXchange continues to be a popular event for those involved in the HTM community. 1 3 5 6 4 2
1. The FSI team took a quick photo at AAMI during exhibit hall hours at AAMI.
2. AAMI eXchange attendees were eager to visit exhibits during the opening reception on Friday, June 14.
3. The AAMI Party hosted at The Duce, a family-owned gem in the heart of Phoenix, was the place to be on Saturday, June 15!
4. Jayme McKelvey proudly awards a lucky attendee prize donated by TechNation for the MedWrench Scavenger Hunt.
5. Pictured, from left to right, Kim Rowand, April Lebo, Elizabeth Cook and Danielle McGeary represent at the Women in Leadership (WIL) happy hour held on Sunday, June 16.
6. Jennifer Chester represented Bella the BMET and Chace Torres represented Ollie the Biomed to increase awareness of the HTM field to audiences new and old.
7. A group photo of the ladies gathered for the Women in Leadership (WIL) happy hour.
8. MJ McLaughlin, Managing Director of Training for AAMI, and Kristin Leavoy, Vice President of MD Publishing, Inc., at the AAMI Party at The Duce.
9. The TechNation team was nothing but smiles headed into day two of exhibit hall hours at the AAMI eXchange.
10. The PioBio and Adepto Medical teams were on hand in the Prescott’s Inc. booth to talk with attendees.
11. Attendees wait patiently (with fingers crossed that their name will be called) as prizes are handed out for the MedWrench Scavenger Hunt drawing. 10 7 11 9 8
• On-Site Repair
• Depot Repair
• Parts Sales and Parts Identification
• Loaner Availability
• Technical Support
• Training
• Injector System Sales
• Preventative Maintenance Tools
Ben Calibrating, or Ben C. for short, is the face of MedWrench! While he may just be a small lego figure, you can find him all over the world.
At MedWrench we have an ongoing contest to see where Ben C. is traveling to and what he’s been up to! Here’s how you can participate:
STEP 1: Like the MedWrench Facebook & LinkedIn pages
Phoenix, AZ
STEP 3: Post a funny caption with your picture telling us what Ben C. is up to
STEP 2: Post your picture of
AUGUST 4-7, 2024
An online resource where medical equipment professionals can find all the information needed to help them be more successful! The easy to navigate Bulletin Board gives you access to informative blogs, expos and events, continuing education opportunities, and a job board. Visit MedWrench.com/BulletinBoard to find out more about this resource.
Follow MedWrench on Facebook & LinkedIn
AUGUST 19-21, 2024
Orange Beach, AL
BY AHMED ABO SULTAN
Providing high-quality services while controlling costs is critical for healthcare businesses. The BME profession is crucial for delivering modern medical equipment, maintaining its operation, and providing dependable support for patient care. However, as medical technology advances, managing service risks becomes increasingly essential to achieve optimal outcomes, cost-effectiveness, and patient safety. This blog will examine the importance of controlling service risks in the BME industry, emphasizing quality assurance, cost management, and proactive risk reduction. READ
STEP 4: Make sure you tag @MedWrench in your post so our team can see it
Omaha, NE
Diag nos t ic Solut ion s i s a
c u s tome r se r v ice ba se d pa r t s pr ov ide r t hat s pe c ia l i ze s i n a l l i mag i ng mod a l it ie s a nd manufacturers Created to offer hos pita l s a nd I SO’s a cos t ef fe c t i ve a nd t i me sav i ng solut ion for or de r i ng i mag i ng r e place me nt pa r t s , e qu ipme nt move s , u lt r a sou nd pr obe r e pa i r a nd on-site se r v ice
Contac t u s today, we a re conf ident you w i l l see u s a s T H E Pa r t s Solut ion!
“We have fresh faces in the classrooms this week. Interested in training with us? Email our coordinator for more information! coordinator@triimaging.com”
- Tri-imaging Solutions
“One day GE OEC 9800 column replacement, team work made the difference”
- Salih Siddeg
“Our National Support team working along our local team on a Canon CT On Job Training. Building our teams and spreading knowledge!”
- Mario Wug
“Wrapping up a month full of fun, learning and growth! Very grateful for the opportunities serving at a sister facility within our health network”
- Nicole Ruffin
Use the hashtag #HTMLife when posting to LinkedIn and a member of the TechNation team will contact you.
Become an Imaging Engineer.
Start an exciting career as a Medical Imaging Service Engineer with the Apprentice Program at Tri-Imaging! We have a world-class hands on training facility at our facility in Madison, TN.