DIGITAL SUPPLEMENT
WISHLIST: PAGE 16 COVER STORY: PAGE 4
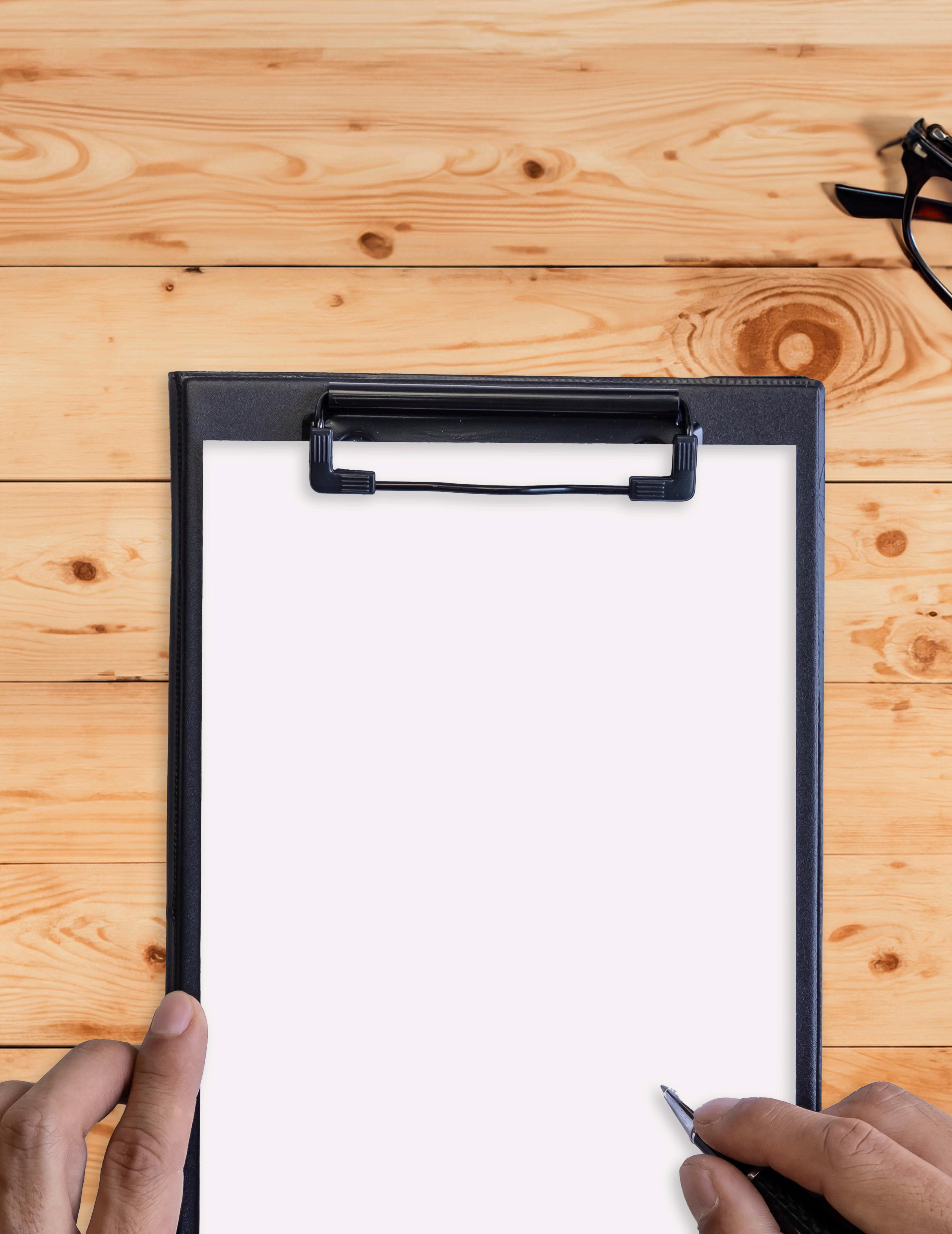
1 6 2 7 3 8 4 9 5 10
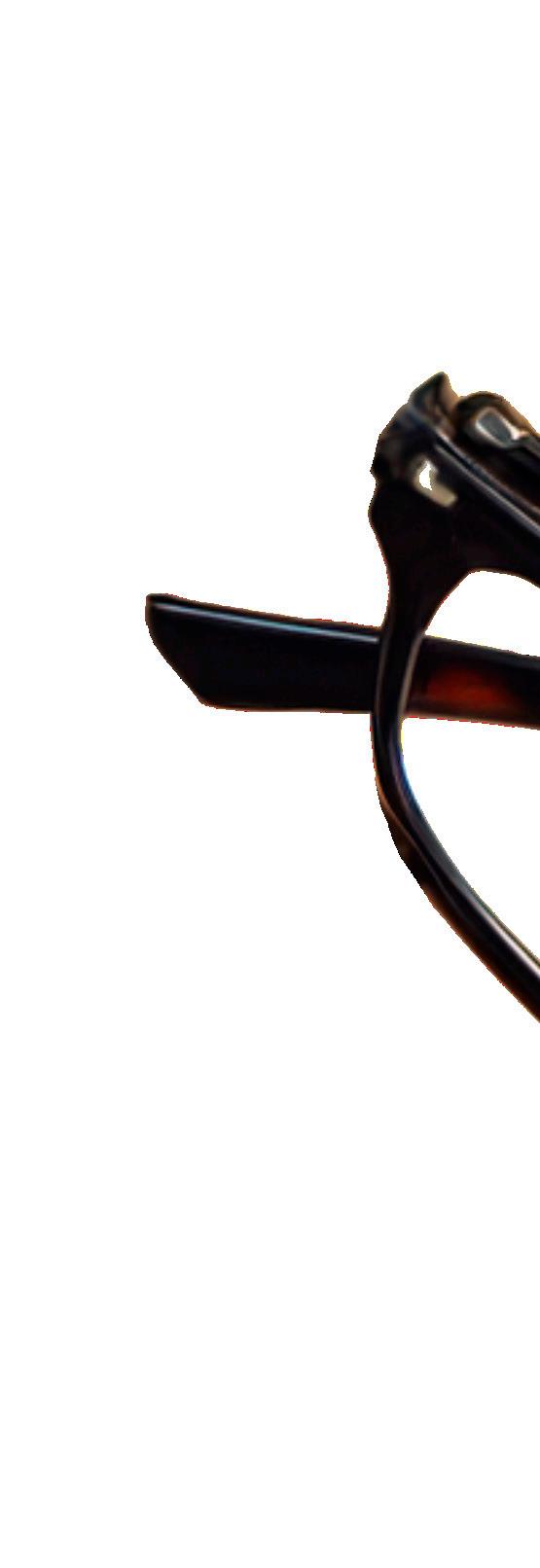

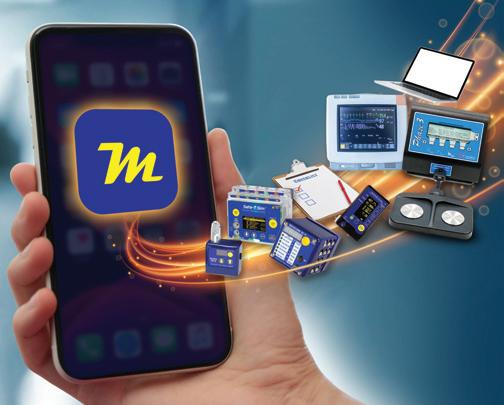
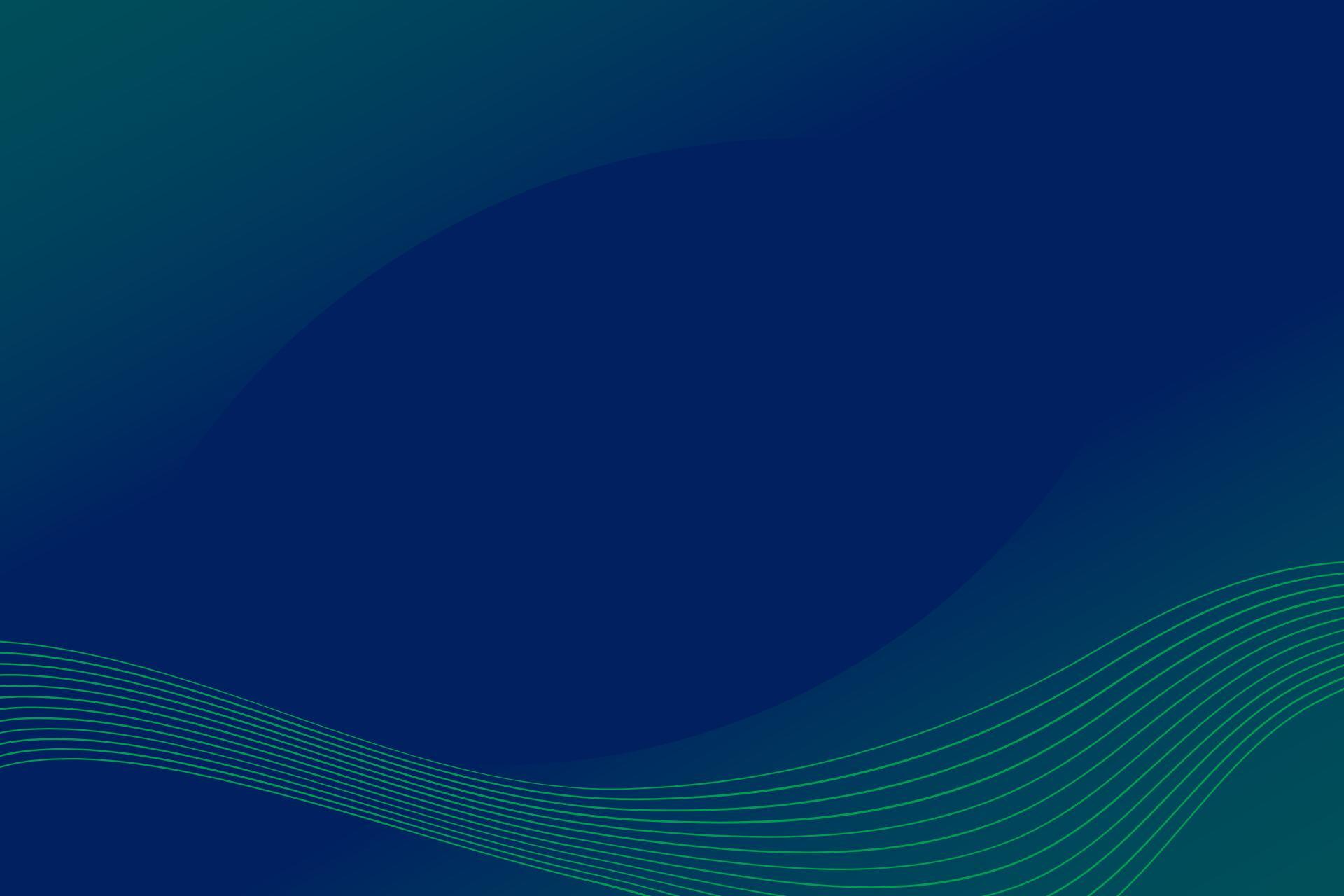
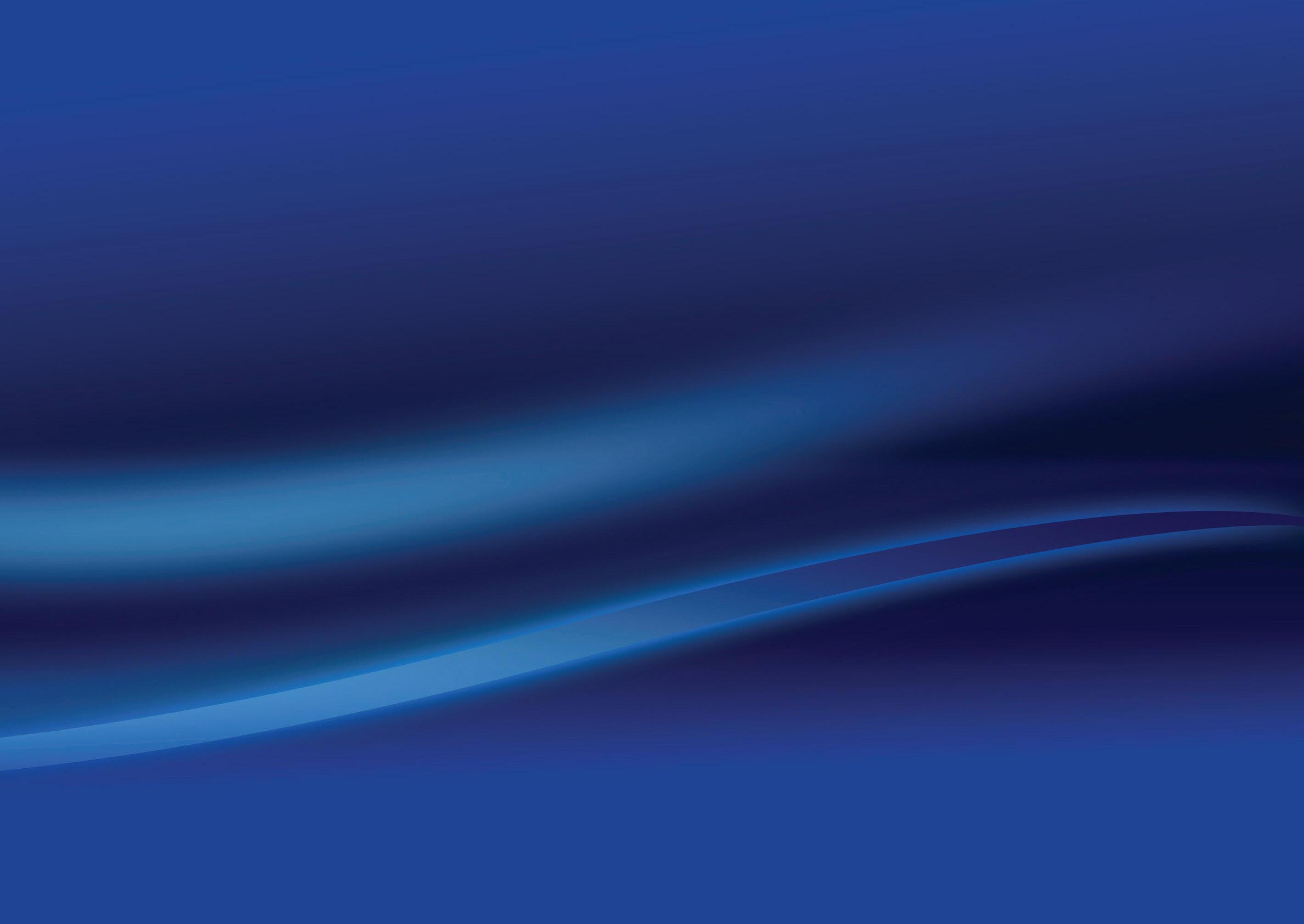
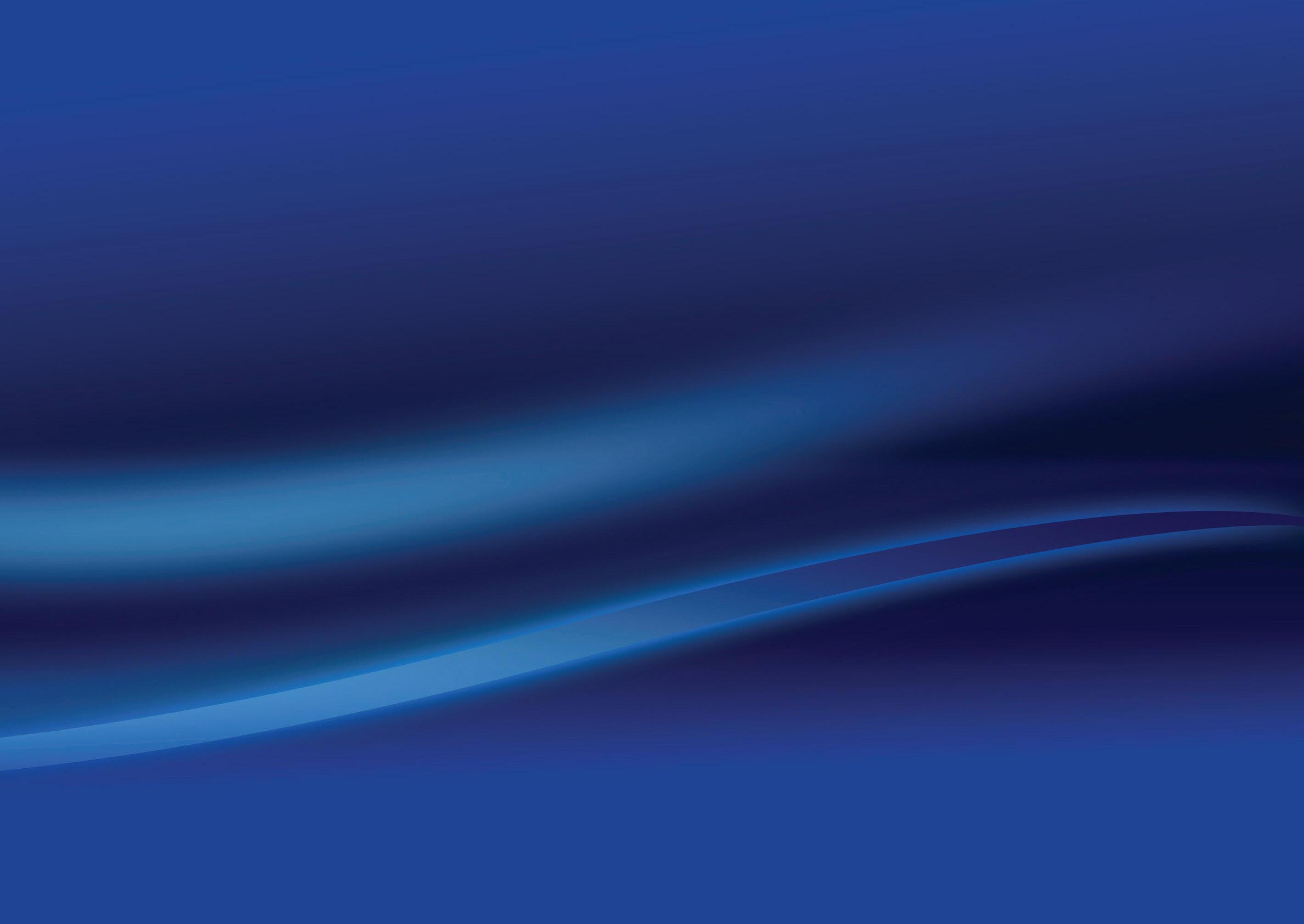
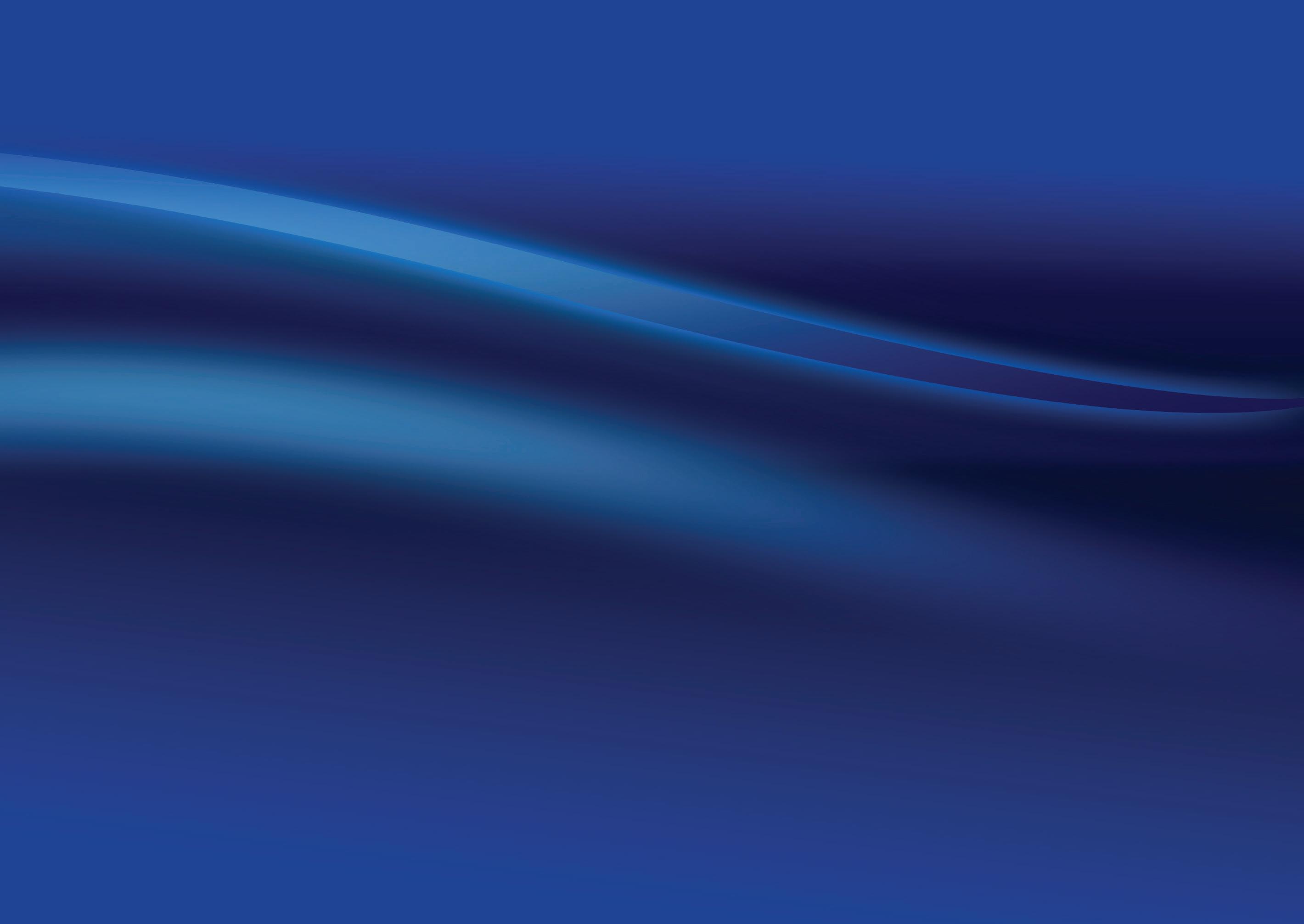
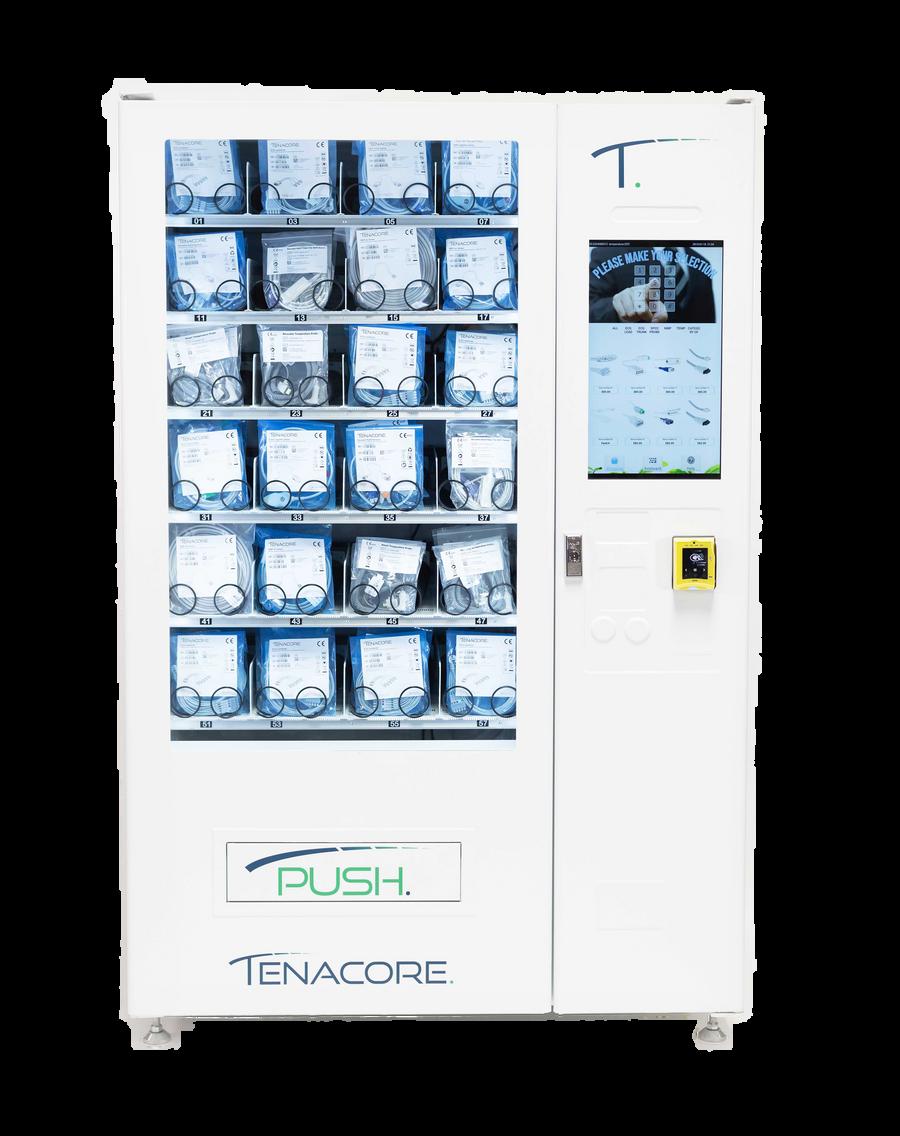
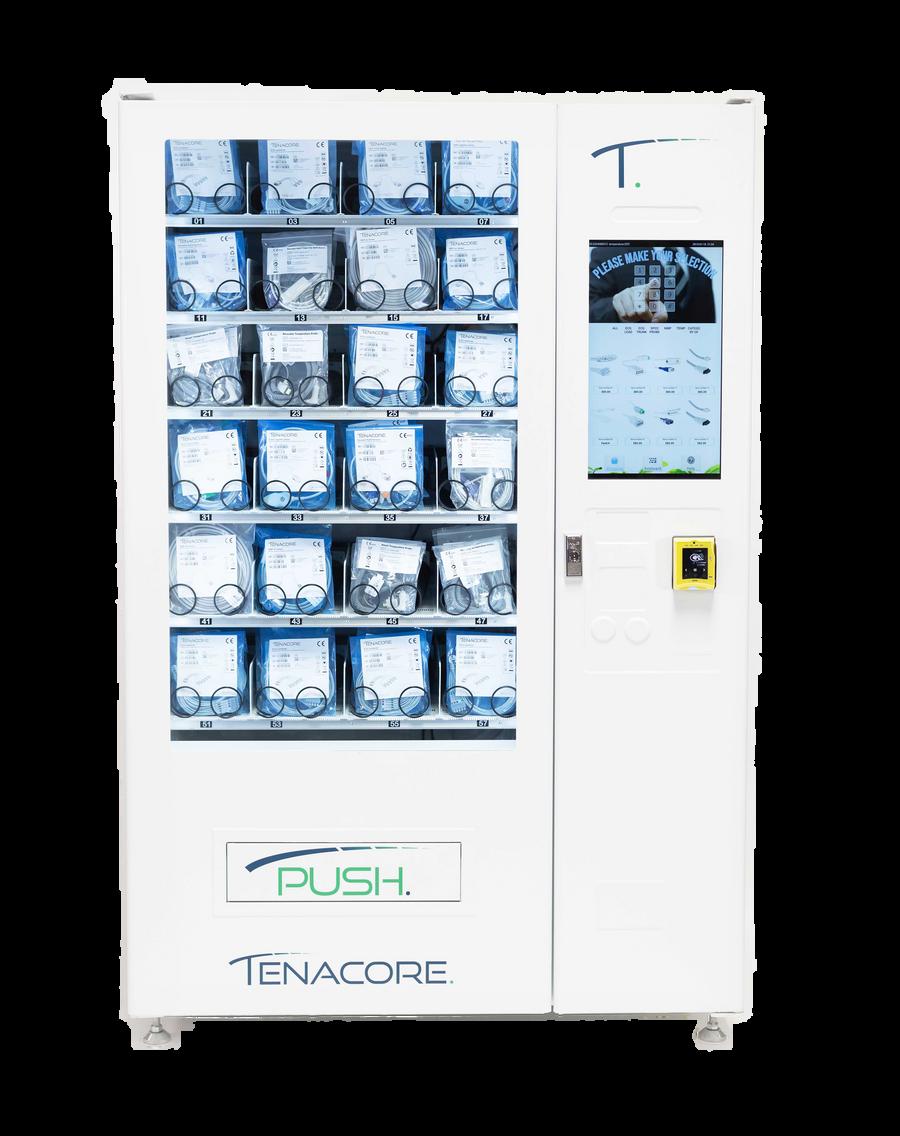

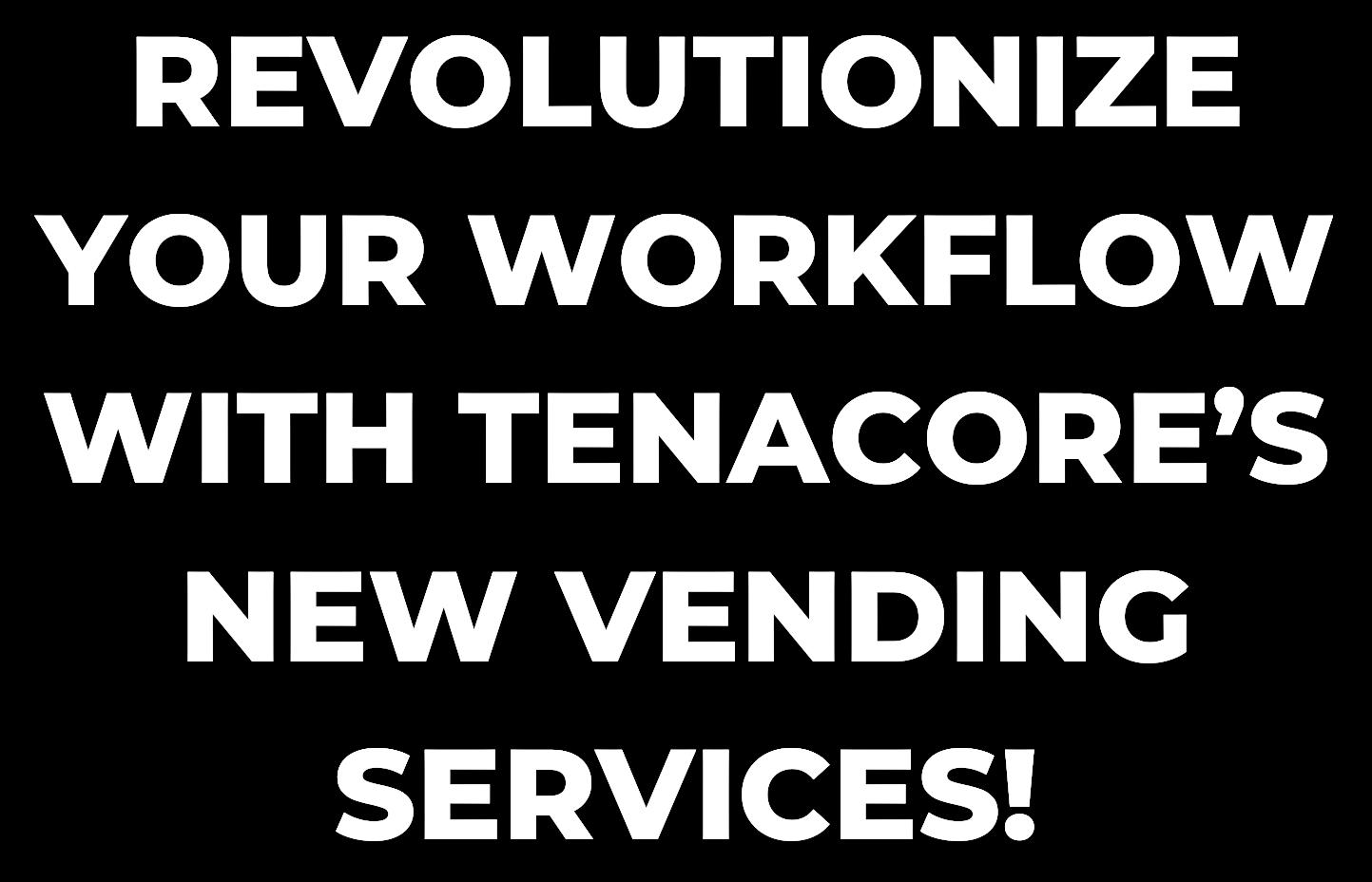

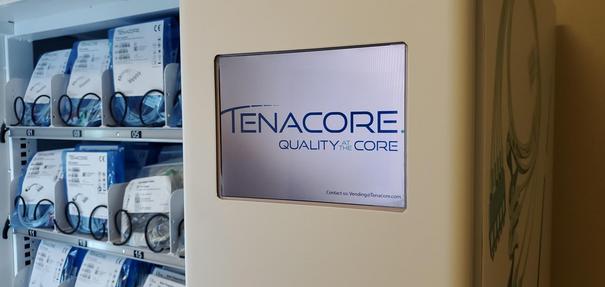
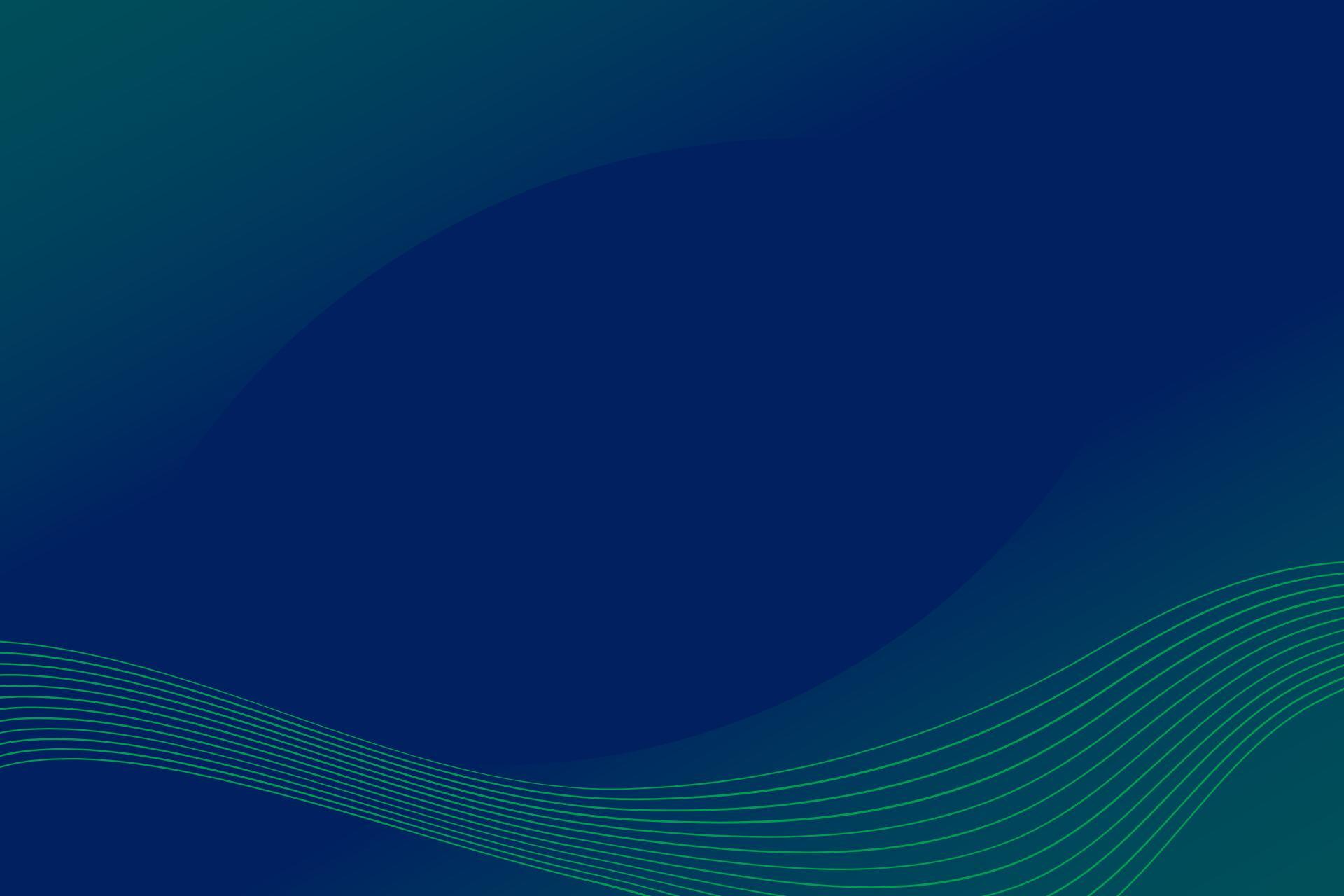

WISHLIST: PAGE 16 COVER STORY: PAGE 4
1 6 2 7 3 8 4 9 5 10
BY K. RICHARD DOUGLAS
h ose who require tools to do their job understand the accuracy of the old saying about the right tool for the job? There is almost always a tool designed and intended for a specific use. There is almost always a time when someone who depends on tools doesn’t have a tool handy that they need in that moment.
If we need to drive a nail into a board, do we use the handle of a screwdriver? Maybe the head of a pipe wrench would work better. The wrench might do the job, yet the head of a hammer works best.
Anybody who has worked extensively with hand tools or measuring instruments knows that there are times when a person runs into a space that is too tight to fit a particular tool or they need a coping saw when they only own a handsaw, or they need a multimeter when all they own is a voltmeter.
As these challenges increase, so does the extent of a person’s tool collection. Many people today have found that there are multi-use tools that fit their needs even better. The bottom line is that there are many projects or repairs that cannot be accomplished without the proper tool.
It’s interesting that the original meaning of the phrase; “the right tool for the job,” was meant to explain how to deal with problems, and tools were just an analogy. Today, just as many people in programming use the phrase with a much different meaning.
For those who work with tools of every stripe, from electronic devices to power tools to hand tools; there is only one meaning.
Most hand tools have reflected the same design and use for decades. A crescent wrench, a screwdriver, a box wrench or a claw hammer have all retained the same fundamental design. Some innovations, like ratcheting wrenches have become popular and screwdrivers and hex sets with driving recesses for Torx and square head have increased in use.
There are now some tools that have associated apps that can monitor usage and maintenance requirements. Even the once-mechanical torque wrench has been digitized and can provide feedback on torque levels, avoiding over-tightening through an audible tone and readout on an LCD display.
Among powered hand tools, one major innovation in recent years has been the ability to cut the cord. Rechargeable battery-powered hand tools have caught on like wildfire, meaning that a construction worker at a job site doesn’t have to worry about a cord when they are cutting lumber with a skill saw. An auto mechanic doesn’t have to be tethered down with a cord when they are using a power ratchet or screwdriver.
Another innovation in many tools is to design the tool using ergonomic considerations to reduce injuries caused by repetitive use. Some tools also incorporate composite
materials to reduce weight.
Of course, one of the most useful tools that has come along in recent years is the smartphone camera. This may be the only tool that was never designed to supplement the tools in a tool box.
Biomeds require a spectrum of tools to do their jobs. Biomeds interviewed for this story stated that they like the convenience of multi-tools, portability and convenience.
Even the most experienced biomeds still have tools they would like to add to their collections. Those wish-list tools are varied and utilitarian.
“I think the top of my list would be for a clinical engineering cart; it would be nice to be able to take all of the tools that you possibly could need with any or all of the test equipment that you would like. I think this would save many trips, going back to the shop and then to the equipment if it was not able to be moved easily,” says Earl Morris Jr., BMET, at Harrison County Hospital in Corydon, Indiana.
He says that the second thing he would like to have would be an electrical safety analyzer as there’s always the need to check equipment for line leakage, high voltage, ground continuity test and insulation test.
“This would be great for ensuring the safety of patient and staff,” Morris says.
Francesca Fam, CBET, a biomedical equipment technician at Stanford Health Care-Tri-Valley in Pleasanton, California, says that she has three items on her wish list. Her choices also reflect portability and versatility.
“[The] ICON Locking Flex Head Ratchet and Bit Set; 35-Piece. It fits right in your back pocket. This set is very useful because it is small, lightweight, and extremely portable. It also has all the necessary bits for handling most service calls I receive without the need to lug
around a giant tool bag,” Fam says.
She says that another pick would be the Knipex plier wrench because it comes in an assortment of sizes.
“I’ve been looking into multi-tools lately and consolidating. Not only is it handy at work, it’s useful for home projects as well,” Fam says.
Rounding out Fam’s choices is the Leatherman Multi-Tool MFR Model #832959, again reflecting the interest in multi-tools.
“This is a gas wrench that doubles as scissors,” she says.
A scope meter with X-ray Mas measurement tools is first on the list for Engineer Naveed Ahmed Khan, P.E., MBA.LSSBB. M.ACCE, assistant maintenance manager at Saudi German Hospital-Riyadh in Saudi Arabia.
Khan’s other two wish-list items are a “digital laser meter to test medical lasers and a dose meter for testing X-ray KV to determine X-ray function,” he says. “Mini electric screwdrivers with multiple bit sizes for working inside the equipment on the boards,” says Donald Sims, BMET II in the healthcare technology management department at Baylor Scott & White in Texas.
Sim’s colleague, Damion Granado, BMET I, expands upon the universe of tools, and says: “A reliable RTLS system to help locate equipment for annual maintenance.”
Another Baylor colleague, Reginald Colemen, says “test equipment that integrates with our CMMS so we don’t have to manually enter results.”
Swandol says he would like a “Hidock H1E GPT-4o Powered Audio Dock with lifetime free AI transcript for creating minutes from board meetings and leadership meetings.”
For biomeds who have been turning a wrench for years, the tools that are favorites would also make good additions to the collections of recent biomed graduates or someone just starting their HTM career.
For that reason, some veteran biomeds share their favorites for the benefit of those just coming on board in the field. No need to engage in guesswork when the voices of experience can offer some sage advice.
“Icon Locking Flex Head Ratchet and Bit Set, Leatherman Charge Plus, Leatherman Raptor Response, Snap On Micro Magnetic Mat, Philips - Xperion 6000 Penlight,” were just a few of the suggestions from Derek Guingon, BMET, at Stanford Medicine in Pleasanton, California.
Guingon also suggested Knipex-Mini pliers and pliers wrench set, Triplett-Receptacle Tester, the Milwaukee 1/4 in drive SAE and Metric socket sets, the Milwaukee Drive Guide Set and the Piscifun tackle bag.
“These tools are my top choices. Having worked in various departments at two Stanford Hospitals, including operating rooms, the main hospital, and clinics, I have noticed that some of my colleagues carry tool bags weighing around 50 pounds. Despite also having a 50-pound tool bag, I found it necessary to assemble the best, versatile, on-the-go, first-call tool kit. My Icon set is meticulously chosen and is my ultimate go-to tool because it includes various common bit sizes, seven security bits, a reversible ratchet with a locking flex head, and a thumb wheel,” Guingon says.
He says that the Snap-on magnetic mat attaches securely to his Icon tool set, keeping all the screws easily accessible.
“The Milwaukee drive guides can function as extensions for various bits or as a cheater bar extension on my Icon set. Carrying different types of Leatherman multitools allows me to have a diverse range of tools at hand. The Philips penlight is equipped with LED and COB lights and features two different magnetic mounts, while my Knipex pliers wrench stands out as the
smallest, slimmest, and most robust wrench I’ve ever owned,” Guingon says.
He says that this collection of tools is designed for mobility.
“Additionally, my Triplett tool is essential for ensuring that the outlet being tested has power for the device,” Guingon adds.
He points out that while tools have traditionally needed to be heavy for strength, he has noted recently that companies are using different materials to make tools more durable and lighter.
Morton Campbell, an imaging specialist in the clinical engineering department at Erlanger Health appreciates the portability tool sets offer.
“Best tool is the Wiha 32-piece drive-loc VI-wallet set, comes with almost everything you will need; cut down my toolbox in half and nice to just throw in a backpack for easy first looks,” Campbell says.
Uriel Vargas Jr., BSEE, A+ certified, healthcare technology regional manager at Baylor Scott & White Health in Texas has a list he describes as a “must-have for every HTM biomed tech; regardless the level.”
He suggests the WERA Multi-Bit Screwdriver: 33 Tips, 5 in overall Lg, quick change, ergonomic grip, single end.
“This can walk with you everywhere and it is and has been the most useful set,” Vargas says.
He says that for both big and small jobs, his go-to power drill is the Milwaukee ¼ inch drive, 0 in-lb to 325 in-lb, 1,700 RPM free speed, brushless motor, 12V screwdriver kit.
Vargas also suggests the FLUKE Digital Multimeter: CAT III 1000V/CAT IV 600V, TRMS, 1,000 V Max AC Volt Measurement.
“Your trusty Fluke DMM always comes in handy,” he says.
Again, a suggestion coming from the voice of experience, Vargas suggests the POWER FIRST cable tie kit: 650 Pieces, nylon 6/6, plastic pawl locking.
“You always need zip ties, and if they tell you otherwise, they are lying,” Vargas says.
Vargas still has a few suggestions beyond the need for zip ties. He also suggests the ESD Precision Nippers: 4 7/8 in overall as a good flush cutter.
Carrying a handy light around your head can be very useful. Vargas likes the Milwaukee headlamp with 4500 Im max brightness and a 25-hour max run time.
“Sometimes you need both your hands, and more light, so this is my go-to,” Vargas says.
To remove stickers, he likes the Scotty Peeler label and sticker remover SP-2.
Eye protection is always important when working with any type of tool, especially power tools. Vargas likes the Milwaukee anti-fog, anti-scratch, wraparound frame safety glasses.
Staying with the Milwaukee brand, he also likes to use the 48-22-8315 15” PACKOUT Tote.
“My bag to carry everything,” Vargas says.
When it comes to more specialized tools for the biomed, Vargas likes the Pronk Technologies BMET Pack Pro.
“And to finish, the complete set the BMET Pack Pro can do all that you need for testing verification,” he says.
“Top used are probably electrical safety analyzer and vital signs simulators for everyday stuff. For repairs, the most helpful is a DMM for troubleshooting. For ultrasound, top for PM and troubleshooting artifacts would be a phantom,” says Bradley Erbe, BMET II at Baylor Scott & White in Texas.
Erbe’s colleague Sims says that useful tools are mini electric screwdrivers with multiple bit sizes for working inside the equipment on the boards.
Sims agrees with Vargas that Scotty peelers are the best tool for removing stickers.
“Cannot go anywhere without it to remove those stubborn stickers,” he says.
Sims likes Milwaukee drills and drivers and says that you can never have too many batteries and battery chargers for the Milwaukee tools.
Granado says that a useful tool is a Fluke multi-channel IV pump analyzer.
“With 2,500 IV pumps due every year, the multi-channel analyzer is a must have; two to four of them preferably,” he says.
The evolution in tools has made many lighter weight, more portable and often capable of multiple uses. As technology advances, the efficiency, accuracy and versatility of many electronic devices will increase. Sets of hand tools will continue to shrink and allow for carrying a greater variety of tools.
As an in-house manufacturer, Elite is dedicated to providing high-quality replacement parts and services for medical devices to improve patient care nationwide. We are FDA Registered and dual ISO Certified (ISO 9001:2015 and ISO 13485:2016) resulting in complete traceability from raw material to finished goods.
Asset tracking is the foundation of a real-time locating system (RTLS). Its facility-wide nature sets the stage for how RTLS can be scaled across a health system to deliver value for additional use cases such as nurse call automation, staff duress and patient flow. When aligning both current and long-term goals with the solutions driven by RTLS, that’s where focused support from an RTLS partner plays a crucial role.
Focused exclusively on healthcare RTLS for more than 30 years, Midmark RTLS and our national network of certified system integrators are dedicated to helping organizations optimize their investment at discovery, launch and beyond. We understand the true key to success is just as much about the right partner and process as it is the technology. We prioritize people by helping organizations plan for the big picture. Deployed in more than 1,000 facilities across the country, our proven methodology utilizes best practices and performance strategies to build a sustainable RTLS investment. Here’s a peek into our approach.
First, we start by understanding your asset management workflow and how it may change with RTLS. For decades, there have been debates about centralized versus decentralized asset management. A centralized approach leans on rounding teams to ensure units are stocked with ready-to-use equipment, or nursing units must request equipment to be delivered when needed. Without RTLS, this is a manual, labor-intensive process that may leave nursing units short on equipment. To save on labor costs, a decentralized approach is often used – each nursing unit manages its own inventory. But because equipment such as IV pumps travel to different units as patients are transferred from Emergency to Surgery, to ICU and Med-Surg, nursing units often lose track of these mobile assets, again leaving units without the equipment they
need. Both models can lead to habitual “hoarding” – stashing away equipment where it can be found for patient care but is hidden from biomedical teams who need to maintain it. This creates the perception of equipment being everywhere and nowhere at the same time. Equipment staff knows they should have is nowhere to be found.
There are pros and cons to each approach, but the good news is RTLS brings the accuracy needed to not only maintain your workflow but enhance it. The key is designing the RTLS deployment to support your desired model – both in how the RTLS software supports the workflow and also choosing the right mix of RTLS technologies that provide both accuracy and cost-effectiveness. For more about the right mix of technologies, keep reading for our RTLS Pro Tip.
With your workflow goals in mind, we then determine which areas of the facility need asset tracking coverage and the desired level of precision that will be required. Infrared (IR) locating technology is the gold standard for room-level accuracy, but most health systems would agree near-room level location details for assets would suffice. Staff don’t need to know the exact shelf an item is sitting on, but rather a general area, like hallway or closet, is just as acceptable for efficiently locating equipment. Bluetooth Low Energy (BLE) technology fills this need with its three-meter range.
RTLS PRO TIP: The best RTLS strategy addresses the long-term vision by comparing both biomedical and nursing team needs. We continually see biomedical teams choose one RTLS to manage assets, but then nursing needs another level of locating precision to automate nurse call, manage patient flow or improve caregiver safety. Addressing these needs separately, out of separate budgets, is costly to the health system. Hybrid technology is emerging as an innovative solution to meet these diverse needs. Combining IR with BLE, for example, provides hybrid locating technology that is strategic yet cost-effective. IR delivers accuracy where highly precise detail is critical, like patient care areas, while BLE delivers just as reliable location information with near-room accuracy, but is more cost-effective for areas in need of just asset tracking.
Whether you choose centralized or decentralized asset management, we’ll also discuss the option for Periodic Automatic Replenishment (PAR). PAR is not a new concept; however, it is a modern approach to monitor inventory levels. The automation it provides helps relieve biomedical team workloads and ensure asset availability for caregivers.
The visualization aspect of PAR allows staff to know at a glance which units are running low or overstocked on key assets. In a centralized model, this alerts the responsible team to take appropriate action to quickly redistribute equipment. In a decentralized model, PAR keeps nursing teams in sync with the inventory in their unit and where they can borrow from if they’re running low. Though not a required component to asset tracking with RTLS, PAR level management can propel efficiency and inventory distribution.
Next, before we begin your RTLS project, we help you evaluate the assets you’re looking to track. Those that deliver the highest ROI or have the highest maintenance or replacement costs are often good places to prioritize. These considerations provide a holistic view of how assets should be managed in your RTLS.
Though asset tag placement is often considered later during implementation, it should be brought into the conversation much earlier. Especially for smaller assets that are easily lost or misplaced, like telemetry packs, tags must be small and secure enough, yet just as accurate. The more often tags emit locating signals, the more “real time” your location data will be, but this can come with battery life tradeoffs. Your RTLS partner will help you weigh all options and variations.
The best RTLS strategy addresses the long-term vision by comparing both biomedical and nursing team needs. We continually see biomedical teams choose one RTLS to manage assets, but then nursing needs another level of locating precision to automate nurse call, manage patient flow or improve caregiver safety. Addressing these needs separately, out of separate budgets, is costly to the health system. Hybrid technology is emerging as an innovative solution to meet these diverse needs. Combining IR with BLE, for example, provides hybrid locating technology that is strategic yet cost-effective. IR delivers accuracy where highly precise detail is critical, like patient care areas, while BLE delivers just as reliable location information with near-room accuracy, but is more cost-effective for areas in need of just asset tracking.
S STEP 5: INCORPORATE CMMS INTEGRATIONS
We’ll also want to discuss your CMMS. Biomedical teams primarily work in the CMMS for asset configuration and work orders. Interfacing your CMMS with your RTLS not only centralizes asset data entry to one system, it also provides real-time location information from the RTLS to the CMMS. Biomedical staff can quickly locate assets through the RTLS location field in the CMMS and navigate to the RTLS for a fleet’s real-time information or bigger picture detail. The end result is streamlined tag configuration and management processes and a smoother workflow.
S STEP 6: PRIORITIZE INSIGHTS + COMMITTED SUPPORT
Health systems can spend all the time in the world finding the right technology, but RTLS is a journey, not a destination.
Midmark RTLS absolutely does the technology right, but it’s our people and decades of experience that make a difference. We and our local partners invest in our customers on day one, and we partner with them throughout their RTLS journey. Customer Success Coaches and local support help analyze data, design best practices and improve processes. We unlock value through deep insights, so that when it all comes together, health systems are empowered to create better patient and caregiver experiences.
Because to us, the experience matters – from assets to workflow to everywhere in between. Our mission is to improve the experience between the patient and caregiver. It’s at the heart of everything we do.
To learn how CareFlow RTLS, along with a dedicated and experienced partner, can turn asset management from “everywhere and nowhere” to “right there,” download our eBook at midmark.com/RTLStracking
The Insulation tester, Leak Tester Tester, Shaver Leak Tester and Cable Continuity Tester are easy-to-use devices for verifying the functionality of equipment for safety
McGan Insulation Tester
Detect & locate defects such as pinholes, cracks and bare spots in the jacket or coating of laparoscopic and bi-polar electrosurgical instruments
Cable Continuity Tester
Test the functionality of automated & handheld endoscope leakage testers with healthmark’s new Leak Tester Tester.
Test the quality of monopolar and bipolar cords with this user-friendly, durable device. A green light noti es the user that the cable passed testing.
Shaver Leak Tester
Designed for pressure testing arthroscopic shavers to help identify leaks caused by failing seals that degrade over time from repeated use and processing.
For more of Healthmark’s intelligent solutions for instrument care & infection control, visit hmark.com hmark.com | 800.521.6224 | healthmark@hmark.com
Our training program at Tri-Imaging transcends traditional education by instilling skills that will resonate throughout your professional journey for years to come. Unlike conventional training experiences focused solely on facts and figures, we prioritize imparting practical, applicable skills.
Our commitment extends to fostering a deep understanding of the intricate inner workings of various devices and machines that our students will service in their careers. Here at Tri-Imaging we believe in nurturing individual growth, and to that end, we provide one-on-one assistance for each student.
Step into the future of education with Tri-Imaging, where our training program transcends boundaries to equip you with skills that stand the test of time.
Introducing the Tenacore Vending Solution – a convenient and innovative product for health care facilities. This state-of-the-art inventory solution is specifically designed to store and dispense patient cables and other high-use products. With its user-friendly interface, clinicians and administrators can quickly access a wide variety of products, ensuring they always have the right equipment on-hand. The machine’s design allows it to fit seamlessly into any environment, while its secure storage system ensures products are kept in stock and organized. Experience the next generation of supply chain management with the Tenacore Vending Solution.
In the fast-evolving landscape, health care technology management (HTM) professionals play a crucial role in ensuring that medical devices function optimally. As they navigate the complexities of equipment maintenance and management, having the right tools at their disposal can significantly enhance their efficiency, accuracy and effectiveness.
The modern health care environment demands precision and reliability, making it imperative for biomedical engineers and technicians to stay equipped with state-of-the-art tools. From diagnostic devices and parts to software and repair kits, the right “tools” streamline workflows and enhance patient safety.
The 2024 Biomed Wishlist highlights the tools and devices HTM professionals need to best meet their responsibilities.
Game-changing gear for your toolkit. The Pronk Inflator is a pressure calibrator hand pump that generates both positive and negative pressures, significantly reducing the time to set pressure test points. Designed for accuracy, it features a lock/unlock mechanism for the plunger that facilitates not only coarse but also fine pressure adjustments with high precision. Rated for up to 50 PSI, it is the ideal accessory for the Pressure MAX Pressure Meter, SimCube NIBP Simulator, and FlowTrax IV Pump Analyzer.
Accruent’s TMS is a purpose-built health care CMMS trusted by over 600 health care organizations. A major player in the health care and biomed facility management market since 1995, it has recently been reimagined (again) into a cloud-centric, mobile friendly application with a strong focus on algorithmic work order prioritization, cybersecurity and data integrity. Accruent has surprised longtime customers with its asset management features and a new user interface that’s been winning strong praise for its ease of use and overall aesthetic. The recent upgrades also strengthened the product’s existing functionality around compliance and
preventive maintenance — including location independent access and on-the-spot data capture and documentation. Users now use their mobile devices to scan barcodes and take photos to document changes to the facility’s equipment roster, making maintenance, warranty management and regulatory compliance easier than ever. Overall, the “New TMS” has been getting high marks from longtime customers and new ones for its user focus, and making it possible for health care facility and clinical engineering teams to streamline their workflows and workloads using devices they already own, and matching the realities of how they work today.
The IPA-3100 is the most compact, feature dense single channel analyzer on the market. It is a high-accuracy, easy-to-use system that incorporates full touch screen control with an intuitive interface. The patented design uses a dual syringe stepper motor driven system that provides continuous monitoring of the fluid flow without the need to stop and perform intermittent drains like older technologies do. This provides a more realistic flow path for the infusion device under test and therefore more accurate readings. The IPA-3100 has configurable test parameters which allows for specific test routines specified by various manufacturers. Tests can be stored manually or automatically with up to 250 different records. These test records can be downloaded to a computer to then create reports that can be printed. The IPA-3100 has Bluetooth capability built-in. With the use of myBC Mobile or BC Flow, multiple test configurations can be stored for quick testing. Records of each test can be created and then saved for later viewing and analysis. Reports can also
The IPA-3400 is the most compact, full featured four channel analyzer on the market. It is a high accuracy, easy-to-use system that incorporates full touch screen control of all processes. This new cutting edge, patented design uses a dual syringe stepper motor driven system that provides continuous monitoring of the fluid flow without the need to stop and perform intermittent drains like older technologies. This provides a more realistic flow path for the infusion device under test and therefore more accurate readings. Also, independent stepper motor control of the custom designed ceramic valving allows the system to run not only more quietly and more smoothly, but it also allows for a bidirectional powered fluid flow for use in the built-in cleaning cycle. The IPA-3400 has built-in auto-sequence capabilities that allows the user to perform automatic test procedures. This allows specific test routines specified by various manufacturers to be run, which provides a significant time savings as well as reduces the risk of human error. Advanced features in the auto-sequences allow the inclusion of pictures to aid with the setup and configuration of each step. The IPA-3400 allows for
be generated from test records for in-depth analysis and/or traceability. Features inclue:
• Bluetooth Built-In
• Bubbles Do Not Interfere with Testing
• 4.3” Color Touch Screen
• Automatic Start
• Smooth Dual Syringe System
• Micro USB Port
• Industrial Grade Pressure Sensor
• Whisper Quiet Operation
easy field expansion. You can buy a 1 channel unit and later purchase additional modules that can be added in the field. Just plug them in and the system will automatically recognize the additional module(s), reconfigure itself and you are ready to go. Features include:
• Bubbles Do Not Interfere with Testing
• Large 7” Color Touch Screen
• Built-In Data Collection
• User-Swappable Flow Modules
• 4 USB Ports & 4 Aux Ports
• Adjustable Back Pressure
• Continuous Fluid Flow Monitoring
Simplify budgeting season with FSI’s Capital Planning tool. As the CMMS/ EAM purpose-built for health care professionals, FSI’s tools are optimized to include the features needed most, including when it comes to financial planning. CMS Capital Planning ensures each department has all of the information it needs to keep an eye on priority metrics and build an effective, data-backed budget plan without getting lost in messy spreadsheets. With intuitive visual overviews of department budget information, CMS Capital Planning puts key data in one spot to centralize budgeting processes. Easily monitor where spend is going to ensure departments are on track with financial goals, analyze trends in data to identify priority areas in asset replacement or preventive maintenance, and create financial plans based
on real needs directly within Capital Planning. Empowering departments with greater visibility and control in budgeting cycles allows more effective, long-term planning to support widespread facility operations. From diving into asset data to pulling equipment maintenance history, checking which assets are nearing end of life dates, to displaying and exporting trends in historical spend to support a budget request to decision makers, FSI’s Capital Planning tool keeps teams in the loop on essential financial data.
Designed for pressure testing arthroscopic shavers to help identify leaks caused by failing seals that degrade over time from repeated use and processing, the Shaver Leak Tester assists health care workers in reprocessing areas to make sure their shaver is working properly by using both a hand pump to apply pressure and a testing stop made from polypropylene to create a temporarily closed system within the fluid pathway of the shaver to pressure test for leaks. Utilizing positive pressure allows the user to confirm if the internal seals are fully intact or if the shaver needs to be sent out for repair. The Shaver Leak Tester helps in reducing the potential for cross-contamination, damage and costly repairs that result from using a shaver with leaks. Simply, select the appropriate brand specific testing stop and insert the stop into the distal end of the shaver’s handpiece until it is fully seated. Then, connect the open end of the silicone tubing attached to the pressure gauge, to the stainless-steel discharge port located at the proximal end of the handpiece. Next, use the bulb of the hand pump to apply pressure and observe that the pressure gauge is displaying and maintaining a positive value. Confirmation of positive static pressure on the pressure gauge indicates no leaks in the fluid pathway and is considered a passing result. The brand-specific Shaver Leak Tester stops are not interchangeable and offered for the following shavers: the Midas Rex shaver, the Stryker Formula shaver, the Stryker Small Joint shaver, the Dyonics shaver, the Conmed Linvatec shaver, and the Arthrex shaver.
Safe, timely and effective care can be jeopardized when the equipment that makes it possible is everywhere … and yet nowhere at the same time. Most hospitals believe they have enough equipment, yet biomedical and nursing teams spend thousands of hours per year searching for equipment they know they should have … but is nowhere to be found. Non-value-added time, preventive maintenance schedules and staff satisfaction are just the beginnings of operational setbacks. With both in-room and near-room accuracy options, CareFlow RTLS can be designed to benefit both biomedical
and nursing teams. Midmark CareFlow Asset Tracking not only helps free biomedical teams from endless rounding to find equipment, it also informs nursing to equipment location with a system that is easy and intuitive for nurses to use. Partnering with Midmark RTLS, you don’t just get the right technology, you get the commitment, the people, and the expertise to ensure seamless integration and adoption. CareFlow RTLS helps guide operations, aligning people to process, while regionally certified local partners help optimize your investment through launch and beyond.
PartsSource PRO is the only comprehensive, clinical management platform built for the specialized workflow and procurement needs of clinical engineering and supply chain teams. Designed to empower health systems, PartsSource PRO’s evidence-based, decision support and workflow software helps unlock value and capacity across your entire organization, maximizing uptime and providing a modernized approach to sourcing, asset management and equipment repair, all while reducing risk and costs. With PRO’s innovative technology, health care organizations can consolidate day-to-day operations into a single, user-friendly dashboard, providing enhanced control and oversight. Imagine being able to manage all orders with data insights to see what you spend and where, consolidate suppliers, optimize contracts, improve purchasing policies and decrease off-contract spending. It is all possible with PartsSource PRO. The platform ensures that critical equipment and services are available when needed, helping to reduce downtime and improve the overall efficiency of health care operations, while giving health care providers the ability to stay focused on delivering high-quality patient care. Discover why over 1,600 health systems across the country rely on PartsSource PRO to leverage their community buying power and maximize time and cost savings.
The Pronk Power Bank will, on a single charge, provide the capacity to run over 1000 NIBP readings on the SimCube NIBP Simulator. It features an LED battery status display, two output ports (USB-A and USB-C), and wireless inductive charging for smart devices and watches. It is the ideal battery power source for Pronk test equipment and smart devices. Rated for 15000mAh, 22.5W, it has an internal lithium polymer battery, weighs only 13.5 oz., and is palm-sized (3.4” x 3.4” X 1.2”).
Designed with the precision and reliability needed for biomedical technicians, the Biomedical Tool Kit is the ultimate companion for maintaining and repairing medical equipment. This comprehensive set includes high-quality hand tools specifically chosen for their effectiveness in the biomedical field. Whether you’re working in a hospital, lab, or field environment, this toolkit ensures you have the right tools at your fingertips. Key features include:
• Specialized Tools: Includes a selection of high-quality, precision-engineered tools tailored for the unique needs of biomedical maintenance and repair.
• Durable Construction: Crafted to withstand rigorous use and provide reliable performance.
• Choice of Case: Available in a sturdy hard case for maximum protection or a flexible soft case for ease of transport and accessibility.
• Organized Layout: Tools are organized in a way that allows for quick identification and efficient use. Whether upgrading a current toolkit or starting fresh, the Biomedical Tool Kit is designed to meet the high standards of professional biomedical technicians.
With a certified ISO 13485 QMS, Summit Imaging offers ultrasound probe repair and maintenance, customized to the type of customer. This includes options like full transducer repair coverage for hospital networks, on-site care and maintenance training to prevent unnecessary damage, and forensic reporting and analysis of incoming transducer damages. When conducting a total cost of ownership analysis comparing an OEM service contract to a transducer repair model like Summit Imaging, health care facilities will likely find a significant savings of 30% to 95% when utilizing the repair model. As the leading ISP of
Tri-Imaging Solutions understands the critical role a GE Optima 660 CT scanner plays in delivering accurate diagnostic imaging and patient care. With its comprehensive service packages, expert training, quality parts, and tailored savings plans, Tri-Imaging Solutions ensures the system operates efficiently and cost-effectively. Tri-Imaging Solutions offers:
• Expertise and Reliability: With years of experience in the medical imaging field, Tri-Imaging Solutions is a trusted partner. Its certified engineers are specially trained on GE systems.
• Comprehensive Service Options: Service plans are designed to fit the unique needs of each facility. From full-service contracts to preventative maintenance, Tri-Imaging Solutions offers flexibility and peace of mind.
• Industry-Leading Training: Tri-Imaging offers hands-on, in-depth training programs tailored specifically for the GE Optima 660. The training ensures that your team
ultrasound parts repair, Summit Imaging sets itself apart with dedication to fast, higher-quality service ensuring the proper systems are in place to protect patients’ safety.
knows how to operate the system to its full potential, improving diagnostic accuracy while reducing the likelihood of technical errors. Tri-Imaging Solutions empowers your staff to become experts in their field.
• Genuine Parts and Components: Tri-Imaging Solutions stocks a vast inventory of OEM and high-quality third-party parts for the GE Optima 660. A quick turnaround on parts delivery helps minimize downtime and ensures the scanner continues to function at peak efficiency.
• Cost-Effective Savings Plans: Tri-Imaging Solutions’ savings plans are designed to keep your budget in check without sacrificing service quality. From discounted parts to flexible payment options on service contracts, Tri-Imaging Solutions makes it easy to manage costs over the life of your equipment. With Tri-Imaging Solutions, facilities get premium service at a competitive price, ensuring facilities get a long life out of a Optima 660.
Registration on WebinarWednesday.live. Eligible for 1 CE credit from the ACI.
Achieve a new level of operational efficiency from a CMMS with the time-saving, error-reducing automation capabilities introduced with FSI’s new Flow Tool.
FSI’s Flow Tool combines added automation with the customization that FSI users benefit from throughout the platform. Flow enables users to create custom automations, streamlining common workflows from a lengthy multitude of clicks to one press of a button.
For an additional level of automation, FSI has partnered with Fluke Biomedical to integrate with OneQA workflow automation software, allowing users
to run OneQA and display results directly within a work order procedure, cutting down manual steps in device testing workflows.
Join us for a 1-hour session led by Mike Zimmer, solutions engineering manager at FSI, on how automation capabilities with FSI’s new Flow Tool for custom automations and OneQA integration for device testing take maintenance management to the next level of efficiency.
For more information, visit fsiservices.com
A.M. Bickford is the authorized US distributor and calibration service provider for the FI-8000P Riken Gas Indicator.
• The all-in-one solution for measuring gas concentration of Sevoflurane, Isoflurane, Desflurane, and Halothane.
• Updated software and firmware.
• Approximately 50% faster than previous model.
• Intuitive user experience.
• One-touch switching between gases.
r escott's was founded in Monument, Colorado in 1980 by an entrepreneurial family from Prescott, Arizona. With its origins as an OEM distributor, Prescott's saw firsthand the need for a high-quality independent service organization specializing in surgical microscopes within the United States.
Q: WHAT ARE SOME ADVANTAGES THAT YOUR COMPANY HAS OVER THE COMPETITION?
Fast forward 44 years and Prescott's has a knowledge base to service, supply parts for, and refurbish all brands, models, and generations of surgical microscopes. Today, Prescott's stands alone as the only independent service organization with national coverage, the ability to service all surgical microscopes, and unmatched response time.
If the story ended here, we would describe Prescott's as an inspiring story of vision, ambition, hard work, and success. But the story doesn't end here.
"We believe the same principles that led to success in surgical microscopes will lead to success in other modalities our customers care about," Prescott’s CEO Brian Straeb explains. "Between 2021 and 2023, Prescott's has acquired four new modalities including infusion pumps (Adepto Medical (Adepto)), patient monitors (Pioneer Biomedical (PioBio)), sterilizers (Preventive Maintenance Medical), and anesthesia machines (Heartland Medical/Vetland)."
Prescott’s Surgical Microscopes and Adepto/PioBio boast the ISO 13485 certification, and there are plans to include additional certifications in the future.
TechNation is eager to share more about this innovative family of companies and how Prescott's can assist hardworking healthcare technology management leaders throughout the nation.
STRAEB: Prescott’s is a family of brands specializing across six critical modalities. Each modality is the legacy of Prescott’s acquired companies who are known as specialized technical experts with a customer first culture. At its core, technical excellence and a customer-centric culture are the two features we look for when considering business fit for acquisition and expansion. Our top priorities will always be to deliver technical excellence when and where needed, to get it right the first time, and to deliver a best-in-class customer experience so patients receive the care they need.
Importantly, our objective is to retain the things each of our businesses has always done best while leveraging the infrastructure of the larger Prescott’s Group. This allows our customers to enjoy the continuity of working with vendors they have come to depend on while benefiting from being a part of a larger organization.
Our advantages come from:
1. Technical Excellence in everything we do.
2. Best in Class Responsiveness minimizing patient disruption.
3. Market leading value.
We can service, sell, rent, or procure products in all modalities including surgical microscopes, infusion pumps, patient monitors, anesthesia machines, sterilizers, and washers, and complete operating room design and buildouts.
Let’s discuss service for a moment. While some of these devices are small and can be mailed in for service, many of the items are extremely large and expensive. Oftentimes hospitals have a limited number of these devices such as surgical microscopes in their inventory, and they rely on those to function correctly to ensure patients receive the care they need. When one malfunctions or is due for service, time is of the essence. Understanding the severity of these situations,
Prescott’s has positioned over 75 expert technicians across the U.S. and the UK. These technicians are in the field both proactively servicing your equipment and ready to respond when something is not properly working.
Prescott’s has serviced microscopes in the field for over 40 years. During that time, they inquired with other companies like theirs that service anesthesia machines, sterilizers, and washers.
Rather than attempting to train their technicians in these areas, they reached out to two of the industry leaders, Heartland Medical and Preventive Maintenance Medical, and the Prescott’s family of brands began to come together. Our organization then saw the struggle our customers were having in keeping their infusion pumps and patient monitors up and running. Bringing Adepto and PioBio into the partnership has provided our customers with the ease of having experts in these modalities along with an easy-to-use RMA/RGA system that removes all the stress when sending a device in.
Adepto and PioBio also bring a large fleet of rental devices to the fingertips of our customers. As experienced during COVID, when high flu season or major health events occur, additional hospital beds are needed. Each bed requires an infusion pump and a patient monitor. Often, hospitals rely on rental devices to accommodate the increased need. Adepto and PioBio have hundreds of devices in many different models ready to be deployed at any given moment. This is especially true during the annual flu season.
With our Vetland brand, we bring the same support to the veterinary community that provides health care to our furry family members.
Q: WHAT ARE SOME CHALLENGES THAT YOUR COMPANY FACED LAST YEAR?
Bringing the brands together to operate as one while retaining their independent strengths has been a fun journey and one that will continue. Bringing together companies as one can be difficult under any circumstances, this can be exceptionally challenging when all companies involved have strong established cultures, strong employee and customer relationships, and are independently successful organizations. These are things we want to keep intact and continue to grow but with many of the departments becoming what we refer to as “group level” departments, we needed to start the process of unifying certain areas as one. Equally important to our internal groups and messaging is our external messaging to the world and, more importantly, our customers about who this group is and what we represent.
We started with the group logo and core values. This process started by forming a group of top management from all brands and working through the process together for several months. We took best practices from all organizations and brought parts of all together to form one unified message and internal belief in what we represent. Keeping the core name of Prescott’s was important to all, but also was keeping identities. For that reason, we incorporated the icons from each of the brands into our messaging and website structure. Allowing our customers to be at ease knowing the level of service and flow of doing business with each of the divisions would not change from what they are accustomed to while providing the platform to grow as one united organization.
Q: CAN YOU EXPLAIN YOUR COMPANY’S CORE COMPETENCIES?
The core values came together in early 2024. After considering best practices from each division, we established this group of core values, known to us as the Gears of Success, we then paired each value with an explanation of what that core value means to this team. We are happy to share those here:
Prescott’s Gears of Success: Integrity: Act with unwavering integrity in every endeavor. Teamwork: Be hard on problems – not people. Excellence: Consistently pursue greatness. Respect: Cultivate harmonious relationships. Innovation: Measure efforts before results.
Q: WHAT PRODUCT OR SERVICE THAT YOUR COMPANY OFFERS ARE YOU MOST EXCITED ABOUT RIGHT NOW?
The core of the group is the service and repair of the devices, and that service is still what is most exciting about
this organization. Each division has decades of experience in their modality, and they continue to expand that knowledge daily. Often health care facilities do not have the budget available to always upgrade their equipment. The devices they have are still great devices and will last years. However, finding the support to service those devices properly is often a challenge. We provide that service and expert knowledge to allow our customers the flexibility to allocate their budget as they see fit while keeping their current fleet functioning properly. We have taken this a step further by perfecting the ease of doing business with each division by either having boots on the ground or streamlining the RMA/RGA systems for our depot service devices to ensure our customers can keep their focus on providing the care their patients need, rather than worrying about how they will keep their fleet of devices running properly.
Q: WHAT IS ON THE HORIZON FOR YOUR COMPANY?
The future is bright for Prescott's. By bringing high-quality service offerings across multiple modalities to our customers, we expect to grow rapidly. Our evolution over the next several years will focus on resource allocation, operational expansion, maintaining the highest level of quality and responsiveness, and building on our great culture.
Q: CAN YOU SHARE SOME COMPANY SUCCESS STORIES?
Below are a few stories/experiences our customers have shared with us:
“If we have something break, I’ll call my rep at Prescott’s, and I’ll say, ‘This is what’s going on.’ And if it’s a quick fix, he’ll tell me over the phone how to fix it, rather than him driving from … wherever he is at that time. … And that’s why they are my preferred [vendor].”
“I tell my coworkers, ‘Check out this RMA. It’s really easy to use, you’ll get a shipping label sent right to you, and you’ll be able to box it up and send it right away, and quick turnaround time, and it works when it comes back.’”
“There hasn’t been one service complaint as I’ve been here for 12 years, and the savings have been substantial. Dependability is through the roof. I cannot say enough good things about the Prescott’s service delivery.”
“If something happens and the microscope is in need of immediate attention, then they will walk me through
what I need to do. So, their service support is outstanding up here as well.”
A customer called at 8:00 am one morning stating that their air dryers failed, and the air lines were filled with water. They had all their 14 anesthesia units down and were quoted a 6-week turnaround from their vendor. We had units in stock and ready to go and by 3:00 am the next morning we had them up and running with 14 units. They resumed business as usual the next morning, and the patients received the procedures they needed on time.
Q: CAN YOU DESCRIBE YOUR COMPANY’S FACILITIES?
Our surgical microscope division is in Monument, Colorado, and along with the 75 field service employees we have, this facility houses over 50 employees from administration, shipping and receiving, in-house technicians and inventory specialties.
Our infusion pump and patient monitor divisions house over 50 employees in Kansas City, Missouri. This is a depot service model meaning all service technicians are on site in Kansas City and our customers mail their devices to them for service or repair.
Our anesthesia experts have a headquarters location in Louisville, Kentucky. The service team and operating room design specialists are in the field.
Our sterilizer and washer technicians are also in the field with headquarters in Mount Vernon, Ohio.
Q: IS THERE ANYTHING ELSE YOU WANT TECHNATION READERS TO KNOW ABOUT YOUR COMPANY?
We are extremely proud to be part of the HTM community.
We know how much work all of our partners, competitors, and customers do to keep these hospitals and facilities up and operational. We also know most of the technicians and employees of these companies don't get the credit and publicity that clinicians get or that they deserve. However, we are very aware that without the equipment and services all of us in the industry provide none of this would be possible.
Thank you to all our customers and to all the HTM professionals for all you do!
Brian Straeb, CEO at Prescott’s.
be
When your ultrasound equipment is down, so is your business. Don’t miss our Solutionist Series videos on Ultrasound Equipment Support where you’ll learn how to service your equipment, keep your business up and running and lower your total cost of ownership.
In this 10-episode virtual training course on the Philips Epiq ultrasound platform, Larry Nguyen, Summit Imaging’s Founder and CIO, identifies common failures and provides solutions for:
• Image quality — 2D grayscale, color, continuous wave or pulsed wave
• Power subsystem — power module and power regulator board
• External interfaces — control panel, touch panel, trackball, monitor and external IO
• Transducer types and applications — Doppler, linear, curved, endo-cavity and more.
• Transducer parts — a breakdown of standard and TEE
• Transducer parts and operational failures — from lens failure to cut or creased cords to CW noise and error codes
Larry Nguyen addresses lots more in our 10-episode Solutionist Series, so be sure to tune in.