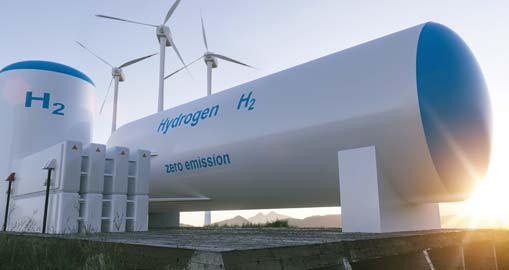
14 minute read
RENEWABLES Enbridge Gas launches first hydrogen- blending project in North America
ENBRIDGE GAS LAUNCHES FIRST HYDROGENBLENDING PROJECT IN NORTH AMERICA
Calgary, AB-based Enbridge Gas Inc. has announced that North America’s first hydrogen-blending project is now fully operational in Markham, ON. Hydrogen blending involves injecting clean hydrogen into the delivered natural gas to reduce its carbon footprint, in this case up to two per cent by volume of the natural gas supplied. According to Enbridge, the innovative technology will supply green gas and lead to larger made-in-Ontario clean energy solutions. The $5.2-million pilot project is in partnership with Cummins Inc., with support from Sustainable Development Technology Canada, the Canadian Gas Association and NGIF Capital Corporation. The project involves enhancements to the existing Markham Power-to-Gas facility built by Enbridge and Cummins in 2018 to allow it to store surplus electricity as pure hydrogen until needed. The project will eliminate up to 117 tons of carbon dioxide emissions annually, without impacting the market cost of natural gas. “Zero-carbon hydrogen is now playing a role in Ontario’s shift to lower-carbon, sustainable energy solutions and is an important example of the investments Enbridge Gas is making across multiple markets to green the natural gas grid while continuing to meet the demand for safe, reliable and affordable energy,” says Cynthia Hansen, executive vice president, and president, gas distribution and storage, for Enbridge.
enbridgegas.com/hydrogen
Hydrogen can be blended into Enbridge’s 145,000 km. natural gas system.

Facts & Figures
• On October 29, 2020, the Ontario Energy Board approved an application by Enbridge Gas for a project to leverage the Markham Power-to-Gas facility in order to pilot the blending of renewable hydrogen gas into the existing natural gas network, reducing greenhouse gas emissions. • Through this pilot project, Enbridge Gas will initially provide a maximum hydrogen blended content of up to two per cent by volume of the natural gas supplied to approximately 3,600 customers in Markham, ON in
Q3-2021, eliminating up to 117 tons of CO2 annually from the atmosphere. • The pilot project will not impact the standard market cost of natural gas. • The hydrogen-blending project construction cost was $5.2M. • The Markham Power-to-Gas facility was commissioned in 2018 through a partnership between Enbridge Gas and
Cummins Inc., which acquired Hydrogenics in 2019, with support from the Province of Ontario. Since then, the facility has provided regulation services to the IESO to help balance electricity supply and demand, and ensure system reliability. • The plant has also proven its potential as a solution to the challenge of storing the province’s surplus electrical energy using Enbridge’s existing natural gas pipeline infrastructure or in the form of pure hydrogen, which can later be reconverted back to electricity.
For more information on blending hydrogen, see Jonathon Harp’s article Is hydrogen entering the NG mix? in Mechanical Business March 2021 at mechanicalbusiness.com. Harp also addressed hydrogen and electrification in Mechanical Business January/February 2022, p66.
THE CRITERIA FOR SUCCESS IN DELIVERING BC’S LARGEST SECONDARY SCHOOL
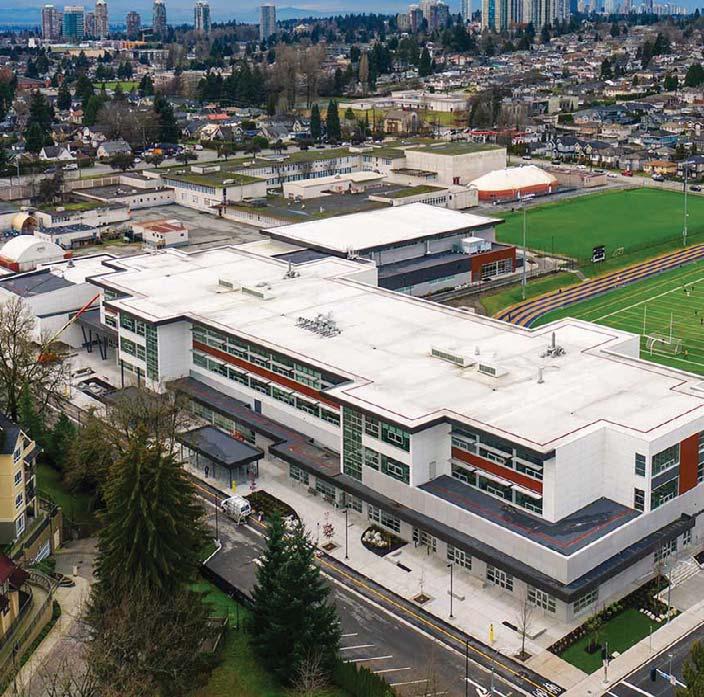
ABLE CONSTRUCTION MANAGEMENT, QUICK RESPONSE TO EMERGING ISSUES, AND ITEM-BY-ITEM PROBLEM-SOLVING GET PROJECT OVER FINISH LINE. New Westminster Secondary officially opened to students in January 2021.
In addition to the standard school attributes, it has a robotics facility, a three-court gymnasium and a theatre.
In 2017, Graham Group was selected as the design-build provider to replace the City of New Westminster’s 70-year-old high school with a state-of-the-art facility for 1,900 students and 200 staff. In addition to managing the project, Graham executed the concrete work and the general carpentry with its own forces.
At the time, the biggest construction-related challenge in BC’s Lower Mainland was the scarcity of trades due to the hot building market. But what was regarded as manageable for an experienced builder delivering a large and richly programed project, would soon spiral into labour shortages, construction slowdowns, sub-contractor interruptions and murky supply-chain disruptions − all brought about by the COVID-19 pandemic. Still, New Westminster Secondary officially opened to students in January 2021.
Deliverance from the effects of COVID-19 was not brought about by any silver bullet. There was no swinging for the fences. Instead, explains Justin Marchiel, Graham’s senior project manager on the three-and-a-half yearlong project, it was more like a game of inches. Keeping the project from bogging down and getting it over the finish line on-budget and to its revised deadline, says Marchiel, was accomplished through able construction management, quick response to emerging issues and item-by-item problem-solving.
KEY ELEMENTS FOR SUCCESS:

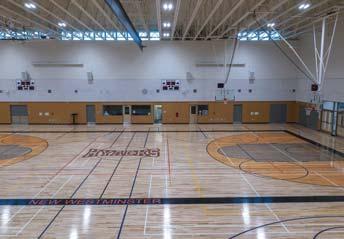

Experience in designbuild contracts
The project’s complexity came not from size or physical layout but its diversity of features − “program” in industry terms. The client and owner had laid out their many needs and wants in a statement of requirements and an “indicative design” document. This required, for example, complicated wiring to support a network of devices and range of equipment – everything from woodworking tools and dust extraction, to theatre lighting and IT networking – as well as numerous wall finishes.
Graham’s experience with large, complex projects and sophisticated contracting models such as designbuild, and its access to top-flight partners − in this case KMBR Architects and Planners – met the foundational criterion for project success.
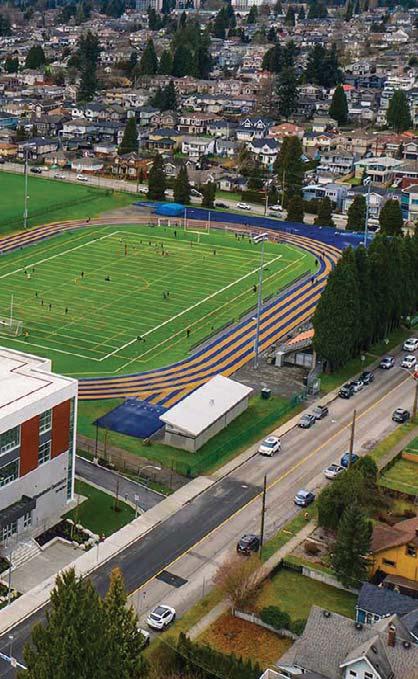
After the qualifying round organized by Infrastructure BC, a competitive field of proponents submitted detailed proposals that met the statement of requirements, including an initial design, and Graham was awarded the project. Division 15 Mechanical Ltd. in Richmond, BC was later selected as mechanical contractor on the $78.8-million project.
“Recognizing potential obstacles at the design stage and solving them on paper is a far better way of doing things than having to go through contortions to develop innovative work-arounds during execution,” is how Marchiel puts it. Because it places a project’s architecture/design/engineering provider and the construction contractor on the same team, the design-build contract model opens a path to avoid “constructability” issues stemming from design elements that are naïve, impractical or too costly. Graham spent a lot of time on acoustics with trial assemblies, building test walls between classrooms several different ways to ensure walls that are high performing acoustically.
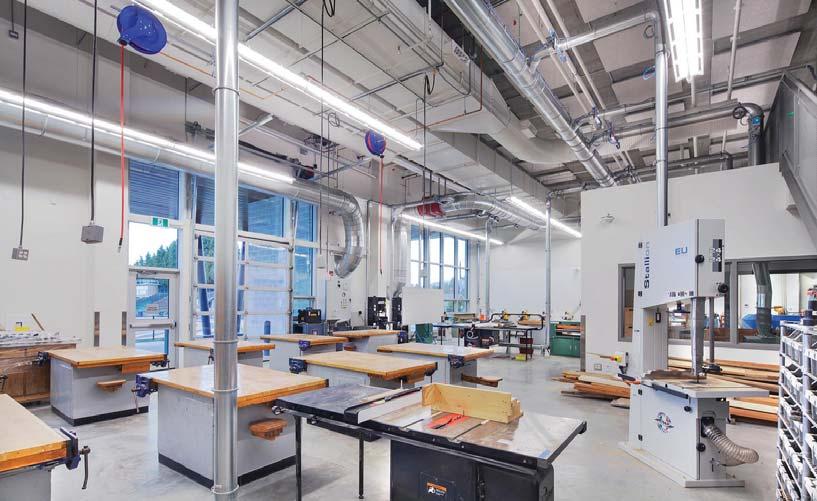
Operating flexibility
Graham knew BC’s hot construction market required particular attentiveness to managing trades and subcontractors, making the most of availabilities, paying immediate attention to delays and minimizing the ripple effect on other trades. Accordingly, Graham deployed more management resources to the site than usual. After COVID descended, even more would be needed.
“After the challenges of lining up and scheduling trades, we were finally underway and had established good momentum, and then the pandemic hit. Things either shut down or slowed down. Some companies shut down, and some workers were no longer available,” recalls Marchiel.
Graham responded by maintaining the extra resources brought in earlier. “We broke the building down into smaller pieces, and deployed sector-by-sector project managers and superintendents,” says Marchiel. “One each for the exterior, for the main floor/gymnasium, and for the upper floors.”
The result, he says, was that “they were able to spend time really focusing and dealing directly with the details. This allowed the trades to deal with someone directly, so that we could identify emerging problems early on and manage them more swiftly and in detail.”
Following all of this, recalls Marchiel, “Then the supply-chain issues sprang up. How do we deal with not having writeable surfaces for the classroom walls, or specialized wall finishes? Audio components? Kitchen equipment? Any number of items were suddenly not available when we actually needed it. Our writeable surfaces were coming from China and we were unsure when they would actually show up.”
Such problems have brought thousands of construction projects and renovations to a virtual standstill. Determined that New Westminster Secondary wouldn’t be one, Marchiel says the team decided “to finish all the physical systems, put all the switches and wall plates on, test and prove the systems, and then when the wall finishes finally showed up, take the plates off again, finish the walls, and replate everything.” In the end, the original writeable surfaces were replaced with alternate ones. “But at least we knew the building would work,” notes Marchiel.
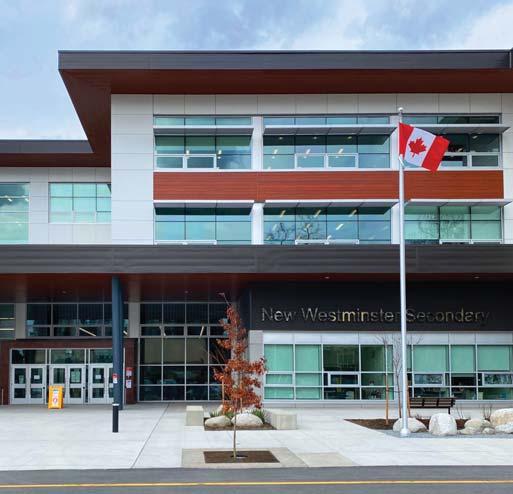
Graham upgraded the fibre cement siding to phenolic panels, and worked with its concrete partner to develop a thin lightweight concrete panel.
The end result
By summer 2020 it was clear the coming school year would not be a normal one and the two sides agreed upon a revised opening of January 2021. The largest high school ever built in BC meets LEED Gold standards, covers 236,000 sq. ft. plus a separate IT and maintenance building serving the whole school district. LEED-related systems include energy-efficient boilers and HVAC systems, glazing on all exterior glass with heat-control shutters, water conservation measures, use of natural light and LED options. The building’s look clearly takes inspiration from West Coast architectural styles, while optimizing the use of glazing. New Westminster Secondary School holds an 18,500-sq.-ft. gymnasium, 272-seat theatre plus a mini or “black box” theatre, full commercial kitchen called the “servery,” band/choir/recording studios, dedicated dance room, fully equipped tech-ed and shop spaces, eight science rooms including an engineering lab, 60 general classrooms, many multipurpose/flexible learning spaces, a wellness centre, welcoming centre and an Indigenous Friendship Centre. “It’s always a wonderful experience, after ‘living’ a project for several years, and you’ve learned every last detail, all the ins and outs, and then to have people walk into the finished facility and see their eyes get big, them looking every which way and expressing awe at how great it turned out, how awesome it is, that’s very gratifying,” says Marchiel.

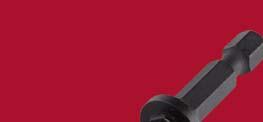
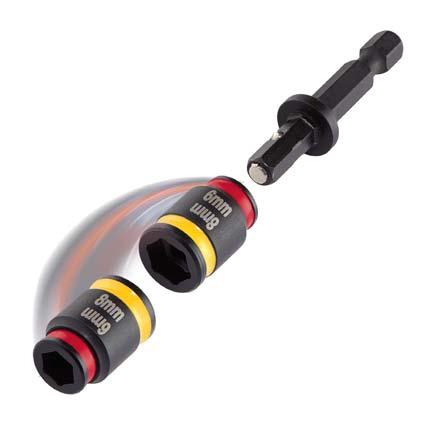
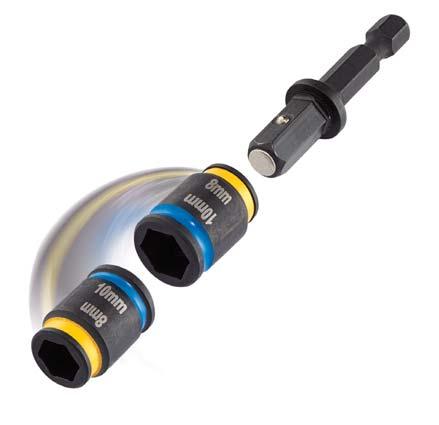
The Real Difference. METRIC
CLEANABLE, REVERSIBLE, MAGNETIC HEX DRIVERS
U.S. Patent No. 10,328,554
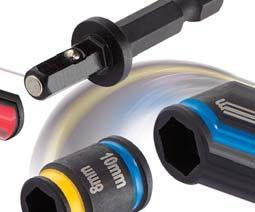
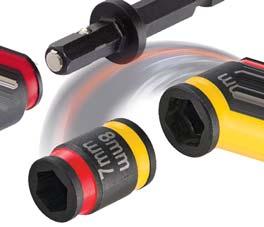
3 Metric Size Variations! 3 Met
6/8 mm, 7/8 mm, and 8/10 mm C-RHEX® hex drivers.
Designed with a slim profile to gain easier access in tight spaces. Available in 2 in., 4 in., and 6 in. lengths.
Malco Products, SBC • Annandale, MN. U.S.A. • www.malcotools.com • ©2021
By Zack Oostrom
Zack Oostrom is a project manager and estimator with Greyter Water Systems. He can be reached at zoostrom@greyter.com.
CREATING WATER-EFFICIENT COMMUNITIES
Water reuse and stormwater management are rapidly becoming a sector of interest in residential, commercial and industrial development. Everybody wins when water-efficient communities are created. Municipalities can reduce fresh water demands and reduce the load on aging infrastructure while meeting conservation targets and maintaining growth security. Developers, builders and engineers can meet local code and sustainability checklists requirements, receive expedited permits, and achieve density bonuses. Building owners can reduce their water consumption cost while committing to environmental mitigation and sustainability. Many cities in North America rely on a combined sanitary-storm sewer system. As the demand on the aging infrastructure rises and large storms become more frequent, overflows and flooding cause erosion, contamination of rivers and lakes, and contribute to the disruptions of municipal water treatment plants. Flooding ultimately has a devastating impact on a city’s infrastructure and its communities. Stormwater recycling is one of many water-efficient strategies that increases water supply while reducing the risk of flooding. Stormwater management looks to mitigate these extenuating pressures on the municipal storm infrastructure. Reused and reclaimed water increases water availability as an alternative to freshwater, and offers opportunities for stormwater integrated design solutions.
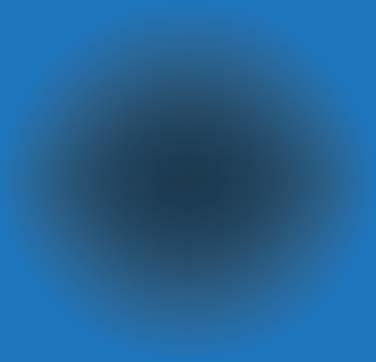
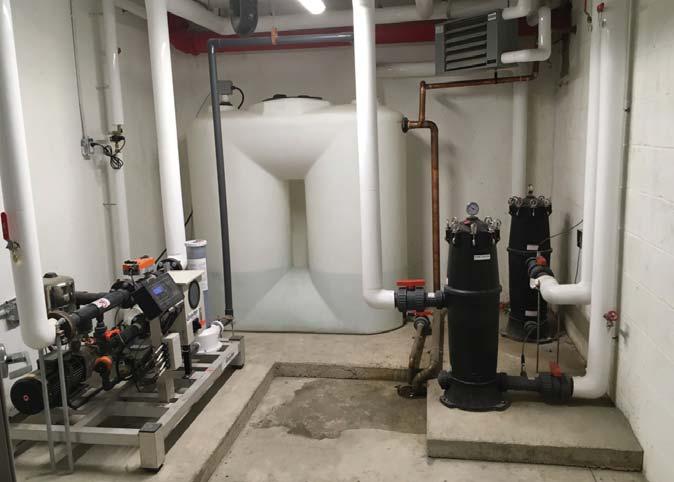
Commercial building water system solution that collects, filters and disinfects reclaimed stormwater for non-potable purposes such as toilet flushing and irrigation is expected to save Platform Condos in Toronto, ON an average of 15,000 L of fresh water each month.
When considering water reuse or rainwater harvesting, best practice would prescribe beginning with identifying the drivers and parameters of the project. Drivers highlight the intentions of the water reclamation project. Examples are stormwater balancing, freshwater conservation, sanitary waste reduction, LEED certification credits, funding incentives, and meeting municipal code requirements. Stormwater balancing reduces the load on the storm sewer during a heavy storm event. Freshwater conservation can be achieved by reducing the overall volume of freshwater demands by introducing an alternative non-potable water source. Sanitary waste reduction targets can be met by treating greywater onsite and reusing it for nonpotable applications. Water reuse parameters include the potential sources and uses for non-potable water (NPW). Potential sources of NPW include rainwater, stormwater, foundation drainage, groundwater, surface water, greywater, and blackwater. Potential uses for reclaimed water are toilet flushing, trap seal primers, spray irrigation, subsurface/drip irrigation, car washes, cooling towers, and ultimately potable water. From a technical perspective, it’s possible to treat water from all these sources to a level suitable for any of the above uses. However, this may not be feasible from a practical perspective. Equipment and operating expenses, health and safety provisions, and regulatory limits pose challenges to many strategies making them less than appealing and economically undesirable.
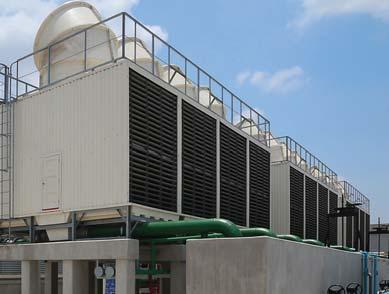
System design
After identifying the drivers and parameters of a project, the next step is to design a system that makes the best sense. Considerations include source water quality, volume, and frequency of replenishment while determining treatment methods that produce desired end-use water quality, flow rates, and pressure requirements for point of connection use. Water storage capacity and water availability is calculated while conforming to regulatory requirements, permits, and agreements. Maintenance requirements are also considered to protect the capital investment of the equipment and most importantly, safety. Health risk and potential exposure risks for human contact are taken very seriously. Treatment method considerations are determined by source water quality and the purpose of end-use. For example, rainwater from a clean roof only requires minimal treatment when used for subsurface irrigation but would require multiple barriers of disinfection if supplied to residential
Figure 1: CSA B805 end use tier approach 1 to 4 Cooling towers by design use significant quantities of water making the application ideal for reclaimed water use.
Codes and Standards to reference
Navigating the pitfalls and challenges of the various reclaimed water sources and uses with accompanying regulatory requirements may be challenging but there are resources available: • Canadian guidelines have been produced by the federal and provincial governments. The Federal
Government published Canadian Guidelines for Domestic Reclaimed Water for Use in Toilet and
Urinal Flushing in 2010. • CSA B128.1 and CSA B128.2 outline the design and installation of non-potable water systems, maintenance, and field testing. • CSA B128.3 outlines the performance requirements of non-potable water re-use systems. • CSA B805 addresses roof surface rainwater and stormwater, that is rainwater that has come in contact with the ground or a green roof. The term “rainwater harvesting” is used generically in this standard and can refer to the harvesting of either roof runoff or stormwater runoff. • Ontario’s Building Code OBC Part 7.7.1.1. Non-
Potable Connections to a plumbing system lists safety precautions to prevent cross-contamination of non-potable and potable water sources.



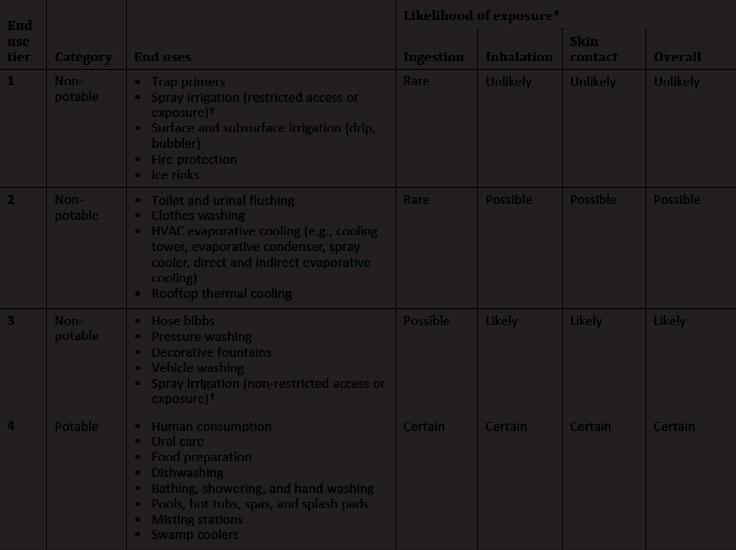
toilet flushing, car washes, and NPW hose bibs. As source water quality decreases, an increase in treatment equipment is required to produce a level of water quality suitable for the end-user. Reducing operations and maintenance costs while providing high standards of water quality will contribute to the quality and effective use of the water management system. The complexities of possible water reuse and reclamation sources and uses are simplified by identifying specific drivers while finding opportunities within the regulatory parameters. With increased water security and flood protection, communities can thrive on dividends of sustainable design. Municipalities, developers, building owners, tenants, and operators all have a role in building a sustainable and water-efficient community. Together, we all win.