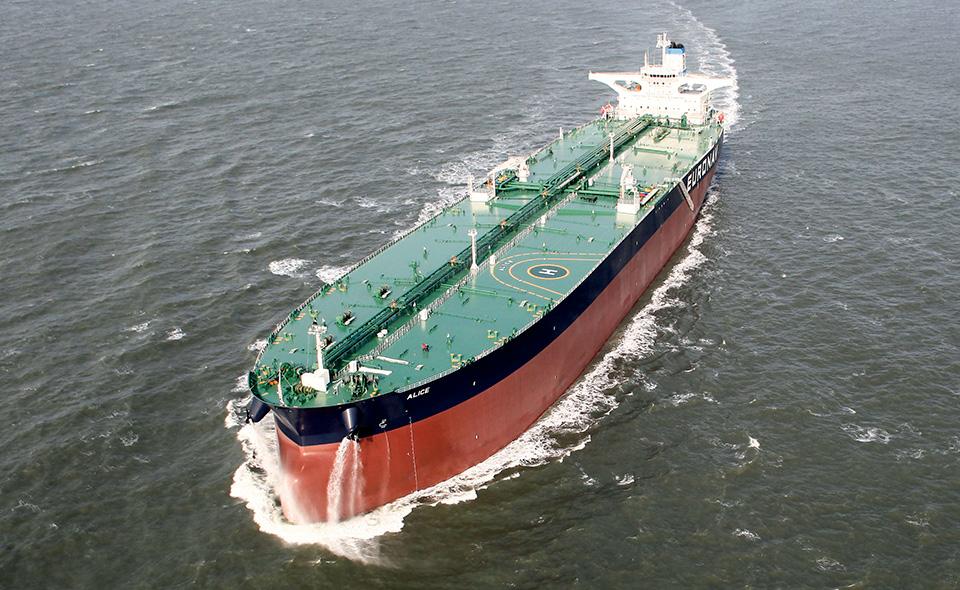
21 minute read
Options for VLCC owners
EEXI COMPLIANCE: CHOICE OF OPTIONS FOR VLCC OWNERS
The expected entry into force of EEXI rules in 2023 will aff ect the VLCC sector signifi cantly and may accelerate the disposal of older tonnage, Kari Reinikainen hears
From a technical point of view, owners have many options in principle to achieve the 10%+ emissions reductions required to make their vessels compliant. However, the commercial considerations that aff ect decision making are extensive, particularly as the Energy Effi ciency Existing Ship Index (EEXI) regulations are planned to take eff ect from the start of 2023, a year after the Ballast Water Management Convention.
There is a wide range of options available for VLCC owners to comply planned EEXI legislation and a lot depends on the strategic choices of the owner, said Andreas Wiesmann, General Manager of Global Sales for 2-Stroke Engine Services, Piet van Mierlo, Team Leader of Propellers Product team and Stavros Zacharias, Global Sales Development General Manager for 2-stroke Services at Wärtsilä, the Finnish technology group.
The first choice an owner needs to make whether to retain the design speed of its ships or to opt for a lower output of main engine. The latter option usually requires the replacement of the propeller and rudder, which often means the engine has to be de-rated, as the load curve is no longer optimal. A number of energy saving solutions can be installed as well.
Air lubrication can be interesting on ballast voyages, but when laden the deep draft of a VLCC means that a lot of power would be needed to produce the necessary pressure for the system to work. However, this can be done by using the main engine, which simplifies matters and reduces the cost.
The installation of wind-assisted propulsion would be viable from a technical point of view and would not reduce the cargo capacity of a ship. However, the capital cost of
Credit: Euronav
investing in such solutions reduces its attractiveness: a VLCC would require four Flettner rotors, for example.
Capex considerations also apply to the conversion of an existing VLCC to dual fuel operation, in addition to the work involved in installing an LNG fuel tank and the fuel gas supply system and related equipment. Locating the fuel tank on deck minimises the impact of cargo capacity.
Such a conversion represents the best option to future proof a vessel, as it would also allow the use of other fuels, such as methanol or ammonia. But it is difficult to assess which fuels are likely to be the best ones towards the end of the lifespan of a vessel: advances in technology and potential changes in legislation means this may change in future.
Nikolaj Peter Lemb Larsen, Chief Naval Architect, Hydrodynamics and Aerodynamics at Force Technology in Denmark said that by de-rating the main engine, replacing the rudder and propeller plus installation of energy saving devices it is possible to reduce the energy consumption of a VLCC by some 10% to 15%, although there can be variations between vessels. The work can be carried out in stages to spread the cost over a number of years if the owner prefers it this way, but then the savings will also emerge gradually as a result.
PRESSURES ON AGEING VLCCS
The planned EEXI regulations mean that a VLCC in operation today would have to meet a 15% reduction factor relative to the EEDI reference line, which could be quite a task for existing vessels, especially the largest vessel, said Catrine Vestereng, Business Director Tankers at DNV GL - Maritime.
8 Advances in
engine technology and vessel design have driven improvements in the fuel effi ciency of modern VLCCs, such as Euronav’s 299,320dwt Alice (pictured)
Engine Power Limitation or Shaft Power Limitation are the most likely first steps, she suggests, as well as potentially installing energy saving devices.
A complicating factor could be the recent entry into force of the Ballast Water Management Convention, she suggests. Many of the vessels currently in the fleet are expected to have to install treatment systems in the next several years - an additional investment for vessels which might already find it hard to compete with the next tonnage coming into the market. “If you look at more modern VLCCs, that have been designed to hit EEDI targets, they are very different, they have hull forms that have been highly optimized for both calm water and waves and are much more efficient than vessels that are 10-15 years older,” she told The Motorship. “Facing this double hit, owners may then look to invest in new tonnage, and we could see an increase in scrapping.”
The requirements to meet the SEEMP (Ship Energy Efficiency Management Plan), looked like they would be more easily obtainable, said Vestereng. “We have data that suggests recently delivered VLCCs 23MW of installed power are operating for 90% of the time, significantly below that output, usually requiring only 14MW. This means that speed reduction, which would be a necessary condition of limiting engine power, as well operational efficiency measures, and deployment of some new efficiency enhancing technologies, could see younger vessels meet these requirements.”
“It’s not just regulations that are sharpening the industry’s focus on efficiency,” adds Vestereng. “Charterers are increasingly looking to impose their own emissions requirements. For example, the recently launched SeaCargo Charter which includes Total, Shell, Equinor, and Cargil, or the Poseidon Principles, and this trend will only ramp up the pressure on older vessels.”
Time would tell on which solutions would work best to help VLCCs meet the requirements, not only from a technical perspective but commercially, said Vestereng. “Especially with some of the new energy saving measures, such as windassisted propulsion systems (wings, sails, rotors, etc.), waste heat recovery systems, or the use of shaft generators, we will have to see how the promised gains in efficiency translate in real world operation. And how commercial factors play into the payback times for these investments. Of course, as the regulations continues to tighten, notably the EEDI, moving to LNG as a ship fuel or other alternatives, for VLCC newbuilds may be an option that becomes more attractive.”
Oyvind Endresen, Environmental Consultant at DNV GL, added that a DNV GL study had shown that the most advantageous fuel of today for a VLCC may not be the same throughout its lifespan. The use of VLSFO or HSFO with scrubbers both result in a major carbon risk in about 2040. In the case of LNG, high capital cost is a disadvantage today, but together with energy saving investment its position should improve in the next two decades.
However, in about 2040 other types of fuel may provide competition. The study concluded that a VLCC should be able to switch to other fuel over its lifetime. If it lacks this flexibility, it may become a stranded asset that has to be scrapped prematurely.
SHIPPING NEEDS TRANSPARENCY
The fuel efficiency of VLCCs has improved significantly over the years. Today one litre of fuel oil burned by a VLCC tanker carries a tonne of crude more than 2,800 km - this is more than twice the figure of 20 years ago, says Euronav, the world’s largest independent VLCC owner, on its website. Yet shipping’s efforts to improve its performance has gone largely unnoticed.
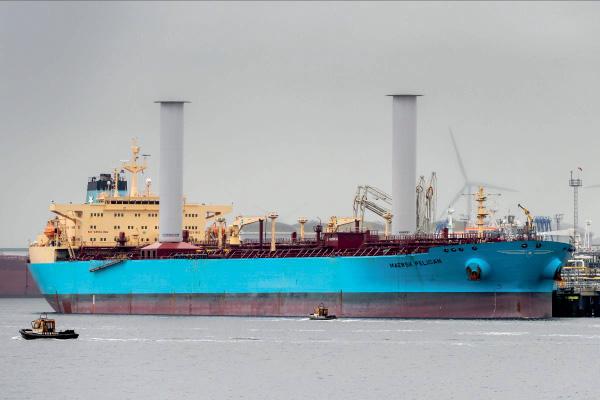
Brian Gallagher, Head of Investor Relations and Communications at the Antwerp-listed company said that shipping itself is partly to blame for this. “Shipping does not have a strong single voice. Instead, most shipping sectors are highly fragmented and it also has many different categories of business, which makes things difficult to have focus.”
However, bearing that in mind, he said the industry should tackle three concerns. Firstly, it should have proper transparency regarding governance and secondly, it should have its proper seat at the table around which decisions regarding it are made. “You cannot complain and whine if you do not agree to broad disclosure yourself,” he noted. Finally, oil traders and other interested parties should also have their say, so that all vested interests are presented in the planning of new legislation. “There is nothing wrong with that, everyone’s viewpoint should be presented at the table to allow a negotiated settlement,” he said.
As far as EEXI is concerned, the company whose fleet accounts for 5% of all the VLCCs in the world, Gallagher said as it now stands, it offers a very clear and usable pathway forward, although owners with older fleets might find bigger challenges ahead as a result. Euronav’s preferred option to comply with EEXI will focus on adjusting the power of each vessel to therefore adjust the emissions along with slower steaming when on ballast legs.
Challenges in the application of EEXI will be technical, he continued, such as the appropriate power-weight ratios of each vessel. However, it also means that the tanker industry must have entry to the rooms in which decisions regarding these are made: engagement is the key. “Let’s get our hands dirty,” he noted.
Accelerated scrapping of VLCCs is the logical conclusion of EEXI, but of course the decision to scrap has multiple inputs and older tonnage ownership is more fragmented than the overall fleet average. It is almost entirely in private
8 A one-year trial
of Norsepower’s Rotor Sails onboard Maersk Tankers’ LR2 product tanker Maersk Pelican resulted in fuel savings of 8.2%
8 Catrine Vestereng,
Business Director Tankers at DNV GL

Credit: DNV GL
hands, making visibility and disclosure more difficult to follow. “But yes EEXI is a numerical framework indicating an emissions “score” which alongside other factors will add to the pressure to exit,” he said.
The planned legislation has also its critics. The guidelines for EEXI are not yet fully developed and this poses problems for owners as they are not confident about the details, said Hans Otto Holmegaard Kristensen, owner of HOK Marineconsult. The key challenge is to show that the reduction in greenhouse gas (GHG) emissions from a particular ship really is the result of it having become more energy efficient.
Kristensen has worked with Denmark’s shipowners’ association Danish Shipping and has also worked together with the country’s maritime administration since the early days of the planning of EEDI and EEXI.
Delegates at the IMO want indicators of improved performance and one of the indicators is the carbon intensity indicator, CII, has been chosen for this purpose. However, for ships like VLCCs the actual performance of the ship could be heavily influenced by e.g. freight markets and the weather conditions the ship encounters.
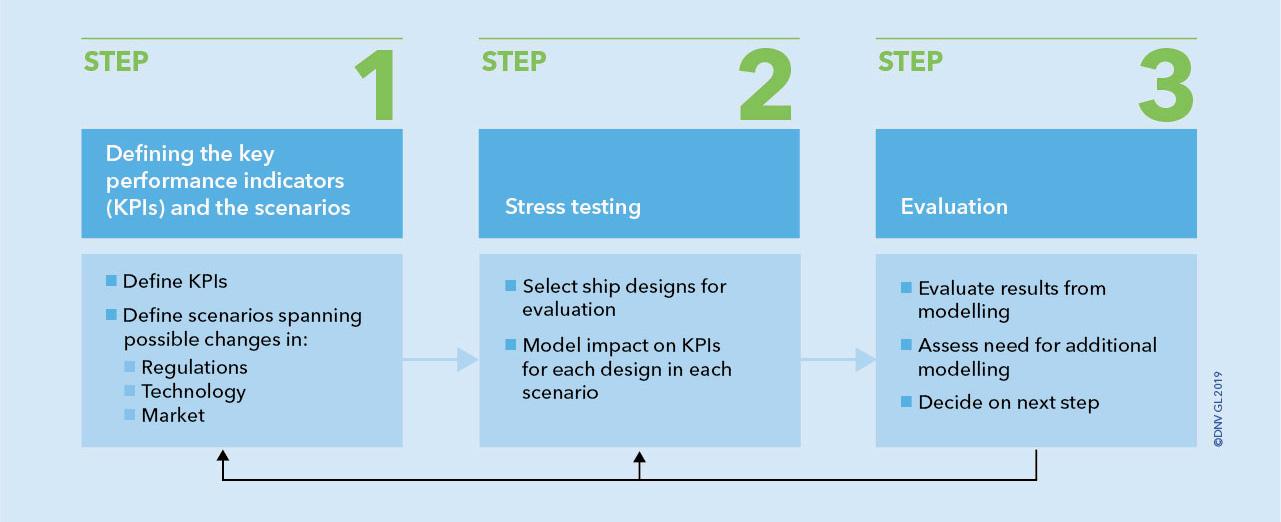

POTENTIAL UNINTENDED CONSEQUENCES
“Let’s assume the freight markets will be very bad in 2021 as a result of Covid-19. There will be lots of ballast voyages and voyages with part cargo. Fuel consumption will be low as a result,” Kristensen said. When this is divided by the maximum deadweight tonnage of the vessel, the ship’s performance looks very good on paper.
Conversely, in a strong market ballast voyages and part cargoes give way to fully laden voyages. With deep draft, the fuel consumption of the ship increases fuel consump considerably. Ships like VLCCs tend to considerably slow steam when freight markets are slow steam weak and sail faster to pick up cargoes weak and when they pay well. “This leads to the when they paradox that a positive paradox financial situation for owners could lead to a bad situation f reading of the indicator,” he told reading o The Motorship. Motorship. Reducing the speed of ships by e.g. deReducing rating the engines can tackle the problem rating the eng of higher speeds when freight pays of high well, but it also creates a few we new ones. “Wind and wave resistance account for 20% of total resistance at full speed, but this figure rises to 60% at slow speeds,” he continued.
Credit: DNV GL
The “hotel load” of ships that is needed to run everything from cooling pumps and other types of pumps, lights to air conditioning and galley equipment is remarkably constant and should speed be lowered, then power to cater for hotel load must be generated e.g. by using auxiliaries. “The effective benefit of lower speeds will be lower than the 35% indicated by theoretical calculations - perhaps as low as 20% or 25%,” he pointed out, when a relatively larger sea margin is used in the performance calculations to show the gain by a speed reduction.
To rectify the problem in the proposed EEXI legislation, Kristensen said the energy consumption should be divided by the amount of cargo the ship actually has carried - and not by its maximum deadweight - and the nautical miles to has travelled, i.e. the energy efficiency operational index (EEOI) value should be used. ”The problem however is that in the official IMO reporting system this is not a part of the data reporting. Only in the EU MRV (monitoring, reporting and verification) recording system EEOI is included in the reported data, but MRV data are only given for ships sailing in EU waters,” he said.
The proposed EEXI legislation may accelerate the removal of ageing VLCCs from the market if their owners consider that these vessels will be uneconomical to operate under these rules. “If owners find that they are commercially unable to operate these vessels feasibly, then yes,” said Lars Robert Pedersen, Deputy Secretary General of BIMCO in Denmark. As so often is the case in shipping, there are many variables that can affect such decisions, the state of freight markets being a significant factor at a given time.
BIMCO takes a positive view regarding regulation that aims to protect the environment or improve safety of shipping and Pedersen said EEXI does not appear to be anything revolutionary in itself. However, the extent of reductions in installed power and vessel speeds may exceed some owners’ preferences and for VLCCs, these reductions would be at the upper end of the scale.
Many owners will carry out modification work on their vessels to comply with EEXI, but Pedersen this is unlikely to lead to shortages of shipyard capacity as this work can often be carried out in stages. Again, the state of the freight markets would also direct owners’ decisions regarding capital expenditure at a given time.
Pedersen also urged the industry to engage in the work regarding regulation. “The IMO has the technical expertise, which the delegates of the member states often do not have. The outside world often sees shipping as an industry that is not happy with regulation. However, you need to work with it to have influence, you need to engage,” he concluded.
8 DNV-GL’s
framework for future testing ships identifi ed a number of variables to consider when future proofi ng a VLCC
8 Lars Robert
Pedersen, Deputy Secretary General of BIMCO
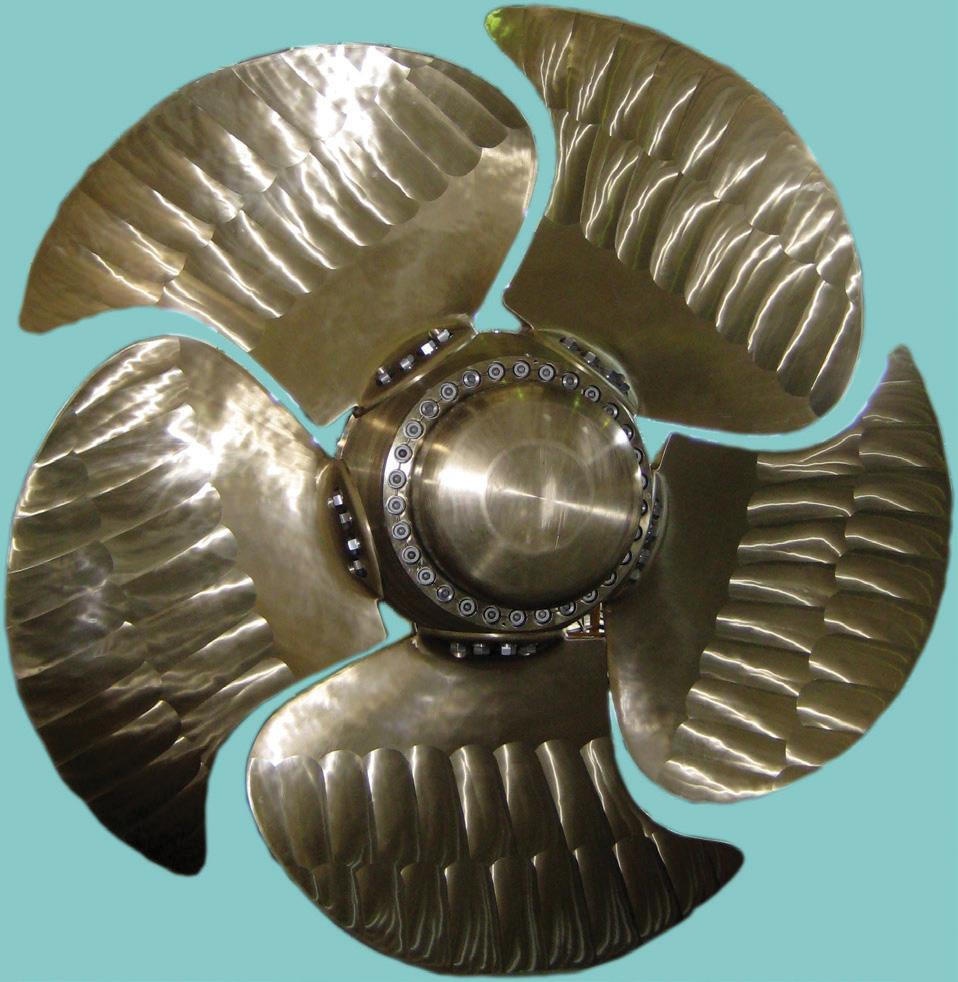
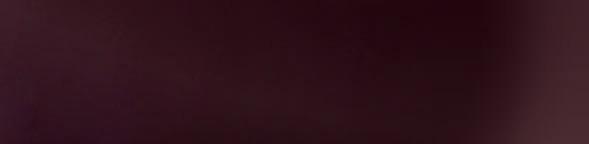

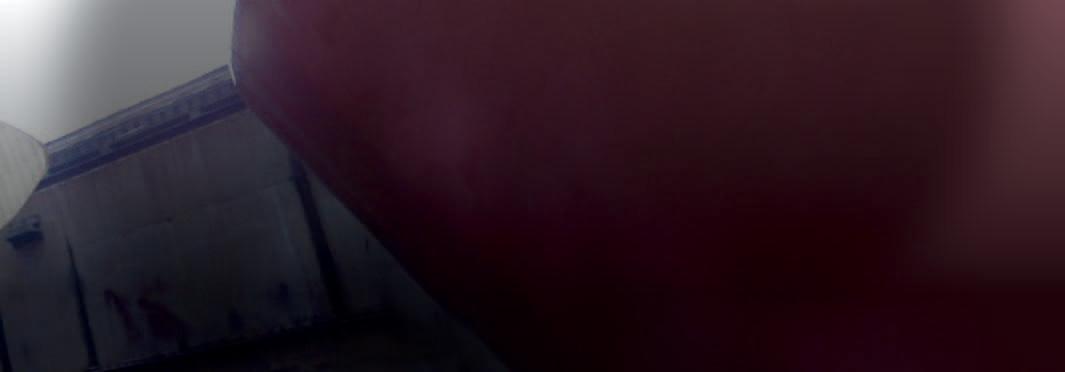
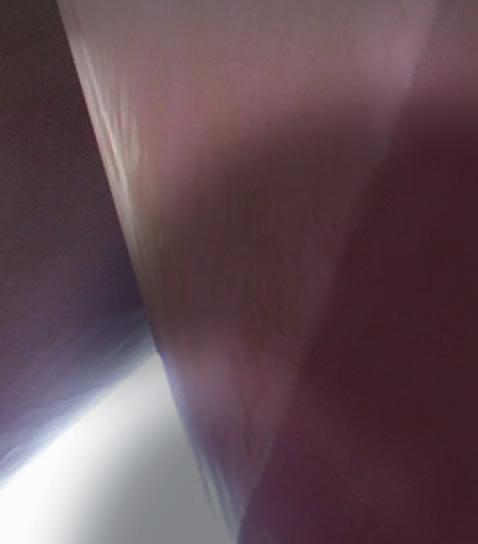


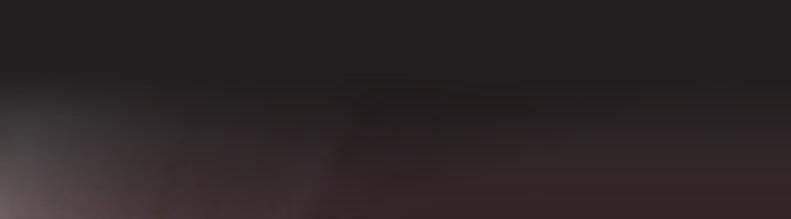
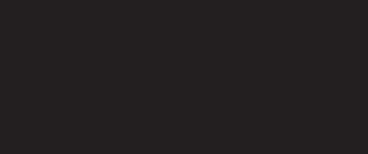
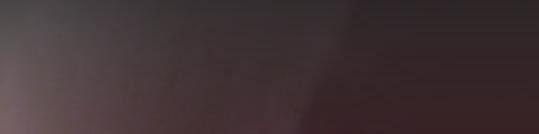

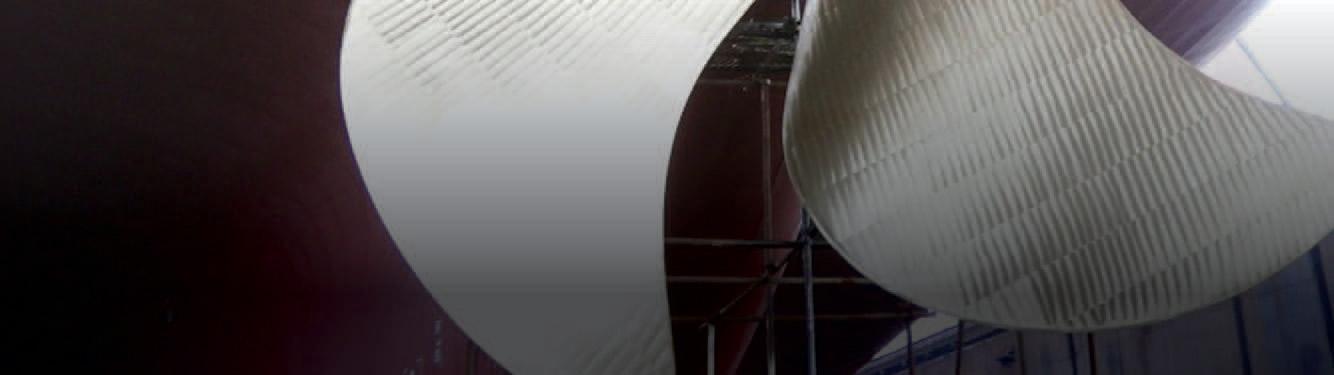

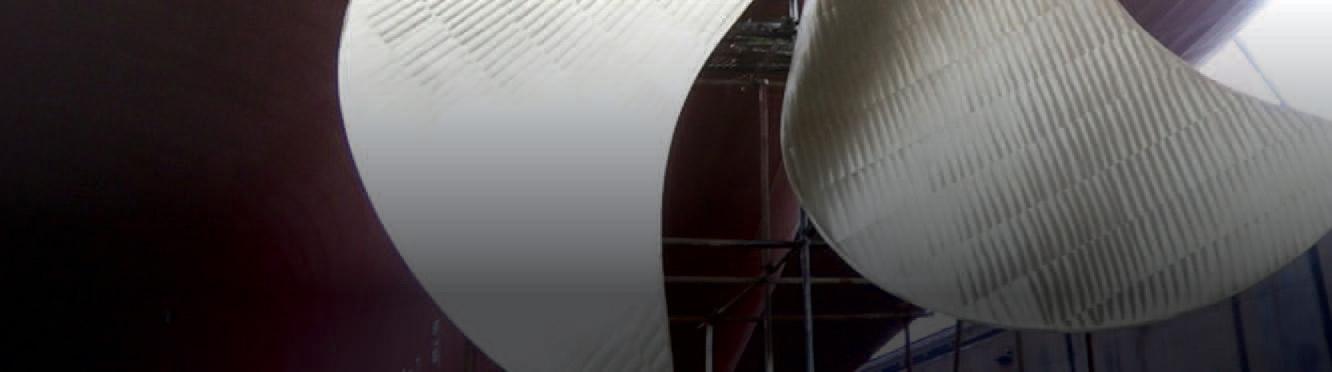
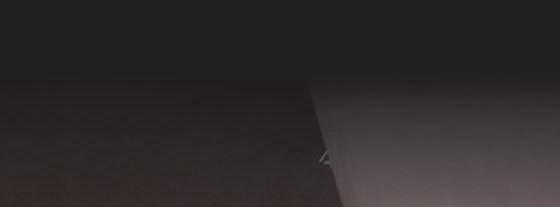


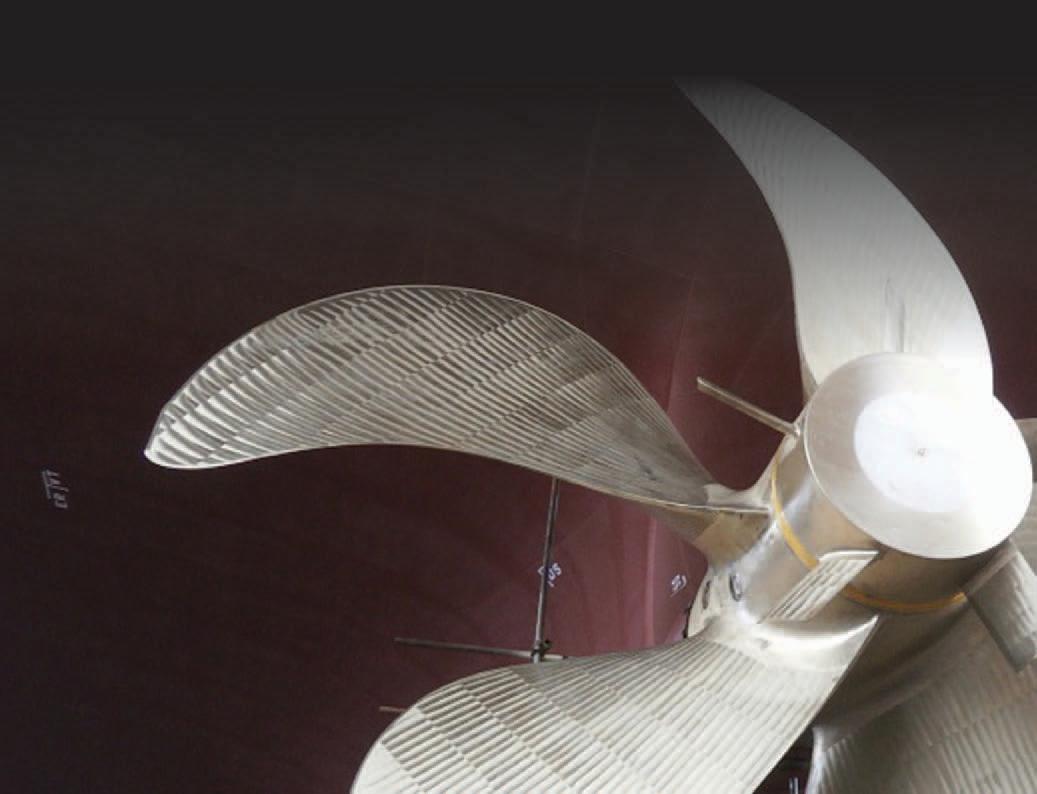
ORC INSTALLATION ECONOMICS DEPEND ON KIT TRADE-OFFS
While the payback period for Organic Rankine Cycle (ORC) systems can be below 10 years, the size of key components heavily influences the economics for smaller vessels
LNG-fuelled ships off er extra potential for waste heat recovery compared to ships running on heavy fuel oil, as there is a reduced need for fuel pre-heating with LNG and therefore a reduced requirement for waste heat from engine exhaust gases to be used to generate service steam. This extra potential was examined in a study undertaken by DTU Mechanical Engineering, MAN Energy Solutions, Fjord Line, Alfa Laval and Lloyd’s Register Marine.
The researchers examined potential heat sources and sinks for a vessel powered by a 7G95ME-C9.5 MAN Energy Solutions dual fuel two-stroke engine with low pressure selective catalytic reduction tuning. Their study considered the economics of four theoretical configurations: main engine exhaust gas and jacket cooling water as heat sources and seawater or LNG pre-heating as the heat sink and jacket cooling water as the only heat source and seawater or LNG Pre-heating as the heat sink.
The combination of exhaust gas and seawater was the optimal configuration, leading to fuel savings of 6.9% if the electricity was used for propulsion and 8.5% if used for auxiliary generators. The use of jacket cooling water provided fuel savings of under 1%. The use of LNG pre-heating as a heat sink resulted in similarly low savings, even when the estimated efficiency of using exhaust gases as a heat source reached 35%. This was attributed to the limited mass flow rate of the LNG that needs to be pre-heated.
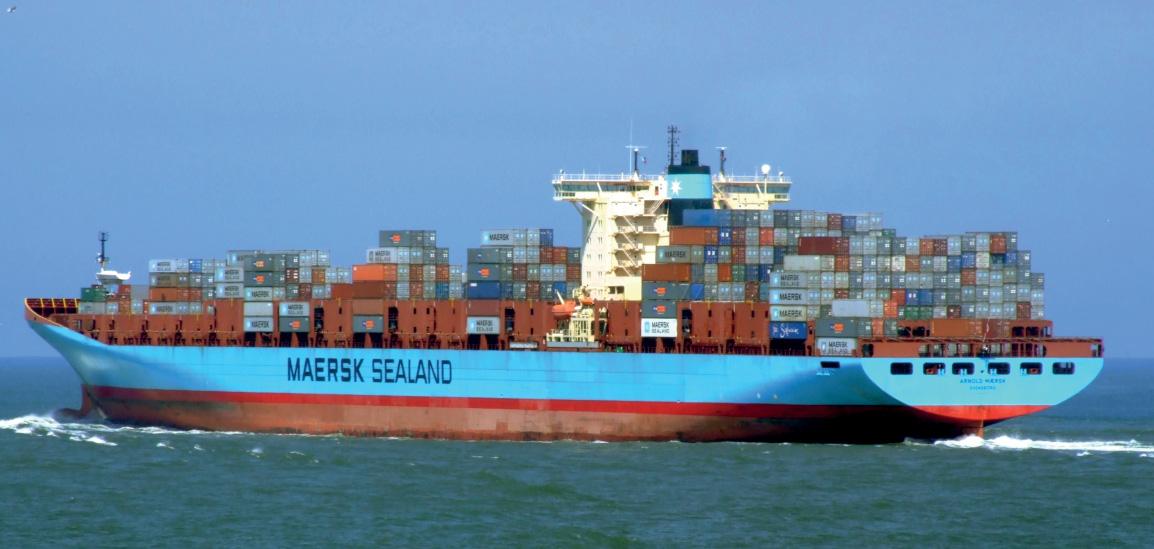
RETROFIT TRADE-OFFS
The performance of optimised ORC systems was then evaluated against the operating profile of a slow-steaming container ship operating in Tier II areas and a container feeder operating in Tier III areas. The container ship case study evaluated a 23,000kW MAN 6S80ME-C9.5-GI engine operating for 6,500 hours annually. The feeder case study evaluated a 10,500kW MAN 7S60E-C10.5-GI engine with an
Credit: Alfvan Beem/CC1.0
exhaust gas recirculation unit, operating for 4,380 hours annually. The ORC working fluid considered was cyclopentane.
The study predicts annual main engine fuel savings of 6.5% for the container ship and 8.4% for the feeder if the energy is used to replace that from an auxiliary generator. The payback for the ORC system on the container ship was six years and for the feeder it was nine years: for the feeder, the ORC’s boiler was divided in two so that one of the parts recovered heat from the exhaust gases recirculated in the EGR unit. This added to installation costs which were estimated at $1,784/ kW for the container ship and $2,542/kW for the feeder.
The study also considered options for retrofitting. The optimal ORC configuration for the container ship required a volume of 17m3 for the heat exchangers. Reducing this to 10m3 reduced fuel savings by 10%. For the feeder, the optimal ORC configuration required a volume of 13.5m3 for the heat exchangers. Reducing this to 7m3 reduced fuel savings by 13%.
BACK PRESSURE OPTIMISATION
The installation of an ORC unit on the exhaust line of a marine engine imposes an increase in the back pressure on the engine resulting in a decrease in engine performance and variation in the available waste heat. Further work conducted at DTU proposed a method for the optimal design for the systems based on performance maps for the engine and numerical models for the ORC unit and the waste heat recovery boiler.
For a hypothetical LNG-fuelled container ship, overall system fuel consumption can be reduced by 0.52 g/kWh to 1.45 g/kWh by allowing higher back pressure levels on the engine. For a fixed power output of the ORC system, the space requirement for the waste heat recovery boiler can be reduced by up to 35% when increasing the maximum allowed engine back pressure from 3kPa to 6kPa.
The work follows a number of earlier studies - including an
8 A Calnetix/MHI
jacket water ORC was fi tted to Arnold Maersk
onboard trial on a container ship. The 2016 installation of a 125kW Calnetix/Mitsubishi Heavy Industries Marine Machinery & Equipment (MHI) ORC system on the container ship Arnold Maersk proved the working concept for having an ORC using engine jacket water as a heat source. The system used heat of less than 100oC from the engine jacket water of the vessel’s Wärtsilä 12RTA96C engine.
The ship sailed through northern latitudes and equatorial regions, and the variation in seawater temperature had an impact on the power output of the ORC system, but modelling indicated that integrating ORC units within the service steam circuit could achieve payback periods of five to 10 years assuming 6,500 operating hours per year and that the electricity produced replaced that from an auxiliary generator.
The retrofit took about a month to complete and required cutting the ORC frame into pieces and then reassembling it in Ongoing research at Newcastle Research & Innovation
a space that had been designed to house an extra diesel generator. The ORC system took up approximately 9.2m x 2.7m x 4.4m and was accessible via two small hatches (1m x 2m).
The system installed on the Arnold Maersk included a newly-developed radial turbine from MHI integrated within a high-speed permanent magnet generator. The “Hydrocurrent” module requires no cooling or lubricating systems and does not require sealing from the external environment. MHI says the result is both compact and highly efficient.
NEW HYBRID MHI SOLUTION
The company is now developing MHI STAR - a hybrid Mitsubishi steam turbine and advanced organic Rankine cycle hybrid system targeted at LNG-fuelled vessels. For high sulphur fuel oil, heat from engine exhaust gases is recovered within a limited temperature range to prevent boiler corrosion that can occur as a result of sulphuric acid formation. In contrast, as a low sulphur fuel, the use of LNG means that waste heat recovery boiler design is simplified, and the temperature range of recovered heat can be extended and exploited with greater efficiency by the two sub-systems in the hybrid configuration. The steam Rankine cycle can be optimised to boost efficiency at high engine loads, and the organic Rankine cycle system, taking advantage of MHI’s radial turbine technology, can be optimised to boost efficiency at lower loads.
Wide variations in engine load are generally considered sub-optimal for ORC systems. However, another study by researchers at Newcastle University examined the potential fuel savings for an 88.8-metre, 5,200dwt multi-purpose offshore support vessel operating 350 days a year. The vessel’s operating profile, carrying supplies to offshore rigs in Malaysia, meant that the four two-stroke Wärtsilä 6L26 engines burning marine gas oil were not operating at high load much of the time. The analysis included a range of operating modes including four engines running at 75% load, two engines running at 85%, 75% or 50% load, and one engine running at 50% or 25% load.
Four ORC system designs were considered: a simple system, the addition of a recuperator between the expander outlet and the evaporator inlet to improve thermal efficiency, a simple system with two heat sources (exhaust gas and engine cooling water) and a simple system with intermediate heating. The working fluids modelled were cyclopentane, n-heptane, n-octane, methanol and ethanol.
The researchers calculated annual fuel savings of between 5% and 9% for installation costs between $5,000/kW and $8,000/kW for a system with net work output between 90 kW to 165kW using engine exhaust gases as the heat source accounted for about 90% of the fuel savings. A simple system using methanol offered the shortest payback time - approximately 10 years with assumed fuel cost of $610/ton.
The cost of the systems varied by around 20%, with the system using a recuperator being the most expensive. However, the system with the recuperator offered the highest fuel savings at around 9%. The expander accounted for 60% to 70% of the total cost. The heat exchangers (evaporator, condenser, pre-heater and intermediate heater) each account for about 10%, and the fluid pumps accounted for less than 5%.
and seawater as the heat sink. Engine loads of 75% and 85% Institute in Singapore (NewRIIS) aims to create a modelbased system engineering methodology using the commercial off-the-shelf engineering program called Amesim from Siemens. The researchers aim to model the performance of ORC components such as heat exchangers and fluid machinery to optimise system performance, especially for ships that have a varying waste heat output due to their operational profile.
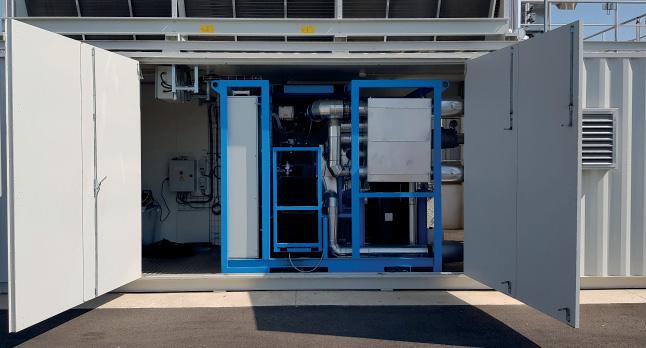
EFFECT OF ALCOHOL FUELS
Several other studies have evaluated different vessel types including a 2017 study where a 20kW system was installed on the fishing vessel Orizzonte, powered by a four-stroke engine. The system achieved estimated fuel savings of 5%. Equipment manufacturer Enogia says its patented hermetic, high-speed micro-turbine technology is the key to efficient heat recovery by the expander. The turbine blades and working fluids for its ORC modules are adapted to suit the specific waste heat temperature ranges onboard, and the system is compact and modular to facilitate installation. Fuel savings and payback time depend on the individual project.
New fuels are expected to change ORC economics, and a 2018 DTU study noted that alcohols improve combustion due to the presence of oxygen in their molecule, leading to a decrease in engine heat loss and exhaust gas temperature. The use of hydrogen as fuel could make it challenging to find the space to integrate an ORC onboard, as the storage tanks of compressed hydrogen require around six times more space than those of heavy fuel oil.
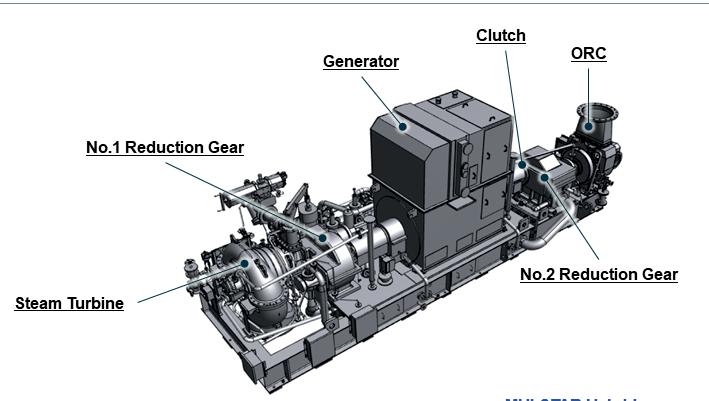
Credit: MHI 8 Equipment
manufacturer Enogia adapts its ORC modules to suit the specifi c waste heat temperature ranges onboard
8 Mitsubishi Heavy