
11 minute read
FiTS2 landmark
FIRST FITS2 IS FITTED INTO BULKCARRIER NEWBUILDING
The engine trials for the fi rst installation of ABB’s Flexible integrated Turbocharging System for Two-Stroke Engines (FiTS2) were carried out in May 2020
The trials in China had to be monitored remotely as Covid-19 restrictions prevented anyone from ABB or the engine designer WinGD attending the tests, explained Alexander Mutter, Senior manager, product management low-speed for ABB Turbocharging. “Nevertheless, we achieved very good results,” he told The Motorship.
The engine and its turbochargers are destined for a bulk carrier under construction at China’s Bohai shipyard for a Singapore-based shipowner Berge Bulk due to go into service in Q1 of 2021.
The tests were carried out at the yard on the ship’s WinGD 6X72-B engine and Mr Mutter confirmed the performance figures reported here on 9 October, when ABB Turbocharging’s Senior Vice President Christoph Rofka spoke of fuel savings of up to 6g/kWh when the FiTS2 technology is engaged, which represents savings of 3-5%.
As reported in February 2018, the system was developed jointly with WinGD, which had developed a special engine tuning to suit FiTS2. Speaking last month, Mr Mutter said that development work had started in 2016 in response to the trend for slow steaming, resulting in engines being operated at 50% or less of their rated power.
Tests were conducted at Diesel United in Japan on a sixcylinder version of the X72 engine and those have provided “the backbone” for the project, Mr Mutter said, because they demonstrated not only the fuel savings but also that NOx emissions could be maintained at IMO Tier II levels.
A FiTS2 installation comprises either two or three turbochargers - for the Berge Bulk installation, the engine has two of ABB’s A265-L units - one of which can be cut out for low-load operation even at relatively high engine loads.
It is this ability that puts the F - for flexibility - into FiTS2 and this feature, along with its compact design, were two goals behind its development, Mr Mutter recalled. On normal turbocharger installations, it is necessary to reduce the engine load to 10% or even less before the turbocharger valves can be operated to remove one turbocharger from operation, which can take half an hour or more, Mr Mutter said.
This flexibility could provide valuable support to ships operating in areas where there is a risk of piracy, he suggested: because the turbochargers’ valves can operate at high loads, a ship operating at low load on one turbocharger could immediately accelerate and the second unit would come on stream as the power increased.
These valves are mounted directly on the turbocharger, which is an unusual arrangement he said, to contribute to the system’s compact layout.
Although both turbochargers on this first application are the same model, they have each been modified so that one delivers 60% of the air to the engine and the other 40%. When the engine is operating above 50% of its rated load, both units are in use but at lower loads the smaller turbocharger is turned off. This channels all the exhaust through the remaining unit which can then deliver a higher charge pressure than if the exhaust was shared between both units. On a triple-turbocharger installation, each could provide 33.3% of the air supply.
This arrangement has an added benefit at low loads since the auxiliary blowers will only be needed below 20% engine load, rather than the normal 30%, which saves energy - and thus fuel - because of their reduced use. Mr Mutter estimated that this can add a further 1.2g/kWh of fuel savings.
8 The fi rst
installation of ABB’s Flexible integrated Turbocharging System for Two-Stroke Engines (FiTS2) solution is due to enter service in 2021
LNG CONVERSIONS: PERKS, PITFALLS AND POSSIBILITIES
If the industry is going to meet its emissions targets, alternative fuel conversions will have to reach beyond newbuilds, and into the existing fl eet - including the bigger, long haul ships: but they’re stubbornly hard to accomplish. So, industry players have come together to talk over the wrinkles... and how to iron them out
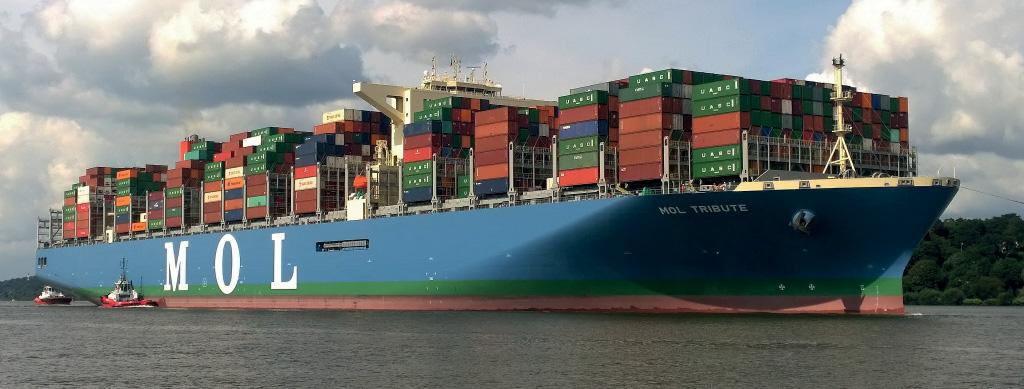
Firstly, the fuel’s power density requires consideration. As Mark Penfold of ABS points out: “all the alternatives being considered require a greater volume than conventional liquid fuels”; Ulf Åstrand of Wärtsilä adds that even the most mature, LNG, “does have an operational impact”.
However, there is an important counterbalance: endurance.
It’s now possible to drop the number of bunkering calls and consequently, reduce the tank installation - and the amount spent on it, says Jonathan Strachan of Houlder. This has only become a viable strategy in the last five or six years with development of the LNG infrastructure, but it makes a big difference to a swathe of vessels. “A standard product carrier can now change two, 500m2 tanks, for three 150 to 300m2 tanks to do the same job,” says Åstrand’s colleague, Mathias Jansson: that’s more than a 40% reduction in tank volume and its correlated CAPEX.
ATTRIBUTES
But the choice of tank type remains pivotal. Membrane versions are a useful, proven technology for newbuilds: their compact design and lighter weight offers fuel efficiency advantages over other larger, heavier solutions.
Unfortunately, they present challenges for retrofits. Beyond their relative expense, they’re also integrated with the hull itself and require support from a double-walled, insulated structure. It can raise yard costs: as a result, Jansson explains “for a larger containership conversion, introducing a membrane tank is quite labour intense”.
It’s a balancing act: while installing a single large membrane tank instead of two of another kind could pare down the fuel gas handling system, they also require extra kit such as pressure control and possibly a gas combustionunit to deal with boil-off, says Strachen’s colleague, David Edwards. He adds that by contrast, C-type tanks can manage the pressure fluctuations and maintain LNG for 15 days without venting to the atmosphere - with no extra burner.
Photo: Hummelhummel
But they do have their limits: “I’d say you can reduce the cost and installation on a type-C pressure vessel, but you are compromising on volume,” says Jansson.
It’s not that this technology can’t be produced to scale; they just don’t make efficient use of space. Therefore, in Strachen’s view, when it comes to giant containerships on long haul routes, C-types “might not give you the range unless you can face losing a considerable amount of cargo”.
However, the field is beginning to open up and it’s no longer a choice between membranes and C-type pressure vessels. According to Penfold, “material developments, such as high manganese austenitic stainless steels or composites... may also bring tank cost reductions”.
All this stands to give alternative configurations a boost. For example, prismatic tanks are designed to make the optimal use of available space. According to DNV GL, type-A tanks gain between 30% and 40% in volume efficiency over type-C models, plus, “they do generally cost less than membranes”, points out Strachan.
ENGINES & FUEL SUPPLY
So, what about the engine itself? Despite the scale, switching even large-bore engines over to LNG isn’t a significantly difficult process, as long as your choice comes with a conversion pack. In fact, since across the engine sizes the drivers are pretty much the same anyway, there’s an argument for saying ‘the bigger, the better’.
Size, however, does impact the rest of the kit: “You also need to know that wider diameter, double-walled LNG pipes can run sensibly through the vessel”, says Strachan, Edwards adding there is also the gradient to get right “or you can get pockets of LNG laying in a pipe”. That’s no easy feat, he says, “even on a newbuild”. Further, big bulk or boxship conversions may well require the creation of an ATEX-proof environment with room for the tank and fuel gas supply system.
It appears that most vessels will find an exhausting number
8 LNG conversions
for large, long-haul ships might prove tricky
of issues to contend with, both large and small. There’s the rise in deadweight and location of the LNG tank, gas valves and even issues around bunker station: SGMF’s recent guidance on the latter “has quite a bit to consider”, says Edwards, including passenger-related areas and whether bunkering from a dedicated vessel or quay. Moreover, there’s ventilation and additional points like exhaust fans, safety relief valves or discs, and EX rated electrical components.
Further, a nitrogen purging system is necessary, “and while you could do it with bottles for a smaller vessel, you’ll probably need a plant for bigger ships,” says Edwards. That doesn’t just take up space, “it adds another electrical load” to the onboard draw.
In short, “if the vessel wasn’t designed with hazardous zone and ATEX regulations in mind, it can be tricky”, says Strachan.
ALTERNATIVES
But then again, not all fuels are as demanding as LNG. MAN ES is currently retrofitting a dozen VLGC LPG carriers for B&W, the first being the 225m Gemini - and these are unlikely to hit the same budget concerns.
Importantly, LPG has a higher boiling point than LNG so “it can be liquefied and kept at relatively low pressures”, says Penfold. As a result, tanks and supply lines are simpler and generally less demanding of both space, design and yard time.
In the same vein, he adds that methanol also represents a cost-effective handling and containment solution especially as it can be stored in “near conventional” fuel tanks, adding this could be “particularly attractive for retrofit applications”.
However, as Åstrand explains consideration extends beyond the fuel supply system: “LNG is low SOx and NOx, but change that, and you may need more after treatment.” Further, despite DF engines being suitable for a range of alternative fuels, he predicts that shipping will probably not immediately switch over even when the new, carbon-free products become available. As a result, he says “blending may be an intermediate option, which could involve another holding tank”.
FUEL-READY
For some ships, it may be a case of ‘you don’t want to start from here’. Strachan comments, “LNG conversions will be much easier and cheaper if the vessel has been built with that in mind.” Class societies like ABS have already have established retrofit ‘fuel-ready’ notations: “Preparation can save time and costs for later conversion - for example, having a credible plan for fuel tank location and the necessary deck strengthening,” adds Penfold.
Even so, Strachan advises leaving a little room in the schedule for class certification. “Sometimes you can achieve the solution to an issue with a change in operating procedure, but it often requires a design change, even if a small one,” he says.
Still, “if your vessel has LNG-ready notation and you’ve selected engines that are DF ready, you are quite a long way there” he concludes, “but if you have neither of those things, do get a feasibility study, before you spend time and money on it”.
YARD AND COSTS
Inevitably, a lot depends on the refitting facilities: as Jansson comments, the most significant uncertainties are “the sum of the additional details... and overrunning time at the yard”.
As Lianghui Xia, Managing Director of Newport Shipping admits: “Even if you try to talk about the yard’s cost separately, it’s difficult to give a figure: so much depends on vessel type
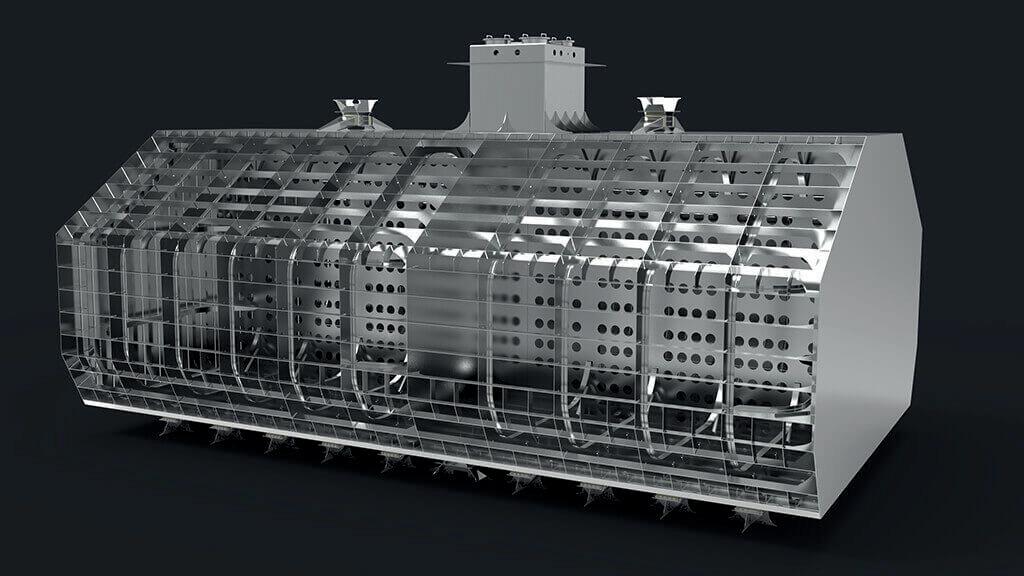
and even the approach.”
However, he adds, while “no-one can give guarantees”, teaming up with reputable suppliers and engineers with the right kind of track records, making sure there’s effective project management in the yards “and there’s a good chance it will work out”, he says. “At the end of the day, a lot is about execution.”
But even if the sums appear to work out, the costs of these conversions can be steep. Given this, Xia explains, “one solution would be paying over a longer period”, Newport being amongst those offering deferred payment terms. However, he adds, “a profit split arrangement with the charterer could give you the extra cash to support the longer-term”.
That makes sense, as it should make vessels more hireable, but there are few guarantees. Newport’s experience with scrubbers shows results can be inconsistent as “you can gain a premium, but market phenomena can just disappear... the free market is highly volatile”.
Still, some say it’s bound to get easier. There’s a “natural cost down curve” for any new technology, says Penfold, who expects the price to eventually lower. Åstrand isn’t so sure, adding that until a financial mechanism, such as a CO2 tax, is in place “conversion over lifetime costs will still remain too high to make it commercially viable for long-haul shipping”.
However, Xia concludes: “These things have their own trajectory: more engine providers, LNG compatible engines, and more competition will reduce the price,” although he adds: “It might be slow.”
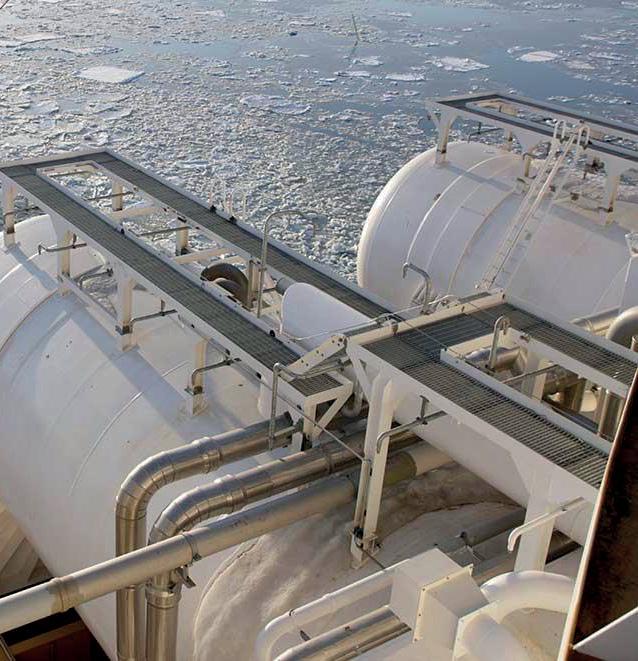
8 Prismatic tanks
could provide an alternative way forward for ship conversions
8 C-type tanks can
reduce cost and installation time, but compromise on volume
Photo: Wärtsilä
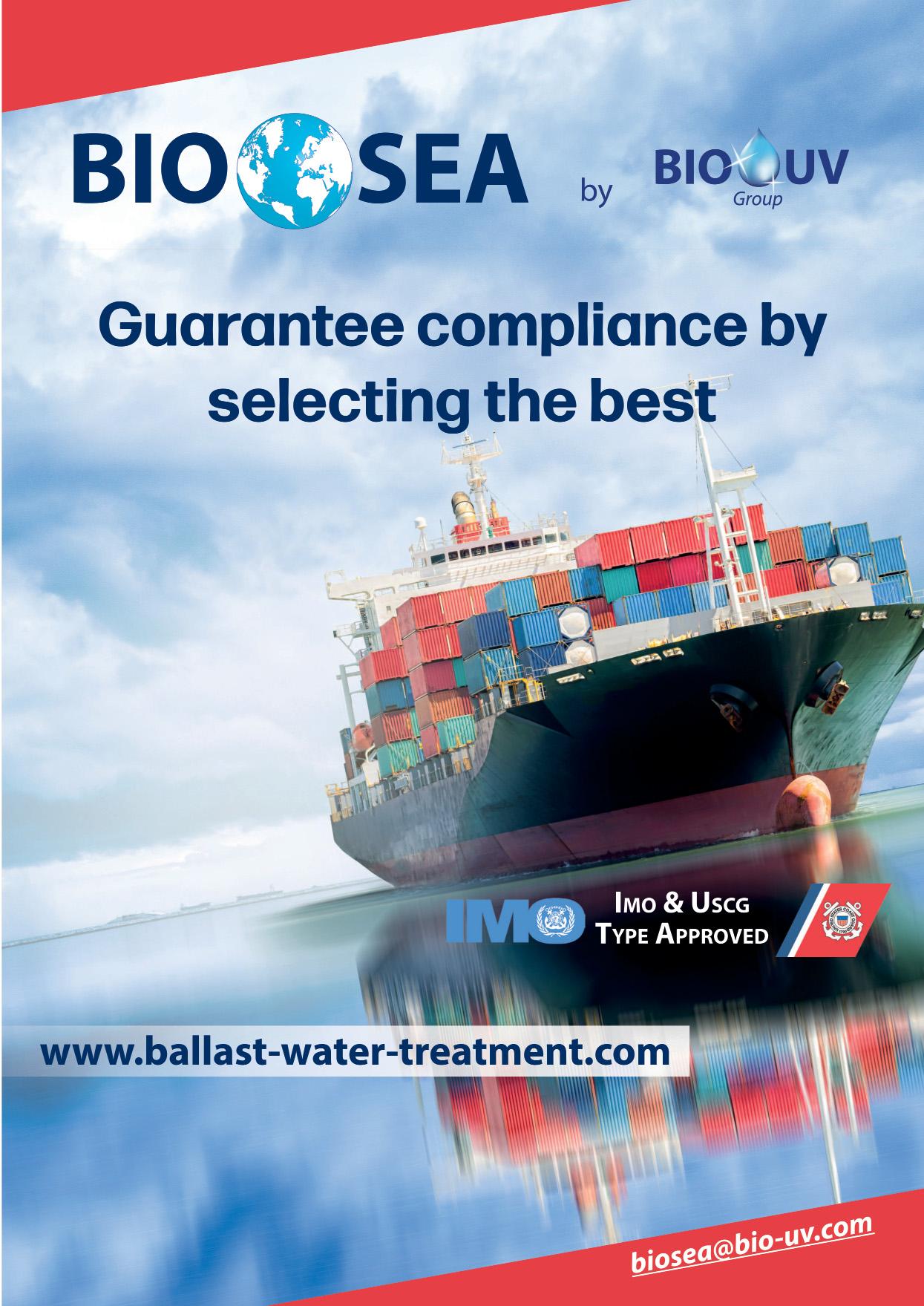