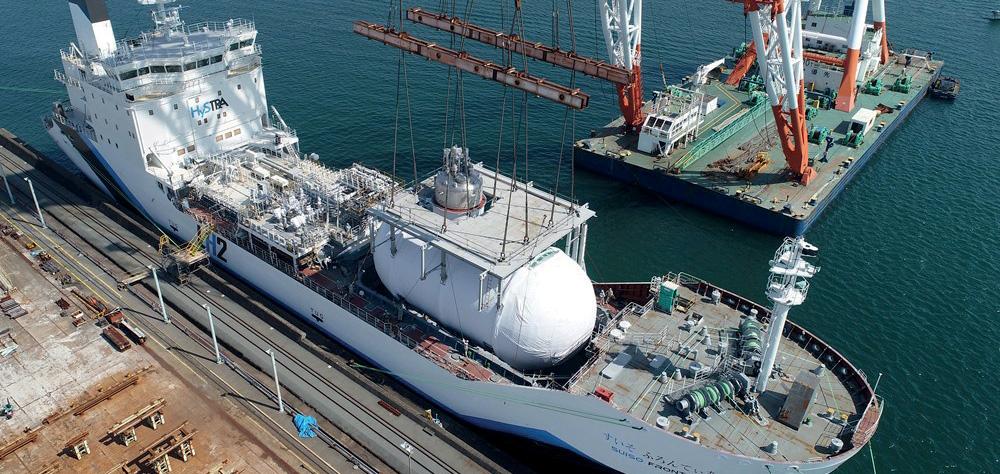
20 minute read
First LH2 carrier
KICK START FOR NEW CLEAN ENERGY TRADE
Japan is a step ahead of the rest of the world with a soon-to-be-commissioned liquefi ed hydrogen carrier, writes David Tinsley
Forty years on from its pioneering role in delivering the fi rst Asian-built LNG carrier, Kawasaki Heavy Industries (KHI) is in the vanguard of a new advance in gas shipping technology through the construction of a liquefi ed hydrogen (LH2) tanker.
The 9,000dwt Suiso Frontier, by providing 1,250m3 of cryogenic cargo containment within a hull length of 116m, will serve as a test platform and demonstrator for a major scheme to transport Australian-produced hydrogen to Japan. The plan ultimately calls for a flotilla of LH2 carriers, fitted with four spherical tanks and comparable in size at 160,000m3 to the latest generation of LNG tankers, dedicated to maintaining the supply line.
Many elements of the ship reflect KHI’s long experience in LNG carrier production and technology, as the Asian pioneer in the construction of such vessels, starting with the 129,000m3 Golar Spirit in 1981. It has maintained a presence in the LNGC market notwithstanding the intensity of the competition from South Korea and emergence of Chinese shipbuilding contenders.
Attuned to the wider national aspirations and endeavours, and possessed of a wide range of cryogenic engineering competences besides those relevant to the marine field, KHI is part of an industrial consortium focused on technological developments aimed at building an energy supply chain that will enable economic and reliable sourcing of hydrogen in large volumes from Australia.
The Hydrogen Energy Supply Chain Technology Research Association (HySTRA), in which KHI is partnered by the Iwatani Corp, Shell Japan, and Electric Power Development Co (J-Power), has the objective of ultimately making hydrogen as common a fuel source as petroleum and natural gas. Suiso Frontier has been built for the Hydrogen Energy Supply Chain (HESC) project which HySTRA will coordinate.
The initiative is being promoted and supported by Japan’s
Credit: HESC
New Energy & Industrial Technological Development Organisation (NEDO). Non-polluting hydrogen is regarded as a fuel of the future and a potentially important element in Japan’s drive to achieve the country’s newly-minted target of ‘carbon neutrality’ by 2050.
Hydrogen will be produced and liquefied in Australia. The raw material for the production will be brown coal mined in Victoria’s Latrobe Valley. As combustion of brown coal, or lignite, can be heavily polluting, coal processing at the hydrogen plant will utilise carbon capture technology and subsequent undersea storage.
Suiso Frontier was launched at KHI’s Kobe yard last December and installation of the cargo tank was carried out at the company’s Harima works in March 2020, with the vessel returning to Kobe for the completion of piping systems and other outfitting. Handover is imminent, this autumn.
Following operational tests in Japanese waters, ranging from tank cool-down to cargo handling at a pilot LH2 receiving terminal newly-built at Kobe, the ship is expected to make her first voyage to load in Australia during early 2021. Thereafter, she will undertake a round-trip every few months. The pilot phase is due to span one year. The decision as to whether or not to proceed to the commercial phase will be made once all reviews have been completed, with the target of full-scale operations in the 2030s. This could see a first contract for high-capacity LH2 carrier newbuilds in 2025-2026.
KHI is also party to a Japanese-Australian consortium that has obtained funding from the Australian government and the State of Victoria to establish the gasification and gas refining facility in the Latrobe Valley, and a liquefaction plant and loading terminal for LH2 carriers at Hastings.
LH2 transport poses major challenges, not least the extremely low carriage temperature of minus 253degC at atmospheric pressure, the wide flammability range and exceptionally high upper explosive level.
8 Installing the
liquefi ed hydrogen cargo tank in the Suiso Frontier
PRINCIPAL PARTICULARS - Suiso Frontier
Length overall 116.0m Length bp 109.0m Breadth, moulded 19.0m Depth, moulded 10.6m Draught 4.5m Gross tonnage c.8,000gt Cargo tank capacity 1,250m3 Propulsion system Diesel-electric Main gensets 3 x 1,320kW Propulsion motors 2 x 1,360kW Speed c.13kts Class ClassNK Complement 25 Operator HySTRA
Nitrogen cannot be used in the barrier or annular spaces, as is the case aboard LNG carriers, because nitrogen becomes liquid at minus 196degC and would therefore condense when in contact with surfaces at the LH2 containment temperature. Similarly, liquid oxygen could form if oxygen or air were to be used in the barrier space, as oxygen has a boiling point of minus 192degC. LH2 also has a very high permeability compared to LNG due to hydrogen’s extremely small molecular size, which leads to a propensity for easier leakage through the tiniest gaps.
The low minimum ignition energy of hydrogen gas/air mixture creates additional challenges for leak prevention and detection and for ignition protection, notably that concerning electrical equipment. The low luminosity of visibility of a hydrogen flame is of itself potentially problematic from a fire detection standpoint, and the high flame velocity can lead to detonation.
The particular properties of hydrogen and the design, construction and operation of a prototype ship such as Suiso Frontier calls for comprehensive risk assessment and adoption of suitable risk mitigation measures in close association with classification societies.
Nippon Kaiji Kyokai (ClassNK) has been proactive in setting out guidelines for LH2 transportation by sea. The guidelines consist of safety requirements applicable to LH2 carriers based on the IMO Interim Recommendations for Carriage of Liquefied Hydrogen in Bulk, and various international standards, as well as additional criteria taking specific hazards arising from the handling of LH2 into consideration. For the Suiso Frontier newbuild, the society was engaged to undertake the requisite verification and validation in accordance with its updated guidelines and rules.
The stainless steel cargo tank has been designed to ensure safe, long-distance transportation of liquefied hydrogen at 1/800th of its original gas state volume, cooled to minus 253degC, far below the temperature (minus 163degC) that has to be maintained for LNG containment.
LH2 evaporates at a rate 10 times greater than LNG. To accommodate this, Suiso Frontier employs a cargo containment system of double-shell structure for vacuum insulation and properties that suppress thermal conduction. The tank support structure has been made using glass fibre reinforced polymers, which are poor conductors of heat but extremely strong. So as to achieve the requisite ultra-high thermal insulation performance demanded in this innovative project, KHI brought to bear its particular know-how in onshore LH2 and LNG holding tanks, complementing its expertise in LNG carriers.
In addition to the management of boil-off through the pressure containment exercised by the Type-C cargo tank, Suiso Frontier is equipped with a gas combustion unit (GCU)
Credit: Saacke

provided by the German firing technology specialist Saacke.
The effectiveness of the patented, hydrogen-compatible GCU and the proprietary SSBG hydrogen burner is a vital factor in ensuring safety in seaborne transportation. Testing and acceptance of the equipment took place in northern Germany last October, providing the endorsement that LH2 can be carried at sea as safely as LNG.
In Saacke’s 100% free-flow solution, the boil-off gas is completely combusted without a compressor and at a pressure of just 0.15 bar. The absence of compressors from the process dispenses with the risk of compressor failure and the attendant safety implications of resulting increased pressure in the tank.
The diesel-electric plant in Suiso Frontier comprises three generators driven by Daihatsu six-cylinder DE-23 engines each turning out 1,320kW at 900rpm. The electrical energy so derived feeds two 1,360kW propulsion motors delivering propulsive effect through a twin-input/single-output gearbox to a controllable pitch propeller.
So as to meet IMO Tier III NOx standard, the Daihatsu medium-speed diesels incorporate selective catalytic reduction (SCR) technology.
For the envisaged generation of high-intake LH2 carriers, construction in Japan would be the province of the larger of KHI’s domestic yards, the Sakaide complex on Shikoku. The group also has substantial shipbuilding capacity in China, by way of its shareholdings in the joint venture companies Dalian COSCO KHI Ship Engineering (DACKS) and Nantong COSCO KHI Ship Engineering (NACKS). A second building dock was opened at DACKS this year.
CHARACTERISTICS of HYDROGEN COMBUSTION
5 The H-atom is the lightest and smallest element of the
Periodic Table 5 H2 is colourless, odourless and tasteless 5 H2 is 8 times lighter than natural gas 5 The calorific value is lower by a factor of 3-3.5 than most commercially available natural gases 5 The flame burns about 8 times faster than natural gas 5 The flammability range is extremely wide (4%-77% by volume compared to 4%-16% by volume for natural gas) 5 15 times less spark energy required for hydrogen ignition than natural gas
8 A large Saacke
gas combustion unit (GCU). A hydrogencompatible GCU has been supplied to Suiso Frontier
CHEMICAL TANKERS SET NEW STANDARD FOR ENVIRONMENT
The two 22,000dwt chemical tankers under construction for Donsötank Rederi are leading the industry in emissions reductions and crew welfare
The island of Donsö off Gothenburg in Sweden is home to a population of 1,500. It is also home to eight shipping companies, most currently involved with newbuildings. The Donsötank newbuilds are a refl ection of that shipping dynamic, says Managing Director Captain Ingvar Lorensson, with the outcome set to raise the bar higher for other shipowners.
The 167.7-metre, LNG-fuelled, Ice Class 1A vessels are being built by Wuhu Shipyard in China and are classed by DNV GL. Final installation of the battery systems and shore power connections will occur once they reach Sweden next year.
The vessels will be named Prospero and Pacifico and will be commercially managed by Donsötanks daughter company Navix Maritime Chartering in Gothenburg from mid-2021.
They are expected to achieve a 13-21% reduction in fuel consumption compared to a standard design. The vessels boast a number of carefully selected design features which mean the newbuildings’ CO2 emissions will be 55% lower than existing vessels in the fleet. Running on LNG, NOx emissions will be reduced by 89%, SOx emissions by 99% and particulates by 95%.
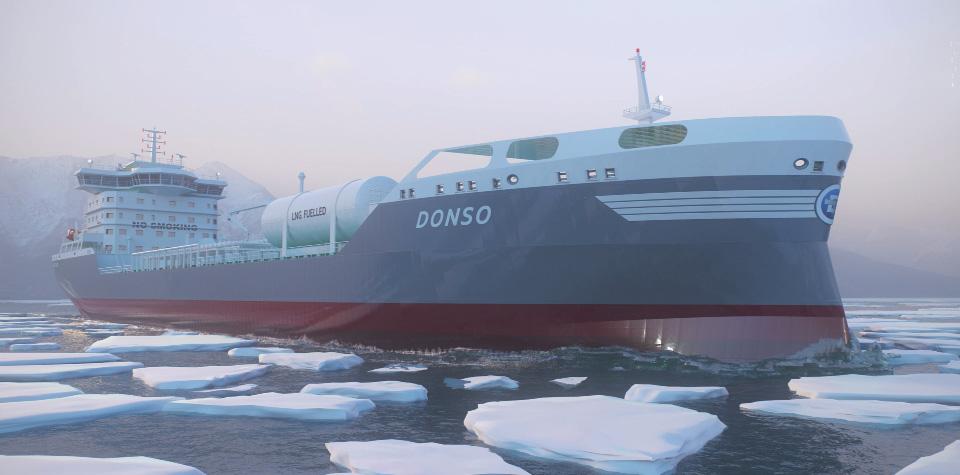
OPTIMISED DESIGN
Donsötank’ technical managers, safety manager and sailing captains and chief engineers brought their experience to the design project, and they worked closely with Uddevalabased naval architecture company FKAB Marine Design. FKAB was involved from the first sketches, developing a design that balanced fuel savings against investment costs. “It’s been a great journey with the very clear goal of achieving environmentally friendly vessels with a good working environment for the crew,” says Osborne Johansson, Technical Senior Adviser Machinery and System at FKAB.
The vessels’ F-Bow hull design is optimised to achieve maximum cargo capacity and for excellent performance. In calm weather it can save 4-8% fuel and harsh weather conditions up to 25%, says Andreas Hagberg, Sales and Marketing Manager at FKAB. Hull optimisation was performed for a number of depths, and the result includes less flair, a lower block, a propeller bulb and pitch optimisation, together giving 25% improvement on the hull lines of existing vessels in the fleet.
The hull coating used is a Jotun silyl acrylate technology coating, Sea Quantum. It is suitable for all activity levels and expected to perform well for up to 90 months.
The 6.2-metre propeller is complemented by a full-spade, full-twist leading edge rudder from MM Offshore. A wakefield and propeller slipstream analysis ensures maximum efficiency, minimal cavitation and therefore less noise at the aft end of the vessel.
DUAL-FUEL ENGINES
The main engine is a Wärtsilä 10V31 DF. “This is the most efficient 4-stroke engine in the world,” notes Lorensson, and it is recognised as such by the Guinness World Records. “It is dual-fuel, but we will run it on LNG and probably a little liquified biogas (LBG) also, if possible.”
The two auxiliary Wärtsilä 8L20 engines are connected to a GESAB SCR-Catamiser for NOx reduction and waste heat recovery. The combined dual-fuel thermal oil heater and inert gas production system, also from GESAB, is low on NOx and SOx emissions.
The 500kWh battery system supplied by Corvus Energy will continuously provide power to the system to boost propulsion, provide an alternative to running auxiliaries during narrow passages and harbour manoeuvring, and, most importantly from an energy saving perspective, allow
8 A rendering of
one of the pair of dual-fuel 22,000dwt chemical tankers under construction for Donsötank Rederi
for peak shaving. The energy storage system provides power for peak-shaving to balance variable loads on the main engine and auxiliary engines, saving an estimated 284 tons of CO2 each year on the open sea and 269 tons of CO2 in port during discharging if shore power is not available.
Lorenssen expects a battery life of eight to 10 years, and a financial payback, at worst, of six years. “But, we predict it will be better than that.”
The battery system alone could power the vessel for a short time in case of blackout, but combined with the 1.5kV shaft generator, the vessel could potentially sail at around eight knots if required during an emergency.
The WE Tech shaft generator features variable frequency drive technology, WE Drive™, variable speed generator technology, DC-link switchboards with dedicated inverter units and a power management system. With the DC-link distributing electrical power, energy efficiency can be increased by up to 35%, the main switchboard can have a smaller footprint with less copper used. Total harmonic distortion is low as is the reactive current flow in the electrical system. This enables the use of smaller inverters and less cabling.
Additionally, an Organic Rankine System waste heat conversion system, Orcan Energy’s Efficiency PACK, is connected to the cooling system. The solution uses waste heat from the thermal oil system and the jacket cooling water to produce electricity, thereby recovering waste heat from both the main engine and the auxiliary engines. At sea, this can provide 71kW net input to the switchboard, and during cargo discharging operations 83kW. This saves an estimated 205 tons of CO2 annually.
Like the two 15,000dwt chemical tankers being built for Tärntank Ship Management, and two 18,000dwt chemical tankers built for Furetank Rederi, companies that also originates from the island of Donsö, the vessels will have the ability to connect to shore power. Negotiations with the Port of Gothenburg have led the sets of newbuilds having the connection point in the manifold area located centrally in the EX cargo handling zone to minimise cabling needs and to enable the ships’ cargo cranes to do the cable lifting. At the Port of Gothenburg, a shore power station will be located centrally on the quay with approximately 50 meters of cable available. A similar arrangement is expected to be available in the Port of Rotterdam.
The 6.6kV power from shore will provide enough power for cargo discharge operations and for charging the battery system. As part of the shore power connection procedures, the plug room, too small for a person to enter, will be overpressurised with nitrogen.
The use of oil onboard has been minimised: the actuators for the cargo and ballast valves are all electric. Supplied by Eltorque, they minimise energy consumption by having a low energy idle state and, they also avoid the need for having hydraulic pipes going down into the tanks. They are made from non-hazardous, fully recyclable materials.
Additionally, to reduce the need for oil, the THR Marine mooring and anchor winches are electric. This avoids the need for a lot of pipework and eliminates oil leakage risks. The Wärtsilä stern tube has a water lubricated seal, and the vessels have a frequency controlled, fixed pitch Wärtsilä bow thruster.
A Hydroniq rack cooler was chosen for its easy inspection and maintenance and for its compact design. The tubes are made from CuNi to prevent marine growth, and there is no galvanic corrosion, as it is fully insulated from the hull. The cooling system is a demand-adjusted system, so it’s not running at full speed all the time. “This makes it more efficient that a normal box cooler,” says Lorensson. “If you need to clean it, you can just close the tank and lift it up from the inside, and if you have dirt in the water from a river, for example, this doesn’t present a problem for the cooling system.”
The vessels are IMO type 2 oil products and chemical tankers with a cargo capacity of 28,000cbm and they feature 14 electric deepwell cargo pumps from Svanehøj . The cargo tanks are coated with Jotun Tankguard Special. Hot water coils are used for tank heating, and all cargo pipes and crossovers are self-drained down from the manifold to the cargo tanks.
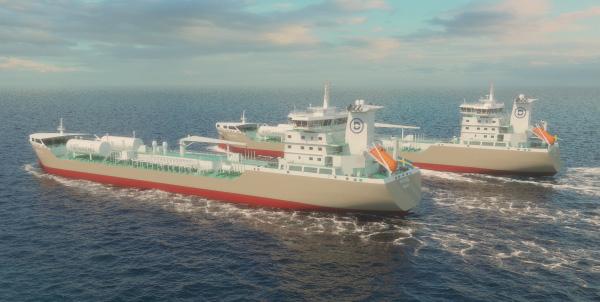
CREW SAFETY
The comfort and safety of the crew was paramount when designing the accommodation areas and the engineroom layout. “Everything was designed in 3D, and we spent a lot of time in the 3D model determining the safest outcome, so that the crew do not need to climb around pipes and equipment,” said Lorensson.
Mooring arrangements have been designed according to Mooring Equipment Guidelines Fourth Edition 2018 (MEG4). “Safe mooring is critical for the crew onboard,” says Lorensson. “We want to avoid incidents, so we also spent a lot of time here to design the best mooring system possible. The design calls for of eight ropes on drums fore and eight aft. The lines are straight, not going through any rollers.
The designers spent a lot of time reducing noise onboard the vessels. Engineroom fans are fitted with silencers, and the cargo pumps are electric to minimise noise. Outside noise level was determined to be at most 65db measured 25 metres from the side of the vessel when running two auxiliary engines and two engineroom fans. This compares very favourably with a similar vessel in the company’s fleet with a main engine of the same size.
Lorensson’s team is proud of what has been achieved and believe the design is the most efficient for the class of vessel to date. While the owners on Donsö are not direct competitors, they watch what each other are doing and learn from each other, always raising the stakes on environmental performance.
FKAB recently designed vessels for Donsö-based Furetank Rederi. These 16,300dwt chemical tankers are also equipped with batteries and dual fuel engines for LNG operation. Further afield, FKAB has also recently designed a series of dual-fuel, battery-ready 10,500dwt chemical tankers for Norwegian owners Utkilen and two 7,000dwt gas-ready stainless steel chemical tankers for German owner GEFO.
Tor Järnberg Business Developer at FKAB notes that FKAB’s environmental friendly designs have low EEDI values, with excellent hull forms and a careful selection of equipment to suit the shipowner’s requirements. This results in efficient energy consumption and low OPEX. “We work in close cooperation with owners to balance CAPEX and OPEX.”
8 The Ice Class
1A vessels feature an F-Bow hull design that off ers signifi cant fuel effi ciencies in harsh weather conditions
RELIABILITY IS THE KEY
MOTORSHIPTHE
INSIGHT FOR MARINE TECHNOLOGY PROFESSIONALS
The international magazine for senior marine engineers
EDITORIAL & CONTENT
Editor: Nick Edstrom editor@mercatormedia.com News Reporter: Rebecca Jeff rey rjeff rey@mercatormedia.com
Correspondents
In the leading editorial for The Motor Ship, November 1970, the writers welcomed a challenge to the marine engines market by MAN, focusing on improved reliability in both the large-bore two-stroke and medium speed sectors.
MAN, which was placed third in both markets behind Sulzer and B&W, and Pielstick and Mitsubishi respectively, had been criticised for producing too wide a range of engines and options in the past, which had prevented it capturing the industry’s demands. Of course, both B&W and Pielstick are now part of MAN Energy Solutions, but 50 years ago they were strong competitors.
The 52/55 four-stroke engine, which had been launched rather cautiously some 18 months previously, had been designed to offer a reliable 1000 bhp/cylinder output, and the soundness of the design was being proven. With the launch of the KSZ105/180 two-stroke, MAN aimed to bring reliable operation to the high-power large-bore engine sector to meet the demands of a new generation of larger and faster ships.
Despite a capability of more than 4,000 bhp/ cylinder, the KSZ was described by MAN as a “simple engine”, designed to reduce maintenance and enhance operational reliability. That’s not to say that the competing large-bore offerings of similar potential output were proving unreliable, rather that MAN had concentrated on this aspect of the design, including a then-novel use of computer modelling to evaluate the new concepts of predictable MTBM (mean time between maintenance) and MTBF (mean time between failure) for all component parts and systems.
The main ship description examined in detail the newly-delivered Song of Norway, first of three passenger ships for cruises in the Caribbean, built for the newly-formed Royal Caribbean Cruise Lines by Wärtsilä in Helsinki. The 18,400gt ship, with singleclass accommodation for 870 passengers catered for by 300 crew, was designed specifically for the particular requirements of the burgeoning US luxury cruise industry. As the report stated “though the design might not be what a naval architect would envisage, the owners are catering for passengers in the American market.” Although the appearance might raise a few eyebrows, with such features as a solarium incorporated in the aft funnel, technically the ship followed established practice. The Wärtsilä designers had a brief to save weight, but the inclusion of such features as the solarium and a permanent ballast being carried to comply with stability requirements.
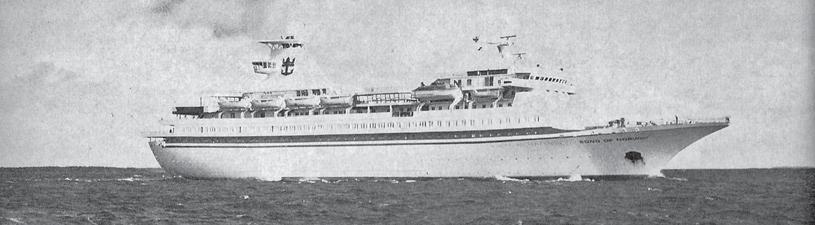
8 The Wärtsilä-built Song of Norway, fi rst in the new
Royal Caribbean cruise fl eet
Engines were four Wärtsilä-built Sulzer 9ZH 40/48 medium speed units, arranged in pairs, driving twin KaMeWa CP propellers through reduction gearboxes. A total power of 18,000bhp was good for 21 knots, though it was envisaged that once in the Caribbean the vessel would operate on three engines. Six Wartsila 814TK auxiliaries handled the considerable domestic load.
With the current focus on digitalisation, one sentence from November 1970 struck a chord: “Full implementation of satellite communication for merchant ships is something for the future.” Indeed, the idea of allocating specific maritime frequencies was not even due to be considered for another six months. But trials had been undertaken in the North Atlantic, where the ACL container ship Atlantic Causeway was fulfilling the role of mobile test bed, having been offered periods for experimentation on a NASA satellite for ship-to-shore voice, data and fax transmissions to a UK coast radio station.
Finally, it was reported that successful trials of nuclear power for ships, with an advanced pressurised water reactor onboard the German bulk carrier and research ship Otto Hahn were expected to lead to an economic marine reactor for higherpowered ships “in the near future”.
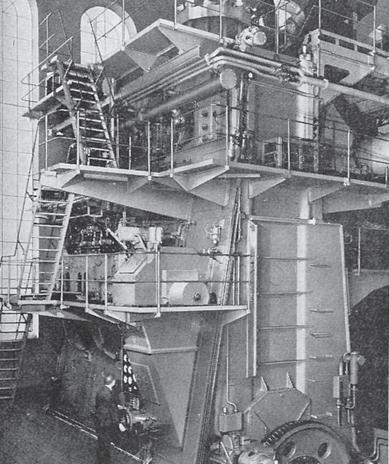
swimming pool area on the sun deck led to
Please contact our correspondents at editor@motorship.com Bill Thomson, David Tinsley, Tom Todd, Stevie Knight, Wendy Laursen
Production
Ian Swain, David Blake, Gary Betteridge production@mercatormedia.com
SALES & MARKETING t +44 1329 825335 f +44 1329 550192
Brand manager: Toni-Rhiannon Sibley tsibley @mercatormedia.com
Marketing marketing@mercatormedia.com
EXECUTIVE
Chief Executive: Andrew Webster awebster@mercatormedia.com
TMS magazine is published monthly by Mercator Media Limited Spinnaker House, Waterside Gardens, Fareham, Hampshire PO16 8SD, UK
t +44 1329 825335 f +44 1329 550192
info@mercatormedia.com www.mercatormedia.com
Subscriptions
Subscriptions@motorship.com or subscribe online at www.motorship.com Also, sign up to the weekly TMS E-Newsletter 1 year’s magazine subscription £GBP178.50 UK & EURO Post area £GBP178.50 Rest of the World
© Mercator Media Limited 2020. ISSN 0027-2000 (print) ISSN 2633-4488 (online). Established 1920. The Motorship is a trade mark of Mercator Media Ltd. All rights reserved. No part of this magazine can be reproduced without the written consent of Mercator Media Ltd. Registered in England Company Number 2427909. Registered offi ce: Spinnaker House, Waterside Gardens, Fareham, Hampshire PO16 8SD, UK. Printed in the UK by Holbrooks Printers Ltd, Portsmouth, PO3 5HX. Distributed by Mail Options Ltd, Unit 41, Waterside Trading Centre, Trumpers Way, London W7 2QD, UK.
8 MAN’s prototype KSZ engine, designed for simplicity