
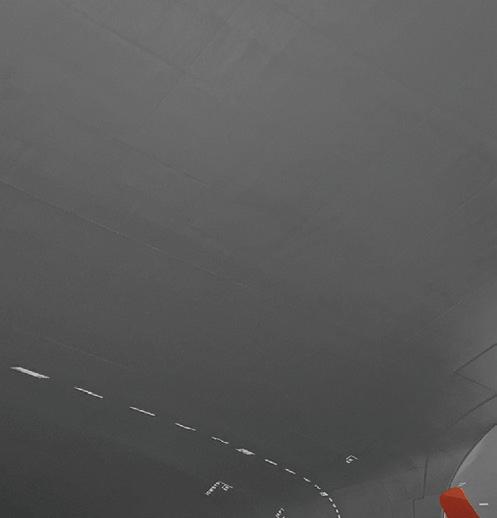
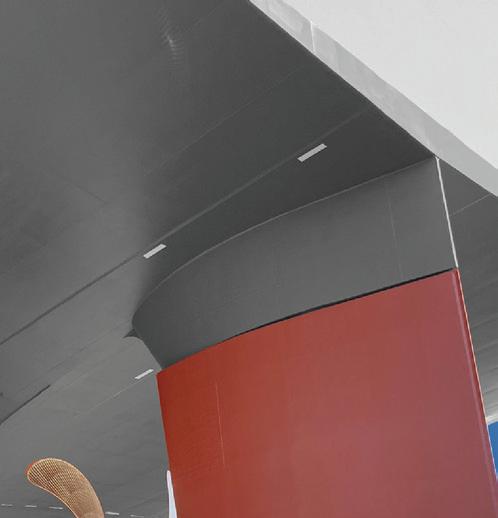
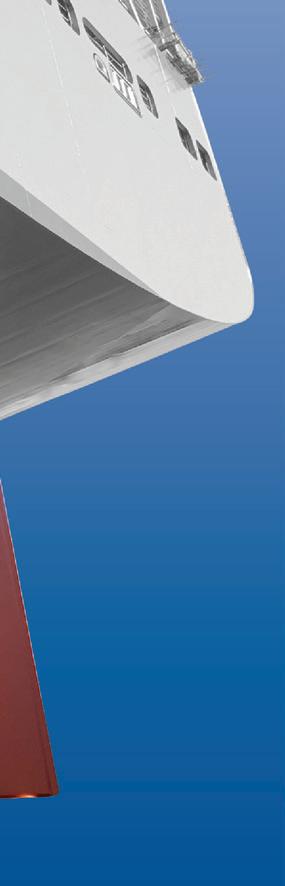
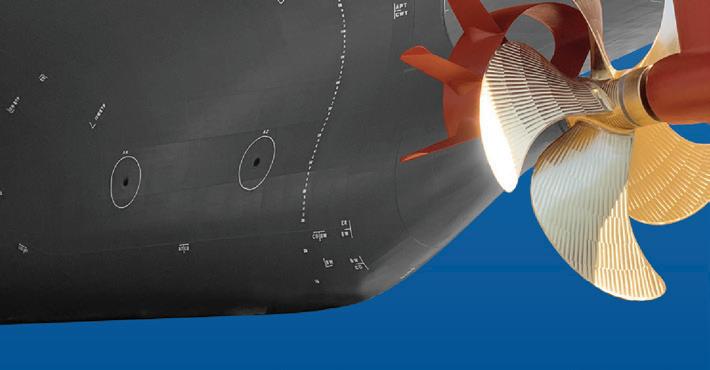

The new MAN 49/60DF
Best fuel costs and long-term compliance Today’s marine propulsion choices are significantly influenced by fuel costs and decarbonization requirements. These factors have driven the development of the MAN 49/60DF. It sets a benchmark in efficiency to keep fuel costs and CO2 emissions low. The built-in flexibility of a dual fuel engine, its low methane emissions and high efficiency ensure multiple paths for long-term emissions compliance. Based on this state-of-the-art engine platform, MAN Energy Solutions plans options ready for future fuels.
WinGD’s engine control system has been granted SP1 type approval by DNV, in line with IACS UR E27 technical system requirements.
The EU agreed to allocate 20 million ETS allowances (EUR1.5 billion) to maritime projects under the Innovation Fund.
Kongsberg Maritime’s new Direct Trunk Support (DTS) system aims to boost rudder performance, promising improved manoeuvring, propulsion performance and weight savings.
Chinese yards have regained primacy in the newbuilding market, and are eyeing expansion into higher-value niches, writes David Tinsley.
As Azipod systems celebrate a milestone, Marcus Högblom, Head of Passenger Segment, Global Marine Propulsion Sales, ABB Marine & Ports sees new opportunities ahead.
GTT’s three-tank LNG tanker design will make it possible to reduce the daily boil-off rate, Wendy Laursen hears.
MAN Energy Solutions’ latest dual-fuel four-stroke engine, the 49/60DF, is its most powerful dual-fuel four-stroke engine yet, exceeding even the larger 51/60DF, thanks to its electronics.
A high-level discussion at PFF 2022 assessed the implications of the upcoming introduction of onshore power system requirements across the EU’s Core TEN-T ports by 2030.
The 43rd Propulsion and Future Fuels Conference underlined the pace of advances in alternative fuel developments and fuel efficiency.
Japan’s Tsuneishi Shipbuilding has delivered the first of a new design of bulk carrier that offers a substantial uplift in cargo capacity within the Kamsarmax category, writes David Tinsley.
Although Maersk plans to shutter TradeLens in Q1 2023, new applications for blockchain technology are likely to emerge for the digital technology.
propulsionconference.com
The Motorship’s Propulsion & Future Fuels Conference will take place on 17-19 November 2020 in Hamburg, Germany. Stay in touch at propulsionconference.com
The Motorship’s Propulsion and Future Fuels Conference will take place this year in Hamburg, Germany. Stay in touch at propulsionconference.com
I was struck by two observations during the Onshore Power System (OPS) high-level panel discussion during this year’s 43rd Motorship Propulsion and Future Fuels conference.
The decision to accelerate the requirement to introduce OPS installations at the EU’s Core TEN-T ports is likely to require significant investments within the ports themselves, and upon the electricity network providers themselves within EU member states. The sums involved are hardly trivial: the European Commission itself believes that the final bill could exceed EUR7bn.
However, the larger challenge would appear to be that early adopting port authorities themselves are finding it difficult to develop a compelling business case to encourage vessel operators to make use of cold ironing.
One significant barrier to adoption is the higher cost of electricity than diesel fuel. This problem is likely to disappear or at least be muddied once the IMO introduces its market-based measures (or economic instruments).
But the larger issue that still perplexes me is how the ports themselves and the electricity companies will handle the continuing uncertainty about electricity demand from shipping going forward.
Just as we have discussed the difference between digitalisation development lead times and engine development cycles previously, we should be aware that electricity infrastructure investments make ship lead times appear extremely brief.
If the EU wishes to compel the majority of container vessels and passenger vessels to make use of OPS facilities with Core TEN-T ports by 2030, one wonders whether the ports have begun to liaise with the local grids around ensuring stable electricity supplies will be available by then.
I suspect that the confidence interval surrounding the size of the expected electricity draw that the ports of Gothenburg, Amsterdam or Marghera can expect to see in December 2030 is likely to be quite significant.
Of course, similar concerns can be made about the sizing of alternative fuel bunkering infrastructure. The size of the investment requirements to develop bunkering infrastructure for alternative fuel dwarfs the EU’s OPS investment requirements. ABS tentatively estimated that the cost could reach USD30bn per annum over the coming 20 years or so.
The only place where such large investments can be raised is likely to be the financial markets. However, bankers and financiers tend to favour clarity, and clear data, and are unlikely to invest significant sums into projects that have significant question marks attached to them.
While I appreciate that the above is likely to be a statement of the obvious for many readers, I should stress that the academic theories underlying associated with decarbonisation of the energy markets put regulations before markets and prices. This reflects the origins of environmental economic theory in the complex world of (stationary) energy markets and national regulation.
In a boost to UK shipbuilding prospects, the British-led Team Resolute consortium has been chosen by the Ministry of Defence as preferred bidder for three Royal Fleet Auxiliary(RFA) support vessels, writes David Tinsley. The award presages a return to ship construction by Harland & Wolff(H&W) at Belfast, after a gap of two decades, albeit drawing on overseas technological know-how.
The series of 216m newbuilds, with the power to operate at speeds up to 19 knots, will have a primary role as replenishment vessels, supplying stores, munitions, spares and equipment to warships at sea.
Team Resolute, comprised of H&W, ship designer BMT, and the new UK arm of Spain’s largest shipbuilder Navantia, has won the bidding round in the face of competition from three other groups. A production contract, valued at £1.6bn($1.9bn)(before inflation), is set to be authorised by the spring of 2023. However, under what has proved to be a long drawn-out competition, building of the first ship will not start before 2025 and the final vessel in the programme is not expected to be operational until 2032.
The majority of the blocks and modules for the ships will be constructed at H&W’s yards in Belfast and Appledore, with components also being sourced from the group’s fabrication sites in Scotland at Methil and Arnish. There will also be significant input from Spain, whereby Navantia’s Puerto Real yard at Cadiz will undertake some of the building work, while the organisation will also provide
technology transfer and skills know-how to Belfast. Final assembly for all three vessels will take place at Belfast.
The formal contract award to Team Resolute will also trigger a £77m($92m) investment in shipyard infrastructure, creating jobs and strengthening the capability to attract future export and domestic shipbuilding and offshore orders to the Northern Ireland yard. Although H&W, under previous ownership, delivered its last commercial vessel in 2003, the yard has maintained a presence in heavy engineering, steel and offshore fabrication, renewables, shiprepair and refurbishment, and business development has accelerated since the 2019 takeover by InfraStrata, now trading as Harland &Wolff Holdings.
The newbuilds, designated fleet solid support ships(FSS), will have cargo space for 9,000m2 of supplies and stores. They will have a beam of 34.5m and will be the longest vessels deployed by the civilian-crewed RFA, and will have some commonality with the 201m Tide-class fleet tankers.
Four of the latter were constructed by Daewoo Shipbuilding & Marine Engineering to BMT’s Aegir design and commissioned between 2017 and 2019.
The RFA series constitutes one of the key projects listed under the 30-year “pipeline” of work for naval and other governmentowned vessels contained in the revised National Shipbuilding Strategy, published in March 2022.
Windcat has ordered a series of hydrogen-powered commissioning service operation vessels (CSOVs) from Damen Shipyards.
The Elevation Series CSOVs have been designed by Damen Shipyards in cooperation with Windcat and CMB.TECH. The vessels are 87 metres long, 20 metres wide, can accommodate 120 people on board and will be powered by hydrogen. Initially, two vessels have been ordered with options for further vessels. The series will be delivered from 2025.
The CSOVs will be built at Ha Long Shipyard, Vietnam, and will be delivered to Windcat Offshore, a new business unit within Windcat, which will focus on offshore energy commissioning
and services.
A CSOV is a vessel that remains in an offshore wind farm for an extended period of up to 30 days, providing maintenance materials and housing technicians in hotel-style accommodation.
To significantly reduce the vessels’ CO2 footprint, Windcat and CMB.TECH, will provide the same dual fuel hydrogen technology for the Elevation Series as on board the Hydrocat, the world’s first hydrogen powered crew transfer vessel.
Kongsberg Maritime has launched a new Direct Trunk Support (DTS) system which aims to boost rudder performance.
The new system transfers the manoeuvring forces from the rudder through the headbox and the steering gear deck directly into the hull structure, promising improved manoeuvring, propulsion performance and weight savings.
“Today, replacement and modernisation of propulsion and manoeuvring systems are key drivers for newbuilds and aftermarket sales,” said Andreas Malmkvist, SVP Propeller & Shaftline Systems, Kongsberg.
WinGD has become the first marine engine designer to gain cybersecurity type approval for its engine control system. DNV has granted WinGD Control Electronics (WiCE) an SP1 type approval, aligning with IACS UR E27 technical system requirements. The approval demonstrates that WiCE meets the IEC62443 standard including software authenticity verification, and backup functionality.
“For Kongsberg, DTS is a significant opportunity to cover a larger market and provide
The EU’s on-going negotiations on the EU ETS for maritime has resulted in an agreement that at least 20 million ETS allowances “(EUR1.5 billion at current prices) will be allocated to maritime projects under the Innovation Fund. The provisional deal is subject to an overall agreement on the ETS revision. The agreement includes all GHGs and outlines steps towards a life cycle perspective, which will include GHG emissions from marine fuel production.
customers with a long-term solution to help them meet their goals.”
The DTS rudder has no upper size limit and works for vessels of any size, from container ships to fishing vessels, and in any segment, from naval ships to superyachts.
It eliminates the radial forces and bending moment transferred from the rudder blade to the steering gear. This is accomplished with an extended pipe integrated into the rudder trunk. This means that the rudder stock (torque shaft) in the DTS system only transfers torque and axial loads.
Some of the most important
ClassNK has issued an AiP for a dual-fuel hydrogen/diesel genset. The technology was designed for a 160,000m3 LH2 carrier developed by KHI. It will be able to use boiloff gas from the ship’s LH2 cargo tanks as the main fuel. ClassNK has already issued AiPs for the vessel’s integrated design, containment and cargo handling systems, and DF main boilers.
benefits of the new DTS system come in the design phase of a ship. The improved load distribution gives ship designer more flexibility in the aft ship design, which enables a lower positioned steering gear deck. This gives greater storage capacity to any vessel.
The DTS system also gives ship owners the option to choose smaller steering gear, since the DTS system only transfers torque load.
The improvement in load distribution allows more freedom in the design of the rudder blade. Higher aspect ratios and slimmer, full-spade rudder designs are possible, which improves the overall performance of the vessel.
ABS launches SaaS unit ABS has launched ABS Wavesight, a new maritime software as a service (SaaS) company.
Wavesight integrates My Digital Fleet, an AI-driven analytics and performance visualization platform, with Nautical Systems, the fleet management system. The platform aims to offer greater visibility into fleet assets.
8
Added-value
In 2021, China regained its position as the world’s biggest shipbuilder, overtaking South Korea for the first time since 2017. Results from the first nine months of 2022 not only keep China on course to retain the top slot but put it to the fore in a number of sectors. For example, Chinese yards booked more than half the contracts awarded for containerships in excess of 10,000TEU capacity, and logged the preponderance of new work involving deep-sea vehicle carriers, a sector that has seen heavy investment this year.
Moreover, the advance to higher value-added tonnage has been underscored this year by China State Shipbuilding Corporation (CSSC) having secured orders for the largest number of LNG carrier newbuilds placed so far this year with any single organisation worldwide. CSSC has assigned most construction to the group’s Hudong-Zhonghua Shipbuilding.
Brokers are forecasting a downturn for 2023 in demand in major areas of the international market that are significant for Chinese yards, specifically bulkers, containerships, large tankers and also LNG carriers. Should such a decline materialise, and notwithstanding the fundamental importance of export work to the industry in China, the country’s own, ever-expanding trade and energy requirements provide a solid domestic platform for Chinese shipbuilding capacity utilisation. The national mercantile marine is growing on all fronts, and its development will be met wholly by recourse to home yards.
Furthermore, and going hand-in-hand with the country’s rise as a superpower, the shipbuilding industry has fundamental strategic as well as economic importance, as the cradle for the huge build-up of the Chinese Navy.
A national champion is born Consolidation is a theme pervading shipbuilding worldwide, and the grand-scale amalgamation effected by China’s two state-controlled groups appears to have given the industry new strength. Greeted with trepidation by South Korea and Japan, and with a surprising lack of response from Europe, a Chinese behemoth was created in 2019 through the remerger after 20 years of China State Shipbuilding Corporatio n(CSSC) and China Shipbuilding Industry Co(CSIC). Over half the nation’s shipbuilding industry was vested in the two government-owned conglomerates, and the successor organisation continues under the CSSC banner.
The Chinese initiative had ostensibly been spurred by the prospect of the creation of a potent new South Korean force through Hyundai Heavy Industries Holdings’ planned acquisition of DSME – a move which, however, was subsequently thwarted on anti-competition grounds by the European Commission.
container liners, each of 24,000TEU capacity. Worth nearly $2.9bn in monetary terms, the project has added technological and commercial significance in its specification of methanol dual-fuel propulsion. COSCO companies already had 34 boxship newbuilds booked with domestic yards, and the latest project extends the workloads at Dalian Cosco KHI Ship Engineering (DACKS) and Nantong Cosco KHI Engineering (NACKS) by five and seven ultra-large vessels, respectively.
LNG carrier investment has been a major feature of the newbuild market this year and China’s shipbuilding industry has made considerable inroads into the sector. Although South Korea’s three largest groups collectively still lead the field, Hudong-Zhonghua has the single largest concentration of LNGC orders worldwide. Moreover, such has been the broader Chinese success in penetrating the market that the contract inflow is more distributed than before, whereby five Chinese builders are engaged in LNGC construction rather than three hitherto.
HZD builds LNG carrier momentum
Hudong-Zhonghua, which has the longest track record in the field, having completed the first Chinese-built LNG tanker in 2008, has landed three ordering tranches this year arising from Qatar’s planned boost to LNG production and exports through its North Field development scheme. An initial contract signed during April with Mitsui OSK Lines (MOL) embracing four 174,000m3 newbuilds, to be run under longterm charter to QatarEnergy, was followed in November by a second MOL deal spanning three vessels, for delivery in 2027.
At the same time, Hudong-Zhonghua won an order from an international consortium calling for five 174,000m3 carriers committed to QatarEnergy. The contractual interests involved, namely NYK Line, K Line, MISC Berhad, and China LNG Shipping, had earlier awarded seven LNGCs of the same size to Hyundai Heavy Industries, also on the strength of longterm charters to Qatar’s state energy company.
Hudong-Zhonghua has also augmented its orderbook with three LNGCs booked by MOL for long-term engagement with the privately-owned Chinese energy group ENN. Incorporating membrane-type cargo containment of around 174,000m3, the ships have been fixed through a Singapore subsidiary of ENN and will primarily transport LNG to China on commissioning during 2027 and 2028.
To the chagrin of Japanese builders, the shift by Japanese shipping groups and trading houses to source tonnage in China has gathered pace. MOL fleet development projects initiated in 2022 and entailing Chinese construction have included four Capesize bulkers and two VLCCs. LNG dual-fuel power has been nominated for each of the six ships in the programme. Production of the 210,000dwt Capesize units has been assigned to CSSC Qingdao Beihai Shipbuilding, while the 309,000dwt crude carriers will come from DACKS.
China has come to dominate the global ro-ro and ro-pax ferry construction market, in the process almost annihilating a former major source of business for European yards. Although some industry sources suggest that the uplift in newbuild costs coupled with rapidly increasing Chinese wage bills could soon see challenges to that current pre-eminence, recent contractual successes on the export front demonstrate continuing competitiveness in the sector.
In fact, on the broader ro-ro front, encompassing dedicated, deep-sea vehicle carriers, the Grimaldi Group’s October placement of an order with CMHI Jiangsu for five newbuild PCTCs of 9,000CEU capacity, plus five options, emphasises the strengths-in-depth of China’s industry. The vessels’ technological standard is implicit from a specification that
features an ammonia-ready class notation, lithium battery pack, under-hull air lubrication system, and cargo area design geared to the transport of electric vehicles.
While Chinese owners have generated only a trickle of projects in the ro-pax sector, one recent exception being the 167m newbuild arising from Chinjif’s fleet modernisation strategy, the shipbuilders’ penetration of the export market to date has been such as to attract virtually all the leading players in Europe.
The production momentum built-up in the large ro-pax ferry segment, which calls for particular capabilities in the outfitting trades, supplier network and project management, impacts on Chinese shipbuilders’ ambitions as to the international cruise vessel market. While a robust bridgehead has already been laid down through the collaboration with Fincantieri and Carnival that has yielded a programme for two high-capacity cruiseship newbuilds at Shanghai Waigaoqiao, the advance of the cruising sector in China itself has faltered through the country’s draconian measures to tackle the upsurge in Covid-19 cases.
The first of the vessels that signal China’s entry into the field of large, luxury passengership construction was launched last December. Tailored to the Chinese market, she is due to be handed over in September 2023 to CSSC Carnival Cruise Shipping. The second vessel will not be a duplication of the lead ship, but will be 17m longer at 341m, and larger in internal volume by some 6,000gt at 142,000gt, with 19 more passenger cabins for a total of 2,144. The original deal carried options for up to four further vessels.
Among the few projects of entirely domestic origination that have been taken forward to the contractual stage is that implemented by China Merchants Group, involving two 37,000gt newbuilds at CMHI (Jiangsu), specifically developed for Chinese passengers and destined to inaugurate the Shanghai Style Cruise brand.
Cruise vessels represent the next frontier Any sustained weakness in global ordering of cruise ships could have greater long-term repercussions for European yards than for China’s shipbuilding industry, given the latter’s highly diversified output, absence of high dependence on particular spheres of construction, and strong direct and indirect government backing. Although the European bastions have orders stretching as far ahead as 2028, and have succeeded in winning the very limited number of cruise vessel contracts placed since the start of the pandemic, those yards will have to confront a difficult and possibly protracted period of soaring costs in finance, materials, energy and labour, against the backcloth of reduced tonnage demand.
Whether or not a freeing-up of European capacity, and any moderation in the wage cost differential between China and Europe, will lead to a re-entry by European cruiseship building specialists into the ferry market remains to be seen. In the meantime, Finnish, Polish, Turkish and Italian yards that are not involved in cruise vessel production have scored contractual successes this year in the ro-pax domain, indicating a degree of revived competitiveness (assuming that the orders prove profitable) in a field that has increasingly become the province of Chinese shipbuilding.
But China’s ever-growing and wide-ranging capabilities, increasing technological self-reliance, overt and covert government backing, and collective industrial endeavour makes for a formidable long-term rival in any sphere of construction. A preoccupation with the environmental standard of the product offering, reflected in current deliveries and boosted R&D resourcing, bodes well for the future.
GTT has received Approvals in Principle (AiP) for its three-tank LNG tanker design from DNV and Bureau Veritas (BV).
The design reduces construction costs by negating the need for one cofferdam, one pump tower and all associated cryogenic equipment (liquid and gas domes, valves, piping, radars, etc.). The overall surface area of the containment system will be reduced by about 2,000 m², generating lower costs for the materials and vessel construction. This could also offer time-savings for shipyards.
The three-tank LNG carrier has been designed with a similar operational flexibility as the conventional four-tank LNG carrier. For instance, several solutions to discharge the cargo with the same flow rate as for the four-tank design are envisaged.
The improved ratio between the volume of LNG transported and the surface area of the cryogenic liner will make it possible to reduce the daily boil-off rate. As an example, GTT estimates that it will achieve a boil-off rate as low as 0.080% of tank volume per day with the Mark III Flex technology, compared to 0.085% of the volume per day with the LNG carriers currently in operation.
The removal of a cofferdam will lighten the hull weight, and if specific reinforcement is deemed necessary during the final design, it will not significantly increase that weight. Ship length and overall cargo capacity might be further adjusted, and the design also allows for greater choice in ballast tank location.
As GTT’s membrane systems are fully modular, they can be used unchanged for any tank dimension with local reinforcement, if required, to withstand sloshing loads. Sloshing studies undertaken by GTT at its model test facility have shown the pre-feasibility of the lengthened tank design. GTT has researched any potential challenges that could be encountered for tank length increases of up to 55%.
As the tanks are modular, there is no limitation intrinsic to GTT containment systems: the three-tank LNG carrier has been initiated for a capacity of 174,000m³ which remains the current standard. Other capacities could be developed so long as the proposed ship design meets rule requirements and the operational flexibility required by terminals. GTT is already working on other innovative concepts to address a wider range of cargo capacities.
DNV and BV have issued an approval in principle for this innovative three-tank LNG carrier design for the Mark III and NO96 technologies developed by GTT.
Tom Klungseth Østvold, Principal Engineer for DNV Maritime, said: “Three different vessel arrangements were considered in the AiP process, for which we examined the intact and damage stability requirements, as well as the ability of the membrane type containment system to sustain the increased sloshing loads associated with the increased cargo tank dimensions for each. In addition, we undertook a high-level evaluation of hull strength based on the general arrangement and midship section drawings.”
The GTT three-tank LNGC concept implies a significant increase in cargo tank length and a change in the watertight compartmentation of the hull, he said. The general vessel safety arrangement, cargo handling systems, safety systems etc. are essentially unchanged by the design
modification but would need to be adapted depending on the individual ship design.
“One of the key questions was the way the increased length of the tank shifts the sloshing resonance periods for the tanks upwards. This can increase exposure to resonant period ship motions and the sloshing impact load level in the tanks, but was addressed by GTT through detailed sloshing studies and strength evaluations of the containment systems. These studies identified an increase in sloshing impact loads compared to existing four cargo tank LNGC designs. However, GTT was able to demonstrate that this can be mitigated by the installation of the appropriate containment system reinforcement level available in the GTT product portfolio.”
Philippe Berterottière, Chairman and CEO of GTT, said: "For almost 60 years, the GTT Group has been constantly improving its technologies to offer its customers solutions that meet their requirements as well as those of the regulatory authorities. Thirty years ago, we upgraded LNG carriers from five to four tanks, and we now hope to bring the market forward with a three-tank LNG carrier. We hope to see this concept become standard in future years."
The new LNG carrier design has generated a lot of interest from shipyards, shipowners and charterers, and is particularly noteworthy, says GTT, because it reduces CAPEX while also improving performance.
8 GTT is planning to develop a RECYCOOL concept for LNG carriers in 2023
8 The three-tank LNG carrier design is expected to reduce the daily boil-off rate by improving the ratio between the volume of LNG transported and the surface area of the cryogenic liner.
Sustainable & Smart Mobility Strategy - Ricardo Batista, Policy Officer, Directorate-General for Mobility and Transport European Commission. Development cycles towards ammonia-fuelled two-stroke engines - Dr Andreas Schmid, General Manager Technology Development, WinGD. Will “multi-fuel” propulsion engines be the solution to solve the “future fuel” uncertainty? - Rolf Stiefel, Regional Chief Executive, Bureau Veritas Marine & Offshore Economic and Ecological Considerations for Wind-Assisted Ship Propulsion Systems - Karsten Hochkirch, Head of Ship Performance Center, DNV
MAN Energy Solutions’ latest dual-fuel four-stroke engine, the 49/60DF, is its most powerful dual-fuel four-stroke engine yet, exceeding even the larger 51/60DF, thanks to its electronics. In fact, under certain conditions, it is the most efficient four-stroke dual-fuel engine on the market, MAN ES’ Sales Manager, Marine Four-Stroke, Thomas Huchatz, told The Motorship.
8 MAN Energy Solutions’ latest dual-fuel fourstroke engine, the 49/60DF, is its most powerful dual-fuel fourstroke engine yet
It is rated at 1,300kW/cyl at 600rpm – making it the most powerful engine in MAN ES’ four-stroke family – and, without its attached pumps, consumes 6,990kJ/kWh in gas mode, giving it an efficiency of 51.5%.
When the engine was formally launched during the SMM exhibition in September, MAN ES listed a number of its technical features, including the OEM’s second-generation Adaptive Combustion Control, ACC 2.0, and the latest version of its SaCoS 5000 (Safety and Control System generation 5) automation system.
These are vital not only to its initial performance but also to its future development, said Stefan Terbeck, principal technical project manager of the 49/60 engine family, in particular naming the ACC 2.0 as ‘key’ to introducing new fuels to the engine. It can operate on LNG and diesel fuel, along with “a number of more sustainable fuels including biofuel blends and synthetic natural gas,” the SMM statement said.
But it also quoted Marita Krems, Head of Four-Stroke Marine and License at MAN ES, noting that engine is making its debut “at a time where … fuels like methanol, ammonia and hydrogen are continuing their rise,” although she
acknowledged that “none [of these fuels] has established market dominance as of yet.”
Nonetheless, Terbeck indicated to The Motorship that methanol was likely to be added to the engine’s fuel options in the future while Huchatz predicted that this will be followed by ammonia and hydrogen, depending on market demands.
MAN ES has previously announced that its stationary gasfuelled engines are hydrogen-ready, capable of operating with up to 25% hydrogen in their gas fuel mix and in an announcement last November, it referenced its ACC – which was introduced about five years ago – as being instrumental for that, saying that the control system “reacts fully automatically to varying hydrogen contents in the natural gas.”
At its heart are firing pressure sensors in each engine cylinder that allow automatic cylinder pressure analysis (CPA) to be performed in real time. Now, the 49/60DF is the first engine type to be fitted with ACC 2.0 which is able to analyse combustion in each cylinder for every cycle, which is made possible by the greater calculating power of ACC 2.0 compared with the original version fitted to the 51/60DF. Terbeck had also been project manager for that engine,
which now has about 8M running hours under its belt and said that “we have seen what can be improved and put that into ACC 2.0.”
One change he mentioned is that the 49/60DF has more sensors, including for NOx, allowing closed-loop control for NOx emissions. This makes it possible to operate the engine closer to limit values rather than allowing an operating margin.
With the data gained by the CPA, Terbeck mentioned that the ACC 2.0 can control numerous combustion parameters, which reflect changing fuel properties, ambient conditions, air fuel ratio and component aging.
For example, if an engine that normally uses MGO or MDO is switched to a blend containing, say, 40% biofuel, the lower heat value will change and combustion can be delayed and the ACC 2.0 takes this into account, he explained.
The CPA will also instantly adjust for factors related to pilot fuel injection to correct the combustion parameters for best efficiency or for best dynamics so, “by having fully electronic access to our actuators, gas valves, pilot fuel valves, waste gate and gas pressure governor, we can adjust the combustion automatically to the fuel used,” he said.
This will be especially relevant for methanol, Huchatz added, because it has a lower energy density from diesel fuel. That also presents some physical challenges, since greater volumes will have to be injected into the combustion chamber.
Readers may recall a first application of SaCoS 5000 on the MAN 45/60CR engine in 2017 but it has been further refined since then. This latest version was first applied to MAN 32/44CR engines and is being introduced on the 35/44DF and other MAN four-stroke machines.
This latest version now finds its place as a vital component in the package of technologies that, together, make the 49/60DF an efficient multi-fuel power platform.
Working alongside the ACC 2.0, SaCoS 5000 helps make the new machine a ‘software engine’, Huchatz said, since it provides an improved interface between the engine and the outside world that can be used to transfer more data than before and in a higher resolution for remote analysis and support, he said.
This goes beyond the now-common practice of collecting data from onboard machinery and transferring it ashore. “This new system is technically capable having data going the other way, so that we can push data onto the engine,” he said. That opportunity could be used, for example, to ensure that the engine always has the latest combustion parameters necessary for its efficient operation. At present, these updates might only be possible when a technician visits and uploads new data directly from a laptop, for example.
“We have to convince owners that there are benefits from
this,” he said, but that is not the only constraint holding back its implementation: over-the-air updating such as this is not yet possible from a regulatory point of view so “we are talking with class societies about how this can be done,” Huchatz said.
This difficulty has arisen because hitherto an engine and its control system is class-approved as a combination of hardware, software and data. If some of that data is subsequently changed, it might have implications for emissions, for example, requiring the class society to reevaluate the set-up, Huchatz explained.
This has implications from a regulatory standpoint, Terbeck added. An engine is allocated an emission identifier related to its NOx-affecting components that, in the past, was based only on its hardware, which would not change. But once software becomes part of the system, any change – for example to the NOx-mapping – requires that this identifier should reflect that change.
Another consideration for any system that relies on data transfer is cyber security and in April this year, the International Association of Classification Societies (IACS) adopted two Unified Requirements related to cyber resilience on ships. These will be applied as mandatory to new ships contracted for construction from 1 January 2024 and the major classes have already defined different levels of cyber security beyond the requirements soon becoming mandatory, Huchatz said.
With increasing use of digital and remote software services, the risk of cyber-attacks increases, he pointed out, and protecting passwords and physical access to systems can only offer basic protection. “If you want to go to beyond Level One, you need features that only SaCoS 5000 can offer, he said.
Terbeck drew a comparison with conventional virus protection software on personal computers, which requires regular updating, but is still at risk of being bypassed.
Such traditional measures are well known in relation to IT security, where the main priority is to protect data, whereas for technical systems the focus is on their safe and secure operation, for which reactive measures such as subscriptionbased virus protection is not sufficient.
For operational technology (OT) security, when the main focus is to ensure the safety and availability of the engines and the ship, SaCoS 5000 was conceived with ‘cyber security by design’ and “’defence in depth’ in mind. “It features a builtin and fit-for-purpose layered design across separate zones using advanced network topologies comprising segregation and segmentation,” Huchatz explained.. These are fundamental features that ensure cyber security resilience and improve uptime and performance, he added.
Coinciding with MAN ES’ public launch of its new engine was an announcement that it had made a cooperation agreement with ABB to develop a next-generation, DualFuel, Electric+ (DFE+) propulsion concept for LNG carriers that will feature the 49/60DF engine and ABB’s Dynamic AC (DAC) technology.
Its aim is to offer variable-speed genset operation over the entire engine load along
with better efficiency with a significant reduction of methane slip over the entire engine map. This will help shipowners cut their carbon footprints and their fuel bills, the project partners said at the time.
Asked why the new engine is especially suitable for this project, Huchatz stressed its efficiency, but he also noted that the SaCoS 5000 control system makes the engine particularly suitable for variable-speed
operations while the ACC 2.0 optimises the engine at reduced speeds. This translates to providing effective variable speed and better efficiency to the propulsion system.
So “the electronics are key to achieving these efficiency levels,” he said. But in turn, they also contribute to a 40% reduction in methane emissions, “so developing with this new system also tackles the topic of methane emissions in four stroke dual-fuel
The like-for-like replacement of a polluting asset such as a ship, building or car might be attractive initially, but little thought is given to the carbon cost of sourcing materials for, and constructing, that replacement – the ‘embodied’ CO2. For the economics to stack up, an asset should provide enough of an operational emissions reduction to pay back its embodied CO2 costs.
In an example of this, in 2019, a new ‘Green NCAP’ rating system was launched for cars. A notable feature of the new scheme was that it incorporated the lifecycle emissions – the carbon cost of acquiring parts and making the car, as well as operating it – into the equation. An operational lifetime of 16 years and 240,000km was assumed, and as these parameters were applied, it came as a surprise to many that some petrol cars performed better, on a lifecycle basis, than electric counterparts.
One of the major concerns with the IMO’s EEXI and CII criteria for existing vessels, is that it will cause many ships to be scrapped, removing capacity which must be replaced with new tonnage.
Though welcomed as necessary by the maritime sector as a whole, shipping lines like Maersk and MSC have expressed misgivings, pointing to the disproportionate age of smaller vessels, which are necessary for efficient feeder trades.
The majors’ biggest complaint, however, is that the CII calculation in its current iteration takes into account only cargo capacity, expressed in deadweight tonnes (DWT), rather than actual cargo carried – a separate calculation known as energy efficiency operational indicator (EEOI). “It would be far better to have an operational indicator that would reward more productive ships, including based on cargo carried rather than on a theoretical value that may not correlate to transport work performed,” said MSC in a statement in October.
Speaking with The Motorship, Laxman Kumar, technical director at scrap buyer GMS, expressed concern that the EEXI and CII might lead to perverse outcomes. “Vessels will naturally be phased out of the fleet as part of a responsible ship recycling strategy, something that GMS supports,” he said. “However, serious thought needs to be given as to the rate at which older vessels are phased out of the fleet and its true benefit to emission savings, to prevent EEXI and CII leading to net-negative outcomes.
“If shipping looks beyond its 2.4% contribution to global CO2 emissions and looks more widely at the carbon contributions of a vessel along its entire value chain, disposing of older vessels, no matter how well-intentioned, may not always be the best approach.”
Globally, steelmaking is responsible for some 8% of global carbon emissions, more than double what is generated by global ship operations. According to the World Steel Association, each (long) ton of steel produced, on average, 1.85 tons of CO2. It would be possible to reduce this using
electric arc furnaces (EAFs), which can use scrap steel as a feedstock.
Unfortunately, there is neither enough scrap, nor sufficient EAFs, to go around. In Turkey, where some vessels now go to be recycled, some 84.1% of new steel is made from scrap, according to the Bureau of International Recycling. But in China, where the vast majority of ships are built, it is a different story. Only around 21% of new Chinese steel is made from scrap, and the rest, from iron ore in coal-fired blast furnaces. Further, Chinese shipyards generate their own emissions, as well. According to a recent Lloyd’s List report, a large Chinese shipyard might consume 20,000MWh, provided by a power grid in which coal plays a large part.
Replacing an older vessel with a new like-for-like one, then, with the latest efficiency upgrades including wing sails, optimised hull geometry and ducts, might yield a 30% operational CO2 emissions reduction; but it could take dozens of voyages before the CO2 cost of building a new vessel creates a return on investment.
“A newbuild bulk carrier, with a 150,000dwt capacity and a hull and machinery weight (lightweight, or LWT) of 20,000 tonnes, would require 15,400 tonnes of coal to be burned to generate enough steel for the vessel,” said Kumar. “This means that before any welding is done, the CO2 footprint of the vessel’s construction is at least 37,000 tonnes.”
Compare the U.S. Jones Act market, where instead of being built anew, sometimes ancient ships are repeatedly
8 Should demolition decisions take into account the potential embodied CO2 savings from extending the operational life of older assets?
It is only recently that the notion of ‘embodied’ CO2 emissions has come under consideration in the popular consciousness
modified to spare their owners the vast expense of building a new ship. Unfortunately, this has ended in tragedy on occasion; S.S. El Faro, originally a break-bulk vessel, was retrofitted to carry containers above the main deck and cars below, with vents for car exhaust, in one hare-brained decision, dangerously close to the waterline.
But there are other places where simply scrapping and rebuilding is not always considered the only option. At this year’s NorShipping, in Oslo, car carrier SC Connector made it into the running for the ‘Next Generation Ship Award,’ despite originally being constructed in 1997. Though it later lost out to coastal cruiseferry Havila Capella, the car carrier had been fitted with Norsepower rotor sails and a large battery pack, enough to reduce its fuel consumption by 25%.
“We pay our workers properly in Norway, and that’s why we get such good results,” Kleven sales manager retrofit, Karl Johann Barstad told The Motorship. But Mr. Barstad’s national pride aside, part of the reason why newbuilding, and not retrofit, has been regarded as a first resort for replacing tonnage is indeed cost. Labour in Chinese yards has been so cheap that there has not been sufficient spread between the cost of far eastern newbuild construction, and retrofits at yards in the West. But the economics might not stack up so handily, if embodied carbon costs were also considered.
If it’s broke, fix it
Though they have a natural advantage in low-carbon shipbuilding thanks to their abundance of renewable hydropower, Norwegian shipyards and equipment manufacturers are currently devising ways of decarbonising the process further.
Ships built in Norway tend to be specialist, and very highlyequipped. A surfeit of componentry, and the need to replace and repair it, has prompted Kongsberg to embark on a project with additive manufacturers Guaranteed, Voestalpine, Addilan and Intertek, with the aim of making additive manufacturing (AM) work well enough to create components as good as their traditionally die-forged and machined counterparts.
The aim is to be able to deliver spare parts faster and cheaper, with the added benefit of using less metal, usually steel. Wire arc additive manufacturing (WAAM), as it is known, was shown in testing to produce a component – in this case, a crank disc for a controllable pitch propeller (CPP) – equally as durable as a forged steel part.
Analysed under the microscope, the bonds between molecules in the steel were found to be nearly identical to that of a forged equivalent, Kongsberg explained. While the part did eventually require some machining and polishing to tidy up the surfaces, entailing some small amount of wasted metal, the process led to orders of magnitude less waste material than so-called ‘subtractive’ manufacturing would allow.
“We very often have to buy new parts for our customers, and we wanted to see if we could 3D-print these,” said Kongsberg’s Mette Lokna Nedreberg, manager of Material Technology. “[Forging] uses a lot of energy and has very long lead times. But if the vessel is waiting for a component, they need it immediately.”
Kongsberg also said that the process could be used to repair a cracked or otherwise damaged part, leading to even less material waste, work time, and associated carbon emissions. This would allow for existing systems to stay in use instead of being replaced, as manufacturers often will no longer carry an inventory of spare parts for deprecated machinery.
More high-tech was evident at Green Yard Kleven, which has weathered Norway’s shipbuilding drought by branching out from a shipbuilding yard to encompass shiprepair and scrapping, as well. Here, the yard is using a laser welding system to join steel plates together.
While the system can only be used to make flat surfaces at present, making it more suitable for superstructures and bulkheads than hulls, the extraordinary precision of laser welding makes it possible to create steel sheets of 5mm thickness. This would not be possible for a human welder, for whom double this thickness would be the minimum to yield a satisfactory weld. The result is a thinner sheet which cuts down on steel use, while maintaining the structural durability of its thicker counterpart.
For Green Yard Kleven, though, lasers powered by renewable energy is not even the half of it. The yard appears to be trying to change the ethos of shipbuilding entirely, to place a much greater emphasis on recycling – albeit, not in the traditional sense.
Instead of merely turning existing ships into piles of scrap steel and nautical-themed furniture, Kleven is reconditioning intact hulls and machinery, and turning them into new vessels, in a process it refers to as ‘recirculation’. In one example, the yard turned a PSV hull into an exploration yacht, the B370 Ulysses.
However outwardly environmentally-conscious Norway may be, its shipowners do not seem to be immune to wasteful attitudes, Karl Johan Barstad admitted. On hearing the first proposal to repurpose functional equipment from a scrapped ship on board a newly converted vessel, he quoted one owner as saying: “I don’t want garbage on my ship,” preferring new equipment. However, he said, when Kleven was able to demonstrate it could recondition used equipment to an asnew standard, the owner was eventually convinced to go along with it.
Currently residing at Kleven’s yard are deck cranes, generators, thrusters and even a seismic array, which are being brought up to a modern standard in order to equip a new vessel. While this will involve replacing wear parts, hinges and so on, it also includes consulting with the OEMs to update the equipment’s firmware and software, as well. After all, over the course of 15 years, crane technology has not changed so very much.
Overdue in the eyes of many, the introduction of CII levies a scrutiny on the way existing vessels are operated, rather than just creating a standard to which new ones should be built. From the point of view of reducing shipping’s overall contribution to global carbon emissions, it represents considerable progress. But now that responsibility is being shared across the entire global fleet, revisiting the lifecycle of vessels, and including their construction and scrapping in the mix, is an obvious next step.
Years ago, says Juuso Reunamo, Design Engineer at ship designer Deltamarin, when dual-fuel LNG engines were introduced to market, they often came as new models, with, for example, new bore sizes. Today, however, the engines being developed can efficiently burn multiple fuels with minor changes. “This opens up a wide range of retrofit choices based on modular design principles,” he says.
This will be a bonus for owners of existing tonnage given that there is no “silver bullet” future fuel. Additionally, almost all new projects undertaken by Deltamarin involve energy saving options. “When considering cold ironing, batteries, solar panels and fuel cells, the electric propulsion and power plant principle starts to look lucrative,” says Reunamo. “Currently the power plant principle, where the engines are only providing electrical power, has been beneficial on ships with large hotels loads, but in future we could also see this on other ships. When considering sails, it can be that on windy day there is very little propulsion power needed from the engines and on calm days there is a big need. With the power plant principle, the number of engines in operation can be selected so that the engines can operate with good loading.”
He says fuel cells are often seen as a good future choice, but for now, in most cases, diesel engines are needed to provide reliable power with fast load acceptance, working together with or backing up other systems. “Even with battery powered vessels we usually see engines taking care of
abnormal conditions such as heavy seas or ice conditions and working as a back up for charging failures.”
A 4-stroke engine coupled with reduction gear so that engines, generators, and motors can be connected and disconnected easily, is a good solution for ships where a hybrid system is preferrable to a fully electric one. This setup would, for example, allow zero emissions operation in port if a battery was installed.
“In the future, we expect to see the uptake of alternative fuels, an increase in energy saving devices and more propulsion lines boosted or solely powered electrically. We still see the need for both 2- and 4-stroke engines, keeping in mind that the flexibility of 4-stroke engines in combination of electrification could open new opportunities for the 4-strokes,” says Reunamo.
Last year, MAN Energy Solutions reassessed the role of 4-strokes and undertook a total cost of ownership analysis for a ropax ferry sailing a specific route with a fuel cell, battery and liquefied hydrogen tank, comparing it to a hydrogen combustion engine and liquefied hydrogen tank. The comparison considered lifetime efficiency, OPEX and CAPEX and found that, even giving the fuel cell setup very favourable terms, its business case only became attractive after 19 years of operation.
That’s not the only new electrification being considered. MAN and ABB recently developed the Dual-Fuel, Electric+ (DFE+) propulsion concept for LNG carriers. The concept
The 4-stroke engine market is expanding its offering, and after meeting the needs of biofuel operation, it is now responding to the prospect of future fuels and greater electrification
features the new MAN 49/60DF engine and involves using variable-speed gensets over the entire engine load. The result is better efficiency with significant reduction of methane slip over the entire engine map.
In continuously developing its portfolio, MAN is enabling its customers to exploit synthetically manufactured, climateneutral fuels. Already today, MAN engines using power-to-X fuels such as synthetic natural gas can be operated in a climate-neutral way.
MAN launched its 49/60DF engine type earlier this year. This latest addition to its four-stroke engine portfolio, is a dual-fuel engine capable of running on LNG, diesel and heavy fuel oil as well as a number of more sustainable fuels including biofuel blends and synthetic natural gas. MAN says it sets a benchmark in terms of fuel efficiency within fourstroke engines – both in gas and diesel modes – and therefore minimises fuel costs.
The 49/60 can start in gas mode where it complies with IMO Tier III without secondary measures. In diesel mode, it complies with Tier III combined with MAN’s SCR system. Soot emissions are halved in diesel mode due to MAN’s new common rail system 2.2, while the 49/60DF’s methane emissions also greatly reduced in gas mode compared to its predecessor.
MAN plans to introduce a pure diesel engine based on the 49/60 platform in 2023 that will inherently be retrofit-ready for running on methanol and LNG should the demand arise at a later stage.
Alexander Feindt, Global Business Development Manager Marine (Four-Stroke) at MAN, says the company recognises its important role since around half of the shipping industry’s approximately 3% contribution to CO2 emissions (Scope 3) can be attributed to MAN engines due to their high market share.
The engine manufacturer is committed to pushing ahead with development of solutions for the combustion of methanol, ammonia and hydrogen, to ensure their customers can remain compliant with IMO and tougher EU regulations. The greatest “pull” from 4-stroke customers at present is for methanol. “Methane: minus 163 degrees, liquefied hydrogen: minus 253 degrees, ammonia: toxic. Methanol is the easiest to handle alternative,” says Feindt.
Methanol is also attractive from a storage perspective, as it only requires 2.5 times the storage capacity of fuel oil to maintain the same bunkering patterns. “Basically, any large cargo ship will turn into liquefied hydrogen carrier when you use liquefied hydrogen as a fuel.”
MAN anticipates offering 4-stroke methanol retrofits from 2024. Due to the modular design of MAN 4-stroke engines, retrofits are feasible for a wide range of models including the 48/60, 51/60 and 32/40. Projects are already underway with Stena and Norwegian Cruise Line.
Methanol requires adaptions of some key systems of the engine including additional, larger injectors, changes to cylinder head, piston crown and revised combustion parameters in engine electronics. Double-walled fuel piping and new detection sensors will be required, and as methanol is aggressive on seals, these may also be changed.
MAN is working on two new-engine methanol technologies: port fuel injection (PFI) expected to be available from 2024 for retrofits and integrated high pressure fuel injection expected to be available from 2026-8. PFI technology enables a solid operating range with a high methanol percentage and will be available for newly built diesel and dual fuel 4-stroke engines. The pre-mixed (Otto cycle) combustion will require a diesel pilot, with 100% MCR to be maintained in diesel mode. This engine will be able to reach IMO Tier III NOx requirements when running on methanol without an SCR system.
The high-pressure direct injection (HP-DI) Diesel cycle technology is considered the more long-term solution and suitable for near 100% methanol (along with a diesel pilot). With this technology, full power output can be achieved with the highest efficiency over the entire engine operation mode.
Despite the current popularity of methanol, MAN is committed to offering solutions for all new fuels. MAN’s hydrogen dual-fuel 4-strokes could enter the market in 2025 or shortly thereafter. MAN Cryotech has already developed and delivered a marine fuel-gas system, including storage tanks, for liquefied hydrogen.
The company continues its involvement in the AmmoniaMot project to develop a medium-speed, ammonia-fueled engine. Testing is currently at the single-cylinder stage. MAN will transfer the technology to large-bore, four-stroke engines and prepare for commercial development and production after 2025.
The recently-released Wärtsilä 25 4-stroke engine is intended to be the first Wärtsilä engine to run on ammonia. Development is currently underway with a technology concept readiness slated for 2023. The engine’s modularity is anticipated to maximise flexibility. It is already capable of operating on diesel, LNG, or on either gas or liquid carbonneutral biofuels, and the manufacturer says it can easily be upgraded to operate with future carbon-free fuels as they become available.
The engine is now available in 6L, 7L, 8L and 9L cylinder configurations. The dual-fuel version has a power output ranging from 1.9 to 3.1 MW, and the diesel version from 2.0 to 3.4 MW. The fuel gas system shares common parts with the Wärtsilä 31DF engine, and the port injection concept provides rapid response for dynamic load control and operational flexibility. Both stepless and on-off type inlet and exhaust valve timing options are available to facilitate optimisation and the use of future fuels.
Rolls-Royce’s business unit Power Systems announced in 2021, as part of its sustainability program, that it would realign its product portfolio so that by 2030, new fuels and climatefriendly mtu technologies can save 35% greenhouse gas emissions compared to 2019. This near-term target plays a significant role in Rolls-Royce Group’s ambition to achieve net zero by 2050 at the latest.
Rolls-Royce Power Systems is evolving from an engine manufacturer to a provider of integrated sustainable solutions, offering solutions from bridge to propeller to marine customers. The Rolls-Royce business unit is also pioneering the development of methanol engines and already has hybrid propulsion systems for marine applications in its portfolio.
Next year, Rolls-Royce will release its mtu Series 2000 and 4000 marine engines for sustainable fuels. Following successful bench and field tests, Rolls-Royce will gradually be approving these engines for EN15940 synthetic diesel fuels from the beginning of 2023. These fuels include the sustainable fuels biomass-to-liquid, hydrotreated vegetable oil/renewable diesel (HVO) and power-to-liquid fuels such as e-diesel. This will enable the reduction of CO2 emissions from existing diesel engines by up to 90%, compared to the use of fossil diesel, without any changes to infrastructure.
“This means that the new generation of Series 2000 and 4000 engines, that currently account for around 85% of our sales revenues, will be qualified to run on second-generation biofuels and on e-fuels,” says Denise Kurtulus, Vice President Global Marine at Rolls-Royce Power Systems.
Future versions of the mtu Series 1163 and 8000 large marine engines, which will meet IMO Tier III standards with mtu SCR systems, are also to be approved for use with sustainable fuels.
Rolls-Royce recently signed a Memorandum of Understanding with renewable fuels producer Neste to build a strategic partnership on the implementation of sustainable fuels for diesel engines. Rolls-Royce is also investing in power-to-x production facilities.
Rolls-Royce’s service strategy for the future includes augmented reality (AR) technology that acts as an onboard digital assistant. It presents the functioning of propulsion and energy systems in an easy-to-understand way through a combination of text, animations and videos. To assist with maintenance and repair work, the AR system projects information onto physical hardware. The AR system can also show where components are located, for example sensors that have triggered an error message, and guide the user there.
“As part of our transformation into a provider of integrated sustainable solutions we strive to deliver complete propulsion and control solutions from bridge to propeller to our marine customers,” says Kurtulus. A key element of this is the automation portfolio mtu NautIQ which includes a range
of platform management and vessel control systems. The core product of the new automation portfolio is mtu NautIQ Master: a fully integrated, turnkey automation solution. Kurtulus says this makes Rolls-Royce the only propulsion manufacturer in the world to supply the electronic platform for monitoring and controlling the entire vessel.
The system can be expanded to include the Equipment Health Management (EHM) system mtu NautIQ Foresight. It monitors the technical condition of an entire ship by collecting and evaluating data from mtu and third-party components. This enables predictive maintenance before a component fails. The EHM system is currently undergoing sea trials on board of high-speed catamaran Halunder Jet.
Recent additions to the mtu NautIQ portfolio are the mtu NautIQ CoPilot, mtu NautIQ CoOperate and mtu NautIQ CoDirect products as a result of the company’s cooperation with Sea Machines Robotics, a developer of autonomous control and remote-vessel command systems. The systems offer different levels of intelligent crew support, autonomous control, and remote command capabilities.
Yanmar Power Technology increased its digital offerings earlier this year with the introduction of its proprietary SCR system with connected functionality and a dedicated management app for smartphones. The control panel of the SCR system has a USB port that can be used to connect it to a smartphone, allowing onboard information to be stored in the cloud through a dedicated application. The app also makes it possible to check performance diagnosis results and maintenance timing notifications even in shipboard environments without Internet access. Yanmar noted in August that it had received orders for over 2,200 units of its SCR system. The catalytic reactors can be used on Yanmar’s
Make the most of marketing & PR support from Seawork, Maritime Journal and our leading commercial marine magazines, in print, online, eNews and via social media.
Showcase your latest innovations in vessels, equipment and services to an international audience of over 100,000 all year on Seawork.com
Seawork & Marine Civils exhibition encompasses 12,000m2 of halls featuring 600 exhibitors and over 70 vessels and floating plant.
Features include the European Commercial Marine Awards (ECMAs) and Innovations Showcase.
The Seawork Conference programme offers opportunities to explore the challenges, changes and emerging opportunities in today’s and tomorrow’s commercial marine and workboat sector.
As we approach the deadline for ballast water treatment systems (BWTS) to be fitted the industry may be starting to breathe a sigh of relief that we are approaching the end. But, as questions remain about maintenance of systems, the ongoing supply of parts and how the convention with be enforced, it looks set that ballast water treatment will still be a hot topic even after the deadline for installation has passed, writes Samantha Fisk
It still seems that there are a lot of questions about BWTS and told some shipping crews may still be scratching their heads about the operation of these systems. A new company has launched on the market that looks to help ease the installation and operation of BWTS. Simplify Ballast is a consultancy that looks to be a bridge between crew and equipment suppliers. Mark Riggio, founder of Simplify Ballast explained that over the years that he worked in the ballast water treatment market one of the glaring problems in the market has been that crews have not understood ballast water treatment systems that have been installed on vessels, either their operation or the value of them for upcoming regulations.
The issue that he notes with this has been that BWTS have not been set up properly and especially now when systems that may have been installed but have laid dormant are now getting switched on, problems are now starting to appear. He notes that crews don’t have the necessary technical knowledge about these systems “there’s only a small knowledge of technical specs, but it takes a certain level of knowledge to operate these systems efficiently”, he explains.
Bio-UV also highlights that a particular challenge is the after sales service and commissioning requirement. 2022 has been a peak year for system installation and commissioning, and whilst it expects system acquisition to slow, commissioning will remain strong throughout 2023. As more systems are installed and enter operation, the maintenance and service market will evolve, with BWTS manufacturers delivering more after sales solutions, such as onsite support and annual performance checks. To meet market demand, the company has already increased its service network to 20 BIOSEA certified service stations around the globe. This expansion will continue across all the key maritime hubs.
The technical complicity of installation of ballast water treatment systems means that installing and setting up of systems isn’t always as simple as just ‘plug-in and play’. This is where Simplify Ballast sees that it can help shipowners with technical advice about the installation and set of BWTS.
Bio-UV also notes that there are still challenges in the market around the supply chain and component shortages. Maxime Dedeurwaerder, Business Unit Director, Bio-UV comments
that: “As a BWTS designer and manufacturer we can better overcome these challenges due to the more standardized nature of the BIO-SEA System. We have also optimised the performance and size of our UV reactors, reducing the number of components required without impacting performance.”
With more consolidation on the horizon of equipment suppliers. Riggio also questions: “What are we going to do when the market shrinks, who’s going to support the existing market/ systems?” Adding to this he asks how the industry will deal with the supply of parts, especially when it comes to the filtration screens, which have been specifically designed for the purpose of ballast water.
One notable trend that Bio-UV is also seeing is the reduction in average required flowrate. Most of the vessels that still require a BWTS installation tend to be smaller ships.
As Riggio highlights there are a number of sectors that are not enjoying the challenge of fitting and using ballast water treatment, such as mid to large vessels, high flows and chlorination systems, mainly due to the complexity of the systems and technical knowledge needed.
Another growing industry concern is the compulsory sampling test requirement, Bio-UV are advising its customers on what they need to do to ensure compliance with the new ruling. As MEPC 79 looms on the industry with a potential convention renewal, concern around how sampling and testing will be carried out. Riggio notes that compliance monitoring solutions are near approval at the IMO and that Port States are driving this legislation. What is of interest is that BEMA (Ballastwater Equipment Manufacturers Association) has been brought onboard with the IMO, signalling to the industry that this is topic is not just for the short-term but looks to be with us for some time.
Dedeurwaerder notes about the upcoming challenges that to make sure that systems stay compliant they are now also recommending that ballast tanks are kept clean so that there is no further contamination that can get into the ballast water treatment systems.
He further highlights that about the adoption of technology that last year was hard to find slots for vessels, which they are now seeing ease up. The company is now starting to see the slow switch from installation to maintenance for its systems, and for this there is a trend for remote support.
The company is also seeing an upturn in the offshore market that a few years ago seemed to be failing, but now seems to be making a comeback. BIO-UV Group’s maritime division and its engineering partner 3C Metal have completed the at-sea retrofit installation and commissioning of a lowflow ballast water treatment system aboard Greatship Maya.
Greatship Maya is a multipurpose offshore supply vessel operated by Greatship Global Offshore service Pte Ltd (Singapore), whose ultimate parent company is the Great Eastern Shipping Company in India.
A BIO-SEA L03-087 modular unit was successfully installed while the 4350dwt ship-maintained rig supply operations offshore Labuan, Malaysia.
Dedeurwaerder explains that: “Together, we surveyed the site, taking 3D scans of the ship’s machinery spaces to simplify pipework, electrical wiring, system integration and installation. This also revealed some space limitations which ensured we were able to design and build a ship-specific solution, allowing 3C Metal’s team to get the BWTS in place without modifying the steel structure in any way.”
All pre-installation pipework was done in parallel with the design and production of the BIO-SEA system, with 3C Metal’s facility in Johor Bahru, Malaysia, fabricating the piping, structural, hydraulic, and electrical connections needed for the project. All components were shipped to the vessel’s port of call prior to ship loading and integration. Inservice installation meant the vessel was able to continue its normal operations throughout the retrofit.
While an “L” Series BIO-SEA unit is recognised as having one of the smallest footprints of any ballast water treatment system in the market, its small size,
however, does not affect the high performance of the system, as Florian Cortes, heading technical operations for BIO-SEA by BIO-UV Group, explained.
“During preliminary work it was identified that the ship’s pumps would also be used for transferring liquids other than ballast water, such as water from drilling operations. But after studying the vessel’s different operational requirements it was found that in ballast mode, the pumps would not be required to run at their full rated capacity of 300m3/hr. 87m3/hr was sufficient. This allowed us to offer a smaller BIO-SEA system that would otherwise have been specified. This resulted in an easier integration and a more costeffective retrofit solution for the end user.”
Although afloat installations do take longer than those carried out in drydock, the arrangement shaves thousands off the total cost of a ballast water treatment retrofit project. “That’s the benefit of an in-service integration,” said Jordan Laurans, Group Operations Manager, 3C Metal. “When you consider drydock hire and the number of people involved, together with the financial losses incurred due to vessel offhire time, then an at-sea installation makes complete commercial sense. The ship continues operating.”
Greatship Maya is a DP II MPSSV built by Singapore’s Keppel Singmarine. When delivered in 2009, the vessel was one of the first to be built in accordance with the then new Special Purpose Ships Code. The vessel can store 1,140m³ of potable/fresh water, 1,140m³ of fuel oil, 1,530m³ of ballast and 1,310m³ of drill water.
Riggio highlights that “for ballast water it is only just beginning. Systems now are going to have to work”, he advises the market that “look where you’re going (sailing) and buy for the worst place that you are going to.”
The challenges around ballast water treatment are not going away soon. Whilst the deadline to have systems fitted may be close by the questions around operation and sampling still stay ever present for the market. It will be important for the industry to get this right and not just try and throw a blanket over it, otherwise as Riggio notes could ended being an expensive exercise for the industry.
8 A skid-mounted BIO-SEA modular reactorOne of the highlights of the first day of The Motorship Propulsion and Future Fuels Conference 2022 was a high-level discussion about the implications of the upcoming introduction of onshore power supply (OPS) requirements across the EU’s Core TEN-T ports by 2030.
Rather than altering the market economics to incentivise shipowners to use ‘cold ironing’, the proposal will introduce requirements for cruise vessels, passenger vessels and container vessels to begin to use shore power connections by 2030, subject to various exemptions for vessels making infrequent calls to European ports.
The panel brought together Torsten Schramm, President Maritime, DNV, Martin Kröger, the ceo of the VDR (German Shipowners’ Association), Valter Selén, a Sustainability Advisor from ESPO, and Kai-Dieter Classen, Deputy Director External Affairs at the Hamburg Port Authority (HHA).
Kai-Dieter Classen, Deputy Director External Affairs at the Hamburg Port Authority (HHA) shared the port of Hamburg’s experience as an early adopter, with the port investing over EUR100 million in the electrification of its container terminals,
One of the obstacles to extending the scope of the EU’s onshore power supply has been the difficulty in attracting investment into the development of those systems. This is partly because supply and demand relationships have yet to develop, because of the lack of demand certainty from shipowners.
Batista added that the failure to develop viable business cases for onshore power supplies until now is underlined by the lack of grid capacity even in ports that have installed OPS connections.
The slow uptake of OPS usage, outside Scandinavian countries that impose higher emissions charges for portside emissions, since 2014 has encouraged the EU to impose requirements for OPS installations, rather than rely on market forces to drive adoption.
Batista noted that the requirements are included in the Alternative Fuel Infrastructure Regulation (AFIR), the Energy Taxation Directive (which establishes taxexemptions for electricity supplied at berth) and under the ETS (where electricity is treated as zero-emission).
Batista concluded by noting that shore power projects were eligible for funding from the EU’s Connecting Europe Facility II (which closed in January 2022), and in the EU’s larger EUR672.5 billion Recovery and Resilience Facility (RRF).
Applications could be made to smaller funds dedicated to zero-emission shipping, such as the Alternative Fuels Infrastructure Facility (AFIF), and Horizon Europe’s Zero Emission Waterborne Partnership, Batista concluded.
The EU agreed to earmark at least 20 million ETS allowances (equivalent to EUR1.5 billion at current ETS carbon prices) from the EU Innovation Fund, which is financed by revenues from the EU’s Emissions Trading System, for maritime projects in late November 2022.
which is expected to be completed by 2028.
However, Classen noted that the high cost of electricity represented a barrier to adoption, with demand from customers lagging behind the installation of supply, which had been enabled by generous national grants.
The challenge of developing commercial models for OPS supply would be helped if the EU committed to extending the current tax-exempt status on electricity supplied over the longer term.
The issue of penalties was raised by Martin Kröger, who noted that there was a risk that ship operators might be declared to be non-compliant if shore power connections at the port are unavailable or not functioning as a particular issue. Batista responded that the regulations had been designed to encourage the adoption of zero-emission at berth technologies more widely, rather than narrowly focusing on OPS adoption.
The decision to apply a zero CO2 emission rating to electricity supplied via an OPS was similarly deliberate, although the regulations might allow subsequent modification to recognise the carbon footprint of the electricity generated, Batista explained.
The EU has previously estimated the cost of installing OPS systems across the Union’s TEN-T port network at over EUR7 billion by 2035.
The panellists discussed the need to invest in strengthening power supply availability and stability, and the need for national grid operators to strengthen connections to ports. The ESPO represent-ative identified issues related to the installation of electricity capacity and as well as grid infrastructure availability in TEN-T ports’ hinterlands as key areas of focus in the proposals. Selén called for the EU to include these issues in its FuelEU Maritime proposals.
More widely, there remains an absence of detailed demand-models, whether on a port-level, regional-level or national-level for OPS demand in the future. The lack of visibility about potential future demand for electricity at a port level was identified as a key vulnerability for ports seeking to attract investment into expanded grid connection capacity.
Despite rapid advances in alternative fuel developments and fuel efficiency, the 43rd Propulsion and Future Fuels Conference continued to be dominated by regulatory discussions.
At a time of unparalleled technological development within the maritime technology field, the 43rd Propulsion and Future Fuels Conference offered an opportunity for the industry to take stock of the latest technological developments in the fields of fuel efficiency and alternative fuels.
PFF also covers regulatory developments at both an EU and IMO level, as such developments play an important role in driving investment decisions.
These developments were reflected in our conference programme, with our first day opening with a high-level discussion about the implications of the upcoming introduction of OPS requirements across the EU’s Core TEN-T ports by 2030.
The opening session of our second day returned to the topics of regulatory developments relating to carbon pricing with Chris Waddington, Technical Director, ICS and Sebastian Ebbing, Technical Advisor at German Shipowners’ Association (VDR) discussing the development of proposals at the IMO for market-based measures (or economic instruments) and the evolution of EU proposals to introduce the extension of the EU Emissions Trading System. Comparing the evolution of submissions between ISWG GHG 12 and ISWG GHG 12, Waddington noted that there had been a clear movement towards a fund and reward scheme, often in combination with a separate Global Fuel Standard.
Meanwhile, a stimulating panel discussion saw questions raised about the timing of the introduction of the ETS with member state ratification likely to delay its introduction until 2024. Interestingly, the discussion aligned closely with the final phase-in agreement reached a week at the end of November, starting from January 2024, will see shipping companies pay allowances that cover 40% of their emissions in 2024, 70% in 2025 and 100% in 2026.
Turning to the technical content covered in the conference, the rapid pace of technological change in the industry in the last 18 months meant that there was shortage of developments to follow, with parallel sessions on the second day of the conference looking at ammonia, methanol, e-fuels, sustainability and retrofit solutions among others.
Among the most enjoyable presentations were Franciska Kjellström of Alfa Laval, who provided a detailed overview of fuel separation, flow control, fuel change-over, filtration and connectivity issues relating to biofuels, and Harriet Brice of Lubrizol, who provided an additive supplier’s perspective on research into lubricant solutions, touching on challenges for lubricants formulated for ammonia and biofuels.
Delegates with an interest in methanol enjoyed Dr GwangHyeon Yu of HHI outlining the progress achieved by HHI’s H32DF-LM engine since its recent launch, booking over 70 orders, while Claes Tretow, Project Manager Newbuildings, at Stena RoRo AB provided a useful case study of the
operational results achieved by two vessels operating on methanol in the last 6 months. He caught the audience’s attention when he told them that by operating on 100% methanol with biodiesel as a pilot fuel, Stena RoRo expects to achieve zero emissions.
The ammonia session was a highlight of the conference, providing a high-quality discussion on the latest developments in the ammonia engine space. Kristian Mogensen, Promotion Manager, MAN ES confirmed that the first full scale engine test for MAN’s 2-stroke ammonia engine has been delayed until early 2023, while René Sejer Laursen of ABS provided a note of realism, outlining progress in recent ammonia-fuelled propulsion designs, but identified a number of wider ammonia safety issues, such as the longterm effects of exposure to low concentrations of NH3, or ammonia dispersion upwind of ports as worthy of further study. Dr Andreas Schmid, General Manager Technology Development, WinGD was compelling as he discussed WinGD’s progress towards bringing a dual-fuel ammonia engine to market by 2025.
Elsewhere, it was interesting to listen to how i-Tech’s nonbiocide hull coating solution continues to deliver positive results in the hull coatings market. Hull fouling remains the low hanging fruit of decarbonisation: reducing fouling could help to reduce emissions by up to 19% per year.
Stam Achillas from Wärtsilä’s 2-Stroke Fuel Conversions team in Switzerland focused on the fuel efficiency opportunities presented by derating engines in older vessels, a subject to which The Motorship hopes to return.
Despite the range and depth of the content presented at the conference, The Motorship Propulsion and Future Fuels conference remains a welcoming event, offering a combination of in-depth technical content, knowledgeable industry participants and a friendly collegiate atmosphere.
8 The MarketBased Measures panel discussion was particularly topical at PFF.
At the end of November, Maersk announced it was shuttering TradeLens, the cargo platform co-developed with IBM, which once promised to revolutionise the way cargoes moved around by leveraging the distributed ledger system, blockchain. TradeLens will finish operation in Q1 2023, a Maersk announcement revealed, mere days before this issue went to print.
The distributed ledger system was envisioned as a way to cut down on paperwork, shipping’s preferred method of exchanging documents between vessels and ports. It would also provide a trust framework wherein no third party could tamper with documents, making shipments impervious to cargo thefts, smuggling, misdeclaring, and other problems.
Blockchain used to enjoy a reputation as a potential solution to issues in fuel quality, the provenance of biofuels, electronic logbooks, measuring ship emissions, crewing, training, classification and so on. Despite high hopes that blockchain would drive transformational change in business processes by offering security and integrity, wider issues have slowed the expected revolution.
In TradeLens’ case, there was scepticism about its independence from the beginning. How could Maersk -- not just any shipping line, but the world’s largest -- possibly be considered a neutral party and broker? However, this did not stop Hapag-Lloyd, Ocean Network Express (ONE), CMA CGM and MSC from signing up, not as users of TradeLens, but as trusted partners, or ‘trust anchors’ as they were originally described, pledging to allow cross-compatibility with their own systems.
In 2019, as his company signed up, ONE MD Corporate & Innovation Noriaki Yamaga said that its involvement would give ONE “…opportunity to drive greater innovation across the shipping supply chain,” and “to provide our leadership and insight to help the platform continue to evolve.”
For TradeLens, things progressed well, if a little slower than expected, well into 2020. But as pandemic year 1 drew to a close, something was happening with blockchain. Bitcoin, a cryptocurrency which runs on a blockchain architecture, was beginning to hit the headlines daily, because the price of the coins was skyrocketing, turning early adopters into multi-millionaires.
This put bitcoin, a fundamentally marginal use case for blockchain, at the forefront of its public perception, leading to associations between blockchain and highly speculative consumer behaviour that have continued until the present.
But TradeLens was still not picking up the kind of traction it would need. The nature of the network meant that its usefulness depended on widespread adoption. More than 20 ports had signed up to be part of the network, but that was still too little, and activity remained slow on the customer side. Maersk, meanwhile, was, like other liner giants, becoming a victim of its own success, generating huge profits from its ship operations, but infuriating governments and authorities in the process. TradeLens’ development partner, IBM, had reportedly begun to put further investment in the project on hold.
Meanwhile, as the crypto boom began to bust, the darker side of bitcoin – still the de-facto blockchain focus – became more widely known. These range from concerns about spiralling energy consumption associated with the ‘mining’ of cryptocurrencies, through to the current repercussions from the collapse of crypto-currency exchange FTX Trading.
Through no fault of its own, then, blockchain’s reputation became tarnished by the pump-and-dump silliness of its loudest and most troublesome offshoot. The word ‘blockchain,’ no longer the shareholder magic-dust it had been, started to disappear from companies’ marketing materials. This left only those such as TradeLens, which had actually believed in the technology and attempted to apply its benefits in earnest, to a real-world problem in want of a solution. Tellingly, in late 2021, when DP World launched its own platform to compete with TradeLens, any mention of blockchain was conspicuous by its absence.
In his November post-mortem, Lars Jensen, who left Maersk Line in 2010 and now works as the CEO of consultant Vespucci Maritime, called TradeLens a “child born out of the blockchain hype seen [in 2017].”
It was not an only child, however. GSBN, a Chinese rival to TradeLens which began in 2018, remains extant. Indeed, Jensen does not appear to have condemned blockchain in principle; like Maersk and its partner IBM, he seemed to suggest that it could, in the right hands, bring tremendous value to the maritime industry. “…it is an indication,” he said, “that it is commercial usage which determines the fate of new technological initiatives and not the sophistication of the technology employed.”
8 A new paradigms? The introduction of transformational technologies has often been accompanied by booms and busts in the past, ranging from canal construction in 18th century England to US railroad expansions in the 19th century
A Finnish project called INTENS – short for Integrated Energy Solutions to Smart and Green Shipping – that included 14 partners and which was concluded in the summer of 2021 gave Deltamarin, the consultant naval architect company, an opportunity to refine and build on digital models, said Mia Elg, R&D Manager at the company
The project allowed digital testing of various parametres of a test case vessel, an Aframax tanker, on various routes and in different weather conditions to monitor the vessel’s fuel consumption. Compared to a traditional “datasheet” representation of a ship’s main characteristics and performance values, the digital model revealed also realistic pattern of typical main engine loading conditions.
The project team developed a digital design portal for showcasing the differences in both approaches. In addition to the digital design tool development, another aim for the project was to find ways to optimize various aspects of the ship’s equipment and as the number of fuel saving devices and other new technologies onboard will increase, the more complex such an optimisation would become, she said.
During INTENS project, Deltamarin also worked with researchers from Technical Research Centre of Finland (VTT) and developed together with them a method for utilising an existing energy simulation model of a ship for optimisation. The work focused on identifying optimal configuration of batteries and waste heat recovery equipment for passenger ships, considering fuel consumption, capital expenditures and engine running hours.
Compared to traditional energy simulation work, where a limited number scenarios are manually chosen and analysed, this multi-objective optimization framework allows studying thousands of possible combinations of processes.
The chosen method of simulation also allowed the team to assess if the chosen path of optimisation really was the right one and it brought to surface some aspects that might not have been noticed without the use of a digital model.
After INTENS, Deltamarin joined a project team working under the headline CHEK (deCarbonising sHipping by Enabling Key technology symbiosis on real vessel concept designs), which proposes to reach zero emissions shipping by reconfiguring the way ships are designed and operated today.
The aim of the EU funded project that entails 11 organisations is the development of two bespoke vessel designs – a wind energy optimised bulk carrier and a hydrogen powered cruise ship – equipped with a combination of innovative energy technologies working in symbiosis. “The ambition of the project is to reduce greenhouse gas emissions
by 99%, while achieving a reduction of energy consumption by at least 50%,” the project team said in a statement.
The new project that started in the summer of 2021will pay attention to how to maximise ship energy efficiency with the combination of operational improvements, smart design and the technology mix– a question of growing importance as the environmental legislation will tighten in the years to come, Elg pointed out.
“Only a decade ago, designing a bulk carrier would have been quite simple as slow speed diesel would have been an obvious propulsion choice. Today the palette is much wider – everything from sails to battery packs will have to be considered,” she told The Motorship
Although much has changed, the basic fundamental of ship design remains intact: a good hull design lays the foundation for an energy efficient vessel. “We should not be distracted from the importance of a good basic design, it is more important than various energy saving devices etc. A good hull is not more expensive (to build) than a bad one,” Elg noted. What is new today is that in all ship design the modern tools give us the opportunity to optimise the design to several operational conditions, instead of traditional single design points.
Digital model should focus on key factors, can help to assess ship’s performance
Digital modeling can provide designers a robust platform on which to build a successful design, but Elg said it is important to understand how the model itself should be built.
“At the concept stage, it shouldn’t be too detailed, yet it should contain the parametres that are relevant at that stage,” she said. As the work progresses, new parametres should be added along the way –hence Elg’s preference of the description of digital model as “thread” rather than “twin.”
Martin Stopford, the British shipping economist, recently said that due to the fragmented nature of the shipping industry, many owners may not have the financial and personnel resources to undertake the work needed to meet future challenges to comply with tightening environmental legislation.
Elg pointed out that digital models can help owners to assess the performance of their ships. They can produce a benchmark for operational data against which actual data accrued from the operations of the vessels can be compared.
8 Mia Elg – R&D Manager at DeltamarinIf analysis of the data reveals deviations between modelled data and data collected onboard, the owner can identify the reason for the deviation and direct the crew towards an answer to put things right if needs be.
A digital model can also help the crew to understand how the various pieces of energy saving devices onboard should work and how to use them so that they will optimize the performance of the vessel, Elg pointed out, but noted that providing day-to-day or real time energy management would not be part of Deltamarin’s business portfolio in the years to come.
Rather, Deltamarin’s approach could be utilised for training purposes and, for example, shortening the learning period what the crew has after starting to operate a new ship with potentially much new technology onboard.
Digital modelling should not aim at perfection in how it
describes the physical vessel, but rather highlight and focus on parameters and details that are relevant at each stage of the design, considering the ship operation. An equipment supplier can have a highly detailed digital model of that particular piece of equipment, but this does not mean that it would entail all the aspects of its use onboard the ship in various conditions.
However, the model too will need updating as the ship receives new equipment over its lifespan: the thread built earlier should not be broken at this point, but the model should continue to produce data to verify the performance of the ship, Elg concluded.
8 Researchers from LUT University worked on the development of a digital twin for an Organic Rankine Cycle (ORC) heat recovery system. (Credit: LUT University/Timo Mikkola)
Only a decade ago, designing a bulk carrier would have been quite simple as slow speed diesel would have been an obvious propulsion choice. Today the palette is much wider – everything from sails to battery packs will have to be considered
But, owing to the supply chain instabilities which have granted huge bonuses to carriers at the expense of their customers, live container tracking has branched out into dry containers. This year, consultancy Drewry estimated that by 2026, around 8.7m boxes – some 25% -- will be fitted with tracking equipment.
“Once the disruption eases, carriers are going to have to start fighting to keep their customers,” said Martin Dixon, Drewry Head of Research Products.
And well into the resumption of normal service across ports and a normalisation – or even, a precipitous plunge – of freight rates, fighting they certainly are.
By way of a value-add, Hapag-Lloyd has committed to fitting tracking devices across its entire fleet of containers, a process which began in August this year. At the time, Andrea Schöning, Hapag-Lloyd Senior Director Container Steering, said: “Digitalising our entire container fleet will be a challenging task. We are now making the first steps of a large-scale project. In this first rollout phase, it will be important to streamline all processes together with our IoT partners so as to achieve the technology’s full potential.
“At the same time, we aim to make this product quickly available to our customers, as they require and increasingly expect these kinds of digitalised solutions,” she added.
The Hapag-Lloyd announcement would be the first of many, Dixon indicated. “Our view is that other carriers will be forced to follow suit; not all of them will, and some carriers will move faster than others, whether it has to do with their finances or their willingness to invest.”
Of interest is an incidental benefit to the trackers. Manufacturer Orbcomm has a specialised tracker for reefer containers, which is capable of monitoring the temperature inside the container. But Orbcomm’s CT 1000 tracker – the one being fitted to Hapag-Lloyd’s dry containers – retains some of this temperature monitoring functionality, affording
the ability to keep track of ambient air temperatures around the unit itself.
This is not a bad way to determine whether a container is on fire. Thanks to an increase in the number of lithium-ion batteries being transported, fires in general appear to be on the up; an analysis by Allianz, comparing insurance claims in the period 2017-2021 versus a previous 2013-’18 analysis found that fires are now making up 18% of claims, versus 13% formerly.
One of the reasons it is so difficult to fight fires on a ship is that a lot of damage can be done before any smoke makes its way out of a container to a smoke detector. This means that a container might be red-hot and several of its neighbours already ablaze before the crew know anything about it.
For this reason, having a container fitted with continuous temperature monitoring could be useful – though Al Tama, Orbcomm GM of Container and Port Solutions, stressed to The Motorship that it is not a headline benefit, and Orbcomm is not selling the CT 1000 as a fire-prevention device. It “measures ambient air temperatures around the container to detect if external temperatures are moving out of range for the goods carried,” told The Motorship. “While this may assist in fire detection, it is not designed overtly for that purpose.”
The system does promise to improve transparency, however, once the worst has come to pass. “Complete asset tracking ability helps to flag damages, fill important information gaps and provide visibility to insurers to reflect the value of safe ship operations and good cargo practice in their premiums or to assign liability when claims are made,” Tama Explained. “With shock detection as a standard feature, tracing the root cause of an incident can become easier. By showing location, operators can see where any shock impacts occurred. Placing liability correctly becomes less onerous than conventional resource-heavy insurance claims.”
The rise of container telemetry in the reefer field was inevitable, as with some cargoes, namely pharmaceuticals, temperature-controlled single containers worth $50m or more are commonplace.
The two largest bunkering hub ports in the world are Singapore and Rotterdam -- though it is hardly close, as the former tends to outstrip the latter by a factor of four times or more, with Fujairah not far behind.
But despite the disparity, it is clear that the two recognise one another as counterparts, and have collaborated on a number of joint projects, a recent example of which comprises a new agreement for green shipping corridors, as well as so-called ‘digital’ corridors, signed in August.
The initiative marks a joint pledge to bring low- and zerocarbon fuels to bear on the routes between them, as well as initiate the use of new digital tools concerned with optimising arrival times and port stays, helmed by partners the Digital Container Shipping Association (DCSA).
But another sense in which Rotterdam is attempting to bring itself up to par with Singapore is in respect of leveraging technology to force improvement in the bunker market. At Rotterdam, expert Blue Insight calculates that the actual fuel provided to vessels may be falling as far as 3% short of what is being paid for.
Given that the cost of bunker fuel this year tripled since the beginning of the pandemic, in line with the oil price – and the cost of bunkering will most likely spiral as new and lessabundant alternative fuels hit the market – the Port of Rotterdam has decided that this disparity can no longer be tolerated. To tackle it, it will borrow a strategy from Singapore’s Maritime and Port Authority (MPA), mandating the use of a strange machine – the mass flow metering system (MFMS).
MFMS’ have already been in use at Rotterdam since 2018, when ExxonMobil began to supply them. The systems improve on tank dipping, a process not unlike checking for engine oil in a car, prone to all manner of human misjudgement. At the time of the installation, ExxonMobil noted that an MFMS “depending on stem size… can help reduce delivery time by up to three hours, compared with conventional tank dipping.”
The MFMS is a U-shaped tube, which houses a pair of dangling cables. Along the length of these cables, evenly spaced, are pairs of electromagnets, which oscillate together as a liquid is pumped though the tube. Through the rhythm of these oscillations, quantified digitally, the ‘mass flow’ – a distinct measure from the volume flow – is calculated.
It is necessary to measure mass rather than volume, as thermal expansion means that bunkering the same fuel in hot or cold climes will entail taking on different amounts of liquid, even if it has the same energy content. One of the shortcomings of dipping is that it does not make this distinction. This, among other “old-fashioned, outmoded operational practices” left “inherent ambiguity” in the bunker supply equation which “…makes it difficult to track and report transactions with confidence and accuracy,” according to Kenneth Dam, global head of bunkering at TFG Marine, speaking in August.
With such a dominant bunkering sector it is little surprise that Singapore has been home to a certain level of grift
among its bunkering suppliers, and in response, the Port made use of MFMS mandatory in 2017. The industry is confident that this has had an effect. In February, a survey by the International Bunker Industry Association (IBIA) and BIMCO found that 76% of respondents credited MPA’s introduction of mandatory MFMS with a positive impact on bunkering in Singapore.
However not everybody was quite so delighted. Perhaps the best evidence of MFMS’ efficacy in straightening out fraudulent fuelling are the attempts to subvert it. In 2019, MPA revoked a license to operate from Southernpec, amid accusations the company had tampered with the mass flow meters using magnets. Two years later, nine people had been convicted to three years in jail each, for defrauding bunker buyers out of $337,000 worth of fuel.
Currently Rotterdam has 30 bunkering vessels equipped with an MFMS, out of a total of 170. “The Port of Rotterdam Authority has indeed conducted research into quantity issues in the Rotterdam bunker port…” and “intends to make the use of MFMS mandatory in Rotterdam,” said Tie Schellekens, spokesman for the Port of Rotterdam, in November, stating it would “make the market more transparent, efficient and reliable.
“However, it still requires a lot of preparation, but is well aware that such a measure has a major impact on the bunker market. That is why preparation time is still needed before the harbour master actually makes the commitment. The Port Authority expects to be able to communicate more about the intention by the end of the year.”
Next year it will be 30 years since the first Azipod® propulsion unit was installed on a merchant vessel - a retrofit on a 16,000dwt Finnish product tanker called Uikku – although the technology had been tested on a smaller government owned ship four years earlier
In the subsequent three decades, other manufacturers have also entered the azimuthing electric propulsor market. These systems now power a wide range of ships, cruise liners are perhaps the best known examples, but also product tankers, various types of offshore vessels, ships that operate in shallow draft environments and various kinds of naval ships also use them.
Marcus Högblom, Head of Passenger Segment, Global Marine Propulsion Sales, ABB Marine & Ports that produces Azipod® propulsion systems, said that the total number of units delivered and on order exceeds 700 and currently, over 300 vessels are featuring Azipod propulsion. “Azipod propulsion has enabled vessels of over 35 types to reduce fuel consumption by up to 20% compared to traditional shaftline systems over the last three decades.”
The shipping industry’s drive to switch to emission free energy sources provides an exciting platform for the future of this technology as many of the solutions on offer are based on the use of electric power. “With the electric system on board, the energy source, or sources – if multiple are used –are decoupled from the propulsion as such; and the energy is converted to electricity which can then be used by the propulsion units or any other consumers in a flexible way,” Högblom said, adding that
Azipod system was from the very beginning of its development designed as a future-proof system able to adapt to a multitude of energy sources.
Electrical power minimizes engine noise and vibration as well, ensuring a smoother, quieter ride. “Azipod propulsion is one of ABB’s ‘anchor products’, by which we mean key technologies for customer operations that are at the heart of a broader integrated electric system that can also include other ABB products such as generators, switchboards, transformers, drives and control systems,” he continued.
Azipod propulsion is available in power ranges from 1MW to 22MW. The maximum output of each unit is based on the vessel
design and operation. For each project, ABB designs a propeller tailored to the specific needs of the ship it will power. “For example, at the core of the new mid-range (7.5-14.5MW) Azipod units product line are the latest fourth generation permanent magnet (PM) motors developed by ABB.
These motors are structurally as sound as the well-proven Azipod units in smaller power ranges , but are optimised further with today’s mass-computing capacity and evolutionary algorithms to a) maximize electrical efficiency and b) minimize the use of expensive rare-earth elements needed to build strong permanent magnets,” Högblom told The Motorship.
For the ship owner this means that mid-range Azipod units with fourth generation PM motor will have extremely high electrical efficiency, typically 98%, at a competitive price.
Synchronous motors are used for Azipod units in the higher power ranges. The steering motors are of the asynchronous induction type or permanent magnet motors depending on the case and each is driven by its own, inverter type, steering frequency converter. The typical steering module configuration includes four motors, depending on the ultimate torque requirements.
Azipod system installation requires considerably less space inside the vessel than competing mechanical systems, yielding greater flexibility to optimize vessel design. “In addition, optimised installation of thrusters working with a pulling propeller increases the hydrodynamic efficiency of the vessel and reduces noise and vibrations. Connecting the propeller directly to the propulsion motor eliminates gears and other auxiliary equipment, meaning reduced maintenance costs and less down time due to faults in these systems,” Högblom stated.
Passenger vessels benefit from the performance provided by 360-degree rotating podded propulsors and reduced fuel consumption. Additionally, lower vibration and the flexibility of design allowed by locating propulsion motors outside, rather than inside the hull, prove compelling for passenger vessel owners. Ropax vessels are increasingly adapting
Azipod propulsion due to significant benefits it offers through fuel savings, improved schedule keeping through time savings in ports, and passenger comfort.
Högblom noted that the Finnish cruise ferry company Viking Line had decided to install two Azipod units in its 64,000 gross ton Viking Glory that was completed last year in a marked contrast to the 2013 built Viking Grace, which has shaft lines. A new step in the ferry sector is a recent letter of intent (LOI) ABB and the Australian fast ferry builder Incat signed to develop a hybrid ferry concept that would feature two Azipod units and have a top speed of 21 knots.
“Incat has a long history in building fast ferries that by necessity have had to be lightweight to reduce energy consumption at 30+ knots. Azipod, while new to catamaran ferries, is ideally suited to take the stored electrical energy and convert it directly to propulsion power while maintaining the maneuverability that e.g. Incat ferries are famous for,” Högblom pointed out
Ferries powered by battery packs are an increasingly interesting sector for ABB as the rapid development of battery technology will make them an attractive option to a widening range of operators: for example, the Incat concept design will have a range between 50 and 60 miles, Högblom said, adding that ferries with hybrid propulsion systems are another growing area of interest.
Azipod units can be installed on vessels that have not been designed with such an installation in mind, but Högblom said that he would highly recommend that owners design a vessel from the start for this type of propulsion. It will allow them to reap a few additional percent in energy saving compared to an installation to a vessel whose design has not been optimized for Azipod system.
However, there are also other significant factors that support the tailored approach. Utilization of space in the engine room and areas that surround it can be optimized when a vessel is designed from the start to use the Azipod technology. This again can have implications for other aspects of the design, such as crew quarters on a cruise vessel or car decks and freight capacity of a ferry.
A 3,000 lane metre capacity roro vessel can have some 15% more freight capacity if Azipod units and batteries are used and the design has been optimized for them compared to a diesel electric vessel with shaft lines – or an Azipod system installation without the optimization of the design. In case of vessels with battery pack propulsion such optimization of space utilization can be highly significant, Högblom pointed out.
The use of an azimuthing, electric propulsor does mean a higher capital expenditure than what is the case in a traditional mechanical power train. However, as electric power is becoming increasingly used to drive ships, the gap is narrowing. Another aspect is the increased space for passengers and cargo that can be made available plus the lower cost of maintenance than this type of system requires compared to traditional power trains.
Looking ahead, Högblom said ABB continues to develop the Azipod propulsion family to increase efficiency and to meet the needs of various power ranges in the market, building on the competence and experience gained during the 30 years of vessels powered by Azipod propulsion.
“For example, ABB has been conducting pioneering research and development in the area of underwater noise pollution for over a decade,” he said. To reach lower underwater noise levels, propeller blade cavitation, propeller loading and characteristics of converter voltage supply waveform must be
taken into account. “With its silent electric motors, ABB’s Azipod propulsion minimizes engine noise and vibration. Moreover, thanks to the enhanced maneuverability, vessels can save time while docking in ports and sail with lower speed from at sea – making less noise,” Högblom concluded.
A number of other companies also manufacture azimuthing thrusters and podded propulsors. Schottel, the German supplier of propulsion technology, has recently unveiled its M- series azimuthing thrusters that it offers with an output of 640kW, 850kW and 1,000kW. “The azimuth modules are available for Z-drives, L-drives and ZY-hybrid drives, making them suitable for horizontal electric, vertical electric or combined direct engine plus horizontal electric motor connection. Thus, the M-series thrusters are also compatible with hybrid solutions,’ the company said, adding that e.g. ice class rules have been updated in the new M-series.
In Norway, Kongsberg Marine has launched a new product in its Azipull range, called Azipull-PM (AZP-PM) It features essentially the same underwater unit as the conventional Azipull, but with a vertical shaft permanent magnet (PM) motor integrated into a new upper unit. The PM motor maintains a very high efficiency over a wide speed range, the company pointed out.
“Combined with the proven high propulsive and hydrodynamic efficiency of the Azipull this will be a winning combination, especially as there is a further small gain in mechanical efficiency by eliminating the upper gearbox,” Kongsberg Maritime said. Furthermore, pace requirements in the thruster room are reduced as the thruster is compact, the PM motor lying within the diameter of the mounting flange giving a small footprint and avoiding the complication of a coupling and foundations for the separate motor of a conventional Z or C drive electric configuration.
“First to be introduced to the market is the AZP-PM L-drive 120 size, rated at 1,800 - 3,500kW continuous. This will be followed by two smaller frame sizes, 085 and 100, and one larger, the 150, so that this azimuth thruster series will in due course span a power range from 900kW to 5,000kW. They will cover the speed range up to 24 knots,” Kongsberg Maritime noted.
Azipulls with CP propeller for Scandlines ferry Kongsberg Maritime will deliver a Azipull thrusters with controllable pitch propeller to a 147 metre hybrid ropax ferry Scandlines is building in Turkiye for its Rodby Havn- Puttgraden service. The thrusters will be delivered with controllable pitch (CP) propellers, in an L-drive configuration with an integrated permanent magnet drive motor. This increases overall energy efficiency while reducing noise and vibrations, as well as reducing the physical footprint of the thruster system compared to previous deliveries,” the company said.
Anette Ustrup Svendsen, Head of Corporate Communications at Scandlines, said that the company and Kongsberg Maritime have a long history of cooperation, but that this would be the first time thrusters with CP propellers.
“The advantage of CP is greater bollard pull, which is required for port maneuvering, as well as the ability to optimise propeller efficiency for different speeds,” she told The Motorship. will be able to make the 11 mile crossing in 75 minutes on electric power at a speed of 10 knots or in 45 minutes at 16 knots on hybrid power.
Bastion of French commercial shipbuilding, Chantiers de l’Atlantique, has handed over the largest cruise ship to date powered by LNG-fuelled engines, writes David Tinsley. The 215,863gt MSC World Europa also features an LNG-fed fuel cell that will serve as a technology demonstrator.
Described by Swiss-based MSC Cruises as an “ultra-modern metropolis at sea”, offering capacity for a maximum 6,762 passengers, the 333m vessel has given first form to the company’s seminal World-class generation. Three further newbuilds of the type are on the books at the Saint-Nazaire yard, occupying delivery slots in 2024, 2025, and 2027.
Aside from the considerable scale economies manifest in the design, the builder claims that MSC World Europa is “the least emitting ship of the entire cruise industry”.
The power plant is based on five 14-cylinder models of the Wartsila 46DF medium-speed engine, suited to either LNG or low-sulphur marine diesel oil. As the nominal maximum rating for the V14 is 16,030kW, the installation has a potential combined output capacity of 80,150kW.
By incorporating proprietary selective catalytic reduction(SCR) technology, whereby a Wartsila NOx Reducer(NOR) unit is fitted on each engine, NOx emissions will be cut by 90% when in diesel mode. The reduction is similar to that obtained under operation on LNG, such that the vessel is capable of meeting IMO Tier III criteria at all times. Two storage tanks and associated supply systems are provided for the LNG fuel.
The 150kW solid oxide fuel cell(SOFC) will act as a testbed at sea, to accelerate the development of the technology for contemporary cruise ships and raise the prospect of such hybrid propulsion options in the future.
The plug-and-play fuel cell plant, which will run in parallel to the auxiliary power system, has been supplied by Bloom Energy Corporation, and is fitted in a 40ft container. It is expected to yield around 60% electrical efficiency, and cut greenhouse gas(GHG) emissions by some 30% relative to an LNG dual-fuel genset.
“We anticipate that SOFC will reduce emissions of greenhouse gas(GHG) substantially compared with conventional LNG engines, without producing emissions of NOx, SOx or fine particles,” stated MSC Cruises’ vice-president Linden Coppell, adding “It also has the advantage of not only being compatible with LNG, but also with low- and zerocarbon fuels such as green methanol, ammonia and hydrogen. We could in the future transition to synthetic LNG or other, alternative non-carbon fuels.”
The multi-engine prime mover installation, feeding electric motors acting on two propulsion shaftlines, provides the flexibility and associated energy efficiency to support the operating profile and load requirements characteristic of high-capacity cruise ships. Efficacy and precision in rotating the hull in all conditions at confined berths and in restricted fairways is conferred by a total of seven manoeuvring thrusters at bow and stern.
The hull form has been optimised to minimise resistance, and the raft of other measures adopted to save energy and running costs include ‘smart’ ventilation and air-conditioning systems, with automated energy recovery loops allowing
effective distribution of heat and cold throughout the ship. LED lighting is universal onboard, controlled by ‘smart’ management systems.
MSC has also invested in remote energy monitoring and advanced analysis, enabling real-time shoreside support to maximise operational efficiency onboard. As with all MSC newbuilds, the latest vessel is fitted with the means of drawing power from the landside grid when berthed in ports that have suitable infrastructure.
Overall, MSC World Europa has been conceived to perform 47% better than her required EEDI measurement.
The vessel has 2,626 passenger cabins. On a doubleoccupancy basis, therefore, passenger capacity is some 5,252, but the configuration and flexibility of the arrangements provide for a maximum 6,762 guests. The ship’s initial employment will be as a floating hotel, berthed at Doha port in Qatar, for visitors to the 2022 World Cup, starting on November 21. She will subsequently inaugurate an Emiratesbased cruise programme.
The French-built behemoth has become the 20th unit of MSC’s Geneva-headquartered cruise division, whose fleet is projected to grow to 23 by 2025, with a further six newbuilds in prospect through to 2030. Steel cutting has begun at Saint-Nazaire for the second of the World-class, to carry the name MSC World America on service entry in 2025.
Length 333.3m Main genset engines 5 x Wartsila 14V46DF Breadth 47.0m Main genset power, combined 80,150kW
Gross tonnage 215,863t Speed c.22kts No. of decks 22 Manoeuvring thrusters 7
Passenger cabins 2,626 Fuel cell 150kW
Passenger capacity, double-occupancy 5,252 Class Bureau Veritas
Passenger capacity, maximum 6,762 Flag Malta
Japan’s Tsuneishi Shipbuilding has delivered the first of a new design of bulk carrier that of fers a substantial uplift in cargo capacity within the Kamsarmax category, writes David Tinsley. Dubbed the Wide Kamsarmax, the latest series has made its debut by way of the 88,939dwt Persistence Diva, completed at the group’s Numakuma yard on the Inland Sea at Fukuyama.
Through its shipyards in Japan, the Philippines and China, Tsuneishi is the market-leading producer of Kamsarmax tonnage, having delivered a total of more than 300 such vessels to date. The new, beamier model retains the versatility of the standard type, which is of the order of 82,500dwt in its latest iteration, but with some 6,400dwt more deadweight and a gain of about 5,300m3 in hold volume.
For the Wide Kamsarmax, the 229m length of the generic Kamsarmax has been retained, representing the maximum for the West African port of Kamsar, in Guinea, a major outlet for the bauxite trade, while the breadth has been increased to 36m from the 32.2m of the standard type. The expansion of the Panama Canal, entailing the construction of larger locks, has facilitated the design development.
The seven-hold configuration in the wide-body version confers an underdeck volume of some 103,500m3, and provides for a very wide range of bulk commodities besides bauxite, including iron ore , coal, grain and fertilisers. The advance in cubic intake is especially salient to scope for lowdensity cargoes, such as grain and other agricultural produce. The builder claims that the wider beam does not penalise trading scope at large, since it still allows entry to approximately 90% of the ports that have been called at to date by the existing Kamsarmax population.
Compared to the regular Kamsarmax, fuel consumption per ton-mile is improved by approximately 5%, through the extra scale economy of the design and its application of the proprietary energy saving device known as MT-FAST. This consists of multiple fins on the aftship bulb, which adjust and maximise water flow to the propeller.
The primary power installation is a six-cylinder engine of the S60ME-C10.5 type manufactured by Mitsui E&S Machinery at Tamano under licence from MAN Energy Solutions. The plant was specified at an output of 9,000kW at 84rpm, indicating the R4 rating of a two-stroke design that is attributed with a nominal maximum continuous rating of 14,940kW at 105rpm.
The main machinery complies with Tier III NOx requirements by way of exhaust gas recirculation(EGR) using bypass matching. Furthermore, the ship’s ClassNK notations confirm that the auxiliaries meet Tier III criteria through the adoption of selective catalytic reduction(SCR).
Persistence Diva is registered in Liberia with KTM Corporation, but Japanese beneficial ownership is indicated by the ship’s assignment to the Osaka-based management company Santoku Senpaku. Leading Japanese operators and trading houses are Santoku Senpaku’s main clients and its fleet includes two 82,540dwt standard Kamsarmax carriers, Honor Diva and Longevity Diva, completed in 2021 by Tsuneishi Heavy Industries(Cebu) of the Philippines.
Tsuneishi handed over its first Kamsarmax in 2005. Compared to the then standard 76,000dwt Panamax bulker,
the length was increased by 4m to 229m so as maximise access and loadings out of Kamsar, while conventional Panamax beam was retained. The result was an increase in transportation efficiency. Through the life of the series, design progression has been such that the fuel consumption per ton-mile of the latest newbuilds is calculated to be around 30% less than that of the 2005-built ship.
The Wide Kamsarmax initiative exemplifies Japanese builders’ focus on the continual refinement of designs crafted for series production, applied across the bulkship spectrum, securing improvements in ship efficiency and performance at minimal or otherwise competitive price premium.
Tsuneishi’s competitive edge in the sector has been sharpened over the years through development and control of yards in lower wage cost countries, complementing the retention of domestic shipbuilding capability. Although the subsidiary Tadotsu shipyard was sold off seven years ago, Tsuneishi has recently added to its asset base in Japan by raising its stake in Mitsui E&S Shipbuilding(MES-S) to 66%. The group is now the largest shareholder in MES-S.
PARTICULARS: MSC World Europa
Length 333.3m Main genset engines 5 x Wartsila 14V46DF
Breadth 47.0m Main genset power, combined 80,150kW
Gross tonnage 215,863t Speed c.22kts No. of decks 22 Manoeuvring thrusters 7
Passenger cabins 2,626 Fuel cell 150kW
Passenger capacity, double-occupancy 5,252 Class Bureau Veritas
Passenger capacity, maximum 6,762 Flag Malta
The international magazine for senior marine engineers
EDITORIAL & CONTENT
Editor: Nick Edstrom editor@mercatormedia.com
Please contact our correspondents at editor@motorship.com
Bill Thomson, David Tinsley, Tom Todd, Stevie Knight, Wendy Laursen
Production David Blake, Paul Dunnington production@mercatormedia.com
t +44 1329 825335 f +44 1329 550192
In December 1972, there was speculation about a proposal by the Onassis group to build a tanker of 1 million dwt. Many in the industry were dismissing this as nonsense, but the leading article in The Motorship for that month reminded us that a similar proposal in 1953 for a 47,000 dwt tanker for the same owner was similarly rubbished – and that ship, the Tina Onassis, was built. But as the 1m dwt vessel would be some 500m long, 85m wide, 33m draught, and that it would require some 20,000t of fuel for a one-way voyage, the practicalities made it an unlikely project. The idea was that the cargo would be contained in four caissons of 250,000 dwt that could be towed to and from the ship. As far as we know, the proposal went no further.
Back to reality, the main ship description concerned the Spirit of London, P&O’s first purposebuilt cruise ship. It was originally ordered by Norwegian group Klosters from Italian yard CNTO, but taken over by P&O and the design adapted for the burgeoning North American cruise market. Built to a Knud E Hansen design, the revised ship specification included flamboyantly-decorated public areas and comprehensive entertainment facilities befitting its target market. It was powered by four medium speed Fiat engines of 4500 bhp each, driving twin cp propellers for a 20.5 knot service speed. Originally five 832 kVA Bergen auxiliary gensets were envisaged, but P&O added a sixth. All main and auxiliary engines could run on HFO, unusual for that time. With a length of 163.3m and capacity for 874 passengers and 322 crew, the vessel was small by modern US cruise standards.
Only slightly smaller, though described as ‘giant’ in The Motorship’s pages, were a pair of ro-pax ferries for the Hull-Rotterdam route, to be operated by North Sea Ferries. These offered 1570 lane metres of vehicle decks plus capacity for up to 1200 passengers within a 153m length. Two StorkWerkspoor medium speed engines of 9000 bhp each would achieve a speed of 18.5 knots.
Meanwhile, Stork-Werkspoor announced the first medium speed engine capable of over 2000 bhp/ cylinder. The TM 620 featured a bore of 620mm and
stroke of 660mm, and with a BMEP of 22.5 kg/cm2 it would be made initially in in-line six cylinder format, with large vee-format engines to follow. A taste of things to come was provided by Gadinia, described as the world’s largest LNG carrier. Built by Chantiers de l’Atlantique for Shell Tankers, the 257m long ship offered a 75,021m3 cargo capacity. The five insulated tanks, cooled to -160 deg C, were designed for a novel loading arrangement, taking on gas at the stern, from a terminal at Brunei located 2.5 miles from the shore. The tanks were designed to be inerted with nitrogen, with liquid methane pumped directly into the tanks, the displaced nitrogen and boil-off gas being returned to the shore terminal.
Propulsion was by a single 20,800hp steam turbine driving a four-blade propeller at 160 rpm. Twin boilers, delivering superheated steam at 60.8 bar and 151 deg C, were configured to burn the boil-off gas during the voyage. The LNG was pumped to the furnaces via a steam-driven compressor located on deck forward of the accommodation. Two diesel-driven SEMT Pielstick auxiliaries covered the electrical needs.
The dangerous cargo meant that elaborate firefighting and detection systems were installed, with fire-proofed accommodation spaces and machinery rooms. Steam smothering equipment, backed up by CO2, powder and sea-water extinguishing systems were provided. The description noted the comprehensive navigation aids and remote controls, enabling berthing to be controlled by a single officer.
Brand manager: Sue Stevens sstevens@mercatormedia.com Marketing marketing@mercatormedia.com
EXECUTIVE
Chief Executive: Andrew Webster awebster@mercatormedia.com
TMS magazine is published monthly by Mercator Media Limited Spinnaker House, Waterside Gardens, Fareham, Hampshire PO16 8SD, UK
t +44 1329 825335 f +44 1329 550192 info@mercatormedia.com www.mercatormedia.com
Subscriptions@mercatormedia.com Register and subscribe at www. motorship.com
1 year’s digital subscription with online access £222.00
For Memberships and Corporate/multi-user subscriptions: corporatesubs@mercatormedia.com
© Mercator Media Limited 2022. ISSN 2633-4488 (online). Established 1920. The Motorship is a trade mark of Mercator Media Ltd. All rights reserved. No part of this magazine can be reproduced without the written consent of Mercator Media Ltd.
Registered in England Company Number 2427909.
Registered office: Spinnaker House, Waterside Gardens, Fareham, Hampshire PO16 8SD, UK