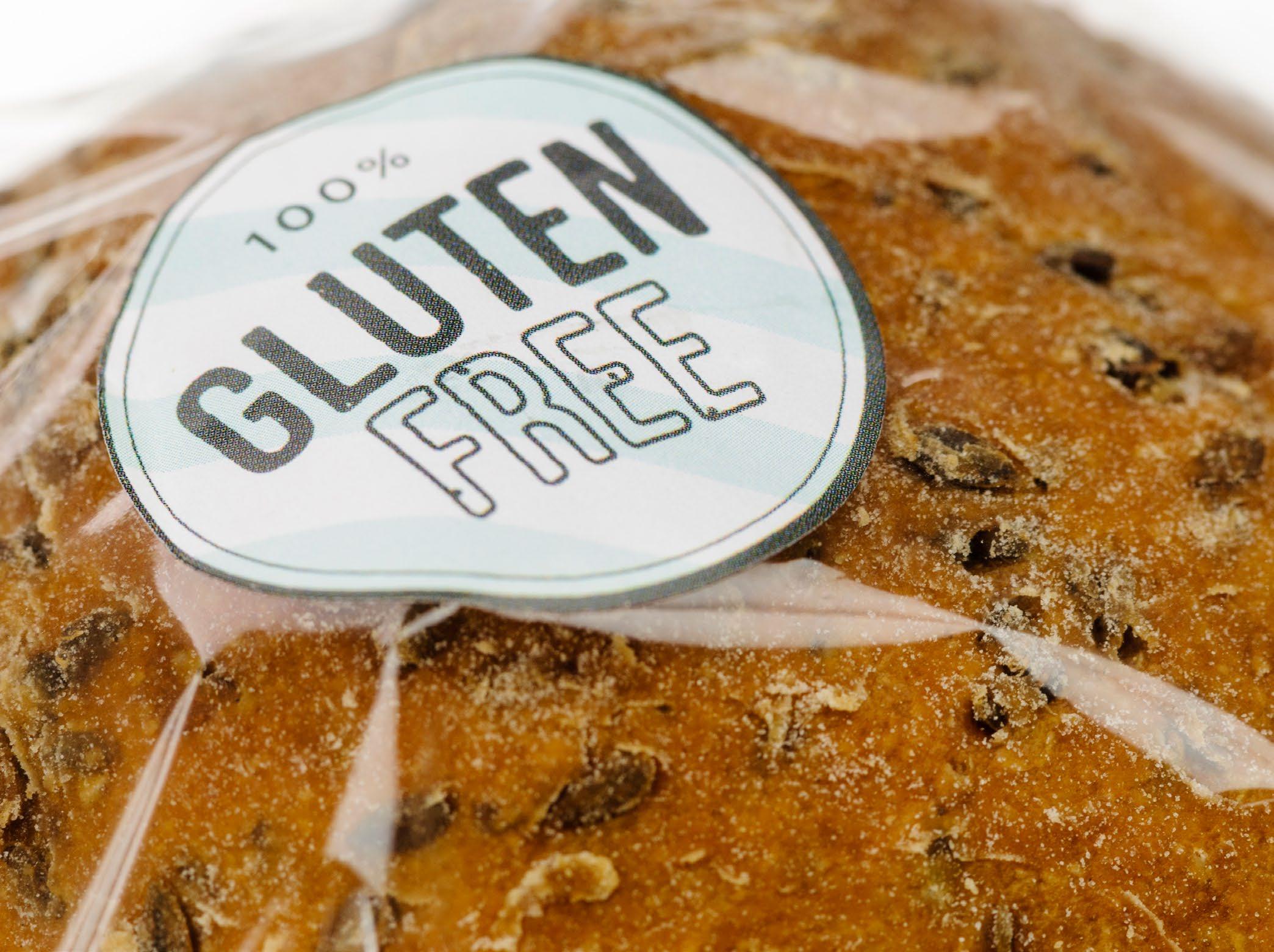
6 minute read
SPARC SYSTEMS
Sparc checkweigher saves free-from bakers ‘dough’
We’ve got a crisis on our hands! The recent free-from boom in pop-culture, on top of a growing epidemic of food allergies, has led to free-from products becoming increasingly integrated into people’s daily diets. But with prices of key ingredients used in a range of freefrom products soaring dramatically, this industry, worth an estimated £652m to the UK, needs to adapt and eliminate costly giveaway.
Rice flour is an integral part of glutenfree bread, cakes, baby food and desserts. With the cost of it rising by 26%, bakers are scrambling for a solution to keep production costs as low as possible. This is where checkweighing comes in as Charlie Graham, European Sales Manager for Sparc Systems explains.
Free-from products typically use expensive ingredients in the manufacturing process; some costing 2-3 times more than their conventional counterparts. Additionally, due to rising allergens, segregated production zones are critical to eliminate cross contamination. Even more essential given the introduction of ‘Natasha’s law’ this October.
Understanding the processing formulations in all free-from products is vital. In free-from bakery categories, for example, several processing variables must be factored in to maintain batch-to-batch consistency.
Inspecting up to 12,000 dough pieces per hour, Sparc Systems’ Hestia Dough Checkweigher provides free-from bakers with unparalleled weighing precision and speed.
Producing high quality and tasty gluten-free bread with comparable volumes and texture requires a degree of experimentation using different flour substitutes. When the perfect free-from dough and process has been achieved, the next challenge is maintaining a consistent weight and bake.
Repeatably delivering a weight accuracy of 0.5 grams, the automated Hestia Dough Checkweigher can save specialist free-from bakers thousands of pounds every day.
Connected to an automated upstream free-from dough dividing line, if a piece of dough is under or overweight by as little as 0.5 grams, the Hestia Dough Checkweigher automatically rejects it. Simultaneously, the machine’s advanced fibre optic-controlled software communicates back to the dough divider in real time to adjust the position of the blade for the next batch.
Charlie expands: “Free-from ingredients can cost over 150% more than conventional breads. There are often 20 or more ingredients within a freefrom bread recipe. Placing even greater emphasis on tightly controlling waste.”
Automated dough checkweighing allows for individual pieces that are off target weight to be removed and reworked, as well as providing corrective feedback to the dough divider. The result is a rapid payback on machinery investment.
“Sourcing alternatives to wheat, barley and rye is high cost, making repeatable weight precision even more critical for free-from bakeries,” reports Charlie.
Price volatility for premium ingredients, combined with the well documented global supply chain challenges, was part of the rationale behind the launch of Fortress and Sparc’s Raptor Checkweigher series. Using highend weighing algorithms alongside sophisticated automated adjustment and data capture software, the robust Raptor checkweigher further supports the rapidly expanding free-from industry to mitigate costly product giveaway. Targeting operational inefficiencies, the Raptor series reduces unnecessary rejections and waste whilst helping to maintain brand reputation.
“A common approach when prices escalate is to reduce the sizes of packs to counteract the rising raw material costs. For premium free-from products it places even greater pressure on the need to adhere to accurate net weights,” Charlie emphasises.
“Harnessing the power of smart checkweighing technology is rapidly becoming a critical part of the inspection mix. This ensures consumers continue to have the choice of affordable freefrom products that don’t compromise their wellbeing and dietary needs,” he concludes.
www.sparc-systems.com
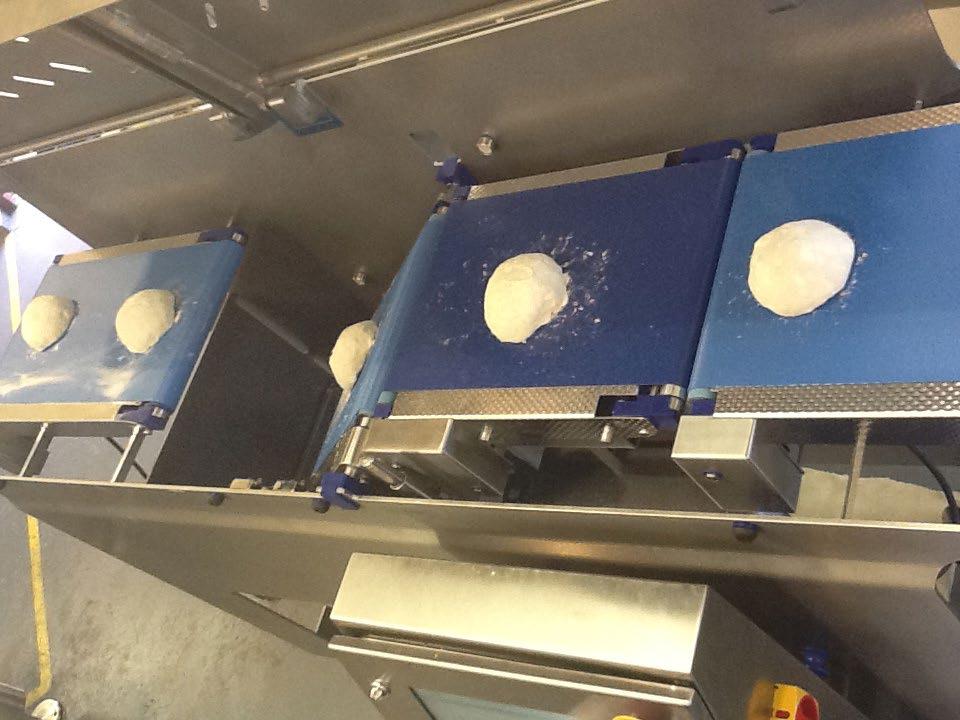
Lasers Support Digital Manufacturing In Carton Production
The traditional methods of manufacturing folding cartons can often be complex and time consuming. Each stage in the process, from artwork approval by the brand owner, through printing, die cutting, finishing, and shipping tends to be performed in isolation. This can often lead to large quantities of work in progress and multiple set-ups to change from one product to another.
However, the flexibility and power of lasers makes it possible to streamline these processes and operations into a single digital production line, which delivers the highest levels of productivity, and even allows the production of different product variants, on the fly.
CartonsInMinutes® is an automated process for laser cutting and scoring folding carton materials into stacks of cartons ready for folding and gluing. The ability to link the individual manufacturing process digitally within LasX’s CartonsInMinutes® digital manufacturing process, makes it possible to produce only what is needed, when it is needed. Eliminating unnecessary work in progress, set up times and product handling reduces both manufacturing timescales and costs.
From a product designer’s perspective, removing the constraints imposed by the mechanical die-sets traditionally used in carton production offers greater degrees of freedom. In addition to the product artwork, each item is located with fiducials and identified by a bar code - originating from a layered PDF file - containing the cut and scoring information required by the laser. Complex, variable, and nested shapes can all be created whilst matching digital printing speeds. 48 FDPP - www.fdpp.co.uk
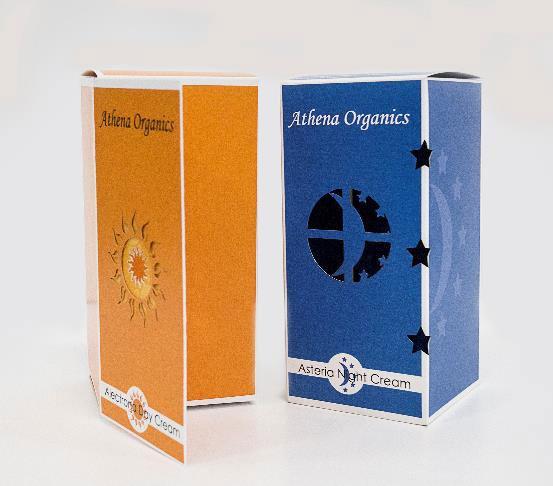
The CartonsInMinutes® process is capable of producing intricate shapes on demand Using LasX’s CartonsInMinutes® process, finished cartons can be available for shipping within minutes of final customer design and artwork approval
Several different sized and shaped folding cartons can be produced on a single sheet, optimising material usage. Furthermore, lasers offer the ability to combine multiple processes in a single run, which means cutting, scoring, perforating, and etching can all be done using the same system in one step as opposed to many. These factors all lead to reduce lead times, setup, and tooling costs.
The CartonsInMinutes® process is a specific configuration for LasX’s digital finishing equipment solutions designed to meet the needs of the folding carton market. LasX’s LaserSharp® equipment uses patented laser control software and advanced vision technology to assure precise, repeatable cut-to-print registration. Instant job change at production speed is accomplished either through programming or by reading the printed bar codes. These digital manufacturing systems, which are capable of using either sheet fed or roll fed material, are scalable to meet the needs of any production environment. Systems can be configured with up to two 1000W lasers to perform mixed converting operations while achieving throughput speeds as high as 15,000 cartons per hour, still with instant order / product changeover capabilities in continuous production runs. Following printing and laser processing, automation also aids in the digital manufacturing workflow. Pick-andplace robots, positioned after the laser-processing module, identify each piece and stack, sort, rotate and / or shingle them as required. By organising the finished parts using automation, significant time-savings can be realised. The laser-processed pieces can then be directly sent to additional finishing processes such as folder-gluers and then packaged. Multiple conveyor belts can be used at the end of a laser-processing module to send different products to various stations.
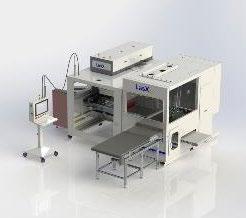
LasX’s CartonsInMinutes® process and technology described in this article are available from Bromsgrove based TLM Laser, who are the UK and Ireland distributors for LasX Industries, a technology and industry leader in high performance production class laser converting systems and services. TLM Laser also offers a comprehensive range of Laser processing systems for cutting, welding, marking, engraving, cleaning, 3D additive layer manufacturing, plus laser safety equipment.