
12 minute read
WEG
Improved IP rating for WEG inverter range
Motor and drive manufacturer, WEG will exhibit its latest range of industrial inverters at Aqua Nederland, held on March 15, 16 & 17, 2022 in Gorinchem. Demonstrating inverters from the CFW range, WEG is showcasing the latest version of the CFW500 variable speed drive at the show, which is now available with an ingress protection (IP) rating of IP66.
Aqua Nederland is the leading event for the water industry in Holland, welcoming over 370 exhibitors to demonstrate the latest technology in water treatment and management. As an intimate trade fair, the show provides a unique opportunity for those working in the industry to discover new product launches and network with other water industry professionals.
At the show, WEG will show the latest version of its well-established CFW500 frequency inverter. The CFW500 is a high-performance variable speed drive (VSD) with power ranging from 0.25 to 75, developed to control the speed and torque of three-phase induction motors. The device is now available with a higher IP rating than ever before, boasting IP66 rating as opposed to the previous IP20, meaning that it is suitable for applications where it may be subjected to direct high-pressure jets of water
Other variable speed drives from the WEG range have also been improved. The CFW700, CFW701 and CFW11 are now available with IP55 protection rating — making these devices ideal choices for applications in the water industry.
WEG has long provided solutions for the water industry, including its control gear and soft starters. Due to the demanding environments of water treatment, management and pumping, WEG is dedicated to engineering products that can adapt to the exact specifications of an application. This includes bespoke changes to the electrical and mechanical design of products.
WEG has also developed bespoke technology for drives used in pumping applications. WEG’s Pump Genius Has features that include broken pipe and leakage detection and programmable schedules with energy savings.
“WEG doesn’t simply sell motors and drives,” explained Marek Lukaszczyk, marketing manager at WEG. “Engineers at WEG work directly with customers to ensure the drives we supply are ideally suited for each application. For the water industry, this process ensures that drives are engineered to operate in the most effective and optimal manner — with an appropriate IP rating and peripheral technology to support the drive once it is in use.
“As a specialist trade fair, Aqua Nederland provides the perfect environment for WEG’s engineers to meet with potential end users and discuss their current challenges for motor and drive deployment in the water industry. The team will be available during the three day show at stand J106.”
More information on WEG’s devices for the water sector can be found on the company website. To arrange a meeting with a representative from WEG at Aqua Nederland 2022, please contact the team directly at: mbrinks@weg.net.
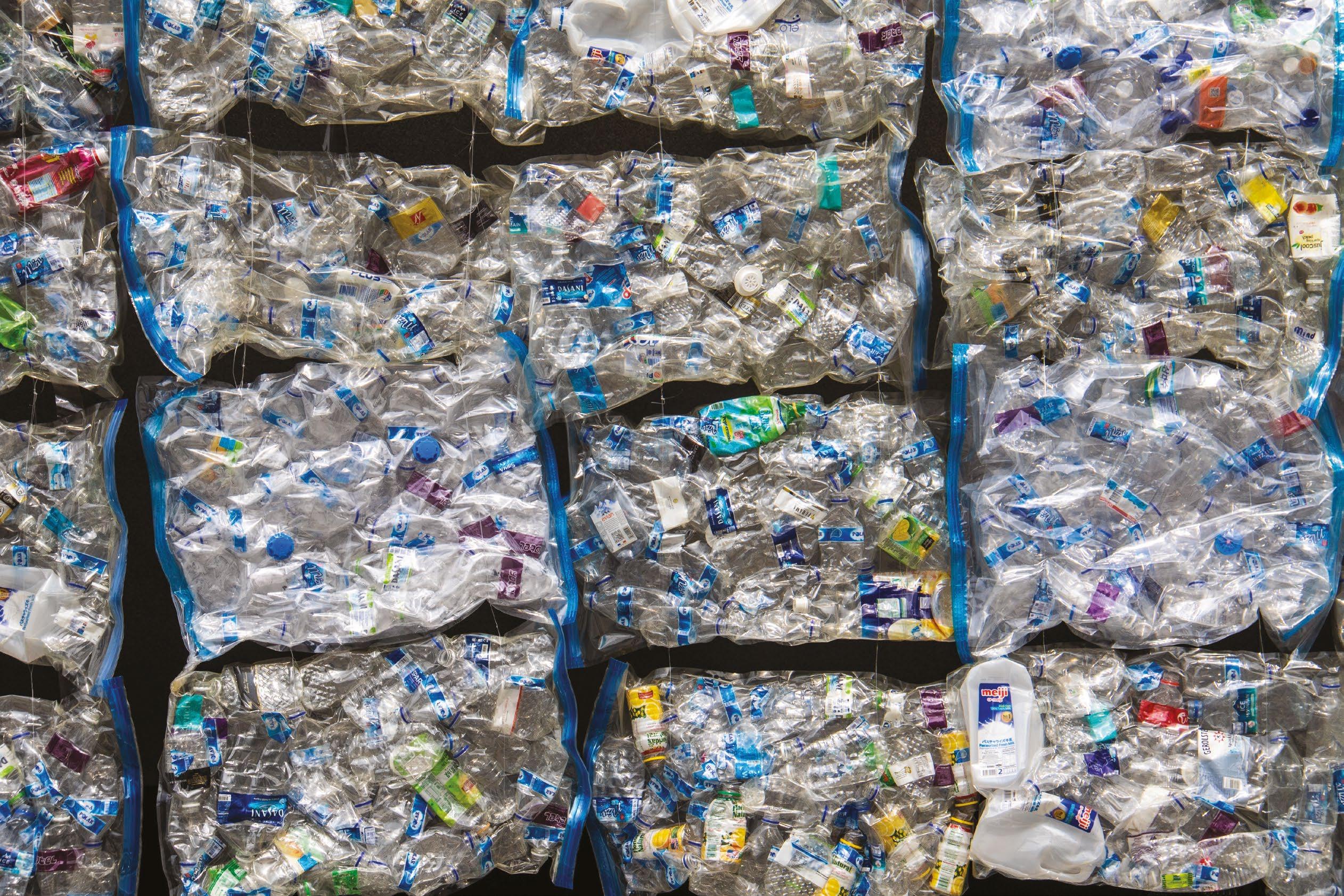
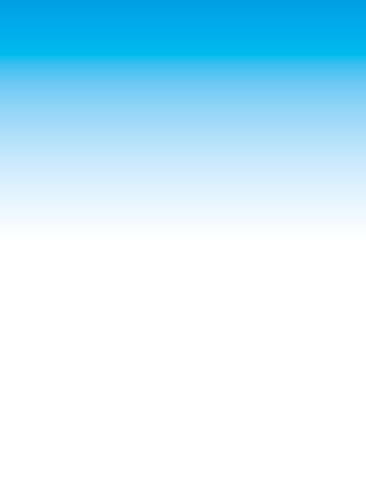
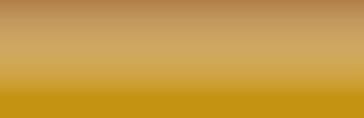
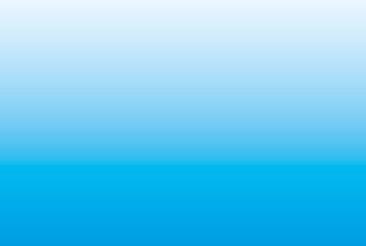
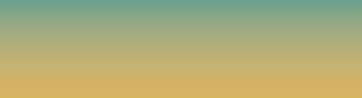
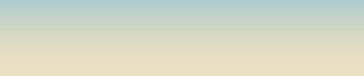
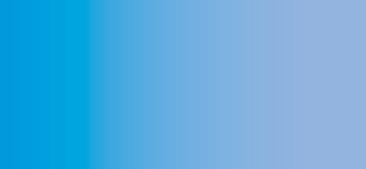
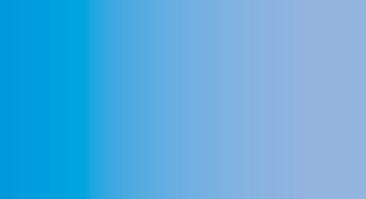
SOCIAL PLASTIC Waste plastic bottles, bags & containers are collected from beaches and riverbanks by local people who are paid for their services – these are taken to local centres for sorting and the recycling process begins.
BELL INTRODUCE REUSED OCEAN PLASTIC REUSED OCEAN PLASTIC
One of the most exciting developments in the plastic packaging industry is our ability to access and reprocess the post-consumer waste found on our beaches, riverbanks and along the perimeters of our oceans.
Unfortunately, plastic is now seen as a bad product – yet out of sight, beneath the surface of our oceans, there are millions of tons of other waste packaging made from glass, paperboard and metal that do not fl oat and therefore cannot be seen. Plastic has become a key focus on social media and in television documentaries, with politicians and supermarkets looking for ways to enhance their green credentials and promote a greener world. There can be no excuse for rubbish being discarded into the environment and Bell are one of the fi rst companies in Europe to endorse and support the collection and recycling of these materials. In 2019 Bell launched Retran® - a polyester-based material containing a minimum 70% recycled content. The credentials of this material are very high – pharmaceutical and food grade, with excellent clarity and full certifi cation. The product has been hugely successful and nearly 80% of our customers around the world have switched to this exciting new product. The 70% recycled content meets the new plastic packaging tax being introduced in April 2022, however Bell recognised the need to keep moving forward and
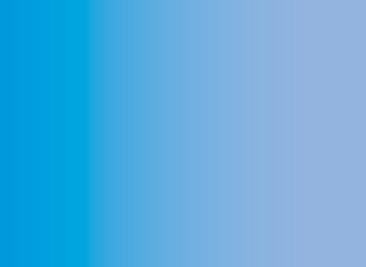
COLLECTED PLASTIC Coastal regions are an increasingly important source of waste plastic. Every year millions of bottles are collected and reprocessed to make plastic containers, bottles and products that can be used and recycled over & over again.
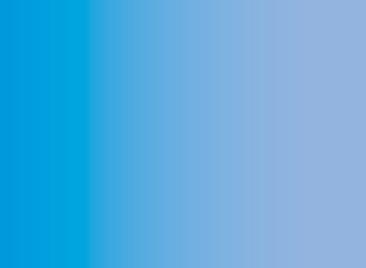
in 2021 introduced Biojet®. In simple terms, this is Retran® with an additive that stimulates and accelerates the biodegrading process. Whilst both of these products have been hugely successful, we recognised that even more needed to be done. Bell have worked throughout the pandemic, to identify reliable sources of plastic derived from the ocean. In simple terms this is “Reused Ocean Plastic”. The polymer used to produce the new packaging is being sourced from companies who organise local communities to collect plastic waste from beaches, riverbanks and ocean perimeters. Generally, these are communities who do not have the infrastructure for waste management but by paying local people to collect the plastic and deliver it to recycling facilities, the problem is reduced. As we have all seen, there are large quantities of plastic waste fl oating in the sea. If we can help to collect and reuse some of this waste, and turn it back into useful products, then we are taking a signifi cant step forward towards a better global environment. The new material has been extensively tested and meets the minimum strength requirements of our processes. It has excellent optical qualities and our testing to date reports that there has been no difference in the performance of the new material, compared to Retran®, Jetran® or Biojet® packaging.
Bell Packaging have started converting Reused Ocean Plastic for our forming and insert divisions, with tubing & boxes to follow in 2022. Samples and more information are available from our offi ces in Luton.
Experts in thermal control and measurement
LAUDA continues to provide an expanding range of feature-rich, future proof solutions with energy efficiency and connectivity front of mind, serving a diverse range of industries including food & beverage , brewing , chemical, pharmaceutical, biotechnology, oil and gas, composites, automotive, aerospace, digital printing, laser and beyond.
From food and drink research laboratories to pilot plant and full-scale production, with typical applications from rotary evaporators, incubators, stills and freezers to autoclaves, fermentation chambers and brewing vessels, LAUDA can supply the right temperature control or measurement solution matched to the precise equipment need.
LAUDA’s new range of water chillers has been designed not only to comply with the new Eco-design directive, but to surpass it through the innovative use of variable speed modules that automatically reduce their duty cycle in line with the cooling demand hence reducing energy consumption and running costs, giving a tangible return on investment for the user, whilst ensuring full compliance with the latest regulations on refrigerant (fluorinated) gases.
Further portfolio expansion delivers the new LAUDA ‘Versafreeze’ ultra-freezers, (deep-freeze storage down to -85°C), and higher power ‘Integral’ process circulators, (process control from -90 to 320°C with >25kW of cooling @20°C), with pressure overlay options to increase the working range of water / glycol up to 140°C.
Furthermore, for applications requiring customised solutions tailored to individual requirements, we offer a made-to-measure design service using a long-established and highly skilled team. Project engineering is a core competence of LAUDA and using the modular engineering approach we can design and scale a system specifically matched to the application needs.
With the capability to provide accurate heating and cooling in the range -150 to +550 °C using a variety of proven modules including heat transfer systems, process cooling systems, secondary circuit systems, fired heaters and molten salt plants, we are able to provide unique,
cost-effective solutions unparalleled by others.
Beyond temperature control, LAUDA has a well-established suite of solutions for measuring viscosity and surface/ interfacial tension aimed at the development of surfactants, oils, and polymers.
LAUDA is here to assist with your technical requirements from the first stage of the application discussion, all the way through the process to the final commissioning, and after-care services throughout the lifetime of the equipment.
A strong and experienced after-sales service function provides further peace of mind, with impressive first-time fix rates, and backed up by a fully kitted workshop at our newly configured facilities near Stamford.
We look forward to hearing from you.
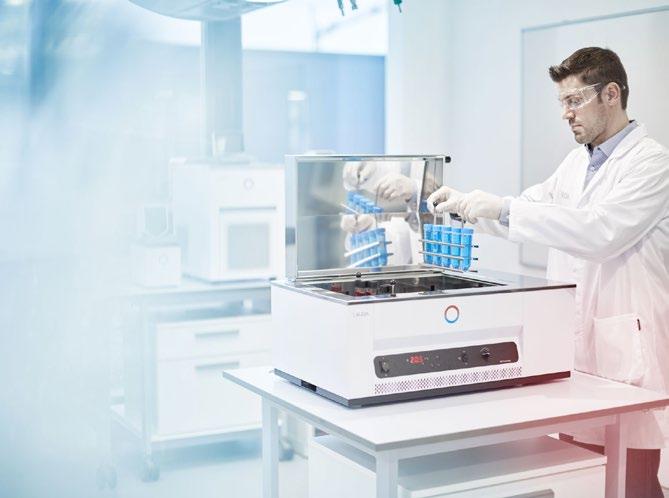
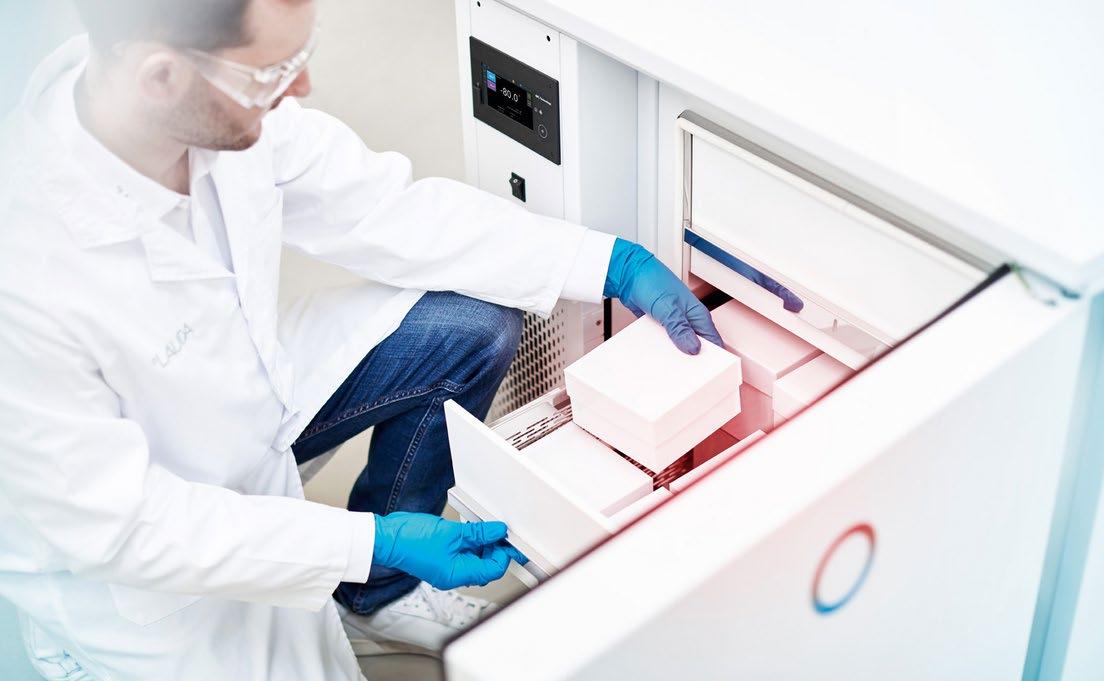
Tel: +44 (0)1780 243118 Email: info@lauda-technology.co.uk Website: www.lauda-technology.co.uk
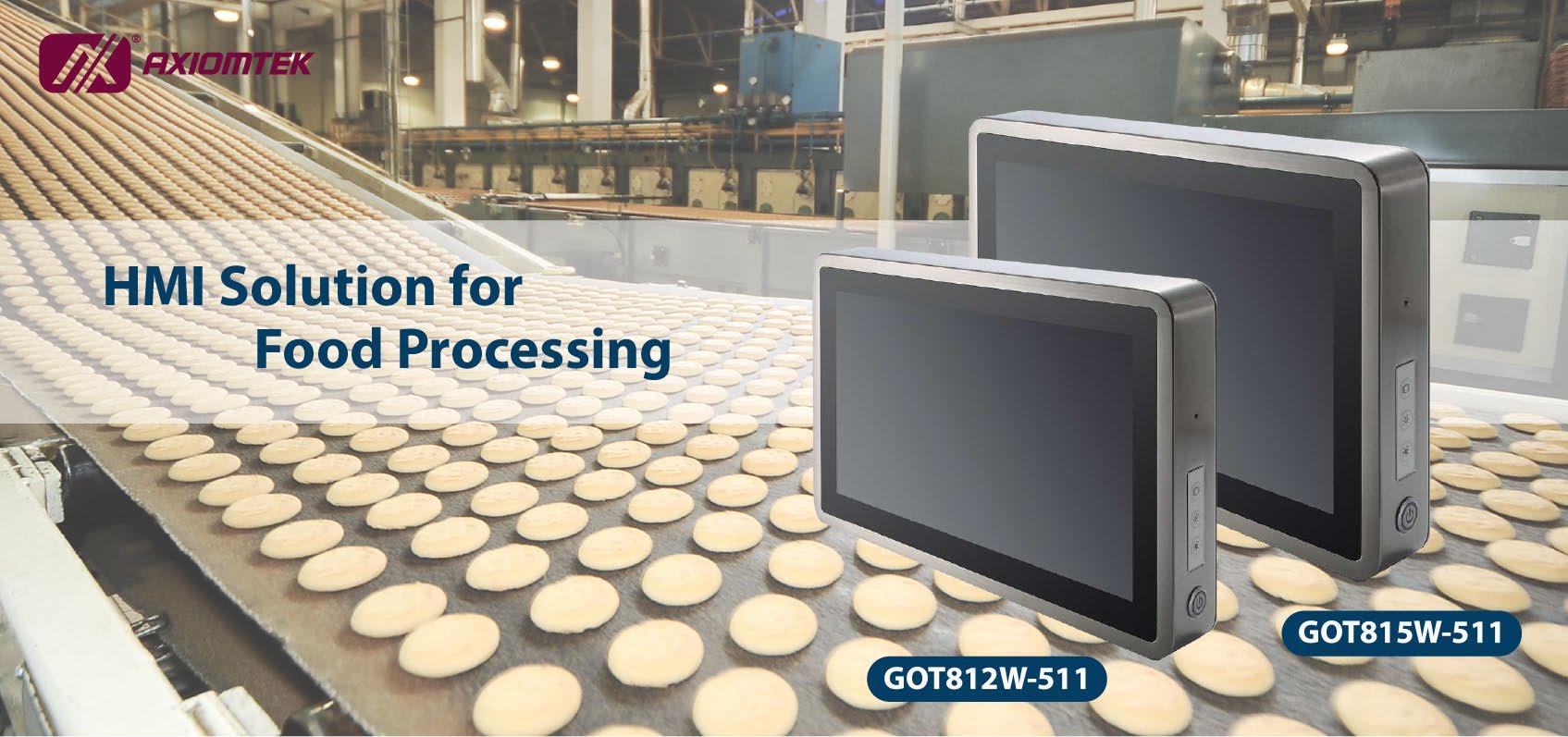
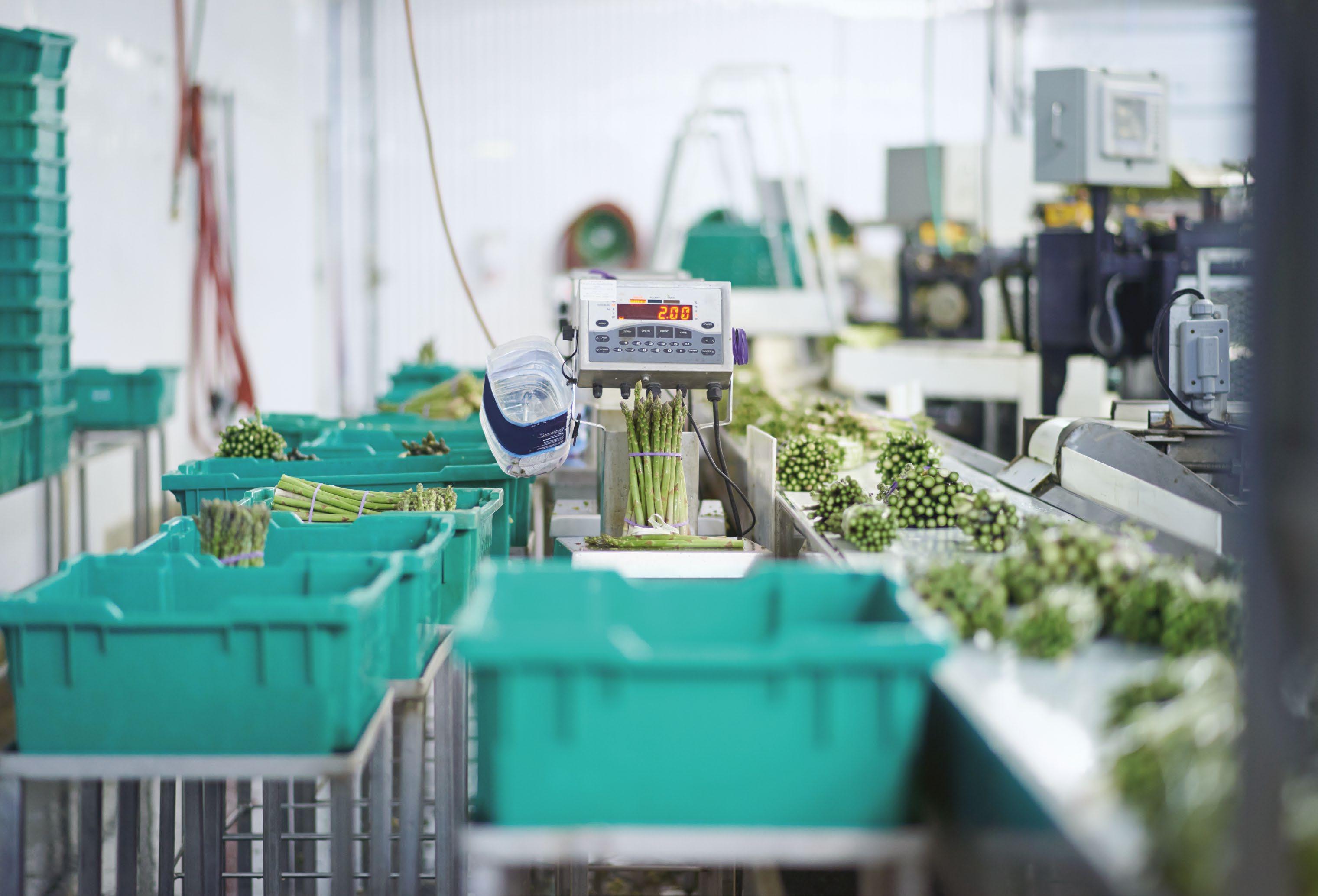
HMI Solution for Food Processing
In the food processing industry, the daily cleaning of automation equipment and process equipment is extremely important to ensure food safety. Therefore, the human machine interface (HMI) for food production facilities must be able to withstand high-pressure and high-temperature washing and be cleaned with acidic cleaners to facilitate daily scrubbing and water washing. A suitable HMI solution for food production facilities should have:
• The IP69K rating ensures the highest degree of protection in food processing environments where sanitation and cleanliness are required.
• The use of stainless steel materials has high anti-corrosion efficiency. prevents the buildup of any dirt on the bezels.
• Waterproof connectors allow complete protection during the cleaning process.
Human Machine Interface (HMI) allows direct data flow collection and communication between machines and facilities, as well as real-time monitoring and control of operating processes, to create fast and collaborative manufacturing processes. In addition to computing performance, HMI systems used in the food industry has many factors to consider, such as whether it can withstand intensive spraying and repeated high-pressure cleaning.
OUR SOLUTIONS
The GOT815W-511 and GOT812W-511 are powered by the Intel® Core™ i5-7300U processor. The high-reliability touch panel PCs offer a choice of either one 2.5” SSD HDD or one 2.5” SATA HDD for storage. For flexible communication, both panel PCs have one full-size and one half-size PCI Express Mini Card slots for WiFi/3G kit. Moreover, they support the VESA mount and are compatible with Windows® 10 and Windows® 10 IoT.
Axiomtek UK Ltd. T: 01612093680 E: info@axiomtek.co.uk W: http://www.axiomtek.co.uk/
Optimising Control Panel Enclosure Flexibility
Processing facility managers are under pressure to manage their space to minimise capital and operational expenses. The need to fit more equipment into an existing space prompts machine designers to reduce the size and footprint of the machines, which challenges the control engineers to design and build control panels within a constrained footprint.
Designing smaller control panels, control engineers need to consider several variables: cable segregation, thermal management, cable entry, electromagnetic interference (EMI), and cable bend radius, not to mention allowing extra space for future additions. A control engineer’s job is further complicated by safety considerations such as arc flash hazards, standards compliance, and minimum separation requirements for electronic components.
START WITH ENCLOSURE FLEXIBILITY
Selecting the proper control enclosure is an essential factor when space optimisation is the objective. Enclosures are designed to support a variety of accessories that facilitate component mounting based on the targeted application.
Choose an enclosure platform that allows full utilisation of the space between the enclosure door and components mounted to the sub-panel in the rear of the enclosure. To accomplish this, the enclosure must be designed to support structural members along the sides, top and/or bottom, as well as on the door. wire management. Enclosures need a full side mount panel with additional wire duct, relays, and grounding provisions that would have been mounted on the rear sub-panel. This design reduces the wall or machine space by 20% compared to a more common sub panel mounted design.
There are several products available to help control engineers utilise this 3D space, as well as often underutilised corner space in control panels that use traditional side equipment mounting plates.
DIN rail wiring ducts with two separate wiring channels enable the user to mount a DIN rail with components that would typically be installed directly to the subpanel, potentially saving 30% of the space on a sub-panel. Corner wiring ducts can provide good wiring transition from rear sub-panels to side sub-panels while reducing the amount of sub-panel space needed by 12%.
Today’s EMI noise shielding allows wiring that would normally require six inches of separation to be much closer together. Panduct PanelMax Shielded Wiring Duct and Noise Shield separate noisy motors and drive cables from sensitive Ethernet or control cables and reduce the space required.
Also consider minimising the external footprint. One consideration is the control panel mounting position. Flexibility with the mounting allows the control panel anywhere in the design, creating an integrated system solution.
When the enclosure houses valuable mission-critical equipment or information, space optimisation may take a back seat to control panel security. An investment in the right security will be less than the cost of a potential loss, but the protection needed can vary. The expense of lost or stolen data or the cost of injury from unintentional access can be mitigated with a layered approach to controlled access.
Access control and power distribution capabilities typically associated with building security can now be integrated directly into network enclosures. Electronic swing handles and built-in low frequency card readers limit access to critical IT equipment to authorised personnel. Intelligent power distribution units enable remote monitoring capabilities and improve efficiency by continuously analysing for electrical overloads and other conditions that place critical IT/OT equipment at risk.
CONCLUSION
Control engineers must overcome complexity when designing control panels in industrial environments. Whether the application is in oil and gas, food, automotive, water treatment, or pharmaceutical, competing design criteria influence decisions about optimising the control panel. Space optimisation can provide more design flexibility both for the control panel itself and the plant floor and help facilitate integrated access control solutions.
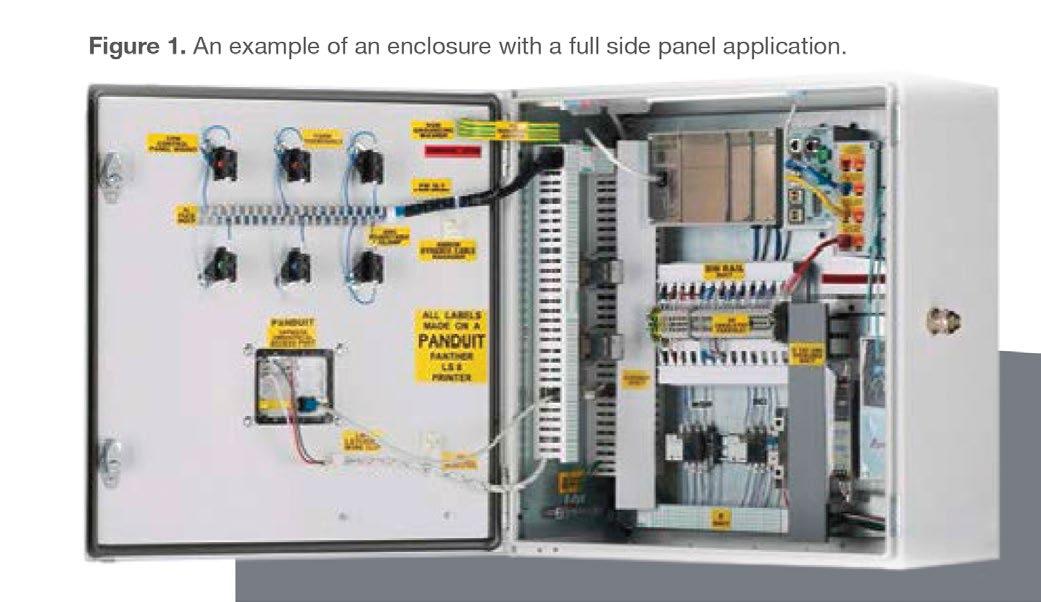