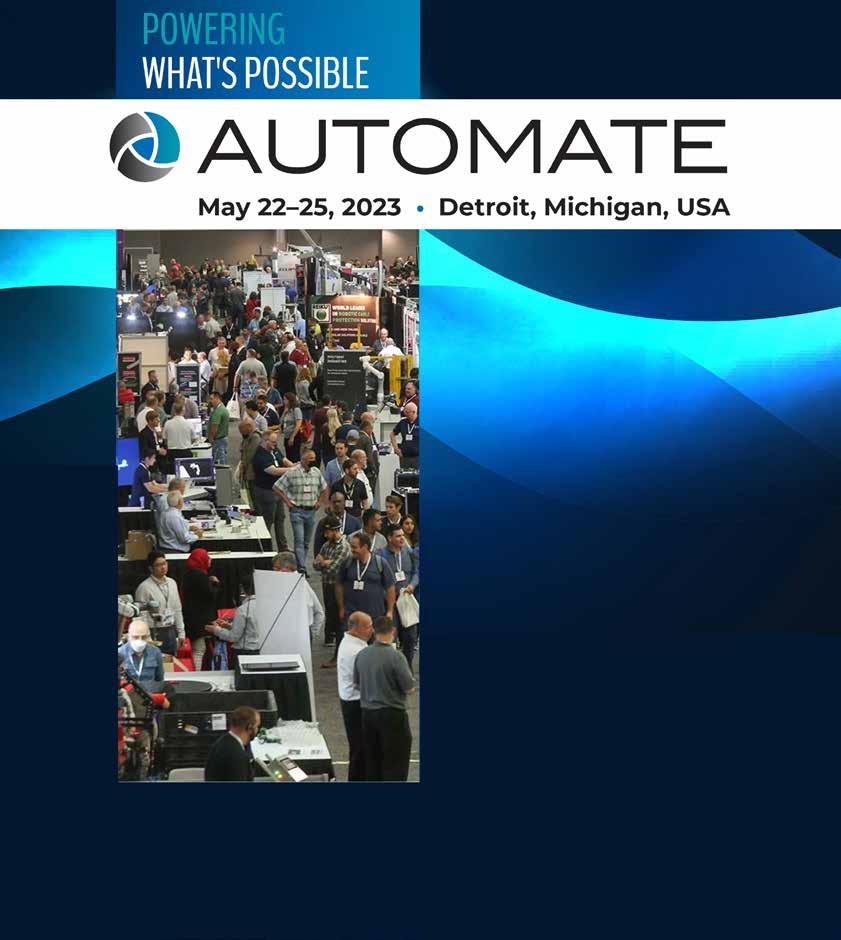
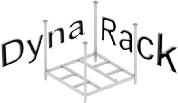
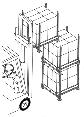
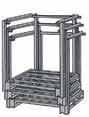
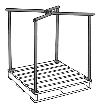
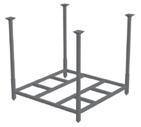

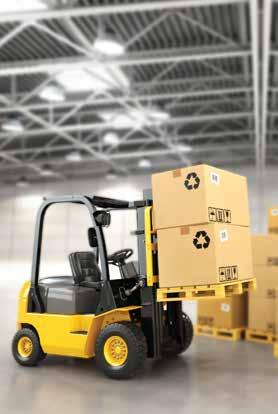
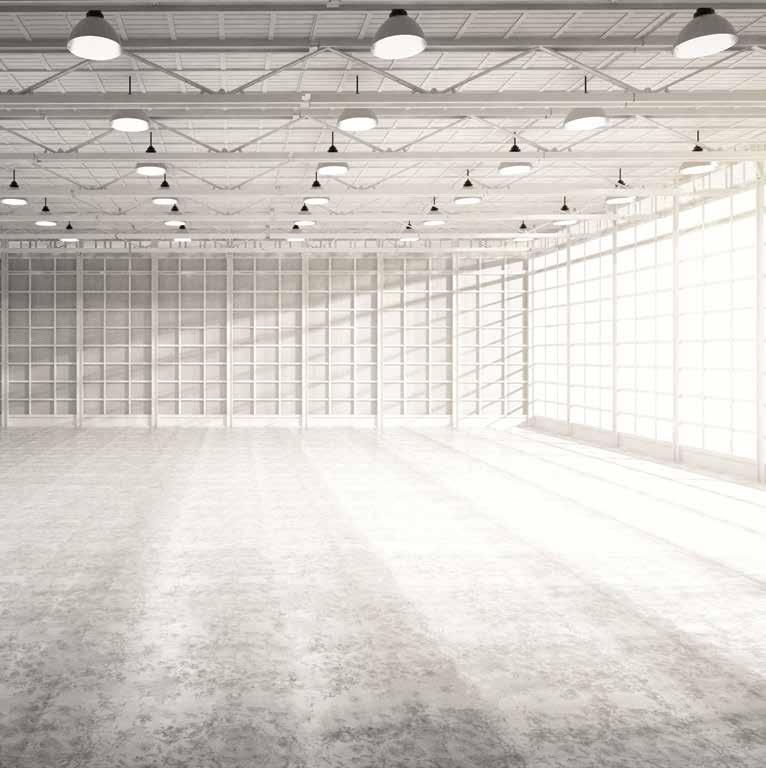

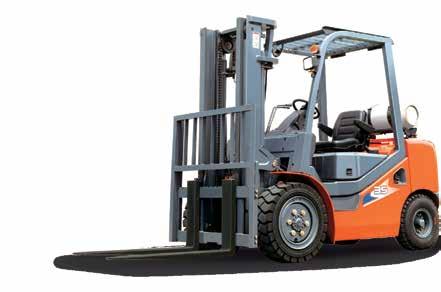
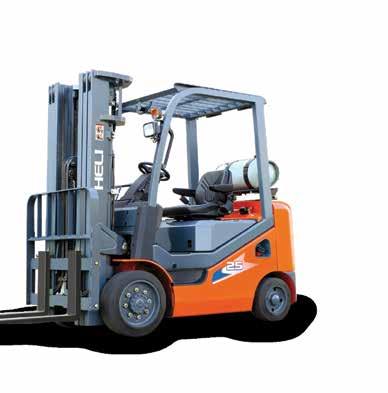

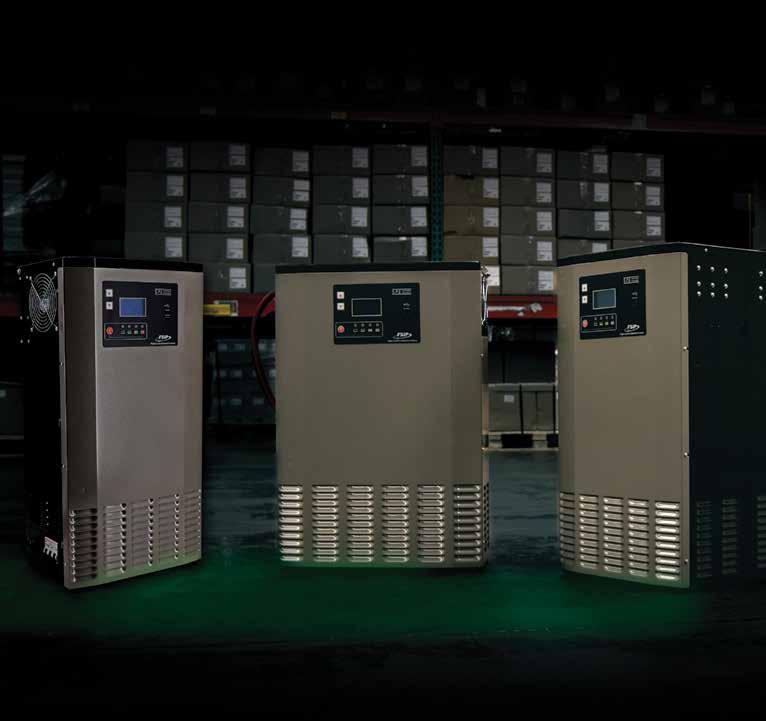
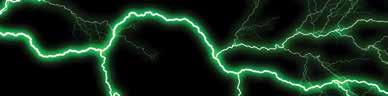
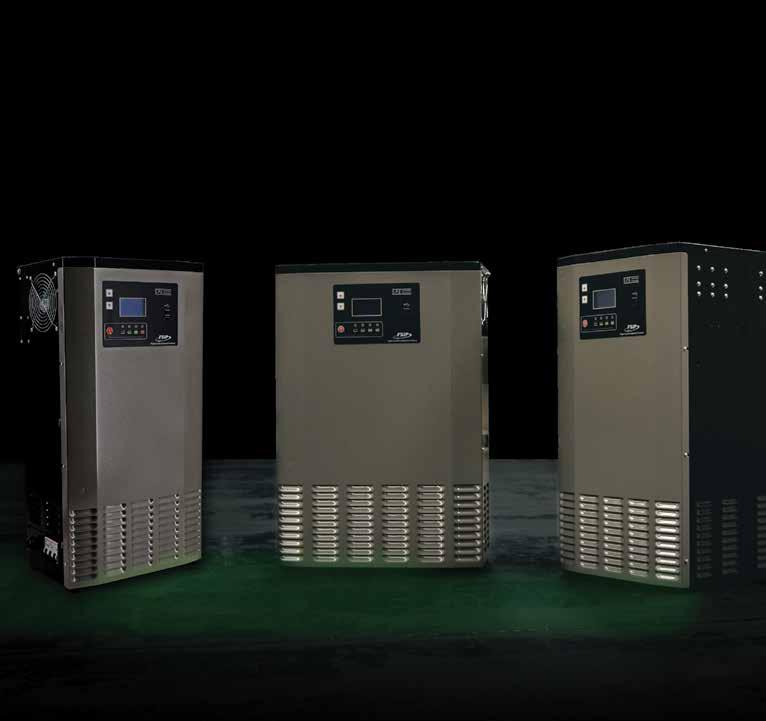
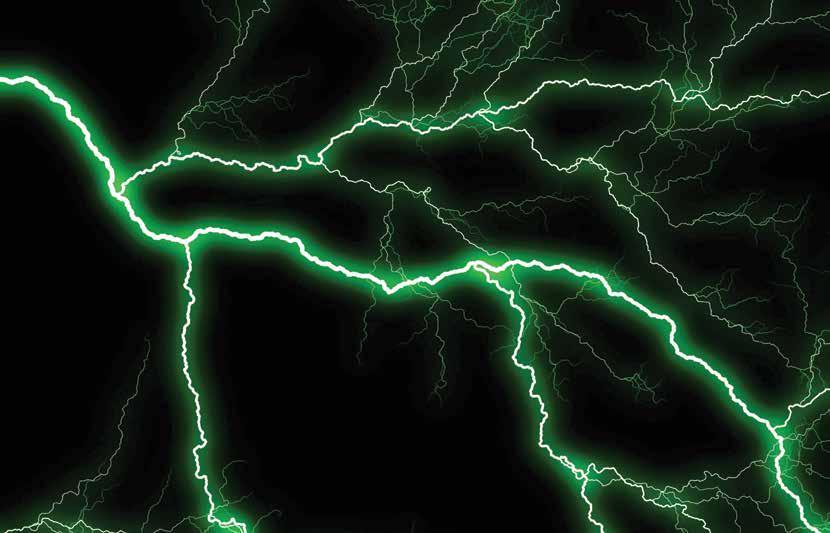
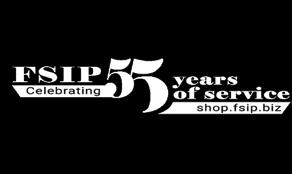
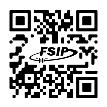
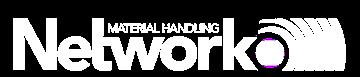
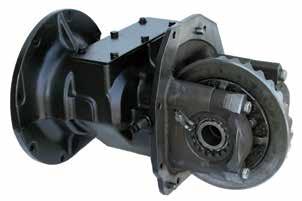

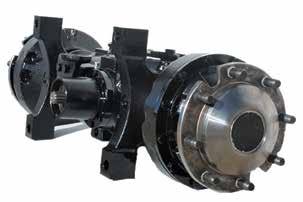

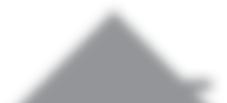

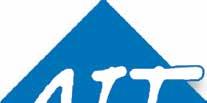
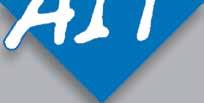
single classes or a full-access pass, the conference is consistently rated as a high-quality, high-value training experience that provides immediate, actionable value.
Automate is held over four days and the chances to learn, collaborate and plan your path ahead are countless at Automate. Between intimate workshops with industry giants, newsmaking keynotes, networking events, innovation competitions and live demonstrations, no other event offers more comprehensive automation education or inspiration.
As Automate continues to grow in prominence and extend its influence, this event has become a must-attend for anyone currently working with automation, companies that want to begin to use automation, and those looking for ways to capitalize on the technology.
As the leading automation showcase in North America, the hands-on, front-row-seat experiences are second to none. The gathering of expertise and experience is unmatched. The opportunities to learn, get better and make a fast impact abound. Whether you already use automation or you’re just curious, Automate is simply a can’t-miss.
Don’t just take a salesperson’s word for it, see the solutions for yourself. Every day and every booth at Automate is a chance to propel you and your colleagues ahead. Connect with more than 600 exhibitors, 200 speakers, 25,000 registrants and experience an array of live automation solutions up close.
If you’re looking to truly gain a competitive edge, then the Automate conference is for you. Featuring
With over 600 leading exhibitors from around the world, our show floor is an inspiring demonstration of what’s possible—the kind of breakthroughs we only dreamed of not so long ago. Discover the latest in cutting-edge robotics, vision, artificial intelligence, motion control and more.
The visionaries, disrupters and leaders who have already automated with great success—and are devising new ways to do it—will be at Automate to help you prepare for your automation blast-off. Visit our keynote speakers page to view this year's lineup!
Monday, May 22, 9–9:45 am
Tom Izzo, Head Coach, Michigan State University Men’s Basketball Program
Tom Izzo shares invaluable leadership lessons from his life's work as a Hall of Fame basketball coach and a beloved mentor. With a career record of 606-232 leading into this season, it’s easy to see that Izzo knows how to win, but he also knows how to win the right way. He has the fifth-most wins of any college coach. He's been to eight Final
Fours. But perhaps, most importantly, 86% of his players left with a college degree. You don't need to be a Spartans fan to learn from Izzo's track record of success.
Tuesday, May 23, 9–9:45 am
Gregory Robinson, Former Director, NASA, James Webb Space Telescope
Today, most organizations must innovate or fall behind. But what’s the key to leading innovation and overcoming challenges and failures? It isn’t just about hiring very talented people. At NASA, Gregory Robinson worked with, led and managed some of the world’s most accomplished scientists and engineers. Instead, he says, it’s about prioritizing relationship-building, creativity, knowledge-sharing and “open communication without fear.” Robinson emphasizes soft skills like knowing when to lead and support, understanding how to collaborate, problem-solving, and reaching out beyond your team to find answers and fresh thinking. Using real-life examples from his 33-year history at NASA, set against a backdrop that takes you a million miles from Earth, Greg Robinson shows how the human element is more critical than ever to driving transformation and achieving our most ambitious goals.
Wednesday, May 24, 9–9:45 am
Barbara Humpton, President & CEO, Siemens Corporation USA
The term “Industry 4.0” went mainstream about 10 years ago. Yet in that short time, we have achieved milestones in digitalization that all but the most optimistic of us would have thought impossible. We can commission virtually. We can run incredibly small lot sizes efficiently. We are gathering, storing and analyzing quantities of data that would have staggered our ten-year-ago selves. And we have proven that we can use that data to simulate and optimize around quality, cost,
sustainability, and many other outcomes. Imagine what the next ten years will bring! Join this talk to explore where we go next, what it will take to get there, and what key issues we as an industry will be confronting and managing along the way.
Wednesday, May 24, 1–1:45 pm
Daniela Rus, Professor of Electrical Engineering and Computer Science, Director of the Computer Science and Artificial Intelligence Laboratory (CSAIL), MIT
The digitization of practically everything coupled with advances in machine learning, the automation of knowledge work, and advanced robotics promises a future with democratized use of machines and wide-spread use of AI, robots and customization. While the last 60 years have defined the field of industrial robots and empowered hardbodied robots to execute complex assembly tasks in constrained industrial settings, the next 60 years could be ushering in our time with Pervasive robots that come in a diversity of forms and materials, helping people with physical and cognitive tasks.
Thursday, May 25, 9–9:45 am
Jan Diekmann, Technical Account Manager, Ericsson
5G is much more than a network—it’s a platform for innovation providing global scale and enabling manufacturing use cases that we haven’t even dreamed of yet. As a new lean manufacturing tool, 5G is taking production into the age of digitalization. It enables lean manufacturing processes and the ability to truly take advantage of technologies like the cloud, automation, digital twins, AI, AR and IIoT. The benefits of 5G support technologies like process automation, remote monitoring and collaborative robots. It also allows for higher flexibility, lower cost, and shorter lead times for factory floor production reconfiguration, layout changes, and alterations, which will result in significant improvements.
In this session, you’ll learn how to apply 5G’s capacity to handle massive amounts of data with low latency to support lean methodologies in a powerful way, unlocking new value and even taking lean concepts beyond the factory.
Our exhibitors provide an up-close look at different ways to solve operational challenges, seize untapped opportunities and propel your business forward. Get to know them before the show.
The Latest AI and Smart Automation Trends for Manufacturing
Manufacturers of all sizes are looking to smart automation and AI to stay ahead of the curve.
Aerospace manufacturers are identifying automation applications that work for their specific needs, and reaping the benefits. Here are four applications.
Everything you need to know about Robots-asa-Service (RaaS)
Wondering what all the fuss is about Robots-asa-Service (RaaS)? Here's everything you need to know, including what it is.
Automate is jam-packed with events, demonstrations, classes and networking events. Don’t miss out on any of the opportunities.
Monday, May 22, 2023
7:00 AM - 5:00 PM Registration
8:00 AM - 5:00 PM Conference Sessions (Additional Ticket Required)
9:00 AM - 9:45 AM Keynote Address: Tom Izzo, Head Coach, Michigan State University
10:00 AM - 5:00 PMShow Floor Open
Tuesday, May 23, 2023
7:30 AM - 5:00 PM Registration
8:00 AM - 5:00 PM Conference Sessions (Additional Ticket Required)
9:00 AM - 9:45 AM Keynote Address: Gregory Robinson, former NASA Director, James Webb Space Telescope Program
10:00 AM - 5:00 PM Show Floor Open
5:15 PM - 7:30 PM Networking Party (Additional Ticket Required)
Wednesday, May 24, 2023
7:30 AM - 5:00 PM Registration
8:00 AM - 5:00 PM Conference Sessions (Additional Ticket Required)
9:00 AM - 9:45 AM Keynote Address: Barbara Humpton, President & CEO, Siemens Corporation USA
10:00 AM - 5:00 PM Show Floor Open
1:00 PM - 1:45 PM Keynote Address: Daniela Rus, Professor, Electrical Engineering & Computer Science, Director of Computer Science and AI Laboratory (CSAIL), MIT
3:30 PM - 4:30 PM CVP Basic Exam
5:15 PM - 8:30 PM Joseph F. Engelberger Robotics Awards Dinner (Additional Ticket Required)
Thursday, May 25, 2023
7:30 AM - 3:00 PM Registration
8:00 AM - 5:00 PM Conference Sessions (Additional Ticket Required)
10:00 AM - 3:00 PM Show Floor Open
4:00 PM - 5:00 PM CMCP Exam (Additional Purchase Required)
Friday, May 26, 2023
8:00 AM - 1:00 PM CVP Advanced Courses (Additional Purchase Required)
1:00 PM - 3:00 PM CVP Advanced Exam (Additional Purchase Required)
One of the aims of Ladder Safety Month is to increase the number of people taking Ladder Safety Training from the American Ladder Institute (ALI). That, of course, is an effort that is not confined to a single month; it continues all year long, every year. One of the ways ALI has extended its ladder safety message and gotten more people into Ladder Safety Training courses is due in part to farsighted adopters of the curriculum like the Retail Learning Institute (RLI).
RLI is a people development organization supported by The Coca-Cola Company, dedicated to providing learning resources for food retailers worldwide. As an educational organization, it serves more than 15,000 businesses in 19 countries with blended training programs that include more than 500 industry-specific online courses divided into different categories: onboarding, compliance, departments, managers, and specialized series.
In 2019, RLI added the American Ladder Institute’s Ladder Safety Training to its compliance curriculum. It has quickly grown to become the institute’s “golden jewel,” according to Ana Velazquez, RLI’s learning solutions director.
“Ladder safety training is one of the courses we recommend all clients add to their employee training,” said Velazquez. More than 300 organizations have incorporated the course into their regular employee training, and more than 10,000 people have taken at least one ladder safety training course from ALI.
The courses help keep employees safer by teaching them the proper way to use ladders. They also protect employers, providing proof that they have made the training available and that employees have completed it.
RLI develops most of its courses in-house and has exceptionally high standards for courses developed from outside sources. “When we choose to partner with another organization to provide training
content, we make the decision based on the quality of content and the credibility of the partner,” said Velazquez. “We want experts in their field like the American Ladder Institute.”
Ladder Safety Training from ALI is fully incorporated into RLI’s course offering, so employees never have to leave RLI’s learning management system to take courses, which are offered for articulated ladders, mobile ladders and platforms, single ladders and extension ladders, and stepladders. RLI also operates sister training services geared toward independent grocers and general retailers, and ALI’s Ladder Safety Training is offered through all of them.
“The American Ladder Institute has done a great service for us by providing this quality training content,” said Velazquez. “We want to offer it to as many people as possible, which is why we make it available across all our training platforms.”
Founded in 1947, the American Ladder Institute (ALI) is a not-forprofit trade association dedicated to promoting safe ladder use through ladder safety resources, safety training, and the development of ANSI ladder safety standards. ALI also represents the common business interests of its members, who are comprised of the leading ladder and ladder component manufacturers in the United States, Mexico, and Canada. National Ladder Safety Month, observed each March and spearheaded by ALI, is the only program dedicated exclusively to promoting ladder safety, at home and work. https://www.americanladderinstitute.org.
If you work in the warehousing industry, it's likely that you're familiar with the term "technology." The reality is that the world of warehouse logistics and supply chain management has been transformed by technology. In fact, it's not uncommon for some warehouses to have more technology than many office buildings. That said, there are some specific areas where emerging technologies are making a big difference in efficiency and productivity within warehouses.
As a warehouse manager, you're probably familiar with the many benefits that warehouse technology can bring to your facility. There are several warehouse technologies on the market today that can help improve efficiency and reduce costs, waste, and the risk of accidents. Let’s take a look at some of them.
A warehouse management system (WMS) typically includes a set of tools and applications that are used to automate and optimize the various tasks and processes involved in managing a warehouse, such as receiving and storing inventory, picking and packing orders, and shipping products to customers. Some of the key benefits of using a WMS include improved efficiency, accuracy, and productivity, as well as better inventory control and cost savings. In addition, many WMS systems include features that help businesses comply with industry regulations and standards, as well as provide real-time visibility into warehouse operations.
A warehouse control system is a software tool used to monitor and/or track your inventory in real-time. This allows you to optimize the flow of goods through your warehouse which results in
increased efficiency, more accurate inventories, and fewer employee hours required for restocking.
A typical warehouse control system contains several components: it collects data about what products are being moved through the system (the "targets"), analyzes that data to provide insight into target activity trends, then uses that analysis to direct decisions about what should be done next (the "actions"). Warehouse control systems can also help with forecasting based on past performance or predicting future demand based on seasonal trends or other factors.
In addition to tracking individual products as they move through different parts of your warehouse, many systems also allow for tracking at an item level — meaning you can see how often each individual piece is being handled by multiple employees over time so you can schedule more efficiently. The result? Fewer mistakes are made by workers who don't understand their role within this larger process!
When it comes to warehouse robotics and automation, the possibilities are endless. No matter what your needs are, there's a solution out there that can help you get the job done better and faster.
Robots in warehouses are typically used for tasks such as picking and packing items, moving and organizing inventory and transporting goods from one location to another. They are programmed to follow specific instructions and work efficiently and accurately to ensure that orders are fulfilled quickly and accurately. Some robots are also equipped with sensors and cameras to help them navigate the warehouse and avoid collisions with other objects or workers. In general, robots in warehouses help to improve productivity, reduce errors and improve overall operational efficiency.
So, what exactly does all this mean? It means that if you're interested in improving efficiency at your warehouse or distribution center, then robotics is worth exploring further. It's important to remember that warehouse technology alone isn't enough; it must be paired with solid business processes so that everyone knows what their role is and how they contribute to overall success.
It's no secret that voice technology is the future of warehouse management. A smart voice-enabled system can help you improve efficiency, accuracy, productivity, and reduce errors. As a result, it can have a positive impact on your bottom line.
Voice technology allows you to automate tasks. You can use voice technology to automate various tasks, such as picking items off shelves or scanning barcodes on pallets. The ability to do these things hands-free means that your workforce will be freed up for more important tasks like customer service and quality control checks instead of being tied down by the monotony of mundane warehouse activities.
Voice technology helps you improve accuracy. Having accurate information is essential for any business, but especially in warehousing because there are so many different products that need tracking, from item number coding through inventory management systems all the way to delivery schedules.
3D simulation is a great way to test your warehouse layout before you build it. 3D simulation allows you to visualize and experience your warehouse layout, including all equipment and materials before they are physically in place. This enables companies to optimize storage, reduce costs and improve productivity.
3D simulations also allow companies to better understand their supply chain logistics. Companies can use this warehouse technology to plan their supply chain by visualizing the flow of products through warehouses and distribution centers (DCs). This helps them avoid bottlenecks or other issues that could arise during the transportation or delivery of goods within the supply chain.
Sensors and connected devices can be used to monitor warehouse conditions, including temperature, humidity, light levels, and noise. Sensors worn by workers can also track their activity levels — helping to improve worker productivity and safety.
In addition, sensors and connected devices can be used in conjunction with machine learning algorithms to monitor product quality across a warehouse or distribution center. For example, if the quantity of defective products increases over time (or if no defects are found), this could indicate that either the packaging needs improvement or there is an issue with one or more machines that are causing product damage during processing.
Finally, sensors and connected devices can also be used in conjunction with machine learning algorithms to monitor inventory levels throughout a warehouse or distribution center. By monitoring how much inventory has been moved from one location on an average day vs. another location on an average day — and making comparisons between different locations within a facility — companies gain insight into where they may need additional storage options for specific types of products (including shelf-stable items like food).
Conclusion
Emerging warehouse technology systems are quickly changing the way you can manage your facility and how efficiently you can fulfill and distribute products.
As we’ve seen, there are a lot of ways technology can make your warehouse more efficient, and the benefits just keep coming. There’s also an opportunity for greater visibility into what is happening in your facility, which will allow you to make better decisions about the future direction of your business and how it interacts with customers.
Bill Denbigh serves as the vice president of product marketing at Tecsys. Bill started working in supply chain software some 30 years ago; his entire career has been laser-focused on designing and building pragmatic supply chain solutions that address the real problems that customers are facing in their supply chain operations.
We tend to believe that famous innovators or other “creative” people have some inherent qualities that we don't have. But the truth is — they don’t. They've simply cracked the code on how to consistently live in a possibility instead of living in obstacles.
Visionary thinkers see possibilities. Always. Most of us mostly see obstacles, most of the time. We move through work, and life, by addressing whatever next obstacle falls into our path. We problem-solve the next issue on a project, we deal with the next customer complaint, and we address the next challenge with our kids. But too rarely do we look up, survey the world, and make a conscious choice to shape our world to be the way we want it to be.
Visionary thinkers make that daily choice - to imagine the possibility of a different world, to hold on to that vision, and to refuse to let the obstacles limit their thinking. They live in possibility.
Visionary thinkers are open-minded, innovative & imaginative, willing to take risks, optimistic, and collaborative – all skills related to creative thinking. They regularly imagine, consider, and pursue new ideas and solutions.
The good news - all of these creative thinking skills are learnable! Anyone can become a more visionary thinker by learning to leverage the creative genius that’s already hidden inside.
One of the primary barriers to living in possibility is the negativity bias, a cognitive bias, or mental shortcut, that all humans share. It’s the phenomenon that negative experiences have a greater impact -- on our thoughts, feelings, and behaviors -- than positive experiences do. That seems counter-intuitive, but there’s a wealth of research that proves negative affects us more than positive. As a result, we are much more motivated to avoid negative than to seek positive.
Our brains have evolved to excel at identifying potential negatives so that we can avoid them. It’s a survival mechanism, and it happens in the most primitive part of our brain – the amygdala. The amygdala is responsible for detecting threats and triggering the fight or flight response. It’s laserfocused and lightning-fast at identifying potential problems. This instant identification of negatives is what can trap us into living in obstacles.
Living in possibility requires refusing to let the negativity bias rule our thinking. There are a few steps that can make a significant impact, helping us to manage this pitfall and transform the way we think.
1. Pinpoint the problem. First, we must be able to spot when the negativity bias is at work. The easiest way to do that is by monitoring one simple phrase we say: “Yes, but….” On the surface, these words seem innocuous. And because we say them and hear them so frequently, they don’t seem like a problem.
However, this short phrase is a massive blockade to creative and visionary thinking. It dismisses any potential positives in an idea or concept, before even identifying what those positives might be. Instead, it focuses the energy and attention of both the speaker and the listeners on all the possible negatives. This can easily overwhelm any idea and immediately kill it.
2. Manage your mind. Once you’ve determined the negativity bias is at work (someone said “yes, but…”), the next step is to make a conscious choice to change your thinking. The key is to FIRST identify the potential positives in any idea, before focusing on the negatives.
This sounds easy. But it’s actually quite hard. It’s counter to a basic instinct, so it really does require a conscious choice to think this way, plus very real discipline to put it into practice regularly.
3. Nix the negatives. The next critical step is to refrain from saying the negatives out loud – at least not yet. The truth is, regardless that you’ve consciously chosen to identify the positives first, your brain will subconsciously identify the negatives anyway. It’s instinctive and instant. So even while you’re enumerating positives, your brain will be busy identifying negatives, too. But the simple trick of not saying those negatives out loud will help dramatically. Force yourself to speak out loud, and write down, the positives first.
4. Teach the team. When working with others, ask them to do the same. Help them understand that letting our natural negativity bias dominate the conversation has the potential to immediately kill ANY idea. Let everyone know that, of course, there will be a time to solve the problems in the idea, but the first task is to identify the potential in the idea. If there aren’t enough potential positives, then it’s time to move to a new idea.
But if the idea is visionary and can make a real difference, it’s imperative to hold off on the negativity bias momentarily and allow the brilliance of the idea to shine through.
5. Transform the troublesome term. Once the above steps have led you to a potentially winning idea, it’s time to address the problems with the idea. To continue to remain in possibility, you must change the conversation; you cannot return to “yes, but…” language.
Instead, articulate the challenges as a “how might we…?” question. So, instead of saying “Yes, but it’s too expensive”, instead say “How might we do it more affordably?” This trick of flipping a problem statement into a problem-solving question is a neuroscience brain hack that will revolutionize your thinking and problem-solving.
This process of identifying positive potential first is the ONLY way to find big ideas. Every successful innovation, in any industry or endeavor, is the result of someone, or a team, choosing to live in possibility in this way.
Visionary thinking requires making space for ideas that initially seem scary or difficult. It takes some real courage to push past our immediate
“yes, but…” response and instead focus the conversation on “what if…?” If we don’t hold ourselves accountable to look for the positives, we’ll never consider nor implement any truly new ideas. Visionary thinkers must master this skill and learn to live in possibility.
Susan Robertson empowers individuals, teams, and organizations to more nimbly adapt to change, by transforming thinking from “why we can’t” to “how might we?” She is a creative thinking expert with over 20 years of experience speaking and coaching in Fortune 500 companies. As an instructor on applied creativity at Harvard, Susan brings a scientific foundation to enhancing human creativity. To learn more, please go to: SusanRobertsonSpeaker.com.
The American Rental Association (ARA) indicates that United States equipment rental revenue surpassed its prepandemic highs in 2022, ending the year as a $56.1 billion industry. The ARA released the updated first-quarter forecast at The ARA Show™ 2023 in Orlando. In 2023, the United States equipment rental industry’s growth with soften, but still grow. Year-over-year growth in 2022 was around 13.5 percent and year-over-year growth is expected to be around 5.3 percent in 2023 and 1.9 percent in 2024. Despite a slowdown, positivity is evident among ARA members with large and small operations.
www.ARArental.org
Toyota Material Handling (TMH), joined representatives from Cornell University’s College of Engineering to officially dedicate the revolutionary Toyota Forklift Learning Studio at Cornell University’s Sibley School of Mechanical and Aerospace Engineering. This is the world’s first Forklift Learning Studio and the result of a unique and dynamic partnership between TMH and Cornell, bringing students a creative outlet for realworld application in a revolutionary and immersive learning experience that could become a model for impactful change in higher education.
www.toyotaforklift.com
Southwestern Scale Company Inc. (SWSCALE), a servicer, manufacturer, and provider of industrial and commercial-grade weighing scales has announced that they have opened a new office in the DallasFort Worth metroplex, in an effort to boost efficiency and services to the Lone Star State. The Phoenix-born business is in its 75th year of operation. www.swscale.com
The Raymond Corporation’s 8910 end rider pallet truck has been named a finalist for an International Intralogistics and Forklift Truck of the Year (IFOY) Award, which recognizes the industry’s best intralogistics products and system solutions from around the world. Adaptability, operator comfort, and sustainability features make the 8910 pallet truck perfect for a range of tasks, especially long hauls. The IFOY Award honors the best industrial lift trucks and intralogistics solutions of the year. www.rayhmondcorp.com
Mitsubishi Logisnext Americas announced that Cat Lift Trucks will return as the Official Lift Truck Provider for the 2023 Houston Livestock Show and Rodeo™. For 19 consecutive years, Cat Lift Trucks and its local dealer Darr Equipment Co, have played a critical role in the production of the largest livestock exhibition and rodeo in the world.
www.logisnextamericas.com
www.rodeohouston.com
www.darrequipment.com
Felling Trailers Inc has recently been awarded a cooperative purchasing contract in the Trailers category at Sourcewell. Felling Trailers, Inc. was awarded a Sourcewell contract following a rigorous request for proposal process resulting in contracts that meet, or exceed, local procurement requirements. Sourcewell is a self-sustaining government organization helping government, education, and nonprofit agencies with access to cooperative purchasing solutions. For close to a decade, Felling Trailers has held a Sourcewell contract. The company received its first Sourcewell awarded contract in 2014 in the Heavy Equipment Trailers category.
www.felling.com
KION North America has announced its territory expansion with dealer partner Carson Material Handling. This expansion includes a new location in Campobello, S.C., and involves the acquisition of J&J Forklift Services. Carson Material Handling is authorized to sell the Linde Material Handling and Baoli brands. For almost 20 years, Carson Material Handling has been a fleet management solutions provider throughout North Carolina and North-Western South Carolina.
www.kion-na.com
www.carsonlift.com
Plus One Robotics announces the appointment of Elle Carroll as sales director, responsible for developing new business and expanding relationships within the 3PL and General Merchandise industries. Carroll comes to the company with significant supply chain and robotic solution experience in both sales and engineering. Prior to joining Plus One, she was employed at Berkshire Grey (Bedford, Mass.) as a principal sales solution architect responsible for designing and contracting its robotic solutions at major retailers.
www.plusonerobotics.com
Hamilton Caster & Mfg. Co. announced that it has named Mark Lippert as its new President. Hamilton Caster, a 116-yearold manufacturer of heavy-duty industrial casters, wheels, carts, and in-plant trailers, is in its fourth generation of family leadership. Mark succeeds his cousin, David R. Lippert, who retired in December. Mark joined Hamilton Caster in 1995 to lead marketing efforts that have resulted in a brand that has been ranked #1 in brand perception studies for the industrial manufacturing market.
www.hamiltoncaster.com
Tompkins Solutions, a supply chain consulting and material handling integration firm, announced that Steven Nickel has joined the company as senior director of operations. In addition to leading the implementation team, Nickel will be
responsible for developing policies and procedures that improve performance and drive productivity. Nickel brings over 30 years of project management experience to Tompkins, successfully managing over $2 billion in various forms of construction procurement delivery. Prior to joining Tompkins, Nickel was senior project manager for Material Handling Systems, Inc.
www.tompkinsinc.com
Felling Trailers Inc.has recently named Joe Pessen as a regional sales manager to serve the South-Central territory. He will be responsible for all sales development, activity, and dealer support within Nebraska, Kansas, Oklahoma, Arkansas, Texas, and Louisiana. As the regional manager for the south-central territory, Joe’s primary responsibilities will be to achieve regional market share objectives with the existing dealer base and develop new dealers in the assigned territory, providing training and product support.
www.felling.com
Lift Atlanta is the latest dealer to join the expanding LiuGong North America dealership network in the South. Leaders of the North Georgia-based business said they were looking for a new manufacturer at the end of 2022 and were intrigued by what they heard from current LiuGong dealers and their customers. Lift Atlanta is headquartered in Decatur, Georgia with an additional location in Augusta. The company was founded as a forklift dealer in 1975 by Mitchell Milovich, Lift Atlanta CEO.
www.liftatlanta.com
www.liugongna.com
WOMEN
POWERFUL
ENERGETIC
STEPS
Data provided by SalesLeads
IMI SalesLeads announced today the February 2023 results for the new planned capital project spending report for the Distribution and Supply Chain industry. The Firm tracks North American planned industrial capital project activity; including facility expansions, new plant construction and significant equipment modernization projects. Research confirms a total of 166 new projects in the Distribution and Supply Chain sector. A 10% increase in new construction projects reported from the previous month with Texas leading the way with 16 projects.
SOUTH CAROLINA: Home appliance mfr. is planning to invest $50 million for the renovation and equipment upgrades on a recently leased 584,800 sf distribution center in GREENVILLE, SC. Completion is slated for early 2024.
MAINE: Federal agency is planning to invest $33 million for the construction of a warehouse, maintenance, and office facility at Acadia National Park in ACADIA, ME. Construction is expected to start in Spring 2023, with completion slated for Fall 2024.
The following are selected highlights on new Distribution Center and Warehouse construction news.
Distribution and Supply Chain - By Project Type
• Distribution/Fulfillment Centers - 16 New Projects
• Industrial Warehouse - 153 New Projects
Distribution and Supply Chain - By Project Scope/Activity
• New Construction - 95 New Projects
• Expansion - 35 New Projects
• Renovations/Equipment Upgrades - 35 New Projects
• Closings - 4 New Projects
Distribution and Supply Chain - By Project Location (Top 5 States)
• Texas - 16
• California - 9
• Iowa - 8
• Wisconsin - 11
• Ohio - 9
During the month of February, our research team identified 3 new Distribution and Supply Chain facility construction projects with an estimated value of $100 million or more.
The largest project is owned by Graphic Packaging International, LLC, who is planning to invest $1 billion for the construction of a 640,000 sf paperboard recycling facility in WACO, TX. Construction is expected to start in Spring 2023, with completion slated for 2026.
NEW YORK: Film and TV production company is planning to invest $400 million for the construction of a 330,000 sf studio and warehouse complex at 744 Clinton St. in BROOKLYN, NY. They are currently seeking approval for the project.
WISCONSIN: Shipping and packaging supplies distributor is planning for the construction of a 1.4 million sf distribution center on their campus in KENOSHA, WI. They are currently seeking approval for the project. Construction is expected to start in late 2023.
PENNSYLVANIA: Grocery retail chain is planning for the construction of a 1.2 million sf distribution center in FAIRLESS HILLS, PA. They are currently seeking approval for the project.
TEXAS: Medical apparel and footwear company is planning for the renovation and equipment upgrades on a recently leased 1 million sf distribution center in DALLAS, TX. They will consolidate their operations upon completion.
MISSOURI: Logistics service provider is planning for the construction of two warehouses totaling 800,000 sf at 11601 N Congress Ave. in KANSAS CITY, MO. They are currently seeking approval for the project.
NORTH CAROLINA: Transportation and logistics service provider is planning for the renovation and equipment upgrades on a recently leased 402,000 sf distribution facility at 4023 Maddux Ct. in GREENSBORO, NC.
NORTH HAMPSHIRE: Apparel retailer is planning for the renovation and equipment upgrades on a recently leased 378,000 sf warehouse, manufacturing, and office facility at 48 Friars Dr. in HUDSON, NH. They will consolidate their operations upon completion.
KENTUCKY: Logistics service provider is planning for the renovation and equipment upgrades on a 200,000 sf warehouse at 4293 Winston Ave. in COVINGTON, KY.
Since 1959, SalesLeads, based in Jacksonville, FL is a leader in delivering industrial capital project intelligence and prospecting services for sales and marketing teams to ensure a predictable and scalable pipeline.
Data provided by SalesLeads
IMI SalesLeads has announced the February 2023 results for the new planned capital project spending report for the Industrial Manufacturing industry. The Firm tracks North American planned industrial capital project activity; including facility expansions, new plant construction, and significant equipment modernization projects. Research confirms 110 new projects in February as compared to 130 in January in the Industrial Manufacturing sector.
COLORADO: Semiconductor mfr. is planning to invest $880 million for the expansion of its manufacturing facility in COLORADO SPRINGS, CO. They have recently received approval for the project.
NEW YORK: Wind turbine mfr. is planning to invest $500 million in the construction of a manufacturing facility in COEYMANS, NY. They are currently seeking approval for the project.
The following are selected highlights on new Industrial Manufacturing industry construction news.
Industrial Manufacturing - By Project Type
• Manufacturing/Production Facilities - 98 New Projects
• Distribution and Industrial Warehouse - 71 New Projects
Industrial Manufacturing - By Project Scope/Activity
• New Construction - 34 New Projects
• Expansion - 38 New Projects
• Renovations/Equipment Upgrades - 41 New Projects
• Plant Closings - 14 New Projects
Industrial Manufacturing - By Project Location (Top 10 States)
• California - 10
• Indiana - 8
• Texas - 7
• North Carolina - 5
• Alabama - 4
• Ohio - 8
• Michigan - 7
• Georgia - 6
• Tennessee - 5
• New York - 4
During the month of February, our research team identified 12 new Industrial Manufacturing facility construction projects with an estimated value of $100 million or more.
The largest project is owned by Texas Instruments Inc., which is planning to invest $11 billion in the construction of a manufacturing facility in LEHI, UT. They are currently seeking approval for the project. Construction is expected to begin in Fall 2023, with completion slated for early 2026.
KANSAS: A defense contractor is planning to invest $2 billion for the construction of a 235,000 S.F. computer chip manufacturing facility in BURLINGTON, KS. They are currently seeking approval for the project.
SOUTH CAROLINA: Semiconductor mfr. is planning to invest $443 million for the renovation and equipment upgrades on a 300,000 S.F. manufacturing and office facility at 1800 Overview Dr. in ROCK HILL, SC. They have recently received approval for the project. They will relocate their headquarter operations upon completion in Fall 2023.
UTAH: Consumer goods mfr. is planning to invest $400 million for the expansion of its paper product manufacturing facility in CORINNE, UT. They have recently received approval for the project.
GEORGIA: Auto body parts mfr. is planning to invest $300 million in the construction of a manufacturing facility in RINCON, GA. They are currently seeking approval for the project. Completion is slated for 2025.
IOWA: Industrial valve mfr. is planning to invest $75 million for a 36,000 S.F. expansion and equipment upgrades on their manufacturing facility in OSKALOOSA, IA. They have recently received approval for the project.
MINNESOTA: Fluid control equipment mfr. is planning to invest $43 million for a 176,000 S.F. expansion of their manufacturing facility in ANOKA, MN. They are currently seeking approval for the project. Construction is expected to start in the Summer of 2023, with completion slated for late 2024.
NORTH CAROLINA: EV charging station mfr. is planning to invest $41 million for the construction of a manufacturing facility in DURHAM, NC. They have recently received approval for the project.
TENNESSEE: Water heater mfr. is planning to invest $30 million for the expansion of its manufacturing facility in LEBANON, TN. They are currently seeking approval for the project.
Since 1959, SalesLeads, based in Jacksonville, FL is a leader in delivering industrial capital project intelligence and prospecting services for sales and marketing teams to ensure a predictable and scalable pipeline.
HeroWear set a new standard for exosuits in 2020. In 2023, they're set to do it again. The industry-leading company has unveiled the highly anticipated Apex 2 — the latest version of its back-assist exosuit.Back injuries and related musculoskeletal disorders (MSDs) cost American companies $225.8 billion per year, according to the CDC — that’s an average of $1,685 per employee every year. www.HeroWearExo.com
Concentric is launching PowerHIVE™, the industry’s first automated forklift battery and charger system, providing ondemand, sustainable, and scalable battery power whenever it is needed. Their newest innovation in equipment power management marries automation with forklift battery systems - eliminating the need to think about forklift charging or battery maintenance. www.concentricusa.com
At the Retailers International Leaders Association, (RILA), AutoScheduler.AI introduced the Make-n-Ship warehouse optimization platform that optimizes loading products straight off the production line to better orchestrate production, warehousing, and transportation plans. Moving production runs directly to a truck eliminates touches, helps with labor shortages, and reduces the need for storage space in a warehouse or distribution center located at the manufacturing site.
www.autoscheduler.ai
In Hamilton’s latest line of new industrial wheels, U-Grooved Track Wheels are designed for easy rolling along straight or curvy tracks or pipes. With a capacity range of 1000 – 7000 lbs., U-Groove Wheels are a great solution when working with crane cables or pulleys, or using rolling gates and doors. They’re also common in food services, washdown, and other industries where tubed tracks are commonplace.
www.hamiltoncaster.com
LEDtronics® announced its latest line of LED Linear High Bay Luminaires. These versatile lighting solutions offer a wide range of features and benefits that make them ideal for various applications.The new Linear High Bays are available in both 2-foot and 4-foot lengths and feature multi-wattage and multi-color temperature tunable units. With the ability to choose from three different CCTs – 3500K Medium White, 4000K Natural White, and 5000K Pure White, and wattage options ranging from 15 to 60 watts.
www.ledtronics.com
Gears and gear racks used for transmitting torque and forces within gearboxes are typically made of hardened steel. For many other uses and applications, gears and racks made from plastic are the better choice. These generally require no lubrication and are lighter, quieter, less expensive, and more resistant to corrosion than metal gears. This is why JW Winco is expanding its range with polyamide gears and racks that can transmit high forces and torques.
www.jwwinco.com
Elebia Autohooks has launched eLINK, a central control system for its range of automatic hooks and rigging products that can be used on mobile and smart devices. eLINK is a plugand-play concept that allows users to automate material handling processes, monitor hook status, conduct remote service, create reports, and oversee lifecycle management. Launched in 2006 to improve safety and productivity, the Elebia range now includes numerous hooks, lifting clamps, grabs, and shackles—all of which are compatible with eLINK. www.elebia.com
ProVeyance Group introduced its innovative new FlexExtend Conveyor System at ProMat 2023. FlexExtend is a flexible gravity conveying system with self-tracking skate wheels. The system is designed for low- to medium-volume, multi-sized conveyance operations. This high-flow product can be extended, contracted, or flexed into curves to meet specific material handling requirements..
www.ProVeyance.com
UgoWork offered a sneak peek into a new lithium-ion battery management solution at ProMat
UgoWork™ unveiled a brand-new lithium-ion battery management solution at ProMat 2023. UgoWork’s showcased its lithium-ion batteries for industrial trucks, pay-per-use approach, and real-time fleet monitoring services, the company’s lithium-ion battery management solution will put material handling team’s in the driver’s seat for more effective and efficient means to track performance levels and energy usage.
www.ugowork.com
Metal fabrication company Penn Sheet Metal, Allentown, Pennsylvania, has cut the time required to stretch-wrap its pallet loads of architectural and roofing components and custom decorative building products from an average of 15 minutes per load to 60 seconds or less by replacing manual stretch-wrapping with the automated TAB Wrapper Tornado orbital wrapping machine. The machine is designed and manufactured by TAB Industries that offers a range of automated and semi-automated orbital wrappers in several sizes to suit nearly any pallet wrapping requirements.
www.tabwrapper.com www.pennsheetmetal.com
West Point Rack is one of the fastest growing companies in the industr y. Our customers recognize quality products, dependability of service and competitive pricing
Our Primar y Goal is to suppor t our dealers, satisf y their customers, earn trust and be the “ Vendor of Choice” for rack products and racking systems
We of fer a full line of light duty, intermediate duty, heav y and extra heav y duty cantilever racks. We provide multiple configurations of a wide variety of stacking racks Our structural pallet racks can be configured for a wide range of applications. West Point Rack h as the products that generates solutions for your storage needs.
We also of fer specialty products such as bar cradle trucks, drum racks, hand car ts and other specialty transpor t and storage products. Give us a call at 866. 245. 3630. We may have what you need Look forward to hearing from you