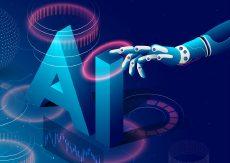
5 minute read
AI in production: Think before you act
ARTIFICIAL INTELLIGENCE
ARTIFICIAL INTELLIGENCE IN PRODUCTION
Advertisement
Although AI offers some great potential benefits, care does need to be exercised before incorporating it into industrial applications. Tim Foreman, offers some guidance.
Companies can be over eager to start implementing Artificial Intelligence (AI) technologies without being fully aware of the challenges they could face.
When considering AI the first step should be to identify the problem that you wish the technology to solve. Companies often find that the biggest problem they face is they are not able to pinpoint the problem they want to solve. Once the problem is realised, companies also find that despite wanting to implement AI, they face another hurdle as some are not yet measuring data, which makes it difficult to incorporate AI solutions. To solve this, companies will need to start collecting and cleaning data before even thinking about introducing AI.
One difficulty is that a lot of existing data is not suitable for analysis, as it is contaminated, duplicated or scattered, or there is key information missing. So, while there is huge potential for the use of new technology, you can only use it if the data being gathered is both sufficient and correct. When starting to think about AI, it is also important to think in a broader sense about data science and what and how much data is needed before coming to a conclusion. You will need a substantial amount of data if you want to reach the right conclusions.
The next step is to consider implementing AI. It can be applied at various levels, depending on the problem that needs to be solved. For example, to compare the performance of two factories, it is necessary to gather the data and put it into the cloud (inside or outside the enterprise), it is then possible to compare and analyse the data and start to draw conclusions.
But the main challenge remains: What problem do you want to solve? A company with strong, toplevel management should know the key challenges it faces and will want to use the most effective tools to optimise its performance. The problems faced will determine what needs to be done. For example, is there a need to look wide, at a lot of data? For example, to compare a large amount of data from 20 factories, this is where AI in the cloud can play a key role. However, if an immediate reaction on a bottling line is needed to avoid downtime, a solution with AI at the edge should be considered.
The machines within a factory are a potential source of valuable data, however there are key questions that need to be addressed from the outset: • Data: Is there enough? Which data is the most relevant? How will it be used? • Infrastructure: What is the cost of infrastructure? • Outcome: What problem really needs to be solved? How can cloud or edge computing improve business efficiency?
Some manufacturing facilities might decide to send all data to the cloud. Large IT companies are promoting this as the solution to everything. However, it isn’t a panacea, as it doesn’t show or respond in real time to what is actually happening in the machines. This is why Omron has focused on the development of tools to help the human brain cope with the challenges of what is happening inside the machines – along with details
of downwards analysis and pattern recognition.
Within an industrial manufacturing environment, you can look at the actual process within the machine with edge computing technologies. Real-time data processing at the edge enables an immediate response to an abnormal situation in a process. With AI at the edge, manufacturers are able to control complexity and security. To translate information into action, manufacturers need efficient control and monitoring for a more natural, proactive relationship between operator and machine.
With edge computing, the data and the computing resources are located close to the machines. This enables users to gain real-time information about the efficiency of different aspects of their industrial automation system. This makes it possible to access intelligence within the machine, which in turn enables deep analysis to be carried out.
In this way, AI can contribute to direct and immediate results, because the intelligence is incorporated within the machine rather than being located elsewhere. Users can focus on potential issues in the process, using the real-time data from the system and its components.
Conclusion
Traditionally, programming a machine to recognise micro-second skill patterns in the local data that might be entering it, has been next to impossible. All machines may have had this information but until recently it has been ignored.
The introduction of AI solutions at the edge – inside the machine – has changed this. It can provide tools that enable you to look at that data. Advances in technology mean that you can have machine control equipment that will process that data and recognise patterns within it.
Ultimately, both cloud computing and edge computing are great solutions for a factory starting to use AI. But it’s clear that in terms of using AI in the production line, edge computing really does appear to have the edge. !
Tim Foreman is european R&D manager at Omron.
ARTIFICIAL INTELLIGENCE
Reducing the complexity of deploying machine learning for quality inspection
Pleora Technologies has introduced a machine vision artificial intelligence (AI) platform that is said to simplify the deployment of advanced machine learning capabilities to improve the reliability and lower the cost of visual quality inspection. “While AI promises to revolutionise quality inspection, integrators and designers struggle with how to costeffectively integrate advanced capabilities into existing and new applications,” said Harry Page, president, Pleora Technologies. “Pleora’s AI Gateway platform is an evolutionary approach to AI, with plug-in machine learning skills for classification, sorting, and defect detection combined with the flexibility to train and deploy open source or custom algorithms. Users can immediately employ AI to reduce inspection errors, falsepositives, and secondary screenings while preparing for more advanced Internet of Things (IoT) and Industry 4.0 applications.”
With Pleora’s new gateway end-users and integrators can more easily deploy AI skills without the need for any additional programming knowledge. Through a web-based interface, images and data are uploaded to ‘no code’ training software on a host PC, which generates a neural network that is deployed onto the Pleora AI Gateway.
Your Global Automation Partner
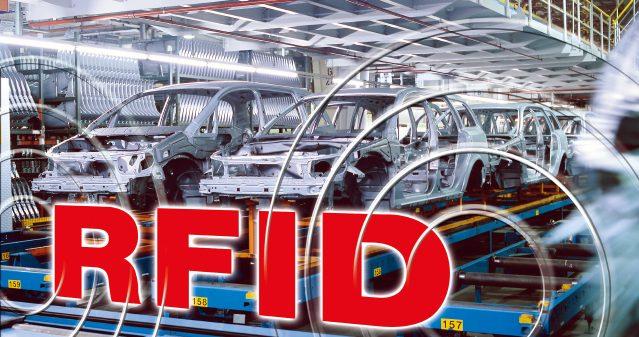
Data, when you want it, where you want it!
Advantages for industrial Automation from TURCK. More effcient production based on higher application speeds. Simple integration into control environment with interfaces for PROFIBUS-DP, DeviceNet™, Ethernet Modbus-TCP, PROFINET IO, EtherNet/IP HF & UHF carriers and read/write heads Extended temperature range data carriers up to 210 °C Specialist data carriers including moisture detection. www.turckbanner.co.uk