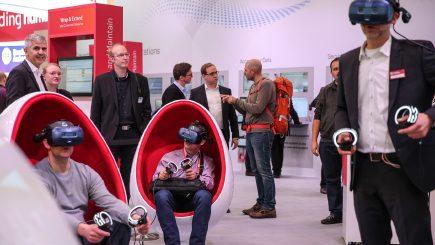
7 minute read
Operation-driven matrix design
EXHIBITION REVIEW
in the field of Single Pair Ethernet (SPE) has recently expanded by the creation of the Single Pair Ethernet - Industrial Partner Network and the news that Würth Elektronik, LEONI, Murrelektronik and Softing IT Networks are now also supporting SPE technology as a future infrastructure solution for the IIoT.
Advertisement
Harting introduced its T1 Industrial, which is said to be the first standardised SPE interface in line with the release of IEC 63171-6, which brings data and power on one pair of wires to previously unattainable locations.
Also on display was the MICA Edge Computing System which demonstrated its ability to work in conjunction with machines and the Cloud.
Blurring boundaries
Under the motto ‘Faster. Better. Connected. discover hybrid automation in a new dimension’, Festo used the event to demonstrate how the boundaries between pneumatic and electrical automation are blurring, with the introduction of many new pneumatic, electrical and hybrid automation solutions. It also set out to focus on its smart production solution, in the context of digitalisation.
With the Simplified Motion Series Festo is expanding its product portfolio in the field of electric drives. The six drives are designed for simple motion and positioning tasks. In addition, the drives can be quickly put into operation without software, previous knowledge of programming or electrical connection technology, with integrated IO-Link offering extended functions.
A highlight on the stand was Automation Suite which includes a range of software tools for commissioning the entire electrical drive package from mechanics to control. The software combines parameterisation, programming and maintenance of Festo components in a single program.
Gigabit EtherCAT
The EtherCAT Technology Group (ETG) used the event to highlight its support for gigabit EtherCat technology, in the form of EtherCAT G, following its acceptance as an addition to the EtherCAT standard.
Commenting on the addition, Dr Guido Beckmann, Chairman of the ETG Technical Committee, said: “EtherCAT is already the fastest industrial Ethernet fieldbus, and will remain so, due to its special functional principle. With EtherCAT G particularly data-hungry applications, such as machine vision and high-end measurement technology, can now also be integrated. This extends the range of applications for EtherCAT technology and makes it even more viable for the future.”
It is thought that the existing 100 Mb/ sec EtherCAT technology will continue to offer the best solution for the majority of applications. However, EtherCAT G offers additional user advantages, especially in applications where particularly large amounts of process data must be transported per device. This can include machine vision, high-end measurement technology or complex motion applications that go beyond the scope of classic drive control. As an extension of standard EtherCAT technology, EtherCAT G is fully compatible; existing devices designed for 100 Mb/sec can be seamlessly integrated into an EtherCAT G system, and EtherCAT G devices in a 100 Mb/sec EtherCAT system behave like classic EtherCAT devices.
The central element of EtherCAT G is the use of EtherCAT Branch Controllers, which fulfil two main functions: On the one hand, they act as a kind of node for the integration of segments from 100 Mb/sec devices; on the other hand, they enable parallel processing of the connected EtherCAT segments. This significantly reduces the propagation delay in the system, which increases system performance many times over previous levels.
Beckhoff demonstrated the benefits of its TwinCAT Analytics offering for machine builders and systems integrators looking to transform their business models through the use of machine and plant process data.
TwinCAT Analytics – which automatically converts analysis configurations into executable PLC code –now also includes a one-click dashboard generation feature. All it
takes for users to generate an entire HTML5-based analytics dashboard based on the PLC code and to load it into a selected Analytics Runtime container is a simple mouse click. When the process completes, users receive a network address that they can then use to access the dashboard in a web browser. The ability to generate dashboards without the need to write a single line of code or design graphics can offer huge timesavings within the engineering process.
Based on TwinCAT 3 HMI, the new functionality provides at least one HMI Control for every TwinCAT Analytics algorithm, each with an up-to-date tile design that follows the latest web standards. The controls contained in a dashboard can be selected individually in an algorithm’s properties with the aid of a control preview. Users can also combine multiple algorithms within an individual HMI Control.
Belden demonstrated how it is able to offer cost and time savings for a wide variety of connectivity requirements – from sensor to the cloud – to help deliver maximum productivity and uptime.
A number of new products and technologies were shown from the Belden, Hirschmann and Lumberg Automation product ranges designed to enhance the productivity of industrial systems and machines. These included Single Pair Ethernet (SPE) technology solutions with Time Sensitive Networking (TSN) capability and the Hirschmann EAGLE40 Industrial Firewall, a ruggedised multiport cybersecurity solution which is designed to maximise uptime in automated environments. Evolving alongside data transfer demands, the EAGLE 40 includes more port options with increased bandwidth and encryption capabilities.
Controller with software separation
On the Emerson Machine Automation Solutions stand the IC695CPL410 controller was pointed out as a highlight. It is said to be unique in its ability to create a software separation of the quad core system into two dualcores capable of running completely separate operating systems. It does this by utilising a powerful quadcore processor and a virtualisation technique known as hypervising.
So, one dual-core system can run the PAC systems engine just like the one that runs on the RX3i PAC systems hardware while the other dual-core system could be treated like any computer.
The design team put Ubuntu Server Linux on the hardware, which offers opportunities for software developers and customers to merge the plant floor with the tools that are taken for granted in the IT environment.
The two halves of the CPL410 connect via an internal NIC that can pass OPC-UA data back and forth. For any tag on the PLC side, it is possible to choose to publish the tag or not. Ultimately, the control of this is on the PLC programmer. Setting the publish tag to False means that the tag won’t be exposed to the Linux side of the CPL410. Another option for this setting is ‘External Read Only’ meaning the tag can be seen by the Linux side, but not changed. The final option is ‘External Read/Write’ meaning that the tag can be seen and changed by the Linux side. This distinction is important as it means that the PLC programmer can pick and choose which variables remain hidden and which can be changed by the Linux side.
Ethernet physical layer
The biggest topic for discussion on the Analog Devices stand was the the release of new industrial Ethernet physical layer (PHY) products to help manufacturers address key Industry 4.0 and smart factory communication challenges surrounding data integration, synchronisation, edge connectivity, and system interoperability.
The ADIN1300, for example is a low-power, single port Ethernet transceiver designed for time-critical industrial Ethernet applications up to Gigabit speeds and designed to
EXHIBITION REVIEW
operate reliably in harsh industrial conditions over extended ambient temperature ranges. It is the latest technology developed for the company’s ADI Chronous portfolio of industrial Ethernet solutions.
ADI Chronous Ethernet solutions encompass a range of industrial Ethernet technologies from realtime Ethernet switches, physical transceivers and protocol processing to complete network interface products. Designed to support scalable and flexible system development, the ADI Chronous product portfolio offers multiple port count, low power consumption, and flexible bandwidth. Being multiprotocol, these solutions are compatible with all existing protocols while also providing the ability to future-proof for TSN features.
On the ABB stand visitors could find out how the company’s Manufacturing Operations Management (MOM) software suite is able to streamline production by enabling seamless plant orchestration. A new version of Ability MOM software platform offers an extended range of capabilities and new digital applications designed to give operators, supervisors and plant managers the visibility and insights to take the right actions for increased productivity, quality and compliance.
New features in the enhanced MOM platform include enhanced user experience based on new HTML 5 web client; a new interactive dashboard application that provides greater visibility and collaboration; a new statistical process control (SPC) application, to determine if each process is in a state of control; and a new Batch Compare application – for advanced batch analysis !