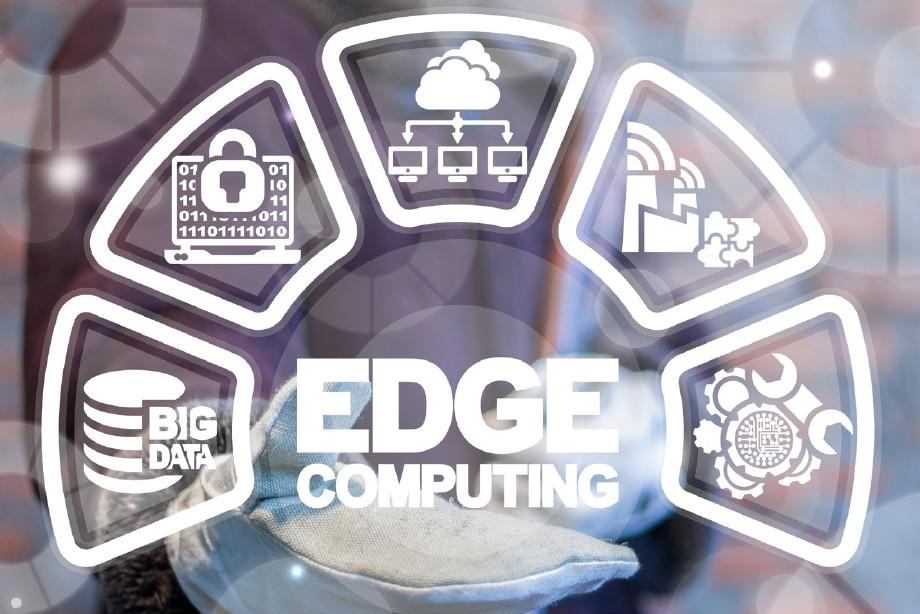
12 minute read
Suzanne Gill looks at the importance of implementing plant connectivity from the edge to the cloud to make the best use of data
MAKING EDGE TO CLOUD INTEGRATION PAY
Suzanne Gill finds out why it is important to implement plant connectivity from the edge to the cloud to make the best use of data made available thanks to the Industrial Internet of Things (IIoT).
Advertisement
Investment in Industry 4.0 technologies – with standardsbased platforms supporting edge infrastructure – will enable critical machine and plant data to be monitored and analysed on site, offering better latency for decision making. Meanwhile, the cloud is able to use data provided by the
IIoT to support higher analytical performance, especially where multiple plants are uploading data.
Industrial enterprises should really be looking to achieve connectivity from the edge to the cloud to allow for fast decision making based on real-time edge data, while also benefitting from higher resilience and secure remote access to mass storage data, reports, updates and notifications, offered by the cloud.
Greg Hookings, head of business development – digitalisation at Stratus
Technologies, agrees with this need, pointing out that while focusing just on edge computing will give valuable real-time insight into operations on the plant-floor, without linking edge computing to the cloud the benefits of consolidating and processing larger amounts of contextualised data are lost. He said: “Without edge to cloud connectivity, artificial intelligence (AI) and broader digital transformation approaches, that require data from cross-business functions, are lost.
“At the other end of the spectrum, a cloud-only approach can reduce efficient management at a local level,” continued Hookings. “While the enterprise would be able to process large amounts of data with information from the entire supply chain, operators at the machine level would be reliant on bandwidth and availability to have access to information. Even in areas with high bandwidth, the data collected by machines needs to be sent to the cloud for analysis and so latency becomes a factor – reducing real-time reactivity. In some manufacturing processes such a delay might be enough to lose an entire batch, or bring production to a halt.”
Bringing these two disciplines together in a combined solution means that, at the machine level, operators have all the information they need as soon as they need it and large amounts of non-time critical data can be sent to the cloud for analysis. “What this creates is an enterprise with a global, contextualised understanding of its processes and an enabled, flexible, agile workforce, equipped to overcome challenges in real-time,” said Hookings.
Taking steps
Slawomir Dziedziula, technical systems engineer at Panduit EMEA, believes that there are a number of steps that will ensure successful data flow from the edge to the cloud. These include: • Plan and implement a robust and high-quality physical infrastructure that is suitable for the harsh environmental conditions of the plant. • Design for standardised and normalised data and protocols to ensure data extraction is simplified and consistent. • Support this with stable and redundant network connectivity between edge and the cloud. • Decide what information and tasks will be analysed locally using real time computing. • •Select a suitable analytical platform and deploy policies to decide which data is sent to the cloud. • Create a central point of control and
decide who can access data and from where it can be accessed.
“With a robust development process an edge structure and cloud solution can maximise an organisations’ capability operationally at a physical site level and corporately in planning, implementation and analytics,” said Dziedziula. “More data analysed faster will benefit the business”.
Steve Pavlosky, director, digital product management at GE Digital, advises that any edge to cloud integration strategy should start with the end in mind. “Consider whether the data will be used for plant level decision making or just in aggregated form from across the enterprise or fleet of assets,” he said. “If the data will be used locally, a solution to aggregate it, such as a historian, can provide the basis for storage, normalisation, and access for local use. In addition, a historian can enable the right subset of data at the right frequency and the right aggregation level to be sent on for cloud-level analytics. Applications that derive value from the aggregation of distributed data only in a centralised way require a different IIoT approach.”
Pavlosky advises that companies embarking on an edge to cloud strategy should also consider the following points: How big a team will be needed to build, and later maintain, this solution and how much time will it take to build and test the solution? What type of skills will be needed on the team and what are the scale requirements? In addition, security should always be top of mind.
“Once these questions have been answered, companies can reduce risk by using supported software that leverages the latest secure-by-design technologies to minimise the threat of cyberattacks,” said Pavlosky.
Generally, he advises that an integration strategy should reside on three main pillars:
Security: While the cloud is largely secure and the OT network should be secure by this point, the only area of vulnerability is the edge gateway device and the pipe to the cloud. Ensuring high levels of security at the edge becomes the foremost consideration.
Scalability: The edge platform should scale with a company’s growth plan and most importantly, it should be priced appropriately.
Flexibility: An edge platform should be flexible enough to work with both legacy and new systems. The edge platform should allow the flexibility to port existing apps onto the platform regardless of the language they were originally written in.
A suitable strategy
Offering his thoughts on how to identify a suitable integration strategy to ensure data flows from the edge to > p14
Leaders in temperature measurement
TemperatureSensors
InStockForImmediateWorldwideDespatch
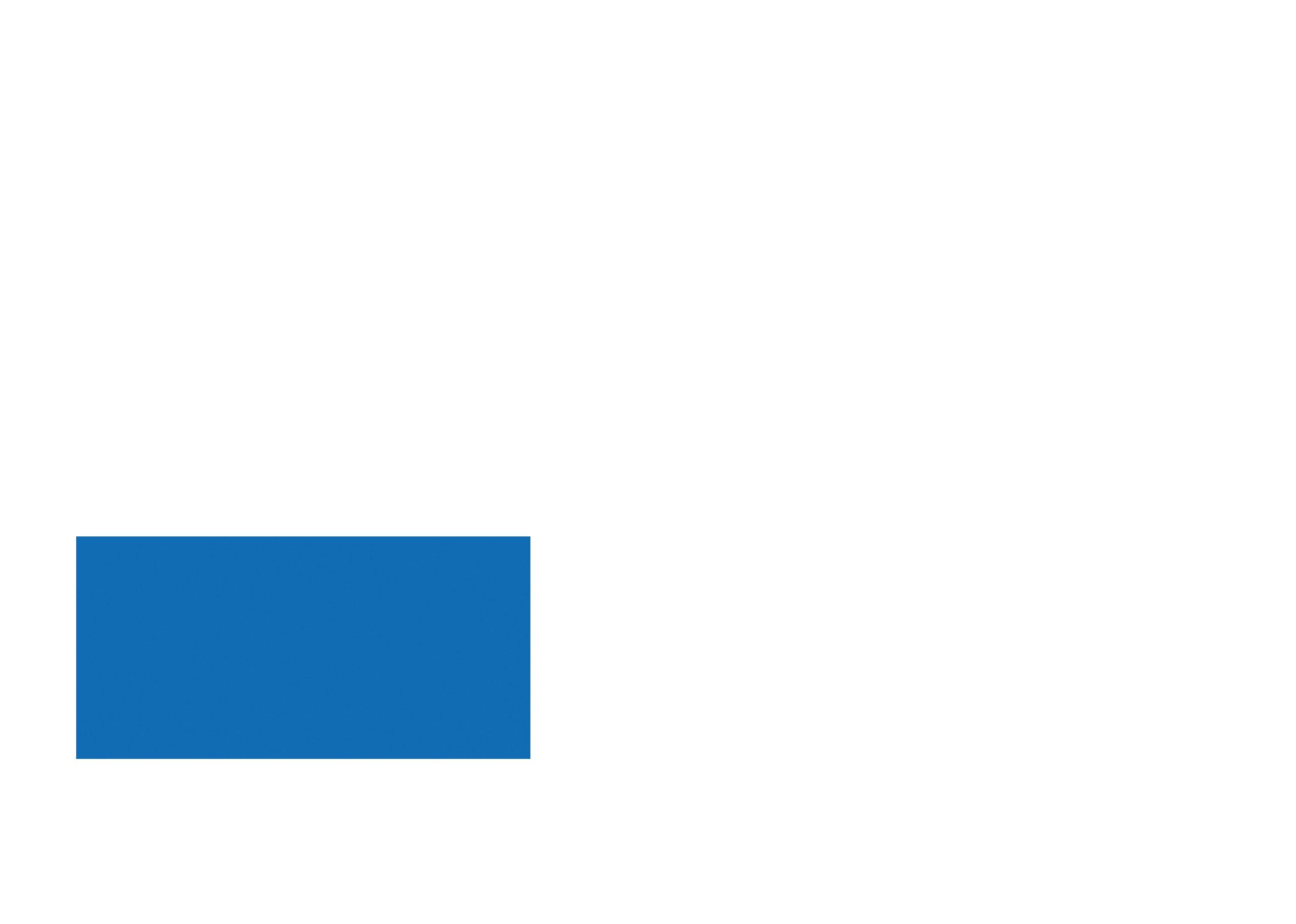
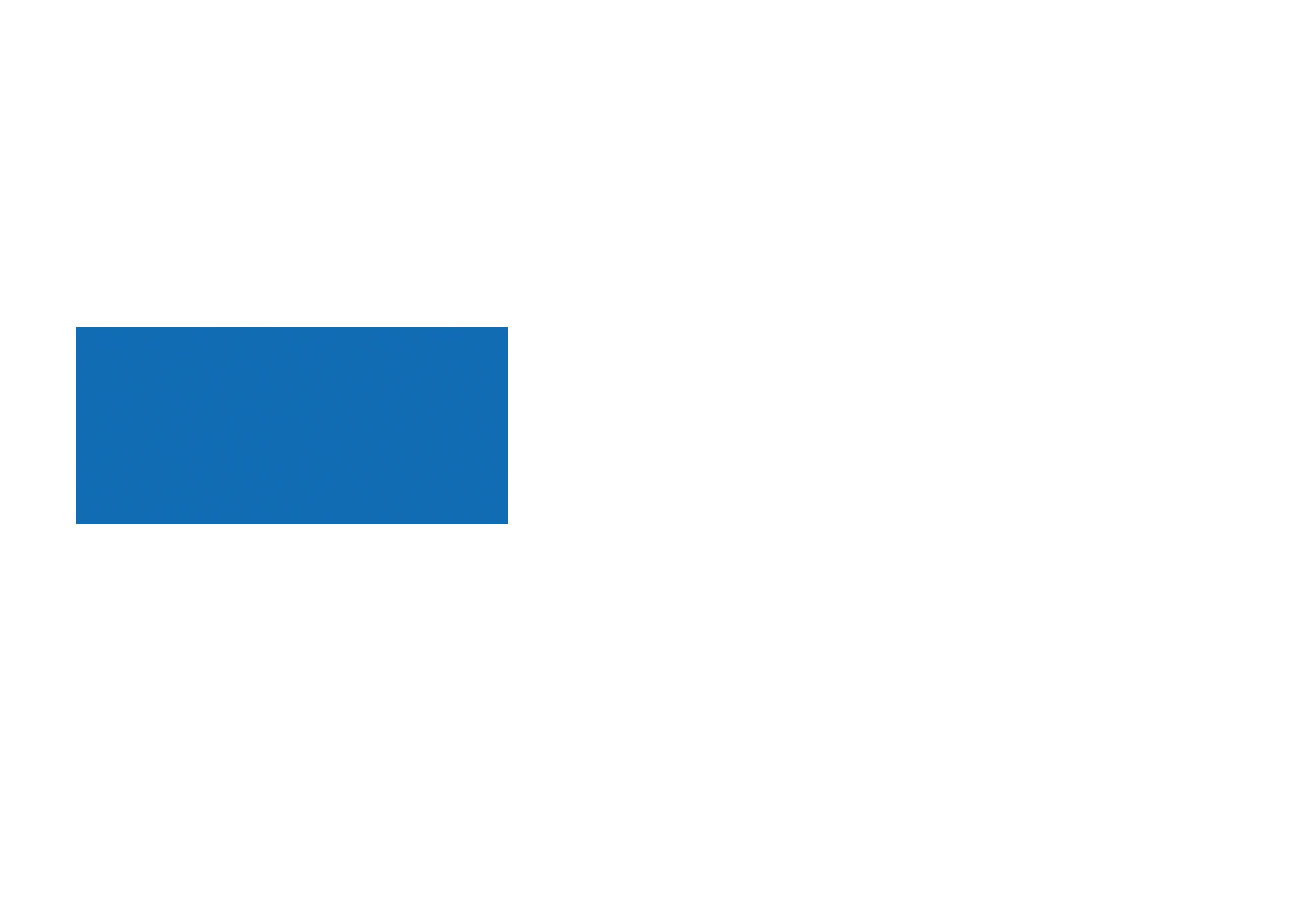
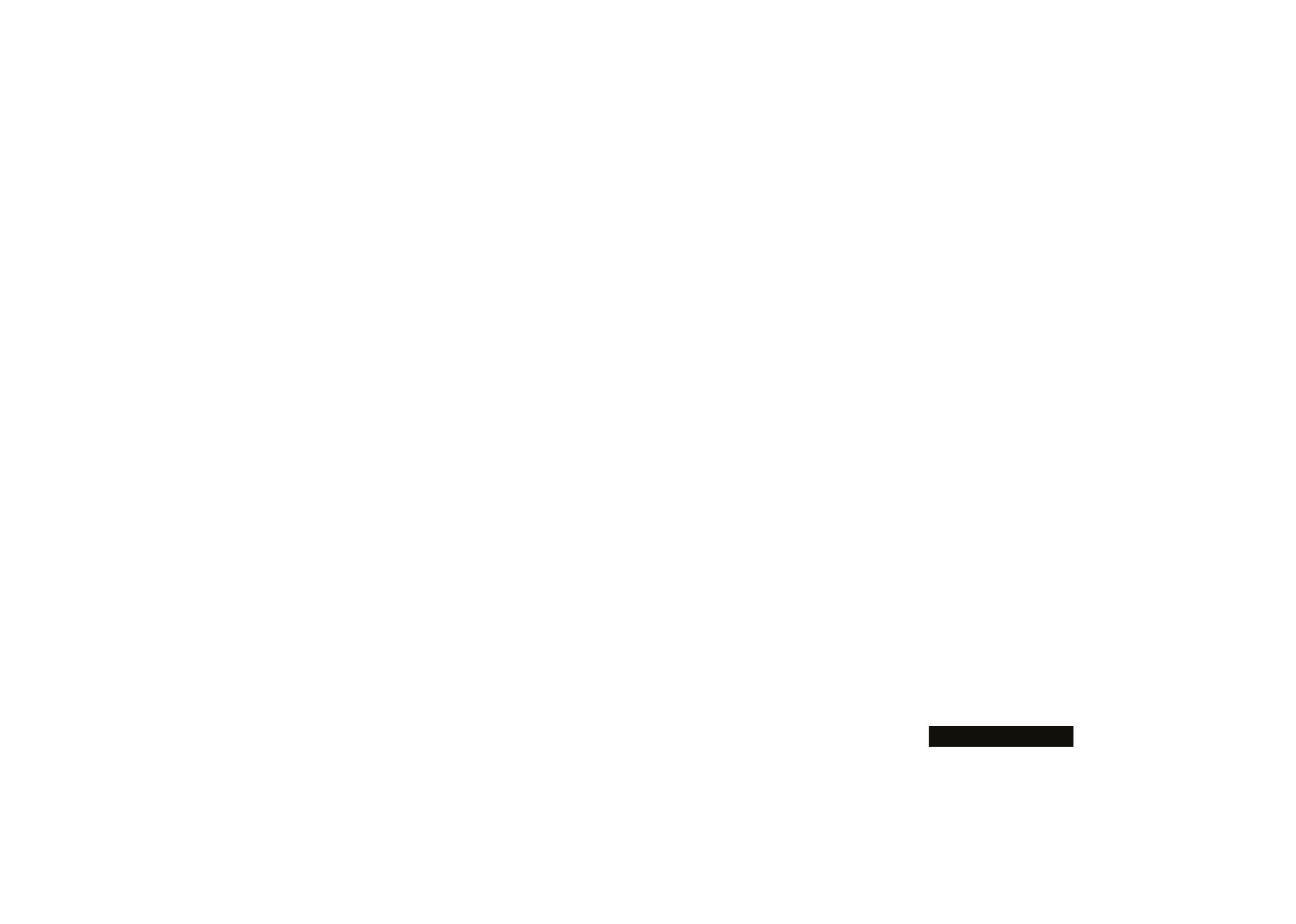
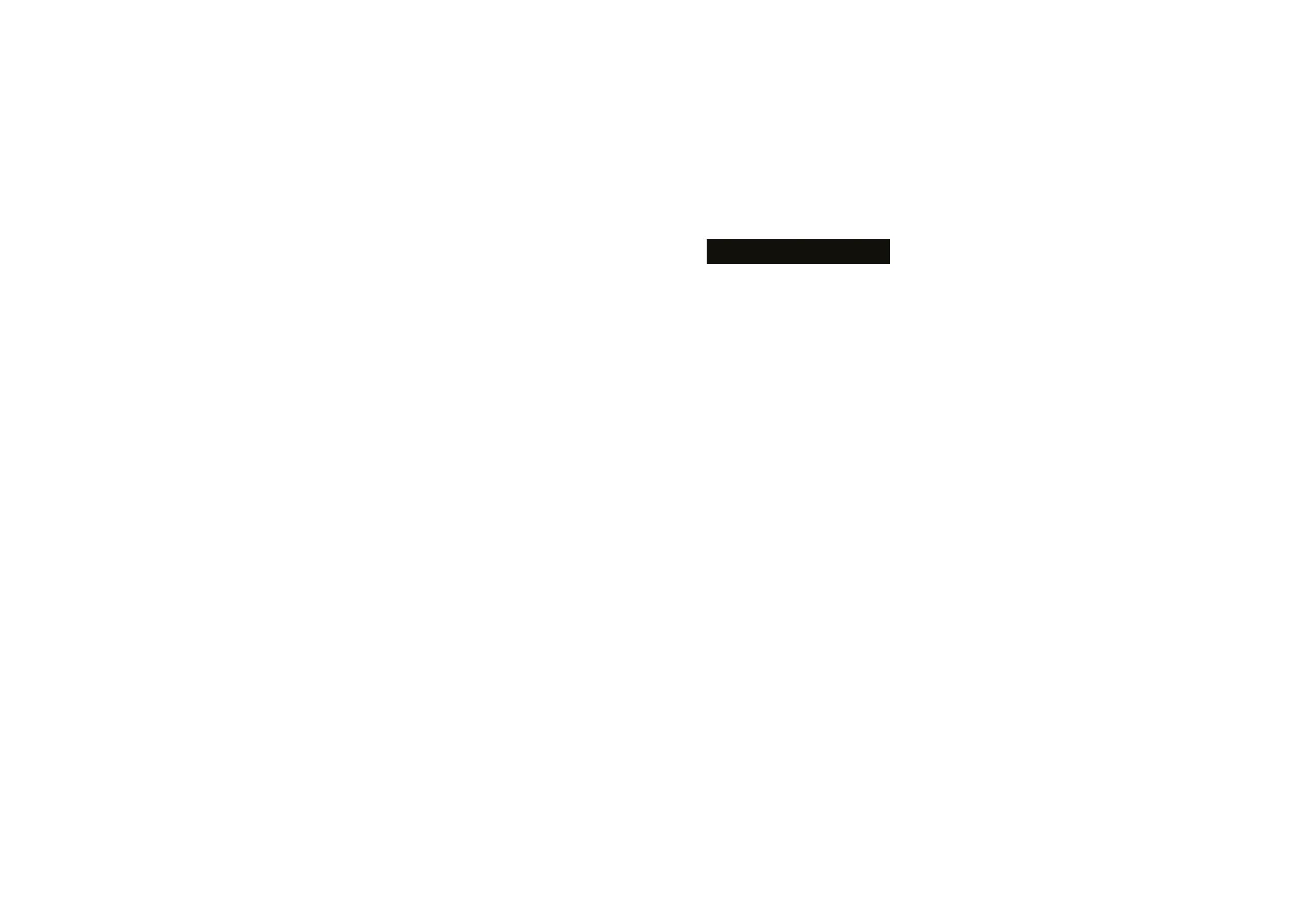
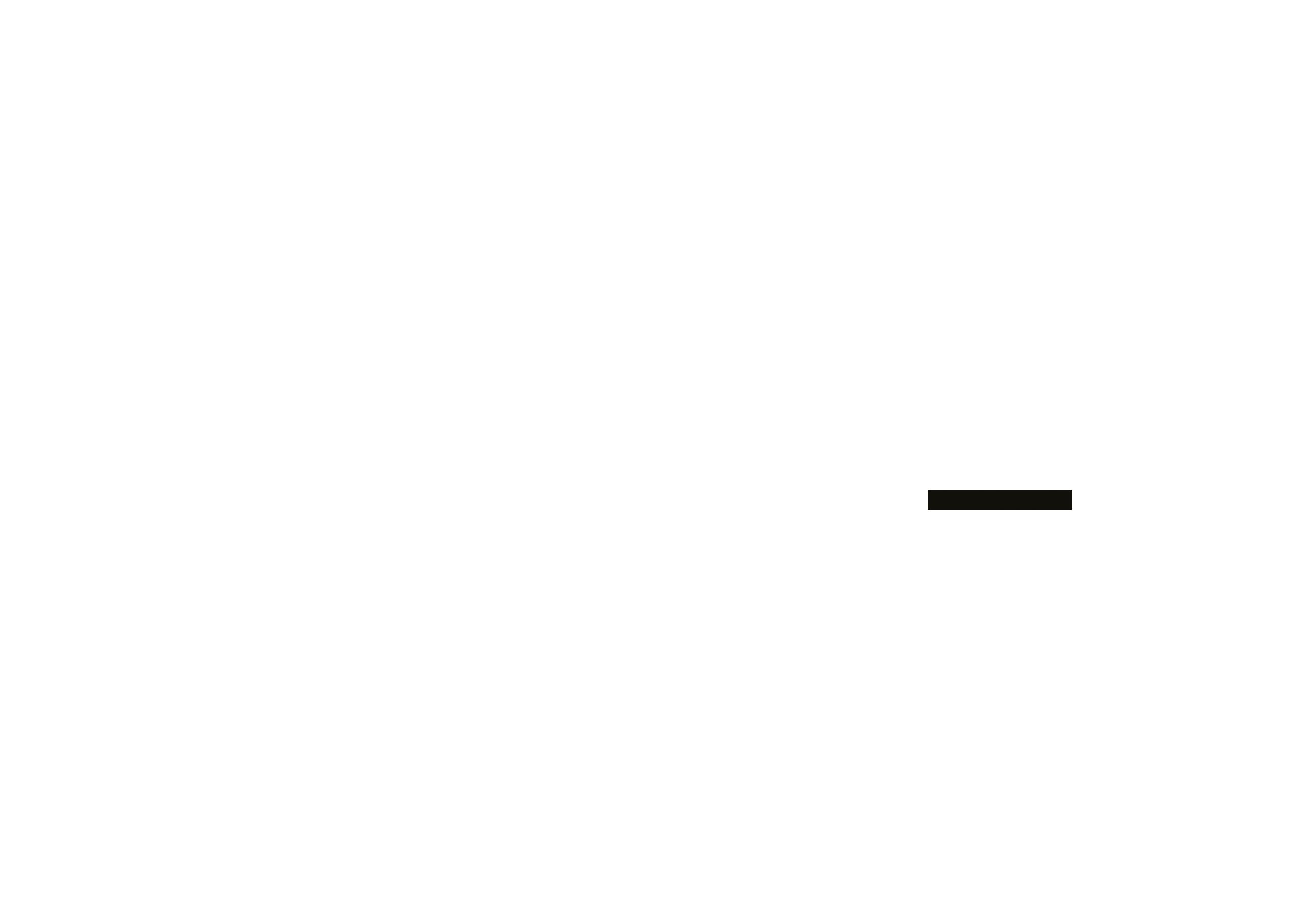
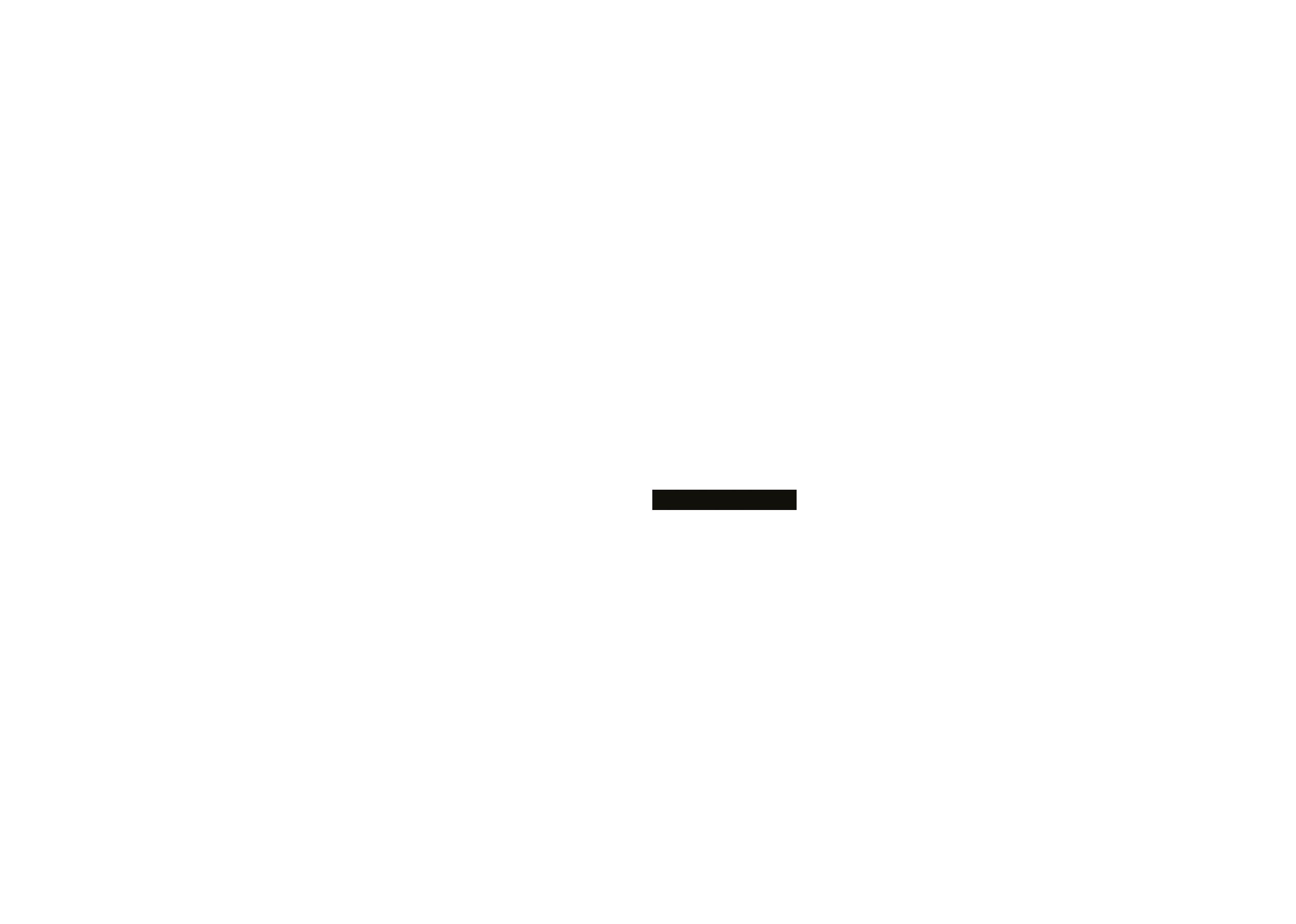
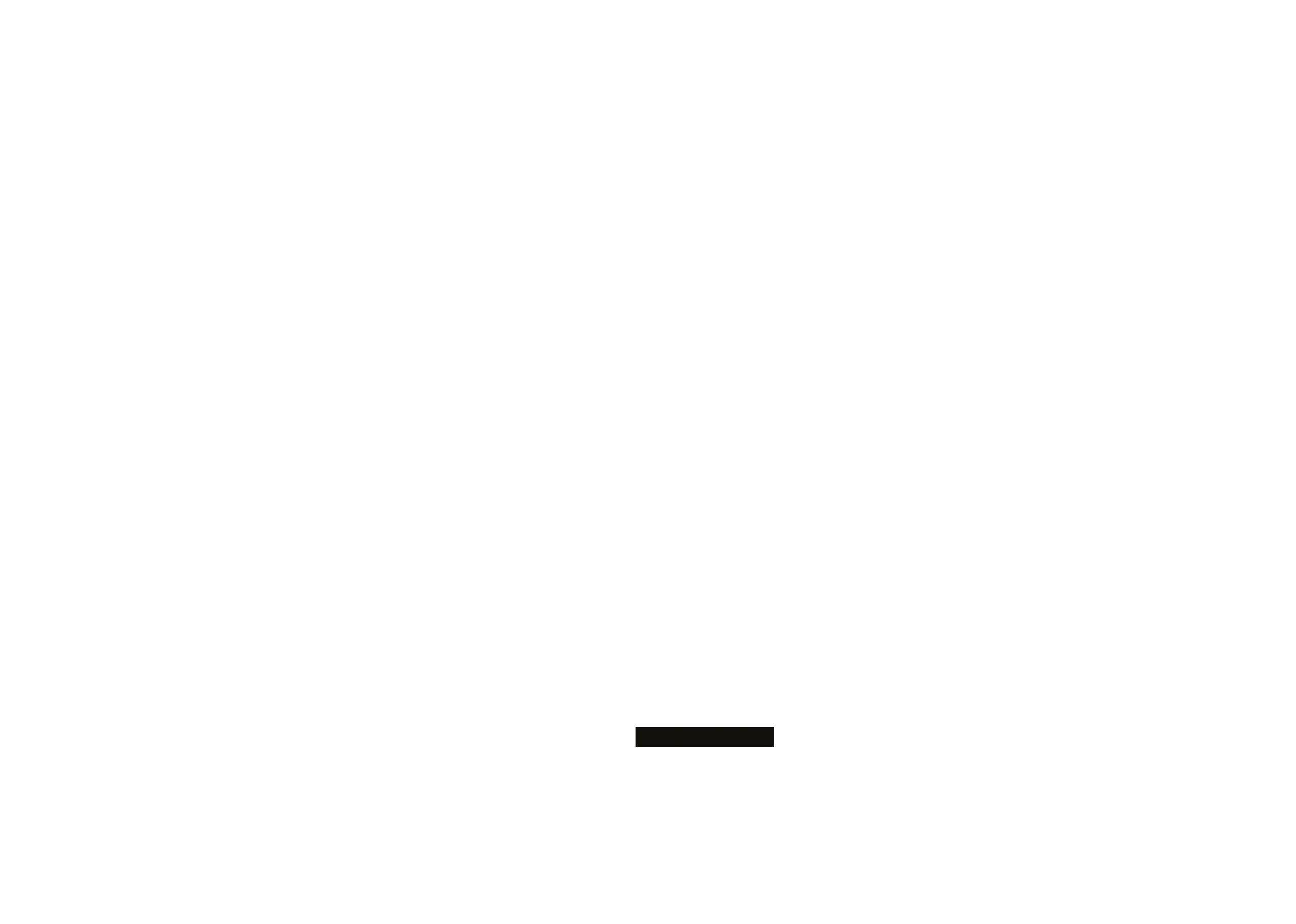
Heading3Manufactured by Labfacility
IEC and ANSI options available
Mineral Insulated Thermocouples with various termination options
Platinum Resistance Thermometers
Pt100
IndustrialIndustrial StyleStyle ThermocoupleThermocouple withwith
Terminal Head
Environmental Sensors
Flat Film and Wire Wound Detectors
Handheld Sensors
Fabricated and Specialist Thermocouples


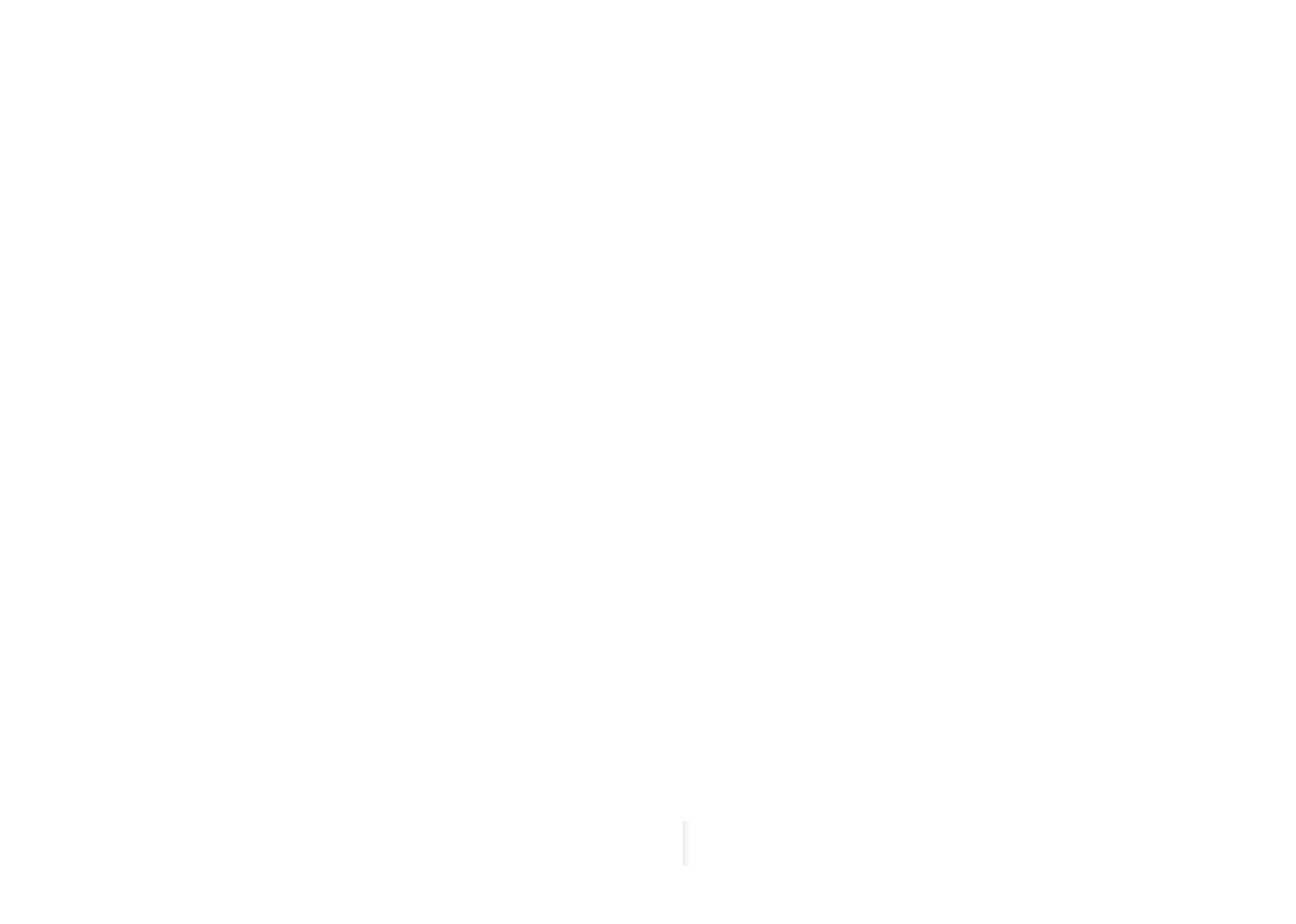
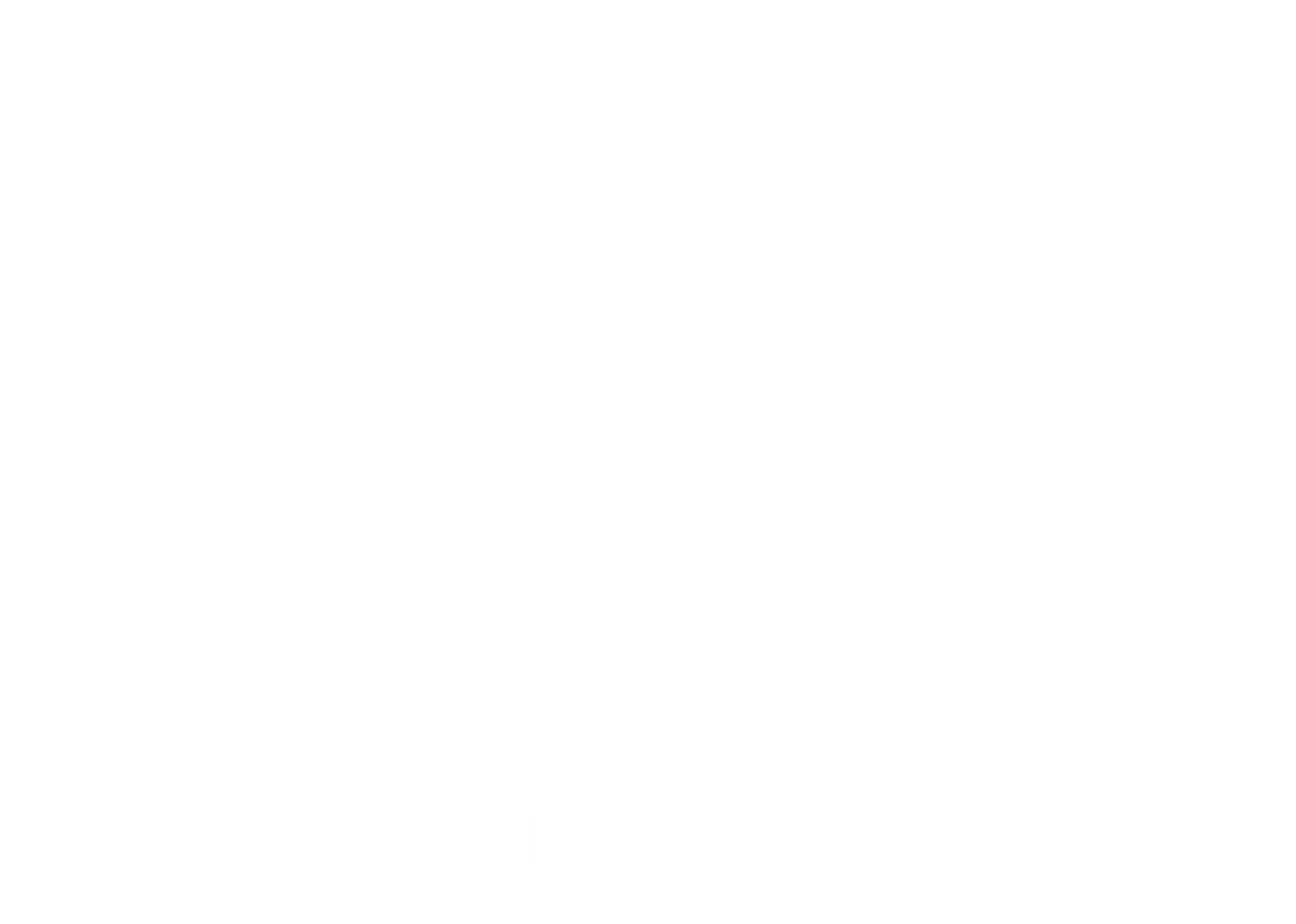



XE - 3630 - 001
XE - 3223 - 001
XE - 3660 -001 XE - 3470 - 001
XE - 3534 - 001
the cloud, Hookings says that this will be unique to each enterprise and will depend on the existing connectivity, the legacy systems, the software languages in use and most importantly, the desired outcome. “The best way to approach data connectivity is to consider it in terms of a broader digital transformation journey that involves every function of the business,” he said. In this way, he believes that the approaches adopted will underpin future development and enable the continuous, exponential development that new technologies offer. “This needn’t be overly complex,” he said. “From a data point of view, simple principles, such as using edge computing platforms that offer virtualisation, simplicity, autonomy and an intrinsically secure deployment, can offer the versatility required to link to existing or planned business software in the data centre, and/or in the cloud. The right place to start is where ROI can most readily be achieved – the low hanging fruit. If you know the cost of IT-related downtime, for example, eliminating – or drastically reducing it – can have an immediate impact on the bottom line.”
Barriers to data flow
Marco Zampolli, Industrial IoT solution architect & senior PSM at Advantech Europe, highlights the fact that the physical location of plant items may make certain technologies impractical or cost prohibitive when it comes to ensuring edge to cloud data flow. He said: “Fundamentally, the communication path must be reliable and must offer enough bandwidth to transfer all the generated data in a timely manner. But, this will mean different things in different situations, and so the value of the data must also be considered.” Offering an example, Zampolli points that it is likely that engineers would want to monitor the temperature of a critical process much more closely, and would therefore accept a higher cost of data collection, than say for the level of fuel supply to a back-up generator, which changes at a much slower rate.
“Processing can be added to filter and transform data as it passes towards the cloud, and this means it is relatively easy to morph the data into any desired data model and protocol as it progresses up the chain,” continued Zampolli. “However, what is possible is ultimately constrained by the characteristics of the plant itself, so the architecture needs to be optimised to maximise connectivity at the plant level, and then edge processing can be applied to transform this data into a unified model as early as possible.” Operating in this way gives the flexibility to optimise the balance between speed, reliability and coverage of the data and the cost of the processing and communication systems needed to recover and process it.
It is an unfortunate fact that, with so many legacy systems in place in plants, there will always be barriers to achieving edge to cloud integration. “Hoping to find a factory without legacy systems is unrealistic,” said Zampolli. “They conspire against the implementation of IIoT architectures simply because they were created to execute a specific task – often without any consideration about exchanging
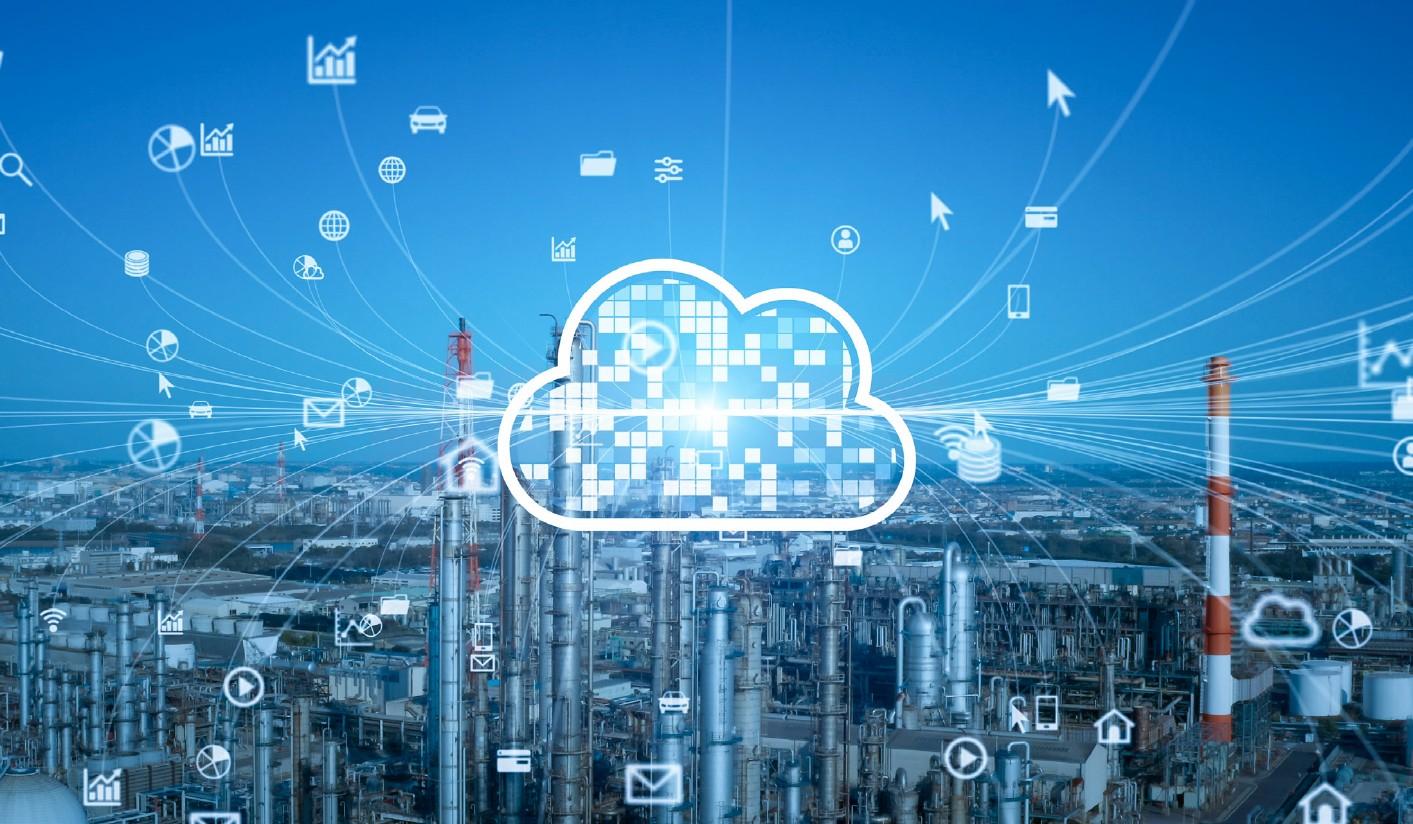
information. Even when information exchange is supported in legacy equipment, it could take place using a plethora of different proprietary protocol standards, often designed to only be used for local physical connections.”
How can this problem be overcome? Zampolli advises the introduction of a layer of intelligence at the edge, close enough to the plant to have physical connectivity to it, which can then translate bidirectionally between any disparate and mutually incompatible protocols into a unified model for onward transmission, adding the necessary error detection and security characteristics. “This edge layer needs two main features,” he said. “Flexibility for easy adaptation to different legacy systems, wherever possible by configuration rather than programming; and a small and industrial footprint to be close to the data generation without interfering with the process.”
Hookings highlighted a legacy equipment issue that can be overcome with edge computing – security. “There is widespread concern that adding previously un-networked operational technology to the enterprise level network can increase security risks by adding more points of vulnerability. However, by deploying the right edge computing hardware to previously unconnected operational technologies, it is possible to protect both the physical asset through restricted access and the cybersecurity with in-built protection. A network is only as secure as its weakest node and this is often legacy equipment. Deploying edge computing can help to bring ageing hardware up to modern standards of protection without huge expense.”
What’s in it for the engineer?
So, how might cloud to edge integration benefit the role of the control engineer? “Edge and cloud computing both have their places in industrial operations, I believe that edge to cloud connectivity will result in the emergence of a hybrid professional,” continued Hookings. “The gap between IT and OT has continued to diminish and this has had an effect on the role of the control engineer. The challenges that once only faced programmers in the IT world now affect control engineers as more businesses enable digital transformation. A control engineer no longer just focuses on configuring SCADA, for example. They have to configure the entire process all the way to real-time asset control.”
Zampolli believes that the seamless integration of edge and cloud, and the corresponding analysis tools which can be brought to bear on the resulting consolidated data lake, can significantly benefit the control engineer. “Big data analysis will show in an automated way the correlation of the different variables in a production environment – irrespective of the complexity,” he said. “The control engineer will be able to consider optimisation not just of each individual machine, but instead of the entire process, adjusting the performance of the individual elements to benefit the whole. Comparison of performance across production lines or across different factories, shift patterns or raw material variations, will lead to more subtle insight into what is really important to improve output and yields. Best of all, this can occur in real time – changes can be implemented and tested, their effects judged and, if positive, can be rolled out across multiple lines in minutes rather than weeks or months taken by traditional, paper based, data collection and reporting.
“With such a solution, instead of being viewed as an operational role, primarily concerned with keeping the factory running, the control engineers position is elevated into a critical strategic asset, focusing on continuous process improvement based in evidential analysis, and using their knowledge of the process and plant to create, test and deploy ever more flexible and efficient working practices,” concludes Zampolli.
Commenting on how edge to cloud integration can benefit the control engineer, Dziedziula believes that the new level of aggregated data analytics is key, especially where multiple sites are contributing data, to provide benefits such as predictive maintenance based on real time and historic data across the organisation. He said: “Simplified and secure access to site data from anywhere and any authorised device, reduces the need for routine on-site inspection. A major benefit is handing maintenance and support for the IT platform to the cloud provider, allowing engineers to refocus on performing their core activities more effectively.”
The last word goes to Hookings, who believes that, by focusing on real-time asset control, the machine level can utilise the deployed edge computing to improve overall equipment efficiency (OEE). Integration right up to the cloud means that the control engineer can make changes and improvements that apply to the entire enterprise. No longer will changes on the plant floor be driven just by the business requirements of the boardroom – indeed, the opposite will also be true – business changes will be driven by new insight, flexibility, and capability from the plant-floor.
“The digital transformation drives the needs of customers just as it drives capabilities for manufacturers. Customers expect faster delivery times at lower prices and the planet requires all of this in a more sustainable, energy efficient way. Enabling edge to cloud integration allows enterprises to use the expertise at machine level to make significant gains in all of these areas without massive, costly changes to production processes. Moreover, well planned and executed digital strategies will help form a digital backbone that enables the progressive change of the digital transformation journey to bear fruit at every step.” plus-circle