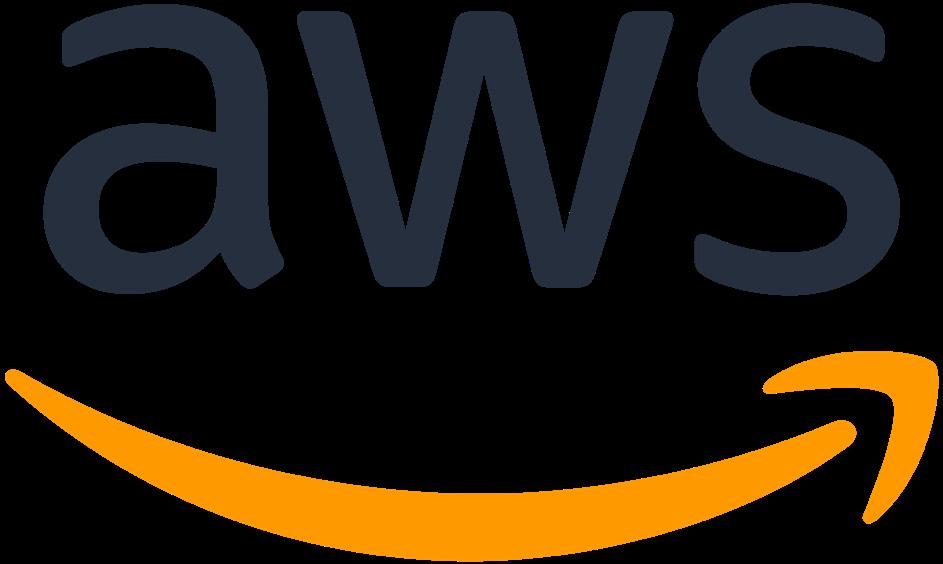
14 minute read
Amazon turns up the heat on predictive maintenance; User conference to focus on enabling smarter, safer and more sustainable operations
Amazon turns up the heat on predictive maintenance
Blake Griffin discusses the recent move by Amazon into the industrial predictive maintenance arena.
Advertisement
At the end of 2020, Amazon announced a suite of new Amazon Web Services (AWS) machine learning services. To many, this appeared to be Amazon’s launching point towards becoming a major supplier of predictive maintenance solutions. However, the announcement follows a long history of Amazon carving out its capabilities in industrial digitalisation. Since the e-commerce behemoth’s 2018 release of AWS IoT Sitewise – a service which enables users to gather and organise asset health related data housed in repositories such as a historian – Amazon has been adding to its industrial digitalisation offering.
In some ways the announcement represents a rounding out of a predictive maintenance offering rather than a jumping off point. When manufacturers are looking at implementing predictive maintenance into their facilities, they are asking fundamental questions such as: Which assets do I have visibility into already and how can I leverage this data? Which assets do I not have visibility into and what can I do to change that?
The announcement of AWS IoT Sitewise was Amazon’s answer to the first question. Industry generates large amounts of data from the devices controlling its machines. This data is often stored in a historian and without the tooling necessary to effectively manage and analyse such data, much of its value can be lost. AWS IoT Sitewise was developed so this data could be more effectively utilised for condition monitoring/predictive maintenance purposes. The solution is deployed through software housed in a gateway which then communicates the collected data to the AWS cloud. This marked Amazon’s true entry into the predictive maintenance market.
Fast forward to Amazon’s most recent announcement and we see the company moving to provide a solution to question two. Assets that are often cited as being ‘offline’ from a condition data perspective are the mechanical portions of a motor driven system. These components are numerous throughout factory floors and their failure can represent significant loss of production if they are part of an application critical process. The industry responded to this need by offering smart sensors – wireless enabled sensors which can be connected to the side of a motor to gather data on vibration and temperature behaviour.
One of the Amazon services announced in late 2020 has been coined Amazon Monitron. The solution utilises smart sensors and gateways produced by Amazon to offer up data on the health of motor system equipment; effectively solving the problem of gathering data on assets not being monitored via historian data. This solution is in direct competition with predictive maintenance providers such as ABB, Siemens and SKF. Amazon’s utilisation of data housed in a historian, combined with its smart sensor offering and vast analytics capability offered through AWS, have one distinct advantage over the competition as Amazon is also a provider of cloud storage.
Every platform offered by the major providers of predictive maintenance are built on cloud storage technology offered largely by either AWS or Microsoft Azure. So, the development of Amazon’s industrial digitalisation offering represents the first time a supplier has the ability to provide both the cloud storage and analytic capabilities under one entity.
It is difficult to foresee what impact this will have on the partnerships AWS has in place with industrial digitalisation providers. What is easy to see, however, are the numerous advantages Amazon will have in potentially winning the business of those investing in industrial digitalisation for the first time. If customers are looking to utilise the cloud for their industrial digitalisation initiatives, Amazon would represent the fewest number of touchpoints between customer and supplier during the sales process. Additionally, many manufacturers may already be using AWS for cloud storage but have yet to invest into further industrial digitalisation technology. In these scenarios, Amazon would already have a ‘foot in the door’ which may give them an advantage when the time comes for users to begin evaluating providers of digitalisation. plus-circle
Blake Griffin is a senior analyst at Interact Analysis
Manufacturing business leaders resist digital progress
The Connected Enterprise report, produced by Sigma Dynamics, in partnership with applied futurist, Tom Cheesewright, reveals that nearly half of manufacturing industry C-suite executives, directors and senior managers are sceptical about the benefits of implementing new business technology.
The research shows that 49% are doubtful that it improves efficiency, 40% cynical about its ability to improve productivity, and 66% question its positive impact on customer relationships.
Over two-fifths think technology can cause problems if not implemented carefully, while one-quarter believe that the cost often outweighs the benefits, 1-in-10 worry that it can create an unnecessary burden on employees.
Commenting on the report, Colin Crow, managing director of Sigma Dynamics, said: “From these statistics we can infer that there are many manufacturing leaders that have been burned by previous digital transformation efforts. It is unfortunately quite common for businesses to choose the wrong technologies, or roll them out without enough support for employees, which can lead to costly mistakes. Some of these misconceptions are therefore understandable, but as the twin threats of Brexit and the Covid-19 have shown us over the past year, the business landscape can change with incredible speed.
“The manufacturing sector must be agile and open-minded in order to cope with the impact of these, and other, national and global challenges that we will all inevitably face, and it will soon become almost impossible for businesses in the industry to thrive without the help of strategically planned and implemented technological innovations. However, from our research it is frustratingly clear that these events still have not served as a wake-up call for complacent business leaders.”
Just 34% think that they will have to implement more technology in order to remain competitive in the future, while 15% said that they believe that the technology they currently use will remain sufficient for the foreseeable future.
Applied futurist, Tom Cheesewright, added: “Covid-19 undoubtedly catalysed investment in technology in the manufacturing sector, but that investment was often overdue. If we are to avoid playing catch-up when the next challenge hits – or the next opportunity appears – then we should be thinking now about what changes to our technology, processes, culture and models can best prepare us for the future. Making the right investments in technology and skills is a critical part of future-proofing any business, adding resilience and agility.”
User conference to focus on enabling smarter, safer and more sustainable operations
Emerson Users Exchange Live 2021 EMEA online conference will offer new in-sights and innovations that are driving performance improvements for manufacturers.
The event will highlight practical innovations and solutions to help industrial manufacturers achieve performance improvements by running their operations smarter, safer and more sustainably.
With the 2021 event being held virtually, due to the Covid-19 pandemic, thousands of delegates will be able to attend more than 120 online presentations taking place live over three days, from March 29 to 31.
The conference will feature over 70 case studies presented by end users to demonstrate how they have achieved measurable business value, increased safety and enhanced their environmental sustainability through the adoption of scalable innovations such as remote collaboration, predictive maintenance and personnel safety-focused monitoring.
In addition, there will also be deep-dive perspectives and the latest insights from automation and software experts and manufacturing leaders on how to rethink processes, identify new efficiencies, reduce costs and reach higher levels of performance.
“Our goal is to drive innovation that makes the world healthier, safer, smarter and more sustainable, and this objective will be reflected across the content of Emerson Users Exchange Live,” said Roel van Doren, president, Emerson Process Management, Europe. “The global health crisis has accelerated the need for digital transformation strategies and technologies to keep the process and manufacturing industries running safely, and Emerson Users Exchange will focus on how these strategies and technologies can be leveraged to optimise operational performance.”
Free to Emerson customers, Emerson Users Exchange Live offers both live and on-demand product technology roadmaps, meet the expert sessions, subject matter expert office hours, user case studies, industry forums and product demonstrations. For more information go to: EmersonExchange.org/EMEA.
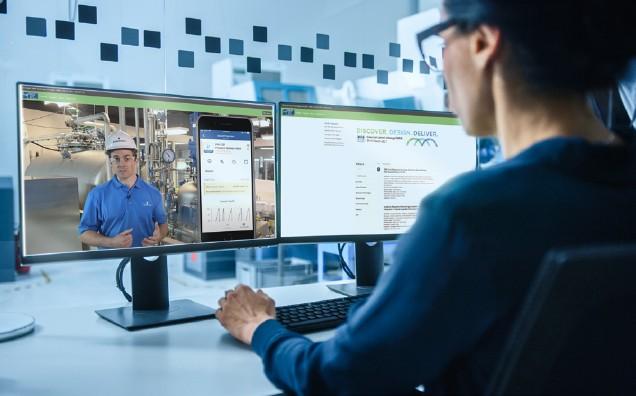
Maurice O’Brien explains how it is now possible to quickly develop and deploy an end-to-end-monitoring and predictive maintenance service-based solution and to benefit from high quality asset health insights and power on two wires.
Real-time, continuous, condition monitoring and predictive maintenance solutions continue to grow in importance as manufacturers and plant operators look to increase throughput while reducing maintenance costs and asset downtime. Condition monitoring can extend equipment lifespans, improve manufacturing quality, and increase safety in manufacturing plants.
Given that unscheduled downtime can amount to nearly a quarter of total manufacturing costs, predictive maintenance has the potential to unlock significant savings and productivity. (ref 1)
Industry market reports focused on condition monitoring and predictive maintenance project compound annual growth rates (CAGR) of 25% to 40%, as driven by two growth areas. The first is the increased deployment of smart sensors to monitor asset health. The second growth area is the increased use of artificial intelligence and advanced analytics to transform asset health data into actionable insights for predictive maintenance and create new servicebased, predictive maintenance business model opportunities. Growth in new condition monitoring deployments will range across multiple industries, including: • Waste and wastewater treatment • Manufacturing • Paper and pulp • Food and beverage • Pharmaceutical • Metal and mining • Energy • Oil and gas installations
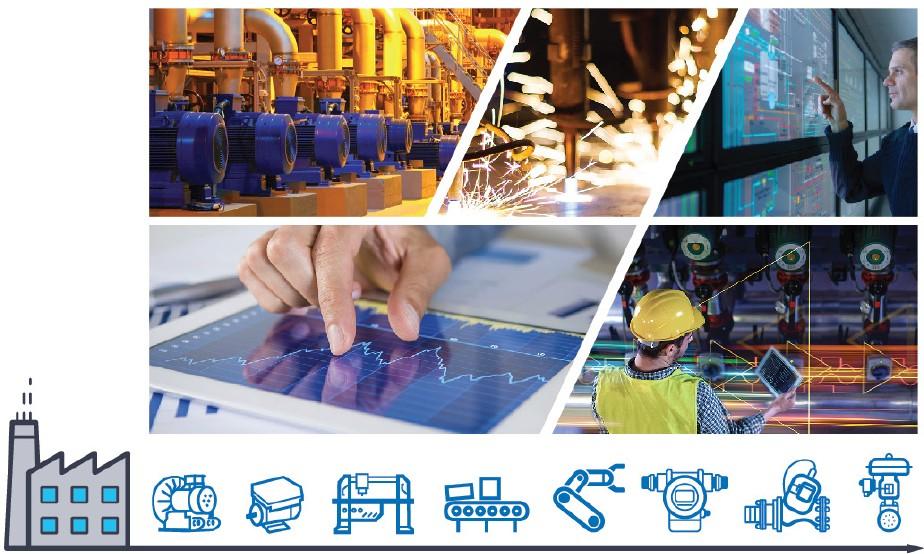
Figure 1: Condition monitoring applications.
Within these industries, condition monitoring applications are expanding beyond the traditional rotating equipment applications (pumps, compressors, and fans) to new applications in CNC machines, machine tools, encoders, conveyor belts, robotics, and instruments (see Figure 1).
Communication challenges
Connectivity from smart sensors to higher level management systems has been one of the key challenges for condition monitoring applications. To date, condition monitoring applications have used wired or wireless connectivity solutions depending on the end application requirements. Wireless connectivity solutions have advantages in terms of ease of deployment but are often limited in terms of bandwidth and/or battery life. Wired connectivity solutions are sometimes limited in data bandwidth, and long distances in harsh industrial environments are not always supported and often require a separate cable for power.
Existing Industrial Ethernet solutions based on 100BASE-TX/10BASE-T provide high data bandwidth up to 100Mb and power over a Cat-5 or Cat-6e cable with PoE but are limited to 100m distance and don’t support hazardous area use cases as they are high power solutions. Condition monitoring applications require support for potentially remote sensors that require robust communication over a long distance where the sensor node is in a space and power constrained IP66/IP67 enclosure due to the harsh industrial environment it is deployed in. These constrained sensor node applications need a low power, high data bandwidth communications solution that delivers both power and data on a low cost, easy to install cable with a small cable connector to the sensor node.
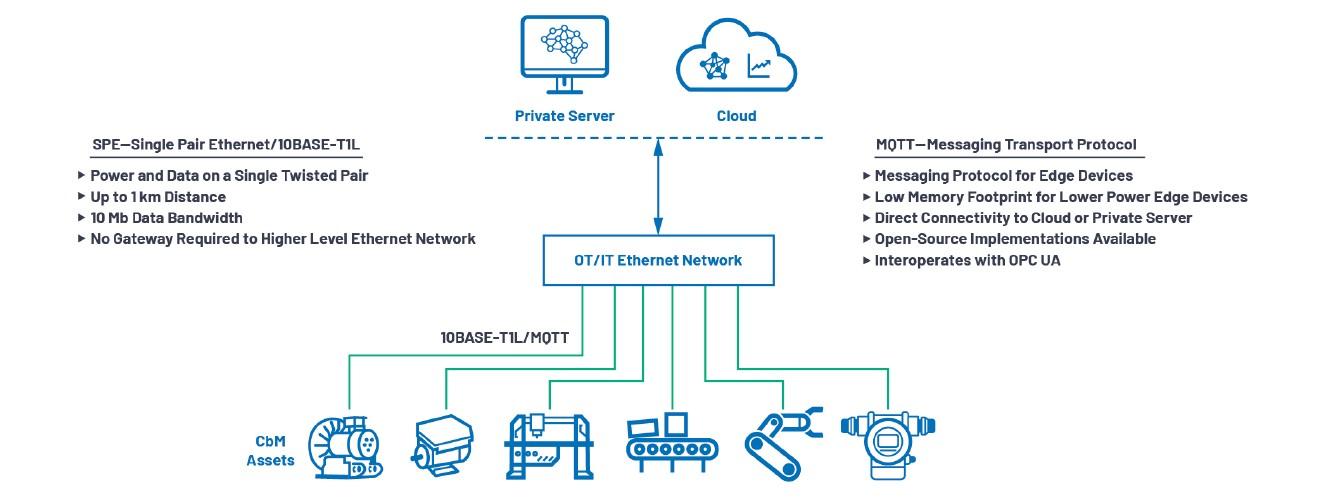
Figure 2: Asset health insights on a converged IT/OT network.
New connectivity solutions
New single pair Ethernet (SPE) physical layer standards developed by the IEEE are offering new connectivity solutions for communicating asset health insights for condition monitoring applications. 10BASE-T1L is a new Ethernet physical layer standard (IEEE 802.3cg-2019) that was approved by the IEEE on November 7, 2019. It will dramatically change the automation industry by significantly improving operational efficiency through seamless Ethernet connectivity to field-level assets. 10BASE-T1L solves the challenges that, to date, have limited the use of Ethernet to the field assets. These challenges include power, bandwidth, cabling, distance, data islands, and Intrinsically Safe Zone 0 (hazardous areas) applications. By solving these challenges for both brownfield upgrades and new greenfield installations, 10BASE-T1L will enable new asset health insights that were previously unavailable and seamlessly communicate them to the control layer and to the cloud/private server. These new insights will awaken new possibilities for data analysis, operational insights, and productivity improvements through a converged Ethernet network from the field assets to the cloud or private server (see Figure 2).
Advantages of 10BASE-T1L Ethernet Connectivity
10BASE-T1L removes the need for complex, power hungry gateways required by legacy communications to connect to the control and management network and enables a converged Ethernet network across the information technology (IT) and operating technology (OT) networks. This converged network delivers a simplified installation, easy device replacement, and faster network commissioning and configuration. This results in faster software updates with simplified root cause analysis and maintenance of field-level assets. The 10BASE-T1L physical layer combined with messaging transport protocol (MQTT) provides a messaging protocol for field assets with a low memory footprint for lower power smart sensors. MQTT provides direct connectivity of asset health insights to the cloud or a private server for advanced data analytics for predictive maintenance techniques.
To communicate with a 10BASE-T1L enabled field asset, a host processor with integrated medium access control (MAC), a passive media converter, or a switch with 10BASE-T1L ports is required. Additional software, special drivers, or customised TCP/IP stacks are not required (see Figure 3). This results in clear advantages for 10BASE-T1L devices:
• 10BASE-T1L is a very low power physical layer technology that can enable very low power smart sensor deployments with a high data bandwidth connectivity solution. • A smart sensor connected with 10BASE-T1L is accessible over the network and can be remotely updated anywhere, at any time. As sensors
become more complex, the probability of software updates increases. Updates are now possible within realistic periods of time via a fast Ethernet connection. • Access to advanced Ethernet network diagnostic tools to simplify root cause analysis. • Increased smart sensor installation flexibility via a single twisted pair cable up to 1km and beyond, with power and data on a single twisted pair cable. • Asset health insights are now available remotely, via a web server running on the field asset, reducing the need for a maintenance technician to walk the floor to monitor an asset’s health – a significant cost saver.
Power and data on two wires
The ADIN1100, ADI’s 10BASE-T1L PHY, enables lower power Ethernet connectivity on a single twisted pair cable that’s over 1000m with only 39mW of power consumption. Single-pair Power over Ethernet (SPoE) or engineered power solutions combined with a 10BASE-T1L PHY provide both power and data over a single twisted pair cable. A 10Mb data bandwidth communication link with significant power capability over the same cable enables smart sensors with the power and connectivity bandwidth to support new condition monitoring applications. With 10BASET1L connectivity, asset health insights are now more accessible as the insights are available across a converged IT/OT Ethernet network. 10BASE-T1L supports > p10
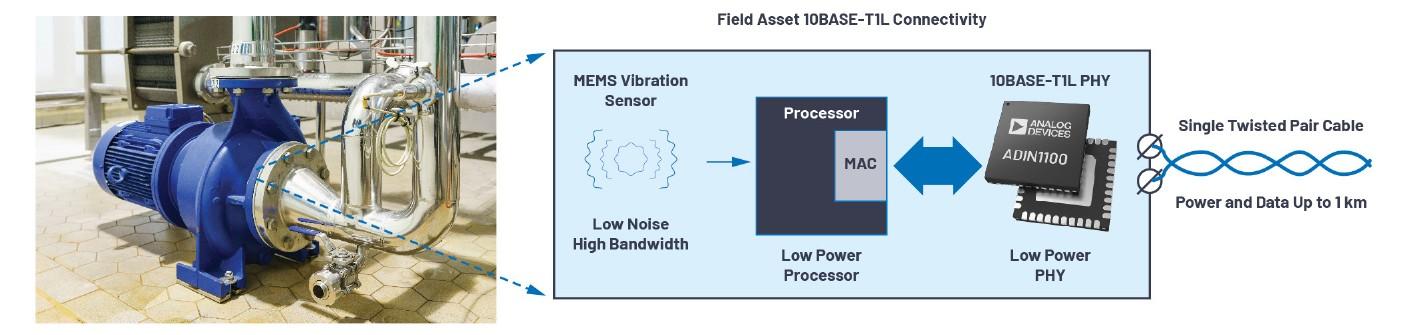
Figure 3: Field asset, smart sensor connectivity with a 10BASE-T1L PHY.
hazardous area use case applications (Intrinsically Safe Zone 0) for process automation deployments and is sometimes referred to as Ethernet-APL. 10BASE-T1L/Ethernet-APL will enable new lower power solutions to connect asset health monitoring smart sensors to the higher level data management systems. This will enable AI and advanced analytic systems to transform asset health data into actionable insights and deploy new predictive maintenance services.
System-level solutions
Complete, system-level solutions for condition monitoring applications will be key to enabling higher quality data and insights, thereby significantly improving manufacturing processes. Advances in 10BASE-T1L/Ethernet-APL, coupled with a real-time, AI-driven sensing technology such as ADI OtoSense, can enable AI integration at all levels of customer systems. The ADI OtoSense platform senses and interprets any sound, vibration, pressure, current, or temperature to provide continuous, condition-based monitoring and ondemand diagnostics. It operates on the field asset at the edge, in real time, both online and offline. The ADI OtoSense system detects anomalies and learns from interaction with condition monitoring domain experts while creating a digital fingerprint to help identify faults in a machine so it can predict breakdowns before they cause costly downtime, damage, or catastrophic failure.
Advancements in sensing, signal processing, connectivity, mechanical packaging techniques, and artificial intelligence at the edge are enabling new condition monitoring solutions and predictive maintenance services that will unlock significant savings and productivity improvements.
New system-level solutions for condition monitoring applications will include MEMS sensors for vibration and shock detection, precision converter technologies for data acquisition, and edge processing to create high quality asset health data. Low power, robust wired and wireless communication solutions provide access to the asset health data from the asset. Wireless communication solutions include SmartMesh or Wireless HART. Wired communications solutions include RS485 or 10BASE-T1L single pair Ethernet that provides power and data on two wires. These technologies along with high performance power management are combined in asset monitoring solutions (such as OtoSense technology), which are complete hardware and AI monitoring solutions that can be mounted on equipment for predictive maintenance (see Figure 4).
Higher quality asset health insights and faster connectivity will extend equipment lifespans, reduce maintenance costs, and eliminate unscheduled downtime while maintaining the highest levels of manufacturing quality and safety in smart factories.
To learn more about complete, systemlevel solutions and artificial intelligence offerings for condition monitoring applications and how ADI can help customers and partners quickly develop and deploy an end-to-end monitoring and predictive maintenance service-based solution, please visit

analog.com/cbm
Maurice O’Brien is the strategic marketing manager for industrial automation at Analog Devices.
Reference: 1 The Costs and Benefits of Advanced Maintenance in Manufacturing. U.S. Department of Commerce, April 2018.
