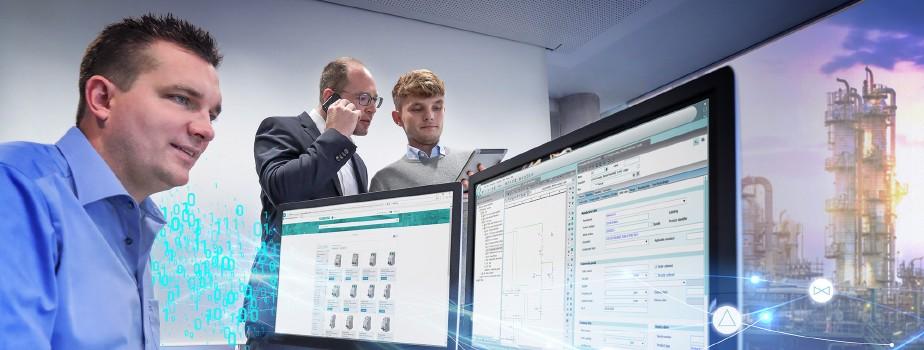
3 minute read
Getting product data at the push of a button
PRODUCT DATA AT THE PUSH OF A BUTTON
Up-to-date and complete product data is vital for the selection of suitable components and for all subsequent steps in the life cycle of the plant. The search for, and the compilation of, this information can be very time-consuming. A new online offer can shorten this process, says Stefanie Westerhaus.
Advertisement
The number of components used in process plants can run into the tens of thousands, even for small projects. Even a simple connection terminal will have certain characteristics that qualify it for a particular application. In addition to electrical rated data according to different standards, there will be connection data, as well as mechanical, geometric or commercial data. More than 50 values are necessary to adequately describe even a simple component. In addition, there will be country-specific approvals, documentation, and corresponding symbols or drawings. Every detail is important – not only for the selection of the suitable component, but also to ensure plant safety.
Attention to detail
The Essen subsidiary of Germany’s Actemium Controlmatic GmbH understands the importance of paying attention to these details. In the automation and process Industry business unit, the company plans and builds plants for its customers. The Essen Actemium branch employs Comos planning software from Siemens – every new Comos project is based on the objects from the in-house master data base. The system stores the technical properties of components as well as administrative, process-specific or costrelated properties. “Our master database contains engineering knowledge from many projects,” explains Björn Hohmeyer, project manager at Actemium and head of the Comos Competence Center. “If a project requires devices that we have not used before, we create them as new base objects – with all the associated data.” Only then are these objects available to all system planners and can be used. This procedure is part of Actemium’s standardisation effort for projects and it helps ensure that the customer later receives the complete plant documentation in a legally compliant manner. “We are the gatekeeper, so to speak, and create the basis for standardised projects in which all components will later work together optimally,” said Hohmeyer. For each component, the team has to retrieve and collect the data from the manufacturer. “The exact typification of the components is one of our challenges. The acquisition of information can resemble the search for a needle in a haystack!”
Anyone involved in engineering processes will recognise this challenge – a great deal of work is required to describe and document a component as completely as possible. With its Comos Engineering Portal (CEP), Siemens has created a web application that delivers free-of-charge product data to Comos users. The manufacturerindependent catalogue is accessible either as a standalone web application or as an embedded interface within the planning software.
Starting with Comos version 10.3, the Product Selector function can be used to select suitable components directly by specifying certain features. The right product can be quickly identified using comparison functions which can then be transferred to Comos projects with just one click. After downloading all specific information, data sheets, design data, etc., these are directly assigned to the component in Comos. The same applies to all accessories.
Reduced time expenditure
Actemium Controlmatic in Essen has been using the CEP since 2019. “Our planning projects continue to be developed with our base objects only. With the CEP, we benefit from an efficient way to add new products to these base objects,” said Hohmeyer. “Today, I can search directly from within Comos in the CEP online catalogue for the required component. With a single mouse click I have all the necessary information at my fingertips, saving huge amounts of time.” plus-circle